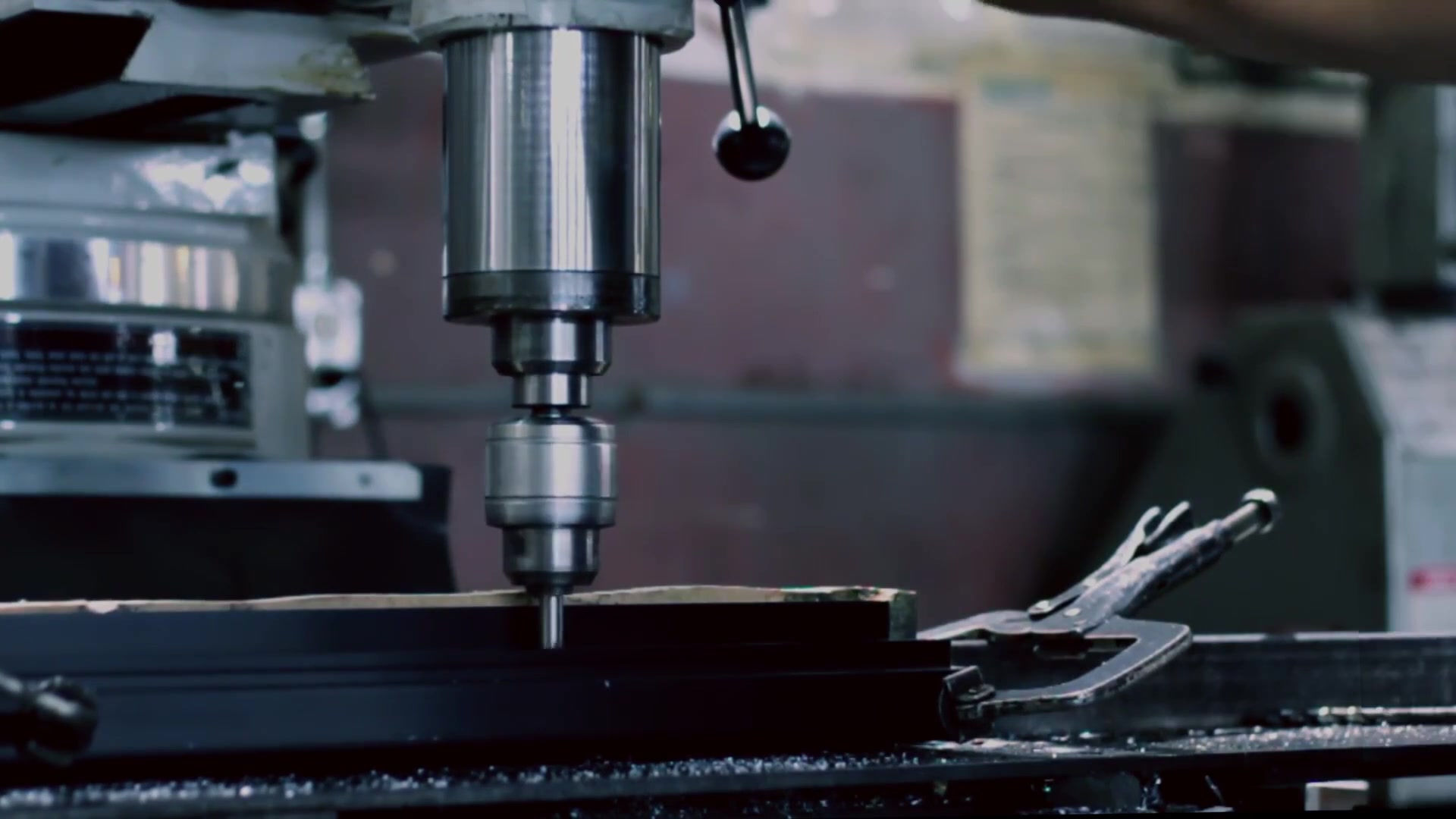
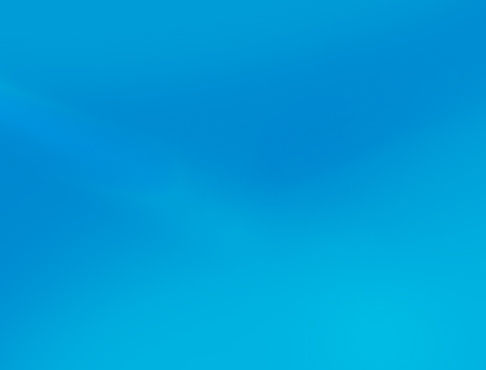
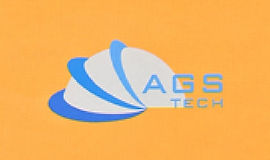
さまざまな製品とサービスのグローバル カスタム メーカー、インテグレーター、コンソリデーター、アウトソーシング パートナー。
私たちは、製造、製造、エンジニアリング、統合、統合、カスタム製造および既製の製品とサービスのアウトソーシングのワンストップ ソースです。
Choose your Language
-
カスタム製造
-
国内およびグローバルな受託製造
-
製造アウトソーシング
-
国内およびグローバル調達
-
連結
-
エンジニアリング統合
-
エンジニアリングサービス
当社が製造に展開する多くの接合技術の中で、溶接、ろう付け、はんだ付け、接着剤接合、およびカスタム機械組立に特に重点が置かれています。これらの技術は、気密アセンブリの製造、ハイテク製品の製造、および特殊なシーリングなどの用途で広く使用されているためです。ここでは、高度な製品やアセンブリの製造に関連するこれらの接合技術のより専門的な側面に焦点を当てます。
FUSION WELDING: 熱を利用して材料を溶かし合体させます。熱は電気または高エネルギービームによって供給されます。当社が展開する溶融溶接の種類は、酸素燃料ガス溶接、アーク溶接、高エネルギービーム溶接です。
SOLID-STATE WELDING: 溶融や融着なしで部品を接合します。当社のソリッドステート溶接法は、コールド、超音波、抵抗、摩擦、爆発溶接、および拡散接合です。
ろう付けとはんだ付け: 溶加材を使用し、溶接よりも低温で作業できるという利点があるため、製品への構造的損傷が少なくなります。セラミックと金属の継手、ハーメチック シーリング、真空フィードスルー、高真空と超高真空、および流体制御コンポーネントを製造する当社のろう付け施設に関する情報 は、次の場所にあります。ろう付け工場のパンフレット
接着剤の接着: 業界で使用される接着剤の多様性と用途の多様性のため、専用のページがあります. 接着に関するページへは、こちらをクリックしてください。
カスタムメカニカルアセンブリ: ボルト、ネジ、ナット、リベットなどのさまざまなファスナーを使用しています。当社のファスナーは、標準的な既製のファスナーに限定されません。特別な用途の要件を満たすことができるように、標準外の材料で作られた特殊なファスナーを設計、開発、製造しています。電気または熱の非伝導性が必要な場合もあれば、伝導性が必要な場合もあります。一部の特殊な用途では、顧客は、製品を破壊せずには取り外せない特殊な留め具を希望する場合があります。無限のアイデアとアプリケーションがあります。すぐに開発できます. 機械の組み立てに関するページに移動するには、ここをクリックしてください。. さまざまな結合手法を詳しく見てみましょう。
OXYFUEL GAS WELDING (OFW): 酸素を混合した燃料ガスを使用して溶接フレームを生成します。アセチレンを燃料とし、酸素を使用することをオキシアセチレンガス溶接と呼んでいます。酸素燃焼ガスの燃焼プロセスでは、次の 2 つの化学反応が発生します。
C2H2 + O2 ------» 2CO + H2 + 熱
2CO + H2 + 1.5 O2--------» 2 CO2 + H2O + 熱
