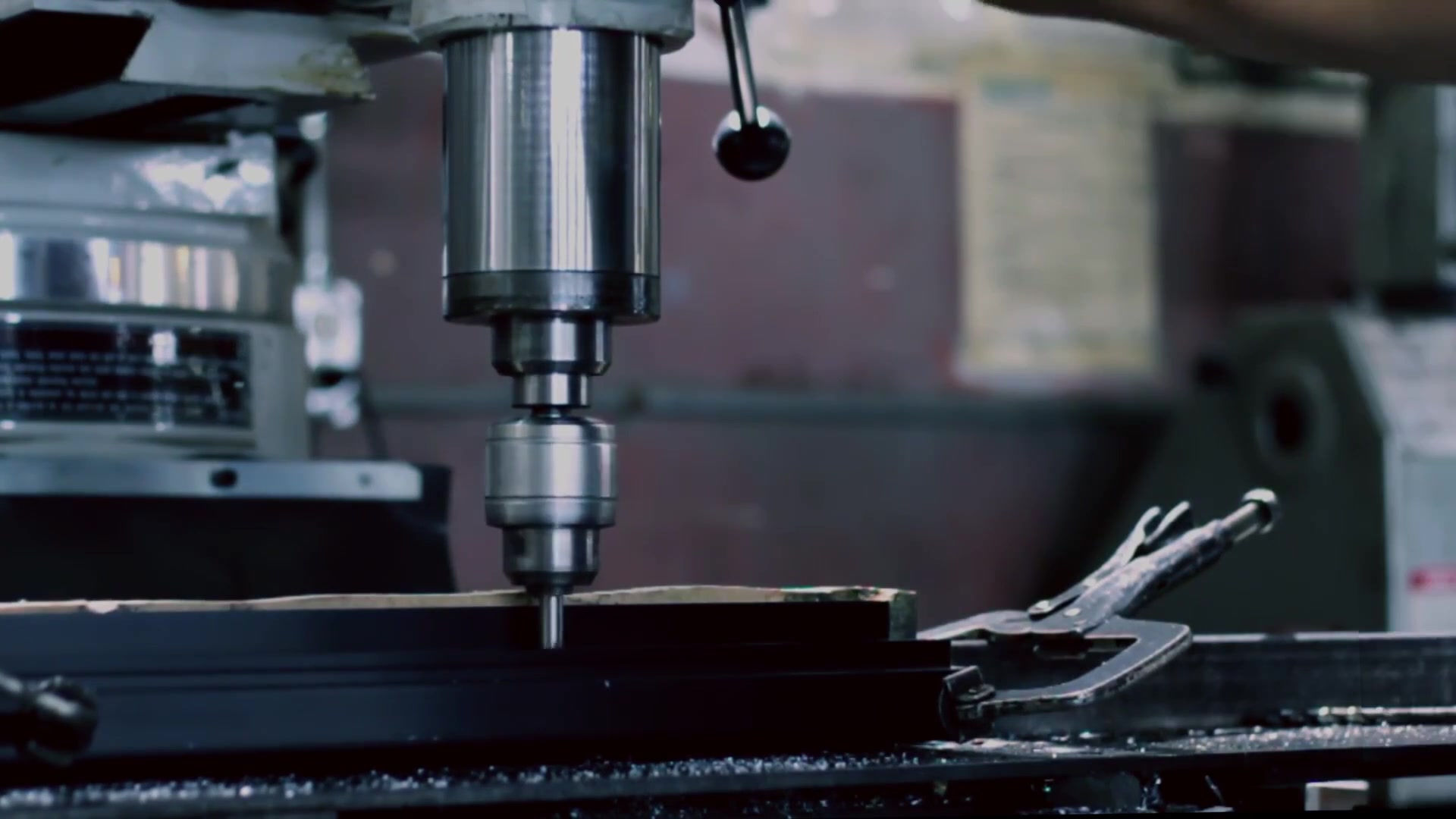
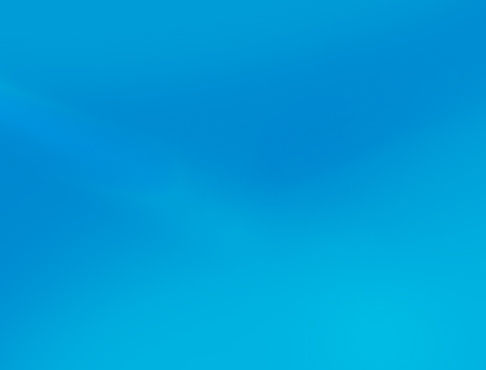
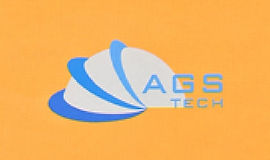
Глобальный производитель на заказ, интегратор, консолидатор, партнер по аутсорсингу широкого спектра продуктов и услуг.
