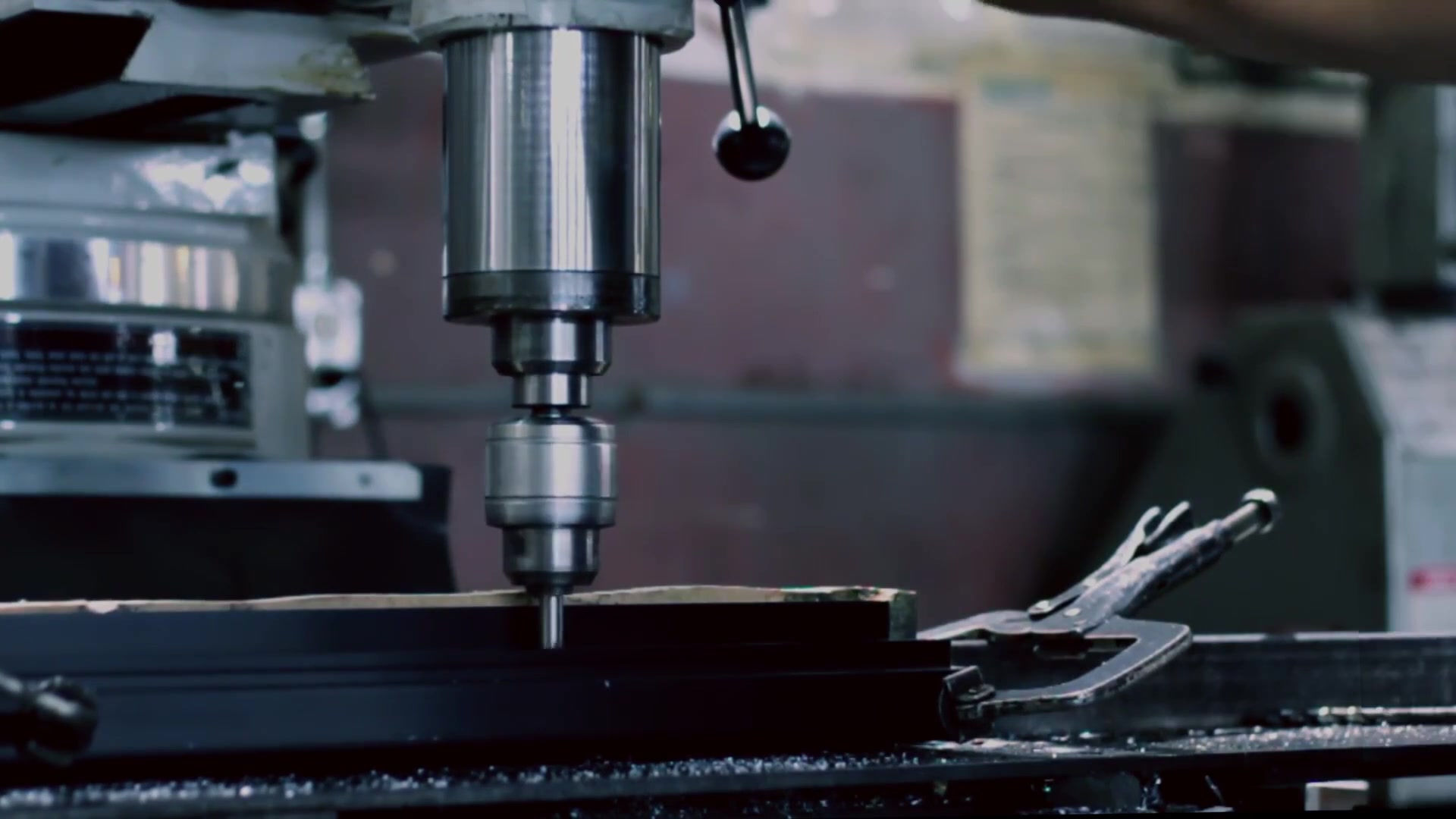
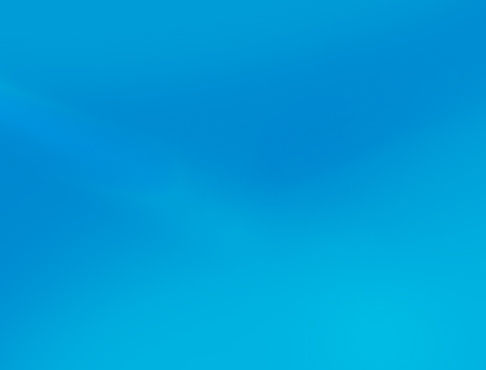
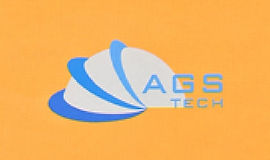
Глобальный производитель на заказ, интегратор, консолидатор, партнер по аутсорсингу широкого спектра продуктов и услуг.
Мы являемся вашим универсальным источником для производства, изготовления, проектирования, консолидации, интеграции, аутсорсинга изготовленных на заказ и готовых продуктов и услуг.
Choose your Language
-
Изготовление на заказ
-
Внутреннее и глобальное контрактное производство
-
Производственный аутсорсинг
-
Внутренние и глобальные закупки
-
Консолидация
-
Инженерная интеграция
-
Инженерные услуги
Search Results
Найден 161 результат с пустым поисковым запросом
- Приборы для механических испытаний - Прибор для испытания на растяжение - Машина для испытания на кручение
Приборы для механических испытаний - Прибор для испытания на растяжение - Машина для испытания на кручение - Прибор для испытания на изгиб - Устройство для испытания на удар - Тестер бетона - Машина для испытания на сжатие Инструменты для механических испытаний Среди большого количества МЕХАНИЧЕСКИЕ ИСПЫТАТЕЛЬНЫЕ ПРИБОРЫ. МЫ фокусируется на наиболее необходимые и популярные: МАШИНЫ ДЛЯ ИСПЫТАНИЙ НА РАСТЯЖЕНИЕ, МАШИНЫ ДЛЯ ИСПЫТАНИЙ НА СЖАТИЕ, ОБОРУДОВАНИЕ ДЛЯ ИСПЫТАНИЙ НА КРУЧЕНИЕ, МАШИНЫ ДЛЯ ИСПЫТАНИЙ НА УСТОЙЧИВОСТЬ, ТЕСТЕРЫ ДЛЯ ТРЕХ И ЧЕТЫРЕХ ТОЧЕЧНЫХ ИЗГИБОВ, ПРИБОРЫ ДЛЯ КОЭФФИЦИЕНТА ТРЕНИЯ, ПРИБОРЫ ТВЕРДОСТИ И ТОЛЩИНЫ, ПРИБОРЫ ДЛЯ ИЗМЕРЕНИЯ ШЕРОВОСТИ ПОВЕРХНОСТИ ПРЕЦИЗИОННЫЕ АНАЛИТИЧЕСКИЕ БАЛАНСЫ. Мы предлагаем нашим клиентам качественные бренды, такие как SADT, SINOAGE for по прейскурантным ценам. Чтобы загрузить каталог нашего метрологического и испытательного оборудования марки SADT, НАЖМИТЕ ЗДЕСЬ. Здесь вы найдете некоторые из этих испытательных устройств, таких как тестеры бетона и тестер шероховатости поверхности. Рассмотрим эти тестовые устройства более подробно: МОЛОТОК ШМИДТА / ИСПЫТАТЕЛЬ БЕТОНА: этот испытательный прибор, также иногда называемый ШВЕЙЦАРНЫМ МОЛОТОКОМ или МОЛОТОКОМ ОТБОЙНОГО, это устройство для измерения упругих свойств или прочности бетона или камня, в основном поверхностной твердости и сопротивления проникновению. Молоток измеряет отскок подпружиненной массы, ударяющейся о поверхность образца. Испытательный молоток ударит по бетону с заданной энергией. Отскок молотка зависит от твердости бетона и измеряется испытательным оборудованием. Взяв за основу диаграмму преобразования, значение отскока можно использовать для определения прочности на сжатие. Молоток Шмидта представляет собой произвольную шкалу от 10 до 100. Молотки Шмидта бывают нескольких различных диапазонов энергии. Их энергетические диапазоны: (i) тип L-энергия удара 0,735 Нм, (ii) тип N-энергия удара 2,207 Нм; и (iii) Энергия удара типа M-29,43 Нм. Локальная изменчивость в образце. Чтобы свести к минимуму локальные вариации в образцах, рекомендуется взять выборку показаний и взять их среднее значение. Перед испытанием молоток Шмидта необходимо откалибровать с помощью калибровочной наковальни, поставляемой производителем. Следует снять 12 показаний, отбрасывая самые высокие и самые низкие, а затем взяв среднее значение из десяти оставшихся показаний. Этот метод считается косвенным измерением прочности материала. Он обеспечивает индикацию, основанную на свойствах поверхности, для сравнения образцов. Этот метод испытаний бетона регулируется ASTM C805. С другой стороны, стандарт ASTM D5873 описывает процедуру испытания породы. В нашем каталоге брендов SADT вы найдете следующие продукты: ЦИФРОВОЙ ИСПЫТАТЕЛЬНЫЙ МОЛОТ ДЛЯ БЕТОНА Модели SADT HT-225D/HT-75D/HT-20D - Модель SADT HT-225D — это интегрированный цифровой молоток для испытания бетона, объединяющий процессор данных и молоток для испытания в единое целое. Он широко используется для неразрушающего контроля качества бетона и строительных материалов. По значению отскока можно автоматически рассчитать прочность бетона на сжатие. Все тестовые данные могут быть сохранены в памяти и переданы на ПК по кабелю USB или по беспроводной сети Bluetooth. Модели HT-225D и HT-75D имеют диапазон измерения 10 – 70 Н/мм2, тогда как модель HT-20D имеет только 1 – 25 Н/мм2. Энергия удара HT-225D составляет 0,225 кгм и подходит для испытаний обычных конструкций зданий и мостов, энергия удара HT-75D составляет 0,075 кгм и подходит для испытаний небольших и чувствительных к ударам деталей из бетона и искусственного кирпича, и, наконец, энергия удара HT-20D составляет 0,020 кг и подходит для испытаний строительных растворов или глиняных изделий. ПРИБОРЫ ДЛЯ ИСПЫТАНИЙ НА УДАР: во время многих производственных операций и в течение срока службы многие компоненты должны подвергаться ударным нагрузкам. При испытании на удар образец с надрезом помещают в прибор для испытания на удар и разбивают качающимся маятником. Существует два основных типа этого теста: ТЕСТ_CC781905-5cde-3194-bb3b-136bad5cf58d_CHARPY TEST и ТЕСТ IZOD. Для испытания по Шарпи образец поддерживается с обоих концов, тогда как для испытания по Изоду они поддерживаются только с одного конца, как консольная балка. Из величины качания маятника получается энергия, рассеиваемая при разрушении образца, эта энергия представляет собой ударную вязкость материала. С помощью ударных испытаний можно определить температуры вязко-хрупкого перехода материалов. Материалы с высокой ударопрочностью обычно обладают высокой прочностью и пластичностью. Эти испытания также выявляют чувствительность ударной вязкости материала к поверхностным дефектам, поскольку надрез на образце можно рассматривать как поверхностный дефект. ТЕСТЕР НА РАСТЯЖЕНИЕ : С помощью этого теста определяются прочностно-деформационные характеристики материалов. Образцы для испытаний готовятся в соответствии со стандартами ASTM. Как правило, испытывают сплошные и круглые образцы, но плоские листы и трубчатые образцы также могут быть испытаны на растяжение. Первоначальная длина образца представляет собой расстояние между калибровочными метками на нем и обычно составляет 50 мм. Обозначается как ло. В зависимости от образцов и продуктов могут использоваться более длинные или более короткие длины. Исходная площадь поперечного сечения обозначается как Ao. Инженерное напряжение, также называемое номинальным напряжением, определяется как: Сигма = P / АО И инженерная деформация определяется как: е = (л – ло) / ло В области линейной упругости образец удлиняется пропорционально нагрузке до пропорционального предела. За пределами этого предела, хотя и нелинейно, образец будет продолжать упруго деформироваться до предела текучести Y. В этой упругой области материал вернется к своей первоначальной длине, если мы удалим нагрузку. Закон Гука применяется в этой области и дает нам модуль Юнга: E = сигма / е Если мы увеличим нагрузку и выйдем за точку текучести Y, материал начнет поддаваться. Другими словами, образец начинает испытывать пластическую деформацию. Пластическая деформация означает остаточную деформацию. Площадь поперечного сечения образца постоянно и равномерно уменьшается. Если образец в этой точке не нагружен, кривая идет по прямой вниз и параллельно исходной линии в упругой области. При дальнейшем увеличении нагрузки кривая достигает максимума и начинает уменьшаться. Точка максимального напряжения называется пределом прочности при растяжении или пределом прочности при растяжении и обозначается как UTS. UTS можно интерпретировать как общую прочность материалов. Когда нагрузка превышает UTS, на образце возникает шейка, и удлинение между калибровочными метками становится неравномерным. Другими словами, образец становится действительно тонким в месте образования шейки. При образовании шейки упругие напряжения падают. Если испытание продолжается, инженерное напряжение падает еще больше, и образец разрушается в области сужения. Уровень напряжения при разрушении – это напряжение разрушения. Деформация в точке разрушения является показателем пластичности. Деформация до UTS называется равномерной деформацией, а удлинение при разрыве — полным удлинением. Удлинение = ((lf – lo) / lo) x 100 Уменьшение площади = ((Ao – Af) / Ao) x 100 Удлинение и уменьшение площади являются хорошими показателями пластичности. МАШИНА ДЛЯ ИСПЫТАНИЙ НА СЖАТИЕ (ТЕСТЕР НА СЖАТИЕ) : В этом испытании образец подвергается сжимающей нагрузке, в отличие от испытания на растяжение, где нагрузка является растягивающей. Как правило, твердый цилиндрический образец помещают между двумя плоскими пластинами и сжимают. Использование смазочных материалов на контактных