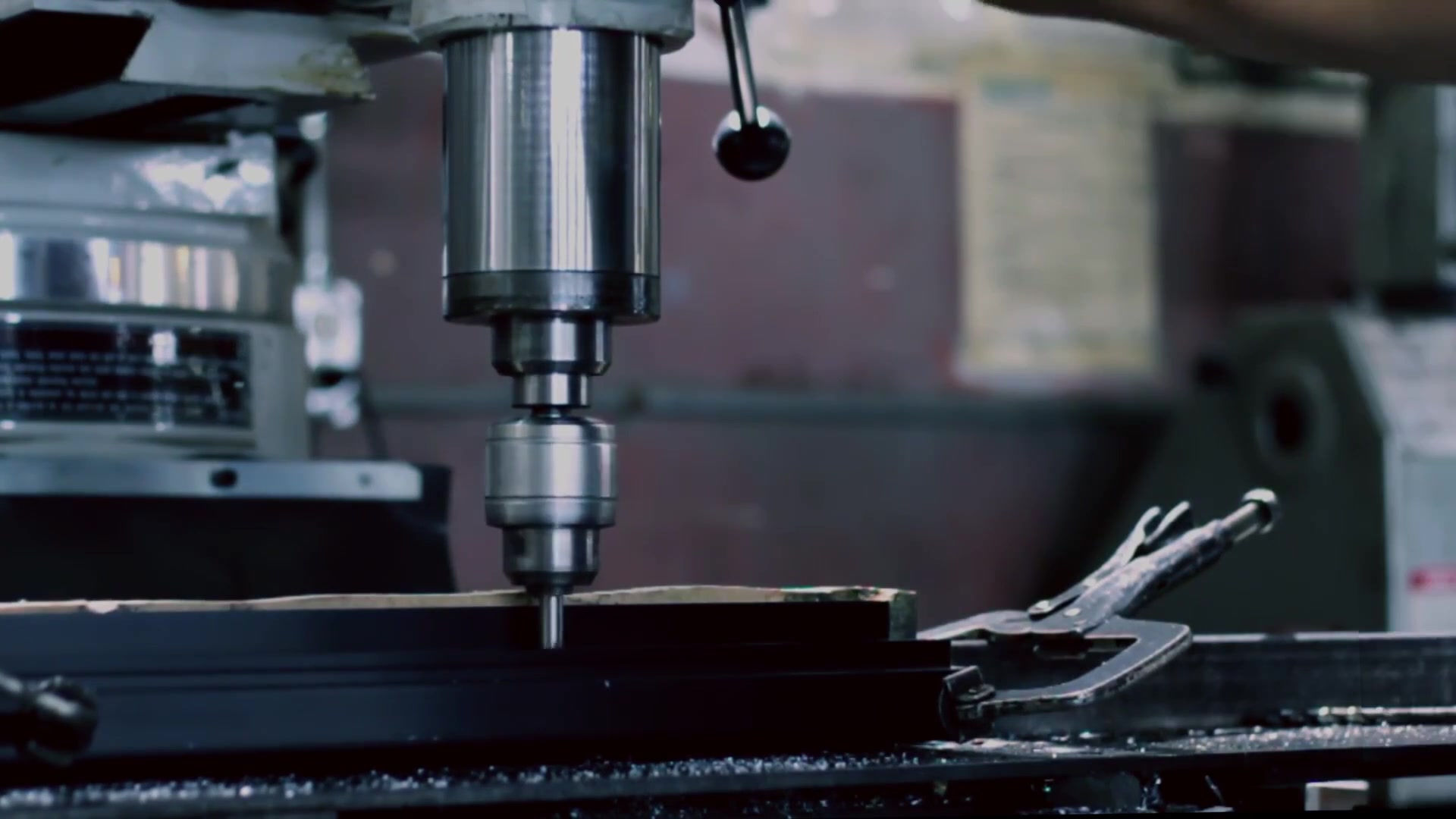
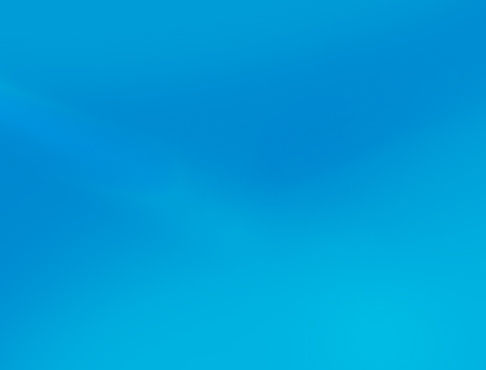
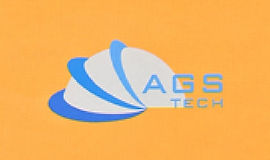
Wereldwijd op maat gemaakte fabrikant, integrator, consolidator, outsourcingpartner voor een breed scala aan producten en diensten.
