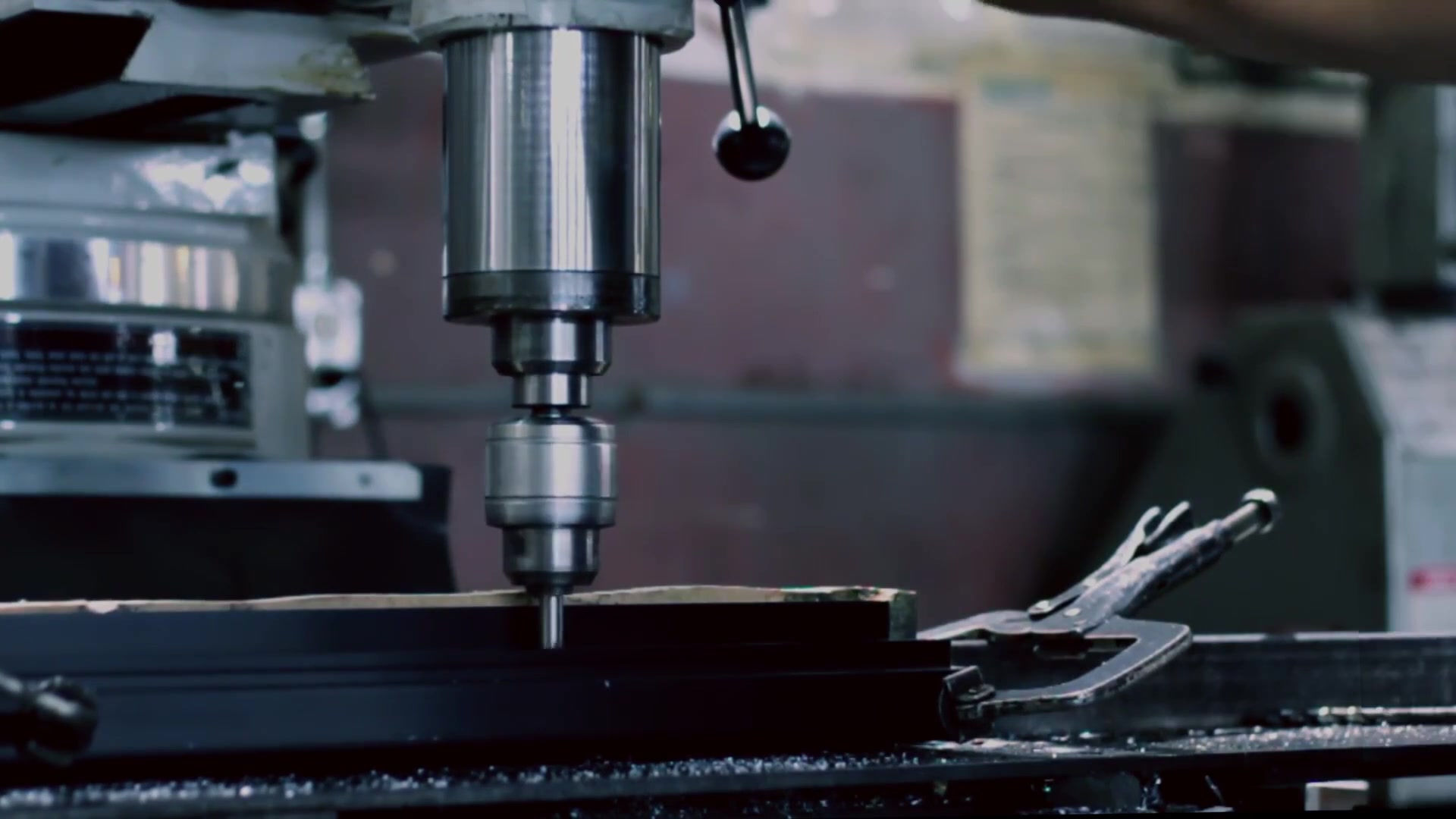
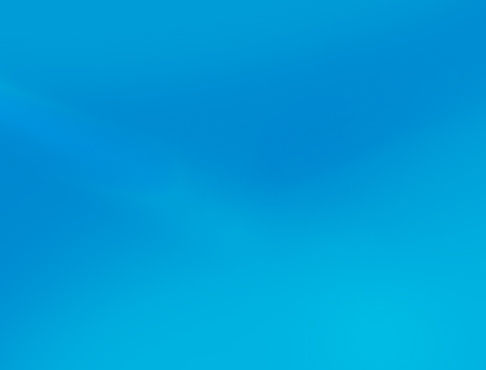
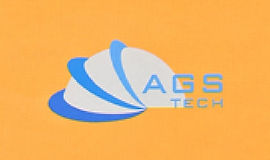
Pengeluar Tersuai Global, Penyepadu, Penyatuan, Rakan Kongsi Penyumberan Luar untuk Pelbagai Pelbagai Produk & Perkhidmatan.
Kami adalah sumber sehenti anda untuk pembuatan, fabrikasi, kejuruteraan, penyatuan, penyepaduan, penyumberan luar bagi produk & perkhidmatan buatan sendiri dan luar rak.
Pilih Bahasa anda
-
Pembuatan Tersuai
-
Pembuatan Kontrak Domestik & Global
-
Penyumberan Luar Pembuatan
-
Perolehan Domestik & Global
-
Consolidation
-
Integrasi Kejuruteraan
-
Perkhidmatan Kejuruteraan
Di antara banyak teknik JOIN yang kami gunakan dalam pembuatan, penekanan khusus diberikan kepada KIMPALAN, BRAZING, PEMATERIAN, IKATAN PELEKAT dan PERHIMPUNAN MEKANIKAL TERSUAI kerana teknik ini digunakan secara meluas dalam aplikasi seperti pembuatan pemasangan hermetik, pembuatan produk berteknologi tinggi dan pengedap khusus. Di sini kita akan menumpukan pada aspek yang lebih khusus bagi teknik penyambungan ini kerana ia berkaitan dengan pembuatan produk dan pemasangan termaju.