поверхностях предотвращает явление, известное как бочкообразность. Скорость инженерной деформации при сжатии определяется по формуле: de / dt = - v / ho, где v - скорость штампа, ho исходная высота образца. С другой стороны, истинная скорость деформации составляет: de = dt = - v/h, где h — мгновенная высота образца. Чтобы поддерживать постоянную истинную скорость деформации во время испытания, кулачковый пластометр за счет кулачкового действия уменьшает величину v пропорционально уменьшению высоты образца h во время испытания. При испытании на сжатие пластичность материалов определяют по трещинам, образовавшимся на бочкообразных цилиндрических поверхностях. Другим испытанием с некоторыми различиями в геометрии штампа и заготовки является ИСПЫТАНИЕ НА СЖАТИЕ НА ПЛОСКОСТНУЮ ДЕФЕКЦИЮ, которое дает нам предел текучести материала при плоской деформации, широко обозначаемый как Y'. Предел текучести материалов при плоской деформации можно оценить как: Y' = 1,15 Y МАШИНЫ ДЛЯ ИСПЫТАНИЙ НА КРУЖЕНИЕ (ТЕСТЕРЫ НА КРУЖЕНИЕ) : The TEST_TORSION это еще один широко используемый метод определения свойств материала. В этом испытании используется трубчатый образец с уменьшенным средним сечением. Напряжение сдвига, T определяется по формуле: T = T / 2 (Pi) (квадрат r) t Здесь T — приложенный крутящий момент, r — средний радиус, t — толщина суженного участка в середине трубы. Деформация сдвига, с другой стороны, определяется выражением: ß = r Ø / л Здесь l — длина приведенного участка, а Ø — угол закручивания в радианах. В диапазоне упругости модуль сдвига (модуль жесткости) выражается как: G = T / ß Связь между модулем сдвига и модулем упругости: G = E / 2( 1 + V ) Испытание на кручение применяется к сплошным круглым стержням при повышенных температурах для оценки способности металлов к ковке. Чем больше скручиваний материал может выдержать до разрушения, тем более он поддается ковке. ТРЕХ И ЧЕТЫРЕХТОЧЕЧНЫЕ ИСПЫТАНИЯ НА ИЗГИБ: для хрупких материалов используйте ИСПЫТАНИЕ НА ИЗГИБ (также называемое ИСПЫТАНИЕ НА ИЗГИБ) подходит. Образец прямоугольной формы поддерживается с обоих концов, и нагрузка прикладывается вертикально. Вертикальная сила прикладывается либо в одной точке, как в случае трехточечной машины для испытаний на изгиб, либо в двух точках, как в случае четырехточечной испытательной машины. Напряжение при разрушении при изгибе называется модулем прочности на разрыв или поперечной прочностью на разрыв. Это дается как: Сигма = М с / I Здесь М — изгибающий момент, с — половина глубины образца, а I — момент инерции поперечного сечения. Величина напряжения одинакова как при трехточечном, так и при четырехточечном изгибе, когда все остальные параметры остаются постоянными. Четырехточечное испытание, вероятно, приведет к более низкому модулю разрыва по сравнению с трехточечным испытанием. Другое преимущество теста на изгиб в четырех точках по сравнению с тестом на изгиб в трех точках заключается в том, что его результаты более согласуются с меньшим статистическим разбросом значений. МАШИНА ДЛЯ ИСПЫТАНИЙ НА УСТОЙЧИВОСТЬ: В ИСПЫТАНИЯ НА УСТОЙЧИВОСТЬ образец многократно подвергается различным состояниям напряжения. Напряжения, как правило, представляют собой комбинацию растяжения, сжатия и кручения. Процесс испытания можно сравнить с изгибом куска проволоки попеременно то в одну, то в другую сторону, пока он не сломается. Амплитуда напряжения может варьироваться и обозначается буквой «S». Число циклов, вызывающих полное разрушение образца, записывается и обозначается как «N». Амплитуда напряжения – это максимальное значение напряжения при растяжении и сжатии, которому подвергается образец. Один вариант испытания на усталость проводится на вращающемся валу с постоянной направленной вниз нагрузкой. Предел выносливости (предел усталости) определяется как макс. значение напряжения, которое материал может выдержать без усталостного разрушения независимо от количества циклов. Усталостная прочность металлов связана с их пределом прочности при растяжении UTS. ТЕСТЕР КОЭФФИЦИЕНТА ТРЕНИЯ : Это испытательное оборудование измеряет легкость, с которой две соприкасающиеся поверхности могут скользить относительно друг друга. Есть два разных значения, связанных с коэффициентом трения, а именно статический и кинетический коэффициент трения. Статическое трение применяется к силе, необходимой для инициализации движения между двумя поверхностями, а кинетическое трение представляет собой сопротивление скольжению, когда поверхности находятся в относительном движении. Перед испытанием и во время испытания необходимо принять соответствующие меры для обеспечения отсутствия грязи, жира и других загрязняющих веществ, которые могут неблагоприятно повлиять на результаты испытаний. ASTM D1894 является основным стандартом испытаний коэффициента трения и используется во многих отраслях промышленности с различными приложениями и продуктами. Мы здесь, чтобы предложить вам наиболее подходящее испытательное оборудование. Если вам нужна индивидуальная установка, специально разработанная для вашего приложения, мы можем соответствующим образом модифицировать существующее оборудование, чтобы оно соответствовало вашим требованиям и потребностям. ТВЕРДОМЕРЫ : Пожалуйста, перейдите на нашу соответствующую страницу, нажав здесь ПРИБОРЫ ТОЛЩИНЫ : Пожалуйста, перейдите на нашу соответствующую страницу, нажав здесь ПРИБОРЫ ШЕРОХОВАТОСТИ ПОВЕРХНОСТИ : Пожалуйста, перейдите на нашу соответствующую страницу, нажав здесь ИЗМЕРИТЕЛЬ ВИБРАЦИИ : Пожалуйста, перейдите на нашу соответствующую страницу, нажав здесь ТАХОМЕТРЫ : Пожалуйста, перейдите на нашу соответствующую страницу, нажав здесь Для получения подробной информации и другого аналогичного оборудования посетите наш веб-сайт: http://www.sourceindustrialsupply.com CLICK Product Finder-Locator Service ПРЕДЫДУЩАЯ СТРАНИЦА
- Обработка и модификация поверхности - Инженерия поверхности - Упрочнение
Обработка и модификация поверхности - Инженерия поверхности - Закалка - Плазма - Лазер - Ионная имплантация - Электронно-лучевая обработка Обработка поверхности и модификация Поверхности покрывают все. Привлекательность и функции материалов, которые обеспечивают нам поверхности, имеют первостепенное значение. Therefore SURFACE TREATMENT and SURFACE MODIFICATION are among our everyday industrial operations. Обработка и модификация поверхности приводят к улучшению свойств поверхности и могут выполняться либо в качестве окончательной отделки, либо перед нанесением покрытия или соединением. , адаптировать поверхности материалов и изделий к: - Контролировать трение и износ - Улучшить коррозионную стойкость - Улучшить адгезию последующих покрытий или соединяемых деталей - Изменение физических свойств проводимости, удельного сопротивления, поверхностной энергии и отражения - Изменять химические свойства поверхностей путем введения функциональных групп - Изменить размеры - Изменение внешнего вида, например, цвета, шероховатости и т. д. - Очистите и/или продезинфицируйте поверхности Используя обработку и модификацию поверхности, можно улучшить функции и срок службы материалов. Наши общие методы обработки и модификации поверхности можно разделить на две основные категории: Обработка поверхности и модификация, которая охватывает поверхности: Органические покрытия: органические покрытия наносят краски, цементы, ламинаты, плавленые порошки и смазки на поверхности материалов. Неорганические покрытия: Нашими популярными неорганическими покрытиями являются гальваническое покрытие, автокаталитическое покрытие (химическое покрытие), конверсионные покрытия, термическое напыление, горячее погружение, наплавка, плавление в печи, тонкопленочные покрытия, такие как SiO2, SiN на металле, стекле, керамике и т. д. Обработка поверхности и модификация с использованием покрытий подробно описаны в соответствующем подменю.