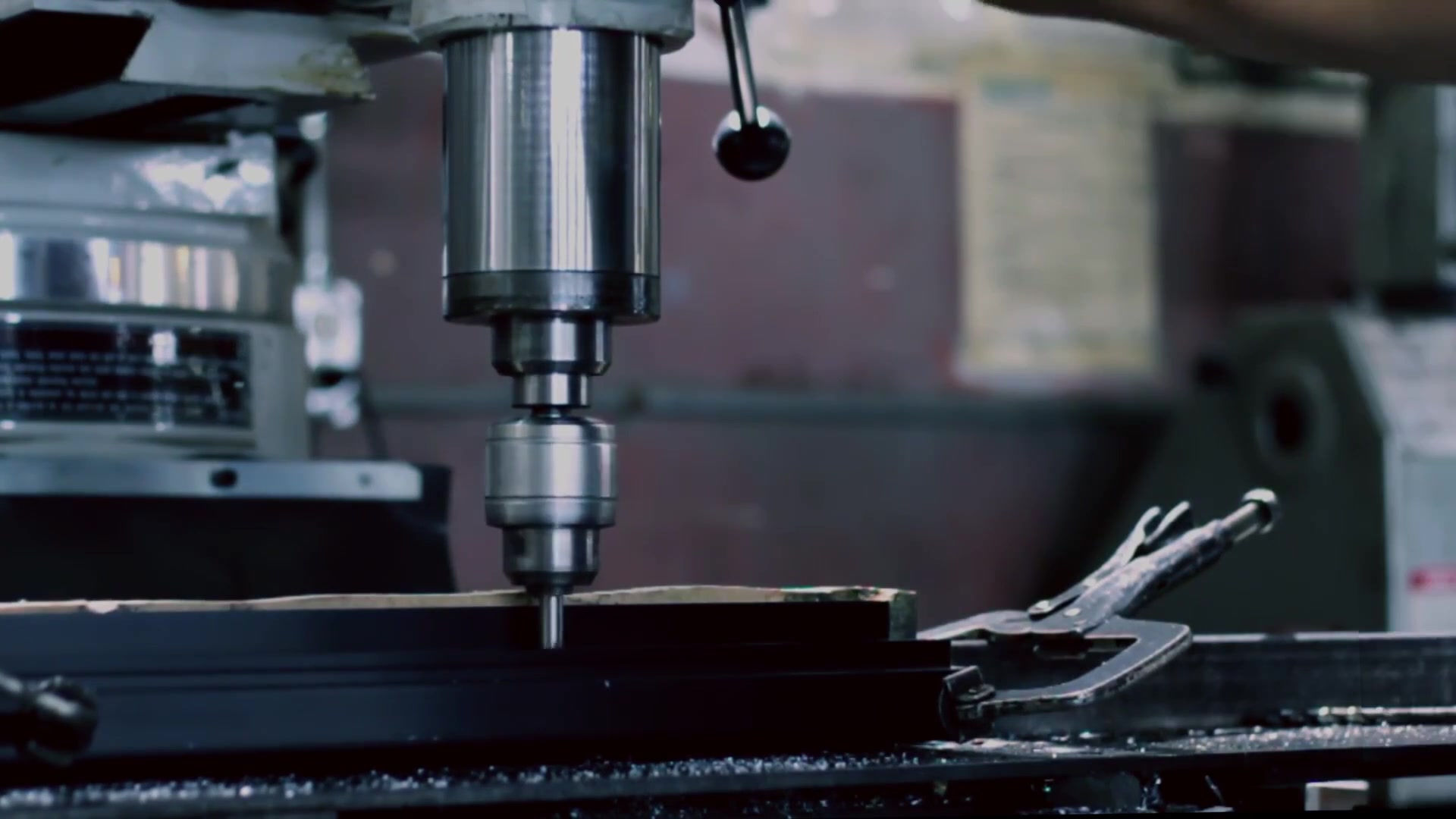
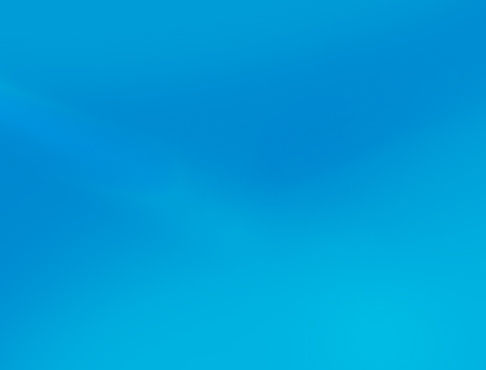
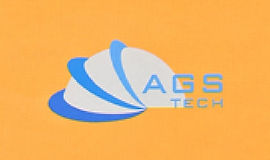
Глобален производител по поръчка, интегратор, консолидатор, аутсорсинг партньор за голямо разнообразие от продукти и услуги.
