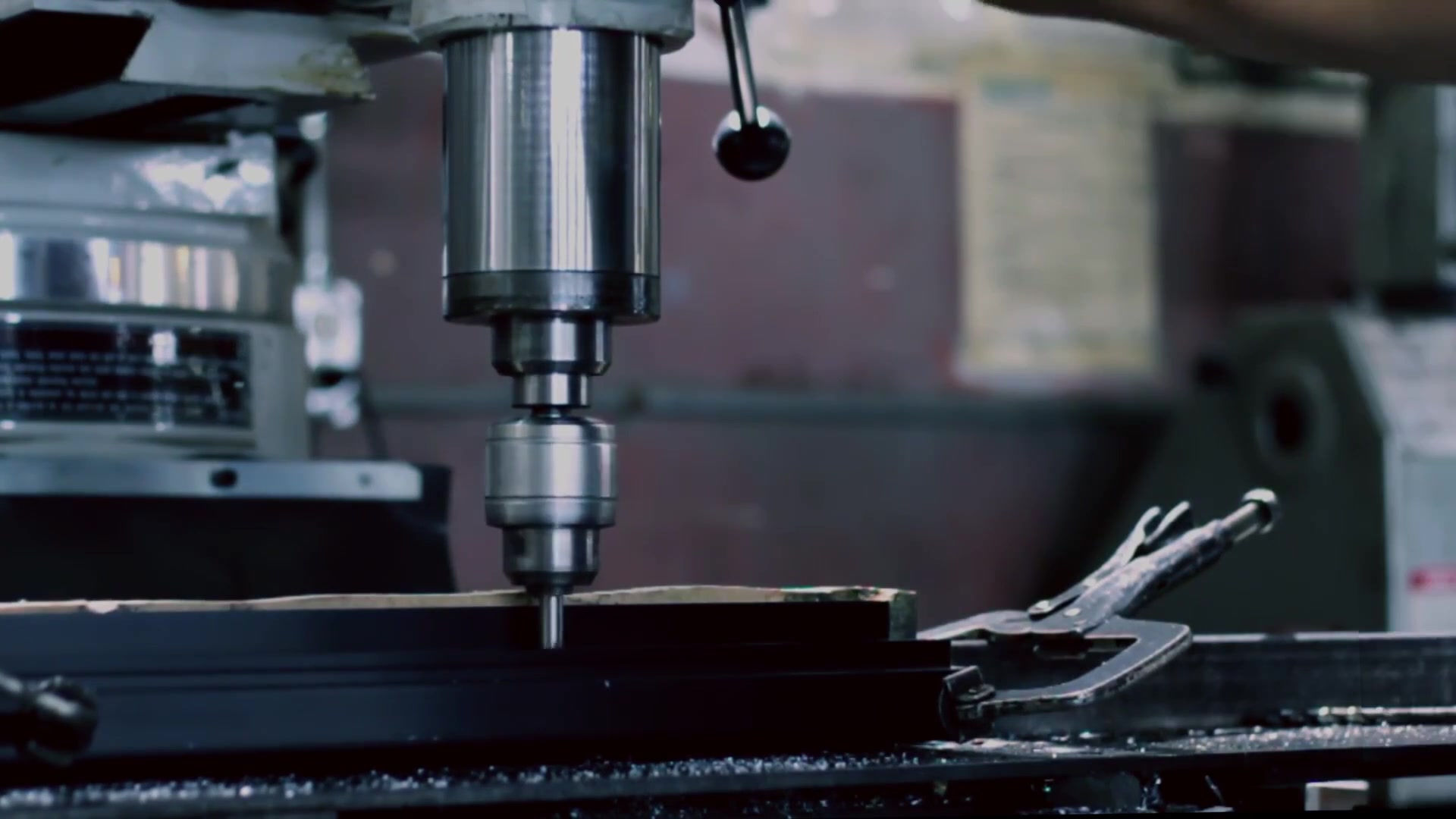
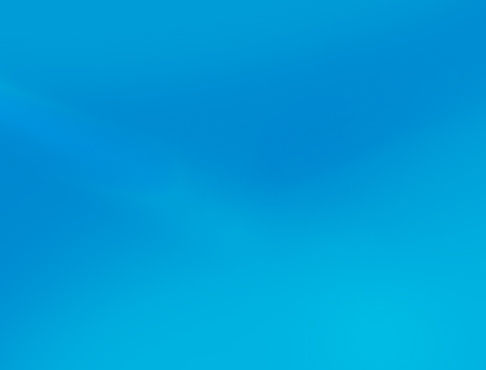
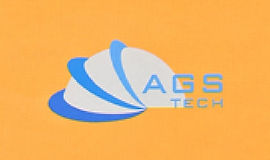
Wereldwijd op maat gemaakte fabrikant, integrator, consolidator, outsourcingpartner voor een breed scala aan producten en diensten.
