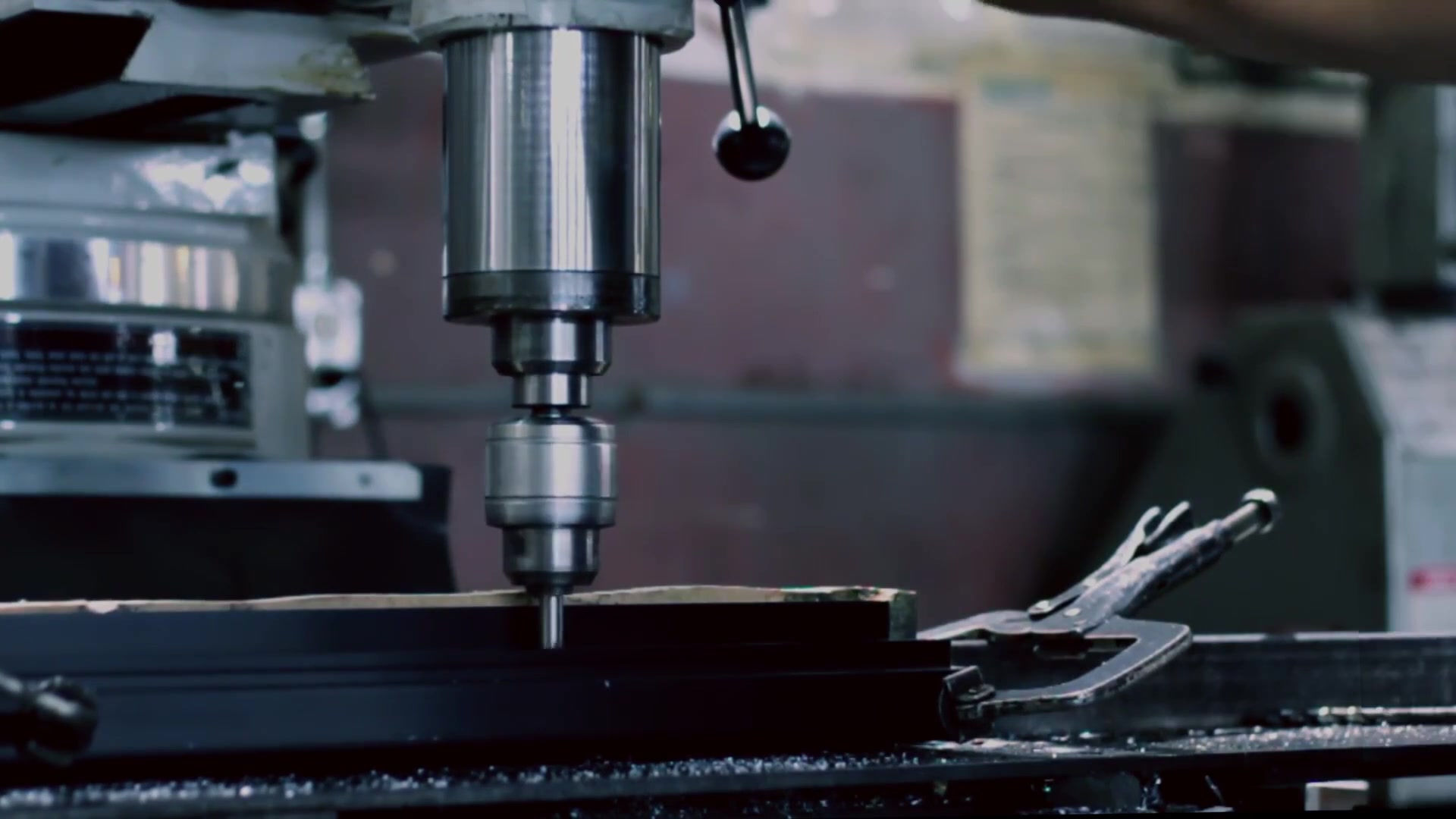
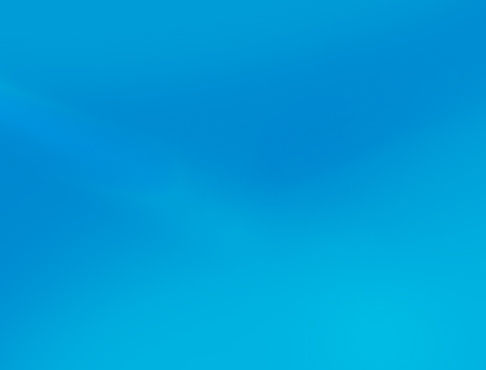
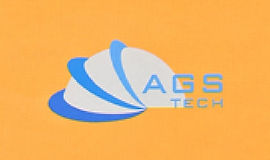
Wereldwijd op maat gemaakte fabrikant, integrator, consolidator, outsourcingpartner voor een breed scala aan producten en diensten.
