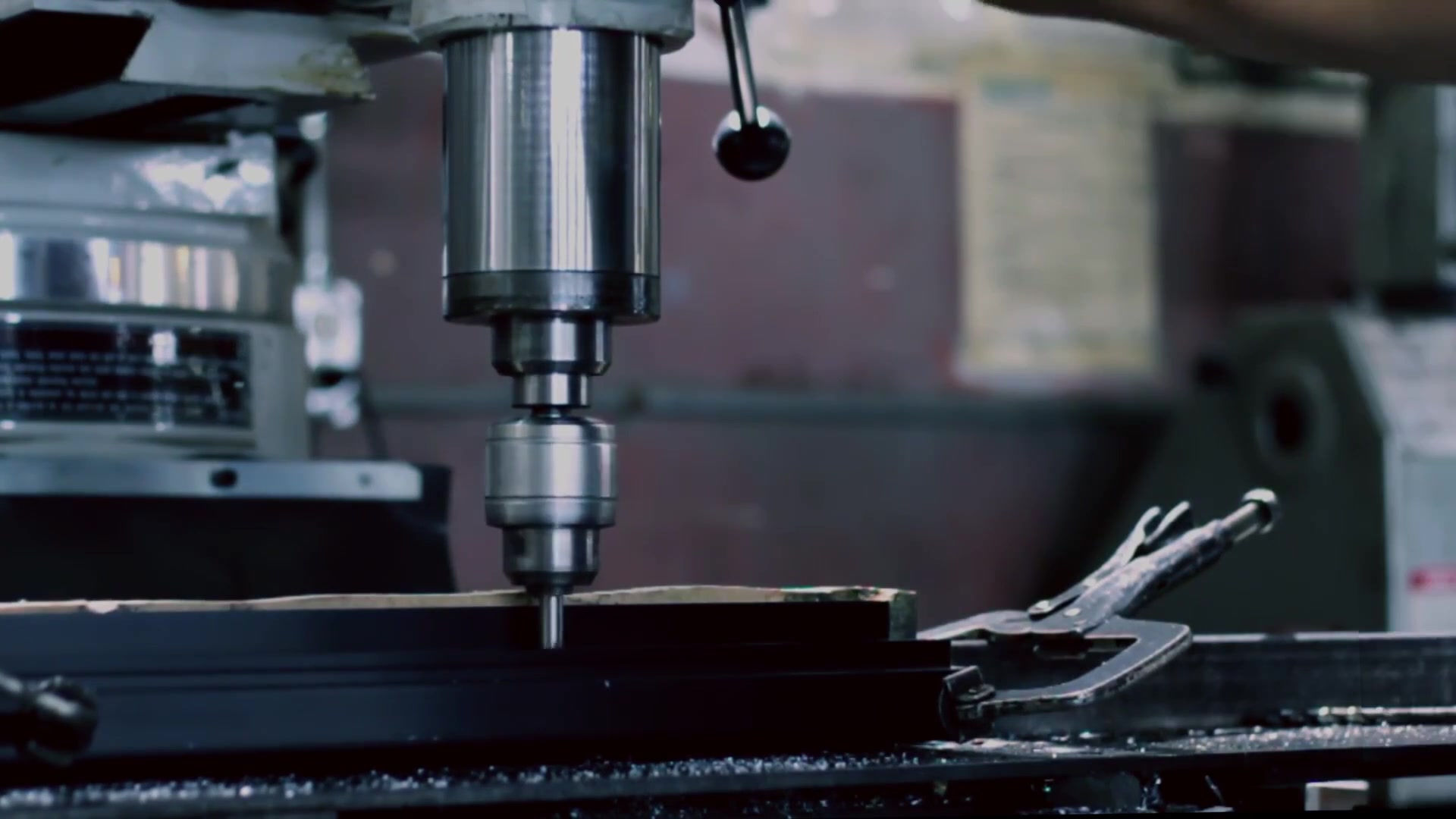
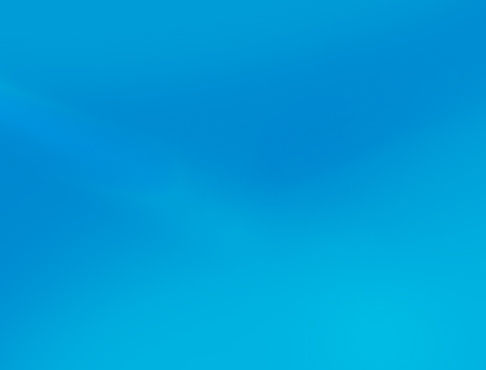
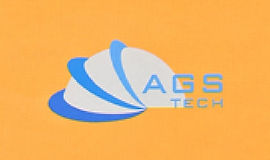
Глобален производител по поръчка, интегратор, консолидатор, аутсорсинг партньор за голямо разнообразие от продукти и услуги.
