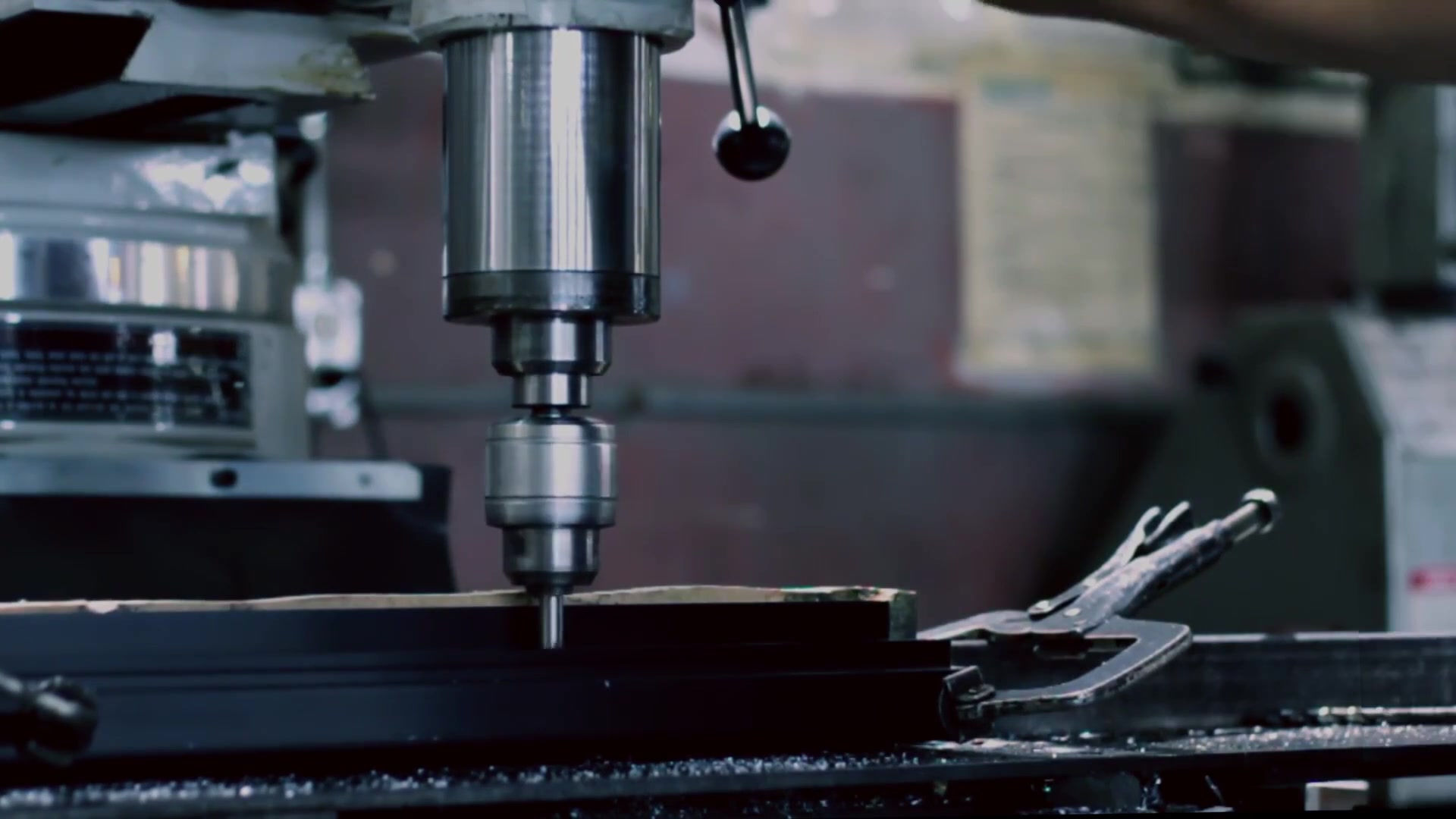
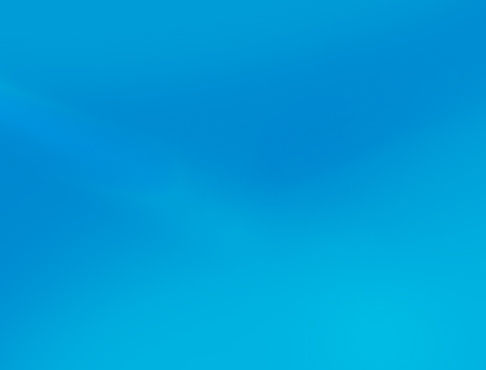
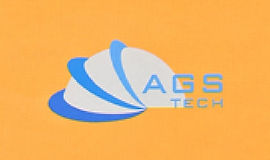
Глобальный производитель на заказ, интегратор, консолидатор, партнер по аутсорсингу широкого спектра продуктов и услуг.