Wij zijn uw one-stop-bron voor productie, fabricage, engineering, consolidatie, integratie, outsourcing van op maat gemaakte en off-shelf producten en diensten.
Choose your Language
-
Aangepaste productie
-
Binnenlandse en wereldwijde contractproductie
-
Uitbesteding van productie
-
Binnenlandse en wereldwijde inkoop
-
Consolidatie
-
Engineering-integratie
-
Ingenieursdiensten
De laatste jaren zien we een toename van de vraag naar RAPID MANUFACTURING of RAPID PROTOTYPING. Dit proces kan ook DESKTOP MANUFACTURING of FREE-FORM FABRICATION worden genoemd. In principe wordt een solide fysiek model van een onderdeel rechtstreeks gemaakt van een driedimensionale CAD-tekening. We gebruiken de term ADDITIVE MANUFACTURING voor deze verschillende technieken waarbij we onderdelen in lagen bouwen. Met behulp van geïntegreerde computergestuurde hardware en software voeren we additive manufacturing uit. Onze snelle prototyping- en productietechnieken zijn STEREOLITHOGRAFIE, POLYJET, FUSED-DEPOSITION MODELING, SELECTIVE LASER SINTERING, ELEKTRONBEAM Smelten, DRIEDIMENSIONAAL PRINTEN, DIRECT MANUFACTURING, RAPID TOOLING. We raden u aan hier te klikken om:DOWNLOAD onze schematische illustraties van additieve productie en snelle productieprocessen door AGS-TECH Inc.
Dit zal u helpen de informatie die we u hieronder verstrekken beter te begrijpen.
Rapid prototyping biedt ons: 1.) Het conceptuele productontwerp wordt vanuit verschillende hoeken bekeken op een monitor met behulp van een 3D / CAD-systeem. 2.) Prototypes van niet-metalen en metalen materialen worden vervaardigd en bestudeerd vanuit functionele, technische en esthetische aspecten. 3.) Prototyping tegen lage kosten in een zeer korte tijd wordt bereikt. Additive manufacturing kan lijken op de constructie van een brood door afzonderlijke sneetjes op elkaar te stapelen en te lijmen. Met andere woorden, het product wordt plak voor plak vervaardigd, of laag voor laag op elkaar aangebracht. De meeste onderdelen kunnen binnen enkele uren worden geproduceerd. De techniek is goed als onderdelen heel snel nodig zijn of als de benodigde hoeveelheden laag zijn en het maken van een mal en gereedschap te duur en tijdrovend is. De kosten van een onderdeel zijn echter duur vanwege de dure grondstoffen.
• STEREOLITHOGRAFIE: Deze techniek, ook wel afgekort als STL, is gebaseerd op het uitharden en uitharden van een vloeibaar fotopolymeer in een specifieke vorm door er een laserstraal op te focussen. De laser polymeriseert het fotopolymeer en hardt het uit. Door de UV-laserstraal volgens de geprogrammeerde vorm langs het oppervlak van het fotopolymeermengsel te scannen, wordt het onderdeel van onder naar boven geproduceerd in afzonderlijke plakjes die op elkaar vallen. Het scannen van de laserspot wordt vele malen herhaald om de in het systeem geprogrammeerde geometrieën te bereiken. Nadat het onderdeel volledig is vervaardigd, wordt het van het platform verwijderd, geblot en ultrasoon en met een alcoholbad gereinigd. Vervolgens wordt het een paar uur blootgesteld aan UV-straling om ervoor te zorgen dat het polymeer volledig is uitgehard en uitgehard. Om het proces samen te vatten, wordt een platform dat is gedompeld in een fotopolymeermengsel en een UV-laserstraal bestuurd en verplaatst door een servo-controlesysteem volgens de vorm van het gewenste onderdeel en het onderdeel wordt verkregen door het polymeer laag voor laag uit te harden. Uiteraard worden de maximale afmetingen van het geproduceerde onderdeel bepaald door de stereolithografische apparatuur.
• POLYJET: Net als bij inkjetprinten, hebben we bij polyjet acht printkoppen die fotopolymeer op de buildtray deponeren. Ultraviolet licht dat naast de jets wordt geplaatst, hardt onmiddellijk uit en verhardt elke laag. In polyjet worden twee materialen gebruikt. Het eerste materiaal is voor het vervaardigen van het eigenlijke model. Het tweede materiaal, een gelachtige hars, wordt gebruikt voor ondersteuning. Deze beide materialen worden laag voor laag afgezet en gelijktijdig uitgehard. Na voltooiing van het model wordt het dragermateriaal verwijderd met een waterige oplossing. De gebruikte harsen zijn vergelijkbaar met stereolithografie (STL). De polyjet heeft de volgende voordelen ten opzichte van stereolithografie: 1.) Onderdelen reinigen is niet nodig. 2.) Nabehandeling niet nodig 3.) Kleinere laagdiktes zijn mogelijk en daardoor krijgen we een betere resolutie en kunnen we fijnere onderdelen vervaardigen.