нажмите здесь Функциональные покрытия / Декоративные покрытия / Тонкая пленка / Толстая пленка Поверхностная обработка и модификация, которые изменяют поверхности: здесь, на этой странице, мы сконцентрируемся на них. Не все методы обработки и модификации поверхности, которые мы описываем ниже, относятся к микро- или наномасштабу, но мы, тем не менее, кратко упомянем о них, поскольку основные цели и методы в значительной степени аналогичны тем, которые используются в микропроизводственном масштабе. Закалка: Селективная поверхностная закалка лазером, пламенем, индукцией и электронным лучом. Высокоэнергетические процедуры: некоторые из наших высокоэнергетических процедур включают ионную имплантацию, лазерное остекление и плавление, а также обработку электронным лучом. Обработка тонкой диффузией: Процессы тонкой диффузии включают ферритно-нитроцементацию, борирование и другие высокотемпературные реакционные процессы, такие как TiC, VC. Тяжелая диффузионная обработка: наши тяжелые диффузионные процессы включают науглероживание, азотирование и карбонитрирование. Специальная обработка поверхности: Специальная обработка, такая как криогенная, магнитная и звуковая обработка, влияет как на поверхности, так и на сыпучие материалы. Процессы селективной закалки могут осуществляться пламенным, индукционным, электронным лучом, лазерным лучом. Большие подложки подвергаются глубокой закалке с использованием закалки пламенем. Индукционная закалка, с другой стороны, используется для мелких деталей. Лазерное и электронно-лучевое упрочнение иногда не отличаются от упрочнения при наплавке или высокоэнергетической обработке. Эти процессы обработки и модификации поверхности применимы только к сталям, которые имеют достаточное содержание углерода и легирующих элементов, чтобы сделать возможной закалку. Чугуны, углеродистые стали, инструментальные стали и легированные стали подходят для этого метода обработки и модификации поверхности. Эти упрочняющие обработки поверхности существенно не изменяют размеры деталей. Глубина упрочнения может варьироваться от 250 мкм до всей глубины сечения. Однако в случае всего сечения сечение должно быть тонким, менее 25 мм (1 дюйм) или малым, поскольку процессы закалки требуют быстрого охлаждения материалов, иногда в течение секунды. Этого трудно добиться в больших заготовках, и поэтому в больших сечениях закаливать можно только поверхности. В качестве популярного процесса обработки и модификации поверхности мы упрочняем пружины, лезвия ножей и хирургические лезвия, а также многие другие продукты. Высокоэнергетические процессы являются относительно новыми методами обработки и модификации поверхности. Свойства поверхностей изменяются без изменения размеров. Нашими популярными высокоэнергетическими процессами обработки поверхности являются обработка электронным лучом, ионная имплантация и обработка лазерным лучом. Электронно-лучевая обработка: Электронно-лучевая обработка поверхности изменяет свойства поверхности за счет быстрого нагрева и быстрого охлаждения — порядка 10Exp6 по Цельсию/сек (10exp6 по Фаренгейту/сек) в очень мелкой области около 100 микрон вблизи поверхности материала. Электронно-лучевая обработка также может использоваться при наплавке для получения поверхностных сплавов. Ионная имплантация: в этом методе обработки и модификации поверхности используется электронный луч или плазма для преобразования атомов газа в ионы с достаточной энергией и имплантации/вставки ионов в атомную решетку подложки, ускоренных магнитными катушками в вакуумной камере. Вакуум облегчает свободное перемещение ионов в камере. Несоответствие между имплантированными ионами и поверхностью металла создает атомарные дефекты, которые упрочняют поверхность. Обработка лазерным лучом: Подобно обработке и модификации поверхности электронным лучом, обработка лазерным лучом изменяет свойства поверхности путем быстрого нагрева и быстрого охлаждения в очень мелкой области вблизи поверхности. Этот метод обработки и модификации поверхности также можно использовать при наплавке для получения поверхностных сплавов. Ноу-хау в области дозирования имплантатов и параметров обработки позволяет нам использовать эти высокоэнергетические методы обработки поверхности на наших производственных предприятиях. Тонкая диффузионная обработка поверхности: Ферритная нитроцементация — это процесс цементации, при котором азот и углерод проникают в черные металлы при докритических температурах. Температура обработки обычно составляет 565 градусов по Цельсию (1049 по Фаренгейту). При этой температуре стали и другие сплавы железа все еще находятся в ферритной фазе, что выгодно по сравнению с другими процессами цементации, происходящими в аустенитной фазе. Процесс используется для улучшения: • устойчивость к истиранию •усталостные свойства •устойчивость к коррозии Благодаря низким температурам обработки в процессе закалки происходит очень небольшое искажение формы. Борирование - это процесс, при котором бор вводится в металл или сплав. Это процесс поверхностного упрочнения и модификации, при котором атомы бора диффундируют в поверхность металлического компонента. В результате поверхность содержит бориды металлов, такие как бориды железа и бориды никеля. В чистом виде эти бориды обладают чрезвычайно высокой твердостью и износостойкостью. Детали из борированного металла обладают чрезвычайной износостойкостью и часто служат в пять раз дольше, чем детали, прошедшие традиционную термическую обработку, такую как закалка, науглероживание, азотирование, нитроцементация или индукционная закалка. Тяжелая диффузионная обработка поверхности и модификация: если содержание углерода низкое (например, менее 0,25%), мы можем увеличить содержание углерода в поверхности для упрочнения. Деталь может быть либо термообработана путем закалки в жидкости, либо охлаждена на воздухе в зависимости от желаемых свойств. Этот метод допускает локальное упрочнение только на поверхности, но не в сердцевине. Иногда это очень желательно, потому что это позволяет получить твердую поверхность с хорошими свойствами износа, как у зубчатых колес, но имеет прочный внутренний сердечник, который хорошо работает при ударных нагрузках. В одном из методов обработки и модификации поверхности, а именно цементации, мы добавляем углерод к поверхности. Мы подвергаем деталь воздействию богатой углеродом атмосферы при повышенной температуре и позволяем диффузии перенести атомы углерода в сталь. Диффузия будет происходить только в том случае, если сталь имеет низкое содержание углерода, потому что диффузия работает по принципу перепада концентраций. Науглероживание в пакете: Детали упаковываются в среду с высоким содержанием углерода, такую как угольный порошок, и нагреваются в печи в течение от 12 до 72 часов при температуре 900 градусов по Цельсию (1652 по Фаренгейту). При этих температурах выделяется газ CO, который является сильным восстановителем. Реакция восстановления происходит на поверхности стали с выделением углерода. Затем углерод диффундирует на поверхность благодаря высокой температуре. Углерод на поверхности составляет от 0,7% до 1,2% в зависимости от условий процесса. Достигаемая твердость составляет 60 - 65 RC. Глубина науглероженного корпуса колеблется от 0,1 мм до 1,5 мм. Пакетное науглероживание требует хорошего контроля однородности температуры и постоянства при нагреве. Газовое науглероживание: В этом варианте обработки поверхности газ окись углерода (CO) подается в нагретую печь, и на поверхности деталей происходит восстановительная реакция осаждения углерода. Этот процесс решает большинство проблем науглероживания набивки. Однако одной из проблем является безопасное удержание газа CO. Жидкая цементация: стальные детали погружаются в ванну с расплавленным углеродом. Азотирование — это процесс обработки и модификации поверхности, включающий диффузию азота в поверхность стали. Азот образует нитриды с такими элементами, как алюминий, хром и молибден. Детали проходят термообработку и отпуск перед азотированием. Затем детали очищают и нагревают в печи в атмосфере диссоциированного аммиака (содержащего N и H) в течение 10-40 часов при температуре 500-625 градусов Цельсия (932-1157 градусов по Фаренгейту). Азот диффундирует в сталь и образует нитридные сплавы. Он проникает на глубину до 0,65 мм. Корпус очень жесткий и искажения низкие. Поскольку корпус тонкий, шлифовка поверхности не рекомендуется, и поэтому обработка поверхности азотированием может не подойти для поверхностей с очень гладкими требованиями к отделке. Процесс карбонитрации и модификации поверхности наиболее подходит для низкоуглеродистых легированных сталей. В процессе карбонитрации и углерод, и азот диффундируют на поверхность. Детали нагреваются в атмосфере углеводорода (такого как метан или пропан), смешанного с аммиаком (NH3). Проще говоря, процесс представляет собой смесь науглероживания и азотирования. Обработка поверхности карбонитрированием выполняется при температуре 760 - 870 градусов по Цельсию (1400 - 1598 по Фаренгейту), затем она закаливается в атмосфере природного газа (бескислородной). Процесс карбонитрации не подходит для высокоточных деталей из-за присущих ему искажений. Достигаемая твердость аналогична науглероживанию (60 - 65 RC), но не так высока, как азотирование (70 RC). Глубина корпуса составляет от 0,1 до 0,75 мм. Корпус богат нитридами, а также мартенситом. Последующий отпуск необходим для уменьшения хрупкости. Процессы специальной обработки и модификации поверхности находятся на ранних стадиях разработки, и их эффективность еще не доказана. Они есть: Криогенная обработка: обычно применяется к закаленным сталям, медленно охлаждает подложку примерно до -166 градусов по Цельсию (-300 по Фаренгейту), чтобы увеличить плотность материала и, таким образом, повысить износостойкость и стабильность размеров. Вибрационная обработка: предназначены для снятия термического напряжения, возникающего при термической обработке, за счет вибрации и увеличения срока службы. Магнитная обработка: они предназначены для изменения состава атомов в материалах с помощью магнитных полей и, как мы надеемся, увеличивают срок службы. Эффективность этих специальных методов обработки и модификации поверхности еще предстоит доказать. Кроме того, эти три описанных выше метода воздействуют не только на поверхности, но и на сыпучий материал. CLICK Product Finder-Locator Service ПРЕДЫДУЩАЯ СТРАНИЦА
