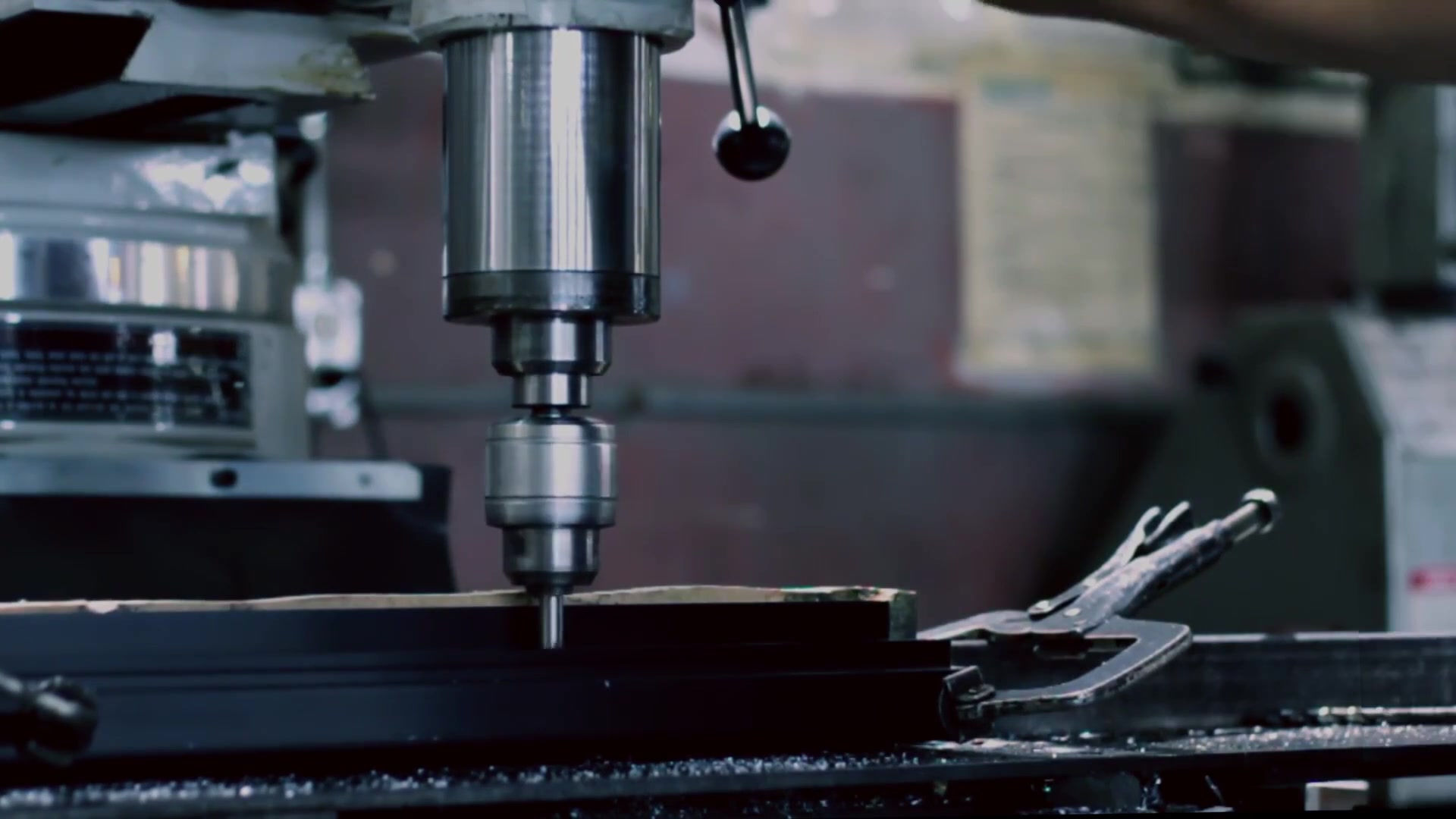
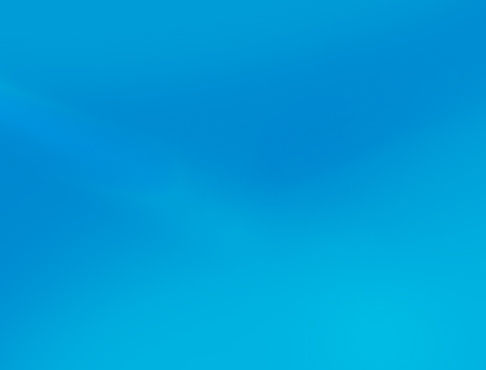
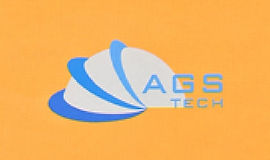
ਗਲੋਬਲ ਕਸਟਮ ਮੈਨੂਫੈਕਚਰਰ, ਇੰਟੀਗਰੇਟਰ, ਕੰਸੋਲੀਡੇਟਰ, ਉਤਪਾਦਾਂ ਅਤੇ ਸੇਵਾਵਾਂ ਦੀ ਵਿਭਿੰਨ ਕਿਸਮਾਂ ਲਈ ਆਊਟਸੋਰਸਿੰਗ ਪਾਰਟਨਰ।
ਅਸੀਂ ਨਿਰਮਾਣ, ਨਿਰਮਾਣ, ਇੰਜੀਨੀਅਰਿੰਗ, ਇਕਸਾਰਤਾ, ਏਕੀਕਰਣ, ਕਸਟਮ ਨਿਰਮਿਤ ਅਤੇ ਆਫ-ਸ਼ੈਲਫ ਉਤਪਾਦਾਂ ਅਤੇ ਸੇਵਾਵਾਂ ਦੀ ਆਊਟਸੋਰਸਿੰਗ ਲਈ ਤੁਹਾਡੇ ਇੱਕ-ਸਟਾਪ ਸਰੋਤ ਹਾਂ।
ਆਪਣੀ ਭਾਸ਼ਾ ਚੁਣੋ
-
ਕਸਟਮ ਨਿਰਮਾਣ
-
ਘਰੇਲੂ ਅਤੇ ਗਲੋਬਲ ਕੰਟਰੈਕਟ ਮੈਨੂਫੈਕਚਰਿੰਗ
-
ਨਿਰਮਾਣ ਆਊਟਸੋਰਸਿੰਗ
-
ਘਰੇਲੂ ਅਤੇ ਗਲੋਬਲ ਖਰੀਦਦਾਰੀ
-
ਇਕਸੁਰਤਾ
-
ਇੰਜੀਨੀਅਰਿੰਗ ਏਕੀਕਰਣ
-
ਇੰਜੀਨੀਅਰਿੰਗ ਸੇਵਾਵਾਂ
ਸਾਡੀਆਂ ਕਸਟਮ ਕਾਸਟਿੰਗ ਅਤੇ ਮਸ਼ੀਨਿੰਗ ਤਕਨੀਕਾਂ ਹਨ ਖਰਚੇ ਯੋਗ ਅਤੇ ਗੈਰ-ਖਰਚਣਯੋਗ ਕਾਸਟਿੰਗ, ਫੈਰਸ ਅਤੇ ਗੈਰ-ਫੈਰਸ ਕਾਸਟਿੰਗ, ਰੇਤ, ਡਾਈ, ਸੈਂਟਰਿਫਿਊਗਲ, ਨਿਰੰਤਰ, ਵਸਰਾਵਿਕ ਉੱਲੀ, ਨਿਵੇਸ਼, ਗੁਆਚਿਆ ਫੋਮ, ਨੇੜੇ-ਨੈੱਟ-ਆਕਾਰ, ਸਥਾਈ ਉੱਲੀ (ਗਰੈਵਿਟੀ ਡਾਈ ਕਾਸਟਿੰਗ), ਪਲਾਸਟਰ ਮੋਲਡ (ਪਲਾਸਟਰ ਕਾਸਟਿੰਗ) ਅਤੇ ਸ਼ੈੱਲ ਕਾਸਟਿੰਗ, ਪਰੰਪਰਾਗਤ ਦੇ ਨਾਲ-ਨਾਲ CNC ਉਪਕਰਣਾਂ ਦੀ ਵਰਤੋਂ ਕਰਕੇ ਮਿਲਿੰਗ ਅਤੇ ਮੋੜ ਦੁਆਰਾ ਤਿਆਰ ਕੀਤੇ ਗਏ ਮਸ਼ੀਨ ਵਾਲੇ ਹਿੱਸੇ, ਉੱਚ ਥ੍ਰੋਪੁੱਟ ਸਸਤੇ ਛੋਟੇ ਸ਼ੁੱਧਤਾ ਵਾਲੇ ਹਿੱਸਿਆਂ ਲਈ ਸਵਿਸ ਟਾਈਪ ਮਸ਼ੀਨਿੰਗ, ਫਾਸਟਨਰਾਂ ਲਈ ਪੇਚ ਮਸ਼ੀਨ, ਗੈਰ-ਰਵਾਇਤੀ ਮਸ਼ੀਨਿੰਗ। ਕਿਰਪਾ ਕਰਕੇ ਧਿਆਨ ਵਿੱਚ ਰੱਖੋ ਕਿ ਧਾਤਾਂ ਅਤੇ ਧਾਤੂ ਮਿਸ਼ਰਣਾਂ ਤੋਂ ਇਲਾਵਾ, ਅਸੀਂ ਵਸਰਾਵਿਕ, ਸ਼ੀਸ਼ੇ ਅਤੇ ਪਲਾਸਟਿਕ ਦੇ ਹਿੱਸਿਆਂ ਦੇ ਨਾਲ-ਨਾਲ ਕੁਝ ਮਾਮਲਿਆਂ ਵਿੱਚ ਮਸ਼ੀਨ ਬਣਾਉਂਦੇ ਹਾਂ ਜਦੋਂ ਇੱਕ ਉੱਲੀ ਬਣਾਉਣਾ ਪਸੰਦ ਨਹੀਂ ਹੁੰਦਾ ਜਾਂ ਵਿਕਲਪ ਨਹੀਂ ਹੁੰਦਾ। ਪੌਲੀਮਰ ਸਮੱਗਰੀ ਦੀ ਮਸ਼ੀਨਿੰਗ ਲਈ ਸਾਡੇ ਕੋਲ ਵਿਸ਼ੇਸ਼ ਤਜ਼ਰਬੇ ਦੀ ਲੋੜ ਹੁੰਦੀ ਹੈ ਕਿਉਂਕਿ ਪਲਾਸਟਿਕ ਅਤੇ ਰਬੜ ਦੀ ਚੁਣੌਤੀ ਉਹਨਾਂ ਦੀ ਨਰਮਤਾ, ਗੈਰ-ਕਠੋਰਤਾ... ਆਦਿ ਕਾਰਨ ਹੈ। ਵਸਰਾਵਿਕ ਅਤੇ ਕੱਚ ਦੀ ਮਸ਼ੀਨਿੰਗ ਲਈ, ਕਿਰਪਾ ਕਰਕੇ ਗੈਰ-ਰਵਾਇਤੀ ਫੈਬਰੀਕੇਸ਼ਨ 'ਤੇ ਸਾਡਾ ਪੰਨਾ ਦੇਖੋ। AGS-TECH Inc. ਹਲਕੇ ਅਤੇ ਭਾਰੀ ਕਾਸਟਿੰਗ ਦੋਵਾਂ ਦਾ ਨਿਰਮਾਣ ਅਤੇ ਸਪਲਾਈ ਕਰਦਾ ਹੈ। ਅਸੀਂ ਬਾਇਲਰ, ਹੀਟ ਐਕਸਚੇਂਜਰ, ਆਟੋਮੋਬਾਈਲ, ਮਾਈਕ੍ਰੋਮੋਟਰ, ਵਿੰਡ ਟਰਬਾਈਨ, ਫੂਡ ਪੈਕਜਿੰਗ ਉਪਕਰਣ ਅਤੇ ਹੋਰ ਲਈ ਮੈਟਲ ਕਾਸਟਿੰਗ ਅਤੇ ਮਸ਼ੀਨਡ ਪਾਰਟਸ ਦੀ ਸਪਲਾਈ ਕਰਦੇ ਰਹੇ ਹਾਂ। ਅਸੀਂ ਸਿਫ਼ਾਰਿਸ਼ ਕਰਦੇ ਹਾਂ ਕਿ ਤੁਸੀਂ ਇੱਥੇ ਕਲਿੱਕ ਕਰੋ AGS-TECH Inc ਦੁਆਰਾ ਮਸ਼ੀਨਿੰਗ ਅਤੇ ਕਾਸਟਿੰਗ ਪ੍ਰਕਿਰਿਆਵਾਂ ਦੇ ਸਾਡੇ ਯੋਜਨਾਬੱਧ ਚਿੱਤਰਾਂ ਨੂੰ ਡਾਊਨਲੋਡ ਕਰੋ।
ਇਹ ਤੁਹਾਨੂੰ ਉਸ ਜਾਣਕਾਰੀ ਨੂੰ ਬਿਹਤਰ ਤਰੀਕੇ ਨਾਲ ਸਮਝਣ ਵਿੱਚ ਮਦਦ ਕਰੇਗਾ ਜੋ ਅਸੀਂ ਤੁਹਾਨੂੰ ਹੇਠਾਂ ਪ੍ਰਦਾਨ ਕਰ ਰਹੇ ਹਾਂ। ਆਉ ਅਸੀਂ ਵਿਸਤਾਰ ਵਿੱਚ ਪੇਸ਼ ਕੀਤੀਆਂ ਕੁਝ ਵੱਖ-ਵੱਖ ਤਕਨੀਕਾਂ ਨੂੰ ਵੇਖੀਏ:
• ਐਕਸਪੇਂਡੇਬਲ ਮੋਲਡ ਕਾਸਟਿੰਗ: ਇਹ ਵਿਆਪਕ ਸ਼੍ਰੇਣੀ ਉਹਨਾਂ ਤਰੀਕਿਆਂ ਨੂੰ ਦਰਸਾਉਂਦੀ ਹੈ ਜਿਹਨਾਂ ਵਿੱਚ ਅਸਥਾਈ ਅਤੇ ਗੈਰ-ਮੁੜ ਵਰਤੋਂ ਯੋਗ ਮੋਲਡ ਸ਼ਾਮਲ ਹੁੰਦੇ ਹਨ। ਉਦਾਹਰਨਾਂ ਹਨ ਰੇਤ, ਪਲਾਸਟਰ, ਸ਼ੈੱਲ, ਨਿਵੇਸ਼ (ਜਿਸ ਨੂੰ ਗੁਆਚਿਆ-ਮੋਮ ਵੀ ਕਿਹਾ ਜਾਂਦਾ ਹੈ) ਅਤੇ ਪਲਾਸਟਰ ਕਾਸਟਿੰਗ।
