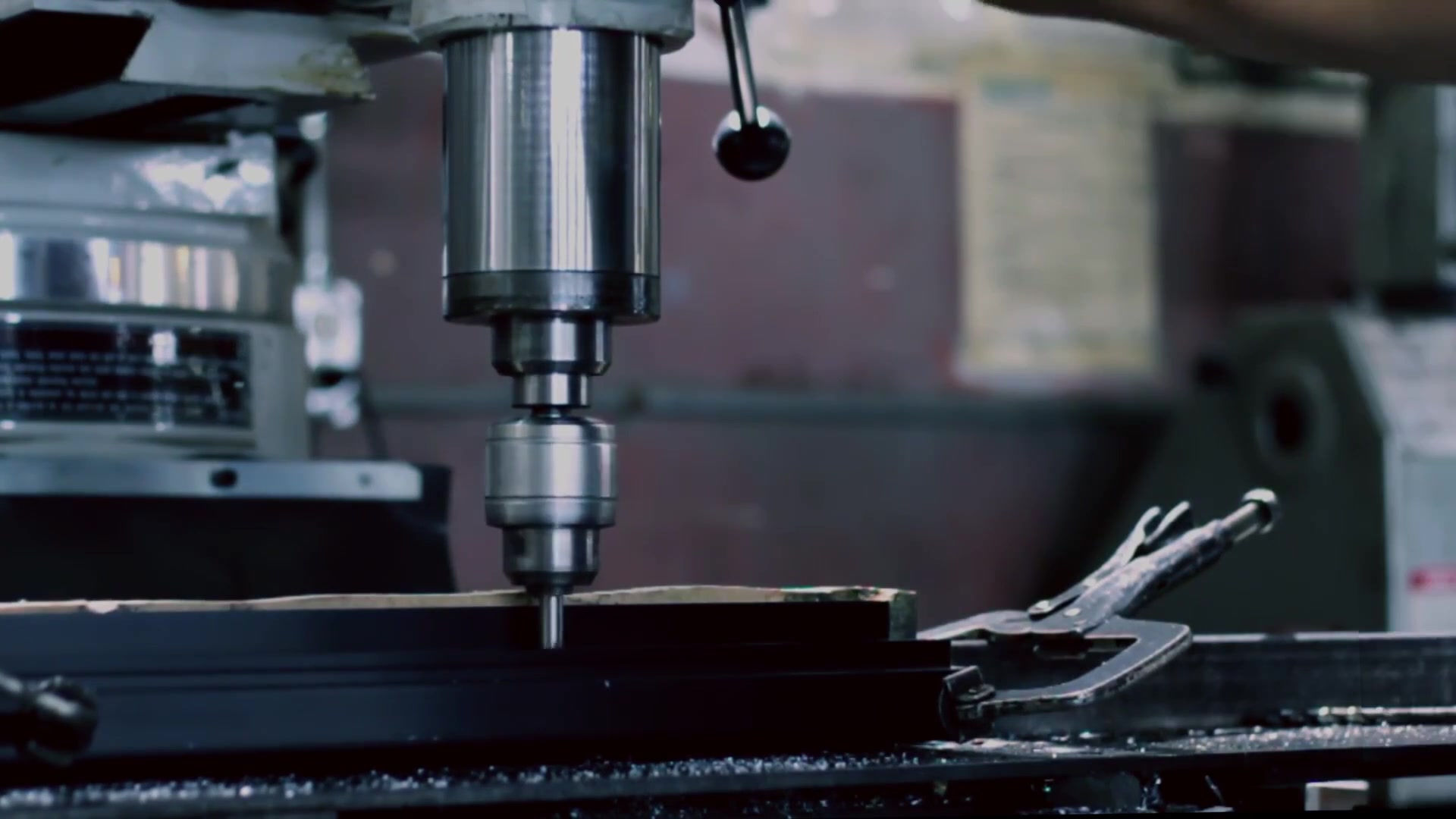
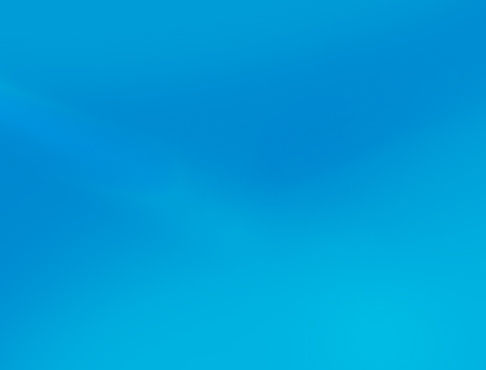
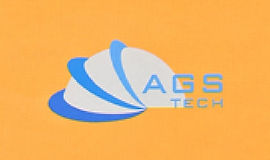
Global Custom Manufacturer, Integrator, