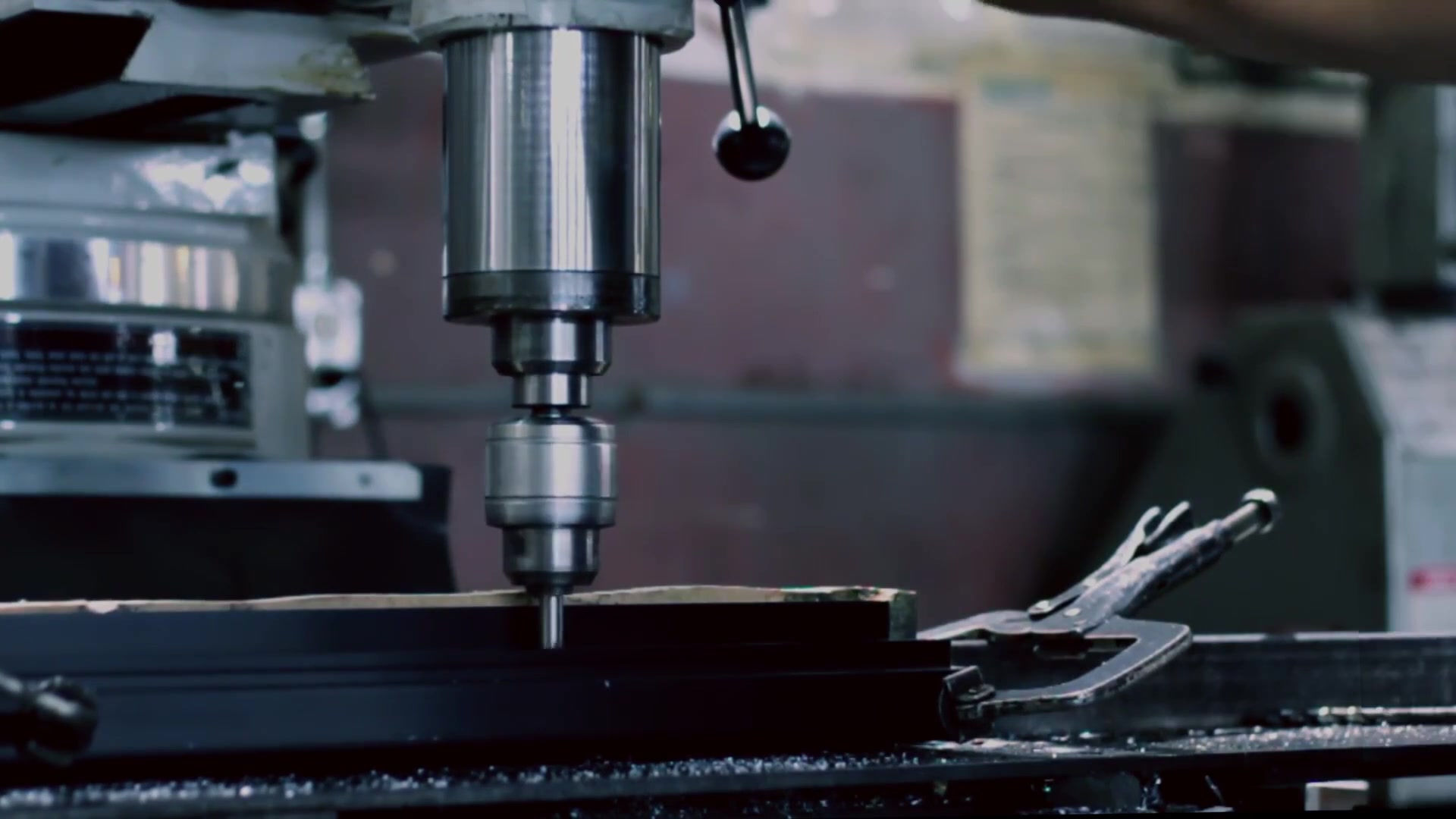
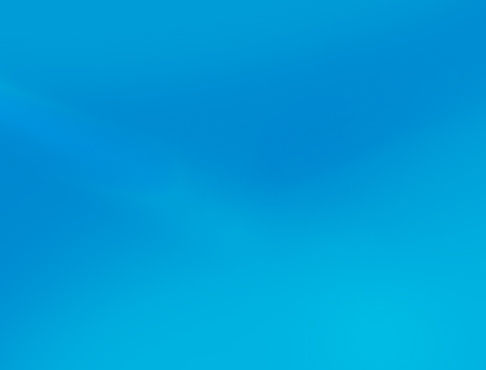
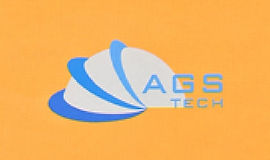
Глобален производител по поръчка, интегратор, консолидатор, аутсорсинг партньор за голямо разнообразие от продукти и услуги.
