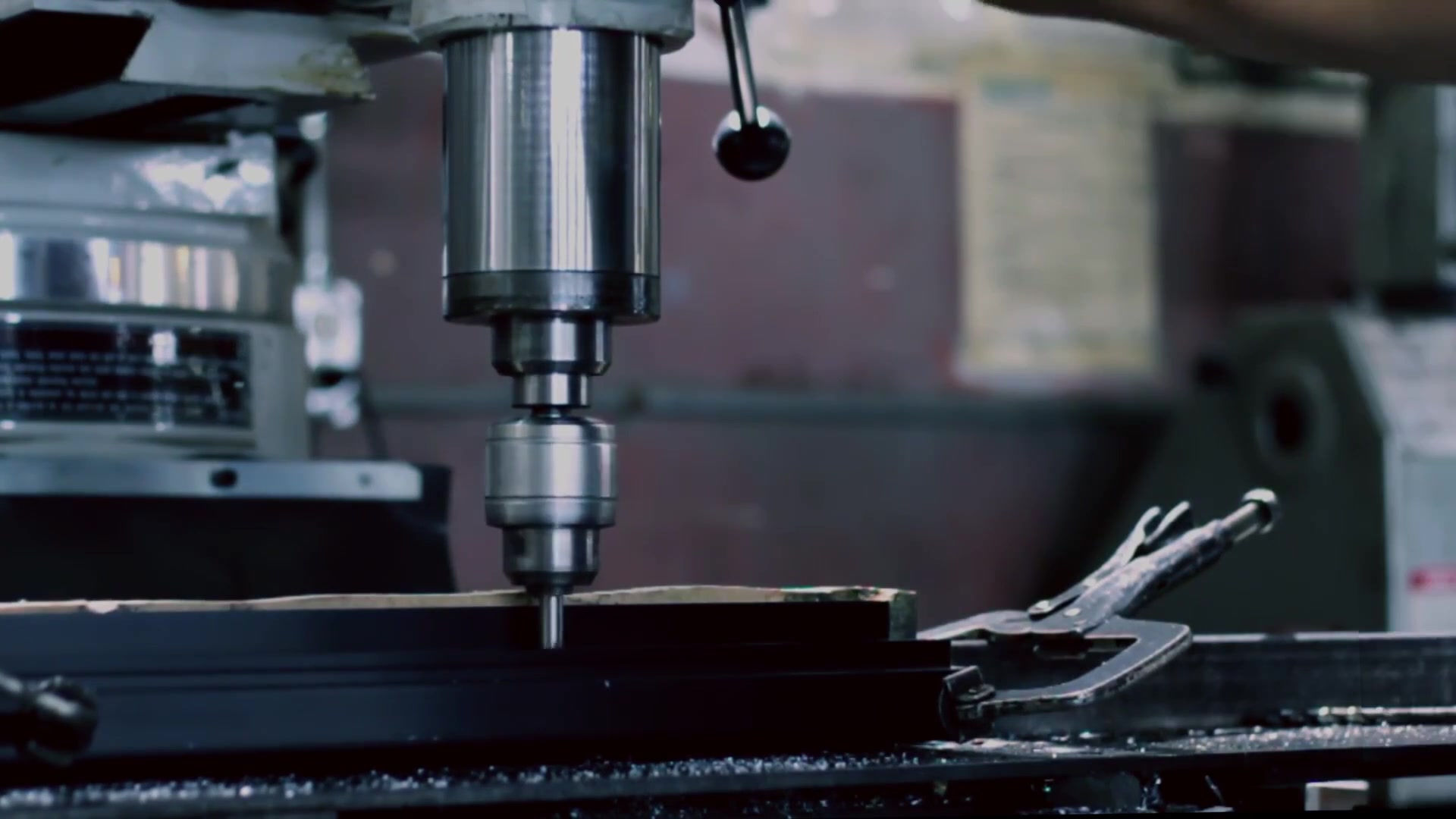
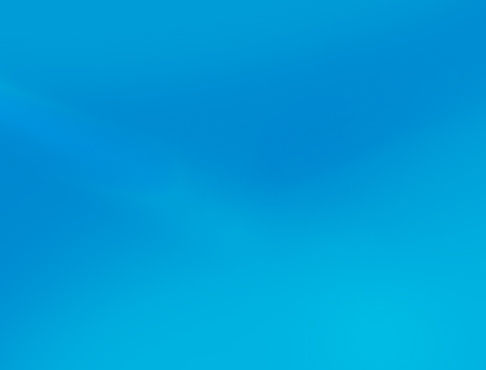
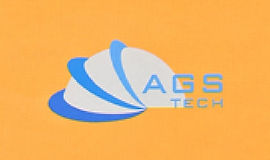
Глобальный производитель на заказ, интегратор, консолидатор, партнер по аутсорсингу широкого спектра продуктов и услуг.
Мы являемся вашим универсальным источником для производства, изготовления, проектирования, консолидации, интеграции, аутсорсинга изготовленных на заказ и готовых продуктов и услуг.
Choose your Language
-
Изготовление на заказ
-
Внутреннее и глобальное контрактное производство
-
Производственный аутсорсинг
-
Внутренние и глобальные закупки
-
Консолидация
-
Инженерная интеграция
-
Инженерные услуги
Среди многих методов СОЕДИНЕНИЯ, которые мы используем в производстве, особое внимание уделяется СВАРКЕ, ПАЙКЕ, ПАЯКЕ, СКЛЕИВАНИЮ и МЕХАНИЧЕСКОЙ СБОРКЕ НА ЗАКАЗ, поскольку эти методы широко используются в таких приложениях, как производство герметичных узлов, производство высокотехнологичных продуктов и специализированное уплотнение. Здесь мы сосредоточимся на более специализированных аспектах этих методов соединения, поскольку они связаны с производством передовых продуктов и узлов.
СВАРКА ПЛАВЕНИЕМ: мы используем тепло для плавления и соединения материалов. Тепло подается электричеством или высокоэнергетическими лучами. Типы сварки плавлением, которые мы применяем: ГАЗОВАЯ СВАРКА КИСЛОРОД, ДУГОВАЯ СВАРКА, СВАРКА ВЫСОКОЭНЕРГЕТИЧЕСКИМ ЛУЧОМ.
СВАРКА В ТВЕРДОМ ТЕЛЕ: Мы соединяем детали без плавления и плавления. Нашими методами сварки твердого тела являются ХОЛОДНАЯ, УЛЬТРАЗВУКОВАЯ, СОПРОТИВНАЯ, ТРЕНИЕМ, ВЗРЫВОМ и ДИФФУЗИОННОЙ СВЯЗКОЙ.
ПАЙКА И ПАЙКА: в них используются присадочные металлы, что дает нам возможность работать при более низких температурах, чем при сварке, что снижает структурные повреждения изделий. Информацию о нашем предприятии для пайки металлов, производящем керамические фитинги, герметики, вакуумные вводы, системы высокого и сверхвысокого вакуума и компоненты управления подачей жидкости можно найти здесь:Брошюра о паяльном заводе
КЛЕЙНОЕ СОЕДИНЕНИЕ: Из-за разнообразия клеев, используемых в промышленности, а также разнообразия областей применения, у нас есть специальная страница для этого. Чтобы перейти на нашу страницу о склеивании, нажмите здесь.
МЕХАНИЧЕСКАЯ СБОРКА НА ЗАКАЗ: Мы используем различные крепежные детали, такие как болты, винты, гайки, заклепки. Наш крепеж не ограничивается стандартными крепежными элементами, имеющимися в наличии. Мы проектируем, разрабатываем и производим специальные крепежные детали из нестандартных материалов, чтобы они могли соответствовать требованиям для специальных применений. Иногда желательна электрическая или тепловая непроводимость, а иногда - проводимость. Для некоторых специальных применений заказчику могут потребоваться специальные крепления, которые невозможно снять без разрушения изделия. Есть бесконечные идеи и приложения. У нас есть все для вас, если нет готовых, мы можем быстро разработать. Чтобы перейти на нашу страницу по механической сборке, нажмите здесь. Давайте рассмотрим наши различные методы соединения более подробно.
КИСЛОРОДНО-ГАЗОВАЯ СВАРКА (OFW): Мы используем горючий газ, смешанный с кислородом, для получения сварочного пламени. Когда мы используем ацетилен в качестве топлива и кислорода, мы называем это кислородно-ацетиленовой газовой сваркой. В процессе горения кислородного газа происходят две химические реакции:
C2H2 + O2 ------» 2CO + H2 + Тепло
2CO + H2 + 1,5 O2 --------» 2 CO2 + H2O + Тепло
Первая реакция диссоциирует ацетилен на монооксид углерода и водород, производя при этом около 33% от общего количества выделяемого тепла. Второй процесс, описанный выше, представляет собой дальнейшее сжигание водорода и монооксида углерода с выделением около 67% общего количества тепла. Температура пламени составляет от 1533 до 3573 Кельвинов. Большое значение имеет процентное содержание кислорода в газовой смеси. Если содержание кислорода больше половины, пламя становится окислителем. Это нежелательно для одних металлов, но желательно для других. Примером, когда желательно окислительное пламя, являются сплавы на основе меди, поскольку оно образует пассивирующий слой на металле. С другой стороны, когда содержание кислорода уменьшается, полное сгорание невозможно, и пламя становится восстановительным (науглероживающим). Температура в восстановительном пламени ниже, поэтому оно подходит для таких процессов, как пайка и пайка твердым припоем. Другие газы также являются потенциальными видами топлива, но они имеют некоторые недостатки по сравнению с ацетиленом. Иногда мы поставляем присадочные металлы в зону сварки в виде присадочных прутков или проволоки. Некоторые из них покрыты флюсом для замедления окисления поверхностей и, таким образом, защиты расплавленного металла. Дополнительным преимуществом флюса является удаление оксидов и других веществ из зоны сварки. Это приводит к более прочному соединению. Разновидностью кислородно-газовой сварки является ГАЗОВАЯ СВАРКА ПОД ДАВЛЕНИЕМ, при которой два компонента нагреваются на границе раздела с помощью кислородно-ацетиленовой газовой горелки, и как только граница раздела начинает плавиться, горелка вынимается и прикладывается осевое усилие для прижатия двух частей друг к другу. пока интерфейс не затвердеет.
ДУГОВАЯ СВАРКА: Мы используем электрическую энергию для создания дуги между наконечником электрода и свариваемыми деталями. Источник питания может быть переменного или постоянного тока, а электроды могут быть расходуемые или нерасходуемые. Теплопередачу при дуговой сварке можно выразить следующим уравнением:
Н/л = ех VI/в
Здесь H — погонная энергия, l — длина сварного шва, V и I — приложенные напряжение и ток, v — скорость сварки, а e — эффективность процесса. Чем выше КПД «е», тем эффективнее используется доступная энергия для плавления материала. Тепловложение также может быть выражено как:
H = ux (объем) = ux A xl
Здесь u — удельная энергия плавления, A — поперечное сечение шва, l — длина шва. Из двух приведенных выше уравнений мы можем получить:
v = ex VI / u A
Разновидностью дуговой сварки является ДУГОВАЯ СВАРКА ЭКРАНИРОВАННЫМ МЕТАЛЛОМ (SMAW), которая составляет около 50% всех промышленных и ремонтных сварочных процессов. ЭЛЕКТРОДУГОВАЯ СВАРКА (ЭЛЕКТРОДУГОВАЯ СВАРКА) выполняется путем прикосновения кончика покрытого электрода к заготовке и быстрого отвода его на расстояние, достаточное для поддержания дуги. Мы также называем этот процесс сваркой стержнем, потому что электроды представляют собой тонкие и длинные стержни. В процессе сварки кончик электрода плавится вместе с его покрытием и основным металлом в непосредственной близости от дуги. В зоне сварного шва затвердевает смесь основного металла, электродного металла и веществ из электродного покрытия. Покрытие электрода раскисляет и обеспечивает защитный газ в зоне сварки, тем самым защищая ее от кислорода окружающей среды. Поэтому этот процесс называется дуговой сваркой защищенным металлом. Мы используем токи от 50 до 300 ампер и уровни мощности, как правило, менее 10 кВт для оптимальной производительности сварки. Также важна полярность постоянного тока (направление тока). Прямая полярность, при которой заготовка является положительной, а электрод - отрицательной, предпочтительна при сварке листового металла из-за ее неглубокого провара, а также для соединений с очень большими зазорами. Когда у нас есть обратная полярность, то есть электрод положительный, а заготовка отрицательный, мы можем добиться более глубокого проплавления сварного шва. На переменном токе, поскольку у нас пульсирующие дуги, мы можем сваривать толстые секции, используя электроды большого диаметра и максимальные токи. Метод сварки SMAW подходит для заготовок толщиной от 3 до 19 мм и даже больше при использовании многопроходной техники. Шлак, образовавшийся поверх сварного шва, необходимо удалить с помощью проволочной щетки, чтобы не было коррозии и разрушения в зоне сварного шва. Это, конечно, увеличивает стоимость дуговой сварки защищенным металлом. Тем не менее SMAW является наиболее популярным методом сварки в промышленности и ремонтных работах.
ДУГОВАЯ СВАРКА ПОД ФЛЮСОМ (SAW): В этом процессе мы защищаем сварочную дугу, используя гранулированные флюсовые материалы, такие как известь, диоксид кремния, фторид кальция, оксид марганца и т. д. Гранулированный флюс подается в зону сварки самотеком через сопло. Флюс, покрывающий расплавленную зону сварки, значительно защищает от искр, дыма, УФ-излучения и т. д. и действует как теплоизолятор, позволяя теплу проникать глубоко в заготовку. Нерасплавленный флюс восстанавливается, обрабатывается и используется повторно. Катушка оголенного металла используется в качестве электрода и подается по трубке к месту сварки. Мы используем токи от 300 до 2000 ампер. Процесс дуговой сварки под флюсом (SAW) ограничен горизонтальными и плоскими положениями и круговыми сварными швами, если во время сварки возможно вращение круглой конструкции (например, труб). Скорость может достигать 5 м/мин. Процесс SAW подходит для толстых листов и позволяет получить высококачественные, прочные, пластичные и однородные сварные швы. Производительность, то есть количество наплавляемого материала в час, в 4-10 раз выше по сравнению с процессом SMAW.
