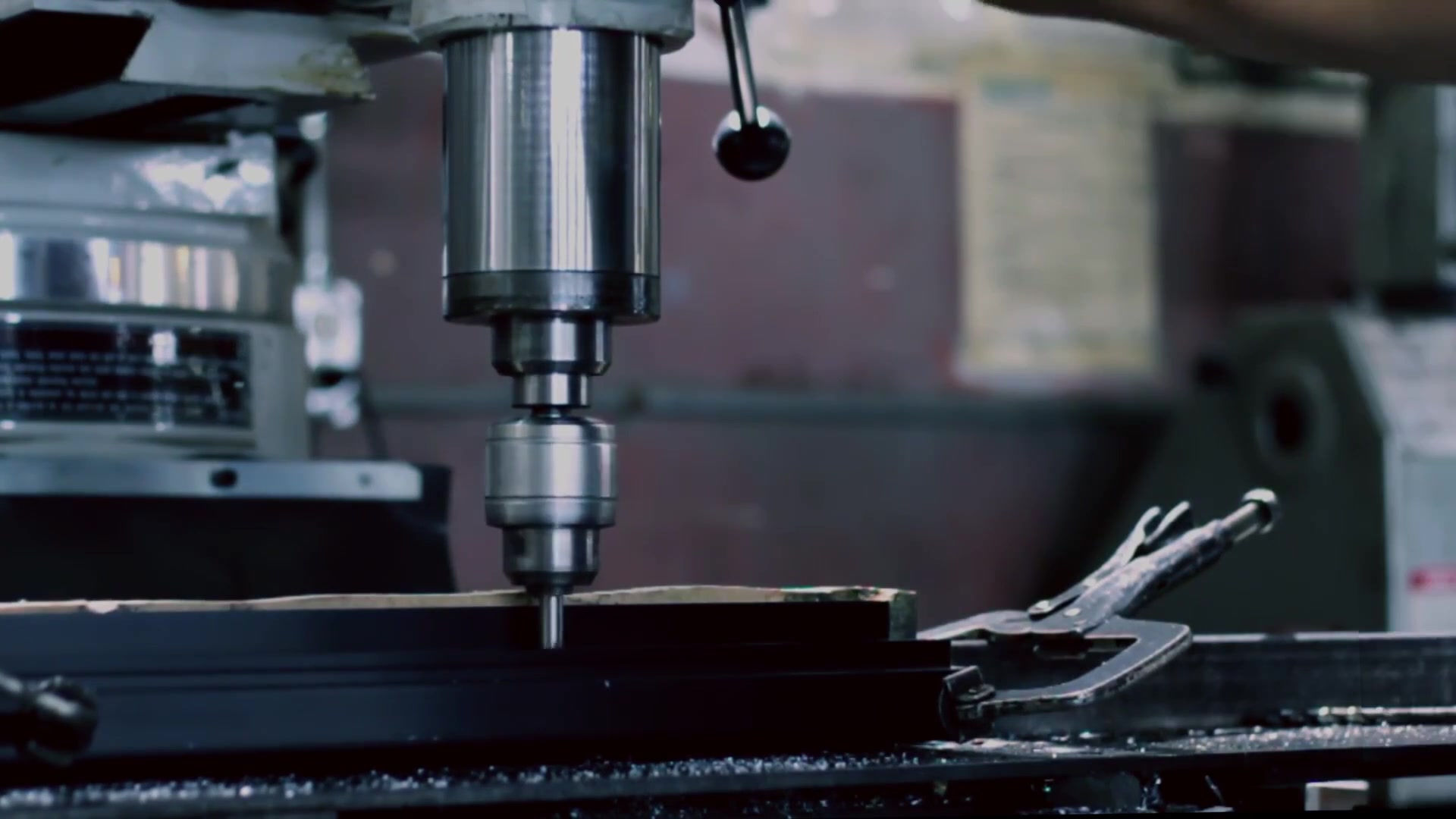
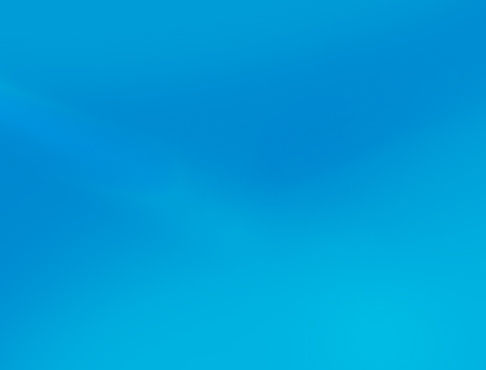
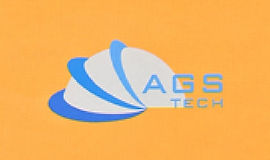
Globalny producent na zamówienie, integrator, konsolidator, partner outsourcingowy w zakresie szerokiej gamy produktów i usług.
