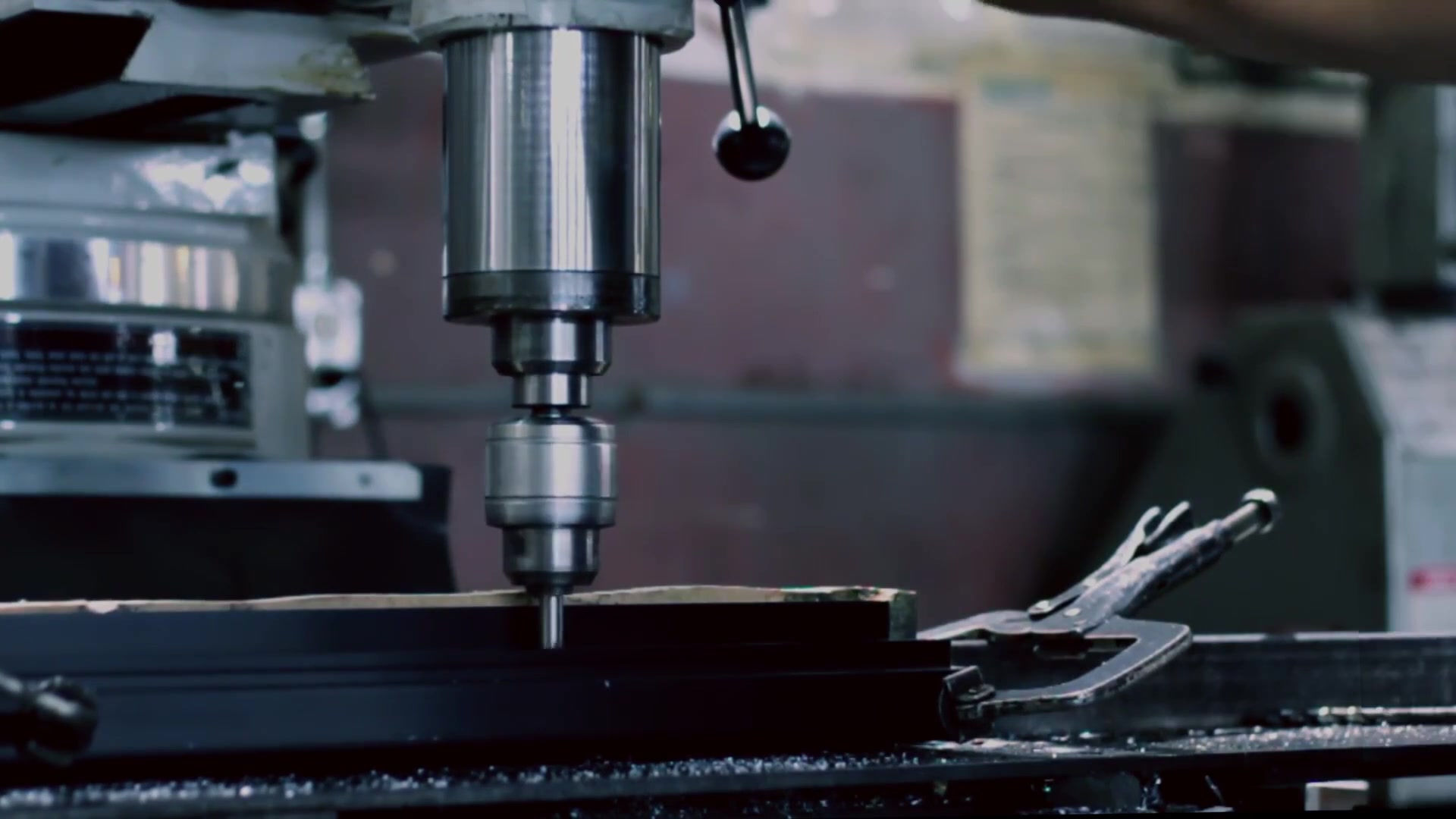
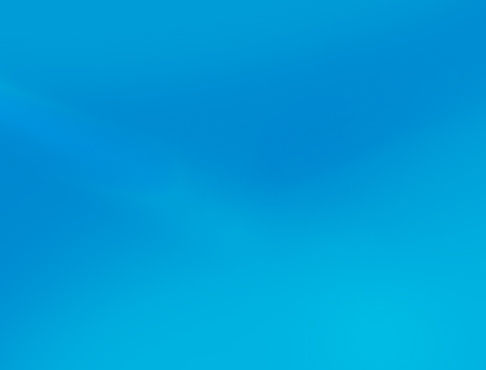
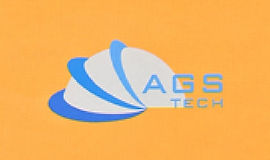
Глобальный производитель на заказ, интегратор, консолидатор, партнер по аутсорсингу широкого спектра продуктов и услуг.