Мы являемся вашим универсальным источником для производства, изготовления, проектирования, консолидации, интеграции, аутсорсинга изготовленных на заказ и готовых продуктов и услуг.
Choose your Language
-
Изготовление на заказ
-
Внутреннее и глобальное контрактное производство
-
Производственный аутсорсинг
-
Внутренние и глобальные закупки
-
Консолидация
-
Инженерная интеграция
-
Инженерные услуги
Мы соединяем, собираем и скрепляем ваши изготовленные детали и превращаем их в готовые изделия или полуфабрикаты, используя СВАРКУ, ПАЙКУ, ПАЙКУ, СПЕЧЕНИЕ, СКЛЕИВАНИЕ, КРЕПЛЕНИЕ, ПРЕСС-ФИТИНГ. Некоторыми из наших самых популярных сварочных процессов являются дуговая, газокислородная, контактная, проекционная, шовная, осадочная, ударная, твердотельная, электронно-лучевая, лазерная, термитная, индукционная сварка. Нашими популярными процессами пайки являются горелка, индукционная пайка, печная пайка и пайка погружением. Нашими методами пайки являются железо, горячая плита, печь, индукция, погружение, волна, пайка оплавлением и ультразвуковая пайка. Для клеевого соединения мы часто используем термопласты и термореактивные, эпоксидные, фенольные, полиуретановые, клеевые сплавы, а также некоторые другие химикаты и ленты. Наконец, наши процессы крепления состоят из забивания гвоздей, завинчивания гаек и болтов, заклепывания, зажима, закрепления штифтами, сшивания и скрепления скобами, а также прессовой посадки.
• СВАРКА: Сварка включает в себя соединение материалов путем плавления заготовок и введения присадочных материалов, которые также соединяются с расплавленной сварочной ванной. Когда участок остынет, получим прочный стык. В некоторых случаях применяется давление. В отличие от сварки, операции пайки и пайки включают только плавление материала с более низкой температурой плавления между заготовками, а заготовки не плавятся. Мы рекомендуем вам нажать здесь, чтобыСКАЧАТЬ наши схематические иллюстрации сварочных процессов от AGS-TECH Inc.
Это поможет вам лучше понять информацию, которую мы предоставляем вам ниже.