KIMPALAN FUSION: Kami menggunakan haba untuk mencairkan dan menggabungkan bahan. Haba dibekalkan oleh elektrik atau rasuk tenaga tinggi. Jenis-jenis kimpalan gabungan yang kami gunakan ialah KIMPALAN GAS OXYFUEL, KIMPALAN ARKA, KIMPALAN RUK TENAGA TINGGI.
KIMPALAN KEADAAN PEPEJAL: Kami menyambung bahagian tanpa lebur dan cantuman. Kaedah kimpalan keadaan pepejal kami ialah SEJUK, ULTRASONIK, RINTANGAN, GESARAN, KIMPALAN LETUPAN dan IKATAN RESAP.
BRAZING & SOLDERING: Mereka menggunakan logam pengisi dan memberi kita kelebihan bekerja pada suhu yang lebih rendah daripada dalam kimpalan, sekali gus mengurangkan kerosakan struktur pada produk. Maklumat tentang kemudahan pateri kami yang menghasilkan kelengkapan seramik kepada logam, pengedap hermetik, suapan vakum, komponen kawalan vakum dan bendalir tinggi dan ultratinggi boleh didapati di sini:Brosur Kilang Pateri
IKATAN PELEKAT: Kerana kepelbagaian pelekat yang digunakan dalam industri dan juga kepelbagaian aplikasi, kami mempunyai halaman khusus untuk ini. Untuk pergi ke halaman kami tentang ikatan pelekat, sila klik di sini.
PERHIMPUNAN MEKANIKAL TERSUAI: Kami menggunakan pelbagai pengikat seperti bolt, skru, nat, rivet. Pengikat kami tidak terhad kepada pengikat luar rak standard. Kami mereka bentuk, membangun dan mengeluarkan pengikat khusus yang diperbuat daripada bahan bukan standard supaya ia boleh memenuhi keperluan untuk aplikasi khas. Kadangkala elektrik atau haba bukan kekonduksian dikehendaki manakala kadangkala kekonduksian. Untuk beberapa aplikasi khas, pelanggan mungkin mahukan pengikat khas yang tidak boleh ditanggalkan tanpa memusnahkan produk. Terdapat idea dan aplikasi yang tidak berkesudahan. Kami mempunyai semuanya untuk anda, jika tidak di luar rak kami boleh membangunkannya dengan cepat. Untuk pergi ke halaman kami mengenai pemasangan mekanikal, sila klik di sini. Mari kita periksa pelbagai teknik cantuman kami dengan lebih terperinci.
KIMPALAN GAS OXYFUEL (OFW): Kami menggunakan gas bahan api yang dicampur dengan oksigen untuk menghasilkan nyalaan kimpalan. Apabila kita menggunakan asetilena sebagai bahan api dan oksigen, kita memanggilnya kimpalan gas oksiasetilena. Dua tindak balas kimia berlaku dalam proses pembakaran gas oxyfuel:
C2H2 + O2 ------» 2CO + H2 + Haba
2CO + H2 + 1.5 O2--------» 2 CO2 + H2O + Haba
Tindak balas pertama mengasingkan asetilena kepada karbon monoksida dan hidrogen sambil menghasilkan kira-kira 33% daripada jumlah haba yang dijana. Proses kedua di atas mewakili pembakaran selanjutnya hidrogen dan karbon monoksida sambil menghasilkan kira-kira 67% daripada jumlah haba. Suhu dalam nyalaan adalah antara 1533 hingga 3573 Kelvin. Peratusan oksigen dalam campuran gas adalah penting. Jika kandungan oksigen lebih daripada separuh, nyalaan menjadi agen pengoksidaan. Ini tidak diingini untuk sesetengah logam tetapi diingini untuk yang lain. Satu contoh apabila nyalaan pengoksidaan adalah wajar ialah aloi berasaskan kuprum kerana ia membentuk lapisan pempasifan di atas logam. Sebaliknya, apabila kandungan oksigen dikurangkan, pembakaran penuh tidak dapat dilakukan dan nyalaan menjadi nyalaan pengurangan (karburisasi). Suhu dalam nyalaan yang berkurangan adalah lebih rendah dan oleh itu ia sesuai untuk proses seperti pematerian dan pematerian. Gas lain juga merupakan bahan api yang berpotensi, tetapi ia mempunyai beberapa kelemahan berbanding asetilena. Sesekali kami membekalkan logam pengisi ke zon kimpalan dalam bentuk rod pengisi atau wayar. Sebahagian daripadanya disalut dengan fluks untuk melambatkan pengoksidaan permukaan dan dengan itu melindungi logam cair. Manfaat tambahan yang diberikan oleh fluks kepada kita ialah penyingkiran oksida dan bahan lain dari zon kimpalan. Ini membawa kepada ikatan yang lebih kuat. Variasi kimpalan gas oxyfuel ialah KIMPALAN GAS TEKANAN, di mana kedua-dua komponen dipanaskan pada antara muka mereka menggunakan obor gas oksiasetilena dan apabila antara muka mula cair, obor ditarik dan daya paksi dikenakan untuk menekan kedua-dua bahagian bersama-sama. sehingga antara muka menjadi padat.
KIMPALAN ARKA: Kami menggunakan tenaga elektrik untuk menghasilkan arka di antara hujung elektrod dan bahagian yang hendak dikimpal. Bekalan kuasa boleh menjadi AC atau DC manakala elektrod sama ada boleh digunakan atau tidak boleh digunakan. Pemindahan haba dalam kimpalan arka boleh dinyatakan dengan persamaan berikut:
H / l = ex VI / v
Di sini H ialah input haba, l ialah panjang kimpalan, V dan I ialah voltan dan arus yang digunakan, v ialah kelajuan kimpalan dan e ialah kecekapan proses. Lebih tinggi kecekapan "e" lebih berfaedah tenaga yang ada digunakan untuk mencairkan bahan. Input haba juga boleh dinyatakan sebagai:
H = ux (Volume) = ux A xl
Di sini u ialah tenaga khusus untuk lebur, A keratan rentas kimpalan dan l panjang kimpalan. Daripada dua persamaan di atas kita boleh mendapatkan:
v = ex VI / u A
Satu variasi kimpalan arka ialah KIMPALAN ARKA LOGAM BERSHIELDED (SMAW) yang membentuk kira-kira 50% daripada semua proses kimpalan industri dan penyelenggaraan. KIMPALAN ARKA ELEKTRIK (KIMPALAN STIK) dilakukan dengan menyentuh hujung elektrod bersalut pada bahan kerja dan dengan cepat menariknya ke jarak yang mencukupi untuk mengekalkan arka. Kami memanggil proses ini juga kimpalan kayu kerana elektrod adalah kayu nipis dan panjang. Semasa proses kimpalan, hujung elektrod cair bersama salutannya dan logam asas di sekitar arka. Campuran logam asas, logam elektrod dan bahan daripada salutan elektrod menjadi pejal di kawasan kimpalan. Salutan elektrod menyahoksida dan menyediakan gas pelindung di kawasan kimpalan, dengan itu melindunginya daripada oksigen dalam persekitaran. Oleh itu proses itu dirujuk sebagai kimpalan arka logam terlindung. Kami menggunakan arus antara 50 dan 300 Ampere dan aras kuasa biasanya kurang daripada 10 kW untuk prestasi kimpalan yang optimum. Juga penting ialah kekutuban arus DC (arah aliran arus). Kekutuban lurus di mana bahan kerja positif dan elektrod negatif lebih disukai dalam mengimpal kepingan logam kerana penembusannya yang cetek dan juga untuk sambungan dengan jurang yang sangat lebar. Apabila kita mempunyai kekutuban terbalik, iaitu elektrod adalah positif dan bahan kerja negatif kita boleh mencapai penembusan kimpalan yang lebih mendalam. Dengan arus AC, kerana kita mempunyai arka berdenyut, kita boleh mengimpal bahagian tebal menggunakan elektrod diameter besar dan arus maksimum. Kaedah kimpalan SMAW sesuai untuk ketebalan bahan kerja 3 hingga 19 mm dan lebih banyak lagi menggunakan teknik berbilang laluan. Sanga yang terbentuk di atas kimpalan perlu dikeluarkan menggunakan berus dawai, supaya tiada kakisan dan kegagalan di kawasan kimpalan. Ini sudah tentu menambah kos kimpalan arka logam terlindung. Walau bagaimanapun, SMAW adalah teknik kimpalan yang paling popular dalam industri dan kerja pembaikan.
KIMPALAN ARKA TERAM (SAW): Dalam proses ini kami melindungi arka kimpalan menggunakan bahan fluks berbutir seperti kapur, silika, kalsium florida, mangan oksida….dsb. Fluks berbutir dimasukkan ke dalam zon kimpalan melalui aliran graviti melalui muncung. Fluks yang meliputi zon kimpalan lebur melindungi dengan ketara daripada percikan api, asap, sinaran UV….dll dan bertindak sebagai penebat haba, dengan itu membiarkan haba menembusi jauh ke dalam bahan kerja. Fluks yang tidak bercantum dipulihkan, dirawat dan digunakan semula. Satu gegelung kosong digunakan sebagai elektrod dan disuap melalui tiub ke kawasan kimpalan. Kami menggunakan arus antara 300 dan 2000 Amperes. Proses kimpalan arka tenggelam (SAW) adalah terhad kepada kedudukan mendatar dan rata dan kimpalan bulat jika putaran struktur bulat (seperti paip) boleh dilakukan semasa mengimpal. Kelajuan boleh mencapai 5 m/min. Proses SAW sesuai untuk plat tebal dan menghasilkan kimpalan yang berkualiti tinggi, lasak, mulur dan seragam. Produktiviti, iaitu jumlah bahan kimpalan yang didepositkan setiap jam adalah 4 hingga 10 kali ganda jumlah berbanding dengan proses SMAW.
Satu lagi proses kimpalan arka, iaitu GAS METAL ARC WELDING (GMAW) atau secara alternatif disebut sebagai METAL INERT GAS WELDING (MIG) adalah berdasarkan kawasan kimpalan yang dilindungi oleh sumber gas luar seperti helium, argon, karbon dioksida….dll. Mungkin terdapat deoxidizer tambahan dalam logam elektrod. Wayar boleh guna disalurkan melalui muncung ke dalam zon kimpalan. Fabrikasi yang melibatkan logam ferus bot dan bukan ferus dijalankan menggunakan kimpalan arka logam gas (GMAW). Produktiviti kimpalan adalah kira-kira 2 kali ganda daripada proses SMAW. Peralatan kimpalan automatik sedang digunakan. Logam dipindahkan dalam salah satu daripada tiga cara dalam proses ini: "Pemindahan Semburan" melibatkan pemindahan beberapa ratus titisan logam kecil sesaat dari elektrod ke kawasan kimpalan. Dalam "Pemindahan Globular" sebaliknya, gas kaya karbon dioksida digunakan dan globul logam cair digerakkan oleh arka elektrik. Arus kimpalan adalah tinggi dan penembusan kimpalan lebih dalam, kelajuan kimpalan lebih besar daripada pemindahan semburan. Oleh itu pemindahan globular adalah lebih baik untuk mengimpal bahagian yang lebih berat. Akhir sekali, dalam kaedah "Litar Pendek", hujung elektrod menyentuh kolam kimpalan cair, litar pintasnya sebagai logam pada kadar lebih 50 titisan/saat dipindahkan dalam titisan individu. Arus dan voltan rendah digunakan bersama dengan wayar yang lebih nipis. Kuasa yang digunakan adalah kira-kira 2 kW dan suhu yang agak rendah, menjadikan kaedah ini sesuai untuk kepingan nipis dengan ketebalan kurang daripada 6mm.
Satu lagi variasi proses FLUX-CORED ARC WELDING (FCAW) adalah serupa dengan kimpalan arka logam gas, kecuali elektrod adalah tiub yang diisi dengan fluks. Kelebihan menggunakan elektrod fluks berteras ialah ia menghasilkan arka yang lebih stabil, memberi kita peluang untuk menambah baik sifat logam kimpalan, sifat fluksnya yang kurang rapuh dan fleksibel berbanding dengan kimpalan SMAW, kontur kimpalan yang dipertingkatkan. Elektrod teras terlindung sendiri mengandungi bahan yang melindungi zon kimpalan terhadap atmosfera. Kami menggunakan kuasa kira-kira 20 kW. Seperti proses GMAW, proses FCAW juga menawarkan peluang untuk mengautomasikan proses untuk kimpalan berterusan, dan ia menjimatkan. Kimia logam kimpalan yang berbeza boleh dibangunkan dengan menambahkan pelbagai aloi kepada teras fluks.
Dalam KIMPALAN ELECTROGAS (EGW) kami mengimpal kepingan yang diletakkan tepi ke tepi. Ia kadangkala juga dipanggil KIMPALAN BUTT. Logam kimpalan dimasukkan ke dalam rongga kimpalan antara dua kepingan yang hendak dicantumkan. Ruang itu dikelilingi oleh dua empangan yang disejukkan air untuk mengelakkan sanga lebur daripada mencurah keluar. Empangan digerakkan ke atas oleh pemacu mekanikal. Apabila bahan kerja boleh diputar, kita boleh menggunakan teknik kimpalan elektrogas untuk mengimpal lilitan paip juga. Elektrod disuap melalui saluran untuk mengekalkan arka berterusan. Arus boleh sekitar 400Amperes atau 750 Ampere dan aras kuasa sekitar 20 kW. Gas lengai yang berasal daripada elektrod berteras fluks atau sumber luaran menyediakan perisai. Kami menggunakan kimpalan elektrogas (EGW) untuk logam seperti keluli, titanium….dll dengan ketebalan dari 12mm hingga 75mm. Teknik ini sesuai untuk struktur besar.
Namun, dalam teknik lain yang dipanggil ELECTROSLAG WELDING (ESW) arka dinyalakan di antara elektrod dan bahagian bawah bahan kerja dan fluks ditambah. Apabila sanga lebur sampai ke hujung elektrod, arka terpadam. Tenaga dibekalkan secara berterusan melalui rintangan elektrik sanga lebur. Kami boleh mengimpal plat dengan ketebalan antara 50 mm dan 900 mm dan lebih tinggi. Arus adalah sekitar 600 Ampere manakala voltan adalah antara 40 – 50 V. Kelajuan kimpalan adalah sekitar 12 hingga 36 mm/min. Aplikasi adalah serupa dengan kimpalan elektrogas.
Salah satu proses elektrod tidak boleh habis kami, KIMPALAN GAS TUNGSTEN ARC (GTAW) juga dikenali sebagai KIMPALAN GAS INERT TUNGSTEN (TIG) melibatkan pembekalan logam pengisi dengan wayar. Untuk sambungan rapat kadangkala kami tidak menggunakan logam pengisi. Dalam proses TIG kami tidak menggunakan fluks, tetapi menggunakan argon dan helium untuk perisai. Tungsten mempunyai takat lebur yang tinggi dan tidak digunakan dalam proses kimpalan TIG, oleh itu arus malar serta jurang arka boleh dikekalkan. Tahap kuasa adalah antara 8 hingga 20 kW dan arus sama ada pada 200 Ampere (DC) atau 500 Ampere (AC). Untuk aluminium dan magnesium kami menggunakan arus AC untuk fungsi pembersihan oksidanya. Untuk mengelakkan pencemaran elektrod tungsten, kami mengelakkan sentuhannya dengan logam cair. Kimpalan Arka Tungsten Gas (GTAW) amat berguna untuk mengimpal logam nipis. Kimpalan GTAW adalah berkualiti tinggi dengan kemasan permukaan yang baik.
Disebabkan oleh kos gas hidrogen yang lebih tinggi, teknik yang kurang kerap digunakan ialah KIMPALAN HIDROGEN ATOM (AHW), di mana kami menjana lengkok antara dua elektrod tungsten dalam suasana pelindung gas hidrogen yang mengalir. AHW juga merupakan proses kimpalan elektrod yang tidak boleh digunakan. Gas hidrogen diatomik H2 terurai kepada bentuk atomnya berhampiran arka kimpalan di mana suhu melebihi 6273 Kelvin. Semasa pecah, ia menyerap sejumlah besar haba daripada arka. Apabila atom hidrogen menyerang zon kimpalan yang merupakan permukaan yang agak sejuk, ia bergabung semula ke dalam bentuk diatomik dan membebaskan haba yang disimpan. Tenaga boleh diubah dengan menukar bahan kerja kepada jarak arka.
