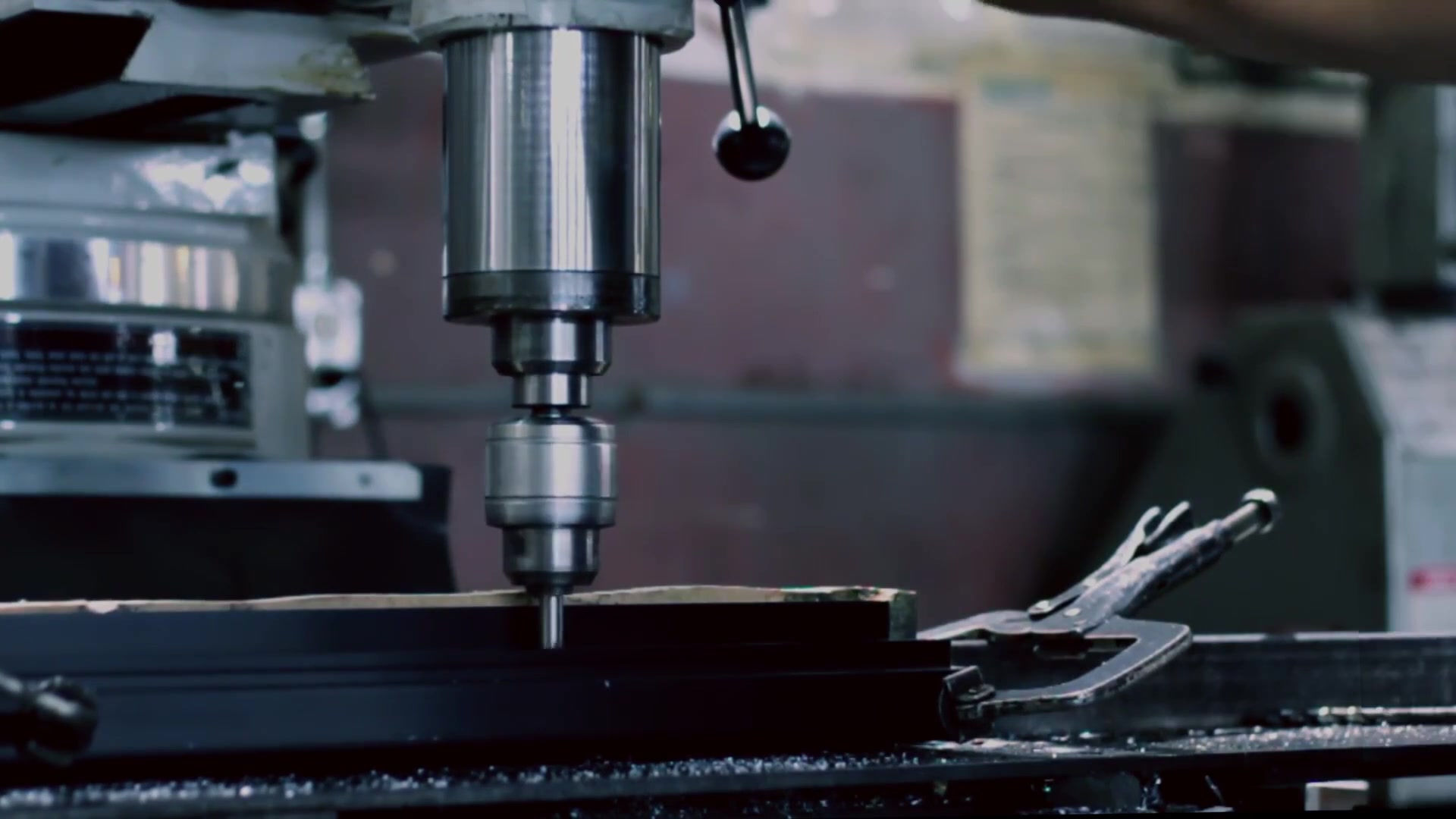
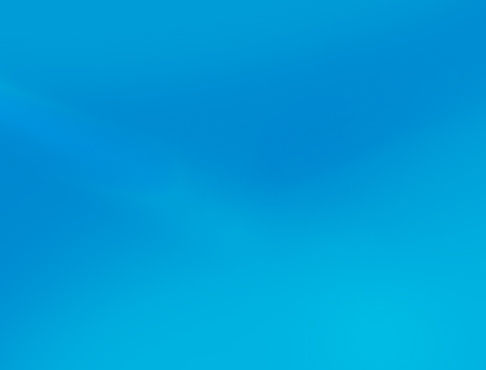
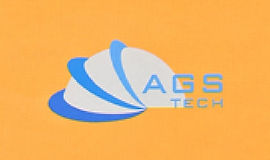
Wereldwijd op maat gemaakte fabrikant, integrator, consolidator, outsourcingpartner voor een breed scala aan producten en diensten.
Wij zijn uw one-stop-bron voor productie, fabricage, engineering, consolidatie, integratie, outsourcing van op maat gemaakte en off-shelf producten en diensten.
Choose your Language
-
Aangepaste productie
-
Binnenlandse en wereldwijde contractproductie
-
Uitbesteding van productie
-
Binnenlandse en wereldwijde inkoop
-
Consolidatie
-
Engineering-integratie
-
Ingenieursdiensten
Van de vele VERBINDINGStechnieken die we toepassen in de productie, wordt speciale nadruk gelegd op LASSEN, SOLDEREN, SOLDEREN, LIJMEN EN MECHANISCHE MONTAGE OP MAAT, omdat deze technieken veel worden gebruikt in toepassingen zoals de fabricage van hermetische assemblages, hightech productproductie en gespecialiseerde afdichting. Hier zullen we ons concentreren op de meer gespecialiseerde aspecten van deze verbindingstechnieken, aangezien deze verband houden met de productie van geavanceerde producten en assemblages.