最初の反応では、アセチレンが一酸化炭素と水素に解離し、発生する全熱の約 33% が生成されます。上記の 2 番目のプロセスは、全熱の約 67% を生成しながら、水素と一酸化炭素をさらに燃焼させることを表しています。炎の温度は 1533 ~ 3573 ケルビンです。混合ガス中の酸素の割合は重要です。酸素含有量が半分以上の場合、炎は酸化剤になります。これは、一部の金属では望ましくありませんが、他の金属では望ましいものです。酸化炎が望ましい例としては、銅ベースの合金が挙げられます。これは、金属の上にパッシベーション層を形成するためです。一方、酸素含有量が減少すると、完全燃焼ができなくなり、火炎は還元(浸炭)火炎になります。還元炎の温度は低いため、はんだ付けやろう付けなどのプロセスに適しています。他のガスも燃料になる可能性がありますが、アセチレンよりもいくつかの欠点があります。場合によっては、フィラー ロッドまたはワイヤーの形で溶加材を溶接部に供給します。それらのいくつかは、表面の酸化を遅らせて溶融金属を保護するためにフラックスでコーティングされています。フラックスがもたらす追加の利点は、溶接部から酸化物やその他の物質を除去できることです。これはより強い結合につながります。酸素燃料ガス溶接のバリエーションとして、圧力ガス溶接があります。この方法では、オキシアセチレン ガス トーチを使用して 2 つのコンポーネントの界面を加熱し、界面が溶融し始めたら、トーチを引き抜き、軸方向の力を加えて 2 つのパーツを一緒に押し付けます。界面が固まるまで。
アーク溶接: 電気エネルギーを使用して、電極の先端と溶接する部品の間にアークを発生させます。電源はACまたはDCで、電極は消耗品または非消耗品です。アーク溶接における熱伝達は、次の式で表すことができます。
H / l = ex VI / v
ここで、H は入熱、l は溶接長さ、V と I は印加される電圧と電流、v は溶接速度、e はプロセス効率です。効率「e」が高ければ高いほど、利用可能なエネルギーが材料を溶融するために使用されます。熱入力は、次のように表すこともできます。
H = ux (ボリューム) = ux A xl
ここで、u は溶融の比エネルギー、A は溶接部の断面、l は溶接部の長さです。上記の 2 つの式から、次の式が得られます。
v = ex VI / u A
アーク溶接のバリエーションとして、SHIELDED METAL ARC WELDING (SMAW) があります。これは、すべての産業およびメンテナンス溶接プロセスの約 50% を占めています。電気アーク溶接 (スティック溶接) は、コーティングされた電極の先端をワークピースに接触させ、アークを維持するのに十分な距離まですばやく引き離すことによって実行されます。電極が細く長い棒状であることから棒溶接とも呼ばれています。溶接プロセス中に、電極の先端は、そのコーティングとアークの近くの母材とともに溶融します。母材金属、電極金属、および電極コーティングからの物質の混合物が溶接領域で固化します。電極のコーティングは、還元し、溶接領域にシールド ガスを提供して、周囲の酸素から保護します。したがって、このプロセスはシールド メタル アーク溶接と呼ばれます。最適な溶接性能を得るために、50 ~ 300 アンペアの電流と一般的に 10 kW 未満の電力レベルを使用します。また、DC 電流の極性 (電流の流れる方向) も重要です。ワークピースがプラスで電極がマイナスのストレート極性は、溶け込みが浅いため板金の溶接や、ギャップが非常に広い接合部に適しています。極性が逆の場合、つまり電極がプラスでワークピースがマイナスの場合、より深い溶込みを実現できます。交流ではアークが脈動するため、大径電極と最大電流で厚肉部の溶接が可能です。 SMAW 溶接法は、3 ~ 19 mm の厚さのワークピースに適しており、マルチパス技術を使用する場合はそれ以上です。溶接部の上部に形成されたスラグは、ワイヤーブラシを使用して除去する必要があるため、溶接部で腐食や破損が発生しません。これはもちろん、シールドされた金属アーク溶接のコストに追加されます。それにもかかわらず、SMAW は産業および修理作業で最も一般的な溶接技術です。