Wij zijn uw one-stop-bron voor productie, fabricage, engineering, consolidatie, integratie, outsourcing van op maat gemaakte en off-shelf producten en diensten.
Choose your Language
-
Aangepaste productie
-
Binnenlandse en wereldwijde contractproductie
-
Uitbesteding van productie
-
Binnenlandse en wereldwijde inkoop
-
Consolidatie
-
Engineering-integratie
-
Ingenieursdiensten
Onze op maat gemaakte giet- en bewerkingstechnieken zijn vervangbare en niet-verbruikbare gietstukken, ferro- en non-ferrogietwerk, zand, matrijs, centrifugaal, continu, keramische mal, investering, verloren schuim, bijna-netvorm, permanente mal (zwaartekrachtgieten), gips mal (gipsgietwerk) en schaalgietstukken, bewerkte onderdelen geproduceerd door frezen en draaien met behulp van zowel conventionele als CNC-apparatuur, zwitserse bewerking voor hoge doorvoer, goedkope kleine precisieonderdelen, schroefbewerking voor bevestigingsmiddelen, niet-conventionele bewerking. Houd er rekening mee dat we naast metalen en metaallegeringen ook keramiek, glas en kunststof onderdelen bewerken in sommige gevallen wanneer het vervaardigen van een mal niet aantrekkelijk of niet de optie is. Het bewerken van polymeermaterialen vereist de gespecialiseerde ervaring die we hebben vanwege de uitdaging die kunststoffen en rubber met zich meebrengen vanwege hun zachtheid, niet-stijfheid ... enz. Voor het bewerken van keramiek en glas, zie onze pagina over niet-conventionele fabricage. AGS-TECH Inc. produceert en levert zowel lichtgewicht als zware gietstukken. We leveren metalen gietstukken en bewerkte onderdelen voor ketels, warmtewisselaars, auto's, micromotoren, windturbines, voedselverpakkingsapparatuur en meer. We raden u aan hier te klikken om DOWNLOAD onze schematische illustraties van bewerkings- en gietprocessen door AGS-TECH Inc.
Dit zal u helpen de informatie die we u hieronder verstrekken beter te begrijpen. Laten we eens kijken naar enkele van de verschillende technieken die we aanbieden in detail:
• EXPENDABLE MOLD CASTING: Deze brede categorie verwijst naar methoden waarbij tijdelijke en niet-herbruikbare mallen worden gebruikt. Voorbeelden zijn zand, gips, schelpen, inbedmassa (ook wel verloren was genoemd) en gipsafgietsel.
• ZANDGIETEN: een proces waarbij zand als malmateriaal wordt gebruikt. Een zeer oude methode en nog steeds erg populair in de mate dat de meeste metalen gietstukken met deze techniek worden gemaakt. Lage kosten, zelfs bij lage productie. Geschikt voor de productie van kleine en grote onderdelen. De techniek kan worden gebruikt om onderdelen binnen enkele dagen of weken te vervaardigen met zeer weinig investeringen. Het vochtige zand wordt met klei, bindmiddelen of speciale oliën aan elkaar gehecht. Zand zit over het algemeen in vormbakken en spouw- en poortsystemen worden gecreëerd door het zand rond modellen te verdichten. De processen zijn:
1.) Het model in zand plaatsen om de mal te maken
2.) Opname van model en zand in een poortsysteem
3.) Model verwijderen
4.) Vullen van vormholte met gesmolten metaal
5.) Afkoeling van het metaal
6.) Het breken van de zandvorm en het verwijderen van het gietstuk
• GIPSGIETEN: Vergelijkbaar met zandgieten, en in plaats van zand wordt gips uit Parijs gebruikt als malmateriaal. Korte productiedoorlooptijden zoals zandgieten en goedkoop. Goede maattoleranties en oppervlakteafwerking. Het grote nadeel is dat het alleen kan worden gebruikt met metalen met een laag smeltpunt, zoals aluminium en zink.