Ние сме вашият източник на едно гише за производство, производство, инженеринг, консолидация, интеграция, аутсорсинг на произведени по поръчка и готови продукти и услуги.
Изберете своя език
-
Производство по поръчка
-
Вътрешно и глобално договорно производство
-
Аутсорсинг на производство
-
Вътрешни и глобални доставки
-
Консолидация
-
Инженерна интеграция
-
Инженерни услуги
Производство и производство на микроелектроника и полупроводници
Много от нашите техники и процеси за нанопроизводство, микропроизводство и мезопроизводство, обяснени в другите менюта, могат да се използват за MICROELECTRONICS MANUFACTURING too. Въпреки това, поради значението на микроелектрониката в нашите продукти, ние ще се концентрираме върху конкретните приложения на тези процеси тук. Процесите, свързани с микроелектрониката, също се наричат широко като SEMICONDUCTOR FABRICATION processes. Нашите услуги за проектиране и производство на полупроводниково инженерство включват:
- FPGA дизайн, разработка и програмиране на платка
- Микроелектронни леярски услуги: Проектиране, създаване на прототипи и производство, услуги на трети страни
- Подготовка на полупроводникови пластини: Нарязване, обратно шлайфане, изтъняване, поставяне на мерна мрежа, сортиране на матрицата, избор и поставяне, проверка
- Микроелектронен дизайн и изработка на опаковката: Както стандартен, така и персонализиран дизайн и изработка
- Сглобяване и опаковане и тест на полупроводникови интегрални схеми: Свързване на матрици, проводници и чипове, капсулиране, сглобяване, маркиране и брандиране
- Оловни рамки за полупроводникови устройства: Както стандартен, така и персонализиран дизайн и производство
- Проектиране и изработка на радиатори за микроелектроника: както готови, така и персонализирани дизайн и изработка
- Дизайн и изработка на сензори и задвижващи механизми: Както стандартен, така и персонализиран дизайн и изработка
- Проектиране и производство на оптоелектронни и фотонни схеми
Нека разгледаме по-подробно технологиите за производство и тестване на микроелектроника и полупроводници, за да можете да разберете по-добре услугите и продуктите, които предлагаме.
Дизайн и разработка на FPGA платка и програмиране: Програмируемите на място гейт масиви (FPGA) са препрограмируеми силициеви чипове. Противно на процесорите, които намирате в персоналните компютри, програмирането на FPGA пренасочва самия чип, за да реализира функционалността на потребителя, вместо да изпълнява софтуерно приложение. Използвайки предварително изградени логически блокове и програмируеми ресурси за маршрутизиране, FPGA чиповете могат да бъдат конфигурирани да реализират персонализирана хардуерна функционалност без използване на макетна платка и поялник. Цифровите изчислителни задачи се изпълняват в софтуер и се компилират до конфигурационен файл или битов поток, който съдържа информация за това как компонентите трябва да бъдат свързани заедно. FPGA могат да се използват за прилагане на всяка логическа функция, която ASIC може да изпълнява и са напълно преконфигурируеми и могат да получат напълно различна „личност“ чрез прекомпилиране на различна конфигурация на верига. FPGA съчетават най-добрите части от специфични за приложения интегрални схеми (ASIC) и системи, базирани на процесори. Тези предимства включват следното:
• По-бързи I/O времена за реакция и специализирана функционалност
• Превишаване на изчислителната мощност на цифровите сигнални процесори (DSP)
• Бързо създаване на прототипи и проверка без процеса на производство на персонализирани ASIC
• Внедряване на персонализирана функционалност с надеждността на специален детерминистичен хардуер
• Надграждане на място, което елиминира разходите за препроектиране и поддръжка по поръчка на ASIC
FPGA осигуряват скорост и надеждност, без да изискват големи обеми, за да оправдаят големите предварителни разходи за персонализиран дизайн на ASIC. Препрограмируемият силикон също има същата гъвкавост като софтуер, работещ на системи, базирани на процесори, и не е ограничен от броя на наличните процесорни ядра. За разлика от процесорите, FPGA са наистина паралелни по природа, така че различните операции на обработка не трябва да се конкурират за едни и същи ресурси. Всяка независима задача за обработка е присвоена на специална секция на чипа и може да функционира автономно без влияние от други логически блокове. В резултат на това производителността на една част от приложението не се влияе, когато се добави повече обработка. Някои FPGA имат аналогови функции в допълнение към цифровите функции. Някои често срещани аналогови характеристики са програмируема скорост на нарастване и сила на задвижване на всеки изходен щифт, което позволява на инженера да зададе бавни скорости на леко натоварени щифтове, които иначе биха звънели или се свързвали неприемливо, и да зададе по-силни, по-бързи скорости на силно натоварени щифтове при висока скорост канали, които иначе биха работили твърде бавно. Друга относително често срещана аналогова характеристика са диференциалните компаратори на входни щифтове, проектирани да бъдат свързани към диференциални сигнални канали. Някои FPGA със смесен сигнал имат интегрирани периферни аналогово-цифрови преобразуватели (ADC) и цифрово-аналогови преобразуватели (DAC) с блокове за обработка на аналогов сигнал, които им позволяват да работят като система върху чип.