Ние сме вашият източник на едно гише за производство, производство, инженеринг, консолидация, интеграция, аутсорсинг на произведени по поръчка и готови продукти и услуги.
Изберете своя език
-
Производство по поръчка
-
Вътрешно и глобално договорно производство
-
Аутсорсинг на производство
-
Вътрешни и глобални доставки
-
Консолидация
-
Инженерна интеграция
-
Инженерни услуги
Типът производство на стъкло, което предлагаме, е контейнерно стъкло, издухване на стъкло, стъклени влакна и тръби и пръти, домакински и промишлени стъклария, лампи и крушки, прецизно формоване на стъкло, оптични компоненти и възли, плоско и листово и флоат стъкло. Извършваме както ръчно, така и машинно формоване.
Нашите популярни производствени процеси за техническа керамика са щанцоване, изостатично пресоване, горещо изостатично пресоване, горещо пресоване, шликерно леене, леене на лента, екструдиране, леене под налягане, зелена обработка, синтероване или изпичане, диамантено шлайфане, херметични възли.
Препоръчваме ви да щракнете тук, за
ИЗТЕГЛЕТЕ нашите схематични илюстрации на процеси за формоване и оформяне на стъкло от AGS-TECH Inc.
Тези файлове за изтегляне със снимки и скици ще ви помогнат да разберете по-добре информацията, която ви предоставяме по-долу.
• ПРОИЗВОДСТВО НА КОНТЕЙНЕРНО СТЪКЛО: Имаме автоматизирани линии за ПРЕСА И ИЗДУХВАНЕ, както и линии за ИЗДУХВАНЕ И ИЗДУХВАНЕ за производство. В процеса на издухване и издухване пускаме парче в празна форма и оформяме гърлото, като прилагаме удар със сгъстен въздух отгоре. Непосредствено след това сгъстеният въздух се издухва втори път от другата посока през гърлото на контейнера, за да се образува предварителната форма на бутилката. Тази предварителна форма след това се прехвърля в действителната форма, загрява се отново, за да омекне и се прилага сгъстен въздух, за да се придаде на предварителната форма окончателната форма на контейнер. По-ясно, той се поставя под налягане и се притиска към стените на кухината на формата за раздуване, за да заеме желаната форма. Накрая, произведеният стъклен контейнер се прехвърля в пещ за отгряване за последващо повторно нагряване и отстраняване на напреженията, получени по време на формоването, и се охлажда по контролиран начин. При метода на пресоване и издухване, разтопените частици се поставят във форма за запарване (празна форма) и се пресоват във формата за запарване (форма за заготовка). След това заготовките се прехвърлят във форми за издухване и се издухват подобно на процеса, описан по-горе в „Процес на издухване и издухване“. Последващите стъпки като отгряване и облекчаване на напрежението са подобни или същите.
• ИЗДУХВАНЕ НА СТЪКЛО: Произвеждаме продукти от стъкло, използвайки конвенционално ръчно издухване, както и използвайки сгъстен въздух с автоматизирано оборудване. За някои поръчки е необходимо конвенционално издуване, като например проекти, включващи произведения на изкуството от стъкло, или проекти, които изискват по-малък брой части с разхлабени толеранси, прототипиране/демо проекти….и т.н. Конвенционалното издуване на стъкло включва потапяне на куха метална тръба в съд с разтопено стъкло и въртене на тръбата за събиране на известно количество от стъкления материал. Стъклото, събрано на върха на тръбата, се търкаля върху плоско желязо, оформя се по желание, удължава се, нагрява се отново и се продухва. Когато е готов, се поставя във форма и се пуска въздух. Кухината на формата е мокра, за да се избегне контакт на стъклото с метал. Водният филм действа като възглавница между тях. Ръчното издухване е трудоемък бавен процес и е подходящ само за създаване на прототипи или артикули с висока стойност, не е подходящ за евтини големи поръчки на бройка.
• ПРОИЗВОДСТВО НА БИТОВА И ПРОМИШЛЕНА СТЪКЛАРИЯ: С помощта на различни видове стъклени материали се произвежда голямо разнообразие от стъклени изделия. Някои чаши са устойчиви на топлина и са подходящи за лабораторни стъклени съдове, докато някои са достатъчно добри, за да издържат многократно миене в съдомиялни машини и са подходящи за производство на домашни продукти. С помощта на машини на Westlake се произвеждат десетки хиляди чаши за пиене на ден. За да се опрости, стопеното стъкло се събира чрез вакуум и се вкарва във форми, за да се направят предварителните форми. След това във формите се вдухва въздух, те се прехвърлят в друга форма и отново се вдухва въздух и стъклото приема окончателната си форма. Подобно на ръчното издухване, тези форми се държат мокри с вода. По-нататъшното разтягане е част от довършителната операция, при която се оформя шийката. Излишното стъкло се изгаря. След това следва контролираният процес на повторно нагряване и охлаждане, описан по-горе.
• ФОРМОВАНЕ НА СТЪКЛЕНИ ТРЪБИ И ПРЪТКИ: Основните процеси, които използваме за производство на стъклени тръби, са процесите DANNER и VELLO. В процеса на Данер стъклото от пещ тече и пада върху наклонена втулка, изработена от огнеупорни материали. Втулката се носи върху въртящ се кух вал или духалка. След това стъклото се увива около втулката и образува гладък слой, който тече надолу по втулката и върху върха на ствола. При формоване на тръби въздухът се издухва през вентилатор с кух връх, а при формоване на пръти използваме твърди накрайници на вала. След това тръбите или прътите се изтеглят върху носещи ролки. Размерите като дебелина на стената и диаметър на стъклените тръби се регулират до желаните стойности чрез задаване на диаметъра на втулката и въздушно налягане на продухване до желана стойност, регулиране на температурата, скоростта на потока на стъклото и скоростта на изтегляне. Процесът на производство на стъклена тръба Vello, от друга страна, включва стъкло, което излиза от пещ и се насочва към купа с кух дорник или камбана. След това стъклото преминава през въздушното пространство между дорника и купата и приема формата на тръба. След това преминава през ролки към машина за изтегляне и се охлажда. В края на охладителната линия се извършва рязане и крайна обработка. Размерите на тръбата могат да се регулират точно както в процеса на Danner. Когато сравняваме процеса Danner с Vello, можем да кажем, че процесът Vello е по-подходящ за производство на големи количества, докато процесът Danner може да е по-подходящ за прецизни поръчки на тръби с по-малък обем.
• ОБРАБОТКА НА ЛИСТА И ПЛОСКО И ФЛОАТ СТЪКЛО: Разполагаме с големи количества плоско стъкло с дебелини, вариращи от субмилиметрови дебелини до няколко сантиметра. Нашите плоски стъкла са с почти оптично съвършенство. Ние предлагаме стъкла със специални покрития като оптични покрития, където се използва техника за химическо отлагане на пари за поставяне на покрития като антирефлексно или огледално покритие. Често се срещат и прозрачни проводими покрития. Предлагат се и хидрофобни или хидрофилни покрития върху стъкло, както и покритие, което прави стъклото самопочистващо се. Закалените, бронираните и ламинираните стъкла са други популярни артикули. Изрязваме стъкло в желана форма с желани толеранси. Налични са и други вторични операции като извиване или огъване на плоско стъкло.