• SHELL MOLD CASTING : Ook vergelijkbaar met zandgieten. Vormholte verkregen door geharde schaal van zand en thermohardend harsbindmiddel in plaats van een kolf gevuld met zand zoals bij het zandgietproces. Vrijwel elk metaal dat geschikt is om met zand te worden gegoten, kan worden gegoten door middel van schaalvormen. Het proces kan worden samengevat als:
1.) Vervaardiging van de schaalvorm. Het gebruikte zand heeft een veel kleinere korrelgrootte in vergelijking met zand dat wordt gebruikt bij het zandgieten. Het fijne zand wordt gemengd met thermohardende hars. Het metalen patroon is gecoat met een scheidingsmiddel om het verwijderen van de schaal gemakkelijker te maken. Daarna wordt het metaalpatroon verwarmd en wordt het zandmengsel geporeerd of geblazen op het hete gietpatroon. Een dunne schaal vormt zich op het oppervlak van het patroon. De dikte van deze schaal kan worden aangepast door de tijdsduur dat het zandharsmengsel in contact is met het metaalpatroon te variëren. Het losse zand wordt vervolgens verwijderd terwijl het met schelpen bedekte patroon overblijft.
2.) Vervolgens worden de schaal en het patroon in een oven verwarmd zodat de schaal hard wordt. Nadat het uitharden is voltooid, wordt de schaal uit het patroon geworpen met behulp van pinnen die in het patroon zijn ingebouwd.
3.) Twee van dergelijke schalen worden door lijmen of klemmen aan elkaar geassembleerd en vormen de volledige mal. Nu wordt de schaalvorm in een container gestoken waarin deze tijdens het gietproces wordt ondersteund door zand of metaalschot.
4.) Nu kan het hete metaal in de schaalvorm worden gegoten.
Voordelen van schaalgieten zijn producten met een zeer goede oppervlakteafwerking, de mogelijkheid om complexe onderdelen te vervaardigen met een hoge maatnauwkeurigheid, het proces is eenvoudig te automatiseren, economisch voor de productie van grote volumes.
Nadelen zijn dat de mallen een goede ventilatie vereisen vanwege gassen die ontstaan wanneer gesmolten metaal in contact komt met het bindmiddel, de thermohardende harsen en metaalpatronen zijn duur. Vanwege de kosten van metaalpatronen is de techniek mogelijk niet geschikt voor productieruns met een kleine hoeveelheid.
• INVESTERINGSGIET (ook bekend als LOST-WAX CASTING): Ook een zeer oude techniek en geschikt voor het vervaardigen van kwaliteitsonderdelen met hoge nauwkeurigheid, herhaalbaarheid, veelzijdigheid en integriteit van vele metalen, vuurvaste materialen en speciale hoogwaardige legeringen. Zowel kleine als grote onderdelen kunnen worden geproduceerd. Een duur proces in vergelijking met sommige van de andere methoden, maar het grote voordeel is de mogelijkheid om onderdelen te produceren met een bijna netvorm, ingewikkelde contouren en details. De kosten worden dus enigszins gecompenseerd door de eliminatie van nabewerking en bewerking in sommige gevallen. Hoewel er variaties kunnen zijn, is hier een samenvatting van het algemene gietproces voor investeringen:
1.) Creatie van origineel masterpatroon van was of plastic. Elk gietstuk heeft één patroon nodig, omdat deze tijdens het proces worden vernietigd. Er is ook een mal nodig waaruit patronen worden vervaardigd en meestal wordt de mal gegoten of machinaal bewerkt. Omdat de mal niet geopend hoeft te worden, kunnen complexe gietstukken worden bereikt, kunnen veel waspatronen worden verbonden als de takken van een boom en samen worden gegoten, waardoor de productie van meerdere onderdelen mogelijk wordt door één keer gieten van het metaal of de metaallegering.