Wij zijn uw one-stop-bron voor productie, fabricage, engineering, consolidatie, integratie, outsourcing van op maat gemaakte en off-shelf producten en diensten.
Choose your Language
-
Aangepaste productie
-
Binnenlandse en wereldwijde contractproductie
-
Uitbesteding van productie
-
Binnenlandse en wereldwijde inkoop
-
Consolidatie
-
Engineering-integratie
-
Ingenieursdiensten
Wij verbinden, assembleren en bevestigen uw gefabriceerde onderdelen en verwerken ze tot eindproducten of halffabrikaten met behulp van LASSEN, SOLDEREN, SOLDEREN, SINTEREN, LIJMEN, BEVESTIGEN, PASSEN. Enkele van onze meest populaire lasprocessen zijn booglassen, autogeengas, weerstand, projectie, naad, stuiklassen, percussie, vaste toestand, elektronenstraal, laser, thermiet, inductielassen. Onze populaire soldeerprocessen zijn toorts-, inductie-, oven- en dompelsolderen. Onze soldeermethoden zijn ijzer, hete plaat, oven, inductie, dip, golf, reflow en ultrasoon solderen. Voor het lijmen gebruiken we vaak thermoplasten en thermoharders, epoxy's, fenolen, polyurethaan, lijmlegeringen en enkele andere chemicaliën en tapes. Tot slot bestaan onze bevestigingsprocessen uit spijkeren, schroeven, bouten en moeren, klinken, clinchen, pinnen, stikken & nieten en persen.
• LASSEN : Lassen omvat het samenvoegen van materialen door de werkstukken te smelten en toevoegmateriaal toe te voegen, dat ook het gesmolten smeltbad verbindt. Als het gebied afkoelt, krijgen we een sterke verbinding. In sommige gevallen wordt druk uitgeoefend. In tegenstelling tot lassen, omvatten de soldeer- en soldeerbewerkingen alleen het smelten van een materiaal met een lager smeltpunt tussen de werkstukken, en werkstukken smelten niet. We raden u aan hier te klikken om:DOWNLOAD onze schematische illustraties van lasprocessen door AGS-TECH Inc.
Dit zal u helpen de informatie die we u hieronder verstrekken beter te begrijpen.
Bij ARC WELDING gebruiken we een voeding en een elektrode om een elektrische boog te creëren die de metalen doet smelten. Laspunt wordt beschermd door een beschermgas of damp of ander materiaal. Dit proces is populair voor het lassen van auto-onderdelen en staalconstructies. Bij afgeschermd metaalbooglassen (SMAW) of ook wel staaflassen genoemd, wordt een elektrodestaaf dicht bij het basismateriaal gebracht en daartussen wordt een elektrische boog gegenereerd. De elektrodestaaf smelt en fungeert als vulmateriaal. De elektrode bevat ook flux die fungeert als een laag slakken en dampen afgeeft die als beschermgas fungeren. Deze beschermen het lasgebied tegen milieuvervuiling. Er worden geen andere vulstoffen gebruikt. De nadelen van dit proces zijn de traagheid, de noodzaak om de elektroden vaak te vervangen, de noodzaak om de resterende slak die afkomstig is van het vloeimiddel weg te hakken. Een aantal metalen zoals ijzer, staal, nikkel, aluminium, koper... enz. Kan worden gelast. De voordelen zijn de goedkope tools en het gebruiksgemak. Gasmetaalbooglassen (GMAW), ook bekend als metaal-inert gas (MIG), we hebben een continue toevoer van een verbruikbare elektrodedraadvuller en een inert of gedeeltelijk inert gas dat rond de draad stroomt tegen omgevingsverontreiniging van het lasgebied. Staal, aluminium en andere non-ferro metalen kunnen worden gelast. De voordelen van MIG zijn hoge lassnelheden en een goede kwaliteit. De nadelen zijn de gecompliceerde uitrusting en de uitdagingen waarmee we worden geconfronteerd in winderige buitenomgevingen, omdat we het beschermgas rond het lasgebied stabiel moeten houden. Een variant van GMAW is flux-Cored Arc Welding (FCAW) dat bestaat uit een fijne metalen buis gevuld met fluxmaterialen. Soms is de flux in de buis voldoende om te beschermen tegen milieuverontreiniging. Ondergedompeld booglassen (SAW) is een algemeen geautomatiseerd proces, waarbij continue draadaanvoer en boog onder een laag fluxdekking wordt geslagen. De productiesnelheden en kwaliteit zijn hoog, lasslakken komen er makkelijk af en we hebben een rookvrije werkomgeving. Het nadeel is dat het alleen kan worden gebruikt om parts in bepaalde posities te lassen. Bij gas-wolfraambooglassen (GTAW) of wolfraam-inert gaslassen (TIG) gebruiken we een wolfraamelektrode samen met een aparte vulstof en inerte of bijna inerte gassen. Zoals we weten heeft Tungsten een hoog smeltpunt en is het een zeer geschikt metaal voor zeer hoge temperaturen. Het wolfraam in TIG wordt niet verbruikt in tegenstelling tot de andere hierboven toegelichte methoden. Een langzame maar hoogwaardige lastechniek die voordelig is boven andere technieken bij het lassen van dunne materialen. Geschikt voor veel metalen. Plasmabooglassen is vergelijkbaar, maar gebruikt plasmagas om de boog te creëren. De boog bij plasmabooglassen is relatief meer geconcentreerd in vergelijking met GTAW en kan worden gebruikt voor een breder scala aan metaaldiktes bij veel hogere snelheden. GTAW en plasmabooglassen kunnen op min of meer dezelfde materialen worden toegepast.
OXY-FUEL / OXYFUEL WELDING ook wel oxyacetyleenlassen genoemd, autogeenlassen, gaslassen wordt uitgevoerd met gasbrandstoffen en zuurstof voor het lassen. Omdat er geen elektriciteit wordt gebruikt, is het draagbaar en kan het worden gebruikt waar er geen elektriciteit is. Met behulp van een lastoorts verhitten we de stukken en het vulmateriaal om een gemeenschappelijk smeltbad te produceren. Er kunnen verschillende brandstoffen worden gebruikt, zoals acetyleen, benzine, waterstof, propaan, butaan, enz. Bij autogeen lassen gebruiken we twee containers, één voor de brandstof en de andere voor zuurstof. De zuurstof oxideert de brandstof (verbrandt deze).
WEERSTANDSLASSEN: Dit type lassen maakt gebruik van joule-verwarming en warmte wordt gegenereerd op de plaats waar gedurende een bepaalde tijd elektrische stroom wordt toegepast. Er worden hoge stromen door het metaal geleid. Op deze locatie worden plassen gesmolten metaal gevormd. Weerstandslasmethoden zijn populair vanwege hun efficiëntie en weinig vervuilingspotentieel. Nadelen zijn echter dat de uitrustingskosten relatief hoog zijn en de inherente beperking tot relatief dunne werkstukken. SPOT WELDING is een belangrijke vorm van weerstandslassen. Hier verbinden we twee of meer overlappende platen of werkstukken met behulp van twee koperen elektroden om de platen aan elkaar te klemmen en er een hoge stroom doorheen te laten gaan. Het materiaal tussen de koperelektroden warmt op en op die plek ontstaat een smeltbad. De stroom wordt dan gestopt en de koperen elektrodepunten koelen de laslocatie omdat de elektroden watergekoeld zijn. Het toepassen van de juiste hoeveelheid warmte op het juiste materiaal en de juiste dikte is de sleutel voor deze techniek, omdat bij verkeerde toepassing de voeg zwak zal zijn. Puntlassen heeft de voordelen dat het geen significante vervorming van werkstukken veroorzaakt, energie-efficiëntie, gemak van automatisering en uitstekende productiesnelheden, en dat er geen vulstoffen nodig zijn. Het nadeel is dat, aangezien het lassen op plaatsen plaatsvindt in plaats van een doorlopende naad te vormen, de algehele sterkte relatief lager kan zijn in vergelijking met andere lasmethoden. SEAM WELDING daarentegen produceert lassen op de faying-oppervlakken van vergelijkbare materialen. De naad kan een stompe of overlappende verbinding zijn. Naadlassen begint aan het ene uiteinde en gaat geleidelijk naar het andere. Deze methode maakt ook gebruik van twee elektroden van koper om druk en stroom uit te oefenen op het lasgebied. De schijfvormige elektroden roteren met constant contact langs de naadlijn en maken een continue las. Ook hier worden elektroden met water gekoeld. De lassen zijn zeer sterk en betrouwbaar. Andere methoden zijn projectie-, flits- en stuiklastechnieken.