Dalam satu lagi proses elektrod yang tidak boleh digunakan, KIMPALAN ARKA PLASMA (PAW) kita mempunyai arka plasma pekat yang diarahkan ke arah zon kimpalan. Suhu mencapai 33,273 Kelvin dalam PAW. Bilangan elektron dan ion yang hampir sama membentuk gas plasma. Arka pandu arus rendah memulakan plasma yang berada di antara elektrod tungsten dan orifis. Arus operasi biasanya sekitar 100 Ampere. Logam pengisi boleh diberi makan. Dalam kimpalan arka plasma, perisai dicapai dengan cincin perisai luar dan menggunakan gas seperti argon dan helium. Dalam kimpalan arka plasma, arka mungkin berada di antara elektrod dan bahan kerja atau antara elektrod dan muncung. Teknik kimpalan ini mempunyai kelebihan berbanding kaedah lain yang mempunyai kepekatan tenaga yang lebih tinggi, keupayaan kimpalan yang lebih dalam dan lebih sempit, kestabilan arka yang lebih baik, kelajuan kimpalan yang lebih tinggi sehingga 1 meter/min, herotan haba yang kurang. Kami biasanya menggunakan kimpalan arka plasma untuk ketebalan kurang daripada 6 mm dan kadangkala sehingga 20 mm untuk aluminium dan titanium.
KIMPALAN RASUK TENAGA TINGGI: Satu lagi jenis kaedah kimpalan gabungan dengan kimpalan rasuk elektron (EBW) dan kimpalan laser (LBW) sebagai dua varian. Teknik ini mempunyai nilai khusus untuk kerja pembuatan produk berteknologi tinggi kami. Dalam kimpalan rasuk elektron, elektron berkelajuan tinggi menyerang bahan kerja dan tenaga kinetiknya ditukar kepada haba. Rasuk elektron yang sempit bergerak dengan mudah dalam kebuk vakum. Secara amnya kami menggunakan vakum tinggi dalam kimpalan e-beam. Plat setebal 150 mm boleh dikimpal. Tiada gas pelindung, bahan fluks atau pengisi diperlukan. Senapang rasuk elektron mempunyai kapasiti 100 kW. Kimpalan dalam dan sempit dengan nisbah aspek tinggi sehingga 30 dan zon kecil yang terjejas haba adalah mungkin. Kelajuan kimpalan boleh mencapai 12 m/min. Dalam kimpalan sinar laser kami menggunakan laser berkuasa tinggi sebagai sumber haba. Rasuk laser sekecil 10 mikron dengan ketumpatan tinggi membolehkan penembusan dalam ke dalam bahan kerja. Nisbah kedalaman-ke-lebar sebanyak 10 adalah mungkin dengan kimpalan sinar laser. Kami menggunakan kedua-dua laser gelombang berdenyut serta berterusan, dengan yang pertama digunakan untuk bahan nipis dan yang kedua kebanyakannya untuk bahan kerja tebal sehingga kira-kira 25 mm. Tahap kuasa adalah sehingga 100 kW. Kimpalan pancaran laser tidak sesuai untuk bahan optik yang sangat reflektif. Gas juga boleh digunakan dalam proses kimpalan. Kaedah kimpalan sinar laser sangat sesuai untuk automasi & pembuatan volum tinggi dan boleh menawarkan kelajuan kimpalan antara 2.5 m/min dan 80 m/min. Satu kelebihan utama yang ditawarkan oleh teknik kimpalan ini ialah akses ke kawasan di mana teknik lain tidak boleh digunakan. Pancaran laser boleh dengan mudah bergerak ke kawasan yang sukar. Tiada vakum seperti dalam kimpalan rasuk elektron diperlukan. Kimpalan dengan kualiti & kekuatan yang baik, pengecutan rendah, herotan rendah, keliangan rendah boleh diperolehi dengan kimpalan pancaran laser. Rasuk laser boleh dimanipulasi dan dibentuk dengan mudah menggunakan kabel gentian optik. Oleh itu, teknik ini sangat sesuai untuk mengimpal pemasangan hermetik ketepatan, pakej elektronik...dsb.
Mari kita lihat teknik KIMPALAN SOLID STATE kami. KIMPALAN SEJUK (CW) ialah satu proses di mana tekanan dan bukannya haba dikenakan menggunakan acuan atau gulung pada bahagian yang dikawinkan. Dalam kimpalan sejuk, sekurang-kurangnya satu daripada bahagian mengawan perlu mulur. Keputusan terbaik diperoleh dengan dua bahan yang serupa. Jika kedua-dua logam yang hendak dicantum dengan kimpalan sejuk adalah berbeza, kita mungkin mendapat sambungan yang lemah dan rapuh. Kaedah kimpalan sejuk sangat sesuai untuk bahan kerja yang lembut, mulur dan kecil seperti sambungan elektrik, tepi bekas sensitif haba, jalur dwilogam untuk termostat...dsb. Satu variasi kimpalan sejuk ialah ikatan gulung (atau kimpalan gulung), di mana tekanan dikenakan melalui sepasang gulung. Kadangkala kami melakukan kimpalan gulung pada suhu tinggi untuk kekuatan antara muka yang lebih baik.
Satu lagi proses kimpalan keadaan pepejal yang kami gunakan ialah KIMPALAN ULTRASONIK (USW), di mana bahan kerja tertakluk kepada daya normal statik dan tegasan ricih berayun. Tegasan ricih berayun dikenakan melalui hujung transduser. Kimpalan ultrasonik menggunakan ayunan dengan frekuensi dari 10 hingga 75 kHz. Dalam beberapa aplikasi seperti kimpalan jahitan, kami menggunakan cakera kimpalan berputar sebagai hujungnya. Tegasan ricih yang dikenakan pada bahan kerja menyebabkan ubah bentuk plastik kecil, memecahkan lapisan oksida, bahan cemar dan membawa kepada ikatan keadaan pepejal. Suhu yang terlibat dalam kimpalan ultrasonik adalah jauh di bawah suhu takat lebur untuk logam dan tiada pelakuran berlaku. Kami kerap menggunakan proses kimpalan ultrasonik (USW) untuk bahan bukan logam seperti plastik. Walau bagaimanapun, dalam termoplastik, suhu mencapai takat lebur.