2.) Vervolgens wordt het patroon ondergedompeld of gegoten met een vuurvaste slurry bestaande uit zeer fijnkorrelige silica, water, bindmiddelen. Dit resulteert in een keramische laag over het oppervlak van het patroon. De vuurvaste laag op het patroon laat men drogen en uitharden. Deze stap is waar de naam investeringsgieten vandaan komt: vuurvaste slurry wordt geïnvesteerd over het waspatroon.
3.) Bij deze stap wordt de geharde keramische mal ondersteboven gekeerd en verwarmd zodat de was smelt en uit de mal stroomt. Er blijft een holte achter voor het metalen gietstuk.
4.) Nadat de was eruit is, wordt de keramische mal verwarmd tot een nog hogere temperatuur, wat resulteert in versteviging van de mal.
5.) Metaalgietwerk wordt in de hete vorm gegoten en vult alle ingewikkelde secties.
6.) Gieten mag stollen
7.) Ten slotte wordt de keramische mal gebroken en worden gefabriceerde onderdelen uit de boom gesneden.
Hier is een link naar de brochure over investeringsgietinstallaties:
• VERDAMPINGSPATROON GIETEN: Het proces maakt gebruik van een patroon gemaakt van een materiaal zoals polystyreenschuim dat zal verdampen wanneer heet gesmolten metaal in de mal wordt gegoten. Er zijn twee soorten van dit proces: LOST FOAM CASTING waarbij gebruik wordt gemaakt van niet-gebonden zand en FULL MOLD CASTING waarbij gebruik wordt gemaakt van gebonden zand. Dit zijn de algemene processtappen:
1.) Vervaardig het patroon van een materiaal zoals polystyreen. Wanneer er grote hoeveelheden worden vervaardigd, wordt het patroon gegoten. Als een onderdeel een complexe vorm heeft, moeten mogelijk meerdere secties van dergelijk schuimmateriaal aan elkaar worden gehecht om het patroon te vormen. We coaten het patroon vaak met een vuurvaste verbinding om een goede oppervlakteafwerking op het gietstuk te creëren.
2.) Het patroon wordt vervolgens in vormzand gelegd.
3.) Het gesmolten metaal wordt in de mal gegoten, waarbij het schuimpatroon, dwz polystyreen in de meeste gevallen, verdampt als het door de malholte stroomt.
4.) Het gesmolten metaal wordt in de zandvorm gelaten om uit te harden.
5.) Nadat het is uitgehard, verwijderen we het gietstuk.
In sommige gevallen vereist het product dat we vervaardigen een kern binnen het patroon. Bij verdampingsgieten is het niet nodig om een kern in de vormholte te plaatsen en vast te zetten. De techniek is geschikt voor het vervaardigen van zeer complexe geometrieën, kan eenvoudig worden geautomatiseerd voor productie van grote volumes en er zijn geen scheidingslijnen in het gegoten onderdeel. Het basisproces is eenvoudig en economisch te implementeren. Voor productie van grote volumes, aangezien een matrijs of mal nodig is om de patronen van polystyreen te produceren, kan dit enigszins kostbaar zijn.
• NIET-UITBREIDBARE VORMGIETEN: Deze brede categorie verwijst naar methoden waarbij de mal niet na elke productiecyclus hoeft te worden hervormd. Voorbeelden zijn permanent, matrijs-, continu- en centrifugaalgieten. Herhaalbaarheid wordt verkregen en onderdelen kunnen worden gekarakteriseerd als NEAR NET SHAPE.
• PERMANENTE VORMGIETEN : Herbruikbare vormen van metaal worden gebruikt voor meerdere gietstukken. Een permanente mal kan over het algemeen tienduizenden keren worden gebruikt voordat deze verslijt. Over het algemeen worden zwaartekracht, gasdruk of vacuüm gebruikt om de mal te vullen. Mallen (ook wel matrijs genoemd) zijn over het algemeen gemaakt van ijzer, staal, keramiek of andere metalen. Het algemene proces is:
1.) Machine en maak de mal. Het is gebruikelijk om de mal uit twee metalen blokken te maken die in elkaar passen en kunnen worden geopend en gesloten. Zowel de onderdeelkenmerken als het poortsysteem worden over het algemeen machinaal in de gietvorm gefreesd.
2.) De interne matrijsoppervlakken zijn gecoat met een suspensie waarin vuurvaste materialen zijn verwerkt. Dit helpt de warmtestroom te beheersen en werkt als smeermiddel voor gemakkelijke verwijdering van het gegoten onderdeel.