SOLID-STATE LASSEN is een beetje anders dan de voorgaande methoden die hierboven zijn uitgelegd. Coalescentie vindt plaats bij temperaturen onder de smelttemperatuur van de samengevoegde metalen en zonder gebruik van metaalvulmiddel. Bij sommige processen kan druk worden gebruikt. Verschillende methoden zijn CO-EXTRUSIELASSEN waarbij ongelijksoortige metalen door dezelfde matrijs worden geëxtrudeerd, KOUDEDRUKLASSEN waarbij we zachte legeringen onder hun smeltpunt verbinden, DIFFUSIELASSEN een techniek zonder zichtbare laslijnen, EXPLOSIELASSEN voor het verbinden van ongelijksoortige materialen, bijv. corrosiebestendige legeringen aan structurele staalsoorten, ELEKTROMAGNETISCH PULSLASSEN waarbij we buizen en platen versnellen door elektromagnetische krachten, SMEEDLASSEN dat bestaat uit het verhitten van de metalen tot hoge temperaturen en samenslaan, FRICTIELASSEN waarbij met voldoende wrijvingslassen wordt uitgevoerd, FRICTIEROERLASSEN waarbij een roterende niet- verbruiksgereedschap dat door de verbindingslijn gaat, HEET DRUKLASSEN waarbij we metalen samenpersen bij verhoogde temperaturen onder de smelttemperatuur in vacuüm of inerte gassen, HEET ISOSTATISCH DRUKLASSEN een proces waarbij we druk uitoefenen met behulp van inerte gassen in een vat, ROLLENLASSEN waar we samenkomen ongelijke materialen door ze tussen twee roterende wielen, ULTRASOON LASSEN waarbij dunne metalen of plastic platen worden gelast met behulp van hoogfrequente trillingsenergie.
Onze andere lasprocessen zijn ELECTRON BEAM WELDING met diepe penetratie en snelle verwerking, maar omdat het een dure methode is, beschouwen we het voor speciale gevallen, ELEKTROSLAG WELDING een methode die alleen geschikt is voor zware dikke platen en werkstukken van staal, INDUCTIELASSEN waarbij we elektromagnetische inductie en onze elektrisch geleidende of ferromagnetische werkstukken verwarmen, LASERBEAM LASSEN ook met diepe penetratie en snelle verwerking maar een dure methode, LASER HYBRID WELDING dat LBW combineert met GMAW in dezelfde laskop en in staat is om openingen van 2 mm tussen platen te overbruggen, PERCUSSION WELDING dat omvat een elektrische ontlading gevolgd door het smeden van de materialen met toegepaste druk, THERMIT-LASSEN waarbij een exotherme reactie tussen aluminium en ijzeroxidepoeders plaatsvindt, ELEKTROGASLASSEN met verbruikselektroden en alleen gebruikt met staal in verticale positie, en ten slotte STUD ARC WELDING voor het verbinden van de bout met de basis materiaal met warmte en druk.
We raden u aan hier te klikken om:DOWNLOAD onze schematische illustraties van soldeer-, soldeer- en lijmverbindingsprocessen door AGS-TECH Inc
Dit zal u helpen de informatie die we u hieronder verstrekken beter te begrijpen.