サブマージ アーク溶接 (SAW): このプロセスでは、石灰、シリカ、フッ化カルシウム、酸化マンガンなどの粒状フラックス材料を使用して溶接アークをシールドします。粒状フラックスは、重力流によってノズルを介して溶接ゾーンに供給されます。溶融溶接部を覆うフラックスは、火花、煙、紫外線などから大幅に保護し、断熱材として機能するため、熱がワークピースの奥深くまで浸透します。融着していないフラックスは回収、処理して再利用します。裸のコイルが電極として使用され、チューブを通して溶接部に供給されます。 300 ~ 2000 アンペアの電流を使用します。サブマージ アーク溶接 (SAW) プロセスは、溶接中に円形構造物 (パイプなど) の回転が可能な場合、水平および平面位置と円形溶接に限定されます。速度は 5 m/min に達することがあります。 SAW プロセスは厚板に適しており、高品質で強靭、延性があり均一な溶接が得られます。生産性、つまり 1 時間あたりの溶着材料の量は、SMAW プロセスと比較して 4 ~ 10 倍です。
別のアーク溶接プロセス、すなわちガス メタル アーク溶接 (GMAW) または代わりにメタル イナート ガス溶接 (MIG) と呼ばれる方法は、ヘリウム、アルゴン、二酸化炭素などの外部ガス源によってシールドされた溶接領域に基づいています。電極金属には追加の脱酸素剤が存在する場合があります。消耗ワイヤは、ノズルを通して溶接ゾーンに供給されます。鉄および非鉄金属を含む製造は、ガス メタル アーク溶接 (GMAW) を使用して実行されます。溶接生産性はSMAWプロセスの約2倍です。自動溶接機を使用しています。金属は、このプロセスで 3 つの方法のいずれかで移動します。「スプレー移動」では、1 秒間に数百個の小さな金属滴が電極から溶接領域に移動します。一方、「Globular Transfer」では、二酸化炭素が豊富なガスが使用され、溶融金属の小球が電気アークによって推進されます。溶接電流が高く、溶込みが深くなり、溶着速度がスプレー移行より速くなります。したがって、グロビュラー トランスファーは、より重いセクションを溶接する場合に適しています。最後に、「短絡」法では、電極先端が溶融溶融池に接触し、毎秒 50 滴を超える速度で金属が個々の溶滴で移動するときに短絡します。低電流と低電圧は、より細いワイヤとともに使用されます。使用される電力は約 2 kW で、温度は比較的低いため、この方法は厚さ 6 mm 未満の薄いシートに適しています。
別のバリエーションである FLUX-CORED ARC WELDING (FCAW) プロセスは、電極がフラックスで満たされたチューブであることを除いて、ガス メタル アーク溶接に似ています。コア付きフラックス電極を使用する利点は、より安定したアークを生成し、溶接金属の特性を改善する機会を与え、SMAW 溶接と比較してそのフラックスの脆性と柔軟性が低く、溶接輪郭が改善されることです。自己シールド芯入り電極には、溶接部を大気から保護する材料が含まれています。約20kWの電力を使用しています。 GMAW プロセスと同様に、FCAW プロセスも連続溶接のプロセスを自動化する機会を提供し、経済的です。フラックスコアにさまざまな合金を追加することにより、さまざまな溶接金属の化学的性質を開発できます。
ELECTROGAS WELDING (EGW) では、配置された部品を端から端まで溶接します。突合せ溶接と呼ばれることもあります。溶接金属は、接合される 2 つのピースの間の溶接キャビティに入れられます。スペースは、溶融スラグが流出しないように 2 つの水冷ダムで囲まれています。ダムは機械駆動で上に移動します。ワークピースが回転できる場合、パイプの円周溶接にもエレクトロガス溶接技術を使用できます。電極は導管を通して供給され、連続アークを維持します。電流は約 400 アンペアまたは 750 アンペアで、電力レベルは約 20 kW です。フラックスコア電極または外部ソースから発生する不活性ガスは、シールドを提供します。厚さ12mmから75mmの鋼、チタンなどの金属にはエレクトロガス溶接(EGW)を使用します。この手法は、大規模な構造に適しています。