Jesteśmy Twoim źródłem kompleksowej obsługi w zakresie produkcji, wytwarzania, inżynierii, konsolidacji, integracji, outsourcingu produktów i usług produkowanych na zamówienie oraz gotowych.
Choose your Language
-
Produkcja na zamówienie
-
Produkcja kontraktowa w kraju i na świecie
-
Outsourcing produkcji
-
Zamówienia krajowe i globalne
-
Konsolidacja
-
Integracja inżynierska
-
Usługi inżynieryjne
Powierzchnie pokrywają wszystko. Atrakcyjność i funkcje, jakie zapewniają nam powierzchnie materiałów, mają ogromne znaczenie. Dlatego POWIERZCHNIA OBRÓBKA and MODYFIKACJA POWIERZCHNI_cc781905-5cde-3194-bb58b-1. Obróbka i modyfikacja powierzchni prowadzi do polepszenia właściwości powierzchni i może być wykonywana jako końcowa operacja wykańczająca lub przed powlekaniem lub operacją łączenia. Procesy obróbki powierzchni i modyfikacji (określane również jako SURFACE ENGINEERING) , dostosować powierzchnie materiałów i produktów do:
- Kontroluj tarcie i zużycie
- Poprawić odporność na korozję
- Poprawić przyczepność kolejnych powłok lub łączonych części
- Zmień właściwości fizyczne przewodnictwo, rezystywność, energię powierzchniową i odbicie
- Zmiana właściwości chemicznych powierzchni poprzez wprowadzenie grup funkcyjnych
- Zmień wymiary
- Zmień wygląd, np. kolor, szorstkość… itp.
- Oczyścić i/lub zdezynfekować powierzchnie
Dzięki obróbce powierzchni i modyfikacji można poprawić funkcje i żywotność materiałów. Nasze wspólne metody obróbki i modyfikacji powierzchni można podzielić na dwie główne kategorie:
Obróbka i modyfikacja powierzchni, która obejmuje powierzchnie:
Powłoki organiczne: Powłoki organiczne nakładają farby, cementy, laminaty, stapiane proszki i smary na powierzchnie materiałów.
Powłoki nieorganiczne: Nasze popularne powłoki nieorganiczne to powlekanie galwaniczne, powlekanie autokatalityczne (powłoki bezelektrodowe), powłoki konwersyjne, natryskiwanie termiczne, zanurzanie na gorąco, napawanie, stapianie w piecach, powłoki cienkowarstwowe, takie jak SiO2, SiN na metalu, szkle, ceramice itp. Obróbka powierzchni i modyfikacja obejmująca powłoki są szczegółowo wyjaśnione w odpowiednim podmenu, proszękliknij tutaj Powłoki funkcjonalne / Powłoki dekoracyjne / Cienkowarstwowe / Grubowarstwowe
Obróbka i modyfikacja powierzchni, która zmienia powierzchnie: Tutaj na tej stronie skoncentrujemy się na nich. Nie wszystkie opisane poniżej techniki obróbki powierzchni i modyfikacji są w skali mikro lub nano, niemniej jednak wspomnimy o nich pokrótce, ponieważ podstawowe cele i metody są w znacznym stopniu podobne do tych, które są w skali mikroprodukcji.