3.) Vervolgens worden de permanente matrijshelften gesloten en wordt de matrijs verwarmd.
4.) Gesmolten metaal wordt in de vorm gegoten en stil gelaten om te stollen.
5.) Voordat er veel afkoeling plaatsvindt, verwijderen we het onderdeel uit de permanente mal met behulp van uitwerpers wanneer de malhelften worden geopend.
Voor metalen met een laag smeltpunt, zoals zink en aluminium, gebruiken we vaak permanent gieten. Voor stalen gietstukken gebruiken we grafiet als malmateriaal. Soms verkrijgen we complexe geometrieën met behulp van kernen in permanente mallen. Voordelen van deze techniek zijn gietstukken met goede mechanische eigenschappen verkregen door snelle afkoeling, uniformiteit in eigenschappen, goede nauwkeurigheid en oppervlakteafwerking, lage uitvalpercentages, mogelijkheid om het proces te automatiseren en economisch hoge volumes te produceren. Nadelen zijn de hoge initiële installatiekosten die het ongeschikt maken voor bewerkingen met een laag volume, en beperkingen op de grootte van de vervaardigde onderdelen.
• DIE CASTING: Een matrijs wordt machinaal bewerkt en gesmolten metaal wordt onder hoge druk in de vormholten geduwd. Zowel non-ferro als ferro metalen spuitgieten zijn mogelijk. Het proces is geschikt voor grote oplagen van kleine tot middelgrote onderdelen met details, extreem dunne wanden, maatvastheid en een goede oppervlakteafwerking. AGS-TECH Inc. is in staat om met deze techniek wanddiktes tot 0,5 mm te vervaardigen. Net als bij permanent gieten, moet de mal uit twee helften bestaan die kunnen openen en sluiten om het geproduceerde onderdeel te verwijderen. Een spuitgietvorm kan meerdere holtes hebben om de productie van meerdere gietstukken bij elke cyclus mogelijk te maken. Spuitgietmatrijzen zijn erg zwaar en veel groter dan de onderdelen die ze produceren, dus ook duur. We repareren en vervangen versleten matrijzen gratis voor onze klanten, zolang ze hun onderdelen bij ons nabestellen. Onze matrijzen hebben een lange levensduur in het bereik van enkele honderdduizenden cycli.
Dit zijn de basis vereenvoudigde processtappen:
1.) Productie van de mal in het algemeen van staal
2.) Schimmel geïnstalleerd op spuitgietmachine;
3.) De zuiger dwingt gesmolten metaal in de matrijsholten te stromen en vult de ingewikkelde functies en dunne wanden in
4.) Na het vullen van de mal met het gesmolten metaal, wordt het gietstuk onder druk gehard
5.) De mal wordt geopend en het gietstuk wordt verwijderd met behulp van uitwerppennen.
6.) Nu wordt de lege matrijs opnieuw gesmeerd en vastgeklemd voor de volgende cyclus.
Bij het spuitgieten gebruiken we vaak insert molding, waarbij we een extra onderdeel in de mal verwerken en het metaal eromheen gieten. Na stollen worden deze delen onderdeel van het gegoten product. Voordelen van spuitgieten zijn goede mechanische eigenschappen van de onderdelen, mogelijkheid van ingewikkelde functies, fijne details en goede oppervlakteafwerking, hoge productiesnelheden, eenvoudige automatisering. Nadelen zijn: Niet erg geschikt voor een laag volume vanwege de hoge matrijs- en apparatuurkosten, beperkingen in de vormen die kunnen worden gegoten, kleine ronde markeringen op gegoten onderdelen als gevolg van contact met uitwerppennen, dunne flits van metaal dat eruit wordt geperst bij de scheidingslijn, noodzaak voor ventilatieopeningen langs de scheidingslijn tussen de matrijs, noodzaak om de maltemperaturen laag te houden met behulp van watercirculatie.