Накратко, първите 5 предимства на FPGA чиповете са:
1. Добро представяне
2. Кратко време за пускане на пазара
3. Ниска цена
4. Висока надеждност
5. Възможност за дългосрочна поддръжка
Добра производителност – Със своята способност за приспособяване към паралелна обработка, FPGA имат по-добра изчислителна мощност от процесорите за цифрови сигнали (DSP) и не изискват последователно изпълнение като DSP и могат да постигат повече за един такт. Контролирането на входове и изходи (I/O) на хардуерно ниво осигурява по-бързи времена за реакция и специализирана функционалност, за да отговаря точно на изискванията на приложението.
Кратко време за пускане на пазара - FPGA предлагат гъвкавост и възможности за бързо създаване на прототипи и по този начин по-кратко време за пускане на пазара. Нашите клиенти могат да тестват идея или концепция и да я проверят в хардуера, без да преминават през дългия и скъп процес на производство на персонализиран ASIC дизайн. Можем да внедрим постепенни промени и да повторим дизайна на FPGA в рамките на часове вместо седмици. Предлага се и готов търговски хардуер с различни типове I/O, които вече са свързани към програмируем от потребителя FPGA чип. Нарастващата наличност на софтуерни инструменти от високо ниво предлага ценни IP ядра (предварително изградени функции) за разширен контрол и обработка на сигнали.
Ниска цена – Еднократните инженерни разходи (NRE) за персонализирани дизайни на ASIC надвишават тези на базираните на FPGA хардуерни решения. Голямата първоначална инвестиция в ASIC може да бъде оправдана за OEM производителите, произвеждащи много чипове годишно, но много крайни потребители се нуждаят от персонализирана хардуерна функционалност за многото системи в процес на разработка. Нашата програмируема силициева FPGA ви предлага нещо без разходи за производство или дълги срокове за сглобяване. Системните изисквания често се променят с времето и разходите за извършване на постепенни промени в дизайна на FPGA са незначителни в сравнение с големите разходи за повторно завъртане на ASIC.
Висока надеждност - Софтуерните инструменти осигуряват среда за програмиране, а FPGA схемите са истинска реализация на изпълнението на програмата. Системите, базирани на процесори, обикновено включват множество слоеве на абстракция, за да помогнат при планирането на задачи и да споделят ресурси между множество процеси. Слоят на драйвера контролира хардуерните ресурси, а операционната система управлява паметта и честотната лента на процесора. За всяко дадено процесорно ядро само една инструкция може да се изпълни в даден момент и системите, базирани на процесор, непрекъснато са изложени на риск критични за времето задачи да се изпреварват една друга. FPGA, не използват операционни системи, създават минимални проблеми с надеждността с истинското си паралелно изпълнение и детерминистичен хардуер, предназначен за всяка задача.
Възможност за дългосрочна поддръжка - FPGA чиповете могат да се надграждат на място и не изискват време и разходи, свързани с препроектирането на ASIC. Цифровите комуникационни протоколи, например, имат спецификации, които могат да се променят с времето, а базираните на ASIC интерфейси могат да причинят предизвикателства при поддръжката и съвместимостта напред. Напротив, реконфигурируемите FPGA чипове могат да се справят с потенциално необходими бъдещи модификации. С напредването на продуктите и системите нашите клиенти могат да направят функционални подобрения, без да губят време за препроектиране на хардуера и модифициране на оформлението на платката.