В ДУГОВОЙ СВАРКЕ мы используем источник питания и электрод для создания электрической дуги, которая плавит металлы. Место сварки защищено защитным газом, паром или другим материалом. Этот процесс популярен для сварки автомобильных деталей и стальных конструкций. При дуговой сварке металлическим электродом (SMAW), также известной как сварка стержнем, стержень электрода подносится близко к основному материалу, и между ними возникает электрическая дуга. Электродный стержень плавится и действует как наполнитель. Электрод также содержит флюс, который действует как слой шлака и выделяет пары, действующие как защитный газ. Они защищают зону сварки от загрязнения окружающей среды. Другие наполнители не используются. Недостатками этого процесса являются его медлительность, необходимость частой замены электродов, необходимость отщепления остаточного шлака от флюса. Ряд металлов, таких как железо, сталь, никель, алюминий, медь и т. д. Можно сваривать. Его преимуществами являются его недорогие инструменты и простота использования. Газовая дуговая сварка металлическим электродом (GMAW), также известная как металл-инертный газ (MIG), у нас есть непрерывная подача наполнителя расходуемой электродной проволоки и инертного или частично инертного газа, который обтекает проволоку, защищая область сварки от загрязнения окружающей средой. Можно сваривать сталь, алюминий и другие цветные металлы. Преимуществами MIG являются высокая скорость сварки и хорошее качество. Недостатками являются его сложное оборудование и проблемы, с которыми приходится сталкиваться в ветреную погоду на открытом воздухе, потому что мы должны поддерживать стабильность защитного газа вокруг зоны сварки. Разновидностью GMAW является дуговая сварка с флюсовой проволокой (FCAW), которая состоит из тонкой металлической трубки, заполненной флюсовыми материалами. Иногда флюса внутри трубки достаточно для защиты от загрязнения окружающей среды. Дуговая сварка под флюсом (SAW) — широко автоматизированный процесс, включающий непрерывную подачу проволоки и дугу, которая зажигается под слоем флюсового покрытия. Производительность и качество высоки, сварочный шлак легко отделяется, и у нас нет дыма на рабочем месте. Недостатком является то, что его можно использовать только для сварки parts в определенных положениях. При дуговой сварке вольфрамовым электродом (GTAW) или сварке вольфрамовым электродом в среде инертного газа (TIG) мы используем вольфрамовый электрод вместе с отдельным наполнителем и инертными или почти инертными газами. Как мы знаем, вольфрам имеет высокую температуру плавления, и это очень подходящий металл для очень высоких температур. Вольфрам в TIG не расходуется, в отличие от других методов, описанных выше. Медленная, но качественная технология сварки, имеющая преимущества перед другими методами сварки тонких материалов. Подходит для многих металлов. Плазменная дуговая сварка аналогична, но для создания дуги используется плазменный газ. Дуга при плазменной дуговой сварке относительно более концентрированная по сравнению с GTAW и может использоваться для более широкого диапазона толщин металла при гораздо более высоких скоростях. GTAW и плазменная дуговая сварка могут применяться к более или менее одинаковым материалам.
КИСЛОРОДНО-ТОПЛИВНАЯ / КИСЛОРОДНАЯ СВАРКА, также называемая кислородно-ацетиленовой сваркой, кислородной сваркой, газовой сваркой, осуществляется с использованием газового топлива и кислорода для сварки. Поскольку электроэнергия не используется, он портативный и может использоваться там, где нет электричества. Используя сварочную горелку, мы нагреваем детали и присадочный материал, чтобы получить общую ванну расплавленного металла. Можно использовать различные виды топлива, такие как ацетилен, бензин, водород, пропан, бутан и т. д. При кислородно-топливной сварке мы используем два контейнера, один для топлива, а другой для кислорода. Кислород окисляет топливо (сжигает его).
СОПРОТИВНАЯ СВАРКА: Этот тип сварки использует джоулев нагрев, и тепло генерируется в месте, где подается электрический ток в течение определенного времени. Через металл пропускают большие токи. В этом месте образуются лужи расплавленного металла. Методы контактной сварки популярны из-за их эффективности и небольшого потенциала загрязнения. Однако недостатками являются относительно высокие затраты на оборудование и присущие этому способу ограничения относительно тонких заготовок. ТОЧЕЧНАЯ СВАРКА является одним из основных видов контактной сварки. Здесь мы соединяем два или более перекрывающихся листа или заготовки, используя два медных электрода, чтобы сжать листы вместе и пропустить через них сильный ток. Материал между медными электродами нагревается, и в этом месте образуется расплавленная ванна. Затем ток прекращается, и наконечники медных электродов охлаждают место сварки, поскольку электроды охлаждаются водой. Применение нужного количества тепла к нужному материалу и толщине является ключевым моментом для этой техники, потому что при неправильном применении соединение будет слабым. Точечная сварка имеет преимущества, заключающиеся в том, что она не вызывает значительной деформации заготовок, энергоэффективна, проста в автоматизации и обеспечивает выдающуюся производительность, а также не требует использования каких-либо наполнителей. Недостатком является то, что, поскольку сварка происходит точечно, а не образует непрерывный шов, общая прочность может быть относительно ниже по сравнению с другими методами сварки. ШВОВАЯ СВАРКА, с другой стороны, производит сварные швы на поверхностях сходных материалов. Шов может быть встык или внахлест. Сварка швов начинается с одного конца и постепенно переходит к другому. В этом методе также используются два электрода из меди для приложения давления и тока к области сварки. Электроды в форме дисков вращаются с постоянным контактом вдоль линии шва и производят непрерывный шов. Здесь также электроды охлаждаются водой. Сварные швы очень прочные и надежные. Другими методами являются проекционная сварка, сварка оплавлением и сварка с осадкой.
СВАРКА ТВЕРДОГО ТЕЛА немного отличается от предыдущих методов, описанных выше. Коалесценция происходит при температурах ниже температуры плавления соединяемых металлов и без использования металлического наполнителя. В некоторых процессах может использоваться давление. Существуют различные методы: СОЭКСТРУЖНАЯ СВАРКА, при которой разнородные металлы выдавливаются через одну и ту же головку, СВАРКА ХОЛОДНЫМ ДАВЛЕНИЕМ, при которой мы соединяем мягкие сплавы при температуре ниже их точки плавления, ДИФФУЗИОННАЯ СВАРКА – метод без видимых линий сварки, СВАРКА ВЗРЫВОМ для соединения разнородных материалов, например, коррозионностойких сплавов с конструкционными. сталей, ЭЛЕКТРОМАГНИТНО-ИМПУЛЬСНАЯ СВАРКА, при которой трубы и листы ускоряются электромагнитными силами, КУЗОВАЯ СВАРКА, заключающаяся в нагреве металлов до высоких температур и сбивании их вместе, СВАРКА ТРЕНИЕМ, при которой выполняется сварка с достаточным трением, СВАРКА ТРЕНИЕМ С ПЕРЕМЕШИВАНИЕМ, при которой вращающийся расходуемый инструмент, пересекающий линию стыка, СВАРКА ГОРЯЧИМ ДАВЛЕНИЕМ, когда мы сжимаем металлы вместе при повышенных температурах ниже температуры плавления в вакууме или инертных газах, СВАРКА ГОРЯЧИМ ИЗОСТАТИЧЕСКИМ ДАВЛЕНИЕМ, процесс, при котором мы применяем давление с использованием инертных газов внутри сосуда, СВАРКА ВАЛКА, где мы соединяем разнородных материалов, помещая их между два вращающихся колеса, УЛЬТРАЗВУКОВАЯ СВАРКА, при которой тонкие листы металла или пластика свариваются с использованием высокочастотной вибрационной энергии.
Другими нашими сварочными процессами являются ЭЛЕКТРОННО-ЛУЧЕВАЯ СВАРКА с глубоким проплавлением и быстрой обработкой, но поскольку это дорогостоящий метод, мы рассматриваем его для особых случаев, ЭЛЕКТРОШЛАКОВАЯ СВАРКА, метод, подходящий только для тяжелых толстых листов и заготовок из стали, ИНДУКЦИОННАЯ СВАРКА, где мы используем электромагнитную индукцию и нагрев наших электропроводящих или ферромагнитных заготовок, ЛАЗЕРНАЯ СВАРКА также с глубоким проплавлением и быстрой обработкой, но является дорогостоящим методом, ЛАЗЕРНАЯ ГИБРИДНАЯ СВАРКА, которая сочетает LBW и GMAW в одной сварочной головке и способна перекрыть зазоры 2 мм между пластинами, УДАРНАЯ СВАРКА, которая включает электрический разряд с последующей ковкой материалов под давлением, ТЕРМИТНАЯ СВАРКА, включающая экзотермическую реакцию между порошками алюминия и оксида железа., ЭЛЕКТРОГАЗОВАЯ СВАРКА с плавящимся электродом и используется только со сталью в вертикальном положении, и, наконец, ДУГОВАЯ СВАРКА ШПИЛЬКИ для соединения шпильки с основанием. материала с помощью тепла и давления.