• CENTRIFUGAAL GIETEN : Gesmolten metaal wordt in het midden van de roterende mal gegoten op de rotatie-as. Centrifugale krachten werpen het metaal naar de periferie en het laat het stollen terwijl de mal blijft draaien. Zowel horizontale als verticale asrotaties kunnen worden gebruikt. Onderdelen met ronde binnenvlakken en andere niet-ronde vormen kunnen worden gegoten. Het proces kan worden samengevat als:
1.) Gesmolten metaal wordt in een centrifugaalvorm gegoten. Het metaal wordt vervolgens door het ronddraaien van de mal naar de buitenmuren geperst.
2.) Terwijl de mal draait, wordt het metalen gietstuk hard
Centrifugaal gieten is een geschikte techniek voor de productie van holle cilindrische onderdelen zoals pijpen, geen behoefte aan sprues, risers en poortelementen, goede oppervlakteafwerking en gedetailleerde eigenschappen, geen krimpproblemen, mogelijkheid om lange pijpen met zeer grote diameters te produceren, hoge productiecapaciteit .
• CONTINU GIETEN ( STRAND CASTING ) : Wordt gebruikt om een ononderbroken stuk metaal te gieten. In principe wordt het gesmolten metaal gegoten in een tweedimensionaal profiel van de mal, maar de lengte ervan is onbepaald. Er wordt constant nieuw gesmolten metaal in de mal gevoerd terwijl het gietstuk naar beneden beweegt en de lengte ervan met de tijd toeneemt. Metalen zoals koper, staal en aluminium worden in lange strengen gegoten met behulp van een continu gietproces. Het proces kan verschillende configuraties hebben, maar de algemene kan worden vereenvoudigd als:
1.) Gesmolten metaal wordt gegoten in een container die zich hoog boven de mal bevindt met goed berekende hoeveelheden en stroomsnelheden en stroomt door de watergekoelde mal. Het metalen gietstuk dat in de mal wordt gegoten, stolt tot een startstaaf die op de bodem van de mal wordt geplaatst. Deze startstang geeft de rollen in eerste instantie iets om aan vast te grijpen.
2.) De lange metalen streng wordt met een constante snelheid door rollen gedragen. De rollen veranderen ook de richting van de stroom van metaalstreng van verticaal naar horizontaal.
3.) Nadat het continugieten een bepaalde horizontale afstand heeft afgelegd, snijdt een toorts of zaag die met het gietstuk meebeweegt het snel op de gewenste lengte.
Het continugietproces kan worden geïntegreerd met ROLLING PROCESS, waarbij het continu gegoten metaal rechtstreeks in een walserij kan worden ingevoerd om I-Beams, T-Beams ... enz. te produceren. Continu gieten produceert uniforme eigenschappen door het hele product, het heeft een hoge stollingssnelheid, verlaagt de kosten door een zeer laag materiaalverlies, biedt een proces waarbij het laden van metaal, gieten, stollen, snijden en verwijderen van het gietstuk allemaal plaatsvinden in een continue bewerking en wat resulteert in een hoge productiviteit en hoge kwaliteit. Een belangrijke overweging is echter de hoge initiële investering, installatiekosten en benodigde ruimte.
• BEWERKINGSDIENSTEN: Wij bieden drie-, vier- en vijfassige bewerkingen aan. De soort bewerkingsprocessen die wij gebruiken zijn DRAAIEN, FREZEN, BOREN, KOOREN, BRAAKKEN, SCHAFFEN, ZAGEN, SLIJPEN, LAPPEN, POLIJSTEN en NIET-TRADITIONEEL BEWERKEN dat verder wordt uitgewerkt in een ander menu van onze website. Voor het grootste deel van onze productie gebruiken we CNC-machines. Voor sommige operaties passen conventionele technieken echter beter en daarom vertrouwen we er ook op. Onze bewerkingsmogelijkheden bereiken het hoogst mogelijke niveau en sommige meest veeleisende onderdelen worden vervaardigd in een AS9100-gecertificeerde fabriek. Schoepen voor straalmotoren vereisen zeer gespecialiseerde productie-ervaring en de juiste apparatuur. De lucht- en ruimtevaartindustrie heeft zeer strikte normen. Sommige componenten met complexe geometrische structuren kunnen het gemakkelijkst worden vervaardigd door middel van vijfassige bewerking, wat alleen in sommige bewerkingsfabrieken, waaronder de onze, wordt aangetroffen. Onze lucht- en ruimtevaart gecertificeerde fabriek heeft de nodige ervaring om te voldoen aan de uitgebreide documentatie-eisen van de lucht- en ruimtevaartindustrie.