Мы являемся вашим универсальным источником для производства, изготовления, проектирования, консолидации, интеграции, аутсорсинга изготовленных на заказ и готовых продуктов и услуг.
Choose your Language
-
Изготовление на заказ
-
Внутреннее и глобальное контрактное производство
-
Производственный аутсорсинг
-
Внутренние и глобальные закупки
-
Консолидация
-
Инженерная интеграция
-
Инженерные услуги
Проще говоря, КОМПОЗИТЫ или КОМПОЗИТНЫЕ МАТЕРИАЛЫ - это материалы, состоящие из двух или нескольких материалов с разными физическими или химическими свойствами, но при объединении они становятся материалом, который отличается от составляющих материалов. Мы должны отметить, что составляющие материалы остаются отдельными и отчетливыми в структуре. Целью производства композитного материала является получение продукта, который превосходит входящие в его состав компоненты и сочетает в себе желаемые свойства каждого из них. В качестве примера; прочность, малый вес или более низкая цена могут быть мотивом для разработки и производства композита. Композиты, которые мы предлагаем, представляют собой армированные частицами композиты, армированные волокнами композиты, в том числе композиты с керамической матрицей / полимерной матрицей / металлической матрицей / углерод-углерод / гибридные композиты, конструкционные, ламинированные и сэндвич-структурированные композиты и нанокомпозиты.
Методы изготовления, которые мы используем в производстве композитных материалов: пултрузия, процессы производства препрега, усовершенствованная укладка волокна, намотка нити, индивидуальная укладка волокна, процесс напыления стекловолокна, тафтинг, процесс ланоксида, z-пиннинг.
Многие композиционные материалы состоят из двух фаз: матрицы, которая является непрерывной и окружает другую фазу; и дисперсная фаза, окруженная матрицей.
Мы рекомендуем вам нажать здесь, чтобыСКАЧАТЬ наши схематические иллюстрации производства композитов и композитных материалов от AGS-TECH Inc.
Это поможет вам лучше понять информацию, которую мы предоставляем вам ниже.
• КОМПОЗИТЫ, УСИЛЕННЫЕ ЧАСТИЦАМИ: Эта категория состоит из двух типов: композиты с крупными частицами и композиты, упрочненные дисперсией. В первом типе взаимодействие частицы с матрицей нельзя рассматривать на атомном или молекулярном уровне. Вместо этого действует механика сплошных сред. С другой стороны, в дисперсионно-упрочненных композитах частицы обычно намного меньше в диапазоне десятков нанометров. Примером композита с крупными частицами являются полимеры, к которым добавлены наполнители. Наполнители улучшают свойства материала и могут заменить часть объема полимера более экономичным материалом. Объемные доли двух фаз влияют на поведение композита. Композиты с крупными частицами используются с металлами, полимерами и керамикой. CERMETS являются примерами керамических/металлических композитов. Самый распространенный кермет – это цементированный карбид. Он состоит из тугоплавкой карбидной керамики, такой как частицы карбида вольфрама, в матрице из металла, такого как кобальт или никель. Эти карбидные композиты широко используются в качестве режущих инструментов для закаленной стали. Твердые частицы карбида отвечают за режущее действие, а их ударная вязкость повышается за счет пластичной металлической матрицы. Таким образом, мы получаем преимущества обоих материалов в одном композите. Другим распространенным примером композита с крупными частицами, который мы используем, являются частицы сажи, смешанные с вулканизированной резиной для получения композита с высокой прочностью на растяжение, ударной вязкостью, сопротивлением разрыву и истиранию. Примером дисперсно-упрочненного композита являются металлы и сплавы металлов, упрочняемые и упрочняемые за счет равномерного диспергирования мелких частиц очень твердого и инертного материала. При добавлении очень мелких чешуек оксида алюминия к металлической алюминиевой матрице мы получаем спеченный алюминиевый порошок, обладающий повышенной жаропрочностью.