• ਰੇਤ ਦੀ ਕਾਸਟਿੰਗ: ਇੱਕ ਪ੍ਰਕਿਰਿਆ ਜਿਸ ਵਿੱਚ ਰੇਤ ਨੂੰ ਮੋਲਡ ਸਮੱਗਰੀ ਵਜੋਂ ਵਰਤਿਆ ਜਾਂਦਾ ਹੈ। ਇੱਕ ਬਹੁਤ ਪੁਰਾਣਾ ਤਰੀਕਾ ਹੈ ਅਤੇ ਅਜੇ ਵੀ ਇਸ ਹੱਦ ਤੱਕ ਬਹੁਤ ਮਸ਼ਹੂਰ ਹੈ ਕਿ ਇਸ ਤਕਨੀਕ ਦੁਆਰਾ ਪੈਦਾ ਕੀਤੇ ਗਏ ਜ਼ਿਆਦਾਤਰ ਧਾਤ ਦੀਆਂ ਕਾਸਟਿੰਗਾਂ ਕੀਤੀਆਂ ਜਾਂਦੀਆਂ ਹਨ। ਘੱਟ ਮਾਤਰਾ ਦੇ ਉਤਪਾਦਨ 'ਤੇ ਵੀ ਘੱਟ ਲਾਗਤ. ਛੋਟੇ ਅਤੇ ਵੱਡੇ ਹਿੱਸੇ ਦੇ ਨਿਰਮਾਣ ਲਈ ਉਚਿਤ. ਤਕਨੀਕ ਦੀ ਵਰਤੋਂ ਬਹੁਤ ਘੱਟ ਨਿਵੇਸ਼ ਨਾਲ ਦਿਨਾਂ ਜਾਂ ਹਫ਼ਤਿਆਂ ਦੇ ਅੰਦਰ ਹਿੱਸੇ ਬਣਾਉਣ ਲਈ ਕੀਤੀ ਜਾ ਸਕਦੀ ਹੈ। ਨਮੀ ਵਾਲੀ ਰੇਤ ਨੂੰ ਮਿੱਟੀ, ਬਾਈਂਡਰ ਜਾਂ ਵਿਸ਼ੇਸ਼ ਤੇਲ ਦੀ ਵਰਤੋਂ ਕਰਕੇ ਜੋੜਿਆ ਜਾਂਦਾ ਹੈ। ਰੇਤ ਆਮ ਤੌਰ 'ਤੇ ਮੋਲਡ ਬਕਸਿਆਂ ਵਿੱਚ ਹੁੰਦੀ ਹੈ ਅਤੇ ਕੈਵਿਟੀ ਅਤੇ ਗੇਟ ਸਿਸਟਮ ਮਾਡਲਾਂ ਦੇ ਆਲੇ ਦੁਆਲੇ ਰੇਤ ਨੂੰ ਸੰਕੁਚਿਤ ਕਰਕੇ ਬਣਾਇਆ ਜਾਂਦਾ ਹੈ। ਪ੍ਰਕਿਰਿਆਵਾਂ ਹਨ:
1.) ਮੋਲਡ ਬਣਾਉਣ ਲਈ ਮਾਡਲ ਨੂੰ ਰੇਤ ਵਿੱਚ ਰੱਖਣਾ
2.) ਇੱਕ ਗੇਟਿੰਗ ਪ੍ਰਣਾਲੀ ਵਿੱਚ ਮਾਡਲ ਅਤੇ ਰੇਤ ਨੂੰ ਸ਼ਾਮਲ ਕਰਨਾ
3.) ਮਾਡਲ ਨੂੰ ਹਟਾਉਣਾ
4.) ਪਿਘਲੇ ਹੋਏ ਧਾਤ ਨਾਲ ਮੋਲਡ ਕੈਵਿਟੀ ਨੂੰ ਭਰਨਾ
5.) ਧਾਤ ਦੀ ਠੰਢਕ
6.) ਰੇਤ ਦੇ ਉੱਲੀ ਨੂੰ ਤੋੜਨਾ ਅਤੇ ਕਾਸਟਿੰਗ ਨੂੰ ਹਟਾਉਣਾ
• ਪਲਾਸਟਰ ਮੋਲਡ ਕਾਸਟਿੰਗ: ਰੇਤ ਦੀ ਕਾਸਟਿੰਗ ਦੇ ਸਮਾਨ, ਅਤੇ ਰੇਤ ਦੀ ਬਜਾਏ, ਪਲਾਸਟਰ ਆਫ਼ ਪੈਰਿਸ ਨੂੰ ਮੋਲਡ ਸਮੱਗਰੀ ਵਜੋਂ ਵਰਤਿਆ ਜਾ ਰਿਹਾ ਹੈ। ਛੋਟੇ ਉਤਪਾਦਨ ਦੇ ਲੀਡ ਟਾਈਮ ਜਿਵੇਂ ਕਿ ਰੇਤ ਕਾਸਟਿੰਗ ਅਤੇ ਸਸਤੀ। ਚੰਗੀ ਆਯਾਮੀ ਸਹਿਣਸ਼ੀਲਤਾ ਅਤੇ ਸਤਹ ਮੁਕੰਮਲ. ਇਸ ਦਾ ਮੁੱਖ ਨੁਕਸਾਨ ਇਹ ਹੈ ਕਿ ਇਸਦੀ ਵਰਤੋਂ ਐਲੂਮੀਨੀਅਮ ਅਤੇ ਜ਼ਿੰਕ ਵਰਗੀਆਂ ਘੱਟ ਪਿਘਲਣ ਵਾਲੀਆਂ ਧਾਤਾਂ ਨਾਲ ਹੀ ਕੀਤੀ ਜਾ ਸਕਦੀ ਹੈ।
• ਸ਼ੈੱਲ ਮੋਲਡ ਕਾਸਟਿੰਗ: ਰੇਤ ਕਾਸਟਿੰਗ ਦੇ ਸਮਾਨ ਵੀ। ਰੇਤ ਨਾਲ ਭਰੇ ਫਲਾਸਕ ਦੀ ਬਜਾਏ ਰੇਤ ਦੇ ਕਠੋਰ ਸ਼ੈੱਲ ਅਤੇ ਥਰਮੋਸੈਟਿੰਗ ਰਾਲ ਬਾਈਂਡਰ ਦੁਆਰਾ ਪ੍ਰਾਪਤ ਕੀਤੀ ਮੋਲਡ ਕੈਵੀਟੀ ਜਿਵੇਂ ਕਿ ਰੇਤ ਕਾਸਟਿੰਗ ਪ੍ਰਕਿਰਿਆ ਵਿੱਚ ਹੁੰਦੀ ਹੈ। ਰੇਤ ਦੁਆਰਾ ਸੁੱਟੇ ਜਾਣ ਲਈ ਢੁਕਵੀਂ ਲਗਭਗ ਕੋਈ ਵੀ ਧਾਤ ਸ਼ੈੱਲ ਮੋਲਡਿੰਗ ਦੁਆਰਾ ਸੁੱਟੀ ਜਾ ਸਕਦੀ ਹੈ। ਪ੍ਰਕਿਰਿਆ ਨੂੰ ਇਸ ਤਰ੍ਹਾਂ ਸੰਖੇਪ ਕੀਤਾ ਜਾ ਸਕਦਾ ਹੈ:
1.) ਸ਼ੈੱਲ ਉੱਲੀ ਦਾ ਨਿਰਮਾਣ. ਰੇਤ ਦੀ ਕਾਸਟਿੰਗ ਵਿੱਚ ਵਰਤੀ ਜਾਂਦੀ ਰੇਤ ਦੀ ਤੁਲਨਾ ਵਿੱਚ ਵਰਤੀ ਗਈ ਰੇਤ ਬਹੁਤ ਛੋਟੇ ਅਨਾਜ ਦੇ ਆਕਾਰ ਦੀ ਹੁੰਦੀ ਹੈ। ਬਰੀਕ ਰੇਤ ਨੂੰ ਥਰਮੋਸੈਟਿੰਗ ਰਾਲ ਨਾਲ ਮਿਲਾਇਆ ਜਾਂਦਾ ਹੈ। ਸ਼ੈੱਲ ਨੂੰ ਹਟਾਉਣਾ ਆਸਾਨ ਬਣਾਉਣ ਲਈ ਧਾਤ ਦੇ ਪੈਟਰਨ ਨੂੰ ਇੱਕ ਵਿਭਾਜਨ ਏਜੰਟ ਨਾਲ ਕੋਟ ਕੀਤਾ ਜਾਂਦਾ ਹੈ। ਇਸ ਤੋਂ ਬਾਅਦ ਧਾਤ ਦੇ ਪੈਟਰਨ ਨੂੰ ਗਰਮ ਕੀਤਾ ਜਾਂਦਾ ਹੈ ਅਤੇ ਰੇਤ ਦੇ ਮਿਸ਼ਰਣ ਨੂੰ ਗਰਮ ਕਾਸਟਿੰਗ ਪੈਟਰਨ 'ਤੇ ਪੋਰਡ ਜਾਂ ਉਡਾ ਦਿੱਤਾ ਜਾਂਦਾ ਹੈ। ਪੈਟਰਨ ਦੀ ਸਤ੍ਹਾ 'ਤੇ ਇੱਕ ਪਤਲਾ ਸ਼ੈੱਲ ਬਣਦਾ ਹੈ। ਇਸ ਸ਼ੈੱਲ ਦੀ ਮੋਟਾਈ ਨੂੰ ਰੇਤ ਦੇ ਰਾਲ ਦੇ ਮਿਸ਼ਰਣ ਦੇ ਮੈਟਲ ਪੈਟਰਨ ਦੇ ਸੰਪਰਕ ਵਿੱਚ ਹੋਣ ਦੇ ਸਮੇਂ ਦੀ ਲੰਬਾਈ ਨੂੰ ਬਦਲ ਕੇ ਐਡਜਸਟ ਕੀਤਾ ਜਾ ਸਕਦਾ ਹੈ। ਢਿੱਲੀ ਰੇਤ ਨੂੰ ਫਿਰ ਸ਼ੈੱਲ ਦੇ ਢੱਕੇ ਪੈਟਰਨ ਦੇ ਨਾਲ ਹਟਾ ਦਿੱਤਾ ਜਾਂਦਾ ਹੈ।
2.) ਅੱਗੇ, ਸ਼ੈੱਲ ਅਤੇ ਪੈਟਰਨ ਨੂੰ ਇੱਕ ਓਵਨ ਵਿੱਚ ਗਰਮ ਕੀਤਾ ਜਾਂਦਾ ਹੈ ਤਾਂ ਜੋ ਸ਼ੈੱਲ ਸਖ਼ਤ ਹੋ ਜਾਵੇ। ਸਖ਼ਤ ਹੋਣ ਤੋਂ ਬਾਅਦ, ਸ਼ੈੱਲ ਨੂੰ ਪੈਟਰਨ ਵਿੱਚ ਬਣੇ ਪਿੰਨਾਂ ਦੀ ਵਰਤੋਂ ਕਰਕੇ ਪੈਟਰਨ ਤੋਂ ਬਾਹਰ ਕੱਢਿਆ ਜਾਂਦਾ ਹੈ।
3.) ਦੋ ਅਜਿਹੇ ਸ਼ੈੱਲ ਗਲੂਇੰਗ ਜਾਂ ਕਲੈਂਪਿੰਗ ਦੁਆਰਾ ਇਕੱਠੇ ਕੀਤੇ ਜਾਂਦੇ ਹਨ ਅਤੇ ਪੂਰਾ ਉੱਲੀ ਬਣਾਉਂਦੇ ਹਨ। ਹੁਣ ਸ਼ੈੱਲ ਮੋਲਡ ਨੂੰ ਇੱਕ ਕੰਟੇਨਰ ਵਿੱਚ ਪਾਇਆ ਜਾਂਦਾ ਹੈ ਜਿਸ ਵਿੱਚ ਕਾਸਟਿੰਗ ਪ੍ਰਕਿਰਿਆ ਦੌਰਾਨ ਇਸਨੂੰ ਰੇਤ ਜਾਂ ਧਾਤ ਦੇ ਸ਼ਾਟ ਦੁਆਰਾ ਸਮਰਥਤ ਕੀਤਾ ਜਾਂਦਾ ਹੈ।
4.) ਹੁਣ ਗਰਮ ਧਾਤ ਨੂੰ ਸ਼ੈੱਲ ਮੋਲਡ ਵਿੱਚ ਡੋਲ੍ਹਿਆ ਜਾ ਸਕਦਾ ਹੈ।
ਸ਼ੈੱਲ ਕਾਸਟਿੰਗ ਦੇ ਫਾਇਦੇ ਬਹੁਤ ਵਧੀਆ ਸਤਹ ਮੁਕੰਮਲ ਹੋਣ ਵਾਲੇ ਉਤਪਾਦ ਹਨ, ਉੱਚ ਅਯਾਮੀ ਸ਼ੁੱਧਤਾ ਦੇ ਨਾਲ ਗੁੰਝਲਦਾਰ ਹਿੱਸਿਆਂ ਦੇ ਨਿਰਮਾਣ ਦੀ ਸੰਭਾਵਨਾ, ਪ੍ਰਕਿਰਿਆ ਨੂੰ ਸਵੈਚਲਿਤ ਕਰਨ ਲਈ ਆਸਾਨ, ਵੱਡੀ ਮਾਤਰਾ ਦੇ ਉਤਪਾਦਨ ਲਈ ਕਿਫ਼ਾਇਤੀ।