Другой процесс дуговой сварки, а именно ДУГОВАЯ СВАРКА МЕТАЛЛОМ В ГАЗЕ (GMAW) или альтернативно называемая СВАРКА МЕТАЛЛА В ИНЕРТНОМ ГАЗЕ (MIG), основан на защите зоны сварки внешними источниками газов, таких как гелий, аргон, углекислый газ и т. д. В электродном металле могут присутствовать дополнительные раскислители. Расходуемая проволока подается через сопло в зону сварки. Изготовление изделий как из черных, так и из цветных металлов осуществляется с помощью дуговой сварки в среде защитного газа (GMAW). Производительность сварки примерно в 2 раза выше, чем у процесса SMAW. Используется автоматизированное сварочное оборудование. В этом процессе металл переносится одним из трех способов: «Распылительный перенос» включает перенос нескольких сотен маленьких капель металла в секунду от электрода к зоне сварки. С другой стороны, в «Глобулярном переносе» используются газы, богатые двуокисью углерода, и шарики расплавленного металла приводятся в движение электрической дугой. Сварочные токи большие, проплавление шва глубже, скорость сварки выше, чем при струйном переносе. Таким образом, шаровидный перенос лучше подходит для сварки более тяжелых профилей. Наконец, в методе «короткого замыкания» кончик электрода касается расплавленной сварочной ванны, вызывая короткое замыкание, поскольку металл со скоростью более 50 капель в секунду переносится отдельными каплями. Низкие токи и напряжения используются вместе с более тонким проводом. Используемая мощность составляет около 2 кВт, а температура относительно низкая, что делает этот метод пригодным для тонких листов толщиной менее 6 мм.
Другой вариант процесса дуговой сварки с флюсовой проволокой (FCAW) аналогичен дуговой сварке металлическим газом, за исключением того, что электрод представляет собой трубку, заполненную флюсом. Преимущества использования порошковых флюсовых электродов в том, что они дают более стабильную дугу, дают возможность улучшить свойства металла шва, менее хрупкий и гибкий характер его флюса по сравнению со сваркой SMAW, улучшенные контуры сварки. Самозащитные порошковые электроды содержат материалы, защищающие зону сварки от атмосферы. Мы используем около 20 кВт мощности. Как и процесс GMAW, процесс FCAW также дает возможность автоматизировать процессы непрерывной сварки и является экономичным. Различные химические составы металла сварного шва могут быть получены путем добавления различных сплавов в флюсовую сердцевину.
При ЭЛЕКТРОГАЗОВОЙ СВАРКЕ (ЭГС) мы свариваем детали, расположенные кромкой к кромке. Иногда ее еще называют СТЫКОВАЯ СВАРКА. Металл шва помещают в полость сварного шва между двумя соединяемыми деталями. Пространство окружено двумя водоохлаждаемыми плотинами, чтобы предотвратить выливание расплавленного шлака. Плотины поднимаются механическим приводом. Когда заготовку можно вращать, мы можем использовать технику электрогазовой сварки и для кольцевой сварки труб. Электроды подаются через трубопровод, чтобы поддерживать непрерывную дугу. Токи могут быть около 400 ампер или 750 ампер, а уровни мощности около 20 кВт. Инертные газы, исходящие от электрода с флюсовой сердцевиной или внешнего источника, обеспечивают защиту. Мы используем электрогазовую сварку (ЭГС) для таких металлов, как сталь, титан и т. д., толщиной от 12 мм до 75 мм. Метод хорошо подходит для больших конструкций.
Тем не менее, в другом методе, называемом ЭЛЕКТРОШЛАКОВАЯ СВАРКА (ЭШС), дуга зажигается между электродом и нижней частью заготовки, и добавляется флюс. Когда расплавленный шлак достигает кончика электрода, дуга гаснет. Энергия непрерывно подается за счет электрического сопротивления расплавленного шлака. Мы можем сваривать листы толщиной от 50 мм до 900 мм и даже больше. Сила тока составляет около 600 ампер, а напряжение — от 40 до 50 В. Скорость сварки — от 12 до 36 мм/мин. Применение аналогично электрогазовой сварке.
Один из наших процессов с неплавящимся электродом, ГАЗОВАЯ ДУГОВАЯ СВАРКА ВОЛЬФРАМОМ (GTAW), также известная как СВАРКА ВОЛЬФРАМОВЫМ ИНЕРТНЫМ ГАЗОМ (TIG), включает в себя подачу присадочного металла с помощью проволоки. Для плотных соединений иногда мы не используем присадочный металл. В процессе TIG мы не используем флюс, а используем аргон и гелий для защиты. Вольфрам имеет высокую температуру плавления и не расходуется в процессе сварки TIG, поэтому можно поддерживать постоянный ток, а также дуговые промежутки. Уровни мощности составляют от 8 до 20 кВт, а сила тока составляет 200 ампер (постоянный ток) или 500 ампер (переменный ток). Для алюминия и магния мы используем переменный ток для его функции очистки от оксидов. Во избежание загрязнения вольфрамового электрода избегаем его контакта с расплавленными металлами. Дуговая сварка вольфрамовым электродом в среде защитного газа (GTAW) особенно полезна для сварки тонких металлов. Сварные швы GTAW имеют очень высокое качество с хорошей обработкой поверхности.