Satu lagi teknik popular, dalam KIMPALAN GESARAN (FRW) haba dijana melalui geseran pada antara muka bahan kerja yang hendak dicantumkan. Dalam kimpalan geseran kami memastikan salah satu bahan kerja tidak bergerak manakala bahan kerja yang lain dipegang dalam lekapan dan diputar pada kelajuan malar. Bahan kerja kemudiannya disentuh di bawah daya paksi. Kelajuan permukaan putaran dalam kimpalan geseran mungkin mencapai 900m/min dalam beberapa kes. Selepas sentuhan antara muka yang mencukupi, bahan kerja berputar dihentikan secara tiba-tiba dan daya paksi meningkat. Zon kimpalan biasanya merupakan kawasan yang sempit. Teknik kimpalan geseran boleh digunakan untuk menyambung bahagian pepejal dan tiub yang diperbuat daripada pelbagai bahan. Sesetengah denyar mungkin berkembang pada antara muka dalam FRW, tetapi denyar ini boleh dikeluarkan dengan pemesinan atau pengisaran sekunder. Variasi proses kimpalan geseran wujud. Contohnya "kimpalan geseran inersia" melibatkan roda tenaga yang tenaga kinetik putarannya digunakan untuk mengimpal bahagian. Kimpalan selesai apabila roda tenaga terhenti. Jisim berputar boleh diubah dan dengan itu tenaga kinetik putaran. Satu lagi variasi ialah "kimpalan geseran linear", di mana gerakan salingan linear dikenakan pada sekurang-kurangnya satu daripada komponen yang akan dicantumkan. Dalam bahagian kimpalan geseran linear tidak perlu bulat, ia boleh menjadi segi empat tepat, persegi atau bentuk lain. Kekerapan boleh dalam puluhan Hz, amplitud dalam julat milimeter dan tekanan dalam puluhan atau ratusan MPa. Akhirnya "kimpalan kacau geseran" agak berbeza daripada dua yang lain yang dijelaskan di atas. Manakala dalam kimpalan geseran inersia dan kimpalan geseran linear pemanasan antara muka dicapai melalui geseran dengan menggosok dua permukaan yang bersentuhan, dalam kaedah kimpalan kacau geseran badan ketiga digosok pada dua permukaan yang hendak dicantumkan. Alat berputar dengan diameter 5 hingga 6 mm disentuh dengan sambungan. Suhu boleh meningkat kepada nilai antara 503 hingga 533 Kelvin. Pemanasan, pencampuran dan kacau bahan dalam sendi berlaku. Kami menggunakan kimpalan kacau geseran pada pelbagai bahan termasuk aluminium, plastik dan komposit. Kimpalan adalah seragam dan berkualiti tinggi dengan liang minimum. Tiada asap atau percikan dihasilkan dalam kimpalan kacau geseran dan prosesnya adalah automatik.
KIMPALAN RINTANGAN (RW): Haba yang diperlukan untuk mengimpal dihasilkan oleh rintangan elektrik antara dua bahan kerja yang hendak dicantum. Tiada fluks, gas pelindung atau elektrod boleh guna digunakan dalam kimpalan rintangan. Pemanasan joule berlaku dalam kimpalan rintangan dan boleh dinyatakan sebagai:
H = (Petak I) x R xtx K
H ialah haba yang dijana dalam joule (watt-saat), arus I dalam Ampere, rintangan R dalam Ohms, t ialah masa dalam saat arus mengalir. Faktor K kurang daripada 1 dan mewakili pecahan tenaga yang tidak hilang melalui sinaran dan pengaliran. Arus dalam proses kimpalan rintangan boleh mencapai tahap setinggi 100,000 A tetapi voltan biasanya 0.5 hingga 10 Volt. Elektrod biasanya diperbuat daripada aloi kuprum. Kedua-dua bahan yang serupa dan tidak serupa boleh disambungkan dengan kimpalan rintangan. Beberapa variasi wujud untuk proses ini: "Kimpalan titik rintangan" melibatkan dua elektrod bulat bertentangan yang menghubungi permukaan sambungan pusingan kedua-dua helaian. Tekanan dikenakan sehingga arus dimatikan. Nuget kimpalan biasanya berdiameter sehingga 10 mm. Kimpalan titik rintangan meninggalkan tanda lekukan yang sedikit berubah warna pada titik kimpalan. Kimpalan titik ialah teknik kimpalan rintangan kami yang paling popular. Pelbagai bentuk elektrod digunakan dalam kimpalan titik untuk mencapai kawasan yang sukar. Peralatan kimpalan tempat kami dikawal oleh CNC dan mempunyai pelbagai elektrod yang boleh digunakan serentak. Satu lagi variasi "kimpalan jahitan rintangan" dijalankan dengan elektrod roda atau penggelek yang menghasilkan kimpalan titik berterusan apabila arus mencapai tahap yang cukup tinggi dalam kitaran kuasa AC. Sambungan yang dihasilkan oleh kimpalan jahitan rintangan adalah ketat cecair dan gas. Kelajuan kimpalan kira-kira 1.5 m/min adalah normal untuk kepingan nipis. Seseorang boleh menggunakan arus terputus-putus supaya kimpalan titik dihasilkan pada selang waktu yang dikehendaki di sepanjang jahitan. Dalam "kimpalan unjuran rintangan" kami menimbulkan satu atau lebih unjuran (lesung pipit) pada salah satu