Леярски услуги за микроелектроника: Нашите леярски услуги за микроелектроника включват проектиране, създаване на прототипи и производство, услуги на трети страни. Ние предоставяме на нашите клиенти съдействие по време на целия цикъл на разработка на продукта - от поддръжка на дизайна до поддръжка на прототипи и производство на полупроводникови чипове. Нашата цел в услугите за поддръжка на проектиране е да позволим правилния подход за първи път за дизайни на полупроводникови устройства с цифрови, аналогови и смесени сигнали. Налични са например специфични инструменти за симулация на MEMS. Фабриките, които могат да работят с 6 и 8 инчови пластини за интегрирани CMOS и MEMS, са на ваше разположение. Ние предлагаме на нашите клиенти поддръжка за проектиране за всички основни платформи за автоматизация на електронното проектиране (EDA), като доставяме правилни модели, комплекти за проектиране на процеси (PDK), аналогови и цифрови библиотеки и поддръжка за проектиране за производство (DFM). Ние предлагаме две опции за създаване на прототипи за всички технологии: услугата Multi Product Wafer (MPW), при която няколко устройства се обработват паралелно на една пластина, и услугата Multi Level Mask (MLM) с четири нива на маска, начертани върху една и съща мрежа. Те са по-икономични от пълния комплект маски. Услугата MLM е много гъвкава в сравнение с фиксираните дати на услугата MPW. Компаниите могат да предпочетат аутсорсинг на полупроводникови продукти пред леярна за микроелектроника поради редица причини, включително необходимостта от втори източник, използване на вътрешни ресурси за други продукти и услуги, желание да се изгради фабрично и да се намали рискът и тежестта от управлението на фабрика за полупроводници… и т.н. AGS-TECH предлага процеси за производство на микроелектроника с отворена платформа, които могат да бъдат намалени за малки тиражи на пластини, както и за масово производство. При определени обстоятелства вашите съществуващи инструменти за производство на микроелектроника или MEMS или пълни комплекти инструменти могат да бъдат прехвърлени като изпратени инструменти или продадени инструменти от вашата фабрика в нашия фабричен сайт или вашите съществуващи микроелектроника и MEMS продукти могат да бъдат преработени с помощта на технологии за процес на отворена платформа и пренесени към процес, достъпен в нашата фабрика. Това е по-бързо и по-икономично от трансфер на технология по поръчка. При желание обаче съществуващите производствени процеси на микроелектроника/MEMS на клиента могат да бъдат прехвърлени.
Подготовка на полупроводникови пластини: При желание от страна на клиентите, след като пластините са микропроизведени, ние извършваме нарязване, обратно шлайфане, изтъняване, поставяне на решетка, сортиране на матрицата, избор и поставяне, операции по проверка на полупроводникови пластини. Обработката на полупроводникови пластини включва метрология между различните етапи на обработка. Например, методите за изпитване на тънък слой, базирани на елипсометрия или рефлектометрия, се използват за строг контрол на дебелината на оксида на затвора, както и на дебелината, индекса на пречупване и коефициента на екстинкция на фоторезиста и други покрития. Използваме оборудване за тестване на полупроводникови пластини, за да проверим дали пластините не са били повредени от предишни стъпки на обработка до тестването. След като предните процеси са завършени, полупроводниковите микроелектронни устройства се подлагат на различни електрически тестове, за да се определи дали функционират правилно. Ние наричаме съотношението на микроелектронните устройства на пластината, за които е установено, че работят правилно, като „добив“. Тестването на микроелектронни чипове върху пластината се извършва с електронен тестер, който притиска малки сонди към полупроводниковия чип. Автоматизираната машина маркира всеки повреден микроелектронен чип с капка багрило. Данните от теста на вафли се записват в централна компютърна база данни и полупроводниковите чипове се сортират във виртуални контейнери според предварително определени тестови граници. Получените данни за групиране могат да бъдат изобразени на графика или регистрирани върху карта на вафла, за да се проследят производствените дефекти и да се маркират лоши чипове. Тази карта може да се използва и по време на сглобяване и опаковане на вафли. При окончателното тестване микроелектронните чипове се тестват отново след опаковането, тъй като свързващите проводници може да липсват или аналоговата производителност може да бъде променена от опаковката. След като полупроводниковата пластина бъде тествана, тя обикновено се намалява по дебелина, преди пластината да бъде набраздена и след това да се раздели на отделни матрици. Този процес се нарича разделяне на полупроводникови пластини. Използваме автоматизирани машини за вземане и поставяне, специално произведени за микроелектронната индустрия, за да сортираме добрите и лошите полупроводникови матрици. Опаковани са само добрите, немаркирани полупроводникови чипове. След това, в процеса на опаковане на микроелектроника от пластмаса или керамика, ние монтираме матрицата на полупроводника, свързваме подложките на матрицата към щифтовете на опаковката и запечатваме матрицата. Малки златни жици се използват за свързване на подложките към щифтовете с помощта на автоматизирани машини. Chip scale package (CSP) е друга технология за пакетиране на микроелектроника. Пластмасов двоен редов пакет (DIP), както повечето пакети, е многократно по-голям от действителния полупроводников матрица, поставен вътре, докато CSP чиповете са почти с размера на микроелектронната матрица; и CSP може да бъде конструиран за всяка матрица, преди полупроводниковата пластина да бъде нарязана на кубчета. Пакетираните микроелектронни чипове се тестват отново, за да се уверите, че не са повредени по време на опаковането и че процесът на свързване между матрицата и щифта е завършен правилно. С помощта на лазери след това гравираме имената и номерата на чиповете върху опаковката.