- Системы и Компоненты Камеры, Оптический Сканер, Оптические Считыватели, ПЗС-матрица
Системы камер - Компоненты - Оптический сканер - Оптические считыватели - Система формирования изображений - CCD - Оптомеханические системы - ИК-камеры Производство и сборка систем камер по индивидуальному заказу АГС-ТЕХ предлагает: • Системы камер, компоненты камер и нестандартные сборки камер. • Специально разработанные и изготовленные оптические сканеры, считыватели, комплекты оптических средств защиты. • Прецизионные оптические, оптико-механические и электрооптические сборки, объединяющие формирующую и неизображающую оптику, светодиодное освещение, волоконную оптику и ПЗС-камеры. • Наши инженеры-оптики разработали следующие продукты: - Всенаправленный перископ и камера для приложений наблюдения и безопасности. Изображение высокого разрешения с полем зрения 360 x 60º, сшивание не требуется. - Широкоугольная видеокамера внутренней полости - Сверхтонкий гибкий видеоэндоскоп диаметром 0,6 мм. Все медицинские видеоконнекторы надеваются на стандартные окуляры эндоскопов, полностью герметичны и водонепроницаемы. Чтобы узнать о наших медицинских эндоскопах и системах камер, посетите: http://www.agsmedical.com - Видеокамера и соединитель для полужесткого эндоскопа - Видеозонд Eye-Q. Бесконтактный зум-видеодатчик для координатно-измерительных машин. - Система оптического спектрографа и инфракрасного изображения (OSIRIS) для спутника ODIN. Наши инженеры работали над сборкой, регулировкой, интеграцией и испытаниями летательного аппарата. - Интерферометр визуализации ветра (WINDII) для спутника НАСА для исследования верхних слоев атмосферы (UARS). Наши инженеры работали над консультированием по сборке, интеграции и тестированию. Производительность и срок службы WINDII намного превышают проектные цели и требования. В зависимости от вашего приложения мы определим, какие размеры, количество пикселей, разрешение, чувствительность к длине волны требуются вашему приложению камеры. Мы можем построить для вас системы, подходящие для инфракрасного, видимого и других длин волн. Свяжитесь с нами сегодня, чтобы узнать больше. Загрузите брошюру для нашего ДИЗАЙН-ПАРТНЕРСКАЯ ПРОГРАММА Также обязательно загрузите наш полный каталог электрических и электронных компонентов для готовой продукции, щелкнув ЗДЕСЬ. CLICK Product Finder-Locator Service ПРЕДЫДУЩАЯ СТРАНИЦА
- Производство микроэлектроники, производство полупроводников, литейное производство, интегральные схемы
Производство микроэлектроники, производство полупроводников - Литейное производство - Программируемые вентильные матрицы - Сборка интегральных схем Упаковка Производство и производство микроэлектроники и полупроводников Многие из наших методов и процессов нанопроизводства, микропроизводства и мезопроизводства, описанные в других меню, могут быть использованы для ПРОИЗВОДСТВО МИКРОЭЛЕКТРОНИКИ тоже. Однако из-за важности микроэлектроники в наших продуктах мы сосредоточимся здесь на конкретном применении этих процессов. Процессы, связанные с микроэлектроникой, также широко называются как Процессы ПРОИЗВОДСТВА ПОЛУПРОВОДНИКОВ. Наши услуги по проектированию и производству полупроводников включают в себя: - Проектирование, разработка и программирование платы FPGA - Литейные услуги Microelectronics: проектирование, прототипирование и производство, сторонние услуги - Подготовка полупроводниковых пластин: нарезка кубиками, обратная шлифовка, истончение, размещение сетки, сортировка штампов, выбор и размещение, проверка - Микроэлектронный дизайн и производство: как стандартные, так и индивидуальные дизайн и производство - Сборка, упаковка и испытания полупроводниковых интегральных схем: штамповка, соединение проводов и микросхем, герметизация, сборка, маркировка и брендирование - Выводные рамки для полупроводниковых приборов: стандартные и индивидуальные разработки и изготовление - Проектирование и производство радиаторов для микроэлектроники: как готовые, так и индивидуальные разработки и изготовление - Датчик и исполнительный механизм: дизайн и изготовление как в готовом виде, так и по индивидуальному заказу - Проектирование и изготовление оптоэлектронных и фотонных схем Давайте более подробно рассмотрим технологии производства и тестирования микроэлектроники и полупроводников, чтобы вы могли лучше понять услуги и продукты, которые мы предлагаем. Проектирование, разработка и программирование плат FPGA. Программируемые вентильные матрицы (FPGA) представляют собой перепрограммируемые кремниевые микросхемы. В отличие от процессоров, которые вы найдете в персональных компьютерах, программирование FPGA переделывает сам чип для реализации пользовательских функций, а не для запуска программного приложения. Используя готовые логические блоки и программируемые ресурсы маршрутизации, микросхемы FPGA можно настроить для реализации пользовательских аппаратных функций без использования макетной платы и паяльника. Задачи цифровых вычислений выполняются в программном обеспечении и компилируются в файл конфигурации или битовый поток, который содержит информацию о том, как компоненты должны быть соединены вместе. FPGA можно использовать для реализации любой логической функции, которую может выполнять ASIC, и они полностью реконфигурируются, и им можно придать совершенно другую «личность» путем перекомпиляции другой конфигурации схемы. ПЛИС сочетают в себе лучшие черты специализированных интегральных схем (ASIC) и систем на базе процессоров. Эти преимущества включают следующее: • Более быстрое время отклика ввода-вывода и специальные функции • Превышение вычислительной мощности цифровых сигнальных процессоров (DSP) • Быстрое прототипирование и проверка без процесса изготовления специализированных ASIC. • Внедрение пользовательских функций с надежностью специализированного детерминированного оборудования. • Возможность модернизации на месте, исключающая затраты на перепроектирование и техническое обслуживание специализированных ASIC. FPGA обеспечивают скорость и надежность, не требуя больших объемов, чтобы оправдать большие авансовые расходы на разработку специализированной ASIC. Перепрограммируемый кремний также обладает такой же гибкостью программного обеспечения, работающего в системах на основе процессоров, и не ограничен количеством доступных процессорных ядер. В отличие от процессоров, ПЛИС по своей природе действительно параллельны, поэтому различные операции обработки не должны конкурировать за одни и те же ресурсы. Каждая независимая задача обработки назначается выделенному разделу микросхемы и может работать автономно без какого-либо влияния со стороны других логических блоков. В результате производительность одной части приложения не снижается при добавлении дополнительной обработки. Некоторые FPGA имеют аналоговые функции в дополнение к цифровым функциям. Некоторыми общими аналоговыми функциями являются программируемая скорость нарастания и сила возбуждения на каждом выходном контакте, что позволяет инженеру устанавливать медленные скорости на слабо нагруженных контактах, которые в противном случае вызывали бы неприемлемое колебание или соединение, и устанавливать более высокие и более высокие скорости на сильно нагруженных контактах на высокоскоростных. каналы, которые в противном случае работали бы слишком медленно. Другой относительно распространенной аналоговой функцией являются дифференциальные