しかし、ELECTROSLAG WELDING (ESW) と呼ばれる別の技術では、電極とワークピースの底部との間でアークが点火され、フラックスが追加されます。溶融スラグが電極先端に到達すると、アークが消えます。エネルギーは、溶融スラグの電気抵抗によって継続的に供給されます。厚さ50mmから900mm以上の厚板の溶接が可能です。電流は約 600 アンペアで、電圧は 40 ~ 50 V です。溶接速度は約 12 ~ 36 mm/分です。アプリケーションは、エレクトロガス溶接に似ています。
当社の非消耗電極プロセスの 1 つであるガス タングステン アーク溶接 (GTAW) は、タングステン イナート ガス溶接 (TIG) としても知られ、ワイヤによるフィラー メタルの供給を伴います。ぴったりとフィットするジョイントの場合、溶加材を使用しないことがあります。 TIGプロセスではフラックスを使用せず、シールドにアルゴンとヘリウムを使用します。タングステンは融点が高く、TIG 溶接プロセスで消費されないため、定電流とアーク ギャップを維持できます。電力レベルは 8 ~ 20 kW で、電流は 200 アンペア (DC) または 500 アンペア (AC) です。アルミニウムとマグネシウムの場合、酸化物洗浄機能のために AC 電流を使用します。タングステン電極の汚染を避けるために、溶融金属との接触を避けます。ガス タングステン アーク溶接 (GTAW) は、薄い金属の溶接に特に役立ちます。 GTAW 溶接は非常に高品質で、表面仕上げが良好です。
水素ガスのコストが高いため、あまり使用されていない技術は原子水素溶接 (AHW) です。この方法では、流れる水素ガスのシールド雰囲気内で 2 つのタングステン電極間にアークを生成します。 AHW も非消耗電極溶接プロセスです。二原子水素ガス H2 は、温度が 6273 ケルビンを超える溶接アークの近くで原子形態に分解されます。分解する際、アークから大量の熱を吸収します。水素原子が比較的冷たい表面である溶接部に衝突すると、水素原子は二原子形態に再結合し、蓄えられた熱を放出します。ワークピースとアーク距離を変えることで、エネルギーを変えることができます。
別の非消耗電極プロセスであるプラズマ アーク溶接 (PAW) では、溶接ゾーンに向けてプラズマ アークを集中させます。温度は PAW で 33,273 ケルビンに達します。ほぼ同数の電子とイオンがプラズマガスを構成します。低電流パイロット アークは、タングステン電極とオリフィスの間のプラズマを開始します。動作電流は一般に約 100 アンペアです。フィラー金属が供給されてもよい。プラズマ アーク溶接では、外側のシールド リングとアルゴンやヘリウムなどのガスを使用してシールドを行います。プラズマ アーク溶接では、アークは電極とワークピースの間、または電極とノズルの間にあります。この溶接技術は、他の方法よりも高いエネルギー集中、より深く狭い溶接能力、優れたアーク安定性、最大 1 メートル/分の高い溶接速度、熱歪みの少ないという利点があります。通常、アルミニウムとチタンの厚さは 6 mm 未満、場合によっては 20 mm まではプラズマ アーク溶接を使用します。
HIGH-ENERGY-BEAM WELDING (高エネルギー ビーム溶接): 電子ビーム溶接 (EBW) とレーザー溶接 (LBW) を 2 つのバリエーションとして使用する別の種類のフュージョン溶接方法。これらの技術は、私たちのハイテク製品製造作業にとって特に価値があります。電子ビーム溶接では、高速の電子がワークピースに衝突し、その運動エネルギーが熱に変換されます。電子の細いビームは、真空チャンバー内を容易に移動します。通常、電子ビーム溶接では高真空を使用します。板厚150mmまで溶接可能。シールドガス、フラックス、充填材は必要ありません。電子ビームガンは100kWの能力を持っています。最大 30 までの高アスペクト比と小さな熱影響部を持つ深くて狭い溶接が可能です。溶接速度は 12 m/min に達することがあります。レーザービーム溶接では、高出力レーザーを熱源として使用します。