Ние сме вашият източник на едно гише за производство, производство, инженеринг, консолидация, интеграция, аутсорсинг на произведени по поръчка и готови продукти и услуги.
Изберете своя език
-
Производство по поръчка
-
Вътрешно и глобално договорно производство
-
Аутсорсинг на производство
-
Вътрешни и глобални доставки
-
Консолидация
-
Инженерна интеграция
-
Инженерни услуги
Типът процеси за МЕТАЛНО КОВАНЕ, които предлагаме, са гореща и студена матрица, отворена матрица и затворена матрица, матрица за отпечатване и изковки без флаш, cogging, запълване, кантиране и прецизно коване, почти мрежова форма, заглавие , щанцоване, изковаване, метално фрезоване, пресоване и валцуване, радиални и орбитални и пръстеновидни и изотермични изковки, монетосечене, занитване, коване на метални топки, пробиване на метал, оразмеряване, коване с висока енергийна скорост.
Нашите техники за ПРАХОВА МЕТАЛУРГИЯ и ОБРАБОТКА НА ПРАХ са прахово пресоване и синтероване, импрегниране, инфилтрация, горещо и студено изостатично пресоване, леене под налягане на метал, уплътняване на руло, валцуване на прах, екструзия на прах, синтероване в насипно състояние, искрово синтероване, горещо пресоване.
Препоръчваме ви да щракнете тук, за
ИЗТЕГЛЕТЕ нашите схематични илюстрации на процеси на коване от AGS-TECH Inc.
ИЗТЕГЛЕТЕ нашите схематични илюстрации на процеси в праховата металургия от AGS-TECH Inc.
Тези файлове за изтегляне със снимки и скици ще ви помогнат да разберете по-добре информацията, която ви предоставяме по-долу.
При коването на метал се прилагат сили на натиск и материалът се деформира и се получава желаната форма. Най-разпространените ковани материали в индустрията са желязо и стомана, но много други като алуминий, мед, титан, магнезий също са широко ковани. Кованите метални части имат подобрена зърнеста структура в допълнение към запечатаните пукнатини и затворените празни пространства, като по този начин здравината на частите, получени чрез този процес, е по-висока. Коването произвежда части, които са значително по-здрави за теглото си от частите, направени чрез леене или машинна обработка. Тъй като кованите части се оформят, като накарат метала да придобие крайната си форма, металът придобива насочена зърнеста структура, която отчита превъзходната здравина на частите. С други думи, частите, получени чрез процес на коване, показват по-добри механични свойства в сравнение с обикновените отлети или машинно обработени части. Теглото на металните изковки може да варира от малки леки части до стотици хиляди паунда. Ние произвеждаме изковки предимно за механично взискателни приложения, където се прилагат високи напрежения върху части като автомобилни части, зъбни колела, работни инструменти, ръчни инструменти, турбинни валове, мотоциклетни съоръжения. Тъй като разходите за инструментална екипировка и настройка са сравнително високи, ние препоръчваме този производствен процес само за голям обем производство и за малки обеми, но с висока стойност на критични компоненти, като например аерокосмически колесник. Освен разходите за инструментална екипировка, времето за производство на големи количества ковани части може да бъде по-дълго в сравнение с някои прости машинно обработени части, но техниката е от решаващо значение за части, които изискват изключителна здравина като болтове, гайки, специално приложение крепежни елементи, части за автомобили, мотокари, кранове.