компараторы на входных контактах, предназначенные для подключения к дифференциальным каналам передачи сигналов. Некоторые ПЛИС со смешанными сигналами имеют встроенные периферийные аналого-цифровые преобразователи (АЦП) и цифро-аналоговые преобразователи (ЦАП) с блоками преобразования аналоговых сигналов, которые позволяют им работать как система на кристалле. Вкратце, 5 основных преимуществ микросхем FPGA: 1. Хорошая производительность 2. Короткое время выхода на рынок 3. Низкая стоимость 4. Высокая надежность 5. Возможность долгосрочного обслуживания Хорошая производительность. Благодаря возможности параллельной обработки FPGA обладают большей вычислительной мощностью, чем цифровые сигнальные процессоры (DSP), и не требуют последовательного выполнения, как DSP, и могут выполнять больше за такт. Управление входами и выходами (I/O) на аппаратном уровне обеспечивает более быстрое время отклика и специализированную функциональность, полностью соответствующую требованиям приложения. Короткий срок выхода на рынок — ПЛИС обеспечивают гибкость и возможности быстрого прототипирования, что сокращает время выхода на рынок. Наши клиенты могут протестировать идею или концепцию и проверить ее на аппаратном уровне, не прибегая к длительному и дорогостоящему процессу изготовления индивидуальной конструкции ASIC. Мы можем внедрять постепенные изменения и итерации проекта FPGA в течение нескольких часов, а не недель. Также доступно готовое коммерческое оборудование с различными типами ввода-вывода, уже подключенными к программируемой пользователем микросхеме FPGA. Растущая доступность программных инструментов высокого уровня предлагает ценные IP-ядра (предварительно встроенные функции) для расширенного управления и обработки сигналов. Низкая стоимость. Единовременные затраты на проектирование (NRE) индивидуальных конструкций ASIC превышают расходы на аппаратные решения на основе FPGA. Крупные первоначальные инвестиции в ASIC могут быть оправданы для OEM-производителей, производящих много микросхем в год, однако многим конечным пользователям требуются специальные аппаратные функции для многих разрабатываемых систем. Наша программируемая кремниевая ПЛИС предлагает вам что-то без затрат на производство или длительных сроков сборки. Системные требования часто меняются со временем, а стоимость внесения дополнительных изменений в конструкции FPGA незначительна по сравнению с большими затратами на повторное вращение ASIC. Высокая надежность. Программные инструменты обеспечивают среду программирования, а схема FPGA является реальной реализацией выполнения программы. Системы на основе процессоров обычно включают несколько уровней абстракции, чтобы помочь планировать задачи и совместно использовать ресурсы между несколькими процессами. Уровень драйвера управляет аппаратными ресурсами, а ОС управляет памятью и пропускной способностью процессора. Для любого заданного процессорного ядра одновременно может выполняться только одна инструкция, а процессорные системы постоянно подвержены риску того, что срочные задачи будут вытеснять друг друга. FPGA, не использующие ОС, создают минимальные проблемы с надежностью из-за их истинного параллельного выполнения и детерминированного оборудования, предназначенного для каждой задачи. Возможность долгосрочного обслуживания. Микросхемы FPGA можно модернизировать в полевых условиях, и они не требуют времени и затрат, связанных с перепроектированием ASIC. Например, протоколы цифровой связи имеют спецификации, которые могут меняться со временем, а интерфейсы на основе ASIC могут вызывать проблемы с обслуживанием и совместимостью с последующими версиями. Напротив, реконфигурируемые микросхемы FPGA могут соответствовать потенциально необходимым будущим модификациям. По мере развития продуктов и систем наши клиенты могут вносить функциональные улучшения, не тратя время на перепроектирование оборудования и изменение компоновки плат. Услуги литейного производства микроэлектроники: Наши услуги литейного производства микроэлектроники включают в себя проектирование, прототипирование и производство, а также услуги третьих сторон. Мы оказываем помощь нашим клиентам на протяжении всего цикла разработки продукта — от поддержки проектирования до прототипирования и поддержки производства полупроводниковых микросхем. Наша цель в сфере услуг по поддержке проектирования состоит в том, чтобы впервые предложить правильный подход к цифровым, аналоговым и смешанным схемам полупроводниковых устройств. Например, доступны специальные инструменты моделирования MEMS. К вашим услугам фабрики, способные работать с 6- и 8-дюймовыми пластинами для интегрированных КМОП и МЭМС. Мы предлагаем нашим клиентам поддержку проектирования для всех основных платформ автоматизации электронного проектирования (EDA), поставляя правильные модели, комплекты проектирования процессов (PDK), аналоговые и цифровые библиотеки, а также поддержку проектирования для производства (DFM). Мы предлагаем два варианта прототипирования для всех технологий: сервис Multi Product Wafer (MPW), при котором несколько устройств обрабатываются параллельно на одной пластине, и сервис Multi Level Mask (MLM) с четырьмя уровнями маски, нарисованными на одной сетке. Они более экономичны, чем полный набор масок. Услуга MLM очень гибкая по сравнению с фиксированными датами услуги MPW. Компании могут предпочесть аутсорсинг полупроводниковых продуктов литейному заводу микроэлектроники по ряду причин, включая потребность во втором источнике, использование внутренних ресурсов для других продуктов и услуг, готовность отказаться от фабрики и снизить риск и нагрузку, связанные с управлением полупроводниковым заводом… и т. д. AGS-TECH предлагает процессы производства микроэлектроники на открытой платформе, которые можно уменьшить для небольших тиражей пластин, а также для массового производства. При определенных обстоятельствах ваши существующие инструменты для производства микроэлектроники или МЭМС или полные наборы инструментов могут быть переданы в качестве консигнационных инструментов или проданных инструментов с вашего завода на нашу фабрику, или ваши существующие продукты для микроэлектроники и МЭМС могут быть переработаны с использованием технологических процессов на открытой платформе и перенесены на процесс, доступный на нашем заводе. Это быстрее и экономичнее, чем заказная передача технологии. Однако, при желании, существующие процессы производства микроэлектроники/МЭМС заказчика могут быть перенесены. Подготовка полупроводниковых пластин: По желанию клиентов после микрообработки пластин мы выполняем нарезку кубиками, обратную шлифовку, истончение, размещение сетки, сортировку штампов, захват и размещение, операции проверки полупроводниковых пластин. Обработка полупроводниковых пластин включает в себя метрологию между различными этапами обработки. Например, методы испытаний тонких пленок, основанные на эллипсометрии или рефлектометрии, используются для точного контроля толщины оксида затвора, а также толщины, показателя преломления и коэффициента экстинкции фоторезиста и других покрытий. Мы используем оборудование для тестирования полупроводниковых пластин, чтобы убедиться, что пластины не были повреждены в результате предыдущих этапов обработки вплоть до тестирования. После завершения предварительных процессов полупроводниковые микроэлектронные устройства подвергаются различным электрическим испытаниям, чтобы определить, правильно ли они функционируют. Мы называем долю устройств микроэлектроники на пластине, которые работают должным образом, как «выход». Тестирование микросхем микроэлектроники на пластине проводится с помощью электронного тестера, который прижимает крошечные щупы к полупроводниковой микросхеме. Автоматическая машина помечает каждую неисправную микросхему микроэлектроники каплей красителя. Данные испытаний пластин регистрируются в базе данных центрального компьютера, а полупроводниковые микросхемы сортируются по виртуальным контейнерам в соответствии с заранее установленными пределами испытаний. Полученные данные биннинга могут быть графически или зарегистрированы на карте пластин, чтобы отслеживать производственные дефекты и помечать неисправные чипы. Эту карту также можно использовать во время сборки и упаковки пластин. При окончательном тестировании микросхемы микроэлектроники снова тестируются после упаковки, поскольку соединительные провода могут отсутствовать или аналоговые характеристики могут быть изменены упаковкой. После того, как полупроводниковая пластина испытана, ее толщина обычно