ਨੁਕਸਾਨ ਇਹ ਹਨ ਕਿ ਮੋਲਡਾਂ ਨੂੰ ਗੈਸਾਂ ਦੇ ਕਾਰਨ ਚੰਗੀ ਹਵਾਦਾਰੀ ਦੀ ਲੋੜ ਹੁੰਦੀ ਹੈ ਜੋ ਉਦੋਂ ਬਣਦੀਆਂ ਹਨ ਜਦੋਂ ਪਿਘਲੀ ਹੋਈ ਧਾਤ ਬਾਈਂਡਰ ਕੈਮੀਕਲ ਨਾਲ ਸੰਪਰਕ ਕਰਦੀ ਹੈ, ਥਰਮੋਸੈਟਿੰਗ ਰੈਜ਼ਿਨ ਅਤੇ ਧਾਤ ਦੇ ਪੈਟਰਨ ਮਹਿੰਗੇ ਹੁੰਦੇ ਹਨ। ਧਾਤ ਦੇ ਪੈਟਰਨਾਂ ਦੀ ਲਾਗਤ ਦੇ ਕਾਰਨ, ਇਹ ਤਕਨੀਕ ਘੱਟ ਮਾਤਰਾ ਦੇ ਉਤਪਾਦਨ ਲਈ ਚੰਗੀ ਤਰ੍ਹਾਂ ਅਨੁਕੂਲ ਨਹੀਂ ਹੋ ਸਕਦੀ।
• ਇਨਵੈਸਟਮੈਂਟ ਕਾਸਟਿੰਗ (ਲੌਸਟ-ਵੈਕਸ ਕਾਸਟਿੰਗ ਵੀ ਕਿਹਾ ਜਾਂਦਾ ਹੈ): ਬਹੁਤ ਪੁਰਾਣੀ ਤਕਨੀਕ ਅਤੇ ਬਹੁਤ ਸਾਰੀਆਂ ਧਾਤਾਂ, ਰਿਫ੍ਰੈਕਟਰੀ ਸਮੱਗਰੀ ਅਤੇ ਵਿਸ਼ੇਸ਼ ਉੱਚ ਪ੍ਰਦਰਸ਼ਨ ਵਾਲੇ ਮਿਸ਼ਰਣਾਂ ਤੋਂ ਉੱਚ ਸ਼ੁੱਧਤਾ, ਦੁਹਰਾਉਣਯੋਗਤਾ, ਬਹੁਪੱਖੀਤਾ ਅਤੇ ਇਕਸਾਰਤਾ ਦੇ ਨਾਲ ਗੁਣਵੱਤਾ ਵਾਲੇ ਹਿੱਸੇ ਬਣਾਉਣ ਲਈ ਢੁਕਵੀਂ ਹੈ। ਛੋਟੇ ਅਤੇ ਵੱਡੇ ਆਕਾਰ ਦੇ ਹਿੱਸੇ ਪੈਦਾ ਕੀਤੇ ਜਾ ਸਕਦੇ ਹਨ. ਇੱਕ ਮਹਿੰਗੀ ਪ੍ਰਕਿਰਿਆ ਜਦੋਂ ਕੁਝ ਹੋਰ ਤਰੀਕਿਆਂ ਨਾਲ ਤੁਲਨਾ ਕੀਤੀ ਜਾਂਦੀ ਹੈ, ਪਰ ਮੁੱਖ ਫਾਇਦਾ ਇਹ ਹੈ ਕਿ ਨੇੜੇ ਦੇ ਸ਼ੁੱਧ ਆਕਾਰ, ਗੁੰਝਲਦਾਰ ਰੂਪਾਂ ਅਤੇ ਵੇਰਵਿਆਂ ਦੇ ਨਾਲ ਹਿੱਸੇ ਬਣਾਉਣ ਦੀ ਸੰਭਾਵਨਾ ਹੈ। ਇਸ ਲਈ ਲਾਗਤ ਕੁਝ ਮਾਮਲਿਆਂ ਵਿੱਚ ਮੁੜ ਕੰਮ ਅਤੇ ਮਸ਼ੀਨਿੰਗ ਨੂੰ ਖਤਮ ਕਰਕੇ ਕੁਝ ਹੱਦ ਤੱਕ ਆਫਸੈੱਟ ਕੀਤੀ ਜਾਂਦੀ ਹੈ। ਭਾਵੇਂ ਭਿੰਨਤਾਵਾਂ ਹੋ ਸਕਦੀਆਂ ਹਨ, ਇੱਥੇ ਆਮ ਨਿਵੇਸ਼ ਕਾਸਟਿੰਗ ਪ੍ਰਕਿਰਿਆ ਦਾ ਸੰਖੇਪ ਹੈ:
1.) ਮੋਮ ਜਾਂ ਪਲਾਸਟਿਕ ਤੋਂ ਅਸਲੀ ਮਾਸਟਰ ਪੈਟਰਨ ਦੀ ਸਿਰਜਣਾ। ਹਰੇਕ ਕਾਸਟਿੰਗ ਨੂੰ ਇੱਕ ਪੈਟਰਨ ਦੀ ਲੋੜ ਹੁੰਦੀ ਹੈ ਕਿਉਂਕਿ ਇਹ ਪ੍ਰਕਿਰਿਆ ਵਿੱਚ ਨਸ਼ਟ ਹੋ ਜਾਂਦੇ ਹਨ। ਉੱਲੀ ਜਿਸ ਤੋਂ ਪੈਟਰਨ ਬਣਾਏ ਜਾਂਦੇ ਹਨ, ਦੀ ਵੀ ਲੋੜ ਹੁੰਦੀ ਹੈ ਅਤੇ ਜ਼ਿਆਦਾਤਰ ਸਮਾਂ ਉੱਲੀ ਨੂੰ ਕਾਸਟ ਜਾਂ ਮਸ਼ੀਨ ਕੀਤਾ ਜਾਂਦਾ ਹੈ। ਕਿਉਂਕਿ ਉੱਲੀ ਨੂੰ ਖੋਲ੍ਹਣ ਦੀ ਜ਼ਰੂਰਤ ਨਹੀਂ ਹੈ, ਗੁੰਝਲਦਾਰ ਕਾਸਟਿੰਗ ਪ੍ਰਾਪਤ ਕੀਤੀ ਜਾ ਸਕਦੀ ਹੈ, ਬਹੁਤ ਸਾਰੇ ਮੋਮ ਦੇ ਪੈਟਰਨ ਨੂੰ ਇੱਕ ਰੁੱਖ ਦੀਆਂ ਸ਼ਾਖਾਵਾਂ ਵਾਂਗ ਜੋੜਿਆ ਜਾ ਸਕਦਾ ਹੈ ਅਤੇ ਇੱਕਠੇ ਡੋਲ੍ਹਿਆ ਜਾ ਸਕਦਾ ਹੈ, ਇਸ ਤਰ੍ਹਾਂ ਧਾਤ ਜਾਂ ਧਾਤ ਦੇ ਮਿਸ਼ਰਤ ਮਿਸ਼ਰਣ ਦੇ ਇੱਕਲੇ ਡੋਲ੍ਹਣ ਤੋਂ ਕਈ ਹਿੱਸਿਆਂ ਦੇ ਉਤਪਾਦਨ ਨੂੰ ਸਮਰੱਥ ਬਣਾਇਆ ਜਾ ਸਕਦਾ ਹੈ।
2.) ਅੱਗੇ, ਪੈਟਰਨ ਨੂੰ ਬਹੁਤ ਬਾਰੀਕ ਦਾਣੇਦਾਰ ਸਿਲਿਕਾ, ਪਾਣੀ, ਬਾਈਂਡਰ ਨਾਲ ਬਣੀ ਰਿਫ੍ਰੈਕਟਰੀ ਸਲਰੀ ਨਾਲ ਡੁਬੋਇਆ ਜਾਂ ਡੋਲ੍ਹਿਆ ਜਾਂਦਾ ਹੈ। ਇਸ ਦੇ ਨਤੀਜੇ ਵਜੋਂ ਪੈਟਰਨ ਦੀ ਸਤ੍ਹਾ ਉੱਤੇ ਵਸਰਾਵਿਕ ਪਰਤ ਆ ਜਾਂਦੀ ਹੈ। ਪੈਟਰਨ 'ਤੇ ਰਿਫ੍ਰੈਕਟਰੀ ਕੋਟ ਨੂੰ ਸੁੱਕਣ ਅਤੇ ਸਖ਼ਤ ਹੋਣ ਲਈ ਛੱਡ ਦਿੱਤਾ ਜਾਂਦਾ ਹੈ। ਇਹ ਕਦਮ ਉਹ ਹੈ ਜਿੱਥੋਂ ਨਾਮ ਨਿਵੇਸ਼ ਕਾਸਟਿੰਗ ਆਉਂਦਾ ਹੈ: ਰਿਫ੍ਰੈਕਟਰੀ ਸਲਰੀ ਨੂੰ ਮੋਮ ਦੇ ਪੈਟਰਨ ਉੱਤੇ ਨਿਵੇਸ਼ ਕੀਤਾ ਜਾਂਦਾ ਹੈ।
3.) ਇਸ ਪੜਾਅ 'ਤੇ, ਕਠੋਰ ਵਸਰਾਵਿਕ ਉੱਲੀ ਨੂੰ ਉਲਟਾ ਕਰ ਦਿੱਤਾ ਜਾਂਦਾ ਹੈ ਅਤੇ ਗਰਮ ਕੀਤਾ ਜਾਂਦਾ ਹੈ ਤਾਂ ਜੋ ਮੋਮ ਪਿਘਲ ਜਾਵੇ ਅਤੇ ਉੱਲੀ ਤੋਂ ਬਾਹਰ ਨਿਕਲ ਜਾਵੇ। ਮੈਟਲ ਕਾਸਟਿੰਗ ਲਈ ਇੱਕ ਕੈਵਿਟੀ ਪਿੱਛੇ ਛੱਡੀ ਜਾਂਦੀ ਹੈ।
4.) ਮੋਮ ਦੇ ਬਾਹਰ ਹੋਣ ਤੋਂ ਬਾਅਦ, ਵਸਰਾਵਿਕ ਉੱਲੀ ਨੂੰ ਉੱਚ ਤਾਪਮਾਨ ਤੱਕ ਗਰਮ ਕੀਤਾ ਜਾਂਦਾ ਹੈ ਜਿਸ ਦੇ ਨਤੀਜੇ ਵਜੋਂ ਉੱਲੀ ਮਜ਼ਬੂਤ ਹੁੰਦੀ ਹੈ।
5.) ਧਾਤੂ ਕਾਸਟਿੰਗ ਨੂੰ ਸਾਰੇ ਗੁੰਝਲਦਾਰ ਭਾਗਾਂ ਨੂੰ ਭਰਨ ਵਾਲੇ ਗਰਮ ਉੱਲੀ ਵਿੱਚ ਡੋਲ੍ਹਿਆ ਜਾਂਦਾ ਹੈ।
6.) ਕਾਸਟਿੰਗ ਨੂੰ ਠੋਸ ਕਰਨ ਦੀ ਆਗਿਆ ਹੈ
7.) ਅੰਤ ਵਿੱਚ ਵਸਰਾਵਿਕ ਉੱਲੀ ਟੁੱਟ ਗਈ ਹੈ ਅਤੇ ਨਿਰਮਿਤ ਹਿੱਸੇ ਦਰਖਤ ਤੋਂ ਕੱਟੇ ਗਏ ਹਨ।
ਇੱਥੇ ਨਿਵੇਸ਼ ਕਾਸਟਿੰਗ ਪਲਾਂਟ ਬਰੋਸ਼ਰ ਦਾ ਲਿੰਕ ਹੈ