Дизайн и производство на микроелектронни пакети: Ние предлагаме както стандартен, така и персонализиран дизайн и производство на микроелектронни пакети. Като част от тази услуга се извършва и моделиране и симулация на микроелектронни пакети. Моделирането и симулацията гарантират виртуално проектиране на експерименти (DoE) за постигане на оптимално решение, вместо тестване на пакети на място. Това намалява разходите и времето за производство, особено за разработване на нови продукти в микроелектрониката. Тази работа също така ни дава възможност да обясним на нашите клиенти как сглобяването, надеждността и тестването ще повлияят на техните микроелектронни продукти. Основната цел на микроелектронните опаковки е да се проектира електронна система, която ще удовлетвори изискванията за конкретно приложение на разумна цена. Поради многото налични опции за свързване и разполагане на микроелектронна система, изборът на технология за опаковане за дадено приложение се нуждае от експертна оценка. Критериите за избор на пакети за микроелектроника могат да включват някои от следните технологични драйвери:
- Възможност за свързване
-Доходност
-Разходи
- Свойства за разсейване на топлината
- Електромагнитно екраниране
- Механична издръжливост
-Надеждност
Тези съображения за проектиране на микроелектронни пакети засягат скоростта, функционалността, температурите на свързване, обема, теглото и др. Основната цел е да се избере най-рентабилната, но надеждна технология за взаимно свързване. Ние използваме усъвършенствани методи за анализ и софтуер за проектиране на пакети за микроелектроника. Микроелектронното опаковане се занимава с проектирането на методи за производство на взаимосвързани миниатюрни електронни системи и надеждността на тези системи. По-конкретно, опаковането на микроелектрониката включва маршрутизиране на сигнали, като същевременно се поддържа целостта на сигнала, разпределяне на земята и захранването към полупроводниковите интегрални схеми, разпръскване на разсейваната топлина, като същевременно се поддържа структурна и материална цялост, и защита на веригата от опасности за околната среда. Като цяло, методите за опаковане на микроелектронни интегрални схеми включват използването на PWB с конектори, които осигуряват входно-изходните данни в реалния свят на електронна верига. Традиционните подходи за опаковане на микроелектроника включват използването на единични опаковки. Основното предимство на пакета с един чип е възможността за пълно тестване на микроелектронната ИС преди свързването й към основния субстрат. Такива опаковани полупроводникови устройства са или монтирани през отвора, или повърхностно монтирани към PWB. Повърхностно монтираните микроелектронни пакети не изискват отвори за преминаване през цялата платка. Вместо това повърхностно монтираните микроелектронни компоненти могат да бъдат запоени към двете страни на PWB, което позволява по-висока плътност на веригата. Този подход се нарича технология за повърхностен монтаж (SMT). Добавянето на пакети в стил площен масив, като масиви с сферична решетка (BGA) и пакети с мащаб на чип (CSP), прави SMT конкурентноспособен с технологиите за опаковане на полупроводникова микроелектроника с най-висока плътност. По-новата технология за опаковане включва прикрепването на повече от едно полупроводниково устройство към субстрат за взаимно свързване с висока плътност, който след това се монтира в голям пакет, осигуряващ както I/O щифтове, така и защита на околната среда. Тази многочипова модулна (MCM) технология се характеризира допълнително с технологиите на субстрата, използвани за свързване на свързаните интегрални схеми. MCM-D представлява отложен тънък филм от метал и многослойни диелектрици. MCM-D субстратите имат най-високата плътност на окабеляването от всички MCM технологии благодарение на усъвършенстваните технологии за обработка на полупроводници. MCM-C се отнася до многослойни „керамични“ субстрати, изпечени от подредени редуващи се слоеве от екранирани метални мастила и неизпечени керамични листове. С помощта на MCM-C получаваме умерено плътен капацитет на окабеляване. MCM-L се отнася до многослойни субстрати, направени от подредени, метализирани PWB „ламинати“, които са индивидуално шарени и след това ламинирани. Преди беше технология за свързване с ниска плътност, но сега MCM-L бързо се доближава до плътността на технологиите за опаковане на микроелектроника MCM-C и MCM-D. Технологията за опаковане на микроелектроника с директно прикрепване на чип (DCA) или чип-на-борда (COB) включва монтиране на микроелектронните ИС директно към PWB. Пластмасов капсулант, който е "глобиран" върху голата IC и след това се втвърдява, осигурява защита на околната среда. Микроелектронните интегрални схеми могат да бъдат свързани помежду си към субстрата, като се използват или флип-чип, или методи за свързване с проводници. DCA технологията е особено икономична за системи, които са ограничени до 10 или по-малко полупроводникови ИС, тъй като по-големият брой чипове може да повлияе на производителността на системата и DCA модулите могат да бъдат трудни за преработка. Предимство, общо за опциите за опаковане на DCA и MCM, е премахването на нивото на взаимно свързване на пакета на полупроводникови IC, което позволява по-голяма близост (по-кратки закъснения при предаване на сигнала) и намалена индуктивност на проводника. Основният недостатък и на двата метода е трудността при закупуване на напълно тествани микроелектронни интегрални схеми. Други недостатъци на технологиите DCA и MCM-L включват лошо термично управление благодарение на ниската топлопроводимост на PWB ламинатите и слабия коефициент на топлинно разширение между матрицата на полупроводника и субстрата. Решаването на проблема с несъответствието на термичното разширение изисква междинен субстрат като молибден за матрица, свързана с тел, и епоксидна смола за запълване за матрица с обръщащ чип. Мултичиповият носещ модул (MCCM) съчетава всички положителни аспекти на DCA с MCM технологията. MCCM е просто малък MCM върху тънък метален носител, който може да бъде свързан или механично прикрепен към PWB. Металното дъно действа както като разсейвател на топлината, така и като междинно напрежение за MCM субстрата. MCCM има периферни проводници за свързване на проводници, запояване или свързване на пластини към PWB. Голите полупроводникови интегрални схеми са защитени с помощта на материал с топка. Когато се свържете с нас, ние ще обсъдим вашето приложение и изисквания, за да изберем най-добрата опция за опаковане на микроелектроника за вас.