FUSIELASSEN: We gebruiken warmte om materialen te smelten en samen te voegen. Warmte wordt geleverd door elektriciteit of hoogenergetische balken. De soorten smeltlassen die we toepassen zijn OXYFUEL GAS LASING, ARC WELDING, HIGH-ENERGY-BEAM LASING.
SOLID-STATE LASSEN: We verbinden onderdelen zonder te smelten en versmelten. Onze solid-state lasmethoden zijn KOUD, ULTRASOON, WEERSTAND, WRIJVING, EXPLOSIELASSEN en DIFFUSIEBONDING.
SOLDEREN & SOLDEREN: Ze gebruiken toevoegmetalen en geven ons het voordeel om bij lagere temperaturen te werken dan bij lassen, dus minder structurele schade aan producten. Informatie over onze soldeerfaciliteit die keramiek-op-metaal fittingen, hermetische afdichting, vacuümdoorvoeren, hoog- en ultrahoog vacuüm en vloeistofregelcomponenten produceert vindt u hier:Brochure soldeerfabriek
LIJMVERBINDING: Vanwege de diversiteit aan lijmen die in de industrie worden gebruikt en ook de diversiteit aan toepassingen, hebben we hiervoor een speciale pagina. Om naar onze pagina over lijmen te gaan, klik hier.
AANGEPASTE MECHANISCHE MONTAGE: We gebruiken een verscheidenheid aan bevestigingsmiddelen zoals bouten, schroeven, moeren, klinknagels. Onze bevestigingsmiddelen zijn niet beperkt tot standaard kant-en-klare bevestigingsmiddelen. We ontwerpen, ontwikkelen en produceren speciale bevestigingsmiddelen die zijn gemaakt van niet-standaard materialen, zodat ze kunnen voldoen aan de vereisten voor speciale toepassingen. Soms is elektrische of warmte niet-geleidbaarheid gewenst, terwijl soms geleidbaarheid. Voor sommige speciale toepassingen kan een klant speciale bevestigingsmiddelen willen die niet kunnen worden verwijderd zonder het product te vernietigen. Er zijn eindeloos veel ideeën en toepassingen. We hebben het allemaal voor je, als het niet standaard is, kunnen we het snel ontwikkelen. Om naar onze pagina over mechanische montage te gaan, klik hier. Laten we onze verschillende verbindingstechnieken nader bekijken.
OXYFUEL GAS WELDING (OFW): We gebruiken een brandstofgas gemengd met zuurstof om de lasvlam te produceren. Wanneer we acetyleen als brandstof en zuurstof gebruiken, noemen we het oxyacetyleengaslassen. Er vinden twee chemische reacties plaats in het oxyfuel-gasverbrandingsproces:
C2H2 + O2 ------» 2CO + H2 + Warmte
2CO + H2 + 1,5 O2--------» 2 CO2 + H2O + Warmte
De eerste reactie dissocieert het acetyleen in koolmonoxide en waterstof terwijl ongeveer 33% van de totale gegenereerde warmte wordt geproduceerd. Het tweede proces hierboven vertegenwoordigt verdere verbranding van waterstof en koolmonoxide terwijl ongeveer 67% van de totale warmte wordt geproduceerd. Temperaturen in de vlam liggen tussen 1533 en 3573 Kelvin. Het zuurstofpercentage in het gasmengsel is belangrijk. Als het zuurstofgehalte meer dan de helft is, wordt de vlam een oxidatiemiddel. Dit is ongewenst voor sommige metalen, maar wenselijk voor andere. Een voorbeeld wanneer oxiderende vlam wenselijk is, zijn legeringen op koperbasis, omdat deze een passiveringslaag over het metaal vormen. Aan de andere kant, wanneer het zuurstofgehalte wordt verlaagd, is volledige verbranding niet mogelijk en wordt de vlam een reducerende (carboniserende) vlam. De temperaturen in een reducerende vlam zijn lager en daardoor geschikt voor processen als solderen en hardsolderen. Andere gassen zijn ook potentiële brandstoffen, maar ze hebben enkele nadelen ten opzichte van acetyleen. Af en toe leveren wij toevoegmetalen aan de laszone in de vorm van toevoegstaven of draad. Sommige zijn gecoat met vloeimiddel om oxidatie van oppervlakken te vertragen en zo het gesmolten metaal te beschermen. Een bijkomend voordeel van de flux is de verwijdering van oxiden en andere stoffen uit de laszone. Dit leidt tot een sterkere binding. Een variant van het autogeengaslassen is het DRUKGASLASSEN, waarbij de twee componenten bij hun interface worden verwarmd met behulp van een zuurstofacetyleengasbrander en zodra de interface begint te smelten, wordt de toorts teruggetrokken en wordt een axiale kracht uitgeoefend om de twee delen samen te drukken totdat de interface is gestold.