• ਈਵੇਪੋਰੇਟਿਵ ਪੈਟਰਨ ਕਾਸਟਿੰਗ: ਇਹ ਪ੍ਰਕਿਰਿਆ ਪੋਲੀਸਟੀਰੀਨ ਫੋਮ ਵਰਗੀ ਸਮੱਗਰੀ ਤੋਂ ਬਣੇ ਪੈਟਰਨ ਦੀ ਵਰਤੋਂ ਕਰਦੀ ਹੈ ਜੋ ਉੱਲੀ ਵਿੱਚ ਗਰਮ ਪਿਘਲੀ ਹੋਈ ਧਾਤ ਨੂੰ ਡੋਲ੍ਹਣ 'ਤੇ ਭਾਫ਼ ਬਣ ਜਾਂਦੀ ਹੈ। ਇਸ ਪ੍ਰਕਿਰਿਆ ਦੀਆਂ ਦੋ ਕਿਸਮਾਂ ਹਨ: LOST FOAM CASTING ਜੋ ਬੰਧਨ ਰਹਿਤ ਰੇਤ ਦੀ ਵਰਤੋਂ ਕਰਦੀ ਹੈ ਅਤੇ ਪੂਰੀ ਮੋਲਡ ਕਾਸਟਿੰਗ ਜੋ ਬੰਧੂਆ ਰੇਤ ਦੀ ਵਰਤੋਂ ਕਰਦੀ ਹੈ। ਇੱਥੇ ਆਮ ਪ੍ਰਕਿਰਿਆ ਦੇ ਕਦਮ ਹਨ:
1.) ਪੋਲੀਸਟੀਰੀਨ ਵਰਗੀ ਸਮੱਗਰੀ ਤੋਂ ਪੈਟਰਨ ਤਿਆਰ ਕਰੋ। ਜਦੋਂ ਵੱਡੀ ਮਾਤਰਾ ਦਾ ਨਿਰਮਾਣ ਕੀਤਾ ਜਾਵੇਗਾ, ਪੈਟਰਨ ਨੂੰ ਢਾਲਿਆ ਜਾਂਦਾ ਹੈ. ਜੇ ਹਿੱਸੇ ਦੀ ਗੁੰਝਲਦਾਰ ਸ਼ਕਲ ਹੈ, ਤਾਂ ਪੈਟਰਨ ਬਣਾਉਣ ਲਈ ਅਜਿਹੇ ਫੋਮ ਸਮੱਗਰੀ ਦੇ ਕਈ ਭਾਗਾਂ ਨੂੰ ਇਕੱਠੇ ਕਰਨ ਦੀ ਲੋੜ ਹੋ ਸਕਦੀ ਹੈ। ਅਸੀਂ ਅਕਸਰ ਕਾਸਟਿੰਗ 'ਤੇ ਚੰਗੀ ਸਤਹ ਫਿਨਿਸ਼ ਬਣਾਉਣ ਲਈ ਪੈਟਰਨ ਨੂੰ ਰਿਫ੍ਰੈਕਟਰੀ ਮਿਸ਼ਰਣ ਨਾਲ ਕੋਟ ਕਰਦੇ ਹਾਂ।
2.) ਪੈਟਰਨ ਫਿਰ ਮੋਲਡਿੰਗ ਰੇਤ ਵਿੱਚ ਪਾ ਦਿੱਤਾ ਗਿਆ ਹੈ.
3.) ਪਿਘਲੀ ਹੋਈ ਧਾਤ ਨੂੰ ਉੱਲੀ ਵਿੱਚ ਡੋਲ੍ਹਿਆ ਜਾਂਦਾ ਹੈ, ਫੋਮ ਪੈਟਰਨ ਨੂੰ ਵਾਸ਼ਪੀਕਰਨ ਕਰਦਾ ਹੈ, ਜਿਵੇਂ ਕਿ ਜ਼ਿਆਦਾਤਰ ਮਾਮਲਿਆਂ ਵਿੱਚ ਪੋਲੀਸਟਾਈਰੀਨ ਜਿਵੇਂ ਕਿ ਇਹ ਮੋਲਡ ਕੈਵਿਟੀ ਵਿੱਚੋਂ ਵਹਿੰਦਾ ਹੈ।
4.) ਪਿਘਲੀ ਹੋਈ ਧਾਤ ਨੂੰ ਸਖ਼ਤ ਹੋਣ ਲਈ ਰੇਤ ਦੇ ਉੱਲੀ ਵਿੱਚ ਛੱਡ ਦਿੱਤਾ ਜਾਂਦਾ ਹੈ।
5.) ਸਖ਼ਤ ਹੋਣ ਤੋਂ ਬਾਅਦ, ਅਸੀਂ ਕਾਸਟਿੰਗ ਨੂੰ ਹਟਾ ਦਿੰਦੇ ਹਾਂ.
ਕੁਝ ਮਾਮਲਿਆਂ ਵਿੱਚ, ਸਾਡੇ ਦੁਆਰਾ ਬਣਾਏ ਗਏ ਉਤਪਾਦ ਨੂੰ ਪੈਟਰਨ ਦੇ ਅੰਦਰ ਇੱਕ ਕੋਰ ਦੀ ਲੋੜ ਹੁੰਦੀ ਹੈ। ਵਾਸ਼ਪੀਕਰਨ ਵਾਲੀ ਕਾਸਟਿੰਗ ਵਿੱਚ, ਮੋਲਡ ਕੈਵਿਟੀ ਵਿੱਚ ਇੱਕ ਕੋਰ ਨੂੰ ਰੱਖਣ ਅਤੇ ਸੁਰੱਖਿਅਤ ਕਰਨ ਦੀ ਕੋਈ ਲੋੜ ਨਹੀਂ ਹੈ। ਇਹ ਤਕਨੀਕ ਬਹੁਤ ਹੀ ਗੁੰਝਲਦਾਰ ਜਿਓਮੈਟਰੀਜ਼ ਦੇ ਨਿਰਮਾਣ ਲਈ ਢੁਕਵੀਂ ਹੈ, ਇਹ ਉੱਚ ਮਾਤਰਾ ਦੇ ਉਤਪਾਦਨ ਲਈ ਆਸਾਨੀ ਨਾਲ ਸਵੈਚਾਲਿਤ ਹੋ ਸਕਦੀ ਹੈ, ਅਤੇ ਕਾਸਟ ਵਾਲੇ ਹਿੱਸੇ ਵਿੱਚ ਕੋਈ ਵਿਭਾਜਨ ਲਾਈਨਾਂ ਨਹੀਂ ਹਨ। ਬੁਨਿਆਦੀ ਪ੍ਰਕਿਰਿਆ ਨੂੰ ਲਾਗੂ ਕਰਨ ਲਈ ਸਧਾਰਨ ਅਤੇ ਕਿਫ਼ਾਇਤੀ ਹੈ. ਵੱਡੀ ਮਾਤਰਾ ਦੇ ਉਤਪਾਦਨ ਲਈ, ਕਿਉਂਕਿ ਪੋਲੀਸਟੀਰੀਨ ਤੋਂ ਪੈਟਰਨ ਬਣਾਉਣ ਲਈ ਇੱਕ ਡਾਈ ਜਾਂ ਮੋਲਡ ਦੀ ਲੋੜ ਹੁੰਦੀ ਹੈ, ਇਹ ਕੁਝ ਮਹਿੰਗਾ ਹੋ ਸਕਦਾ ਹੈ।
• ਗੈਰ-ਵਿਸਥਾਰਯੋਗ ਮੋਲਡ ਕਾਸਟਿੰਗ: ਇਹ ਵਿਆਪਕ ਸ਼੍ਰੇਣੀ ਉਹਨਾਂ ਤਰੀਕਿਆਂ ਨੂੰ ਦਰਸਾਉਂਦੀ ਹੈ ਜਿੱਥੇ ਹਰੇਕ ਉਤਪਾਦਨ ਚੱਕਰ ਤੋਂ ਬਾਅਦ ਉੱਲੀ ਨੂੰ ਸੁਧਾਰਨ ਦੀ ਲੋੜ ਨਹੀਂ ਹੁੰਦੀ ਹੈ। ਉਦਾਹਰਨਾਂ ਹਨ ਸਥਾਈ, ਡਾਈ, ਨਿਰੰਤਰ ਅਤੇ ਸੈਂਟਰਿਫਿਊਗਲ ਕਾਸਟਿੰਗ। ਦੁਹਰਾਉਣਯੋਗਤਾ ਪ੍ਰਾਪਤ ਕੀਤੀ ਜਾਂਦੀ ਹੈ ਅਤੇ ਭਾਗਾਂ ਨੂੰ ਨਜ਼ਦੀਕੀ ਨੈੱਟ ਆਕਾਰ ਵਜੋਂ ਦਰਸਾਇਆ ਜਾ ਸਕਦਾ ਹੈ।
• ਸਥਾਈ ਮੋਲਡ ਕਾਸਟਿੰਗ: ਧਾਤੂ ਤੋਂ ਬਣੇ ਮੁੜ ਵਰਤੋਂ ਯੋਗ ਮੋਲਡ ਮਲਟੀਪਲ ਕਾਸਟਿੰਗ ਲਈ ਵਰਤੇ ਜਾਂਦੇ ਹਨ। ਇੱਕ ਸਥਾਈ ਉੱਲੀ ਨੂੰ ਆਮ ਤੌਰ 'ਤੇ ਇਸ ਦੇ ਖਤਮ ਹੋਣ ਤੋਂ ਪਹਿਲਾਂ ਹਜ਼ਾਰਾਂ ਵਾਰ ਵਰਤਿਆ ਜਾ ਸਕਦਾ ਹੈ। ਗਰੈਵਿਟੀ, ਗੈਸ ਦਾ ਦਬਾਅ ਜਾਂ ਵੈਕਿਊਮ ਆਮ ਤੌਰ 'ਤੇ ਉੱਲੀ ਨੂੰ ਭਰਨ ਲਈ ਵਰਤਿਆ ਜਾਂਦਾ ਹੈ। ਮੋਲਡ (ਜਿਸ ਨੂੰ ਡਾਈ ਵੀ ਕਿਹਾ ਜਾਂਦਾ ਹੈ) ਆਮ ਤੌਰ 'ਤੇ ਲੋਹੇ, ਸਟੀਲ, ਵਸਰਾਵਿਕ ਜਾਂ ਹੋਰ ਧਾਤਾਂ ਦੇ ਬਣੇ ਹੁੰਦੇ ਹਨ। ਆਮ ਪ੍ਰਕਿਰਿਆ ਹੈ:
1.) ਮਸ਼ੀਨ ਅਤੇ ਉੱਲੀ ਬਣਾਓ. ਦੋ ਧਾਤ ਦੇ ਬਲਾਕਾਂ ਵਿੱਚੋਂ ਉੱਲੀ ਨੂੰ ਮਸ਼ੀਨ ਕਰਨਾ ਆਮ ਗੱਲ ਹੈ ਜੋ ਇਕੱਠੇ ਫਿੱਟ ਹੁੰਦੇ ਹਨ ਅਤੇ ਖੋਲ੍ਹੇ ਅਤੇ ਬੰਦ ਕੀਤੇ ਜਾ ਸਕਦੇ ਹਨ। ਦੋਵੇਂ ਭਾਗਾਂ ਦੀਆਂ ਵਿਸ਼ੇਸ਼ਤਾਵਾਂ ਦੇ ਨਾਲ ਨਾਲ ਗੇਟਿੰਗ ਪ੍ਰਣਾਲੀ ਨੂੰ ਆਮ ਤੌਰ 'ਤੇ ਕਾਸਟਿੰਗ ਮੋਲਡ ਵਿੱਚ ਬਣਾਇਆ ਜਾਂਦਾ ਹੈ।
2.) ਅੰਦਰੂਨੀ ਉੱਲੀ ਦੀਆਂ ਸਤਹਾਂ ਨੂੰ ਰਿਫ੍ਰੈਕਟਰੀ ਸਮੱਗਰੀ ਨੂੰ ਸ਼ਾਮਲ ਕਰਨ ਵਾਲੀ ਸਲਰੀ ਨਾਲ ਕੋਟ ਕੀਤਾ ਜਾਂਦਾ ਹੈ। ਇਹ ਗਰਮੀ ਦੇ ਪ੍ਰਵਾਹ ਨੂੰ ਨਿਯੰਤਰਿਤ ਕਰਨ ਵਿੱਚ ਮਦਦ ਕਰਦਾ ਹੈ ਅਤੇ ਪਲੱਸਤਰ ਵਾਲੇ ਹਿੱਸੇ ਨੂੰ ਆਸਾਨੀ ਨਾਲ ਹਟਾਉਣ ਲਈ ਇੱਕ ਲੁਬਰੀਕੈਂਟ ਵਜੋਂ ਕੰਮ ਕਰਦਾ ਹੈ।