• FUSED DEPOSITION MODELING : Ook afgekort als FDM, bij deze methode beweegt een robotgestuurde extruderkop in twee principiële richtingen over een tafel. De kabel wordt indien nodig naar beneden en naar boven gebracht. Uit de opening van een verwarmde matrijs op de kop wordt een thermoplastisch filament geëxtrudeerd en een eerste laag wordt op een schuimbasis aangebracht. Dit wordt bereikt door de extruderkop die een vooraf bepaald pad volgt. Na de eerste laag wordt de tafel neergelaten en worden volgende lagen op elkaar gedeponeerd. Soms zijn bij het vervaardigen van een gecompliceerd onderdeel ondersteuningsstructuren nodig zodat de depositie in bepaalde richtingen kan doorgaan. In deze gevallen wordt een dragermateriaal geëxtrudeerd met een minder dichte afstand van filament op een laag, zodat het zwakker is dan het modelmateriaal. Deze draagstructuren kunnen later na voltooiing van het onderdeel worden opgelost of afgebroken. De afmetingen van de extrudermatrijs bepalen de dikte van de geëxtrudeerde lagen. Het FDM-proces produceert onderdelen met getrapte oppervlakken op schuine buitenvlakken. Als deze ruwheid onaanvaardbaar is, kan chemisch polijsten met damp of een verwarmd gereedschap worden gebruikt om deze glad te maken. Zelfs een polijstwas is beschikbaar als coatingmateriaal om deze stappen te elimineren en redelijke geometrische toleranties te bereiken.
• SELECTIEVE LASER SINTERING: Ook wel aangeduid als SLS, is het proces gebaseerd op het selectief sinteren van een polymeer, keramiek of metaalpoeder in een object. De bodem van de verwerkingskamer heeft twee cilinders: een gedeeltelijk gebouwde cilinder en een poedertoevoercilinder. De eerstgenoemde wordt stapsgewijs neergelaten tot waar het gesinterde onderdeel wordt gevormd en de laatste wordt stapsgewijs omhoog gebracht om poeder via een rolmechanisme aan de deelcilinder toe te voeren. Eerst wordt een dunne laag poeder afgezet in de gedeeltelijk gebouwde cilinder, vervolgens wordt een laserstraal op die laag gefocust, waarbij een bepaalde dwarsdoorsnede wordt getraceerd en gesmolten / gesinterd, die vervolgens weer stolt tot een vaste stof. Het poeder is dat gebieden die niet door de laserstraal worden geraakt, los blijven maar wel het vaste gedeelte ondersteunen. Vervolgens wordt er nog een laag poeder aangebracht en wordt het proces vele malen herhaald om het onderdeel te verkrijgen. Op het einde worden de losse poederdeeltjes eraf geschud. Al deze worden uitgevoerd door een procesbesturingscomputer met behulp van instructies die worden gegenereerd door het 3D CAD-programma van het onderdeel dat wordt vervaardigd. Verschillende materialen zoals polymeren (zoals ABS, PVC, polyester), was, metalen en keramiek met geschikte polymeerbindmiddelen kunnen worden afgezet.
• ELECTRON-BEAM MELTING: vergelijkbaar met selectief lasersinteren, maar met behulp van elektronenstraal om titanium- of kobaltchroompoeders te smelten om prototypes in vacuüm te maken. Er zijn enkele ontwikkelingen gedaan om dit proces uit te voeren op roestvast staal, aluminium en koperlegeringen. Als de vermoeiingssterkte van de geproduceerde onderdelen moet worden verhoogd, gebruiken we heet isostatisch persen na de fabricage van het onderdeel als secundair proces.