• ГОРЕЩО ЩАМПОВАНЕ и СТУДЕНО КОВАНЕ: Горещото щамповане, както подсказва името, се извършва при високи температури, следователно пластичността е висока, а якостта на материала ниска. Това улеснява лесното деформиране и коване. Напротив, студеното коване се извършва при по-ниски температури и изисква по-високи сили, което води до втвърдяване на деформация, по-добро покритие на повърхността и точност на произведените части.
• ОТВОРЕНО КОВАНЕ НА МАТРИЦА и ОТПЕЧАНОВАНЕ НА МАТРИЦА: При коване с отворена матрица матриците не ограничават компресирания материал, докато при коване с отпечатъчна матрица кухините в матриците ограничават потока на материала, докато той се изковава в желаната форма. UPSET FORGING или наричан също UPSETTING, който всъщност не е същият, но много подобен процес, е процес на отворена матрица, при който детайлът е притиснат между две плоски матрици и силата на натиск намалява височината му. Тъй като височината е reduced, ширината на работния детайл се увеличава. HEADING, процесът на изковаване с изкривяване включва цилиндрична заготовка, която е извита в края си и нейното напречно сечение се увеличава локално. В заглавието материалът се подава през матрицата, изковава се и след това се нарязва на дължина. Операцията е способна да произвежда големи количества крепежни елементи бързо. Предимно това е операция за студена обработка, защото се използва за изработване на краища на пирони, краища на винтове, гайки и болтове, където материалът трябва да бъде укрепен. Друг процес на отворена матрица е COGGING, при който детайлът се кове в серия от стъпки, като всяка стъпка води до компресия на материала и последващото движение на отворената матрица по дължината на детайла. На всяка стъпка дебелината се намалява, а дължината се увеличава с малко. Процесът прилича на нервен ученик, който гризе молива си през цялото време на малки стъпки. Процесът, наречен FULLERING, е друг отворен метод за коване на матрици, който често използваме като по-ранна стъпка за разпределяне на материала в детайла, преди да се извършат други операции по коване на метал. Използваме го, когато детайлът изисква няколко forging operations. По време на операцията матрицата с изпъкнали повърхности се деформира и предизвиква изтичане на метал от двете страни. Подобен процес на фулиране, EDGING от друга страна включва отворена матрица с вдлъбнати повърхности за деформиране на обработвания детайл. Кантирането също е подготвителен процес за последващи операции по коване, което кара материала да тече от двете страни в зона в центъра. ОТПЕЧАТЪЧНО КОВАНЕ или ЗАТВОРЕНО КОВАНЕ, както се нарича, използва матрица/форма, която компресира материала и ограничава потока му вътре в себе си. Матрицата се затваря и материалът приема формата на кухината на матрицата/формата. ПРЕЦИЗНОТО КОВАНЕ, процес, изискващ специално оборудване и матрица, произвежда части без или с много малко пламване. С други думи, частите ще имат почти крайни размери. При този процес добре контролирано количество материал се вкарва внимателно и позиционира във формата. Ние използваме този метод за сложни форми с тънки профили, малки допуски и ъгли на наклон и когато количествата са достатъчно големи, за да оправдаят разходите за матрица и оборудване.
• КОВАНЕ БЕЗ ФЛАШ: Заготовката се поставя в матрицата по такъв начин, че никакъв материал да не може да изтече от кухината, за да образува флаш. Следователно не е необходимо нежелано изрязване на светкавица. Това е процес на прецизно коване и следователно изисква строг контрол на количеството използван материал.
• МЕТАЛНО ЩАБОВАНЕ или РАДИАЛНО КОВАНЕ: Заготовката се въздейства периферно от матрица и се изковава. Дорник може също да се използва за изковаване на вътрешната геометрия на работния детайл. При операцията по щамповане детайлът обикновено получава няколко удара в секунда. Типичните артикули, произведени чрез щанцоване, са инструменти със заострен връх, заострени пръти, отвертки.
• ПРОБИВАНЕ НА МЕТАЛ: Използваме тази операция често като допълнителна операция при производството на части. Създава се дупка или кухина с пробиване върху повърхността на работния детайл, без да се пробие през нея. Моля, имайте предвид, че пробиването е различно от пробиването, което води до проходен отвор.