3.) ਅੱਗੇ, ਸਥਾਈ ਉੱਲੀ ਦੇ ਅੱਧੇ ਹਿੱਸੇ ਨੂੰ ਬੰਦ ਕਰ ਦਿੱਤਾ ਜਾਂਦਾ ਹੈ ਅਤੇ ਉੱਲੀ ਨੂੰ ਗਰਮ ਕੀਤਾ ਜਾਂਦਾ ਹੈ।
4.) ਪਿਘਲੀ ਹੋਈ ਧਾਤ ਨੂੰ ਉੱਲੀ ਵਿੱਚ ਡੋਲ੍ਹਿਆ ਜਾਂਦਾ ਹੈ ਅਤੇ ਸਥਿਰਤਾ ਲਈ ਛੱਡ ਦਿੱਤਾ ਜਾਂਦਾ ਹੈ।
5.) ਜ਼ਿਆਦਾ ਕੂਲਿੰਗ ਹੋਣ ਤੋਂ ਪਹਿਲਾਂ, ਜਦੋਂ ਮੋਲਡ ਦੇ ਅੱਧੇ ਖੁੱਲ੍ਹੇ ਹੁੰਦੇ ਹਨ ਤਾਂ ਅਸੀਂ ਈਜੇਕਟਰਾਂ ਦੀ ਵਰਤੋਂ ਕਰਕੇ ਸਥਾਈ ਉੱਲੀ ਤੋਂ ਹਿੱਸੇ ਨੂੰ ਹਟਾ ਦਿੰਦੇ ਹਾਂ।
ਅਸੀਂ ਅਕਸਰ ਘੱਟ ਪਿਘਲਣ ਵਾਲੇ ਬਿੰਦੂ ਧਾਤਾਂ ਜਿਵੇਂ ਕਿ ਜ਼ਿੰਕ ਅਤੇ ਐਲੂਮੀਨੀਅਮ ਲਈ ਸਥਾਈ ਮੋਲਡ ਕਾਸਟਿੰਗ ਦੀ ਵਰਤੋਂ ਕਰਦੇ ਹਾਂ। ਸਟੀਲ ਕਾਸਟਿੰਗ ਲਈ, ਅਸੀਂ ਗ੍ਰਾਫਾਈਟ ਨੂੰ ਮੋਲਡ ਸਮੱਗਰੀ ਵਜੋਂ ਵਰਤਦੇ ਹਾਂ। ਅਸੀਂ ਕਈ ਵਾਰ ਸਥਾਈ ਮੋਲਡਾਂ ਦੇ ਅੰਦਰ ਕੋਰ ਦੀ ਵਰਤੋਂ ਕਰਕੇ ਗੁੰਝਲਦਾਰ ਜਿਓਮੈਟਰੀ ਪ੍ਰਾਪਤ ਕਰਦੇ ਹਾਂ। ਇਸ ਤਕਨੀਕ ਦੇ ਫਾਇਦੇ ਤੇਜ਼ ਕੂਲਿੰਗ, ਗੁਣਾਂ ਵਿੱਚ ਇਕਸਾਰਤਾ, ਚੰਗੀ ਸ਼ੁੱਧਤਾ ਅਤੇ ਸਤਹ ਦੀ ਸਮਾਪਤੀ, ਘੱਟ ਰੱਦ ਦਰਾਂ, ਪ੍ਰਕਿਰਿਆ ਨੂੰ ਸਵੈਚਾਲਤ ਕਰਨ ਦੀ ਸੰਭਾਵਨਾ ਅਤੇ ਆਰਥਿਕ ਤੌਰ 'ਤੇ ਉੱਚ ਮਾਤਰਾ ਪੈਦਾ ਕਰਨ ਦੁਆਰਾ ਪ੍ਰਾਪਤ ਕੀਤੀਆਂ ਚੰਗੀਆਂ ਮਕੈਨੀਕਲ ਵਿਸ਼ੇਸ਼ਤਾਵਾਂ ਵਾਲੇ ਕਾਸਟਿੰਗ ਹਨ। ਨੁਕਸਾਨ ਉੱਚ ਸ਼ੁਰੂਆਤੀ ਸੈੱਟਅੱਪ ਲਾਗਤਾਂ ਹਨ ਜੋ ਇਸਨੂੰ ਘੱਟ ਵਾਲੀਅਮ ਓਪਰੇਸ਼ਨਾਂ ਲਈ ਅਣਉਚਿਤ ਬਣਾਉਂਦੀਆਂ ਹਨ, ਅਤੇ ਨਿਰਮਿਤ ਹਿੱਸਿਆਂ ਦੇ ਆਕਾਰ 'ਤੇ ਸੀਮਾਵਾਂ ਹਨ।
• ਡਾਈ ਕਾਸਟਿੰਗ: ਇੱਕ ਡਾਈ ਮਸ਼ੀਨ ਕੀਤੀ ਜਾਂਦੀ ਹੈ ਅਤੇ ਪਿਘਲੀ ਹੋਈ ਧਾਤ ਨੂੰ ਉੱਚ ਦਬਾਅ ਹੇਠ ਮੋਲਡ ਕੈਵਿਟੀਜ਼ ਵਿੱਚ ਧੱਕਿਆ ਜਾਂਦਾ ਹੈ। ਨਾਨਫੈਰਸ ਅਤੇ ਨਾਲ ਹੀ ਫੈਰਸ ਮੈਟਲ ਡਾਈ ਕਾਸਟਿੰਗ ਸੰਭਵ ਹਨ। ਇਹ ਪ੍ਰਕਿਰਿਆ ਵੇਰਵਿਆਂ, ਬਹੁਤ ਹੀ ਪਤਲੀਆਂ ਕੰਧਾਂ, ਅਯਾਮੀ ਇਕਸਾਰਤਾ ਅਤੇ ਚੰਗੀ ਸਤਹ ਫਿਨਿਸ਼ ਦੇ ਨਾਲ ਛੋਟੇ ਤੋਂ ਦਰਮਿਆਨੇ ਆਕਾਰ ਦੇ ਹਿੱਸਿਆਂ ਦੇ ਉੱਚ ਮਾਤਰਾ ਵਿੱਚ ਉਤਪਾਦਨ ਲਈ ਢੁਕਵੀਂ ਹੈ। AGS-TECH Inc. ਇਸ ਤਕਨੀਕ ਦੀ ਵਰਤੋਂ ਕਰਕੇ ਕੰਧ ਦੀ ਮੋਟਾਈ 0.5 ਮਿਲੀਮੀਟਰ ਤੱਕ ਬਣਾਉਣ ਦੇ ਸਮਰੱਥ ਹੈ। ਸਥਾਈ ਮੋਲਡ ਕਾਸਟਿੰਗ ਦੀ ਤਰ੍ਹਾਂ, ਉੱਲੀ ਵਿੱਚ ਦੋ ਅੱਧੇ ਹੋਣੇ ਚਾਹੀਦੇ ਹਨ ਜੋ ਪੈਦਾ ਹੋਏ ਹਿੱਸੇ ਨੂੰ ਹਟਾਉਣ ਲਈ ਖੁੱਲ੍ਹ ਅਤੇ ਬੰਦ ਹੋ ਸਕਦੇ ਹਨ। ਇੱਕ ਡਾਈ ਕਾਸਟਿੰਗ ਮੋਲਡ ਵਿੱਚ ਹਰੇਕ ਚੱਕਰ ਦੇ ਨਾਲ ਮਲਟੀਪਲ ਕਾਸਟਿੰਗ ਦੇ ਉਤਪਾਦਨ ਨੂੰ ਸਮਰੱਥ ਕਰਨ ਲਈ ਕਈ ਕੈਵਿਟੀਜ਼ ਹੋ ਸਕਦੀਆਂ ਹਨ। ਡਾਈ ਕਾਸਟਿੰਗ ਮੋਲਡ ਬਹੁਤ ਭਾਰੀ ਹੁੰਦੇ ਹਨ ਅਤੇ ਉਹਨਾਂ ਦੁਆਰਾ ਬਣਾਏ ਗਏ ਹਿੱਸਿਆਂ ਨਾਲੋਂ ਬਹੁਤ ਵੱਡੇ ਹੁੰਦੇ ਹਨ, ਇਸਲਈ ਮਹਿੰਗੇ ਵੀ ਹੁੰਦੇ ਹਨ। ਅਸੀਂ ਆਪਣੇ ਗ੍ਰਾਹਕਾਂ ਲਈ ਖਰਾਬ ਮਰਨ ਦੀ ਮੁਰੰਮਤ ਅਤੇ ਬਦਲਦੇ ਹਾਂ ਜਦੋਂ ਤੱਕ ਉਹ ਸਾਡੇ ਤੋਂ ਆਪਣੇ ਪੁਰਜ਼ਿਆਂ ਨੂੰ ਦੁਬਾਰਾ ਕ੍ਰਮਬੱਧ ਕਰਦੇ ਹਨ। ਸਾਡੇ ਮਰਨ ਵਾਲਿਆਂ ਦਾ ਕਈ ਲੱਖ ਚੱਕਰਾਂ ਦੀ ਸੀਮਾ ਵਿੱਚ ਲੰਮੀ ਉਮਰ ਹੁੰਦੀ ਹੈ।
ਇੱਥੇ ਬੁਨਿਆਦੀ ਸਰਲ ਪ੍ਰਕਿਰਿਆ ਦੇ ਕਦਮ ਹਨ:
1.) ਆਮ ਤੌਰ 'ਤੇ ਸਟੀਲ ਤੋਂ ਉੱਲੀ ਦਾ ਉਤਪਾਦਨ
2.) ਡਾਈ ਕਾਸਟਿੰਗ ਮਸ਼ੀਨ 'ਤੇ ਮੋਲਡ ਲਗਾਇਆ ਗਿਆ
3.) ਪਿਸਟਨ ਪਿਘਲੀ ਹੋਈ ਧਾਤ ਨੂੰ ਗੁੰਝਲਦਾਰ ਵਿਸ਼ੇਸ਼ਤਾਵਾਂ ਅਤੇ ਪਤਲੀਆਂ ਕੰਧਾਂ ਨੂੰ ਭਰ ਕੇ ਡਾਈ ਕੈਵਿਟੀਜ਼ ਵਿੱਚ ਵਹਿਣ ਲਈ ਮਜਬੂਰ ਕਰਦਾ ਹੈ।
4.) ਪਿਘਲੇ ਹੋਏ ਧਾਤ ਨਾਲ ਉੱਲੀ ਨੂੰ ਭਰਨ ਤੋਂ ਬਾਅਦ, ਕਾਸਟਿੰਗ ਨੂੰ ਦਬਾਅ ਹੇਠ ਸਖ਼ਤ ਹੋਣ ਦਿੱਤਾ ਜਾਂਦਾ ਹੈ
5.) ਈਜੇਕਟਰ ਪਿੰਨ ਦੀ ਮਦਦ ਨਾਲ ਮੋਲਡ ਨੂੰ ਖੋਲ੍ਹਿਆ ਜਾਂਦਾ ਹੈ ਅਤੇ ਕਾਸਟਿੰਗ ਨੂੰ ਹਟਾ ਦਿੱਤਾ ਜਾਂਦਾ ਹੈ।
6.) ਹੁਣ ਖਾਲੀ ਡਾਈ ਨੂੰ ਦੁਬਾਰਾ ਲੁਬਰੀਕੇਟ ਕੀਤਾ ਜਾਂਦਾ ਹੈ ਅਤੇ ਅਗਲੇ ਚੱਕਰ ਲਈ ਕਲੈਂਪ ਕੀਤਾ ਜਾਂਦਾ ਹੈ।