高密度の10ミクロンのレーザービームは、ワークへの深い浸透を可能にします。レーザービーム溶接では、深さと幅の比率が 10 まで可能です。パルスレーザーと連続波レーザーの両方を使用します。前者は薄い材料のアプリケーションに使用され、後者は主に約 25 mm までの厚いワークピースに使用されます。電力レベルは最大 100 kW です。レーザー ビーム溶接は、光学的に非常に反射性の高い材料にはあまり適していません。ガスは、溶接プロセスでも使用できます。レーザー ビーム溶接法は、自動化および大量生産に適しており、2.5 m/min ~ 80 m/min の溶接速度を提供できます。この溶接技術が提供する主な利点の 1 つは、他の技術を使用できない領域へのアクセスです。レーザー光線は、そのような困難な領域に簡単に到達できます。電子ビーム溶接のような真空は必要ありません。レーザービーム溶接では、品質と強度が高く、収縮が少なく、歪みが少なく、気孔率の低い溶接が得られます。レーザー ビームは、光ファイバー ケーブルを使用して簡単に操作および成形できます。したがって、この技術は、精密ハーメチック アセンブリ、電子パッケージなどの溶接に適しています。
当社の固体溶接技術を見てみましょう。 COLD WELDING (CW) は、金型やロールを使用して熱の代わりに圧力を加えて部品を接合するプロセスです。冷間圧接では、嵌合部品の少なくとも 1 つが延性である必要があります。 2 つの類似した材料を使用すると、最良の結果が得られます。冷間圧接で接合する 2 つの金属が異なる場合、接合部が弱く脆くなることがあります。冷間圧接法は、電気接続、熱に敏感な容器の縁、サーモスタット用のバイメタル ストリップなど、軟らかく延性があり小さなワークピースに適しています。冷間圧接の 1 つのバリエーションは、一対のロールを介して圧力が加えられるロール接合 (またはロール圧接) です。界面強度を高めるために、高温でロール溶接を行うこともあります。
当社が使用するもう 1 つの固相溶接プロセスは超音波溶接 (USW) です。この場合、ワークピースは静的垂直力と振動せん断応力にさらされます。振動せん断応力は、トランスデューサの先端を通して適用されます。超音波溶接は、10 ~ 75 kHz の周波数で振動を展開します。シーム溶接などの一部の用途では、回転する溶接ディスクを先端として使用します。ワークピースに加えられるせん断応力は、小さな塑性変形を引き起こし、酸化物層や汚染物質を破壊し、固体結合を引き起こします。超音波溶着に関わる温度は、金属の融点温度よりはるかに低く、融合は起こりません。プラスチックなどの非金属材料には、超音波溶接 (USW) プロセスを頻繁に使用します。ただし、熱可塑性樹脂では、温度は融点に達します。
もう 1 つの一般的な技術である摩擦溶接 (FRW) では、接合するワークピースの界面での摩擦によって熱が発生します。摩擦圧接では、一方のワークピースを固定し、もう一方のワークピースを治具に保持して一定速度で回転させます。次に、工作物は軸力の下で接触させられます。摩擦圧接の表面回転速度は、場合によっては900m/minに達することもあります。十分な界面接触の後、回転するワークピースは突然停止し、軸力が増加します。溶接部は一般に狭い領域です。摩擦圧接技術は、さまざまな材料で作られた中実部品と管状部品を接合するために使用できます。 FRW の界面にバリが発生する場合がありますが、このバリは二次加工または研磨によって除去できます。摩擦圧接プロセスにはさまざまなバリエーションがあります。たとえば、「慣性摩擦溶接」では、フライホイールの回転運動エネルギーを使用して部品を溶接します。フライホイールが止まると溶接完了です。回転質量を変化させることができるため、回転運動エネルギーを変化させることができます。もう 1 つのバリエーションは「線形摩擦溶接」で、結合するコンポーネントの少なくとも 1 つに線形往復運動が加えられます。