Сглобяване и опаковане и тестване на полупроводникови интегрални схеми: Като част от нашите услуги за производство на микроелектроника ние предлагаме свързване на матрици, проводници и чипове, капсулиране, сглобяване, маркиране и брандиране, тестване. За да функционира полупроводников чип или интегрирана микроелектронна схема, тя трябва да бъде свързана към системата, която ще управлява или ще й предоставя инструкции. Сглобяването на микроелектронни интегрални схеми осигурява връзките за захранване и трансфер на информация между чипа и системата. Това се постига чрез свързване на микроелектронния чип към пакет или директно свързване към PCB за тези функции. Връзките между чипа и пакета или печатната платка (PCB) се осъществяват чрез свързване на кабели, сглобяване на чипа чрез отвор или обръщане. Ние сме лидер в индустрията в намирането на микроелектронни IC опаковъчни решения, за да отговорим на сложните изисквания на безжичните и интернет пазарите. Ние предлагаме хиляди различни пакетни формати и размери, вариращи от традиционни IC пакети за микроелектроника с водещи рамки за монтиране през дупки и повърхностен монтаж, до най-новите решения за скала на чипове (CSP) и сферична решетка (BGA), необходими при приложения с голям брой пинове и висока плътност . Голямо разнообразие от пакети се предлагат от склад, включително CABGA (Chip Array BGA), CQFP, CTBGA (Chip Array Thin Core BGA), CVBGA (Very Thin Chip Array BGA), Flip Chip, LCC, LGA, MQFP, PBGA, PDIP, PLCC, PoP - Package on Package, PoP TMV - Through Mold Via, SOIC / SOJ, SSOP, TQFP, TSOP, WLP (Wafer Level Package)…..и др. Свързването на проводници с помощта на мед, сребро или злато е сред популярните в микроелектрониката. Медната (Cu) жица е била метод за свързване на силициеви полупроводникови матрици към клемите на пакета за микроелектроника. С неотдавнашното увеличение на цената на златен (Au) проводник, медният (Cu) проводник е привлекателен начин за управление на общите разходи за пакет в микроелектрониката. Той също така прилича на златна (Au) жица поради подобните си електрически свойства. Самоиндуктивността и собственият капацитет са почти еднакви за златен (Au) и меден (Cu) проводник, като медният (Cu) проводник има по-ниско съпротивление. В микроелектронни приложения, където съпротивлението, дължащо се на свързващия проводник, може да повлияе отрицателно на производителността на веригата, използването на меден (Cu) проводник може да предложи подобрение. Медни, медни с покритие от паладий (PCC) и сребърни (Ag) сплави се появиха като алтернативи на златните жици поради цената. Проводниците на основата на мед са евтини и имат ниско електрическо съпротивление. Твърдостта на медта обаче я прави трудна за използване в много приложения, като например тези с крехки структури на свързващи подложки. За тези приложения Ag-Alloy предлага свойства, подобни на тези на златото, докато цената му е подобна на тази на PCC. Жицата от Ag-Alloy е по-мека от PCC, което води до по-ниско пръскане на Al и по-малък риск от повреда на свързващата подложка. Ag-Alloy телта е най-добрият евтин заместител за приложения, които се нуждаят от щанцо-към-щанцо залепване, водопадно лепене, ултра фина стъпка на залепващата подложка и малки отвори за залепваща подложка, ултра ниска височина на примката. Ние предоставяме пълна гама от услуги за тестване на полупроводници, включително тестване на пластини, различни видове окончателно тестване, тестване на системно ниво, тестване на ленти и цялостни услуги в края на линията. Тестваме различни типове полупроводникови устройства във всички наши семейства пакети, включително радиочестоти, аналогови и смесени сигнали, цифрови, управление на мощността, памет и различни комбинации като ASIC, многочипови модули, система в пакет (SiP) и подредени 3D опаковки, сензори и MEMS устройства като акселерометри и сензори за налягане. Нашият тестов хардуер и контактно оборудване са подходящи за персонализиран размер на пакета SiP, двустранни контактни решения за пакет върху пакет (PoP), TMV PoP, гнезда FusionQuad, многоредова MicroLeadFrame, фина медна колона. Тестовото оборудване и тестовите подове са интегрирани с CIM / CAM инструменти, анализ на добивите и мониторинг на производителността, за да осигурят много висока ефективност от първия път. Ние предлагаме многобройни адаптивни тестови процеси за микроелектроника за нашите клиенти и предлагаме разпределени тестови потоци за SiP и други сложни монтажни потоци. AGS-TECH предоставя пълна гама от тестови консултации, развойна