• КОМПОЗИТЫ, АРМИРОВАННЫЕ ВОЛОКНОМ: Эта категория композитов на самом деле является самой важной. Целью достижения является высокая прочность и жесткость на единицу веса. Состав, длина, ориентация и концентрация волокон в этих композитах имеют решающее значение для определения свойств и полезности этих материалов. Мы используем три группы волокон: усы, волокна и проволоки. УИСКЕРЫ представляют собой очень тонкие и длинные монокристаллы. Они относятся к самым прочным материалам. Некоторыми примерами нитевидных материалов являются графит, нитрид кремния, оксид алюминия. ВОЛОКОНЫ, с другой стороны, представляют собой в основном полимеры или керамику и находятся в поликристаллическом или аморфном состоянии. Третья группа — это тонкие ПРОВОЛОКИ, которые имеют относительно большие диаметры и часто состоят из стали или вольфрама. Примером композитного материала, армированного проволокой, являются автомобильные шины, в которых стальная проволока находится внутри резины. В зависимости от материала матрицы, мы имеем следующие композиты:
ПОЛИМЕРНО-МАТРИЧНЫЕ КОМПОЗИТЫ: изготавливаются из полимерной смолы и волокон в качестве армирующего компонента. Подгруппа из них, называемая композитами из полимера, армированного стекловолокном (GFRP), содержит непрерывные или прерывистые стекловолокна в полимерной матрице. Стекло обладает высокой прочностью, экономично, легко превращается в волокна и химически инертно. Недостатками являются их ограниченная жесткость и жесткость, температура эксплуатации только до 200 – 300 градусов по Цельсию. Стекловолокно подходит для автомобильных кузовов и транспортного оборудования, кузовов морских транспортных средств, контейнеров для хранения. Они не подходят для аэрокосмической промышленности и изготовления мостов из-за ограниченной жесткости. Другая подгруппа называется Композитный полимер, армированный углеродным волокном (CFRP). Здесь углерод — это наш волокнистый материал в полимерной матрице. Углерод известен своим высоким удельным модулем и прочностью, а также способностью сохранять их при высоких температурах. Углеродные волокна могут предложить нам стандартные, промежуточные, высокие и сверхвысокие модули растяжения. Кроме того, углеродные волокна обладают разнообразными физическими и механическими характеристиками и, следовательно, подходят для различных индивидуальных инженерных приложений. Композиты из углепластика можно рассматривать для производства спортивного и развлекательного оборудования, сосудов под давлением и компонентов аэрокосмической конструкции. Тем не менее, другая подгруппа, полимерные композиты, армированные арамидным волокном, также являются высокопрочными и модульными материалами. Соотношение прочности и веса у них исключительно высокое. Арамидные волокна также известны под торговыми названиями KEVLAR и NOMEX. При растяжении они работают лучше, чем другие полимерные волокнистые материалы, но слабы при сжатии. Арамидные волокна прочны, ударопрочны, устойчивы к ползучести и усталости, стабильны при высоких температурах, химически инертны, за исключением воздействия сильных кислот и щелочей. Арамидные волокна широко используются в спортивных товарах, бронежилетах, шинах, канатах, оболочках оптоволоконных кабелей. Существуют и другие армирующие волокна материалы, но они используются в меньшей степени. В основном это бор, карбид кремния, оксид алюминия. С другой стороны, материал полимерной матрицы также имеет решающее значение. Он определяет максимальную рабочую температуру композита, поскольку полимер обычно имеет более низкую температуру плавления и разложения. Полиэфиры и виниловые эфиры широко используются в качестве полимерной матрицы. Также используются смолы, обладающие отличной влагостойкостью и механическими свойствами. Например, полиимидная смола может использоваться при температуре до 230 градусов Цельсия.