Мы являемся вашим универсальным источником для производства, изготовления, проектирования, консолидации, интеграции, аутсорсинга изготовленных на заказ и готовых продуктов и услуг.
Choose your Language
-
Изготовление на заказ
-
Внутреннее и глобальное контрактное производство
-
Производственный аутсорсинг
-
Внутренние и глобальные закупки
-
Консолидация
-
Инженерная интеграция
-
Инженерные услуги
ЛАЗЕРНАЯ РЕЗКА is a HIGH-ENERGY-BEAM MANUFACTURING технология, в которой обычно используется лазерная резка материалов. В ЛАЗЕРНАЯ ОБРАБОТКА (LBM) лазерный источник фокусирует оптическую энергию на поверхности заготовки. Лазерная резка направляет высокосфокусированный и плотный выход мощного лазера с помощью компьютера на материал, подлежащий резке. Затем целевой материал либо плавится, сгорает, испаряется, либо сдувается струей газа контролируемым образом, оставляя кромку с высококачественной отделкой поверхности. Наши промышленные лазерные станки подходят для резки плоского листового материала, а также конструкционных и трубных материалов, металлических и неметаллических заготовок. Как правило, в процессах лазерной обработки и резки вакуум не требуется. Существует несколько типов лазеров, используемых в лазерной резке и производстве. Импульсный или непрерывный лазер CO2 LASER подходит для резки, сверления и гравировки. The NEODYMIUM (Nd) and neodymium yttrium-aluminum-garnet (Nd-YAG) LASERS are identical по стилю и отличаются только применением. Неодим Nd используется для сверления и там, где требуется высокая энергия, но мало повторений. Лазер Nd-YAG, с другой стороны, используется там, где требуется очень высокая мощность, а также для сверления и гравировки. Для LASER СВАРКИ можно использовать как CO2, так и Nd/Nd-YAG лазеры. Другие лазеры, которые мы используем в производстве, включают Nd:GLASS, RUBY и EXCIMER. В лазерно-лучевой обработке (LBM) важны следующие параметры: отражательная способность и теплопроводность поверхности заготовки, ее удельная теплоемкость и скрытая теплота плавления и испарения. Эффективность процесса лазерной обработки (LBM) увеличивается с уменьшением этих параметров. Глубина резания может быть выражена как:
t~P/(vxd)
Это означает, что глубина резания «t» пропорциональна подводимой мощности P и обратно пропорциональна скорости резания v и диаметру пятна лазерного луча d. Поверхность, полученная с помощью LBM, обычно шероховатая и имеет зону термического влияния.