ਡਾਈ ਕਾਸਟਿੰਗ ਵਿੱਚ, ਅਸੀਂ ਅਕਸਰ ਇਨਸਰਟ ਮੋਲਡਿੰਗ ਦੀ ਵਰਤੋਂ ਕਰਦੇ ਹਾਂ ਜਿੱਥੇ ਅਸੀਂ ਮੋਲਡ ਵਿੱਚ ਇੱਕ ਵਾਧੂ ਹਿੱਸਾ ਸ਼ਾਮਲ ਕਰਦੇ ਹਾਂ ਅਤੇ ਇਸਦੇ ਦੁਆਲੇ ਧਾਤ ਨੂੰ ਸੁੱਟ ਦਿੰਦੇ ਹਾਂ। ਠੋਸ ਹੋਣ ਤੋਂ ਬਾਅਦ, ਇਹ ਹਿੱਸੇ ਕਾਸਟ ਉਤਪਾਦ ਦਾ ਹਿੱਸਾ ਬਣ ਜਾਂਦੇ ਹਨ। ਡਾਈ ਕਾਸਟਿੰਗ ਦੇ ਫਾਇਦੇ ਭਾਗਾਂ ਦੀਆਂ ਚੰਗੀਆਂ ਮਕੈਨੀਕਲ ਵਿਸ਼ੇਸ਼ਤਾਵਾਂ, ਗੁੰਝਲਦਾਰ ਵਿਸ਼ੇਸ਼ਤਾਵਾਂ ਦੀ ਸੰਭਾਵਨਾ, ਵਧੀਆ ਵੇਰਵੇ ਅਤੇ ਚੰਗੀ ਸਤਹ ਮੁਕੰਮਲ, ਉੱਚ ਉਤਪਾਦਨ ਦਰਾਂ, ਆਸਾਨ ਆਟੋਮੇਸ਼ਨ ਹਨ। ਨੁਕਸਾਨ ਹਨ: ਉੱਚ ਡਾਈ ਅਤੇ ਸਾਜ਼ੋ-ਸਾਮਾਨ ਦੀ ਲਾਗਤ ਦੇ ਕਾਰਨ ਘੱਟ ਵਾਲੀਅਮ ਲਈ ਬਹੁਤ ਢੁਕਵਾਂ ਨਹੀਂ, ਕਾਸਟ ਕੀਤੇ ਜਾ ਸਕਣ ਵਾਲੇ ਆਕਾਰਾਂ ਵਿੱਚ ਸੀਮਾਵਾਂ, ਇਜੈਕਟਰ ਪਿੰਨ ਦੇ ਸੰਪਰਕ ਦੇ ਨਤੀਜੇ ਵਜੋਂ ਪਲੱਸਤਰ ਵਾਲੇ ਹਿੱਸਿਆਂ 'ਤੇ ਛੋਟੇ ਗੋਲ ਨਿਸ਼ਾਨ, ਵਿਭਾਜਨ ਲਾਈਨ 'ਤੇ ਧਾਤ ਦੀ ਪਤਲੀ ਫਲੈਸ਼, ਲੋੜ ਡਾਈ ਦੇ ਵਿਚਕਾਰ ਵਿਭਾਜਨ ਲਾਈਨ ਦੇ ਨਾਲ ਵੈਂਟਾਂ ਲਈ, ਪਾਣੀ ਦੇ ਗੇੜ ਦੀ ਵਰਤੋਂ ਕਰਕੇ ਉੱਲੀ ਦੇ ਤਾਪਮਾਨ ਨੂੰ ਘੱਟ ਰੱਖਣ ਦੀ ਜ਼ਰੂਰਤ।
• ਸੈਂਟਰਿਫਿਊਗਲ ਕਾਸਟਿੰਗ: ਪਿਘਲੀ ਹੋਈ ਧਾਤ ਨੂੰ ਰੋਟੇਸ਼ਨ ਦੇ ਧੁਰੇ 'ਤੇ ਘੁੰਮਦੇ ਉੱਲੀ ਦੇ ਕੇਂਦਰ ਵਿੱਚ ਡੋਲ੍ਹਿਆ ਜਾਂਦਾ ਹੈ। ਸੈਂਟਰਿਫਿਊਗਲ ਬਲ ਧਾਤ ਨੂੰ ਘੇਰੇ ਵੱਲ ਸੁੱਟ ਦਿੰਦੇ ਹਨ ਅਤੇ ਇਸ ਨੂੰ ਠੋਸ ਹੋਣ ਦਿੱਤਾ ਜਾਂਦਾ ਹੈ ਕਿਉਂਕਿ ਉੱਲੀ ਘੁੰਮਦੀ ਰਹਿੰਦੀ ਹੈ। ਹਰੀਜੱਟਲ ਅਤੇ ਵਰਟੀਕਲ ਧੁਰੀ ਰੋਟੇਸ਼ਨਾਂ ਦੀ ਵਰਤੋਂ ਕੀਤੀ ਜਾ ਸਕਦੀ ਹੈ। ਗੋਲ ਅੰਦਰੂਨੀ ਸਤਹਾਂ ਦੇ ਨਾਲ-ਨਾਲ ਹੋਰ ਗੈਰ-ਗੋਲ ਆਕਾਰਾਂ ਵਾਲੇ ਹਿੱਸੇ ਕਾਸਟ ਕੀਤੇ ਜਾ ਸਕਦੇ ਹਨ। ਪ੍ਰਕਿਰਿਆ ਨੂੰ ਇਸ ਤਰ੍ਹਾਂ ਸੰਖੇਪ ਕੀਤਾ ਜਾ ਸਕਦਾ ਹੈ:
1.) ਪਿਘਲੀ ਹੋਈ ਧਾਤ ਨੂੰ ਸੈਂਟਰਿਫਿਊਗਲ ਮੋਲਡ ਵਿੱਚ ਡੋਲ੍ਹਿਆ ਜਾਂਦਾ ਹੈ। ਫਿਰ ਧਾਤ ਨੂੰ ਉੱਲੀ ਦੇ ਕਤਾਈ ਕਾਰਨ ਬਾਹਰੀ ਕੰਧਾਂ ਵੱਲ ਧੱਕਿਆ ਜਾਂਦਾ ਹੈ।
2.) ਜਿਵੇਂ ਕਿ ਉੱਲੀ ਘੁੰਮਦੀ ਹੈ, ਧਾਤ ਦੀ ਕਾਸਟਿੰਗ ਸਖਤ ਹੋ ਜਾਂਦੀ ਹੈ
ਸੈਂਟਰਿਫਿਊਗਲ ਕਾਸਟਿੰਗ ਪਾਈਪਾਂ ਵਰਗੇ ਖੋਖਲੇ ਸਿਲੰਡਰ ਵਾਲੇ ਹਿੱਸਿਆਂ ਦੇ ਉਤਪਾਦਨ ਲਈ ਇੱਕ ਢੁਕਵੀਂ ਤਕਨੀਕ ਹੈ, ਸਪ੍ਰੂਜ਼, ਰਾਈਜ਼ਰ ਅਤੇ ਗੇਟਿੰਗ ਐਲੀਮੈਂਟਸ ਦੀ ਕੋਈ ਲੋੜ ਨਹੀਂ, ਚੰਗੀ ਸਤਹ ਫਿਨਿਸ਼ ਅਤੇ ਵਿਸਤ੍ਰਿਤ ਵਿਸ਼ੇਸ਼ਤਾਵਾਂ, ਕੋਈ ਸੁੰਗੜਨ ਦੀ ਸਮੱਸਿਆ ਨਹੀਂ, ਬਹੁਤ ਵੱਡੇ ਵਿਆਸ ਵਾਲੀਆਂ ਲੰਬੀਆਂ ਪਾਈਪਾਂ ਬਣਾਉਣ ਦੀ ਸੰਭਾਵਨਾ, ਉੱਚ ਦਰ ਉਤਪਾਦਨ ਸਮਰੱਥਾ। .
• ਨਿਰੰਤਰ ਕਾਸਟਿੰਗ (ਸਟ੍ਰੈਂਡ ਕਾਸਟਿੰਗ): ਧਾਤ ਦੀ ਇੱਕ ਨਿਰੰਤਰ ਲੰਬਾਈ ਨੂੰ ਕਾਸਟ ਕਰਨ ਲਈ ਵਰਤਿਆ ਜਾਂਦਾ ਹੈ। ਮੂਲ ਰੂਪ ਵਿੱਚ ਪਿਘਲੀ ਹੋਈ ਧਾਤ ਨੂੰ ਉੱਲੀ ਦੇ ਦੋ-ਅਯਾਮੀ ਪ੍ਰੋਫਾਈਲ ਵਿੱਚ ਸੁੱਟਿਆ ਜਾਂਦਾ ਹੈ ਪਰ ਇਸਦੀ ਲੰਬਾਈ ਅਨਿਸ਼ਚਿਤ ਹੁੰਦੀ ਹੈ। ਨਵੀਂ ਪਿਘਲੀ ਹੋਈ ਧਾਤ ਨੂੰ ਲਗਾਤਾਰ ਉੱਲੀ ਵਿੱਚ ਖੁਆਇਆ ਜਾਂਦਾ ਹੈ ਕਿਉਂਕਿ ਕਾਸਟਿੰਗ ਸਮੇਂ ਦੇ ਨਾਲ ਇਸਦੀ ਲੰਬਾਈ ਵਧਣ ਦੇ ਨਾਲ ਹੇਠਾਂ ਵੱਲ ਜਾਂਦੀ ਹੈ। ਤਾਂਬਾ, ਸਟੀਲ, ਅਲਮੀਨੀਅਮ ਵਰਗੀਆਂ ਧਾਤਾਂ ਨੂੰ ਲਗਾਤਾਰ ਕਾਸਟਿੰਗ ਪ੍ਰਕਿਰਿਆ ਦੀ ਵਰਤੋਂ ਕਰਦੇ ਹੋਏ ਲੰਬੇ ਤਾਰਾਂ ਵਿੱਚ ਸੁੱਟਿਆ ਜਾਂਦਾ ਹੈ। ਪ੍ਰਕਿਰਿਆ ਦੀਆਂ ਵੱਖ-ਵੱਖ ਸੰਰਚਨਾਵਾਂ ਹੋ ਸਕਦੀਆਂ ਹਨ ਪਰ ਆਮ ਨੂੰ ਇਸ ਤਰ੍ਹਾਂ ਸਰਲ ਬਣਾਇਆ ਜਾ ਸਕਦਾ ਹੈ:
1.) ਪਿਘਲੀ ਹੋਈ ਧਾਤ ਨੂੰ ਚੰਗੀ ਤਰ੍ਹਾਂ ਗਣਨਾ ਕੀਤੀ ਮਾਤਰਾ ਅਤੇ ਵਹਾਅ ਦਰਾਂ 'ਤੇ ਉੱਲੀ ਦੇ ਉੱਪਰ ਸਥਿਤ ਇੱਕ ਕੰਟੇਨਰ ਵਿੱਚ ਡੋਲ੍ਹਿਆ ਜਾਂਦਾ ਹੈ ਅਤੇ ਵਾਟਰ ਕੂਲਡ ਮੋਲਡ ਵਿੱਚੋਂ ਲੰਘਦਾ ਹੈ। ਉੱਲੀ ਵਿੱਚ ਪਾਈ ਗਈ ਧਾਤ ਦੀ ਕਾਸਟਿੰਗ ਮੋਲਡ ਦੇ ਤਲ 'ਤੇ ਰੱਖੀ ਇੱਕ ਸਟਾਰਟਰ ਬਾਰ ਵਿੱਚ ਠੋਸ ਹੋ ਜਾਂਦੀ ਹੈ। ਇਹ ਸਟਾਰਟਰ ਬਾਰ ਰੋਲਰਸ ਨੂੰ ਸ਼ੁਰੂ ਵਿੱਚ ਫੜਨ ਲਈ ਕੁਝ ਦਿੰਦਾ ਹੈ।
2.) ਲੰਬੇ ਧਾਤ ਦੇ ਸਟ੍ਰੈਂਡ ਨੂੰ ਰੋਲਰਾਂ ਦੁਆਰਾ ਇੱਕ ਸਥਿਰ ਗਤੀ ਨਾਲ ਲਿਜਾਇਆ ਜਾਂਦਾ ਹੈ। ਰੋਲਰ ਮੈਟਲ ਸਟ੍ਰੈਂਡ ਦੇ ਵਹਾਅ ਦੀ ਦਿਸ਼ਾ ਨੂੰ ਲੰਬਕਾਰੀ ਤੋਂ ਖਿਤਿਜੀ ਤੱਕ ਬਦਲਦੇ ਹਨ।