уменьшается до того, как пластина будет надрезана, а затем разбита на отдельные матрицы. Этот процесс называется нарезкой полупроводниковых пластин. Мы используем автоматизированные машины для подбора и размещения, специально изготовленные для микроэлектронной промышленности, для сортировки хороших и плохих полупроводниковых кристаллов. Упаковываются только хорошие полупроводниковые микросхемы без маркировки. Далее, в процессе изготовления пластиковой или керамической упаковки для микроэлектроники мы устанавливаем полупроводниковый кристалл, соединяем контактные площадки кристалла с контактами на корпусе и герметизируем кристалл. Крошечные золотые провода используются для соединения контактных площадок с контактами с помощью автоматических машин. Пакет в масштабе чипа (CSP) - еще одна технология упаковки микроэлектроники. Пластиковый двухрядный корпус (DIP), как и большинство корпусов, в несколько раз больше, чем реальный полупроводниковый кристалл, помещенный внутри, тогда как чипы CSP почти такого же размера, как кристалл микроэлектроники; и CSP может быть сконструирован для каждого кристалла до того, как полупроводниковая пластина будет нарезана кубиками. Упакованные микросхемы микроэлектроники повторно тестируются, чтобы убедиться, что они не были повреждены во время упаковки и что процесс соединения кристалла с выводом был выполнен правильно. Затем с помощью лазера мы гравируем названия и номера чипов на упаковке. Разработка и изготовление микроэлектронных корпусов: Мы предлагаем как стандартные, так и индивидуальные разработки и изготовление микроэлектронных корпусов. В рамках данной услуги также осуществляется моделирование и симуляция микроэлектронных пакетов. Моделирование и симуляция обеспечивают виртуальный план экспериментов (DoE) для достижения оптимального решения, а не для тестирования пакетов в полевых условиях. Это снижает стоимость и время производства, особенно при разработке новых продуктов в микроэлектронике. Эта работа также дает нам возможность объяснить нашим клиентам, как сборка, надежность и тестирование повлияют на их микроэлектронные продукты. Основная цель микроэлектронной упаковки — разработать электронную систему, которая будет удовлетворять требованиям конкретного приложения по разумной цене. Из-за множества доступных вариантов соединения и размещения системы микроэлектроники выбор технологии упаковки для данного приложения требует экспертной оценки. Критерии выбора пакетов микроэлектроники могут включать некоторые из следующих технологических факторов: -Возможность подключения -Урожай -Расходы -Теплорассеивающие свойства -Электромагнитное экранирование производительности -Механическая прочность -Надежность Эти конструктивные соображения для корпусов микроэлектроники влияют на скорость, функциональность, температуру перехода, объем, вес и многое другое. Основная цель состоит в том, чтобы выбрать наиболее экономичную, но надежную технологию присоединения. Мы используем сложные методы анализа и программное обеспечение для разработки корпусов микроэлектроники. Упаковка микроэлектроники связана с разработкой методов изготовления взаимосвязанных миниатюрных электронных систем и обеспечением надежности этих систем. В частности, корпус микроэлектроники включает в себя маршрутизацию сигналов при сохранении целостности сигнала, распределение земли и питания по полупроводниковым интегральным схемам, рассеивание рассеянного тепла при сохранении структурной и материальной целостности, а также защиту схемы от опасностей окружающей среды. Как правило, методы компоновки микросхем микроэлектроники включают использование печатной платы с разъемами, которые обеспечивают реальный ввод-вывод для электронной схемы. Традиционные подходы к компоновке микроэлектроники предполагают использование отдельных корпусов. Основным преимуществом однокристального корпуса является возможность полного тестирования микросхемы микроэлектроники перед ее подключением к основной подложке. Такие корпусированные полупроводниковые устройства монтируются либо в сквозное отверстие, либо на поверхность печатной платы. Корпуса микроэлектроники для поверхностного монтажа не требуют сквозных отверстий, проходящих через всю плату. Вместо этого компоненты микроэлектроники для поверхностного монтажа могут быть припаяны к обеим сторонам печатной платы, что обеспечивает более высокую плотность схем. Такой подход называется технологией поверхностного монтажа (SMT). Добавление корпусов в виде площадных массивов, таких как массивы шариковых решеток (BGA) и корпуса в масштабе кристалла (CSP), делает SMT конкурентоспособным с технологиями корпусирования полупроводниковой микроэлектроники с самой высокой плотностью. Более новая технология упаковки включает в себя прикрепление более одного полупроводникового устройства к подложке межсоединений высокой плотности, которая затем монтируется в большой корпус, обеспечивая как контакты ввода-вывода, так и защиту от окружающей среды. Эта технология многокристальных модулей (MCM) дополнительно характеризуется технологиями подложек, используемыми для соединения подключенных ИС. MCM-D представляет собой напыленные тонкопленочные металлические и диэлектрические мультислои. Подложки MCM-D имеют самую высокую плотность проводки среди всех технологий MCM благодаря сложным технологиям обработки полупроводников. MCM-C относится к многослойным «керамическим» подложкам, обожженным из сложенных чередующихся слоев экранированных металлических красок и необожженных керамических листов. Используя MCM-C, мы получаем умеренно плотную пропускную способность. MCM-L относится к многослойным подложкам, изготовленным из уложенных друг на друга металлизированных «ламинатов» печатных плат, на которые нанесен индивидуальный рисунок, а затем они ламинированы. Раньше это была технология межсоединений с низкой плотностью, однако теперь MCM-L быстро приближается к плотности технологий упаковки микроэлектроники MCM-C и MCM-D. Технология упаковки микроэлектроники с прямым подключением микросхемы (DCA) или чип-на-плате (COB) включает монтаж микросхем микроэлектроники непосредственно на печатную плату. Пластиковый герметик, который «наносится» на голую ИС, а затем отверждается, обеспечивает защиту от окружающей среды. Микросхемы микроэлектроники могут быть соединены с подложкой с использованием методов флип-чипа или проволочного соединения. Технология DCA особенно экономична для систем, которые ограничены 10 или менее полупроводниковыми ИС, поскольку большее количество микросхем может повлиять на производительность системы, а сборки DCA могут быть трудны для доработки. Преимущество, общее для вариантов корпусов DCA и MCM, заключается в устранении уровня межсоединений корпуса полупроводниковой ИС, что обеспечивает более близкое расположение (более короткие задержки передачи сигнала) и меньшую индуктивность выводов. Основным недостатком обоих методов является сложность приобретения полностью протестированных микросхем микроэлектроники. Другие недостатки технологий DCA и MCM-L включают плохое управление температурой из-за низкой теплопроводности ламинатов PWB и плохого соответствия коэффициента теплового расширения между полупроводниковым кристаллом и подложкой. Для решения проблемы несоответствия теплового расширения требуется промежуточная подложка, такая как молибден для кристалла с проволочным соединением и эпоксидная смола с недостаточным заполнением для кристалла с перевернутым кристаллом. Многокристальный несущий модуль (MCCM) сочетает в себе все положительные аспекты технологии DCA и MCM. MCCM — это просто небольшой MCM на тонком металлическом носителе, который можно приклеить или механически прикрепить к печатной плате. Металлическое дно действует как рассеиватель тепла и как интерполятор напряжения для подложки MCM. MCCM имеет периферийные выводы для присоединения проводов, пайки или лепесткового соединения с печатной платой. Неизолированные полупроводниковые ИС защищены специальным материалом. Когда вы свяжетесь с нами, мы обсудим ваше приложение и требования, чтобы выбрать лучший вариант упаковки микроэлектроники для вас. Сборка, упаковка и тестирование полупроводниковых интегральных схем: В рамках наших услуг по изготовлению микроэлектроники мы предлагаем склеивание кристаллов, проводов и микросхем, инкапсуляцию, сборку, маркировку и брендирование, а также тестирование. Чтобы полупроводниковый чип или интегральная микроэлектронная схема функционировали, он должен быть подключен к системе, которой он будет управлять или давать инструкции. Сборка ИС микроэлектроники обеспечивает соединения для питания и передачи информации между чипом и системой. Это достигается подключением микросхемы микроэлектроники к корпусу или прямым подключением ее к печатной плате для выполнения этих функций. Соединения между чипом и корпусом или печатной платой (PCB) осуществляются с помощью проволочного соединения, сквозного отверстия или сборки с перевернутым чипом. Мы являемся лидером отрасли в поиске решений для упаковки микросхем микроэлектроники, отвечающих сложным требованиям рынка беспроводной связи и Интернета. Мы предлагаем тысячи различных форматов и размеров корпусов, начиная от традиционных корпусов интегральных схем микроэлектроники в виде выводных рамок для сквозного и поверхностного монтажа и заканчивая новейшими решениями в виде чип-масштаба (CSP) и массива шариковых решеток (BGA), необходимых для приложений с большим количеством выводов и высокой плотностью. . На складе доступен широкий выбор корпусов, включая CABGA (чип-массив BGA), CQFP, CTBGA (чип-массив с тонким сердечником BGA), CVBGA (очень тонкий чип-массив BGA), Flip Chip, LCC, LGA, MQFP, PBGA, PDIP, PLCC, PoP — упаковка на упаковке, PoP TMV — через пресс-форму, SOIC / SOJ, SSOP, TQFP, TSOP, WLP (пакет уровня пластины)…..