Hartowanie: selektywne hartowanie powierzchni za pomocą lasera, płomienia, indukcji i wiązki elektronów.
Zabiegi wysokoenergetyczne: Niektóre z naszych zabiegów wysokoenergetycznych obejmują implantację jonów, szklenie i fuzję laserową oraz leczenie wiązką elektronów.
Obróbki cienkiej dyfuzji: Procesy cienkiej dyfuzji obejmują azotonawęglanie ferrytowe, borowanie, inne procesy reakcji wysokotemperaturowych, takie jak TiC, VC.
Obróbki ciężkiej dyfuzji: Nasze procesy ciężkiej dyfuzji obejmują nawęglanie, azotowanie i węgloazotowanie.
Specjalne zabiegi powierzchniowe: Specjalne zabiegi, takie jak obróbka kriogeniczna, magnetyczna i dźwiękowa, wpływają zarówno na powierzchnie, jak i materiały sypkie.
Selektywne procesy hartowania mogą być prowadzone płomieniem, indukcją, wiązką elektronów, wiązką lasera. Duże podłoża są głęboko utwardzane za pomocą hartowania płomieniowego. Z drugiej strony hartowanie indukcyjne stosuje się do małych części. Hartowanie wiązką laserową i elektronową czasami nie różni się od utwardzania lub obróbki wysokoenergetycznej. Te procesy obróbki powierzchni i modyfikacji mają zastosowanie tylko do stali, które mają wystarczającą zawartość węgla i stopu, aby umożliwić hartowanie. Do tej metody obróbki powierzchni i modyfikacji nadają się żeliwa, stale węglowe, stale narzędziowe i stale stopowe. Wymiary części nie ulegają znaczącym zmianom w wyniku utwardzania powierzchni. Głębokość utwardzenia może wynosić od 250 mikronów do całej głębokości przekroju. Jednak w przypadku całej sekcji, sekcja musi być cienka, mniejsza niż 25 mm (1 cal) lub mała, ponieważ procesy hartowania wymagają szybkiego chłodzenia materiałów, czasami w ciągu sekundy. Jest to trudne do osiągnięcia w przypadku dużych detali, dlatego w przypadku dużych przekrojów można utwardzać tylko powierzchnie. Jako popularny proces obróbki i modyfikacji powierzchni hartujemy sprężyny, ostrza noży i ostrza chirurgiczne wśród wielu innych produktów.
Procesy wysokoenergetyczne to stosunkowo nowe metody obróbki powierzchni i modyfikacji. Właściwości powierzchni są zmieniane bez zmiany wymiarów. Nasze popularne wysokoenergetyczne procesy obróbki powierzchni to obróbka wiązką elektronów, implantacja jonów i obróbka wiązką laserową.
Obróbka wiązką elektronów: Obróbka powierzchni wiązką elektronów zmienia właściwości powierzchni poprzez szybkie nagrzewanie i szybkie chłodzenie — rzędu 10Exp6 stopni Celsjusza/s (10exp6 Fahrenheit/s) w bardzo płytkim obszarze około 100 mikronów w pobliżu powierzchni materiału. Obróbka wiązką elektronów może być również stosowana w napawaniu do produkcji stopów powierzchniowych.
Implantacja jonów: Ta metoda obróbki i modyfikacji powierzchni wykorzystuje wiązkę elektronów lub plazmę do konwersji atomów gazu na jony o wystarczającej energii i implantacji/wstawienia jonów do sieci atomowej podłoża, przyspieszanej przez cewki magnetyczne w komorze próżniowej. Próżnia ułatwia swobodny ruch jonów w komorze. Niedopasowanie implantowanych jonów do powierzchni metalu powoduje defekty atomowe, które utwardzają powierzchnię.