• ФРЕЗОВАНЕ: Щанс с желаната геометрия се притиска в детайла и създава кухина с желаната форма. Ние наричаме този пунш HOB. Операцията включва високо налягане и се извършва на студено. В резултат на това материалът е студено обработен и закален. Следователно този процес е много подходящ за производство на форми, матрици и кухини за други производствени процеси. След като плочата е произведена, човек може лесно да произвежда много еднакви кухини, без да е необходимо да ги обработва една по една.
• КОВАНЕ НА РОЛКИ или ФОРМОВАНЕ НА РОЛКИ: Използват се две противоположни ролки за оформяне на металната част. Работният детайл се подава в ролките, ролките се завъртат и издърпват детайла в процепа, след това детайлът се подава през набраздената част на ролките и силите на натиск придават на материала желаната форма. Това не е процес на валцуване, а процес на коване, защото е по-скоро дискретна, отколкото непрекъсната операция. Геометрията на горичките на ролките изковава материала до необходимата форма и геометрия. Изпълнява се горещо. Тъй като е процес на коване, той произвежда части с изключителни механични свойства и затова го използваме за производство на автомобилни части като валове, които трябва да имат изключителна издръжливост в тежки работни среди.
• ОРБИТАЛНО КОВАНЕ: Заготовката се поставя в кухината на матрицата за коване и се изковава от горна матрица, която се движи по орбитална траектория, докато се върти около наклонена ос. При всяко завъртане горната матрица завършва упражняването на натиск върху целия детайл. Чрез повтаряне на тези обороти няколко пъти се извършва достатъчно коване. Предимствата на тази производствена техника са нейният нисък шум при работа и по-ниските необходими усилия. С други думи, с малки сили човек може да завърти тежка матрица около ос, за да приложи голям натиск върху част от обработвания детайл, който е в контакт с матрицата. Дискови или конусовидни части понякога са подходящи за този процес.
• КОВАНЕ НА ПРЪСТЕН: Ние често използваме за производство на безшевни пръстени. Материалът се нарязва на дължина, разгъва се и след това се пробива докрай, за да се създаде централен отвор. След това се поставя върху дорник и ковашка матрица го изчуква отгоре, докато пръстенът се върти бавно, докато се получат желаните размери.
• ЗАНИТОВВАНЕ: Общ процес за съединяване на части, започва с права метална част, вкарана в предварително направени отвори през частите. След това двата края на металната част се изковават чрез притискане на съединението между горната и долната матрица.
• КОНЕНЕ: Друг популярен процес, извършван чрез механична преса, упражняваща големи сили на кратко разстояние. Името „сечене“ идва от фините детайли, които са изковани върху повърхностите на металните монети. Това е най-вече довършителен процес за продукт, при който се получават фини детайли върху повърхностите в резултат на голямата сила, приложена от матрицата, която пренася тези детайли върху обработвания детайл.
• КОВАНЕ НА МЕТАЛНИ ТОПЧЕТА: Продукти като сачмени лагери изискват висококачествени прецизно произведени метални топки. В една техника, наречена КРИВО ВЪРТАЛЯНЕ, ние използваме две срещуположни ролки, които непрекъснато се въртят, докато материалът непрекъснато се подава в ролките. В единия край на двете ролки метални сфери се изхвърлят като продукт. Вторият метод за коване на метални топки е използването на матрица, която изстисква материалната маса, поставена между тях, приемайки сферичната форма на кухината на формата. Често произведените топки изискват някои допълнителни стъпки като довършителни работи и полиране, за да се превърнат в висококачествен продукт.
• ИЗОТЕРМИЧНО КОВАНЕ / ГОРЕЩО КОВАНЕ: Скъп процес, извършван само когато съотношението полза/цена е оправдано. Процес на горещ работен процес, при който матрицата се нагрява до приблизително същата температура като детайла. Тъй като и матрицата, и работата са с приблизително еднаква температура, няма охлаждане и характеристиките на потока на метала са подобрени. Операцията е подходяща за супер сплави и материали с по-лоша ковакост и материали, чийто
механичните свойства са много чувствителни към малки температурни градиенти и промени.