Из-за более высокой стоимости газообразного водорода менее часто используемым методом является АТОМНО-ВОДОРОДНАЯ СВАРКА (AHW), при которой мы генерируем дугу между двумя вольфрамовыми электродами в защитной атмосфере потока газообразного водорода. AHW также является процессом сварки неплавящимся электродом. Двухатомный газообразный водород H2 распадается на атомарную форму вблизи сварочной дуги, где температура превышает 6273 Кельвина. При разрушении он поглощает большое количество тепла от дуги. Когда атомы водорода ударяются о зону сварки, которая представляет собой относительно холодную поверхность, они рекомбинируют в двухатомную форму и выделяют аккумулированное тепло. Энергию можно варьировать, изменяя расстояние между заготовкой и дугой.
В другом процессе с неплавящимся электродом, ПЛАЗМЕННО-ДУГОВОЙ СВАРКЕ (PAW), у нас есть концентрированная плазменная дуга, направленная к зоне сварки. Температура достигает 33 273 Кельвина в PAW. Почти равное количество электронов и ионов составляет плазменный газ. Слаботочная дежурная дуга инициирует плазму, которая находится между вольфрамовым электродом и отверстием. Рабочий ток обычно составляет около 100 ампер. Можно подавать присадочный металл. При плазменной дуговой сварке экранирование осуществляется внешним защитным кольцом и использованием таких газов, как аргон и гелий. При плазменной дуговой сварке дуга может быть между электродом и заготовкой или между электродом и соплом. Этот метод сварки имеет преимущества перед другими методами: более высокая концентрация энергии, более глубокая и узкая сварка, лучшая стабильность дуги, более высокая скорость сварки до 1 м / мин, меньшая тепловая деформация. Обычно мы используем плазменно-дуговую сварку для толщины менее 6 мм, а иногда и до 20 мм для алюминия и титана.
СВАРКА ВЫСОКОЭНЕРГЕТИЧЕСКИМ ЛУЧОМ: Другой тип метода сварки плавлением с электронно-лучевой сваркой (EBW) и лазерной сваркой (LBW) в двух вариантах. Эти методы имеют особое значение для нашей работы по производству высокотехнологичной продукции. При электронно-лучевой сварке электроны с высокой скоростью ударяются о заготовку, и их кинетическая энергия преобразуется в тепло. Узкий пучок электронов легко перемещается в вакуумной камере. Обычно мы используем высокий вакуум при электронно-лучевой сварке. Можно сваривать листы толщиной до 150 мм. Не требуются защитные газы, флюс или наполнитель. Электронно-лучевые пушки имеют мощность 100 кВт. Возможны глубокие и узкие сварные швы с большим удлинением до 30 и небольшими зонами термического влияния. Скорость сварки может достигать 12 м/мин. При лазерной сварке в качестве источника тепла используются мощные лазеры. Лазерные лучи размером всего 10 микрон с высокой плотностью обеспечивают глубокое проникновение в заготовку. При лазерной сварке возможно соотношение глубины к ширине до 10. Мы используем как импульсные, так и непрерывные лазеры, причем первые применяются для тонких материалов, а вторые — в основном для толстых заготовок до 25 мм. Уровни мощности до 100 кВт. Сварка лазерным лучом плохо подходит для оптически сильно отражающих материалов. Газы также могут использоваться в процессе сварки. Метод лазерной сварки хорошо подходит для автоматизации и крупносерийного производства и может обеспечивать скорость сварки от 2,5 м/мин до 80 м/мин. Одним из основных преимуществ этого метода сварки является доступ к областям, где другие методы не могут быть использованы. Лазерные лучи могут легко добраться до таких труднодоступных мест. Вакуум, как при электронно-лучевой сварке, не требуется. Сварка с хорошим качеством и прочностью, низкой усадкой, малым искажением, низкой пористостью может быть получена с помощью лазерной сварки. Лазерными лучами можно легко управлять и формировать их с помощью оптоволоконных кабелей. Таким образом, этот метод хорошо подходит для сварки прецизионных герметичных узлов, электронных блоков и т. д.
Давайте посмотрим на наши методы СВАРКИ ТВЕРДОГО ТЕЛА. ХОЛОДНАЯ СВАРКА (CW) — это процесс, при котором к соединяемым деталям прикладывается давление вместо тепла с помощью штампов или валков. При холодной сварке хотя бы одна из сопрягаемых деталей должна быть пластичной. Наилучшие результаты получаются при использовании двух одинаковых материалов. Если два металла, которые должны быть соединены холодной сваркой, неодинаковы, мы можем получить слабые и хрупкие соединения. Метод холодной сварки хорошо подходит для мягких, пластичных и небольших деталей, таких как электрические соединения, термочувствительные края контейнеров, биметаллические пластины для термостатов и т. д. Одним из вариантов холодной сварки является валковая сварка (или валковая сварка), при которой давление прикладывается через пару валков. Иногда мы выполняем сварку роликами при повышенных температурах для лучшей межфазной прочности.