BOOGLASSEN: We gebruiken elektrische energie om een boog te produceren tussen de elektrodepunt en de te lassen onderdelen. De voeding kan AC of DC zijn, terwijl de elektroden verbruikbaar of niet-verbruikbaar zijn. Warmteoverdracht bij booglassen kan worden uitgedrukt door de volgende vergelijking:
H / l = ex VI / v
Hier is H de warmte-invoer, l is de laslengte, V en I zijn de aangelegde spanning en stroom, v is de lassnelheid en e is de procesefficiëntie. Hoe hoger het rendement "e", hoe voordeliger de beschikbare energie wordt gebruikt om het materiaal te smelten. De warmte-inbreng kan ook worden uitgedrukt als:
H = ux (Volume) = ux A xl
Hierin is u de specifieke smeltenergie, A de doorsnede van de las en l de laslengte. Uit de twee bovenstaande vergelijkingen kunnen we verkrijgen:
v = ex VI / u A
Een variatie op booglassen is het SHIELDED METAL ARC WELDING (SMAW), dat ongeveer 50% van alle industriële en onderhoudslasprocessen uitmaakt. ELEKTRISCH BOOGLASSEN (STOKLASSEN) wordt uitgevoerd door de punt van een gecoate elektrode tegen het werkstuk aan te raken en deze snel terug te trekken tot een afstand die voldoende is om de boog te behouden. We noemen dit proces ook wel staaflassen omdat de elektroden dun zijn en lange staafjes. Tijdens het lasproces smelt de punt van de elektrode samen met de coating en het basismetaal in de buurt van de boog. Een mengsel van het basismetaal, elektrodemetaal en stoffen van de elektrodecoating stolt in het lasgebied. De coating van de elektrode deoxideert en zorgt voor een beschermend gas in het lasgebied, waardoor het wordt beschermd tegen de zuurstof in de omgeving. Daarom wordt het proces afgeschermd metaalbooglassen genoemd. We gebruiken stromen tussen 50 en 300 ampère en vermogensniveaus over het algemeen minder dan 10 kW voor optimale lasprestaties. Ook van belang is de polariteit van de gelijkstroom (stroomrichting). Rechte polariteit waarbij het werkstuk positief is en de elektrode negatief, heeft de voorkeur bij het lassen van plaatmetalen vanwege de ondiepe penetratie en ook voor verbindingen met zeer brede openingen. Wanneer we omgekeerde polariteit hebben, dwz de elektrode is positief en het werkstuk negatief, kunnen we diepere laspenetraties bereiken. Met wisselstroom, omdat we pulserende bogen hebben, kunnen we dikke secties lassen met behulp van elektroden met een grote diameter en maximale stromen. De SMAW-lasmethode is geschikt voor werkstukdiktes van 3 tot 19 mm en zelfs meer met behulp van meerlaagse technieken. De slak die bovenop de las wordt gevormd, moet met een staalborstel worden verwijderd, zodat er geen corrosie en breuk optreedt bij het lasgebied. Dit draagt natuurlijk bij aan de kosten van booglassen met afgeschermd metaal. Toch is de SMAW de meest populaire lastechniek in de industrie en reparatiewerkzaamheden.
ONDERDOMPELBOOGLASSEN (ZAAG): In dit proces schermen we de lasboog af met behulp van granulaire fluxmaterialen zoals kalk, silica, calciumfloride, mangaanoxide ... enz. De granulaire flux wordt in de laszone toegevoerd door zwaartekracht door een mondstuk. De flux die de gesmolten laszone bedekt, beschermt aanzienlijk tegen vonken, dampen, UV-straling ... enz. en werkt als een thermische isolator, waardoor warmte diep in het werkstuk kan doordringen. De niet-gefuseerde flux wordt teruggewonnen, behandeld en hergebruikt. Een kaal stuk wordt als elektrode gebruikt en door een buis naar het lasgebied gevoerd. We gebruiken stromen tussen 300 en 2000 Ampère. Het proces van ondergedompeld booglassen (SAW) is beperkt tot horizontale en vlakke posities en cirkelvormige lassen als rotatie van de cirkelvormige structuur (zoals buizen) tijdens het lassen mogelijk is. Snelheden kunnen oplopen tot 5 m/min. Het SAW-proces is geschikt voor dikke platen en resulteert in hoogwaardige, taaie, ductiele en uniforme lassen. De productiviteit, dat wil zeggen de hoeveelheid lasmateriaal die per uur wordt afgezet, is 4 tot 10 keer de hoeveelheid in vergelijking met het SMAW-proces.
Een ander booglasproces, namelijk het GAS METAL ARC WELDING (GMAW) of ook wel METAL INERT GAS WELDING (MIG) genoemd, is gebaseerd op het lasgebied dat wordt afgeschermd door externe bronnen van gassen zoals helium, argon, kooldioxide, enz. Er kunnen extra desoxidatiemiddelen in het elektrodemetaal aanwezig zijn. Verbruiksdraad wordt door een mondstuk in de laszone gevoerd. Fabricage van zowel ferro- als non-ferrometalen wordt uitgevoerd met behulp van gasmetaalbooglassen (GMAW). De lasproductiviteit is ongeveer 2 keer die van het SMAW-proces. Er wordt gebruik gemaakt van geautomatiseerde lasapparatuur. Metaal wordt in dit proces op drie manieren overgebracht: "Spray Transfer" omvat de overdracht van enkele honderden kleine metaaldruppels per seconde van de elektrode naar het lasgebied. In "Globular Transfer" daarentegen worden koolstofdioxiderijke gassen gebruikt en worden bolletjes gesmolten metaal voortgestuwd door de elektrische boog. De lasstromen zijn hoog en de laspenetratie dieper, de lassnelheid is hoger dan bij sproeioverdracht. De bolvormige overdracht is dus beter voor het lassen van zwaardere secties. Ten slotte, in de "kortsluiting"-methode, raakt de elektrodepunt het gesmolten smeltbad, waardoor het wordt kortgesloten als metaal met snelheden van meer dan 50 druppeltjes/seconde wordt overgebracht in afzonderlijke druppeltjes. Lage stromen en spanningen worden gebruikt in combinatie met dunnere draad. De gebruikte vermogens zijn ongeveer 2 kW en de temperaturen zijn relatief laag, waardoor deze methode geschikt is voor dunne platen met een dikte van minder dan 6 mm.