• ПРЕЦИЗНО ФОРМОВАНЕ НА СТЪКЛО: Използваме тази техника най-вече за производство на прецизни оптични компоненти без необходимост от по-скъпи и отнемащи време техники като шлайфане, прилепване и полиране. Тази техника не винаги е достатъчна, за да се направи най-доброто от най-добрата оптика, но в някои случаи като потребителски продукти, цифрови фотоапарати, медицинска оптика може да бъде по-евтин добър вариант за производство в голям обем. Също така има предимство пред другите техники за оформяне на стъкло, където се изискват сложни геометрии, като например в случая на асфери. Основният процес включва зареждане на долната страна на нашата форма със стъклената заготовка, евакуация на процесната камера за отстраняване на кислорода, близо до затваряне на формата, бързо и изотермично нагряване на матрицата и стъклото с инфрачервена светлина, по-нататъшно затваряне на половините на матрицата бавно и контролирано пресоване на омекотеното стъкло до желаната дебелина и накрая охлаждане на стъклото и пълнене на камерата с азот и отстраняване на продукта. Прецизният температурен контрол, разстоянието на затваряне на матрицата, силата на затваряне на матрицата, съответствието на коефициентите на разширение на матрицата и стъкления материал са ключови в този процес.
• ПРОИЗВОДСТВО НА СТЪКЛЕНИ ОПТИЧНИ КОМПОНЕНТИ И ВЪЗЛОВИ: Освен прецизното формоване на стъкло, има редица ценни процеси, които използваме за изработване на висококачествени оптични компоненти и възли за взискателни приложения. Шлифоването, прилепването и полирането на оптични стъкла във фини специални абразивни суспензии е изкуство и наука за изработка на оптични лещи, призми, плоски и други. Плоскостта на повърхността, вълнообразността, гладкостта и оптичните повърхности без дефекти изискват много опит с такива процеси. Малки промени в околната среда могат да доведат до продукти извън спецификациите и спиране на производствената линия. Има случаи, при които едно избърсване на оптичната повърхност с чиста кърпа може да накара продукта да отговаря на спецификациите или да се провали на теста. Някои използвани популярни стъклени материали са разтопен силициев диоксид, кварц, BK7. Освен това сглобяването на такива компоненти изисква специализиран нишов опит. Понякога се използват специални лепила. Понякога обаче техника, наречена оптичен контакт, е най-добрият избор и не включва материал между прикрепените оптични стъкла. Състои се от физически контакт с плоски повърхности, за да се закрепят една към друга без лепило. В някои случаи се използват механични дистанционни елементи, прецизни стъклени пръчки или топки, скоби или обработени метални компоненти за сглобяване на оптичните компоненти на определени разстояния и с определени геометрични ориентации един спрямо друг. Нека разгледаме някои от нашите популярни техники за производство на оптика от висок клас.
ШЛИФОВАНЕ & ЛЕПИРАНЕ & ПОЛИРАНЕ: Грубата форма на оптичния компонент се получава чрез шлайфане на стъклена заготовка. След това се извършва прилепване и полиране чрез въртене и триене на грапавите повърхности на оптичните компоненти срещу инструменти с желани повърхностни форми. Суспензии с малки абразивни частици и течност се изсипват между оптиката и оформящите инструменти. Размерите на абразивните частици в такива суспензии могат да бъдат избрани според желаната степен на плоскост. Отклоненията на критичните оптични повърхности от желаните форми се изразяват чрез дължини на вълните на използваната светлина. Нашата оптика с висока прецизност има допустими отклонения от една десета от дължината на вълната (дължина на вълната/10) или е възможно дори по-строго. Освен профила на повърхността, критичните повърхности се сканират и оценяват за други повърхностни характеристики и дефекти като размери, драскотини, чипове, вдлъбнатини, петна...и т.н. Строгият контрол на условията на околната среда в цеха за оптично производство и обширните изисквания за метрология и изпитване с най-съвременно оборудване правят този отрасъл предизвикателство.