permukaan bahan kerja yang akan dikimpal. Unjuran ini mungkin bulat atau bujur. Suhu setempat yang tinggi dicapai di tempat timbul yang bersentuhan dengan bahagian mengawan. Elektrod memberikan tekanan untuk memampatkan unjuran ini. Elektrod dalam kimpalan unjuran rintangan mempunyai hujung rata dan merupakan aloi kuprum yang disejukkan dengan air. Kelebihan kimpalan unjuran rintangan ialah keupayaan kami untuk beberapa kimpalan dalam satu lejang, oleh itu hayat elektrod dilanjutkan, keupayaan untuk mengimpal kepingan pelbagai ketebalan, keupayaan untuk mengimpal nat dan bolt ke kepingan. Kelemahan kimpalan unjuran rintangan ialah kos tambahan untuk mengeluarkan lesung pipit. Satu lagi teknik, dalam "kimpalan kilat" haba dihasilkan daripada arka di hujung kedua-dua bahan kerja apabila ia mula bersentuhan. Kaedah ini juga boleh dianggap sebagai kimpalan arka. Suhu di antara muka meningkat, dan bahan menjadi lembut. Daya paksi dikenakan dan kimpalan terbentuk di kawasan lembut. Selepas kimpalan kilat selesai, sambungan boleh dimesin untuk penampilan yang lebih baik. Kualiti kimpalan yang diperolehi dengan kimpalan kilat adalah baik. Tahap kuasa adalah 10 hingga 1500 kW. Kimpalan kilat sesuai untuk penyambungan tepi-ke-tepi bagi logam yang serupa atau tidak serupa sehingga diameter 75 mm dan kepingan antara 0.2 mm hingga 25 mm ketebalan. "Kimpalan arka stud" sangat serupa dengan kimpalan kilat. Stud seperti bolt atau rod berulir berfungsi sebagai satu elektrod semasa dicantumkan pada bahan kerja seperti plat. Untuk menumpukan haba yang dijana, mengelakkan pengoksidaan dan mengekalkan logam cair dalam zon kimpalan, cincin seramik pakai buang diletakkan di sekeliling sambungan. Akhirnya "kimpalan perkusi" satu lagi proses kimpalan rintangan, menggunakan kapasitor untuk membekalkan tenaga elektrik. Dalam kimpalan perkusi, kuasa dilepaskan dalam masa milisaat dengan cepat menghasilkan haba setempat yang tinggi pada sambungan. Kami menggunakan kimpalan perkusi secara meluas dalam industri pembuatan elektronik di mana pemanasan komponen elektronik sensitif di sekitar sambungan perlu dielakkan.
Teknik yang dipanggil KIMPALAN LETUPAN melibatkan letupan lapisan bahan letupan yang diletakkan di atas salah satu bahan kerja yang hendak dicantumkan. Tekanan yang sangat tinggi yang dikenakan pada bahan kerja menghasilkan antara muka yang bergelora dan beralun dan saling mengunci mekanikal berlaku. Kekuatan ikatan dalam kimpalan letupan adalah sangat tinggi. Kimpalan letupan adalah kaedah yang baik untuk pelapisan plat dengan logam yang berbeza. Selepas pelapisan, plat boleh digulung menjadi bahagian yang lebih nipis. Kadang-kadang kami menggunakan kimpalan letupan untuk mengembangkan tiub supaya ia dimeterai rapat pada plat.
Kaedah terakhir kami dalam domain penyambungan keadaan pepejal ialah SAMBUNGAN RESAPAN atau KIMPALAN RESAPAN (DFW) di mana sambungan yang baik dicapai terutamanya melalui resapan atom merentasi antara muka. Beberapa ubah bentuk plastik pada antara muka juga menyumbang kepada kimpalan. Suhu yang terlibat adalah sekitar 0.5 Tm di mana Tm ialah suhu lebur logam. Kekuatan ikatan dalam kimpalan resapan bergantung pada tekanan, suhu, masa sentuhan dan kebersihan permukaan sentuhan. Kadangkala kami menggunakan logam pengisi di antara muka. Haba dan tekanan diperlukan dalam ikatan resapan dan dibekalkan oleh rintangan elektrik atau relau dan pemberat mati, tekan atau sebaliknya. Logam yang serupa dan tidak serupa boleh dicantumkan dengan kimpalan resapan. Proses ini agak perlahan disebabkan oleh masa yang diperlukan untuk atom berhijrah. DFW boleh diautomasikan dan digunakan secara meluas dalam fabrikasi bahagian kompleks untuk industri aeroangkasa, elektronik, perubatan. Produk yang dikeluarkan termasuk implan ortopedik, penderia, ahli struktur aeroangkasa. Ikatan resapan boleh digabungkan dengan PEMBENTUKAN SUPERPLASTIC untuk menghasilkan struktur kepingan logam yang kompleks. Lokasi terpilih pada helaian adalah pertama difusi terikat dan kemudian kawasan tidak terikat dikembangkan menjadi acuan menggunakan tekanan udara. Struktur aeroangkasa dengan nisbah kekakuan-kepada-berat yang tinggi dihasilkan menggunakan gabungan kaedah ini. Proses gabungan kimpalan resapan / pembentukan superplastik mengurangkan bilangan bahagian yang diperlukan dengan menghapuskan keperluan untuk pengikat, menghasilkan bahagian yang sangat tepat tekanan rendah secara ekonomi dan dengan masa pendahuluan yang singkat.