Мы рекомендуем вам нажать здесь, чтобыСКАЧАТЬ наши схематические иллюстрации процессов пайки, пайки и склеивания от AGS-TECH Inc.
Это поможет вам лучше понять информацию, которую мы предоставляем вам ниже.
• ПАЙКА: Мы соединяем два или более металлов, нагревая присадочные металлы между ними до температуры их плавления и используя капиллярное действие для их растекания. Процесс похож на пайку, но температура плавления наполнителя при пайке выше. Как и при сварке, флюс защищает присадочный материал от атмосферного загрязнения. После охлаждения заготовки соединяются между собой. Процесс включает в себя следующие ключевые этапы: хорошая посадка и зазор, правильная очистка основных материалов, правильное крепление, правильный выбор флюса и атмосферы, нагрев сборки и, наконец, очистка паяной сборки. Одним из наших процессов пайки является ГОРЕЛКА, популярный метод, выполняемый вручную или автоматически. Подходит для небольших производственных заказов и особых случаев. Тепло подается с помощью газового пламени вблизи места пайки. ПАЙКА В ПЕЧИ требует меньше навыков оператора и представляет собой полуавтоматический процесс, пригодный для промышленного массового производства. Преимуществом этого метода являются как контроль температуры, так и контроль атмосферы в печи, поскольку первый позволяет нам контролировать циклы нагрева и устранять локальный нагрев, как в случае пайки горелкой, а второй защищает деталь от окисления. Используя отсадочное оборудование, мы можем снизить производственные затраты до минимума. Недостатками являются высокое энергопотребление, стоимость оборудования и более сложные конструктивные решения. ВАКУУМНАЯ ПАЙКА происходит в вакуумной печи. Температурная однородность сохраняется, и мы получаем очень чистые соединения без флюсов с очень небольшими остаточными напряжениями. Термическая обработка может иметь место во время вакуумной пайки из-за низких остаточных напряжений, возникающих во время медленных циклов нагрева и охлаждения. Основным недостатком является его высокая стоимость, поскольку создание вакуумной среды является дорогостоящим процессом. Еще один метод – ПАЯКА ПОГРУЖЕНИЕМ – соединяет неподвижные детали, при этом на сопрягаемые поверхности наносится припой. После этого детали fixtured погружают в ванну с расплавленной солью, такой как хлорид натрия (поваренная соль), которая действует как теплоноситель и флюс. Воздух исключается, и поэтому не происходит образования оксида. При ИНДУКЦИОННОЙ ПАЯКЕ мы соединяем материалы присадочным металлом, температура плавления которого ниже, чем у основных материалов. Переменный ток от индукционной катушки создает электромагнитное поле, которое вызывает индукционный нагрев в основном ферромагнитных материалов. Этот метод обеспечивает избирательный нагрев, хорошие соединения с наполнителями, текущими только в нужных областях, небольшое окисление, поскольку отсутствует пламя, а охлаждение происходит быстро, быстрый нагрев, консистенция и пригодность для крупносерийного производства. Для ускорения наших процессов и обеспечения согласованности мы часто используем преформы. Информацию о нашем предприятии для пайки керамики и металла, герметизации, вакуумных вводов, высоком и сверхвысоком вакууме и компонентах управления подачей жидкости можно найти здесь: Брошюра о паяльном заводе
• ПАЯЯ: При пайке мы имеем дело не с плавлением заготовок, а с плавлением присадочного металла с более низкой температурой плавления, чем у соединяемых деталей, который затекает в соединение. Припой при пайке плавится при более низкой температуре, чем при пайке. Мы используем бессвинцовые сплавы для пайки и соответствуют требованиям RoHS, а для различных применений и требований у нас есть различные и подходящие сплавы, такие как серебряный сплав. Пайка предлагает нам соединения, непроницаемые для газа и жидкости. При МЯГКОЙ ПАЙКЕ наш припой имеет температуру плавления ниже 400 градусов по Цельсию, в то время как при ПАЯКЕ СЕРЕБРОМ и ПАЙКЕ нам нужны более высокие температуры. Мягкая пайка использует более низкие температуры, но не дает прочных соединений для требовательных приложений при повышенных температурах. С другой стороны, серебряная пайка требует