• ОПРЕДЕЛЯНЕ НА МЕТАЛ: Това е студен довършителен процес. Материалният поток е неограничен във всички посоки с изключение на посоката, в която се прилага силата. В резултат на това се получава много добро покритие на повърхността и точни размери.
• ВИСОКО ЕНЕРГИЙНО КОВАНЕ: Техниката включва горна форма, прикрепена към рамото на бутало, което се избутва бързо, докато гориво-въздушната смес се запалва от свещ. Наподобява работата на буталата в автомобилен двигател. Формата удря обработвания детайл много бързо и след това се връща в първоначалната си позиция много бързо благодарение на обратното налягане. Произведението се изковава за няколко милисекунди и следователно няма време за изстиване на произведението. Това е полезно за трудни за изковаване части, които имат много чувствителни към температурата механични свойства. С други думи, процесът е толкова бърз, че детайлът се формира при постоянна температура през цялото време и няма да има температурни градиенти на интерфейсите на матрицата/работния детайл.
• При КОВАНЕТО, металът се набива между два съвпадащи стоманени блока със специални форми в тях, наречени матрици. Когато металът се изковава между матриците, той приема същата форма като формите в матрицата. Когато придобие окончателната си форма се изважда да се охлади. Този процес произвежда здрави части с прецизна форма, но изисква по-голяма инвестиция за специализираните матрици. Изкованото изковаване увеличава диаметъра на парче метал чрез сплескването му. Обикновено се използва за изработка на малки части, особено за оформяне на глави на крепежни елементи като болтове и пирони.
• ПРАХОВА МЕТАЛУРГИЯ / ОБРАБОТКА НА ПРАХ: Както подсказва името, тя включва производствени процеси за изработване на твърди части с определени геометрии и форми от прахове. Ако за тази цел се използват метални прахове, това е сферата на праховата металургия, а ако се използват неметални прахове, това е прахова обработка. Твърдите части се произвеждат от прахове чрез пресоване и синтероване.
ПРЕСОВАНЕТО НА ПРАХ се използва за уплътняване на прахове в желани форми. Първо, първичният материал е физически прахообразен, разделяйки го на много малки отделни частици. Праховата смес се напълва в матрицата и щанцата се придвижва към праха и го уплътнява в желаната форма. Най-често се извършва при стайна температура, при пресоване на прах се получава твърда част и се нарича зелен компакт. Свързващите вещества и лубрикантите обикновено се използват за подобряване на компактността. Ние сме способни да формоваме с прахова преса с помощта на хидравлични преси с капацитет няколко хиляди тона. Също така имаме преси с двойно действие с противоположни горни и долни щанци, както и преси с множество действия за изключително сложни геометрии на детайли. Уеднаквяването, което е важно предизвикателство за много предприятия за прахова металургия / прахова обработка, не е голям проблем за AGS-TECH поради нашия богат опит в производството на такива части по поръчка в продължение на много години. Дори и с по-дебели части, където еднаквостта представлява предизвикателство, ние успяхме. Ако се ангажираме с вашия проект, ние ще направим вашите части. Ако видим потенциални рискове, ще ви информираме in
предварително.
СИНТЕРОВАНЕТО НА ПРАХ, което е втората стъпка, включва повишаване на температурата до определена степен и поддържане на температурата на това ниво за определено време, така че частиците на праха в пресованата част да могат да се свържат заедно. Това води до много по-здрави връзки и укрепване на обработвания детайл. Агломерирането се извършва близо до температурата на топене на праха. По време на синтероването ще настъпи свиване, силата на материала, плътността, пластичността, топлопроводимостта, електрическата проводимост се увеличават. Разполагаме с периодични и непрекъснати пещи за синтероване. Една от възможностите ни е регулиране нивото на порьозност на детайлите, които произвеждаме. Например ние сме в състояние да произвеждаме метални филтри, като поддържаме частите порести до известна степен.
Използвайки техника, наречена ИМПРЕГНАЦИЯ, ние запълваме порите в метала с течност като масло. Ние произвеждаме например импрегнирани с масло лагери, които са самосмазващи се. В процеса на ИНФИЛТРАЦИЯ ние запълваме порите на метала с друг метал с по-ниска точка на топене от основния материал. Сместа се нагрява до температура между температурите на топене на двата метала. В резултат на това могат да се получат някои специални свойства. Ние също така често извършваме вторични операции като машинна обработка и коване на части, произведени на прах, когато трябва да се получат специални характеристики или свойства или когато частта може да бъде произведена с по-малко стъпки на процеса.