• BRAZING : We verbinden twee of meer metalen door vulmetalen ertussen te verhitten tot boven hun smeltpunt en door capillaire werking te gebruiken om zich te verspreiden. Het proces is vergelijkbaar met solderen, maar de temperaturen die nodig zijn om het vulmiddel te smelten zijn hoger bij het solderen. Net als bij lassen beschermt flux het vulmateriaal tegen atmosferische vervuiling. Na afkoeling worden de werkstukken samengevoegd. Het proces omvat de volgende belangrijke stappen: goede pasvorm en speling, juiste reiniging van basismaterialen, juiste bevestiging, juiste flux- en atmosfeerselectie, verwarming van de assemblage en tenslotte het reinigen van de gesoldeerde assemblage. Sommige van onze soldeerprocessen zijn TORCH BRAZING, een populaire methode die handmatig of op een geautomatiseerde manier wordt uitgevoerd. Het is geschikt voor productieorders met een laag volume en gespecialiseerde gevallen. Warmte wordt toegepast met behulp van gasvlammen in de buurt van de verbinding die wordt gesoldeerd. Ovensolderen vereist minder vaardigheid van de operator en is een semi-automatisch proces dat geschikt is voor industriële massaproductie. Zowel temperatuurregeling als regeling van de atmosfeer in de oven zijn voordelen van deze techniek, omdat de eerste ons in staat stelt om gecontroleerde warmtecycli te hebben en lokale verwarming te elimineren, zoals het geval is bij het solderen van de toorts, en de laatste het onderdeel beschermt tegen oxidatie. Met behulp van jigging zijn we in staat om de fabricagekosten tot een minimum te beperken. De nadelen zijn een hoog stroomverbruik, apparatuurkosten en meer uitdagende ontwerpoverwegingen. VACUM BRAZING vindt plaats in een vacuümoven. De gelijkmatigheid van de temperatuur wordt behouden en we verkrijgen vloeimiddelvrije, zeer schone verbindingen met zeer weinig restspanningen. Warmtebehandelingen kunnen plaatsvinden tijdens vacuümsolderen, vanwege de lage restspanningen die aanwezig zijn tijdens langzame verwarmings- en afkoelcycli. Het grootste nadeel zijn de hoge kosten omdat het creëren van een vacuümomgeving een duur proces is. Nog een andere techniek DIP-BRAZING verbindt vaste delen waar soldeermassa wordt aangebracht op pasvlakken. Daarna worden de fixtured onderdelen gedompeld in een bad van een gesmolten zout zoals natriumchloride (keukenzout) dat fungeert als een warmteoverdrachtsmedium en flux. Lucht is uitgesloten en er vindt dus geen oxidevorming plaats. Bij INDUCTIEBRAZING verbinden we materialen met een vulmetaal dat een lager smeltpunt heeft dan de basismaterialen. De wisselstroom van de inductiespoel creëert een elektromagnetisch veld dat inductieverwarming induceert op voornamelijk ferromagnetische materialen. De methode zorgt voor selectieve verwarming, goede verbindingen met vulstoffen die alleen in de gewenste gebieden stromen, weinig oxidatie omdat er geen vlammen aanwezig zijn en koeling is snel, snelle verwarming, consistentie en geschikt voor productie van grote volumes. Om onze processen te versnellen en consistentie te garanderen, gebruiken we vaak preforms. Informatie over onze soldeerfaciliteit die keramiek-op-metaal fittingen, hermetische afdichting, vacuümdoorvoeren, hoog- en ultrahoog vacuüm en vloeistofregelcomponenten produceert vindt u hier: Brochure soldeerfabriek
• SOLDEREN : Bij het solderen hebben we geen smelten van de werkstukken, maar een vulmetaal met een lager smeltpunt dan de verbindende delen die in de voeg vloeien. Het vulmetaal bij het solderen smelt bij een lagere temperatuur dan bij het solderen. We gebruiken loodvrije legeringen voor het solderen en voldoen aan RoHS en voor verschillende toepassingen en vereisten hebben we verschillende en geschikte legeringen zoals zilverlegeringen. Solderen biedt ons verbindingen die gas- en vloeistofdicht zijn. Bij ZACHT SOLDEREN heeft ons vulmetaal een smeltpunt onder 400 Celsius, terwijl we bij ZILVER SOLDEREN en BRAZING hogere temperaturen nodig hebben. Zachtsolderen gebruikt lagere temperaturen maar resulteert niet in sterke verbindingen voor veeleisende toepassingen bij verhoogde temperaturen. Zilversolderen daarentegen vereist hoge temperaturen van de toorts en geeft ons sterke verbindingen die geschikt zijn voor toepassingen bij hoge