высоких температур, обеспечиваемых горелкой, и дает нам прочные соединения, подходящие для высокотемпературных применений. Пайка требует самых высоких температур, и обычно используется горелка. Поскольку паяные соединения очень прочные, они хорошо подходят для ремонта тяжелых железных предметов. В наших производственных линиях мы используем как ручную пайку, так и автоматические линии пайки. ИНДУКЦИОННАЯ ПАЙКА использует высокочастотный переменный ток в медной катушке для облегчения индукционного нагрева. В месте пайки индуцируются токи, в результате чего на высоком сопротивлении joint выделяется тепло. Это тепло расплавляет присадочный металл. Также используется флюс. Индукционная пайка является хорошим методом пайки цилиндров и труб в непрерывном процессе путем наматывания на них катушек. Пайка некоторых материалов, таких как графит и керамика, более сложна, поскольку требует покрытия деталей подходящим металлом перед пайкой. Это облегчает межфазное соединение. Мы припаиваем такие материалы специально для герметичных упаковок. Мы производим наши печатные платы (PCB) в больших объемах, в основном, с использованием пайки волной. Только для небольшого количества прототипов мы используем ручную пайку паяльником. Мы используем пайку волной припоя как для сквозных, так и для поверхностного монтажа печатных плат (PCBA). Временный клей удерживает компоненты прикрепленными к печатной плате, а сборка помещается на конвейер и проходит через оборудование, содержащее расплавленный припой. Сначала печатная плата оплавляется, а затем поступает в зону предварительного нагрева. Расплавленный припой находится в поддоне и имеет на своей поверхности узор стоячих волн. Когда печатная плата движется по этим волнам, эти волны касаются нижней части печатной платы и прилипают к контактным площадкам для пайки. Припой остается только на выводах и контактных площадках, но не на самой печатной плате. Волны в расплавленном припое должны хорошо контролироваться, чтобы не было разбрызгивания, а вершины волн не касались и не загрязняли нежелательные участки платы. При пайке оплавлением мы используем липкую паяльную пасту для временного прикрепления электронных компонентов к плате. Затем платы помещают в печь оплавления с контролем температуры. Здесь припой плавится и соединяет компоненты навсегда. Мы используем эту технику как для компонентов поверхностного монтажа, так и для компонентов сквозного монтажа. Надлежащий контроль температуры и регулировка температуры печи необходимы, чтобы избежать разрушения электронных компонентов на плате из-за их перегрева выше их максимальных температурных пределов. В процессе пайки оплавлением у нас фактически есть несколько областей или стадий, каждая из которых имеет свой температурный профиль, например, стадия предварительного нагрева, стадия термической выдержки, стадия оплавления и охлаждения. Эти различные шаги необходимы для безповрежденной пайки оплавлением сборок печатных плат (PCBA). УЛЬТРАЗВУКОВАЯ ПАЯЯ — еще один часто используемый метод с уникальными возможностями. Его можно использовать для пайки стекла, керамики и неметаллических материалов. Например, фотогальванические панели, которые являются неметаллическими, нуждаются в электродах, которые можно прикрепить с помощью этого метода. При ультразвуковой пайке используется нагретое паяльное жало, которое также излучает ультразвуковые колебания. Эти вибрации создают кавитационные пузырьки на границе подложки с расплавленным припоем. Имплозивная энергия кавитации модифицирует оксидную поверхность и удаляет грязь и оксиды. За это время также образуется слой сплава. Припой на склеиваемой поверхности содержит кислород и обеспечивает прочную общую связь между стеклом и припоем. ПАЙКА ПОГРУЖЕНИЕМ может рассматриваться как более простая версия пайки волной припоя, подходящая только для мелкосерийного производства. Первый очищающий флюс применяется, как и в других процессах. Платы с установленными компонентами погружаются вручную или в полуавтоматическом режиме в емкость с расплавленным припоем. Расплавленный припой прилипает к открытым металлическим участкам платы, незащищенным паяльной маской. Оборудование простое и недорогое.