Een andere variant van het FLUX-CORED ARC WELDING (FCAW)-proces is vergelijkbaar met gasmetaalbooglassen, behalve dat de elektrode een buis is die gevuld is met flux. De voordelen van het gebruik van gevulde fluxelektroden zijn dat ze stabielere bogen produceren, ons de mogelijkheid bieden om de eigenschappen van lasmetalen te verbeteren, minder bros en flexibel karakter van de flux in vergelijking met SMAW-lassen, verbeterde lascontouren. Zelfbeschermde elektroden met kern bevatten materialen die de laszone afschermen tegen de atmosfeer. We gebruiken ongeveer 20 kW vermogen. Net als het GMAW-proces biedt het FCAW-proces ook de mogelijkheid om processen voor continu lassen te automatiseren en is het economisch. Door verschillende legeringen aan de fluxkern toe te voegen, kunnen verschillende lasmetaalchemie worden ontwikkeld.
Bij ELECTROGAS WELDING (EGW) lassen we de stukken rand aan rand. Het wordt ook wel BUTT WELDING genoemd. Lasmetaal wordt in een lasholte geplaatst tussen twee te verbinden stukken. De ruimte wordt omsloten door twee watergekoelde dammen om te voorkomen dat de gesmolten slak naar buiten stroomt. De dammen worden omhoog bewogen door mechanische aandrijvingen. Wanneer het werkstuk kan worden gedraaid, kunnen we de elektrogaslastechniek ook gebruiken voor het omtrekslassen van buizen. Elektroden worden door een leiding gevoerd om een continue boog te behouden. Stroomsterktes kunnen rond de 400 ampère of 750 ampère zijn en de vermogensniveaus rond de 20 kW. Inerte gassen afkomstig van ofwel een gevulde elektrode of een externe bron zorgen voor afscherming. We gebruiken het elektrogas lassen (EGW) voor metalen zoals staal, titanium….etc met diktes van 12 mm tot 75 mm. De techniek is geschikt voor grote constructies.
Maar in een andere techniek genaamd ELEKTROSLAG WELDING (ESW) wordt de boog ontstoken tussen de elektrode en de onderkant van het werkstuk en wordt flux toegevoegd. Wanneer gesmolten slak de elektrodepunt bereikt, dooft de boog. Door de elektrische weerstand van de gesmolten slak wordt continu energie toegevoerd. Wij kunnen platen lassen met diktes tussen 50 mm en 900 mm en zelfs hoger. De stroomsterkte ligt rond de 600 Ampère terwijl de spanning tussen de 40 – 50 V ligt. De lassnelheden liggen rond de 12 tot 36 mm/min. Toepassingen zijn vergelijkbaar met elektrogaslassen.
Een van onze niet-verbruikbare elektrodeprocessen, de GAS TUNGSTEN ARC WELDING (GTAW), ook bekend als TUNGSTEN INERT GAS WELDING (TIG), omvat de toevoer van een toevoegmetaal door een draad. Voor nauw aansluitende verbindingen gebruiken we soms het vulmetaal niet. In het TIG-proces gebruiken we geen flux, maar gebruiken we argon en helium voor afscherming. Wolfraam heeft een hoog smeltpunt en wordt niet verbruikt in het TIG-lasproces, waardoor een constante stroom en boogopeningen kunnen worden gehandhaafd. Vermogensniveaus liggen tussen 8 en 20 kW en stromen van 200 ampère (DC) of 500 ampère (AC). Voor aluminium en magnesium gebruiken we wisselstroom voor de oxidereinigingsfunctie. Om verontreiniging van de wolfraamelektrode te voorkomen, vermijden we het contact met gesmolten metalen. Gas Tungsten Arc Welding (GTAW) is vooral handig voor het lassen van dunne metalen. GTAW-lassen zijn van zeer hoge kwaliteit met een goede oppervlakteafwerking.
Vanwege de hogere kosten van waterstofgas is een minder vaak gebruikte techniek ATOMIC HYDROGEN WELDING (AHW), waarbij we een boog genereren tussen twee wolfraamelektroden in een afschermende atmosfeer van stromend waterstofgas. De AHW is ook een niet-verbruikbaar elektrodelasproces. Het twee-atomige waterstofgas H2 valt uiteen in zijn atomaire vorm nabij de lasboog, waar de temperatuur hoger is dan 6273 Kelvin. Tijdens het afbreken absorbeert het een grote hoeveelheid warmte van de boog. Wanneer de waterstofatomen de laszone raken, die een relatief koud oppervlak is, recombineren ze in diatomische vorm en geven ze de opgeslagen warmte af. Energie kan worden gevarieerd door het werkstuk te veranderen in boogafstand.