• ВТОРИЧНИ ПРОЦЕСИ В ПРОИЗВОДСТВОТО НА СТЪКЛО: Отново, ние сме ограничени само с вашето въображение, когато става дума за вторични и довършителни процеси на стъкло. Тук изброяваме някои от тях:
-Покрития върху стъкло (оптични, електрически, трибологични, термични, функционални, механични...). Като пример можем да променим свойствата на повърхността на стъклото, правейки го например да отразява топлината, така че да поддържа интериора на сградата хладен, или да направим едната страна абсорбираща инфрачервените лъчи с помощта на нанотехнология. Това помага да се запази топлината във вътрешността на сградите, тъй като най-външният повърхностен слой стъкло ще абсорбира инфрачервеното лъчение вътре в сградата и ще го излъчва обратно навътре.
-Офорт на стъкло
-Приложено керамично етикетиране (ACL)
-Гравиране
- Пламъчно полиране
- Химическо полиране
-Оцветяване
ПРОИЗВОДСТВО НА ТЕХНИЧЕСКА КЕРАМИКА
• ПРЕСОВАНЕ НА МАТРИЦА: Състои се от едноосно уплътняване на гранулирани прахове, затворени в матрица
• ГОРЕЩО ПРЕСОВАНЕ: Подобно на пресоването на матрицата, но с добавяне на температура за подобряване на уплътняването. Прах или пресована заготовка се поставя в графитна матрица и се прилага едноосно налягане, докато матрицата се поддържа при високи температури като 2000 C. Температурите могат да бъдат различни в зависимост от вида на керамичния прах, който се обработва. За сложни форми и геометрии може да е необходима друга последваща обработка, като диамантено шлайфане.
• ИЗОСТАТИЧНО ПРЕСОВАНЕ: Гранулиран прах или пресовани пресовани пресовани се поставят в херметически затворени контейнери и след това в затворен съд под налягане с течност вътре. След това те се уплътняват чрез увеличаване на налягането в съда под налягане. Течността вътре в съда пренася равномерно силите на налягане върху цялата повърхност на херметически затворения контейнер. По този начин материалът се уплътнява равномерно и приема формата на своя гъвкав контейнер и неговия вътрешен профил и характеристики.
• ГОРЕЩО ИЗОСТАТИЧНО ПРЕСОВАНЕ: Подобно на изостатичното пресоване, но в допълнение към газовата атмосфера под налягане, ние синтероваме компакта при висока температура. Горещото изостатично пресоване води до допълнително уплътняване и повишена якост.
• Шликерно леене / дренажно леене: Напълваме матрицата със суспензия от керамични частици с микрометрови размери и носеща течност. Тази смес се нарича "приплъзване". Формата има пори и затова течността в сместа се филтрира във формата. В резултат на това се образува отливка върху вътрешните повърхности на формата. След синтероване частите могат да бъдат извадени от формата.
• ЛЕЕНЕ НА ЛЕНТИ: Ние произвеждаме керамични ленти чрез леене на керамични суспензии върху плоски движещи се носещи повърхности. Суспензиите съдържат керамични прахове, смесени с други химикали за свързване и пренасяне. Тъй като разтворителите се изпаряват, остават плътни и гъвкави листове от керамика, които могат да бъдат нарязани или навити по желание.
• ЕКСТРУЗИОННО ФОРМУВАНЕ: Както при други процеси на екструзия, мека смес от керамичен прах със свързващи вещества и други химикали преминава през матрица, за да придобие формата на напречното си сечение и след това се нарязва на желаните дължини. Процесът се извършва със студени или загряти керамични смеси.