temperaturen. Solderen vereist de hoogste temperaturen en meestal wordt een toorts gebruikt. Omdat soldeerverbindingen erg sterk zijn, zijn ze een goede kandidaat voor het repareren van zware ijzeren voorwerpen. In onze productielijnen gebruiken we zowel handmatig handmatig solderen als geautomatiseerde soldeerlijnen. INDUCTION SOLDERING gebruikt hoogfrequente wisselstroom in een koperen spoel om inductieverwarming te vergemakkelijken. Er worden stromen geïnduceerd in het gesoldeerde onderdeel en als resultaat wordt warmte gegenereerd bij de hoge weerstand joint. Door deze warmte smelt het vulmetaal. Flux wordt ook gebruikt. Inductiesolderen is een goede methode om cilinders en buizen in een continu proces te solderen door de spoelen eromheen te wikkelen. Het solderen van sommige materialen, zoals grafiet en keramiek, is moeilijker omdat de werkstukken vóór het solderen moeten worden geplateerd met een geschikt metaal. Dit vergemakkelijkt de grensvlakbinding. We solderen dergelijke materialen speciaal voor hermetische verpakkingstoepassingen. Wij vervaardigen onze printplaten (PCB's) in hoog volume, meestal met behulp van GOLFSOLDEREN. Alleen voor kleine hoeveelheden prototyping-doeleinden gebruiken we handsolderen met een soldeerbout. We gebruiken golfsolderen voor zowel through-hole als surface mount PCB-assemblies (PCBA). Een tijdelijke lijm houdt de componenten vast aan de printplaat en het geheel wordt op een transportband geplaatst en beweegt door een apparaat dat gesmolten soldeer bevat. Eerst wordt de printplaat gefluxt en komt dan in de voorverwarmingszone. Het gesmolten soldeer zit in een pan en heeft een patroon van staande golven op het oppervlak. Wanneer de printplaat over deze golven beweegt, komen deze golven in contact met de onderkant van de printplaat en kleven aan de soldeerpads. Het soldeer blijft alleen op pinnen en pads en niet op de print zelf. De golven in het gesmolten soldeer moeten goed worden gecontroleerd, zodat er geen spatten zijn en de golftoppen ongewenste delen van de platen niet raken en vervuilen. Bij REFLOW SOLDERING gebruiken we een kleverige soldeerpasta om de elektronische componenten tijdelijk op de printplaten te bevestigen. Vervolgens gaan de planken door een reflow-oven met temperatuurregeling. Hier smelt het soldeer en verbindt het de componenten permanent. We gebruiken deze techniek zowel voor opbouwcomponenten als voor doorlopende componenten. Een goede temperatuurregeling en aanpassing van de oventemperaturen is essentieel om vernietiging van elektronische componenten op het bord te voorkomen door oververhitting boven hun maximale temperatuurlimieten. In het proces van reflow-solderen hebben we in feite verschillende regio's of fasen met elk een duidelijk thermisch profiel, zoals voorverwarmstap, thermische inweekstap, reflow- en koelstappen. Deze verschillende stappen zijn essentieel voor een schadevrij reflow-solderen van printplaatassemblages (PCBA). ULTRASOON SOLDEREN is een andere veelgebruikte techniek met unieke mogelijkheden. Het kan worden gebruikt om glas, keramiek en niet-metalen materialen te solderen. Bijvoorbeeld fotovoltaïsche panelen die niet-metalen zijn, hebben elektroden nodig die met deze techniek kunnen worden bevestigd. Bij ultrasoon solderen zetten we een verwarmde soldeerpunt in die ook ultrasone trillingen afgeeft. Deze trillingen produceren cavitatiebellen op het grensvlak van het substraat met het gesmolten soldeermateriaal. De implosieve energie van cavitatie wijzigt het oxide-oppervlak en verwijdert het vuil en de oxiden. Gedurende deze tijd wordt ook een legeringslaag gevormd. Het soldeer op het hechtoppervlak neemt zuurstof op en maakt de vorming van een sterke gedeelde binding tussen het glas en het soldeer mogelijk. DIP SOLDEREN kan worden beschouwd als een eenvoudigere versie van golfsolderen die alleen geschikt is voor productie op kleine schaal. Eerste reinigingsvloeimiddel wordt toegepast zoals bij andere processen. PCB's met gemonteerde componenten worden handmatig of semi-automatisch gedompeld in een tank met gesmolten soldeer. Het gesmolten soldeer plakt aan de blootgestelde metalen delen die niet worden beschermd door een soldeermasker op het bord. De apparatuur is eenvoudig en goedkoop.