BRAZING: Teknik pematerian dan pematerian melibatkan suhu yang lebih rendah daripada suhu yang diperlukan untuk mengimpal. Walau bagaimanapun, suhu pematerian lebih tinggi daripada suhu pematerian. Dalam pematerian logam pengisi diletakkan di antara permukaan yang hendak dicantum dan suhu dinaikkan kepada suhu lebur bahan pengisi melebihi 723 Kelvin tetapi di bawah suhu lebur bahan kerja. Logam cair memenuhi ruang yang rapat antara bahan kerja. Penyejukan dan pemejalan seterusnya logam penyambung menghasilkan sambungan yang kuat. Dalam kimpalan braze logam pengisi diendapkan pada sambungan. Lebih banyak logam pengisi digunakan dalam kimpalan pateri berbanding pematerian. Obor oksiasetilena dengan nyalaan pengoksidaan digunakan untuk mendepositkan logam pengisi dalam kimpalan pateri. Disebabkan oleh suhu yang lebih rendah dalam pematerian, masalah pada zon yang terjejas haba seperti ledingan dan tegasan baki adalah kurang. Semakin kecil jurang kelegaan dalam pematerian semakin tinggi kekuatan ricih sambungan. Walau bagaimanapun, kekuatan tegangan maksimum dicapai pada jurang optimum (nilai puncak). Di bawah dan di atas nilai optimum ini, kekuatan tegangan dalam pematerian berkurangan. Kelegaan biasa dalam pematerian boleh antara 0.025 dan 0.2 mm. Kami menggunakan pelbagai bahan pematerian dengan bentuk yang berbeza seperti persembahan, serbuk, cincin, dawai, jalur…..dsb. dan boleh mengeluarkan persembahan ini khas untuk reka bentuk atau geometri produk anda. Kami juga menentukan kandungan bahan pematerian mengikut bahan asas dan aplikasi anda. Kami kerap menggunakan fluks dalam operasi pematerian untuk membuang lapisan oksida yang tidak diingini dan mencegah pengoksidaan. Untuk mengelakkan kakisan seterusnya, fluks biasanya dikeluarkan selepas operasi penyambungan. AGS-TECH Inc. menggunakan pelbagai kaedah pematerian, termasuk:
- Memateri Obor
- Pateri Relau
- Memateri Induksi
- Memateri Rintangan
- Dip Brazing
- Memateri Inframerah
- Pateri Penyebaran
- Pancaran Tenaga Tinggi
Contoh sambungan brazed kami yang paling biasa diperbuat daripada logam yang berbeza dengan kekuatan yang baik seperti bit gerudi karbida, sisipan, pakej hermetik optoelektronik, pengedap.
PEMATERIAN : Ini adalah salah satu teknik kami yang paling kerap digunakan di mana pateri (logam pengisi) mengisi sambungan seperti dalam pematerian antara komponen yang dipasang rapat. Pateri kami mempunyai takat lebur di bawah 723 Kelvin. Kami menggunakan pematerian manual dan automatik dalam operasi pembuatan. Berbanding dengan pematerian, suhu pematerian lebih rendah. Pematerian tidak begitu sesuai untuk aplikasi suhu tinggi atau kekuatan tinggi. Kami menggunakan pateri tanpa plumbum serta aloi timah-plumbum, timah-zink, plumbum-perak, kadmium-perak, zink-aluminium selain yang lain untuk pematerian. Kedua-dua berasaskan resin tidak menghakis serta asid dan garam tak organik digunakan sebagai fluks dalam pematerian. Kami menggunakan fluks khas untuk memateri logam dengan kebolehpaterian rendah. Dalam aplikasi di mana kita perlu memateri bahan seramik, kaca atau grafit, kita mula-mula menyadur bahagian dengan logam yang sesuai untuk meningkatkan kebolehmaterian. Teknik pematerian popular kami ialah:
-Pematerian Aliran Semula atau Tampal
-Pematerian Gelombang
-Pematerian Relau
-Pematerian Obor
-Pematerian Induksi
-Pematerian Besi
-Pematerian Rintangan
-Pematerian celup
-Pematerian Ultrasonik
-Pematerian Inframerah
Penyolderan ultrasonik menawarkan kepada kami kelebihan unik di mana keperluan untuk fluks dihapuskan disebabkan oleh kesan peronggaan ultrasonik yang mengeluarkan filem oksida daripada permukaan yang dicantumkan. Reflow dan Wave pematerian adalah teknik industri kami yang cemerlang untuk pembuatan volum tinggi dalam elektronik dan oleh itu patut dijelaskan dengan lebih terperinci. Dalam pematerian aliran semula, kami menggunakan pes separa pepejal yang termasuk zarah logam pateri. Tampalan diletakkan pada sendi menggunakan proses saringan atau stensilan. Dalam papan litar bercetak (PCB) kami kerap menggunakan teknik ini. Apabila komponen elektrik diletakkan pada pad ini daripada tampal, tegangan permukaan memastikan bungkusan pelekap permukaan sejajar. Selepas meletakkan komponen, kami memanaskan pemasangan di dalam relau supaya pematerian aliran semula berlaku. Semasa proses ini, pelarut dalam pes menguap, fluks dalam pes diaktifkan, komponen dipanaskan terlebih dahulu, zarah pateri dicairkan dan membasahi sambungan, dan akhirnya pemasangan PCB disejukkan dengan perlahan. Teknik popular kedua kami untuk pengeluaran papan PCB volum tinggi, iaitu pematerian gelombang bergantung pada fakta bahawa pemateri lebur permukaan logam basah dan membentuk ikatan yang baik hanya apabila logam dipanaskan terlebih dahulu. Gelombang laminar berdiri pateri cair mula-mula dihasilkan oleh pam dan PCB yang dipanaskan dan prafluks disalurkan ke atas gelombang. Pateri membasahkan hanya permukaan logam yang terdedah tetapi tidak membasahi bungkusan polimer IC mahupun papan litar bersalut polimer. Pancutan air panas berkelajuan tinggi meniup lebihan pateri daripada sambungan dan menghalang penyambungan antara petunjuk bersebelahan. Dalam pematerian gelombang bungkusan pelekap permukaan kami mula-mula mengikatnya pada papan litar sebelum pematerian. Sekali lagi saringan dan stensilan digunakan tetapi kali ini untuk epoksi. Selepas komponen diletakkan di lokasi yang betul, epoksi disembuhkan, papan diterbalikkan dan pematerian gelombang berlaku.