дейност и инженерингови услуги през целия ви жизнен цикъл на полупроводникови и микроелектронни продукти. Ние разбираме уникалните пазари и изисквания за тестване за SiP, автомобили, мрежи, игри, графики, компютри, RF / безжични. Процесите на производство на полупроводници изискват бързи и прецизно контролирани решения за маркиране. Скорости на маркиране над 1000 знака/секунда и дълбочини на проникване на материала под 25 микрона са често срещани в индустрията за полупроводникова микроелектроника, използваща модерни лазери. Ние сме способни да маркираме смеси за форми, вафли, керамика и други с минимално влагане на топлина и перфектна повторяемост. Използваме лазери с висока точност, за да маркираме и най-малките части без повреди.
Оловни рамки за полупроводникови устройства: Възможни са както готови, така и персонализирани дизайн и производство. Оловните рамки се използват в процесите на сглобяване на полупроводникови устройства и по същество представляват тънки слоеве метал, които свързват окабеляването от малки електрически клеми на повърхността на полупроводниковата микроелектроника към големите вериги на електрически устройства и печатни платки. Оловните рамки се използват в почти всички пакети за полупроводникова микроелектроника. Повечето IC пакети за микроелектроника се правят чрез поставяне на полупроводниковия силициев чип върху оловна рамка, след това свързване на чипа с метални кабели на тази оловна рамка и впоследствие покриване на микроелектронния чип с пластмасов капак. Тази проста и относително евтина опаковка за микроелектроника все още е най-доброто решение за много приложения. Оловните рамки се произвеждат на дълги ленти, което позволява бързото им обработване на автоматизирани машини за сглобяване и обикновено се използват два производствени процеса: някакъв вид фотоецване и щамповане. В микроелектрониката дизайнът на водещата рамка често изисква персонализирани спецификации и характеристики, дизайни, които подобряват електрическите и термичните свойства и специфични изисквания за време на цикъл. Имаме задълбочен опит в производството на оловни рамки за микроелектроника за редица различни клиенти, използвайки лазерно фотоецване и щамповане.
Проектиране и производство на радиатори за микроелектроника: както стандартни, така и персонализирани дизайн и производство. С увеличаването на разсейването на топлината от микроелектронните устройства и намаляването на общите форм-фактори, управлението на топлината става все по-важен елемент от дизайна на електронни продукти. Постоянността на производителността и продължителността на живота на електронното оборудване са обратно пропорционални на температурата на компонентите на оборудването. Връзката между надеждността и работната температура на типично силициево полупроводниково устройство показва, че намаляването на температурата съответства на експоненциално увеличение на надеждността и продължителността на живота на устройството. Следователно, дълъг живот и надеждна работа на компонент на полупроводниковата микроелектроника могат да бъдат постигнати чрез ефективно контролиране на работната температура на устройството в границите, определени от дизайнерите. Радиаторите са устройства, които подобряват разсейването на топлината от гореща повърхност, обикновено външния корпус на компонент, генериращ топлина, към по-хладна среда като въздух. За следващите дискусии се приема, че въздухът е охлаждащата течност. В повечето ситуации преносът на топлина през интерфейса между твърдата повърхност и охлаждащия въздух е най-малко ефективен в рамките на системата, а интерфейсът твърд въздух представлява най-голямата бариера за разсейване на топлината. Радиаторът намалява тази бариера главно чрез увеличаване на повърхността, която е в пряк контакт с охлаждащата течност. Това позволява да се разсейва повече топлина и/или понижава работната температура на полупроводниковото устройство. Основната цел на радиатора е да поддържа температурата на микроелектронното устройство под максимално допустимата температура, посочена от производителя на полупроводниковото устройство.
Можем да класифицираме радиаторите по отношение на методите на производство и техните форми. Най-често срещаните видове радиатори с въздушно охлаждане включват:
- Щамповани: Медни или алуминиеви ламарини се щамповат в желани форми. те се използват в традиционното въздушно охлаждане на електронни компоненти и предлагат икономично решение на топлинни проблеми с ниска плътност. Подходящи са за производство в голям обем.