3.) ਲਗਾਤਾਰ ਕਾਸਟਿੰਗ ਦੇ ਇੱਕ ਨਿਸ਼ਚਿਤ ਲੇਟਵੀਂ ਦੂਰੀ ਦੀ ਯਾਤਰਾ ਕਰਨ ਤੋਂ ਬਾਅਦ, ਇੱਕ ਟਾਰਚ ਜਾਂ ਆਰਾ ਜੋ ਕਾਸਟਿੰਗ ਦੇ ਨਾਲ ਚਲਦਾ ਹੈ, ਇਸਨੂੰ ਲੋੜੀਂਦੀ ਲੰਬਾਈ ਤੱਕ ਤੇਜ਼ੀ ਨਾਲ ਕੱਟ ਦਿੰਦਾ ਹੈ।
ਨਿਰੰਤਰ ਕਾਸਟਿੰਗ ਪ੍ਰਕਿਰਿਆ ਨੂੰ ਰੋਲਿੰਗ ਪ੍ਰਕਿਰਿਆ ਨਾਲ ਜੋੜਿਆ ਜਾ ਸਕਦਾ ਹੈ, ਜਿੱਥੇ ਆਈ-ਬੀਮ, ਟੀ-ਬੀਮ ਆਦਿ ਪੈਦਾ ਕਰਨ ਲਈ ਲਗਾਤਾਰ ਕਾਸਟ ਧਾਤ ਨੂੰ ਸਿੱਧੇ ਰੋਲਿੰਗ ਮਿੱਲ ਵਿੱਚ ਖੁਆਇਆ ਜਾ ਸਕਦਾ ਹੈ। ਨਿਰੰਤਰ ਕਾਸਟਿੰਗ ਪੂਰੇ ਉਤਪਾਦ ਵਿੱਚ ਇਕਸਾਰ ਵਿਸ਼ੇਸ਼ਤਾਵਾਂ ਪੈਦਾ ਕਰਦੀ ਹੈ, ਇਸਦੀ ਉੱਚ ਠੋਸਤਾ ਦਰ ਹੁੰਦੀ ਹੈ, ਸਮੱਗਰੀ ਦੇ ਬਹੁਤ ਘੱਟ ਨੁਕਸਾਨ ਕਾਰਨ ਲਾਗਤ ਘਟਾਉਂਦੀ ਹੈ, ਇੱਕ ਪ੍ਰਕਿਰਿਆ ਦੀ ਪੇਸ਼ਕਸ਼ ਕਰਦੀ ਹੈ ਜਿੱਥੇ ਧਾਤ ਨੂੰ ਲੋਡ ਕਰਨਾ, ਡੋਲਣਾ, ਠੋਸ ਬਣਾਉਣਾ, ਕੱਟਣਾ ਅਤੇ ਕਾਸਟਿੰਗ ਹਟਾਉਣਾ ਸਭ ਇੱਕ ਨਿਰੰਤਰ ਕਾਰਜ ਵਿੱਚ ਹੁੰਦਾ ਹੈ ਅਤੇ ਇਸ ਤਰ੍ਹਾਂ ਉੱਚ ਉਤਪਾਦਕਤਾ ਦਰ ਅਤੇ ਉੱਚ ਗੁਣਵੱਤਾ ਦੇ ਨਤੀਜੇ ਵਜੋਂ. ਇੱਕ ਪ੍ਰਮੁੱਖ ਵਿਚਾਰ ਹਾਲਾਂਕਿ ਉੱਚ ਸ਼ੁਰੂਆਤੀ ਨਿਵੇਸ਼, ਸੈੱਟਅੱਪ ਲਾਗਤਾਂ ਅਤੇ ਸਪੇਸ ਲੋੜਾਂ ਹਨ।
• ਮਸ਼ੀਨਿੰਗ ਸੇਵਾਵਾਂ: ਅਸੀਂ ਤਿੰਨ, ਚਾਰ ਅਤੇ ਪੰਜ - ਐਕਸਿਸ ਮਸ਼ੀਨਿੰਗ ਦੀ ਪੇਸ਼ਕਸ਼ ਕਰਦੇ ਹਾਂ। ਮਸ਼ੀਨਿੰਗ ਪ੍ਰਕਿਰਿਆਵਾਂ ਦੀ ਕਿਸਮ ਜਿਸ ਦੀ ਅਸੀਂ ਵਰਤੋਂ ਕਰਦੇ ਹਾਂ ਉਹ ਹਨ ਟਰਨਿੰਗ, ਮਿਲਿੰਗ, ਡਰਿਲਿੰਗ, ਬੋਰਿੰਗ, ਬ੍ਰੋਚਿੰਗ, ਪਲੈਨਿੰਗ, ਸਾਵਿੰਗ, ਗ੍ਰਾਈਂਡਿੰਗ, ਲੈਪਿੰਗ, ਪਾਲਿਸ਼ਿੰਗ ਅਤੇ ਗੈਰ-ਰਵਾਇਤੀ ਮਸ਼ੀਨਾਂ ਜੋ ਸਾਡੀ ਵੈਬਸਾਈਟ ਦੇ ਇੱਕ ਵੱਖਰੇ ਮੀਨੂ ਦੇ ਹੇਠਾਂ ਵਿਸਤ੍ਰਿਤ ਹਨ। ਸਾਡੇ ਜ਼ਿਆਦਾਤਰ ਨਿਰਮਾਣ ਲਈ, ਅਸੀਂ ਸੀਐਨਸੀ ਮਸ਼ੀਨਾਂ ਦੀ ਵਰਤੋਂ ਕਰਦੇ ਹਾਂ. ਹਾਲਾਂਕਿ ਕੁਝ ਓਪਰੇਸ਼ਨਾਂ ਲਈ ਪਰੰਪਰਾਗਤ ਤਕਨੀਕਾਂ ਇੱਕ ਬਿਹਤਰ ਫਿਟ ਹਨ ਅਤੇ ਇਸ ਲਈ ਅਸੀਂ ਉਹਨਾਂ 'ਤੇ ਵੀ ਭਰੋਸਾ ਕਰਦੇ ਹਾਂ। ਸਾਡੀ ਮਸ਼ੀਨਿੰਗ ਸਮਰੱਥਾ ਉੱਚਤਮ ਪੱਧਰ 'ਤੇ ਪਹੁੰਚ ਜਾਂਦੀ ਹੈ ਅਤੇ ਕੁਝ ਸਭ ਤੋਂ ਵੱਧ ਮੰਗ ਵਾਲੇ ਹਿੱਸੇ AS9100 ਪ੍ਰਮਾਣਿਤ ਪਲਾਂਟ 'ਤੇ ਬਣਾਏ ਜਾਂਦੇ ਹਨ। ਜੈੱਟ ਇੰਜਣ ਬਲੇਡਾਂ ਲਈ ਬਹੁਤ ਹੀ ਵਿਸ਼ੇਸ਼ ਨਿਰਮਾਣ ਅਨੁਭਵ ਅਤੇ ਸਹੀ ਉਪਕਰਨ ਦੀ ਲੋੜ ਹੁੰਦੀ ਹੈ। ਏਰੋਸਪੇਸ ਉਦਯੋਗ ਦੇ ਬਹੁਤ ਸਖਤ ਮਾਪਦੰਡ ਹਨ। ਗੁੰਝਲਦਾਰ ਜਿਓਮੈਟ੍ਰਿਕਲ ਢਾਂਚੇ ਵਾਲੇ ਕੁਝ ਹਿੱਸੇ ਸਭ ਤੋਂ ਆਸਾਨੀ ਨਾਲ ਪੰਜ ਧੁਰੀ ਮਸ਼ੀਨਾਂ ਦੁਆਰਾ ਬਣਾਏ ਜਾਂਦੇ ਹਨ, ਜੋ ਕਿ ਸਾਡੇ ਸਮੇਤ ਕੁਝ ਮਸ਼ੀਨਿੰਗ ਪਲਾਂਟਾਂ ਵਿੱਚ ਹੀ ਪਾਏ ਜਾਂਦੇ ਹਨ। ਸਾਡੇ ਏਰੋਸਪੇਸ ਪ੍ਰਮਾਣਿਤ ਪਲਾਂਟ ਕੋਲ ਏਰੋਸਪੇਸ ਉਦਯੋਗ ਦੀ ਵਿਆਪਕ ਦਸਤਾਵੇਜ਼ੀ ਲੋੜਾਂ ਦੀ ਪਾਲਣਾ ਕਰਨ ਲਈ ਲੋੜੀਂਦਾ ਅਨੁਭਵ ਹੈ।
ਟਰਨਿੰਗ ਓਪਰੇਸ਼ਨਾਂ ਵਿੱਚ, ਇੱਕ ਵਰਕਪੀਸ ਨੂੰ ਘੁੰਮਾਇਆ ਜਾਂਦਾ ਹੈ ਅਤੇ ਇੱਕ ਕੱਟਣ ਵਾਲੇ ਟੂਲ ਦੇ ਵਿਰੁੱਧ ਹਿਲਾਇਆ ਜਾਂਦਾ ਹੈ। ਇਸ ਪ੍ਰਕਿਰਿਆ ਲਈ ਲੇਥ ਨਾਮਕ ਮਸ਼ੀਨ ਦੀ ਵਰਤੋਂ ਕੀਤੀ ਜਾ ਰਹੀ ਹੈ।
ਮਿਲਿੰਗ ਵਿੱਚ, ਮਿਲਿੰਗ ਮਸ਼ੀਨ ਨਾਮਕ ਇੱਕ ਮਸ਼ੀਨ ਵਿੱਚ ਇੱਕ ਵਰਕਪੀਸ ਦੇ ਵਿਰੁੱਧ ਸਹਿਣ ਲਈ ਕੱਟਣ ਵਾਲੇ ਕਿਨਾਰਿਆਂ ਨੂੰ ਲਿਆਉਣ ਲਈ ਇੱਕ ਰੋਟੇਟਿੰਗ ਟੂਲ ਹੁੰਦਾ ਹੈ।
ਡ੍ਰਿਲੰਗ ਓਪਰੇਸ਼ਨਾਂ ਵਿੱਚ ਕੱਟਣ ਵਾਲੇ ਕਿਨਾਰਿਆਂ ਵਾਲਾ ਇੱਕ ਘੁੰਮਦਾ ਕਟਰ ਸ਼ਾਮਲ ਹੁੰਦਾ ਹੈ ਜੋ ਵਰਕਪੀਸ ਦੇ ਸੰਪਰਕ ਵਿੱਚ ਆਉਣ 'ਤੇ ਛੇਕ ਪੈਦਾ ਕਰਦਾ ਹੈ। ਡ੍ਰਿਲ ਪ੍ਰੈਸ, ਖਰਾਦ ਜਾਂ ਮਿੱਲਾਂ ਦੀ ਵਰਤੋਂ ਆਮ ਤੌਰ 'ਤੇ ਕੀਤੀ ਜਾਂਦੀ ਹੈ।
ਬੋਰਿੰਗ ਓਪਰੇਸ਼ਨਾਂ ਵਿੱਚ ਮੋਰੀ ਨੂੰ ਥੋੜ੍ਹਾ ਵੱਡਾ ਕਰਨ ਅਤੇ ਸ਼ੁੱਧਤਾ ਵਿੱਚ ਸੁਧਾਰ ਕਰਨ ਲਈ ਇੱਕ ਕਤਾਈ ਵਾਲੇ ਵਰਕਪੀਸ ਵਿੱਚ ਇੱਕ ਮੋਰੀ ਹੋਈ ਨੋਕ ਵਾਲੇ ਇੱਕ ਟੂਲ ਨੂੰ ਇੱਕ ਮੋਟੇ ਮੋਰੀ ਵਿੱਚ ਭੇਜਿਆ ਜਾਂਦਾ ਹੈ। ਇਹ ਵਧੀਆ ਮੁਕੰਮਲ ਕਰਨ ਦੇ ਉਦੇਸ਼ਾਂ ਲਈ ਵਰਤਿਆ ਜਾਂਦਾ ਹੈ.