線形摩擦溶接では、パーツは円形である必要はなく、長方形、正方形、またはその他の形状にすることができます。周波数は数十 Hz、振幅はミリメートル範囲、圧力は数十または数百 MPa です。最後に、「摩擦攪拌接合」は、上記で説明した他の 2 つの接合とは多少異なります。慣性摩擦圧接と線形摩擦圧接では、2 つの接触面を摩擦することによって界面の加熱が行われますが、摩擦攪拌接合法では、接合する 2 つの面に 3 番目の物体が擦り付けられます。直径5~6mmの回転工具を関節に当てます。温度は、503 ~ 533 ケルビンの値まで上昇する可能性があります。ジョイント内の材料の加熱、混合、攪拌が行われます。アルミニウム、プラスチック、複合材など、さまざまな材料に摩擦攪拌接合を使用しています。溶接は均一で、気孔が最小限に抑えられた高品質です。摩擦攪拌接合ではヒュームやスパッタが発生せず、プロセスは十分に自動化されています。
抵抗溶接 (RW): 溶接に必要な熱は、接合される 2 つのワークピース間の電気抵抗によって生成されます。抵抗溶接では、フラックス、シールドガス、消耗電極は使用しません。ジュール熱は抵抗溶接で発生し、次のように表すことができます。
H = (二乗 I) x R xtx K
H はジュール (ワット秒) 単位で生成される熱、I 電流 (アンペア単位)、R 抵抗 (オーム単位)、t は電流が流れる時間 (秒単位) です。係数 K は 1 未満で、放射と伝導によって失われないエネルギーの割合を表します。抵抗溶接プロセスの電流は 100,000 A にも達することがありますが、電圧は通常 0.5 ~ 10 ボルトです。電極は通常、銅合金でできています。抵抗溶接により同種・異材の接合が可能です。このプロセスにはいくつかのバリエーションがあります。「抵抗スポット溶接」では、2 枚のシートの重ね継ぎ面に接触する 2 つの対向する丸い電極が使用されます。電流がオフになるまで圧力をかけます。溶接ナゲットは通常、直径 10 mm までです。抵抗スポット溶接では、溶接部にわずかに変色した圧痕が残ります。スポット溶接は、最もポピュラーな抵抗溶接技術です。スポット溶接では、困難な箇所に到達するために、さまざまな電極形状が使用されます。当社のスポット溶接装置は CNC 制御で、同時に使用できる複数の電極を備えています。もう 1 つのバリエーション「抵抗シーム溶接」は、AC 電源サイクルで電流が十分に高いレベルに達するたびに連続スポット溶接を生成するホイールまたはローラー電極を使用して実行されます。抵抗シーム溶接によって生成された接合部は、液密および気密です。薄板の場合、約 1.5 m/min の溶接速度が通常です。シームに沿って所望の間隔でスポット溶接が生成されるように、断続的な電流を適用することができる。 「抵抗プロジェクション溶接」では、溶接するワーク表面の1つに1つまたは複数の突起(ディンプル)をエンボス加工します。これらの突起は円形または楕円形です。合わせ部品と接触するこれらのエンボス加工されたスポットでは、局部的に高い温度に達します。電極は、これらの突起を圧縮する圧力を加えます。抵抗プロジェクション溶接の電極は先端が平らで、水冷式の銅合金です。抵抗プロジェクション溶接の利点は、1回のストロークで多数の溶接ができることです。したがって、電極の寿命が長くなり、さまざまな厚さのシートを溶接でき、ナットとボルトをシートに溶接できます。抵抗プロジェクション溶接の欠点は、ディンプルをエンボス加工する追加コストです。さらに別の技術である「フラッシュ溶接」では、2 つのワークピースが接触し始めると、2 つのワークピースの端でアークから熱が発生します。この方法は、代わりにアーク溶接を考慮することもできます。界面の温度が上昇し、材料が軟化します。軸力が加えられ、軟化した領域に溶接が形成されます。フラッシュ溶接が完了したら、接合部を機械加工して外観を向上させることができます。フラッシュ溶接による溶接品質は良好です。電力レベルは 10 ~ 1500 kW です。