РЕЗКА И ОБРАБОТКА УГЛЕРОДНЫМ (СО2) ЛАЗЕРОМ: CO2-лазеры с возбуждением постоянным током накачиваются за счет пропускания тока через газовую смесь, тогда как CO2-лазеры с радиочастотным возбуждением используют для возбуждения радиочастотную энергию. Радиочастотный метод является относительно новым и стал более популярным. Конструкции постоянного тока требуют электродов внутри резонатора, и поэтому они могут иметь электродную эрозию и покрытие электродного материала на оптике. Напротив, у ВЧ-резонаторов есть внешние электроды, и поэтому они не подвержены этим проблемам. Мы используем CO2-лазеры для промышленной резки многих материалов, таких как мягкая сталь, алюминий, нержавеющая сталь, титан и пластик.
YAG LASER CUTTING and MACHINING: Мы используем лазеры YAG для резки и разметки металлов и керамики. Лазерный генератор и внешняя оптика требуют охлаждения. Отработанное тепло генерируется и передается хладагентом или непосредственно воздуху. Вода является обычным хладагентом, обычно циркулирующим через чиллер или систему теплопередачи.
ЭКСИМЕРНАЯ ЛАЗЕРНАЯ РЕЗКА И ОБРАБОТКА: Эксимерный лазер представляет собой тип лазера с длиной волны в ультрафиолетовой области. Точная длина волны зависит от используемых молекул. Например, молекулам, указанным в скобках, соответствуют следующие длины волн: 193 нм (ArF), 248 нм (KrF), 308 нм (XeCl), 353 нм (XeF). Некоторые эксимерные лазеры являются перестраиваемыми. Эксимерные лазеры обладают привлекательным свойством, заключающимся в том, что они могут удалять очень тонкие слои поверхностного материала практически без нагрева или перехода к остальной части материала. Поэтому эксимерные лазеры хорошо подходят для прецизионной микрообработки органических материалов, таких как некоторые полимеры и пластмассы.
ГАЗОВАЯ ЛАЗЕРНАЯ РЕЗКА: иногда мы используем лазерные лучи в сочетании с газовым потоком, таким как кислород, азот или аргон, для резки тонких листовых материалов. Это делается с помощью a LASER-BEAM TORCH. Для нержавеющей стали и алюминия мы используем лазерную резку под высоким давлением в среде инертного газа с использованием азота. Это приводит к кромкам без оксидов для улучшения свариваемости. Эти газовые потоки также сдувают расплавленный и испарившийся материал с поверхностей деталей.
В a LASER MICROJET CUTTING у нас есть водоструйный управляемый лазер, в котором импульсный лазерный луч соединяется со струей воды низкого давления. Мы используем его для выполнения лазерной резки, используя водяную струю для направления лазерного луча, подобно оптическому волокну. Преимущества лазерной микроструйной резки заключаются в том, что вода также удаляет мусор и охлаждает материал, это быстрее, чем традиционная «сухая» лазерная резка с более высокой скоростью нарезки, параллельным пропилом и возможностью всенаправленной резки.
Мы применяем различные методы резки с использованием лазеров. Некоторыми из методов являются испарение, плавление и продувка, расплавление продувкой и сжигание, растрескивание под тепловым напряжением, скрайбирование, холодная резка и обжиг, стабилизированная лазерная резка.
- Резка испарением: сфокусированный луч нагревает поверхность материала до точки кипения и создает отверстие. Отверстие приводит к резкому увеличению поглощающей способности и быстрому углублению отверстия. По мере того, как отверстие углубляется и материал закипает, образующийся пар разрушает расплавленные стенки, выдувая материал и еще больше увеличивая отверстие. Этим методом обычно режут неплавкие материалы, такие как дерево, углерод и термореактивные пластмассы.
- Резка расплавом и продувкой: мы используем газ под высоким давлением для выдувания расплавленного материала из зоны резки, что снижает требуемую мощность. Материал нагревается до точки плавления, а затем струя газа выдувает расплавленный материал из пропила. Это устраняет необходимость дальнейшего повышения температуры материала. Мы режем металлы этой техникой.
- Термическое растрескивание: Хрупкие материалы чувствительны к термическому разрушению. Луч фокусируется на поверхности, вызывая локальный нагрев и тепловое расширение. Это приводит к трещине, которую затем можно направить, перемещая луч. Мы используем эту технику в резке стекла.