In een ander niet-verbruikbaar elektrodeproces, PLASMA ARC WELDING (PAW), hebben we een geconcentreerde plasmaboog die naar de laszone is gericht. De temperaturen bereiken 33.273 Kelvin in PAW. Een bijna gelijk aantal elektronen en ionen vormen het plasmagas. Een pilootboog met lage stroomsterkte initieert het plasma dat zich tussen de wolfraamelektrode en de opening bevindt. Bedrijfsstromen zijn over het algemeen ongeveer 100 Ampère. Een vulmetaal kan worden toegevoerd. Bij plasmabooglassen wordt de afscherming bereikt door een buitenste afschermring en met behulp van gassen zoals argon en helium. Bij plasmabooglassen kan de boog zich tussen de elektrode en het werkstuk of tussen de elektrode en het mondstuk bevinden. Deze lastechniek heeft als voordelen ten opzichte van andere methoden een hogere energieconcentratie, dieper en smaller lasvermogen, betere boogstabiliteit, hogere lassnelheden tot 1 meter/min, minder thermische vervorming. Over het algemeen passen we plasmabooglassen toe voor diktes van minder dan 6 mm en soms tot 20 mm voor aluminium en titanium.
HIGH-ENERGY-BEAM-LASSEN: Een ander type smeltlasmethode met elektronenstraallassen (EBW) en laserlassen (LBW) als twee varianten. Deze technieken zijn bijzonder waardevol voor onze productie van hightech producten. Bij het lassen met elektronenbundels treffen elektronen met hoge snelheid het werkstuk en wordt hun kinetische energie omgezet in warmte. De smalle bundel elektronen verplaatst zich gemakkelijk in de vacuümkamer. Over het algemeen gebruiken we hoogvacuüm bij e-beam lassen. Platen tot 150 mm dik kunnen worden gelast. Er zijn geen beschermgassen, flux of vulmateriaal nodig. Elektronstraalkanonnen hebben een capaciteit van 100 kW. Diepe en smalle lassen met hoge aspectverhoudingen tot 30 en kleine hittebeïnvloede zones zijn mogelijk. Lassnelheden kunnen oplopen tot 12 m/min. Bij laserstraallassen gebruiken we krachtige lasers als warmtebron. Laserstralen van slechts 10 micron met een hoge dichtheid maken een diepe penetratie in het werkstuk mogelijk. Diepte-breedteverhoudingen tot 10 zijn mogelijk met laserstraallassen. We gebruiken zowel gepulseerde als continue golflasers, de eerste in toepassingen voor dunne materialen en de laatste meestal voor dikke werkstukken tot ongeveer 25 mm. Vermogensniveaus zijn tot 100 kW. Het laserstraallassen is niet goed geschikt voor optisch sterk reflecterende materialen. Bij het lasproces kunnen ook gassen worden gebruikt. De laserstraallasmethode is zeer geschikt voor automatisering en productie van grote volumes en biedt lassnelheden tussen 2,5 m/min en 80 m/min. Een groot voordeel van deze lastechniek is de toegang tot gebieden waar andere technieken niet kunnen worden gebruikt. Laserstralen kunnen gemakkelijk naar zulke moeilijke gebieden reizen. Er is geen vacuüm nodig zoals bij elektronenstraallassen. Lassen met een goede kwaliteit en sterkte, lage krimp, lage vervorming, lage porositeit kunnen worden verkregen met laserstraallassen. Laserstralen kunnen eenvoudig worden gemanipuleerd en gevormd met behulp van glasvezelkabels. De techniek is dus zeer geschikt voor het lassen van hermetische precisie-assemblages, elektronische pakketten, enz.
Laten we eens kijken naar onze SOLID STATE LAStechnieken. KOUD LASSEN (CW) is een proces waarbij druk in plaats van warmte wordt toegepast met behulp van matrijzen of rollen op de onderdelen die zijn gekoppeld. Bij koudlassen moet ten minste één van de in elkaar passende delen ductiel zijn. De beste resultaten worden verkregen met twee vergelijkbare materialen. Als de twee metalen die met koud lassen moeten worden verbonden, niet hetzelfde zijn, kunnen we zwakke en broze verbindingen krijgen. De koude lasmethode is zeer geschikt voor zachte, kneedbare en kleine werkstukken zoals elektrische verbindingen, hittegevoelige containerranden, bimetalen strips voor thermostaten... enz. Een variant van koudlassen is rolverlijming (of rollassen), waarbij de druk wordt uitgeoefend door een paar rollen. Soms voeren we rollassen uit bij verhoogde temperaturen voor een betere grensvlaksterkte.
Een ander solid state lasproces dat we gebruiken is het ULTRASONIC WELDING (USW), waarbij de werkstukken worden onderworpen aan een statische normaalkracht en oscillerende schuifspanningen. De oscillerende schuifspanningen worden aangebracht via de punt van een transducer. Ultrasoon lassen maakt gebruik van trillingen met frequenties van 10 tot 75 kHz. Bij sommige toepassingen, zoals naadlassen, gebruiken we een roterende lasschijf als punt. Schuifspanningen die op de werkstukken worden uitgeoefend, veroorzaken kleine plastische vervormingen, breken oxidelagen en verontreinigingen af en leiden tot vaste stofbinding. De temperaturen bij ultrasoon lassen liggen ver onder het smeltpunt van metalen en er vindt geen fusie plaats. We gebruiken vaak het ultrasone lasproces (USW) voor niet-metalen materialen zoals kunststoffen. Bij thermoplasten bereiken de temperaturen echter wel het smeltpunt.