• ADHESIVE LIJMING: Dit is een andere populaire techniek die we vaak gebruiken en het betreft het verlijmen van oppervlakken met behulp van lijm, epoxy, plastic middelen of andere chemicaliën. Hechting wordt bereikt door ofwel het oplosmiddel te verdampen, door warmte-uitharding, door UV-lichtuitharding, door drukuitharding of door een bepaalde tijd te wachten. In onze productielijnen worden verschillende hoogwaardige lijmen gebruikt. Met goed ontworpen applicatie- en uithardingsprocessen kan lijmverlijming resulteren in zeer sterke en betrouwbare verbindingen met zeer lage spanning. Lijmverbindingen kunnen goede beschermers zijn tegen omgevingsfactoren zoals vocht, verontreinigingen, corrosieve stoffen, trillingen, enz. Voordelen van lijmen zijn: ze kunnen worden toegepast op materialen die anders moeilijk te solderen, lassen of hardsolderen zouden zijn. Het kan ook de voorkeur hebben voor warmtegevoelige materialen die zouden worden beschadigd door lassen of andere processen bij hoge temperaturen. Andere voordelen van lijmen zijn dat ze op onregelmatig gevormde oppervlakken kunnen worden aangebracht en het gewicht van de montage met zeer kleine hoeveelheden kunnen verhogen in vergelijking met andere methoden. Ook maatveranderingen in onderdelen zijn zeer minimaal. Sommige lijmen hebben index-matching-eigenschappen en kunnen tussen optische componenten worden gebruikt zonder de licht- of optische signaalsterkte aanzienlijk te verminderen. Nadelen aan de andere kant zijn langere uithardingstijden die productielijnen kunnen vertragen, bevestigingsvereisten, vereisten voor oppervlaktevoorbereiding en moeilijkheid om te demonteren wanneer herbewerking nodig is. De meeste van onze lijmverbindingen omvatten de volgende stappen:
- Oppervlaktebehandeling: speciale reinigingsprocedures zoals reiniging met gedeïoniseerd water, alcoholreiniging, plasma- of corona-reiniging komen vaak voor. Na reiniging kunnen we hechtingsbevorderaars op de oppervlakken aanbrengen om de best mogelijke verbindingen te garanderen.
-Deelbevestiging: Voor zowel lijmtoepassing als voor uitharding ontwerpen en gebruiken we aangepaste armaturen.
-Lijmtoepassing: we gebruiken soms handmatige, en soms, afhankelijk van het geval, geautomatiseerde systemen zoals robotica, servomotoren, lineaire actuatoren om de lijmen op de juiste locatie af te leveren en we gebruiken dispensers om het in het juiste volume en de juiste hoeveelheid te leveren.
-Uitharding: Afhankelijk van de lijm kunnen we eenvoudig drogen en uitharden, maar ook uitharden onder UV-lampen die fungeren als katalysator of warmteuitharding in een oven of met behulp van resistieve verwarmingselementen die op mallen en armaturen zijn gemonteerd.
We raden u aan hier te klikken om:DOWNLOAD onze schematische illustraties van bevestigingsprocessen door AGS-TECH Inc.
Dit zal u helpen de informatie die we u hieronder verstrekken beter te begrijpen.