フラッシュ溶接は、直径 75 mm までの同種または異種金属、および厚さ 0.2 mm ~ 25 mm のシートの端と端の接合に適しています。 「スタッドアーク溶接」はフラッシュ溶接と非常によく似ています。ボルトやねじ棒などのスタッドは、プレートなどのワークピースに接合された状態で 1 つの電極として機能します。発生した熱を集中させ、酸化を防ぎ、溶融金属を溶接部に保持するために、使い捨てのセラミック リングがジョイントの周りに配置されます。最後に、「パーカッション溶接」は別の抵抗溶接プロセスで、コンデンサを使用して電気エネルギーを供給します。パーカッション溶接では、電力が数ミリ秒以内に放電され、接合部に局所的な高熱が非常に急速に発生します。パーカッション溶接は、接合部付近の敏感な電子部品の加熱を避ける必要がある電子機器製造業界で広く使用されています。
爆発溶接と呼ばれる技術では、結合するワークピースの 1 つに爆薬の層を爆発させます。ワークピースにかかる非常に高い圧力により、乱流と波状の界面が生成され、機械的な連結が行われます。爆発溶接における結合強度は非常に高いです。爆発溶接は、異種金属のプレートのクラッディングに適した方法です。クラッディングの後、プレートはより薄い部分に丸められます。チューブをプレートにしっかりと密着させるために、チューブを拡張するために爆発溶接を使用することがあります。
固相接合の分野における最後の方法は、主に界面を横切る原子の拡散によって良好な接合が達成される拡散接合または拡散溶接 (DFW) です。界面でのいくらかの塑性変形も溶接に寄与します。関連する温度は約 0.5 Tm で、Tm は金属の融解温度です。拡散溶着の接着強度は、圧力、温度、接触時間、および接触面の清浄度に依存します。界面に溶加材を使用することもあります。拡散接合では熱と圧力が必要であり、電気抵抗または炉と自重、プレスなどによって供給されます。類似および異種の金属は、拡散溶接で接合できます。原子が移動するのに時間がかかるため、プロセスは比較的遅くなります。 DFW は自動化が可能で、航空宇宙、エレクトロニクス、医療産業向けの複雑な部品の製造に広く使用されています。製造される製品には、整形外科用インプラント、センサー、航空宇宙構造部材が含まれます。拡散接合を超塑性成形と組み合わせて、複雑な板金構造を製造できます。シート上の選択された位置が最初に拡散結合され、次に非結合領域が空気圧を使用して金型内に拡張されます。剛性と重量の比率が高い航空宇宙構造は、この方法の組み合わせを使用して製造されます。拡散溶着と超塑性成形を組み合わせたプロセスにより、留め具が不要になるため、必要な部品の数が減り、低応力で高精度な部品を経済的かつ短いリードタイムで実現できます。
ろう付け: ろう付けおよびはんだ付け技術では、溶接に必要な温度よりも低い温度が必要です。ただし、ろう付け温度ははんだ付け温度よりも高くなります。ろう付けでは、接合する表面の間にフィラー金属を配置し、723 ケルビンを超えるがワークピースの溶融温度よりも低いフィラー材料の溶融温度まで温度を上げます。溶融金属は、ワークピースの間のぴったりとフィットするスペースを満たします。フィラー金属の冷却とその後の固化により、強力な接合が得られます。ろう付け溶接では、溶加材が接合部に堆積します。ろう付けと比較して、ろう付け溶接ではかなり多くの溶加材が使用されます。酸化炎を伴うオキシアセチレントーチは、ろう付け溶接で溶加材を溶着するために使用されます。ろう付けの温度が低いため、熱影響部での反りや残留応力などの問題が少なくなります。ろう付けの隙間が小さいほど、接合部のせん断強度が高くなります。ただし、最大の引張強度は、最適なギャップ (ピーク値) で達成されます。この最適値の上下では、ろう付けの引張強度が低下します。ろう付けの一般的なクリアランスは、0.025 ~ 0.2 mm です。プレフォーム、パウダー、リング、ワイヤー、ストリップなど、さまざまな形状のさまざまなろう材を使用しています。また、お客様の設計または製品の形状に合わせてこれらのプリフォームを特別に製造することもできます。また、母材や用途に合わせてロウ材の含有量を決定いたします。不要な酸化物層を除去し、酸化を防ぐために、ろう付け作業でフラックスを頻繁に使用します。その後の腐食を避けるために、フラックスは通常、接合作業後に除去されます。 AGS-TECH Inc. では、次のようなさまざまなろう付け方法を使用しています。