Een andere populaire techniek, bij FRICTION WELDING (FRW), wordt de warmte gegenereerd door wrijving op het grensvlak van de te verbinden werkstukken. Bij wrijvingslassen houden we een van de werkstukken stationair terwijl het andere werkstuk in een opspanning wordt gehouden en met een constante snelheid wordt geroteerd. De werkstukken worden vervolgens onder een axiale kracht met elkaar in contact gebracht. De rotatiesnelheid van het oppervlak bij wrijvingslassen kan in sommige gevallen 900 m/min bereiken. Na voldoende grensvlakcontact wordt het draaiende werkstuk abrupt tot stilstand gebracht en wordt de axiale kracht vergroot. De laszone is over het algemeen een smal gebied. De wrijvingslastechniek kan worden gebruikt om massieve en buisvormige delen van verschillende materialen te verbinden. Er kan wat flits ontstaan op de interface in FRW, maar deze flits kan worden verwijderd door secundaire bewerking of slijpen. Variaties van het wrijvingslasproces bestaan. Bij "traagheidswrijvingslassen" wordt bijvoorbeeld een vliegwiel gebruikt waarvan de kinetische rotatie-energie wordt gebruikt om de onderdelen te lassen. De las is voltooid wanneer het vliegwiel tot stilstand komt. De roterende massa kan worden gevarieerd en daarmee de roterende kinetische energie. Een andere variatie is "lineair wrijvingslassen", waarbij lineaire heen en weer gaande beweging wordt opgelegd aan ten minste één van de te verbinden componenten. Bij lineaire wrijvingslassen hoeven onderdelen niet cirkelvormig te zijn, ze kunnen rechthoekig, vierkant of een andere vorm hebben. Frequenties kunnen in de tientallen Hz liggen, amplitudes in het millimeterbereik en drukken in de tientallen of honderden MPa. Ten slotte is "wrijvingsroerlassen" enigszins anders dan de andere twee die hierboven zijn uitgelegd. Terwijl bij traagheidswrijvingslassen en lineair wrijvingslassen verwarming van interfaces wordt bereikt door wrijving door twee contactoppervlakken te wrijven, wordt bij de wrijvingsroerlasmethode een derde lichaam tegen de twee te verbinden oppervlakken gewreven. Een roterend gereedschap met een diameter van 5 tot 6 mm wordt in contact gebracht met de verbinding. De temperaturen kunnen oplopen tot waarden tussen 503 en 533 Kelvin. Het materiaal in de voeg wordt verwarmd, gemengd en geroerd. We gebruiken het wrijvingsroerlassen op een verscheidenheid aan materialen, waaronder aluminium, kunststoffen en composieten. De lasnaden zijn uniform en de kwaliteit is hoog met minimale poriën. Bij het wrijvingsroerlassen worden geen dampen of spatten geproduceerd en het proces is goed geautomatiseerd.
WEERSTANDSLASSEN (RW): De warmte die nodig is voor het lassen wordt geproduceerd door de elektrische weerstand tussen de twee te verbinden werkstukken. Bij weerstandslassen worden geen flux, beschermgassen of verbruikbare elektroden gebruikt. Joule-verwarming vindt plaats bij weerstandslassen en kan worden uitgedrukt als:
H = (Vierkant I) x R xtx K
H is warmte gegenereerd in joule (watt-seconden), I stroom in ampère, R weerstand in ohm, t is de tijd in seconden dat de stroom er doorheen stroomt. De factor K is kleiner dan 1 en vertegenwoordigt de fractie energie die niet verloren gaat door straling en geleiding. De stromen in weerstandslasprocessen kunnen oplopen tot 100.000 A, maar de spanningen zijn doorgaans 0,5 tot 10 volt. Elektroden zijn meestal gemaakt van koperlegeringen. Zowel gelijkaardige als ongelijksoortige materialen kunnen worden verbonden door weerstandslassen. Er bestaan verschillende variaties voor dit proces: "Weerstandspuntlassen" omvat twee tegenover elkaar liggende ronde elektroden die contact maken met de oppervlakken van de overlappende verbinding van de twee platen. Er wordt druk uitgeoefend totdat de stroom wordt uitgeschakeld. De lasnugget heeft over het algemeen een diameter tot 10 mm. Weerstandspuntlassen laat licht verkleurde indruksporen achter op laspunten. Puntlassen is onze meest populaire weerstandslastechniek. Bij het puntlassen worden verschillende elektrodevormen gebruikt om moeilijk bereikbare plaatsen te bereiken. Onze puntlasapparatuur is CNC-gestuurd en heeft meerdere elektroden die tegelijkertijd kunnen worden gebruikt. Een andere variant "weerstandsnaadlassen" wordt uitgevoerd met wiel- of rolelektroden die continue puntlassen produceren wanneer de stroom een voldoende hoog niveau bereikt in de AC-stroomcyclus. Verbindingen geproduceerd door weerstandsnaadlassen zijn vloeistof- en gasdicht. Lassnelheden van ongeveer 1,5 m/min zijn normaal voor dunne platen. Men kan intermitterende stromen toepassen zodat puntlassen op gewenste intervallen langs de naad worden geproduceerd. Bij “weerstand projectielassen” ciseleren we één of meerdere