• BEVESTIGINGSPROCESSEN: Onze mechanische verbindingsprocessen vallen in twee brad-categorieën: BEVESTIGINGSMIDDELEN en INTEGRALE VERBINDINGEN. Voorbeelden van bevestigingsmiddelen die wij gebruiken zijn schroeven, pennen, moeren, bouten, klinknagels. Voorbeelden van integrale verbindingen die we gebruiken zijn klik- en krimppassingen, naden, plooien. Met behulp van verschillende bevestigingsmethoden zorgen we ervoor dat onze mechanische verbindingen sterk en betrouwbaar zijn voor jarenlang gebruik. SCHROEVEN en BOUTEN zijn enkele van de meest gebruikte bevestigingsmiddelen om objecten bij elkaar te houden en te positioneren. Onze schroeven en bouten voldoen aan de ASME-normen. Er worden verschillende soorten schroeven en bouten gebruikt, waaronder zeskantbouten en zeskantbouten, houtdraadbouten en -bouten, tweezijdige schroeven, deuvelschroef, oogschroef, spiegelschroef, plaatschroef, fijnafstelschroef, zelfborende en zelftappende schroeven , stelschroef, schroeven met ingebouwde ringen,...en meer. We hebben verschillende typen schroefkoppen zoals verzonken, bolle, ronde, flenskop en verschillende typen schroefaandrijvingen zoals sleuf, kruiskop, vierkant, zeskant. Een RIVET daarentegen is een permanente mechanische sluiting bestaande uit een gladde cilindrische as en een kop enerzijds. Na het inbrengen wordt het andere uiteinde van de klinknagel vervormd en wordt de diameter vergroot zodat deze op zijn plaats blijft. Met andere woorden, vóór installatie heeft een klinknagel één kop en na installatie twee. We installeren verschillende soorten klinknagels, afhankelijk van de toepassing, sterkte, toegankelijkheid en kosten, zoals klinknagels met massieve/ronde kop, structurele, halfbuisvormige, blinde, oscar-, drive-, flush-, frictie-lock-, zelfborende klinknagels. Klinken kan de voorkeur hebben in gevallen waar warmtevervorming en verandering in materiaaleigenschappen als gevolg van laswarmte moeten worden vermeden. Klinken biedt ook een laag gewicht en vooral een goede sterkte en uithoudingsvermogen tegen schuifkrachten. Tegen trekbelastingen kunnen echter schroeven, moeren en bouten beter geschikt zijn. In het CLINCHING-proces gebruiken we speciale ponsen en matrijzen om een mechanische vergrendeling te vormen tussen plaatmetalen die worden samengevoegd. De pons duwt de lagen plaatmetaal in de matrijsholte en resulteert in de vorming van een permanente verbinding. Er is geen verwarming en geen koeling nodig bij het clinchen en het is een koud werkproces. Het is een economisch proces dat in sommige gevallen puntlassen kan vervangen. Bij PINNING gebruiken we pennen die machine-elementen zijn die worden gebruikt om posities van machineonderdelen ten opzichte van elkaar vast te zetten. De belangrijkste typen zijn gaffelpennen, splitpen, veerpennen, paspennen, en splitpen. Bij NIETEN gebruiken we nietpistolen en nietjes die tweeledige bevestigingsmiddelen zijn die worden gebruikt om materialen aan elkaar te verbinden of te binden. Nieten heeft de volgende voordelen: Economisch, eenvoudig en snel in gebruik, de kroon van de nietjes kan worden gebruikt om materialen tegen elkaar te overbruggen. schadelijke, relatief gemakkelijke verwijdering. PRESS FITTING wordt uitgevoerd door onderdelen tegen elkaar te duwen en de wrijving tussen hen maakt de onderdelen vast. Perspassingsonderdelen bestaande uit een overmaatse as en een ondermaats gat worden over het algemeen op twee manieren geassembleerd: ofwel door kracht uit te oefenen of door gebruik te maken van thermische uitzetting of samentrekking van de onderdelen. Wanneer een persfitting tot stand wordt gebracht door een kracht uit te oefenen, gebruiken we een hydraulische pers of een handbediende pers. Aan de andere kant, wanneer perspassing tot stand wordt gebracht door thermische uitzetting, verwarmen we de omhullende delen en assembleren ze op hun plaats terwijl ze heet zijn. Als ze afkoelen, krimpen ze en krijgen ze hun normale afmetingen terug. Dit resulteert in een goede perspassing. We noemen dit alternatief SHRINK-FITTING. De andere manier om dit te doen is door de omhulde delen vóór montage af te koelen en ze vervolgens in hun passende delen te schuiven. Als de assemblage opwarmt, zetten ze uit en krijgen we een strakke pasvorm. Deze laatste methode kan de voorkeur hebben in gevallen waar verwarming het risico met zich meebrengt dat de materiaaleigenschappen veranderen. Koelen is dan veiliger.
Pneumatische en hydraulische componenten en assemblages
• Kleppen, hydraulische en pneumatische componenten zoals O-ring, ring, afdichtingen, pakking, ring, shim.
Omdat kleppen en pneumatische componenten er in een grote verscheidenheid zijn, kunnen we hier niet alles opnoemen. Afhankelijk van de fysische en chemische omgevingen van uw toepassing hebben wij wel speciale producten voor u. Geef ons alstublieft de toepassing, het type component, specificaties, omgevingscondities zoals druk, temperatuur, vloeistoffen of gassen die in contact komen met uw kleppen en pneumatische componenten; en we zullen het meest geschikte product voor u kiezen of het speciaal voor uw toepassing vervaardigen.