КОМПОЗИТЫ С МЕТАЛЛИЧЕСКОЙ МАТРИЦЕЙ: В этих материалах мы используем пластичную металлическую матрицу, а рабочие температуры, как правило, выше, чем у составляющих их компонентов. По сравнению с композитами с полимерной матрицей они могут иметь более высокие рабочие температуры, быть негорючими и могут иметь лучшую стойкость к разложению органическими жидкостями. Однако они дороже. Армирующие материалы, такие как вискеры, частицы, непрерывные и прерывистые волокна; и обычно используются матричные материалы, такие как медь, алюминий, магний, титан, суперсплавы. Примерами применения являются компоненты двигателя, изготовленные из матрицы из алюминиевого сплава, армированной оксидом алюминия и углеродными волокнами.
КЕРАМИЧЕСКИЕ МАТРИЧНЫЕ КОМПОЗИТЫ: Керамические материалы известны своей исключительно хорошей надежностью при высоких температурах. Однако они очень хрупкие и имеют низкие значения вязкости разрушения. Встраивая частицы, волокна или нитевидные кристаллы одной керамики в матрицу другой, мы можем получить композиты с более высокой стойкостью к разрушению. Эти встроенные материалы в основном препятствуют распространению трещины внутри матрицы с помощью некоторых механизмов, таких как отклонение вершины трещины или образование перемычек через поверхности трещины. Например, оксиды алюминия, армированные нитевидными кристаллами SiC, используются в качестве режущих пластин для обработки твердых сплавов. Они могут показать лучшие характеристики по сравнению с цементированными карбидами.
УГЛЕРОД-УГЛЕРОДНЫЕ КОМПОЗИТЫ: как армирование, так и матрица изготовлены из углерода. Они обладают высокими модулями растяжения и прочностью при высоких температурах свыше 2000°С, сопротивлением ползучести, высокой вязкостью разрушения, низким коэффициентом теплового расширения, высокой теплопроводностью. Эти свойства делают их идеальными для применений, требующих устойчивости к тепловому удару. Однако слабостью углерод-углеродных композитов является их уязвимость к окислению при высоких температурах. Типичными примерами использования являются пресс-формы для горячего прессования, производство современных компонентов газотурбинных двигателей.
ГИБРИДНЫЕ КОМПОЗИТЫ: два или более разных типа волокон смешаны в одной матрице. Таким образом, можно адаптировать новый материал с комбинацией свойств. Например, когда в полимерную смолу включены и углеродные, и стеклянные волокна. Углеродные волокна обеспечивают жесткость и прочность низкой плотности, но они дороги. С другой стороны, стекло недорогое, но ему не хватает жесткости углеродного волокна. Гибридный стеклоуглеродный композит прочнее и жестче, и его можно производить с меньшими затратами.
ПЕРЕРАБОТКА АРМИРОВАННЫХ ВОЛОКНОМ КОМПОЗИТОВ: Для непрерывных армированных волокном пластиков с равномерно распределенными волокнами, ориентированными в одном направлении, мы используем следующие методы.