uitsteeksels (dimples) op één van de te lassen werkstukoppervlakken. Deze uitsteeksels kunnen rond of ovaal zijn. Op deze reliëfplekken die in contact komen met het pasgedeelte worden hoge plaatselijke temperaturen bereikt. Elektroden oefenen druk uit om deze projecties samen te drukken. Elektroden bij weerstandsprojectielassen hebben platte punten en zijn watergekoelde koperlegeringen. Het voordeel van weerstandsprojectielassen is ons vermogen om een aantal lassen in één slag te maken, dus de langere levensduur van de elektrode, het vermogen om platen van verschillende diktes te lassen, het vermogen om moeren en bouten aan platen te lassen. Nadeel van weerstandsprojectielassen zijn de extra kosten van het reliëf van de kuiltjes. Nog een andere techniek, bij "flitslassen", wordt warmte gegenereerd door de boog aan de uiteinden van de twee werkstukken wanneer ze contact beginnen te maken. Deze methode kan ook worden beschouwd als booglassen. De temperatuur aan het grensvlak stijgt en het materiaal wordt zachter. Er wordt een axiale kracht uitgeoefend en er wordt een las gevormd in het verweekte gebied. Nadat het flitslassen is voltooid, kan de verbinding worden bewerkt voor een beter uiterlijk. De laskwaliteit verkregen door flitslassen is goed. Vermogensniveaus zijn 10 tot 1500 kW. Flitslassen is geschikt voor rand-tot-rand verbinding van gelijkaardige of ongelijksoortige metalen tot 75 mm diameter en platen met een dikte van 0,2 mm tot 25 mm. "Stoppenbooglassen" lijkt sterk op flitslassen. De bout zoals een bout of draadstang dient als één elektrode terwijl deze wordt verbonden met een werkstuk zoals een plaat. Om de gegenereerde warmte te concentreren, oxidatie te voorkomen en het gesmolten metaal in de laszone te houden, wordt een wegwerpbare keramische ring rond de verbinding geplaatst. Ten slotte "percussielassen", een ander weerstandslasproces, maakt gebruik van een condensator om de elektrische energie te leveren. Bij percussielassen wordt het vermogen binnen milliseconden zeer snel ontladen, waarbij een hoge plaatselijke warmte bij de verbinding ontstaat. We passen slaglassen veel toe in de elektronica-industrie waar verhitting van gevoelige elektronische componenten in de buurt van de verbinding moet worden vermeden.
Een techniek die EXPLOSIELASSEN wordt genoemd, houdt in dat een laag explosief tot ontploffing wordt gebracht die over een van de te verbinden werkstukken wordt aangebracht. De zeer hoge druk die op het werkstuk wordt uitgeoefend, produceert een turbulent en golvend grensvlak en er vindt mechanische vergrendeling plaats. Hechtsterkten bij explosief lassen zijn zeer hoog. Explosielassen is een goede methode voor het bekleden van platen met verschillende metalen. Na het bekleden kunnen de platen in dunnere secties worden gerold. Soms gebruiken we explosielassen voor het uitzetten van buizen, zodat ze strak tegen de plaat worden afgedicht.
Onze laatste methode binnen het domein van solid-state verbinding is DIFFUSIEBONDING of DIFFUSIELASSEN (DFW), waarbij een goede verbinding voornamelijk wordt bereikt door diffusie van atomen over het grensvlak. Enige plastische vervorming op het grensvlak draagt ook bij aan het lassen. De betrokken temperaturen liggen rond de 0,5 Tm, waarbij Tm de smelttemperatuur van het metaal is. Hechtsterkte bij diffusielassen hangt af van druk, temperatuur, contacttijd en reinheid van contactoppervlakken. Soms gebruiken we vulmetalen op het grensvlak. Warmte en druk zijn vereist bij diffusiebinding en worden geleverd door elektrische weerstand of oven en dode gewichten, pers of anders. Gelijkaardige en ongelijksoortige metalen kunnen worden verbonden met diffusielassen. Het proces is relatief traag vanwege de tijd die atomen nodig hebben om te migreren. DFW kan worden geautomatiseerd en wordt veel gebruikt bij de fabricage van complexe onderdelen voor de lucht- en ruimtevaart, elektronica en medische industrie. Gefabriceerde producten omvatten orthopedische implantaten, sensoren, structurele onderdelen voor de ruimtevaart. Diffusieverlijming kan worden gecombineerd met SUPERPLASTIC FORMING om complexe plaatwerkconstructies te vervaardigen. Geselecteerde locaties op vellen worden eerst diffusiegebonden en vervolgens worden de niet-gebonden gebieden met luchtdruk geëxpandeerd tot een mal. Lucht- en ruimtevaartconstructies met hoge stijfheid-gewichtsverhoudingen worden vervaardigd met behulp van deze combinatie van methoden. Het gecombineerde proces van diffusielassen / superplastische vorming vermindert het aantal benodigde onderdelen door de noodzaak voor bevestigingsmiddelen te elimineren, wat resulteert in zeer nauwkeurige onderdelen met lage spanning, economisch en met korte doorlooptijden.