- Екструзия: Тези радиатори позволяват формирането на сложни двуизмерни форми, способни да разсейват големи топлинни натоварвания. Те могат да бъдат изрязани, обработени и добавени опции. Напречното рязане ще произведе многопосочни, правоъгълни радиатори с щифтови ребра, а включването на назъбени ребра подобрява производителността с приблизително 10 до 20%, но с по-бавна скорост на екструдиране. Ограниченията на екструзията, като например височината на ребрата до дебелината на ребрата, обикновено диктуват гъвкавостта на опциите за проектиране. Типично съотношение на височината на ребрата към процепа до 6 и минимална дебелина на ребрата от 1,3 мм са постижими със стандартни техники за екструдиране. Съотношение 10 към 1 и дебелина на перката от 0,8 инча могат да бъдат получени със специални характеристики на дизайна на матрицата. Въпреки това, тъй като съотношението на страните се увеличава, толерансът на екструдиране е компрометиран.
- Свързани/изработени ребра: Повечето радиатори с въздушно охлаждане са с ограничена конвекция и общата топлинна ефективност на радиатора с въздушно охлаждане често може да бъде значително подобрена, ако по-голяма повърхност може да бъде изложена на въздушния поток. Тези високопроизводителни радиатори използват термично проводима епоксидна смола, напълнена с алуминий, за свързване на равнинни перки към набраздена екструдирана основна плоча. Този процес позволява много по-голямо съотношение на височината на ребрата към процепа от 20 до 40, което значително увеличава капацитета на охлаждане, без да увеличава нуждата от обем.
- Отливки: Процесите на пясък, изгубен восък и леене под налягане за алуминий или мед/бронз се предлагат със или без вакуумна помощ. Ние използваме тази технология за производство на радиатори с щифтови ребра с висока плътност, които осигуряват максимална производителност при използване на импулсно охлаждане.
- Сгънати перки: Вълнообразна ламарина от алуминий или мед увеличава повърхностната площ и обемната производителност. След това радиаторът се закрепва към основна плоча или директно към нагревателната повърхност чрез епоксидна смола или спояване. Не е подходящ за радиатори с висок профил поради наличността и ефективността на перките. Следователно, той позволява да се произвеждат високоефективни радиатори.
При избора на подходящ радиатор, отговарящ на необходимите термични критерии за вашите микроелектронни приложения, ние трябва да проучим различни параметри, които влияят не само на самата производителност на радиатора, но и на цялостната производителност на системата. Изборът на конкретен тип радиатор в микроелектрониката зависи до голяма степен от топлинния бюджет, разрешен за радиатора и външните условия около радиатора. Никога няма една единствена стойност на топлинно съпротивление, присвоено на даден радиатор, тъй като топлинното съпротивление варира в зависимост от външните условия на охлаждане.
Проектиране и производство на сензори и задвижващи механизми: Предлагат се както готови, така и персонализирани дизайн и производство. Ние предлагаме решения с готови за използване процеси за инерционни сензори, сензори за налягане и относително налягане и инфрачервени температурни сензори. Като използваме нашите IP блокове за акселерометри, инфрачервени сензори и сензори за налягане или прилагаме вашия дизайн според наличните спецификации и правила за проектиране, ние можем да ви доставим базирани на MEMS сензорни устройства в рамките на седмици. Освен MEMS могат да бъдат произведени и други видове сензорни и задвижващи структури.
Проектиране и производство на оптоелектронни и фотонни схеми: Фотонна или оптична интегрална схема (PIC) е устройство, което интегрира множество фотонни функции. Може да се наподобява на електронни интегрални схеми в микроелектрониката. Основната разлика между двете е, че фотонната интегрална схема осигурява функционалност за информационни сигнали, наложени върху оптични дължини на вълните във видимия спектър или близо до инфрачервения 850 nm-1650 nm. Техниките за производство са подобни на тези, използвани в интегралните схеми на микроелектрониката, където фотолитографията се използва за моделиране на пластини за ецване и отлагане на материал. За разлика от полупроводниковата микроелектроника, където основното устройство е транзисторът, в оптоелектрониката няма едно доминиращо устройство. Фотонните чипове включват свързващи вълноводи с ниски загуби, разделители на мощност, оптични усилватели, оптични модулатори, филтри, лазери и детектори. Тези устройства изискват разнообразие от различни материали и техники за производство и затова е трудно да се реализират всички на един чип. Нашите приложения на фотонни интегрални схеми са главно в областта на оптичните комуникации, биомедицинските и фотонните изчисления. Някои примерни оптоелектронни продукти, които можем да проектираме и произведем за вас, са светодиоди (светлоизлъчващи диоди), диодни лазери, оптоелектронни приемници, фотодиоди, лазерни дистанционни модули, персонализирани лазерни модули и др.