и т. д. Соединение проводов с использованием меди, серебра или золота является одним из популярных в микроэлектронике. Медный (Cu) провод был методом соединения кремниевых полупроводниковых кристаллов с клеммами корпуса микроэлектроники. В связи с недавним увеличением стоимости золотой (Au) проволоки медная (Cu) проволока является привлекательным способом управления общей стоимостью упаковки в микроэлектронике. Он также напоминает золотую (Au) проволоку из-за сходных электрических свойств. Собственная индуктивность и собственная емкость почти одинаковы для золотой (Au) и медной (Cu) проволоки, при этом медная (Cu) проволока имеет более низкое удельное сопротивление. В приложениях микроэлектроники, где сопротивление соединительного провода может отрицательно сказаться на характеристиках схемы, использование медного (Cu) провода может улучшить характеристики. Проволока из сплава меди, меди с палладиевым покрытием (PCC) и серебра (Ag) стала альтернативой проволоке с золотым покрытием из-за ее стоимости. Провода на основе меди недороги и имеют низкое удельное электрическое сопротивление. Однако твердость меди затрудняет ее использование во многих приложениях, например, с хрупкими структурами контактных площадок. Для этих применений Ag-Alloy предлагает свойства, аналогичные свойствам золота, а его стоимость аналогична стоимости PCC. Проволока из Ag-Alloy мягче, чем PCC, что снижает брызги алюминия и риск повреждения контактной площадки. Проволока из Ag-Alloy является лучшей недорогой заменой для приложений, в которых требуется соединение кристалл-к-кристаллу, соединение водопадом, сверхмалый шаг контактных площадок и небольшие отверстия контактных площадок, сверхмалая высота петли. Мы предоставляем полный спектр услуг по тестированию полупроводников, включая тестирование полупроводниковых пластин, различные виды окончательного тестирования, тестирование на системном уровне, тестирование полосы и полный комплекс услуг по завершению производства. Мы тестируем различные типы полупроводниковых устройств во всех наших семействах корпусов, включая радиочастотные, аналоговые и смешанные сигналы, цифровые, устройства управления питанием, память и различные комбинации, такие как ASIC, многочиповые модули, System-in-Package (SiP) и многослойные 3D-упаковки, датчики и устройства MEMS, такие как акселерометры и датчики давления. Наше тестовое оборудование и контактное оборудование подходят для SiP-упаковки нестандартного размера, двухсторонних контактных решений для упаковки на упаковке (PoP), TMV PoP, разъемов FusionQuad, многорядных рамок MicroLeadFrame, медных опор с мелким шагом. Испытательное оборудование и испытательные площадки интегрированы с инструментами CIM / CAM, анализом производительности и мониторингом производительности, чтобы с первого раза обеспечить очень высокую эффективность. Мы предлагаем множество адаптивных процессов тестирования микроэлектроники для наших клиентов и предлагаем распределенные потоки тестирования для SiP и других сложных процессов сборки. AGS-TECH предоставляет полный спектр консультационных услуг по тестированию, разработке и инжинирингу на протяжении всего жизненного цикла полупроводниковой и микроэлектронной продукции. Мы понимаем уникальные рынки и требования к тестированию для SiP, автомобильной промышленности, сетей, игр, графики, вычислений, RF/беспроводной связи. Процессы производства полупроводников требуют быстрых и точно контролируемых решений для маркировки. Скорость маркировки более 1000 символов в секунду и глубина проникновения в материал менее 25 микрон являются обычными в промышленности полупроводниковой микроэлектроники с использованием передовых лазеров. Мы можем маркировать компаунды для форм, пластины, керамику и многое другое с минимальным подводом тепла и идеальной воспроизводимостью. Мы используем лазеры с высокой точностью, чтобы маркировать даже самые маленькие детали без повреждений. Выводные рамки для полупроводниковых устройств: возможны как стандартные, так и индивидуальные разработки и изготовление. Выводные рамки используются в процессах сборки полупроводниковых устройств и представляют собой тонкие слои металла, которые соединяют проводку от крошечных электрических клемм на поверхности полупроводниковой микроэлектроники с крупными схемами на электрических устройствах и печатных платах. Выводные рамки используются практически во всех корпусах полупроводниковой микроэлектроники. Большинство корпусов интегральных схем для микроэлектроники изготавливаются путем размещения полупроводникового кремниевого чипа на выводной рамке, затем проволочного соединения чипа с металлическими выводами этого выводного каркаса и последующего покрытия микроэлектронного чипа пластиковой крышкой. Этот простой и относительно недорогой корпус микроэлектроники по-прежнему остается лучшим решением для многих приложений. Свинцовые рамки изготавливаются в виде длинных полос, что позволяет быстро обрабатывать их на автоматизированных сборочных машинах, и обычно используются два производственных процесса: какое-либо фототравление и штамповка. В микроэлектронике конструкция выводной рамы часто требует индивидуальных спецификаций и функций, конструкции, улучшающей электрические и тепловые свойства, и конкретных требований к времени цикла. У нас есть обширный опыт производства выводных рамок для микроэлектроники для множества различных клиентов с использованием лазерного фототравление и штамповки. Проектирование и производство радиаторов для микроэлектроники: как готовые, так и индивидуальные разработки и изготовление. С увеличением рассеивания тепла микроэлектронными устройствами и уменьшением общих форм-факторов управление температурным режимом становится все более важным элементом дизайна электронных продуктов. Стабильность производительности и ожидаемый срок службы электронного оборудования обратно пропорциональны температуре компонентов оборудования. Соотношение между надежностью и рабочей температурой типичного кремниевого полупроводникового устройства показывает, что снижение температуры соответствует экспоненциальному увеличению надежности и ожидаемого срока службы устройства. Следовательно, долгий срок службы и надежная работа компонента полупроводниковой микроэлектроники могут быть достигнуты за счет эффективного контроля рабочей температуры устройства в пределах, установленных разработчиками. Радиаторы — это устройства, которые улучшают отвод тепла от горячей поверхности, обычно внешнего корпуса тепловыделяющего компонента, к более прохладной окружающей среде, такой как воздух. В дальнейшем в качестве охлаждающей жидкости предполагается воздух. В большинстве случаев теплопередача через границу между твердой поверхностью и охлаждающим воздухом в системе наименее эффективна, а граница твердого тела и воздуха представляет собой наибольший барьер для рассеивания тепла. Радиатор снижает этот барьер главным образом за счет увеличения площади поверхности, непосредственно контактирующей с хладагентом. Это позволяет рассеивать больше тепла и/или снижает рабочую температуру полупроводникового устройства. Основной целью радиатора является поддержание температуры устройства микроэлектроники ниже максимально допустимой температуры, указанной производителем полупроводникового устройства. Мы можем классифицировать