- トーチろう付け
- 炉ろう付け
- 誘導ろう付け
- 抵抗ろう付け
- ディップろう付け
- 赤外線ろう付け
- 拡散ろう付け
- 高エネルギービーム
当社のろう付け接合の最も一般的な例は、超硬ドリル ビット、インサート、オプトエレクトロニック ハーメチック パッケージ、シールなど、強度の高い異種金属でできています。
はんだ付け : これは、密接に適合するコンポーネント間のろう付けのように、はんだ (フィラー金属) が接合部を埋める最も頻繁に使用される技術の 1 つです。当社のはんだの融点は 723 ケルビン未満です。製造工程では、手動はんだ付けと自動はんだ付けの両方を展開しています。ろう付けに比べて、はんだ付け温度が低くなります。はんだ付けは、高温または高強度の用途にはあまり適していません。はんだ付けには、鉛フリーはんだをはじめ、すず-鉛、すず-亜鉛、鉛-銀、カドミウム-銀、亜鉛-アルミニウム合金などを使用しています。はんだ付けのフラックスとしては、非腐食性の樹脂系と無機酸、無機塩の両方が使用されています。はんだ付け性の低い金属のはんだ付けには、特殊なフラックスを使用しています。セラミック材料、ガラス、またはグラファイトをはんだ付けする必要がある用途では、最初に部品を適切な金属でメッキして、はんだ付け性を高めます。当社の一般的なはんだ付け技術は次のとおりです。
-リフローまたはペーストはんだ
-ウェーブはんだ付け
-炉はんだ付け
-トーチはんだ付け
-誘導はんだ付け
-はんだごて
・抵抗はんだ付け
-ディップはんだ付け
-超音波はんだ付け
-赤外線はんだ付け
超音波はんだ付けは、接合面から酸化膜を除去する超音波キャビテーション効果により、フラックスが不要になるという独自の利点を提供します。リフローおよびウェーブはんだ付けは、電子機器の大量生産向けの当社の工業的に優れた技術であるため、詳細に説明する価値があります。リフローはんだ付けでは、はんだ金属粒子を含む半固体ペーストを使用します。ペーストは、スクリーニングまたはステンシル プロセスを使用して接合部に配置されます。プリント回路基板 (PCB) では、この手法を頻繁に使用します。電気部品がペーストからこれらのパッドに配置されると、表面張力によって表面実装パッケージが整列された状態に保たれます。コンポーネントを配置した後、リフローはんだ付けが行われるように、アセンブリを炉で加熱します。このプロセス中に、ペースト内の溶剤が蒸発し、ペースト内のフラックスが活性化され、部品が予熱され、はんだ粒子が溶けて接合部を濡らし、最後に PCB アセンブリがゆっくりと冷却されます。 PCB ボードの大量生産のための 2 番目の一般的な技術であるウェーブはんだ付けは、溶融はんだが金属表面を濡らし、金属が予熱された場合にのみ良好な結合を形成するという事実に依存しています。溶融はんだの定在層波が最初にポンプによって生成され、予熱および予フラックスされた PCB が波の上を運ばれます。はんだは、露出した金属面のみを濡らしますが、IC ポリマー パッケージやポリマー コーティングされた回路基板は濡らしません。高速の温水ジェットが接合部から余分なはんだを吹き飛ばし、隣接するリード間のブリッジングを防ぎます。表面実装パッケージのウェーブはんだ付けでは、はんだ付けの前に、最初にそれらを回路基板に接着します。ここでもスクリーニングとステンシルが使用されますが、今回はエポキシ用です。コンポーネントが正しい位置に配置された後、エポキシが硬化され、ボードが反転され、ウェーブはんだ付けが行われます。