ИЗОСТАТИЧНО ПРЕСОВАНЕ: В този процес се използва налягане на течността за уплътняване на детайла. Металните прахове се поставят във форма, направена от запечатан гъвкав контейнер. При изостатичното пресоване налягането се прилага отвсякъде, за разлика от аксиалното налягане, наблюдавано при конвенционалното пресоване. Предимствата на изостатичното пресоване са еднаква плътност в частта, особено за по-големи или по-дебели части, превъзходни свойства. Неговият недостатък е дългите времена на цикъла и относително ниската геометрична точност. СТУДЕНОТО ИЗОСТАТИЧНО ПРЕСОВАНЕ се извършва при стайна температура и гъвкавата форма е изработена от гума, PVC или уретан или подобни материали. Течността, използвана за херметизиране и уплътняване, е масло или вода. Това следва конвенционалното синтероване на зелената преса. ГОРЕЩОТО ИЗОСТАТИЧНО ПРЕСОВАНЕ, от друга страна, се извършва при високи температури и материалът за формата е ламарина или керамика с достатъчно висока точка на топене, която издържа на температурите. Флуидът под налягане обикновено е инертен газ. Операциите по пресоване и синтероване се извършват на един етап. Порьозността е почти напълно елиминирана, получава се равномерна зърнеста структура. Предимството на горещото изостатично пресоване е, че може да произвежда части, сравними с комбинацията от леене и коване, като същевременно прави възможно използването на материали, които не са подходящи за леене и коване. Недостатък на горещото изостатично пресоване е неговото дълго време на цикъл и следователно цената. Подходящ е за критични части с малък обем.
ИНЖЕКТИРАНЕ НА МЕТАЛ: Много подходящ процес за производство на сложни части с тънки стени и детайлна геометрия. Най-подходящ за по-малки части. Праховете и полимерното свързващо вещество се смесват, нагряват се и се инжектират във форма. Полимерното свързващо вещество покрива повърхностите на прахообразните частици. След формоване, свързващото вещество се отстранява чрез нагряване при ниска температура или чрез разтворител.
УТЪПНЯВАНЕ НА РОЛКИ/ВАЛЦАНЕ НА ПРАХ: Праховете се използват за производство на непрекъснати ленти или листове. Прахът се подава от захранващо устройство и се уплътнява от две въртящи се ролки в лист или ленти. Операцията се извършва на студено. Листът се пренася в пещ за синтероване. Процесът на синтероване може да се повтори втори път.
ЕКСТРУЗИЯ НА ПРАХ: Части с големи съотношения на дължина към диаметър се произвеждат чрез екструдиране на тънък метален контейнер с прах.
РАЗХЛАБЕНО СИНТЕРОВАНЕ: Както подсказва името, това е метод за уплътняване и синтероване без налягане, подходящ за производство на много порести части като метални филтри. Прахът се подава в кухината на формата без уплътняване.
РАЗХЛАБЕНО СИНТЕРОВАНЕ: Както подсказва името, това е метод за уплътняване и синтероване без налягане, подходящ за производство на много порести части като метални филтри. Прахът се подава в кухината на формата без уплътняване.
ИСКРОВО СИНТЕРОВАНЕ: Прахът се компресира във формата от два противоположни щанца и електрически ток с голяма мощност се прилага към щанцата и преминава през компактния прах, поставен между тях. Силният ток изгаря повърхностните филми от прахообразните частици и ги синтерува с генерираната топлина. Процесът е бърз, защото топлината не се прилага отвън, а вместо това се генерира от матрицата.
ГОРЕЩО ПРЕСОВАНЕ: Праховете се пресоват и синтероват в една стъпка във форма, която може да издържи на високи температури. Докато матрицата се уплътнява, топлината на праха се прилага към нея. Добрата точност и механични свойства, постигнати чрез този метод, го правят привлекателна опция. Дори огнеупорни метали могат да бъдат обработени с помощта на материали за формоване като графит.