радиаторы с точки зрения методов изготовления и их формы. К наиболее распространенным типам радиаторов с воздушным охлаждением относятся: - Штамповки: медные или алюминиевые листы штампуются в желаемые формы. они используются в традиционном воздушном охлаждении электронных компонентов и предлагают экономичное решение тепловых проблем с низкой плотностью. Они подходят для крупносерийного производства. - Экструзия: эти радиаторы позволяют формировать сложные двумерные формы, способные рассеивать большие тепловые нагрузки. Их можно резать, обрабатывать и добавлять опции. Сквозная резка позволит получить всенаправленные радиаторы с прямоугольными штыревыми ребрами, а включение зубчатых ребер улучшит производительность примерно на 10–20%, но с более медленной скоростью экструзии. Ограничения экструзии, такие как высота ребра до толщины зазора, обычно определяют гибкость вариантов конструкции. Типичное соотношение высоты ребра к зазору до 6 и минимальная толщина ребра 1,3 мм достижимы с помощью стандартных методов экструзии. Соотношение сторон 10 к 1 и толщина ребра 0,8 дюйма могут быть получены за счет специальных конструктивных особенностей матрицы. Однако по мере увеличения соотношения сторон устойчивость к экструзии снижается. - Склеенные/изготовленные ребра: большинство радиаторов с воздушным охлаждением ограничены конвекцией, и общие тепловые характеристики радиатора с воздушным охлаждением часто могут быть значительно улучшены, если большая площадь поверхности может подвергаться воздействию воздушного потока. В этих высокоэффективных радиаторах используется теплопроводящая эпоксидная смола с алюминиевым наполнителем для приклеивания плоских ребер к рифленой экструзионной базовой пластине. Этот процесс позволяет значительно увеличить соотношение высоты ребра к зазору от 20 до 40, что значительно увеличивает охлаждающую способность без увеличения объема. - Отливки: процессы литья алюминия или меди/бронзы в песок, восковые модели и литье под давлением доступны как с использованием вакуума, так и без него. Мы используем эту технологию для изготовления радиаторов с игольчатыми ребрами высокой плотности, которые обеспечивают максимальную производительность при использовании импинджментного охлаждения. - Сложенные ребра: гофрированный листовой металл из алюминия или меди увеличивает площадь поверхности и объемные характеристики. Затем радиатор прикрепляется либо к базовой пластине, либо непосредственно к нагревательной поверхности с помощью эпоксидной смолы или пайки. Он не подходит для высокопрофильных радиаторов из-за доступности и эффективности ребер. Следовательно, это позволяет изготавливать высокопроизводительные радиаторы. При выборе подходящего радиатора, отвечающего требуемым тепловым критериям для ваших приложений микроэлектроники, нам необходимо изучить различные параметры, которые влияют не только на характеристики самого радиатора, но и на общую производительность системы. Выбор конкретного типа радиатора в микроэлектронике во многом зависит от теплового баланса, допустимого для радиатора, и внешних условий, окружающих радиатор. Никогда не существует единого значения теплового сопротивления, назначенного для данного радиатора, поскольку тепловое сопротивление зависит от внешних условий охлаждения. Конструкция и изготовление датчика и исполнительного механизма: Доступны как стандартные, так и индивидуальные конструкции и изготовление. Мы предлагаем решения с готовыми к использованию процессами для инерциальных датчиков, датчиков давления и относительного давления, а также инфракрасных датчиков температуры. Используя наши IP-блоки для акселерометров, ИК-датчиков и датчиков давления или применяя вашу конструкцию в соответствии с доступными спецификациями и правилами проектирования, мы можем доставить вам сенсорные устройства на основе МЭМС в течение нескольких недель. Помимо МЭМС, могут быть изготовлены другие типы конструкций датчиков и приводов. Разработка и производство оптоэлектронных и фотонных схем: фотонная или оптическая интегральная схема (PIC) — это устройство, которое объединяет несколько фотонных функций. Это можно сравнить с электронными интегральными схемами в микроэлектронике. Основное различие между ними заключается в том, что фотонная интегральная схема обеспечивает функциональность для информационных сигналов, наложенных на оптические длины волн в видимом спектре или ближнем инфракрасном диапазоне 850–1650 нм. Методы изготовления аналогичны тем, которые используются в интегральных схемах микроэлектроники, где фотолитография используется для создания рисунка пластин для травления и осаждения материала. В отличие от полупроводниковой микроэлектроники, где основным устройством является транзистор, в оптоэлектронике нет единого доминирующего устройства. Фотонные чипы включают межблочные волноводы с малыми потерями, делители мощности, оптические усилители, оптические модуляторы, фильтры, лазеры и детекторы. Для этих устройств требуется множество различных материалов и технологий изготовления, поэтому реализовать их все на одном чипе сложно. Мы применяем фотонные интегральные схемы в основном в областях оптоволоконной связи, биомедицинских и фотонных вычислений. Некоторые примеры оптоэлектронных продуктов, которые мы можем спроектировать и изготовить для вас, включают светодиоды (светоизлучающие диоды), диодные лазеры, оптоэлектронные приемники, фотодиоды, лазерные дистанционные модули, индивидуальные лазерные модули и многое другое. CLICK Product Finder-Locator Service ПРЕДЫДУЩАЯ СТРАНИЦА
- Промышленный, специальный и функциональный текстиль, Гидрофобно-гидрофильные текстильные материалы, Огнестойкие, Антибастерические, Противогрибковые, Антистатические ткани, Фильтровальные ткани
Промышленный, специальный и функциональный текстиль, Гидрофобно-гидрофильные текстильные материалы, Огнестойкий текстиль, Антибастериальные, противогрибковые, антистатические, Защитные ткани от UC, Фильтрующая одежда, Текстиль для хирургии, Биосовместимая ткань Промышленный, специальный и функциональный текстиль Нас интересуют только специальные и функциональные ткани, а также ткани и изделия из них, предназначенные для конкретного применения. Это инженерный текстиль исключительной ценности, также иногда называемый техническим текстилем и тканями. Тканые, а также нетканые ткани и ткани доступны для многочисленных применений. Ниже приведен список некоторых основных типов промышленного, специального и функционального текстиля, которые находятся в сфере разработки и производства нашей продукции. Мы готовы работать с вами над проектированием, разработкой и производством вашей продукции из: Гидрофобные (водоотталкивающие) и гидрофильные (водопоглощающие) текстильные материалы Текстиль и ткани необычайной прочности, долговечности и устойчивости к суровым условиям окружающей среды (например, пуленепробиваемые, высокотермостойкие, низкотемпературные, огнестойкие, инертные или устойчивые к агрессивным жидкостям и газам, устойчивые к плесени формирование….) Антибактериальные и противогрибковые средства текстиль и ткани УФ защитный Электропроводящие и непроводящие текстиль и ткани Антистатические ткани для защиты от электростатических разрядов….и т.д. Текстиль и ткани с особыми оптическими свойствами и эффектами (флуоресцентные и т.д.) Текстиль, ткани и полотна со специальными фильтрующими свойствами, производство фильтров Промышленный текстиль, такой как ткани для воздуховодов, прокладки, армирование, приводные ремни, армирование резины (конвейерные ленты, печатные полотна, шнуры), текстиль для лент и абразивы. Текстиль для автомобильной промышленности (шланги, ремни, подушки безопасности, прокладки, шины) Текстиль для строительства, строительных и инфраструктурных изделий (бетонное полотно, геомембраны и тканевые внутренние воздуховоды) Композитный многофункциональный текстиль, имеющий разные слои или компоненты для разных функций. Текстиль, изготовленный из активированного угля infusion on полиэфирных волокон, обеспечивает ощущение хлопка на ощупь, выделение запаха, управление влажностью и защиту от ультрафиолетового излучения. Текстиль из полимеров с памятью формы Текстиль для хирургии и хирургических имплантатов, биосовместимые ткани Обратите внимание, что мы проектируем, разрабатываем и производим продукцию в соответствии с вашими потребностями и спецификациями. Мы можем либо изготовить продукцию в соответствии с вашими спецификациями, либо, при желании, мы можем помочь вам в выборе правильных материалов и разработке дизайна продукта. ПРЕДЫДУЩАЯ СТРАНИЦА