Obróbka wiązką laserową: Podobnie jak obróbka i modyfikacja powierzchni wiązką elektronów, obróbka wiązką laserową zmienia właściwości powierzchni poprzez szybkie nagrzewanie i szybkie chłodzenie w bardzo płytkim obszarze w pobliżu powierzchni. Ta metoda obróbki i modyfikacji powierzchni może być również stosowana w napawaniu do produkcji stopów powierzchniowych.
Know-how w zakresie dawkowania implantów i parametrów obróbki umożliwia nam stosowanie tych wysokoenergetycznych technik obróbki powierzchni w naszych zakładach produkcyjnych.
Obróbka powierzchni cienkiej dyfuzji:
Węgloazotowanie ferrytyczne to proces hartowania powierzchniowego, który polega na dyfuzji azotu i węgla do metali żelaznych w temperaturach podkrytycznych. Temperatura przetwarzania wynosi zwykle 565 stopni Celsjusza (1049 Fahrenheita). W tej temperaturze stale i inne stopy żelaza nadal znajdują się w fazie ferrytycznej, co jest korzystne w porównaniu z innymi procesami hartowania powierzchniowego zachodzącymi w fazie austenitycznej. Proces służy do poprawy:
• odporność na ścieranie
•właściwości zmęczeniowe
•odporność na korozję
Dzięki niskim temperaturom obróbki podczas procesu hartowania dochodzi do bardzo niewielkich zniekształceń kształtu.
Borowanie to proces, w którym bor jest wprowadzany do metalu lub stopu. Jest to proces utwardzania i modyfikacji powierzchni, w którym atomy boru są dyfundowane na powierzchnię elementu metalowego. W rezultacie powierzchnia zawiera borki metali, takie jak borki żelaza i borki niklu. W stanie czystym borki te mają wyjątkowo wysoką twardość i odporność na zużycie. Części z borowanego metalu są wyjątkowo odporne na zużycie i często wytrzymują do pięciu razy dłużej niż elementy poddane konwencjonalnym obróbkom cieplnym, takim jak hartowanie, nawęglanie, azotowanie, azotonawęglanie lub hartowanie indukcyjne.
Obróbka i modyfikacja powierzchni o dużej dyfuzji: Jeśli zawartość węgla jest niska (na przykład mniej niż 0,25%), możemy zwiększyć zawartość węgla w powierzchni w celu utwardzenia. Część można poddać obróbce cieplnej poprzez hartowanie w cieczy lub schłodzić w nieruchomym powietrzu, w zależności od pożądanych właściwości. Ta metoda umożliwi tylko miejscowe utwardzenie na powierzchni, ale nie w rdzeniu. Czasami jest to bardzo pożądane, ponieważ pozwala na uzyskanie twardej powierzchni o dobrych właściwościach ścieralnych, jak w przypadku kół zębatych, ale ma twardy rdzeń wewnętrzny, który będzie dobrze działał pod obciążeniem udarowym.
W jednej z technik obróbki i modyfikacji powierzchni, a mianowicie nawęglaniu, dodajemy węgiel do powierzchni. Wystawiamy część na działanie atmosfery bogatej w węgiel w podwyższonej temperaturze i umożliwiamy dyfuzję przeniesienia atomów węgla do stali. Dyfuzja nastąpi tylko wtedy, gdy stal ma niską zawartość węgla, ponieważ dyfuzja działa na zasadzie różnicy stężeń.
Nawęglanie pakietowe: Części są pakowane w medium wysokowęglowym, takim jak proszek węglowy, i ogrzewane w piecu przez 12 do 72 godzin w temperaturze 900 stopni Celsjusza (1652 Fahrenheita). W tych temperaturach powstaje gaz CO, który jest silnym środkiem redukującym. Reakcja redukcji zachodzi na powierzchni stali uwalniającej węgiel. Węgiel jest następnie dyfundowany do powierzchni dzięki wysokiej temperaturze. Węgiel na powierzchni wynosi od 0,7% do 1,2% w zależności od warunków procesu. Osiągnięta twardość to 60 - 65 RC. Głębokość nawęglanej obudowy waha się od około 0,1 mm do 1,5 mm. Nawęglanie pakietowe wymaga dobrej kontroli równomierności temperatury i konsystencji ogrzewania.