Bij DRAAIEN-bewerkingen wordt een werkstuk geroteerd en tegen een snijgereedschap bewogen. Voor dit proces wordt een machine genaamd draaibank gebruikt.
In FREZEN heeft een machine die freesmachine wordt genoemd, een roterend gereedschap om snijkanten tegen een werkstuk aan te brengen.
BOORbewerkingen omvatten een roterende frees met snijkanten die gaten produceert bij contact met het werkstuk. Over het algemeen worden boorpersen, draaibanken of molens gebruikt.
Bij BORING-bewerkingen wordt een gereedschap met een enkele gebogen puntige punt in een ruw gat in een draaiend werkstuk bewogen om het gat iets te vergroten en de nauwkeurigheid te verbeteren. Het wordt gebruikt voor fijne afwerkingsdoeleinden.
BRAAKKEN betreft een getand gereedschap om materiaal van een werkstuk te verwijderen in één doorgang van het aansnijden (getand gereedschap). Bij lineair brootsen loopt de broots lineair tegen een oppervlak van het werkstuk om de snede te bewerkstelligen, terwijl bij roterend brootsen de broots wordt geroteerd en in het werkstuk wordt gedrukt om een assymmetrische vorm te snijden.
ZWITSERSE TYPE BEWERKING is een van onze waardevolle technieken die we gebruiken voor de productie van grote hoeveelheden kleine, zeer nauwkeurige onderdelen. Met behulp van een Zwitserse draaibank draaien we kleine, complexe precisieonderdelen goedkoop. In tegenstelling tot conventionele draaibanken waar het werkstuk stationair wordt gehouden en het gereedschap in beweging wordt gehouden, mag het werkstuk in Zwitserse draaicentra in de Z-as bewegen en staat het gereedschap stil. Bij de bewerking van het Zwitserse type wordt het stafmateriaal in de machine vastgehouden en door een geleidebus in de z-as voortbewogen, waardoor alleen het te bewerken gedeelte wordt blootgelegd. Op deze manier is een stevige grip verzekerd en is de nauwkeurigheid zeer hoog. De beschikbaarheid van onder spanning staande gereedschappen biedt de mogelijkheid om te frezen en te boren terwijl het materiaal uit de geleidingsbus komt. De Y-as van de apparatuur van het Zwitserse type biedt volledige freesmogelijkheden en bespaart veel tijd bij de productie. Bovendien hebben onze machines boren en kottergereedschappen die op het onderdeel werken wanneer het in de subspil wordt gehouden. Onze bewerkingscapaciteit van het Zwitserse type geeft ons een volledig geautomatiseerde complete bewerkingsmogelijkheid in één enkele bewerking.
Verspaning is een van de grootste segmenten van de activiteiten van AGS-TECH Inc. We gebruiken het als primaire bewerking of als secundaire bewerking na het gieten of extruderen van een onderdeel, zodat aan alle tekeningspecificaties wordt voldaan.
• OPPERVLAKTE AFWERKINGSDIENSTEN: We bieden een grote verscheidenheid aan oppervlaktebehandelingen en oppervlakteafwerking, zoals oppervlaktebehandeling om de hechting te verbeteren, het afzetten van een dunne oxidelaag om de hechting van de coating te verbeteren, zandstralen, chem-film, anodiseren, nitreren, poedercoaten, spraycoaten , diverse geavanceerde metallisatie- en coatingtechnieken waaronder sputteren, elektronenstraal, verdamping, plating, harde coatings zoals diamantachtige koolstof (DLC) of titaniumcoating voor boor- en snijgereedschappen.
• PRODUCTMARKERING & ETIKETTERINGSDIENSTEN: Veel van onze klanten hebben behoefte aan markering en etikettering, lasermarkering, gravure op metalen onderdelen. Als u een dergelijke behoefte heeft, laten we dan bespreken welke optie het beste voor u is.
Hier zijn enkele veelgebruikte metalen gegoten producten. Omdat deze kant-en-klaar zijn, kunt u besparen op matrijskosten als een van deze aan uw eisen voldoet:
KLIK HIER OM onze 11-serie gegoten aluminium dozen van AGS-Electronics te downloaden