ਬ੍ਰੋਚਿੰਗ ਵਿੱਚ ਬਰੋਚ (ਦੰਦਾਂ ਵਾਲਾ ਟੂਲ) ਦੇ ਇੱਕ ਪਾਸ ਵਿੱਚ ਵਰਕਪੀਸ ਤੋਂ ਸਮੱਗਰੀ ਨੂੰ ਹਟਾਉਣ ਲਈ ਦੰਦਾਂ ਵਾਲਾ ਟੂਲ ਸ਼ਾਮਲ ਹੁੰਦਾ ਹੈ। ਲੀਨੀਅਰ ਬ੍ਰੋਚਿੰਗ ਵਿੱਚ, ਬਰੋਚ ਕੱਟ ਨੂੰ ਪ੍ਰਭਾਵਤ ਕਰਨ ਲਈ ਵਰਕਪੀਸ ਦੀ ਇੱਕ ਸਤਹ ਦੇ ਵਿਰੁੱਧ ਰੇਖਿਕ ਤੌਰ 'ਤੇ ਚੱਲਦਾ ਹੈ, ਜਦੋਂ ਕਿ ਰੋਟਰੀ ਬ੍ਰੋਚਿੰਗ ਵਿੱਚ, ਇੱਕ ਧੁਰੀ ਸਮਮਿਤੀ ਆਕਾਰ ਨੂੰ ਕੱਟਣ ਲਈ ਬਰੋਚ ਨੂੰ ਘੁੰਮਾਇਆ ਜਾਂਦਾ ਹੈ ਅਤੇ ਵਰਕਪੀਸ ਵਿੱਚ ਦਬਾਇਆ ਜਾਂਦਾ ਹੈ।
ਸਵਿਸ ਟਾਈਪ ਮਸ਼ੀਨਿੰਗ ਸਾਡੀ ਕੀਮਤੀ ਤਕਨੀਕਾਂ ਵਿੱਚੋਂ ਇੱਕ ਹੈ ਜੋ ਅਸੀਂ ਛੋਟੇ ਉੱਚ ਸ਼ੁੱਧਤਾ ਵਾਲੇ ਹਿੱਸਿਆਂ ਦੇ ਉੱਚ ਵਾਲੀਅਮ ਨਿਰਮਾਣ ਲਈ ਵਰਤਦੇ ਹਾਂ। ਸਵਿਸ-ਕਿਸਮ ਦੀ ਖਰਾਦ ਦੀ ਵਰਤੋਂ ਕਰਕੇ ਅਸੀਂ ਛੋਟੇ, ਗੁੰਝਲਦਾਰ, ਸਟੀਕ ਪੁਰਜ਼ਿਆਂ ਨੂੰ ਸਸਤੇ ਢੰਗ ਨਾਲ ਬਦਲਦੇ ਹਾਂ। ਰਵਾਇਤੀ ਖਰਾਦ ਦੇ ਉਲਟ ਜਿੱਥੇ ਵਰਕਪੀਸ ਨੂੰ ਸਥਿਰ ਰੱਖਿਆ ਜਾਂਦਾ ਹੈ ਅਤੇ ਟੂਲ ਚਲਦਾ ਰਹਿੰਦਾ ਹੈ, ਸਵਿਸ-ਕਿਸਮ ਦੇ ਮੋੜ ਕੇਂਦਰਾਂ ਵਿੱਚ, ਵਰਕਪੀਸ ਨੂੰ Z-ਧੁਰੇ ਵਿੱਚ ਜਾਣ ਦੀ ਇਜਾਜ਼ਤ ਦਿੱਤੀ ਜਾਂਦੀ ਹੈ ਅਤੇ ਟੂਲ ਸਥਿਰ ਹੁੰਦਾ ਹੈ। ਸਵਿਸ-ਕਿਸਮ ਦੀ ਮਸ਼ੀਨਿੰਗ ਵਿੱਚ, ਬਾਰ ਸਟਾਕ ਨੂੰ ਮਸ਼ੀਨ ਵਿੱਚ ਰੱਖਿਆ ਜਾਂਦਾ ਹੈ ਅਤੇ z-ਧੁਰੇ ਵਿੱਚ ਇੱਕ ਗਾਈਡ ਬੁਸ਼ਿੰਗ ਦੁਆਰਾ ਅੱਗੇ ਵਧਾਇਆ ਜਾਂਦਾ ਹੈ, ਸਿਰਫ ਮਸ਼ੀਨ ਕੀਤੇ ਜਾਣ ਵਾਲੇ ਹਿੱਸੇ ਦਾ ਪਰਦਾਫਾਸ਼ ਕਰਦਾ ਹੈ। ਇਸ ਤਰ੍ਹਾਂ ਇੱਕ ਸਖ਼ਤ ਪਕੜ ਯਕੀਨੀ ਬਣਾਈ ਜਾਂਦੀ ਹੈ ਅਤੇ ਸ਼ੁੱਧਤਾ ਬਹੁਤ ਜ਼ਿਆਦਾ ਹੁੰਦੀ ਹੈ। ਲਾਈਵ ਟੂਲਸ ਦੀ ਉਪਲਬਧਤਾ ਗਾਈਡ ਬੁਸ਼ਿੰਗ ਤੋਂ ਸਮੱਗਰੀ ਦੇ ਅੱਗੇ ਵਧਣ ਦੇ ਨਾਲ ਮਿਲ ਅਤੇ ਡ੍ਰਿਲ ਕਰਨ ਦਾ ਮੌਕਾ ਪ੍ਰਦਾਨ ਕਰਦੀ ਹੈ। ਸਵਿਸ-ਕਿਸਮ ਦੇ ਸਾਜ਼ੋ-ਸਾਮਾਨ ਦਾ Y-ਧੁਰਾ ਪੂਰੀ ਮਿਲਿੰਗ ਸਮਰੱਥਾ ਪ੍ਰਦਾਨ ਕਰਦਾ ਹੈ ਅਤੇ ਨਿਰਮਾਣ ਵਿੱਚ ਬਹੁਤ ਸਮਾਂ ਬਚਾਉਂਦਾ ਹੈ। ਇਸ ਤੋਂ ਇਲਾਵਾ, ਸਾਡੀਆਂ ਮਸ਼ੀਨਾਂ ਵਿਚ ਡ੍ਰਿਲਸ ਅਤੇ ਬੋਰਿੰਗ ਟੂਲ ਹਨ ਜੋ ਉਸ ਹਿੱਸੇ 'ਤੇ ਕੰਮ ਕਰਦੇ ਹਨ ਜਦੋਂ ਇਹ ਸਬ ਸਪਿੰਡਲ ਵਿਚ ਰੱਖੀ ਜਾਂਦੀ ਹੈ। ਸਾਡੀ ਸਵਿਸ-ਟਾਈਪ ਮਸ਼ੀਨਿੰਗ ਸਮਰੱਥਾ ਸਾਨੂੰ ਇੱਕ ਸਿੰਗਲ ਓਪਰੇਸ਼ਨ ਵਿੱਚ ਇੱਕ ਪੂਰੀ ਤਰ੍ਹਾਂ ਸਵੈਚਲਿਤ ਸੰਪੂਰਨ ਮਸ਼ੀਨਿੰਗ ਦਾ ਮੌਕਾ ਦਿੰਦੀ ਹੈ।
ਮਸ਼ੀਨਿੰਗ AGS-TECH Inc. ਕਾਰੋਬਾਰ ਦੇ ਸਭ ਤੋਂ ਵੱਡੇ ਹਿੱਸਿਆਂ ਵਿੱਚੋਂ ਇੱਕ ਹੈ। ਅਸੀਂ ਜਾਂ ਤਾਂ ਇਸਨੂੰ ਇੱਕ ਪ੍ਰਾਇਮਰੀ ਓਪਰੇਸ਼ਨ ਦੇ ਤੌਰ ਤੇ ਜਾਂ ਕਿਸੇ ਹਿੱਸੇ ਨੂੰ ਕੱਢਣ ਜਾਂ ਕੱਢਣ ਤੋਂ ਬਾਅਦ ਇੱਕ ਸੈਕੰਡਰੀ ਓਪਰੇਸ਼ਨ ਦੇ ਤੌਰ ਤੇ ਵਰਤਦੇ ਹਾਂ ਤਾਂ ਜੋ ਸਾਰੀਆਂ ਡਰਾਇੰਗ ਵਿਸ਼ੇਸ਼ਤਾਵਾਂ ਨੂੰ ਪੂਰਾ ਕੀਤਾ ਜਾ ਸਕੇ।
• ਸਰਫੇਸ ਫਿਨਿਸ਼ਿੰਗ ਸੇਵਾਵਾਂ: ਅਸੀਂ ਸਰਫੇਸ ਟਰੀਟਮੈਂਟ ਅਤੇ ਸਰਫੇਸ ਫਿਨਿਸ਼ਿੰਗ ਦੀ ਇੱਕ ਵਿਸ਼ਾਲ ਕਿਸਮ ਦੀ ਪੇਸ਼ਕਸ਼ ਕਰਦੇ ਹਾਂ ਜਿਵੇਂ ਕਿ ਅਡਿਸ਼ਨ ਨੂੰ ਵਧਾਉਣ ਲਈ ਸਤਹ ਕੰਡੀਸ਼ਨਿੰਗ, ਕੋਟਿੰਗ ਦੇ ਅਡਜਸ਼ਨ ਨੂੰ ਵਧਾਉਣ ਲਈ ਪਤਲੀ ਆਕਸਾਈਡ ਪਰਤ ਜਮ੍ਹਾ ਕਰਨਾ, ਸੈਂਡ ਬਲਾਸਟਿੰਗ, ਕੈਮ-ਫਿਲਮ, ਐਨੋਡਾਈਜ਼ਿੰਗ, ਨਾਈਟ੍ਰਾਈਡਿੰਗ, ਪਾਊਡਰ ਕੋਟਿੰਗ, ਸਪਰੇਅ ਕੋਟਿੰਗ। , ਵੱਖ-ਵੱਖ ਉੱਨਤ ਧਾਤੂਕਰਨ ਅਤੇ ਪਰਤ ਦੀਆਂ ਤਕਨੀਕਾਂ ਜਿਵੇਂ ਕਿ ਸਪਟਰਿੰਗ, ਇਲੈਕਟ੍ਰੋਨ ਬੀਮ, ਵਾਸ਼ਪੀਕਰਨ, ਪਲੇਟਿੰਗ, ਹਾਰਡ ਕੋਟਿੰਗ ਜਿਵੇਂ ਕਿ ਹੀਰਾ ਜਿਵੇਂ ਕਿ ਕਾਰਬਨ (DLC) ਜਾਂ ਡ੍ਰਿਲੰਗ ਅਤੇ ਕੱਟਣ ਵਾਲੇ ਸਾਧਨਾਂ ਲਈ ਟਾਈਟੇਨੀਅਮ ਕੋਟਿੰਗ।
• ਉਤਪਾਦ ਮਾਰਕਿੰਗ ਅਤੇ ਲੇਬਲਿੰਗ ਸੇਵਾਵਾਂ: ਸਾਡੇ ਬਹੁਤ ਸਾਰੇ ਗਾਹਕਾਂ ਨੂੰ ਮਾਰਕਿੰਗ ਅਤੇ ਲੇਬਲਿੰਗ, ਲੇਜ਼ਰ ਮਾਰਕਿੰਗ, ਧਾਤ ਦੇ ਹਿੱਸਿਆਂ 'ਤੇ ਉੱਕਰੀ ਕਰਨ ਦੀ ਲੋੜ ਹੁੰਦੀ ਹੈ। ਜੇਕਰ ਤੁਹਾਨੂੰ ਅਜਿਹੀ ਕੋਈ ਲੋੜ ਹੈ, ਤਾਂ ਆਓ ਇਸ ਬਾਰੇ ਚਰਚਾ ਕਰੀਏ ਕਿ ਤੁਹਾਡੇ ਲਈ ਕਿਹੜਾ ਵਿਕਲਪ ਸਭ ਤੋਂ ਵਧੀਆ ਹੋਵੇਗਾ।
ਇੱਥੇ ਕੁਝ ਆਮ ਤੌਰ 'ਤੇ ਵਰਤੇ ਜਾਂਦੇ ਮੈਟਲ ਕਾਸਟ ਉਤਪਾਦ ਹਨ। ਕਿਉਂਕਿ ਇਹ ਸ਼ੈਲਫ ਤੋਂ ਬਾਹਰ ਹਨ, ਜੇਕਰ ਇਹਨਾਂ ਵਿੱਚੋਂ ਕੋਈ ਵੀ ਤੁਹਾਡੀਆਂ ਜ਼ਰੂਰਤਾਂ ਨੂੰ ਪੂਰਾ ਕਰਦਾ ਹੈ ਤਾਂ ਤੁਸੀਂ ਮੋਲਡ ਲਾਗਤਾਂ ਨੂੰ ਬਚਾ ਸਕਦੇ ਹੋ:
AGS-Electronics ਤੋਂ ਸਾਡੇ 11 ਸੀਰੀਜ਼ ਡਾਈ-ਕਾਸਟ ਐਲੂਮੀਨੀਅਮ ਬਾਕਸ ਨੂੰ ਡਾਊਨਲੋਡ ਕਰਨ ਲਈ ਇੱਥੇ ਕਲਿੱਕ ਕਰੋ