Другой процесс сварки в твердом состоянии, который мы используем, — это УЛЬТРАЗВУКОВАЯ СВАРКА (USW), при которой заготовки подвергаются статическому нормальному усилию и осциллирующим напряжениям сдвига. Осциллирующие касательные напряжения прикладывают через наконечник преобразователя. Ультразвуковая сварка использует колебания с частотой от 10 до 75 кГц. В некоторых случаях, таких как шовная сварка, мы используем вращающийся сварочный диск в качестве наконечника. Касательные напряжения, приложенные к заготовкам, вызывают небольшие пластические деформации, разрушают оксидные слои, загрязнения и приводят к твердофазному соединению. Температуры, связанные с ультразвуковой сваркой, намного ниже температуры плавления металлов, и плавления не происходит. Мы часто используем процесс ультразвуковой сварки (УЗС) для неметаллических материалов, таких как пластмассы. Однако в термопластах температуры достигают точки плавления.
Другой популярный метод, СВАРКА ТРЕНИЕМ (FRW), тепло генерируется за счет трения на границе раздела соединяемых деталей. При сварке трением мы удерживаем одну из заготовок неподвижной, в то время как другая заготовка удерживается в приспособлении и вращается с постоянной скоростью. Затем заготовки приводятся в контакт под действием осевой силы. Скорость вращения поверхности при сварке трением в некоторых случаях может достигать 900 м/мин. После достаточного межфазного контакта вращающаяся заготовка резко останавливается, а осевое усилие увеличивается. Зона сварки обычно представляет собой узкую область. Техника сварки трением может использоваться для соединения сплошных и трубчатых деталей из различных материалов. Некоторый заусенец может образовываться на границе раздела в FRW, но этот заусенец можно удалить вторичной обработкой или шлифовкой. Существуют вариации процесса сварки трением. Например, в «инерционной сварке трением» используется маховик, кинетическая энергия вращения которого используется для сварки деталей. Сварка завершается, когда маховик останавливается. Вращающаяся масса может варьироваться и, следовательно, кинетическая энергия вращения. Другим вариантом является «линейная сварка трением», при которой линейное возвратно-поступательное движение создается по крайней мере для одного из соединяемых компонентов. При линейной сварке трением детали не обязательно должны быть круглыми, они могут быть прямоугольными, квадратными или другой формы. Частоты могут быть в десятках Гц, амплитуды в миллиметровом диапазоне и давление в десятках или сотнях МПа. Наконец, «сварка трением с перемешиванием» несколько отличается от двух других, описанных выше. Если при инерционной сварке трением и линейной сварке трением нагрев поверхностей раздела достигается за счет трения путем трения двух контактирующих поверхностей, то при сварке трением с перемешиванием третье тело трется о две соединяемые поверхности. Вращающийся инструмент диаметром 5-6 мм приводится в контакт с соединением. Температура может повышаться до значений от 503 до 533 Кельвинов. Происходит нагрев, перемешивание и перемешивание материала в стыке. Мы используем сварку трением с перемешиванием для различных материалов, включая алюминий, пластмассы и композиты. Сварные швы равномерные, качество высокое, поры минимальны. При сварке трением с перемешиванием не образуются пары или брызги, и процесс хорошо автоматизирован.
СОПРОТИВНАЯ СВАРКА (RW): Тепло, необходимое для сварки, производится за счет электрического сопротивления между двумя соединяемыми деталями. При контактной сварке не используются флюс, защитные газы или расходуемые электроды. Джоулев нагрев происходит при сварке сопротивлением и может быть выражен как:
H = (Квадрат I) x R xtx K
H — выделяемое тепло в джоулях (ватт-секундах), I — ток в амперах, R — сопротивление в омах, t — время в секундах, через которое протекает ток. Коэффициент K меньше 1 и представляет долю энергии, которая не теряется на излучение и проводимость. Токи в процессах контактной сварки могут достигать уровней до 100 000 А, но напряжения обычно составляют от 0,5 до 10 вольт. Электроды обычно изготавливаются из медных сплавов. С помощью контактной сварки можно соединять как сходные, так и разнородные материалы. Существует несколько вариантов этого процесса: «Точечная сварка сопротивлением» включает два противоположных круглых электрода, контактирующих с поверхностями соединения внахлестку двух листов. Давление прикладывается до тех пор, пока не отключится ток. Диаметр сварного шва обычно не превышает 10 мм. Точечная сварка сопротивлением оставляет слегка обесцвеченные вмятины в точках сварки. Точечная сварка является наиболее популярным методом контактной сварки. Различные формы электродов используются при точечной сварке, чтобы добраться до труднодоступных мест. Наше оборудование для точечной сварки управляется ЧПУ и имеет несколько электродов, которые можно использовать одновременно. Другой вариант «сварки контактным швом» выполняется с помощью колесных или роликовых электродов, которые производят непрерывную точечную сварку всякий