• ИНЖЕКТИРАНЕ ПОД НИСКО НАЛЯГАНЕ: Ние приготвяме смес от керамичен прах със свързващи вещества и разтворители и я загряваме до температура, при която може лесно да бъде пресована и принудена в кухината на инструмента. След като цикълът на формоване приключи, детайлът се изхвърля и свързващият химикал се изгаря. Използвайки леене под налягане, ние можем да получим сложни части в големи обеми икономично. Възможни са дупки , които са малка част от милиметър на стена с дебелина 10 mm, възможни са резби без допълнителна обработка, възможни са допуски до +/- 0,5% и дори по-ниски, когато частите се обработват , възможни са дебелини на стените от порядъка на 0,5 mm до дължина 12,5 mm, както и дебелини на стените от 6,5 mm до дължина 150 mm.
• ЗЕЛЕНА МАШИННА ОБРАБОТКА: Използвайки същите инструменти за метална обработка, можем да обработваме пресовани керамични материали, докато те са все още меки като тебешир. Възможни са допустими отклонения от +/- 1%. За по-добри толеранси използваме диамантено шлайфане.
• СИНТЕРОВАНЕ или ИЗПЕЧВАНЕ: Спечаването прави възможно пълното уплътняване. Появява се значително свиване на зелените компактни части, но това не е голям проблем, тъй като ние вземаме предвид тези промени в размерите, когато проектираме частта и инструменталната екипировка. Частиците на праха се свързват заедно и порьозността, предизвикана от процеса на уплътняване, се отстранява до голяма степен.
• ДИАМАНТЕНО ШЛИФОВАНЕ: Най-твърдият материал в света „диамант“ се използва за шлайфане на твърди материали като керамика и се получават прецизни части. Постигат се толеранси в микрометровия диапазон и много гладки повърхности. Поради разходите си, ние обмисляме тази техника само когато наистина имаме нужда от нея.
• ХЕРМЕТИЧНИ ВЪЗЛИ са тези, които на практика не позволяват обмен на материя, твърди вещества, течности или газове между интерфейсите. Херметичното запечатване е херметично. Например херметичните електронни кутии са тези, които пазят чувствителното вътрешно съдържание на опаковано устройство невредимо от влага, замърсители или газове. Нищо не е 100% херметично, но когато говорим за херметичност, имаме предвид, че на практика има херметичност до степента, в която степента на изтичане е толкова ниска, че устройствата са безопасни при нормални условия на околната среда за много дълго време. Нашите херметични възли се състоят от метални, стъклени и керамични компоненти, метал-керамика, керамика-метал-керамика, метал-керамика-метал, метал към метал, метал-стъкло, метал-стъкло-метал, стъкло-метал-стъкло, стъкло- метал и стъкло към стъкло и всички други комбинации на залепване метал-стъкло-керамика. Ние можем например да покрием керамичните компоненти с метално покритие, така че те да могат да бъдат здраво свързани с други компоненти в сглобката и да имат отлична способност за уплътняване. Имаме ноу-хауто за покриване на оптични влакна или захранващи канали с метал и запояването им или запояването им към корпусите, така че да не преминават или изтичат газове в корпусите. Поради това те се използват за производство на електронни кутии за капсулиране на чувствителни устройства и защитата им от външната атмосфера. Освен техните отлични характеристики на уплътняване, други свойства като коефициент на топлинно разширение, устойчивост на деформация, неотделяне на газове, много дълъг живот, непроводим характер, топлоизолационни свойства, антистатично естество... и т.н. правят стъклените и керамичните материали избор за определени приложения. Информация за нашето съоръжение, произвеждащо керамични към метални фитинги, херметично запечатване, вакуумни захранващи канали, висок и свръхвисок вакуум и компоненти за контрол на течности може да бъде намерена тук:Брошура на завода за херметични компоненти