ПУЛЬТРУЗИЯ: Изготавливаются стержни, балки и трубы непрерывных длин и постоянных сечений. Ровинги из непрерывных волокон пропитывают термореактивной смолой и протягивают через стальную фильеру, чтобы предварительно придать им желаемую форму. Затем они проходят через прецизионную матрицу для отверждения, чтобы получить окончательную форму. Так как отверждающая головка нагревается, она отверждает полимерную матрицу. Съемники протягивают материал через матрицы. Используя вставленные полые стержни, мы можем получить трубы и полые геометрические формы. Метод пултрузии автоматизирован и обеспечивает высокую производительность. Возможно изготовление изделия любой длины.
ПРОЦЕСС ПРОИЗВОДСТВА ПРЕПРЕГА: Препрег представляет собой арматуру из непрерывных волокон, предварительно пропитанную частично отвержденной полимерной смолой. Он широко используется для структурных приложений. Материал поставляется в виде ленты и поставляется в виде ленты. Производитель формирует его напрямую и полностью отверждает без добавления смолы. Поскольку препреги подвергаются реакциям отверждения при комнатной температуре, их хранят при 0°С или более низких температурах. После использования оставшиеся ленты хранятся обратно при низких температурах. Используются термопластичные и термореактивные смолы, широко распространены армирующие волокна из углерода, арамида и стекла. Чтобы использовать препреги, сначала удаляют бумажную подложку, а затем осуществляют изготовление, укладывая ленту препрега на обработанную поверхность (процесс укладки). Для получения желаемой толщины можно уложить несколько слоев. Частой практикой является чередование ориентации волокон для получения ламината с поперечными или угловыми слоями. Наконец, для отверждения применяются тепло и давление. Для резки препрегов и укладки используются как ручная обработка, так и автоматизированные процессы.
НАМОТКА ВОЛОТА: Непрерывные армирующие волокна точно располагаются по заданному шаблону, чтобы следовать полой и обычно циклокруглой форме. Волокна сначала проходят через ванну со смолой, а затем автоматически наматываются на оправку. После нескольких повторений намотки получают желаемую толщину и отверждение проводят либо при комнатной температуре, либо в печи. Теперь оправку снимают и изделие извлекают из формы. Намотка нитей может обеспечить очень высокое отношение прочности к весу за счет намотки волокон по окружности, спирали и полярным узорам. По этой технологии изготавливаются трубы, резервуары, кожухи.
• КОНСТРУКЦИОННЫЕ КОМПОЗИТЫ: Обычно они состоят как из гомогенных, так и из композиционных материалов. Поэтому их свойства определяются составляющими материалами и геометрическим рисунком его элементов. Вот основные типы:
ЛАМИНАРНЫЕ КОМПОЗИТЫ: Эти конструкционные материалы изготавливаются из двумерных листов или панелей с предпочтительными направлениями высокой прочности. Слои укладываются и цементируются вместе. Чередуя направления высокой прочности в двух перпендикулярных осях, мы получаем композит, обладающий высокой прочностью в обоих направлениях в двумерной плоскости. Регулируя углы слоев, можно изготовить композит с прочностью в предпочтительных направлениях. Так производятся современные лыжи.
СЭНДВИЧ-ПАНЕЛИ: Эти конструкционные композиты легкие, но при этом обладают высокой жесткостью и прочностью. Сэндвич-панели состоят из двух внешних листов, изготовленных из жесткого и прочного материала, такого как алюминиевые сплавы, армированный волокном пластик или сталь, и сердцевины между внешними листами. Сердечник должен быть легким и в большинстве случаев иметь низкий модуль упругости. Популярными материалами сердцевины являются жесткие полимерные пены, дерево и соты. Сэндвич-панели широко используются в строительной отрасли в качестве кровельного, напольного или стенового материала, а также в аэрокосмической промышленности.
• НАНОКОМПОЗИТЫ: Эти новые материалы состоят из частиц наноразмеров, встроенных в матрицу. Используя нанокомпозиты, мы можем производить каучуковые материалы, которые являются очень хорошими барьерами для проникновения воздуха, сохраняя при этом свои каучуковые свойства неизменными.