раз, когда ток достигает достаточно высокого уровня в цикле питания переменного тока. Соединения, полученные контактной шовной сваркой, герметичны для жидкостей и газов. Скорость сварки около 1,5 м/мин является нормальной для тонких листов. Можно применять прерывистые токи, чтобы точечная сварка производилась через желаемые интервалы вдоль шва. При «сварке контактным выступом» мы выдавливаем один или несколько выступов (ямочек) на одной из поверхностей свариваемой детали. Эти выступы могут быть круглыми или овальными. В этих выпуклых местах, которые соприкасаются с сопрягаемой деталью, достигаются высокие локальные температуры. Электроды оказывают давление, чтобы сжать эти выступы. Электроды для контактной рельефной сварки имеют плоские концы и изготовлены из медных сплавов с водяным охлаждением. Преимуществом контактной рельефной сварки является наша способность выполнять несколько сварных швов за один проход, а значит, увеличенный срок службы электрода, возможность сваривать листы различной толщины, возможность приваривать гайки и болты к листам. Недостатком контактной рельефной сварки являются дополнительные затраты на тиснение углублений. Еще один метод, при «сварке оплавлением», тепло генерируется дугой на концах двух заготовок, когда они начинают соприкасаться. В качестве альтернативы этому методу можно также рассматривать дуговую сварку. Температура на границе раздела повышается, и материал размягчается. Прикладывается осевое усилие, и в размягченной области формируется сварной шов. После завершения сварки оплавлением соединение можно обработать для улучшения внешнего вида. Качество шва, полученного при сварке оплавлением, хорошее. Уровни мощности от 10 до 1500 кВт. Сварка оплавлением подходит для соединения встык одинаковых или разнородных металлов диаметром до 75 мм и листов толщиной от 0,2 мм до 25 мм. «Дуговая сварка стержнем» очень похожа на сварку оплавлением. Шпилька, такая как болт или резьбовой стержень, служит одним электродом при соединении с заготовкой, такой как пластина. Для концентрации выделяющегося тепла, предотвращения окисления и удержания расплавленного металла в зоне сварки вокруг стыка размещается одноразовое керамическое кольцо. Наконец, «ударная сварка», еще один процесс сварки сопротивлением, использует конденсатор для подачи электроэнергии. При ударной сварке мощность высвобождается в течение миллисекунд, что очень быстро приводит к сильному локализованному нагреву в месте соединения. Мы широко используем ударную сварку в электронной промышленности, где необходимо избегать нагрева чувствительных электронных компонентов вблизи места соединения.
Техника, называемая СВАРКА ВЗРЫВОМ, заключается в детонации слоя взрывчатого вещества, который наносится на одну из соединяемых деталей. Очень высокое давление, оказываемое на заготовку, создает турбулентную и волнистую поверхность, и происходит механическое зацепление. Прочность соединения при сварке взрывом очень высока. Сварка взрывом является хорошим методом плакирования листов разнородными металлами. После плакирования пластины могут быть прокатаны в более тонкие секции. Иногда мы используем сварку взрывом для расширения труб, чтобы они плотно прилегали к пластине.
Наш последний метод в области соединения твердого тела — это ДИФФУЗИОННАЯ СВЯЗКА или ДИФФУЗИОННАЯ СВАРКА (DFW), в которой хорошее соединение достигается в основном за счет диффузии атомов через поверхность раздела. Некоторая пластическая деформация на границе раздела также способствует сварке. Используемые температуры составляют около 0,5 Tm, где Tm — температура плавления металла. Прочность соединения при диффузионной сварке зависит от давления, температуры, времени контакта и чистоты контактирующих поверхностей. Иногда мы используем присадочные металлы на границе раздела. Для диффузионной сварки необходимы тепло и давление, которые обеспечиваются электрическим сопротивлением, печью и мертвыми грузами, прессом или другим способом. Одинаковые и разнородные металлы можно соединять диффузионной сваркой. Процесс относительно медленный из-за времени, необходимого для миграции атомов. DFW поддается автоматизации и широко используется при изготовлении сложных деталей для аэрокосмической, электронной, медицинской промышленности. Производимая продукция включает ортопедические имплантаты, датчики, элементы аэрокосмической конструкции. Диффузионное соединение можно комбинировать с СУПЕРПЛАСТИКОВЫМ ФОРМОВАНИЕМ для изготовления сложных конструкций из листового металла. Выбранные места на листах сначала подвергаются диффузионному соединению, а затем несвязанные области расширяются в форму с помощью давления воздуха. С использованием этой комбинации методов изготавливаются аэрокосмические конструкции с высоким отношением жесткости к весу. Комбинированный процесс диффузионной сварки и сверхпластического формования уменьшает количество необходимых деталей за счет устранения необходимости в крепежных элементах, что позволяет получать высокоточные детали с низким напряжением, экономично и с короткими сроками изготовления.