- Стелс-нарезка кремниевых пластин: отделение микроэлектронных чипов от кремниевых пластин осуществляется с помощью процесса стелс-нарезки с использованием импульсного Nd:YAG-лазера, длина волны 1064 нм хорошо адаптирована к электронной запрещенной зоне кремния (1,11 эВ или 1117 нм). Это популярно в производстве полупроводниковых устройств.
- Реактивная резка: эта техника, также называемая резкой пламенем, похожа на резку кислородной горелкой, но с лазерным лучом в качестве источника воспламенения. Мы используем его для резки углеродистой стали толщиной более 1 мм и даже очень толстых стальных листов с небольшой мощностью лазера.
ИМПУЛЬСНЫЕ ЛАЗЕРЫ обеспечивают мощный выброс энергии в течение короткого периода времени и очень эффективны в некоторых процессах лазерной резки, таких как прошивка, или когда требуются очень маленькие отверстия или очень низкая скорость резки. Если бы вместо этого использовался постоянный лазерный луч, тепло могло бы достичь точки плавления всей обрабатываемой детали. Наши лазеры могут работать в импульсном режиме или резать CW (непрерывную волну) под управлением программы NC (числового управления). Мы используем ДВУХИМПУЛЬСНЫЕ ЛАЗЕРЫ излучающие серию пар импульсов для улучшения скорости съема материала и качества отверстия. Первый импульс удаляет материал с поверхности, а второй импульс предотвращает повторное прилипание выброшенного материала к стенке отверстия или вырезу.
Допуски и чистота поверхности при лазерной резке и механической обработке выдающиеся. Наши современные лазерные резаки имеют точность позиционирования около 10 микрометров и повторяемость 5 микрометров. Стандартная шероховатость Rz увеличивается с толщиной листа, но уменьшается с увеличением мощности лазера и скорости резки. Процессы лазерной резки и механической обработки позволяют добиться жестких допусков, часто с точностью до 0,001 дюйма (0,025 мм). Геометрия деталей и механические характеристики наших станков оптимизированы для достижения наилучших допусков. Чистота поверхности, которую мы можем получить при лазерной резке, может варьироваться от 0,003 мм до 0,006 мм. Как правило, мы легко получаем отверстия диаметром 0,025 мм, а отверстия размером до 0,005 мм и отношением глубины отверстия к диаметру 50:1 были изготовлены из различных материалов. Наши самые простые и самые стандартные станки для лазерной резки режут металл из углеродистой стали толщиной от 0,020–0,5 дюйма (0,51–13 мм) и могут работать в тридцать раз быстрее, чем стандартная резка.
Лазерно-лучевая обработка широко используется для сверления и резки металлов, неметаллов и композиционных материалов. Преимущества лазерной резки по сравнению с механической резкой заключаются в более легком удерживании, чистоте и меньшем загрязнении заготовки (поскольку нет режущей кромки, как при традиционной фрезерной или токарной обработке, которая может загрязняться материалом или загрязнять материал, т.е. налипать). Абразивная природа композиционных материалов может затруднить их обработку обычными методами, но легко с помощью лазерной обработки. Поскольку лазерный луч не изнашивается во время процесса, получаемая точность может быть выше. Поскольку лазерные системы имеют небольшую зону термического воздействия, вероятность деформации разрезаемого материала меньше. Для некоторых материалов лазерная резка может быть единственным вариантом. Процессы лазерной резки являются гибкими, а доставка оптоволоконного луча, простота крепления, короткое время настройки, наличие трехмерных систем ЧПУ позволяют лазерной резке и механической обработке успешно конкурировать с другими процессами изготовления листового металла, такими как штамповка. При этом лазерную технологию иногда можно комбинировать с технологиями механического производства для повышения общей эффективности.