Nawęglanie gazowe: W tym wariancie obróbki powierzchni gazowy tlenek węgla (CO) jest dostarczany do rozgrzanego pieca, a reakcja redukcji osadzania węgla odbywa się na powierzchni części. Proces ten przezwycięża większość problemów związanych z nawęglaniem pakietowym. Jedną z obaw jest jednak bezpieczne przechowywanie gazu CO.
Nawęglanie płynne: Części stalowe są zanurzane w kąpieli bogatej w stopiony węgiel.
Azotowanie to proces obróbki i modyfikacji powierzchni polegający na dyfuzji azotu na powierzchnię stali. Azot tworzy azotki z pierwiastkami takimi jak aluminium, chrom i molibden. Części są poddawane obróbce cieplnej i odpuszczaniu przed azotowaniem. Części są następnie czyszczone i ogrzewane w piecu w atmosferze zdysocjowanego amoniaku (zawierającego N i H) przez 10 do 40 godzin w temperaturze 500-625 stopni Celsjusza (932-1157 Fahrenheita). Azot dyfunduje do stali i tworzy stopy azotkowe. Wnika na głębokość do 0,65 mm. Koperta jest bardzo twarda, a zniekształcenia niewielkie. Ponieważ obudowa jest cienka, szlifowanie powierzchni nie jest zalecane i dlatego azotowanie może nie być opcją dla powierzchni o bardzo gładkich wymaganiach wykończeniowych.
Proces obróbki i modyfikacji powierzchni węgloazotowania jest najbardziej odpowiedni dla stali niskowęglowych. W procesie węgloazotowania zarówno węgiel, jak i azot są dyfundowane do powierzchni. Części są ogrzewane w atmosferze węglowodoru (takiego jak metan lub propan) zmieszanego z amoniakiem (NH3). Mówiąc najprościej, proces jest mieszanką nawęglania i azotowania. Węgloazotowanie powierzchni przeprowadza się w temperaturach 760 - 870 stopni Celsjusza (1400 - 1598 Fahrenheita), a następnie hartuje się w atmosferze gazu ziemnego (beztlenowego). Proces węgloazotowania nie jest odpowiedni dla części o wysokiej precyzji ze względu na nieodłączne zniekształcenia. Osiągnięta twardość jest podobna do nawęglania (60 - 65 RC), ale nie tak wysoka jak podczas azotowania (70 RC). Głębokość koperty wynosi od 0,1 do 0,75 mm. Obudowa jest bogata w azotki oraz martenzyt. Konieczne jest późniejsze odpuszczanie, aby zmniejszyć kruchość.
Specjalne procesy obróbki powierzchni i modyfikacji znajdują się na wczesnym etapie rozwoju, a ich skuteczność nie została jeszcze udowodniona. Oni są:
Obróbka kriogeniczna: Zwykle stosowana na stalach hartowanych, powoli schładza podłoże do około -166 stopni Celsjusza (-300 Fahrenheita), aby zwiększyć gęstość materiału, a tym samym zwiększyć odporność na zużycie i stabilność wymiarów.
Obróbka wibracyjna: mają na celu złagodzenie naprężeń termicznych nagromadzonych podczas obróbki cieplnej poprzez wibracje i wydłużenie żywotności.
Obróbka magnetyczna: mają one na celu zmianę układu atomów w materiałach za pomocą pól magnetycznych i miejmy nadzieję, że poprawią się żywotność.
Skuteczność tych specjalnych technik obróbki powierzchni i modyfikacji wciąż pozostaje do udowodnienia. Również te trzy powyższe techniki wpływają na materiał sypki oprócz powierzchni.