• КЛЕЙНОЕ СОЕДИНЕНИЕ: Это еще один популярный метод, который мы часто используем, и он включает в себя склеивание поверхностей с помощью клея, эпоксидных смол, пластификаторов или других химикатов. Склеивание осуществляется путем испарения растворителя, термоотверждения, отверждения УФ-светом, отверждения под давлением или ожидания в течение определенного времени. В наших производственных линиях используются различные высокоэффективные клеи. При правильно спроектированных процессах нанесения и отверждения клеевое соединение может привести к прочным и надежным соединениям с очень низким напряжением. Адгезионные соединения могут быть хорошими защитниками от факторов окружающей среды, таких как влага, загрязняющие вещества, коррозионные вещества, вибрация и т. д. Преимущества клеевого соединения: они могут применяться к материалам, которые в противном случае было бы трудно паять, сваривать или паять. Также это может быть предпочтительнее для термочувствительных материалов, которые могут быть повреждены при сварке или других высокотемпературных процессах. Другие преимущества клея заключаются в том, что его можно наносить на поверхности неправильной формы и очень незначительно увеличивать вес сборки по сравнению с другими методами. Кроме того, размерные изменения деталей очень минимальны. Некоторые клеи обладают свойствами согласования преломления и могут использоваться между оптическими компонентами без значительного снижения силы света или оптического сигнала. Недостатками, с другой стороны, являются более длительное время отверждения, которое может замедлить производственные линии, требования к креплению, требования к подготовке поверхности и трудности с разборкой, когда требуется доработка. Большинство наших операций по склеиванию состоят из следующих этапов:
-Обработка поверхности: распространены специальные процедуры очистки, такие как очистка деионизированной водой, очистка спиртом, плазменная очистка или очистка коронным разрядом. После очистки мы можем нанести на поверхности усилители адгезии, чтобы обеспечить наилучшее соединение.
- Крепление деталей: как для нанесения клея, так и для отверждения мы разрабатываем и используем специальные приспособления.
- Нанесение клея: мы иногда используем ручные, а иногда, в зависимости от случая, автоматизированные системы, такие как робототехника, серводвигатели, линейные приводы, для доставки клея в нужное место, и мы используем диспенсеры для доставки его в нужном объеме и количестве.
-Отверждение: в зависимости от клея, мы можем использовать простую сушку и отверждение, а также отверждение под воздействием УФ-излучения, которое действует как катализатор, или отверждение при нагревании в печи или с использованием резистивных нагревательных элементов, установленных на приспособлениях и приспособлениях.
Мы рекомендуем вам нажать здесь, чтобыСКАЧАТЬ наши схематические иллюстрации процессов крепления от AGS-TECH Inc.
Это поможет вам лучше понять информацию, которую мы предоставляем вам ниже.