Лазерная резка листового металла имеет преимущества перед плазменной резкой, поскольку она более точна и требует меньше энергии, однако большинство промышленных лазеров не могут резать металл большей толщины, чем плазма. Лазеры, работающие на более высоких мощностях, таких как 6000 Вт, приближаются к плазменным машинам по своей способности прорезать толстые материалы. Однако капитальные затраты на эти лазерные резаки мощностью 6000 Вт намного выше, чем у машин плазменной резки, способных резать толстые материалы, такие как стальной лист.
Существуют также недостатки лазерной резки и механической обработки. Лазерная резка требует больших энергозатрат. Эффективность промышленных лазеров может варьироваться от 5% до 15%. Потребляемая мощность и эффективность любого конкретного лазера будут варьироваться в зависимости от выходной мощности и рабочих параметров. Это будет зависеть от типа лазера и от того, насколько хорошо лазер соответствует выполняемой работе. Мощность лазерной резки, необходимая для конкретной задачи, зависит от типа материала, толщины, используемого процесса (реактивный/инертный) и желаемой скорости резки. Максимальная производительность при лазерной резке и механической обработке ограничена рядом факторов, включая мощность лазера, тип процесса (реактивный или инертный), свойства и толщину материала.
In ЛАЗЕРНАЯ АБЛЯЦИЯ мы удаляем материал с твердой поверхности, облучая ее лазерным лучом. При малом лазерном потоке материал нагревается за счет поглощенной лазерной энергии и испаряется или сублимируется. При высоком лазерном потоке материал обычно превращается в плазму. Лазеры высокой мощности очищают большое пятно одним импульсом. Лазеры меньшей мощности используют множество малых импульсов, которые можно сканировать по площади. При лазерной абляции мы удаляем материал импульсным лазером или лазерным лучом с непрерывной волной, если интенсивность лазера достаточно высока. Импульсные лазеры могут просверливать очень маленькие и глубокие отверстия в очень твердых материалах. Очень короткие лазерные импульсы удаляют материал так быстро, что окружающий материал поглощает очень мало тепла, поэтому лазерное сверление можно выполнять на хрупких или термочувствительных материалах. Энергия лазера может избирательно поглощаться покрытиями, поэтому импульсные лазеры CO2 и Nd:YAG можно использовать для очистки поверхностей, удаления краски и покрытия или подготовки поверхностей к покраске без повреждения основной поверхности.
Мы используем ЛАЗЕРНУЮ ГРАВИРОВКУ и ЛАЗЕРНУЮ МАРКИРОВКУ для гравировки или маркировки объекта.. Эти два метода на самом деле являются наиболее широко используемыми приложениями. При этом не используются чернила и не используются наконечники инструментов, которые соприкасаются с гравируемой поверхностью и изнашиваются, как в случае с традиционными методами механической гравировки и маркировки. Материалы, специально разработанные для лазерной гравировки и маркировки, включают чувствительные к лазерному излучению полимеры и специальные новые металлические сплавы. Хотя оборудование для лазерной маркировки и гравировки относительно дороже по сравнению с такими альтернативами, как штампы, штифты, щупы, штампы для травления и т. д., они стали более популярными благодаря своей точности, воспроизводимости, гибкости, простоте автоматизации и онлайн-применению. в различных производственных условиях.
Наконец, мы используем лазерные лучи для нескольких других производственных операций:
- ЛАЗЕРНАЯ СВАРКА
- ЛАЗЕРНАЯ ТЕРМООБРАБОТКА: Мелкомасштабная термообработка металлов и керамики для изменения механических и трибологических свойств их поверхности.
- ЛАЗЕРНАЯ ОБРАБОТКА ПОВЕРХНОСТИ / МОДИФИКАЦИЯ: Лазеры используются для очистки поверхностей, введения функциональных групп, модификации поверхностей с целью улучшения адгезии перед нанесением покрытия или процессами соединения.