SOLDEREN: Bij de soldeer- en soldeertechnieken zijn lagere temperaturen nodig dan bij het lassen. Soldeertemperaturen zijn echter hoger dan soldeertemperaturen. Bij het solderen wordt een vulmetaal tussen de te verbinden oppervlakken geplaatst en worden de temperaturen verhoogd tot de smelttemperatuur van het vulmateriaal boven 723 Kelvin maar onder de smelttemperaturen van de werkstukken. Het gesmolten metaal vult de nauw passende ruimte tussen de werkstukken. Afkoeling en daaropvolgende stolling van het vulmetaal resulteert in sterke verbindingen. Bij hardsolderen wordt het toevoegmetaal op de verbinding afgezet. Bij hardsolderen wordt aanzienlijk meer toevoegmetaal gebruikt dan bij hardsolderen. Oxyacetyleentoorts met oxiderende vlam wordt gebruikt om het vulmetaal af te zetten bij hardsolderen. Door lagere temperaturen bij het solderen zijn problemen in door warmte aangetaste zones zoals kromtrekken en restspanningen minder. Hoe kleiner de speling bij het solderen, hoe hoger de afschuifsterkte van de verbinding. Maximale treksterkte wordt echter bereikt bij een optimale spleet (een piekwaarde). Onder en boven deze optimale waarde neemt de treksterkte bij het solderen af. Typische spelingen bij het solderen kunnen tussen 0,025 en 0,2 mm zijn. We gebruiken een verscheidenheid aan soldeermaterialen met verschillende vormen, zoals prestaties, poeder, ringen, draad, strip ... enz. en kan deze uitvoeringen speciaal voor uw ontwerp of productgeometrie vervaardigen. Ook bepalen we het gehalte van de soldeermaterialen op basis van uw basismaterialen en toepassing. We gebruiken vaak vloeimiddelen bij hardsolderen om ongewenste oxidelagen te verwijderen en oxidatie te voorkomen. Om latere corrosie te voorkomen, worden vloeimiddelen in het algemeen verwijderd na de verbindingsbewerking. AGS-TECH Inc. gebruikt verschillende soldeermethoden, waaronder:
- Toorts solderen
- Oven Solderen
- Inductiesolderen
- Weerstandssolderen
- Dip solderen
- Infrarood solderen
- Diffusiesolderen
- Hoge energiestraal
Onze meest voorkomende voorbeelden van gesoldeerde verbindingen zijn gemaakt van verschillende metalen met een goede sterkte, zoals hardmetalen boren, inzetstukken, opto-elektronische hermetische pakketten, afdichtingen.
SOLDEREN: Dit is een van onze meest gebruikte technieken waarbij het soldeer (vulmetaal) de verbinding vult zoals bij het solderen tussen nauw aansluitende componenten. Onze soldeer heeft smeltpunten onder 723 Kelvin. We gebruiken zowel handmatig als geautomatiseerd solderen in productieprocessen. In vergelijking met solderen zijn de soldeertemperaturen lager. Solderen is niet erg geschikt voor toepassingen met hoge temperaturen of hoge sterkte. We gebruiken voor het solderen naast andere loodvrije soldeer ook tin-lood, tin-zink, lood-zilver, cadmium-zilver, zink-aluminium legeringen. Zowel niet-corrosieve harsgebaseerde als anorganische zuren en zouten worden gebruikt als vloeimiddel bij het solderen. We gebruiken speciale vloeimiddelen om metalen met een lage soldeerbaarheid te solderen. In toepassingen waar we keramische materialen, glas of grafiet moeten solderen, plateren we de onderdelen eerst met een geschikt metaal voor een verhoogde soldeerbaarheid. Onze populaire soldeertechnieken zijn:
-Reflow of plakken solderen
-Golf solderen
-Oven Solderen
-Toorts Solderen
-Inductie Solderen
-Ijzer Solderen
-Weerstand Solderen
-Dip-solderen
-Ultrasoon solderen
-Infrarood Solderen
Ultrasoon solderen biedt ons een uniek voordeel waarbij de noodzaak voor vloeimiddelen wordt geëlimineerd vanwege het ultrasone cavitatie-effect dat oxidefilms verwijdert van de te verbinden oppervlakken. Reflow- en Wave-solderen zijn onze industrieel uitstekende technieken voor de productie van grote volumes in de elektronica en daarom de moeite waard om nader uit te leggen. Bij reflow-solderen gebruiken we halfvaste pasta's die soldeermetaaldeeltjes bevatten. De pasta wordt met behulp van een zeef- of sjablonerproces op de voeg aangebracht. Bij printplaten (PCB's) gebruiken we deze techniek veelvuldig. Wanneer elektrische componenten uit pasta op deze pads worden geplaatst, houdt de oppervlaktespanning de op het oppervlak gemonteerde pakketten uitgelijnd. Na het plaatsen van de componenten verwarmen we het geheel in een oven zodat het reflow-solderen plaatsvindt. Tijdens dit proces verdampen de oplosmiddelen in de pasta, wordt de flux in de pasta geactiveerd, worden de componenten voorverwarmd, worden de soldeerdeeltjes gesmolten en wordt de verbinding nat, en tenslotte wordt de PCB-assemblage langzaam afgekoeld. Onze tweede populaire techniek voor de productie van printplaten in grote volumes, namelijk golfsolderen, is gebaseerd op het feit dat gesmolten soldeer metalen oppervlakken nat maakt en alleen goede hechtingen vormt als het metaal voorverwarmd is. Een staande laminaire golf van gesmolten soldeer wordt eerst gegenereerd door een pomp en de voorverwarmde en voorgevloeide PCB's worden over de golf getransporteerd. Het soldeer bevochtigt alleen blootgestelde metalen oppervlakken, maar maakt de IC-polymeerverpakkingen of de met polymeer beklede printplaten niet nat. Een hoge snelheid van hete waterstraal blaast overtollig soldeer uit de verbinding en voorkomt overbrugging tussen aangrenzende draden. Bij het golfsolderen van opbouwpakketten lijmen we ze voor het solderen eerst op de printplaat. Opnieuw wordt screenen en sjabloneren gebruikt, maar deze keer voor epoxy. Nadat de componenten op de juiste plaats zijn geplaatst, wordt de epoxy uitgehard, worden de platen omgekeerd en vindt golfsolderen plaats.