• DRIEDIMENSIONAAL PRINTEN: Ook wel aangeduid met 3DP, bij deze techniek deponeert een printkop een anorganisch bindmiddel op een laag niet-metalen of metaalpoeder. Een zuiger die het poederbed draagt, wordt stapsgewijs neergelaten en bij elke stap wordt het bindmiddel laag voor laag gedeponeerd en door het bindmiddel versmolten. Gebruikte poedermaterialen zijn mengsels en vezels van polymeren, gietzand, metalen. Door gelijktijdig verschillende bindkoppen en verschillende kleuren bindmiddelen te gebruiken, kunnen we verschillende kleuren verkrijgen. Het proces is vergelijkbaar met inkjetprinten, maar in plaats van een gekleurd vel te verkrijgen, verkrijgen we een gekleurd driedimensionaal object. De geproduceerde onderdelen kunnen poreus zijn en kunnen daarom sinteren en metaalinfiltratie vereisen om de dichtheid en sterkte te vergroten. Sinteren zal het bindmiddel verbranden en de metaalpoeders samensmelten. Metalen zoals roestvrij staal, aluminium, titanium kunnen worden gebruikt om de onderdelen te maken en als infiltratiemateriaal gebruiken we meestal koper en brons. Het mooie van deze techniek is dat zelfs gecompliceerde en bewegende assemblages zeer snel kunnen worden vervaardigd. Er kan bijvoorbeeld een tandwielsamenstel, een moersleutel als gereedschap worden gemaakt en hebben bewegende en draaiende onderdelen klaar voor gebruik. Verschillende componenten van de assemblage kunnen in verschillende kleuren worden vervaardigd en allemaal in één keer. Download onze brochure op:Basisprincipes van 3D-printen van metaal
• DIRECT MANUFACTURING en RAPID TOOLING: Naast ontwerpevaluatie, troubleshooting gebruiken we rapid prototyping voor directe fabricage van producten of directe toepassing in producten. Met andere woorden, rapid prototyping kan worden opgenomen in conventionele processen om ze beter en concurrerender te maken. Rapid prototyping kan bijvoorbeeld patronen en mallen produceren. Patronen van een smeltend en brandend polymeer gecreëerd door snelle prototyping-operaties kunnen worden geassembleerd voor investeringsgieten en geïnvesteerd. Een ander voorbeeld om te noemen is het gebruik van 3DP om een keramische gietschaal te produceren en die te gebruiken voor schaalgietbewerkingen. Zelfs spuitgietmatrijzen en matrijsinzetstukken kunnen worden geproduceerd door middel van rapid prototyping en men kan vele weken of maanden aan doorlooptijd voor het maken van matrijzen besparen. Door alleen een CAD-bestand van het gewenste onderdeel te analyseren, kunnen we de gereedschapsgeometrie softwarematig produceren. Hier zijn enkele van onze populaire snelle tooling-methoden:
RTV (Room-Temperature Vulcanizing) MOLDING / URETHANE CASTING : Met behulp van rapid prototyping kan het patroon van het gewenste onderdeel worden gemaakt. Vervolgens wordt dit patroon gecoat met een scheidingsmiddel en wordt vloeibaar RTV-rubber over het patroon gegoten om de malhelften te produceren. Vervolgens worden deze matrijshelften gebruikt om vloeibare urethanen te spuitgieten. De levensduur van de mal is kort, slechts 0 of 30 cycli, maar voldoende voor productie in kleine series.
ACES (Acetal Clear Epoxy Solid) INJECTIEMOLEN : Met behulp van rapid prototyping-technieken zoals stereolithografie produceren we spuitgietmatrijzen. Deze mallen zijn schalen met een open uiteinde om te kunnen vullen met materialen zoals epoxy, aluminium gevulde epoxy of metalen. Nogmaals, de levensduur van de mal is beperkt tot tientallen of maximaal honderden onderdelen.
GESPUIT METALEN GEREEDSCHAPSPROCES: We gebruiken rapid prototyping en maken een patroon. We spuiten een zink-aluminium legering op het patroonoppervlak en coaten dit. Het patroon met de metalen coating wordt vervolgens in een kolf geplaatst en ingegoten met een epoxy of aluminium gevulde epoxy. Ten slotte wordt het verwijderd en door twee van dergelijke matrijshelften te produceren, verkrijgen we een complete matrijs voor spuitgieten. Deze mallen hebben een langere levensduur, in sommige gevallen kunnen ze, afhankelijk van het materiaal en de temperaturen, duizenden onderdelen produceren.
KEELTOOL-PROCES: Deze techniek kan mallen produceren met 100.000 tot 10 miljoen levenscyclussen. Met behulp van rapid prototyping maken we een RTV-mal. Vervolgens wordt de mal gevuld met een mengsel bestaande uit A6 gereedschapsstaalpoeder, wolfraamcarbide, polymeerbindmiddel en laten uitharden. Deze mal wordt vervolgens verwarmd om het polymeer te laten afbranden en de metaalpoeders te laten smelten. De volgende stap is koperinfiltratie om de uiteindelijke mal te produceren. Indien nodig kunnen secundaire bewerkingen zoals machinale bewerking en polijsten op de mal worden uitgevoerd voor een betere maatnauwkeurigheid.