• ПРОЦЕССЫ КРЕПЛЕНИЯ: Наши процессы механического соединения делятся на две категории: КРЕПЕЖНЫЕ СОЕДИНЕНИЯ и ЦЕЛЬНЫЕ СОЕДИНЕНИЯ. Примеры используемых нами крепежных элементов: винты, штифты, гайки, болты, заклепки. Примерами неразъемных соединений, которые мы используем, являются защелки и термоусадки, швы, гофры. Используя различные методы крепления, мы обеспечиваем прочность и надежность наших механических соединений в течение многих лет эксплуатации. ВИНТЫ и БОЛТЫ являются одними из наиболее часто используемых крепежных элементов для скрепления объектов и их позиционирования. Наши винты и болты соответствуют стандартам ASME. Используются различные типы винтов и болтов, включая винты с шестигранной головкой и болты с шестигранной головкой, винты и болты с запаздыванием, двухсторонний винт, дюбельный винт, винт с проушиной, винт для зеркала, винт для листового металла, винт для точной регулировки, самосверлящие и самонарезающие винты. , установочный винт, винты со встроенными шайбами и многое другое. У нас есть различные типы головок винтов, такие как потайная, купольная, круглая, с фланцевой головкой, а также различные типы винтовых приводов, такие как шлицевые, крестообразные, квадратные, шестигранные. RIVET, с другой стороны, представляет собой постоянное механическое крепление, состоящее из гладкого цилиндрического стержня и головки с одной стороны. После вставки другой конец заклепки деформируется, а ее диаметр увеличивается, чтобы она оставалась на месте. Другими словами, до установки заклепка имеет одну головку, а после установки две. Мы устанавливаем различные типы заклепок в зависимости от области применения, прочности, доступности и стоимости, такие как заклепки со сплошной/круглой головкой, конструкционные, полутрубчатые, глухие, оскарные, приводные, заподлицо, фрикционные, самонарезающие заклепки. Клепка может быть предпочтительнее в тех случаях, когда необходимо избежать тепловой деформации и изменения свойств материала из-за тепла сварки. Клепка также предлагает легкий вес и особенно хорошую прочность и устойчивость к сдвиговым усилиям. Однако при растягивающих нагрузках более подходящими могут быть винты, гайки и болты. В процессе CLINCHING мы используем специальные пуансоны и штампы для создания механического сцепления между соединяемыми листовыми металлами. Пуансон проталкивает слои листового металла в полость штампа, что приводит к образованию неразъемного соединения. При клинче не требуется ни нагрева, ни охлаждения, это холодный рабочий процесс. Это экономичный процесс, который в некоторых случаях может заменить точечную сварку. В СОЕДИНЕНИИ мы используем штифты, которые представляют собой элементы машины, используемые для фиксации положения частей машины относительно друг друга. Основные типы: шплинт, шплинт, пружинный штифт, установочный штифт, и шплинт. В СТЕПЛЕНИИ мы используем степлеры и скобы, которые представляют собой двухсторонние застежки, используемые для соединения или связывания материалов. Сшивание скобами имеет следующие преимущества: экономичность, простота и быстрота в использовании, головка скобы может использоваться для соединения материалов, соединенных встык, головка скобы может облегчить соединение куска, такого как кабель, и крепление его к поверхности без прокалывания или повреждения, относительно легкое удаление. ПРЕСС-ФИТИНГ выполняется путем сближения деталей, а трение между ними скрепляет детали. Детали с прессовой посадкой, состоящие из вала увеличенного размера и отверстия меньшего размера, обычно собираются одним из двух способов: либо путем приложения силы, либо с использованием теплового расширения или сжатия деталей. Когда пресс-фитинг устанавливается с усилием, мы используем либо гидравлический пресс, либо ручной пресс. С другой стороны, когда пресс-фитинг устанавливается за счет теплового расширения, мы нагреваем обволакивающие детали и собираем их на место в горячем виде. При охлаждении они сжимаются и возвращаются к своим нормальным размерам. Это приводит к хорошей прессовой посадке. Альтернативно мы называем это ТЕРМОФИТИНГОМ. Другой способ сделать это - охладить детали в оболочке перед сборкой, а затем вставить их в сопрягаемые детали. Когда сборка прогревается, они расширяются, и мы получаем плотную посадку. Этот последний метод может быть предпочтительнее в тех случаях, когда нагрев создает риск изменения свойств материала. Охлаждение в таких случаях более безопасно.
Пневматические и гидравлические компоненты и узлы
• Клапаны, гидравлические и пневматические компоненты, такие как уплотнительное кольцо, шайба, уплотнения, прокладка, кольцо, прокладка.
Поскольку существует большое разнообразие клапанов и пневматических компонентов, мы не можем перечислить здесь все. В зависимости от физической и химической среды вашего применения у нас есть специальные продукты для вас. Пожалуйста, укажите область применения, тип компонента, технические характеристики, условия окружающей среды, такие как давление, температура, жидкости или газы, которые будут контактировать с вашими клапанами и пневматическими компонентами; и мы подберем для вас наиболее подходящий продукт или изготовим его специально для вашего применения.