ПАЙКА: Методы пайки и пайки требуют более низких температур, чем те, которые требуются для сварки. Однако температура пайки выше, чем температура пайки. При пайке присадочный металл помещают между соединяемыми поверхностями и температуру повышают до температуры плавления присадочного материала выше 723 К, но ниже температуры плавления заготовок. Расплавленный металл заполняет плотно прилегающее пространство между заготовками. Охлаждение и последующее затвердевание металла наполнителя приводит к получению прочных соединений. При сварке пайкой присадочный металл наносится в месте соединения. При сварке твердым припоем используется значительно больше присадочного металла, чем при пайке твердым припоем. Кислородно-ацетиленовая горелка с окислительным пламенем используется для нанесения присадочного металла при сварке твердым припоем. Благодаря более низким температурам при пайке меньше проблем в зонах термического влияния, таких как коробление и остаточные напряжения. Чем меньше зазор при пайке, тем выше прочность соединения на сдвиг. Однако максимальная прочность на растяжение достигается при оптимальном зазоре (пиковое значение). Ниже и выше этого оптимального значения предел прочности при пайке снижается. Типичные зазоры при пайке могут составлять от 0,025 до 0,2 мм. Мы используем различные материалы для пайки различной формы, такие как выступы, порошок, кольца, проволока, полоса и т. д. и может изготовить их специально для вашего дизайна или геометрии продукта. Мы также определяем содержание припоев в соответствии с вашими основными материалами и областью применения. Мы часто используем флюсы при пайке для удаления нежелательных оксидных слоев и предотвращения окисления. Во избежание последующей коррозии флюсы обычно удаляют после операции соединения. AGS-TECH Inc. использует различные методы пайки, в том числе:
- Факельная пайка
- Пайка в печи
- Индукционная пайка
- Пайка сопротивлением
- Пайка погружением
- Инфракрасная пайка
- Диффузионная пайка
- Луч высокой энергии
Наши наиболее распространенные образцы паяных соединений изготовлены из разнородных металлов с хорошей прочностью, таких как твердосплавные сверла, вставки, оптоэлектронные герметичные пакеты, уплотнения.
ПАЯЯ: Это один из наших наиболее часто используемых методов, при котором припой (присадочный металл) заполняет соединение, как при пайке между плотно прилегающими компонентами. Наши припои имеют температуру плавления ниже 723 кельвинов. Мы используем как ручную, так и автоматизированную пайку в производственных операциях. По сравнению с пайкой температура пайки ниже. Пайка не очень подходит для высокотемпературных или высокопрочных приложений. Мы используем бессвинцовые припои, а также сплавы олово-свинец, олово-цинк, свинец-серебро, кадмий-серебро, цинк-алюминий и другие для пайки. В качестве флюса при пайке используются как неагрессивные смолы, так и неорганические кислоты и соли. Мы используем специальные флюсы для пайки металлов с низкой паяемостью. В тех случаях, когда нам приходится паять керамические материалы, стекло или графит, мы сначала покрываем детали подходящим металлом для повышения способности к пайке. Наши популярные методы пайки:
-пайка оплавлением или пастой
- Волновая пайка
-печь для пайки
-Факел Пайка
-Индукционная пайка
-Железная пайка
-Сопротивление пайки
- Пайка погружением
-Ультразвуковая пайка
-Инфракрасная пайка
Ультразвуковая пайка предлагает нам уникальное преимущество, заключающееся в том, что необходимость в флюсах отпадает благодаря эффекту ультразвуковой кавитации, удаляющему оксидные пленки с соединяемых поверхностей. Пайка оплавлением и пайка волной припоя — наши выдающиеся промышленные технологии для крупносерийного производства электроники, поэтому их стоит объяснить более подробно. При пайке оплавлением мы используем полутвердые пасты, содержащие частицы припоя. Паста наносится на сустав с помощью просеивания или нанесения по трафарету. В печатных платах (PCB) мы часто используем этот метод. Когда электрические компоненты размещаются на этих контактных площадках из пасты, поверхностное натяжение поддерживает выравнивание корпусов для поверхностного монтажа. После размещения компонентов мы нагреваем сборку в печи, чтобы произошла пайка оплавлением. Во время этого процесса растворители в пасте испаряются, флюс в пасте активируется, компоненты предварительно нагреваются, частицы припоя расплавляются и смачивают соединение, и, наконец, сборка печатной платы медленно охлаждается. Наш второй популярный метод крупносерийного производства печатных плат, а именно пайка волной припоя, основан на том факте, что расплавленные припои смачивают металлические поверхности и образуют хорошие соединения только при предварительном нагреве металла. Стоячая ламинарная волна расплавленного припоя сначала создается насосом, а предварительно нагретые и предварительно профлюсованные печатные платы перемещаются по волне. Припой смачивает только открытые металлические поверхности, но не смачивает полимерные корпуса интегральных схем и печатные платы с полимерным покрытием. Струя горячей воды с высокой скоростью выдувает излишки припоя из соединения и предотвращает образование перемычек между соседними выводами. При пайке волной припоя корпусов для поверхностного монтажа мы сначала приклеиваем их к печатной плате перед пайкой. Снова используется экранирование и трафарет, но на этот раз для эпоксидной смолы. После того, как компоненты размещены на своих местах, эпоксидная смола затвердевает, платы переворачиваются и выполняется пайка волной припоя.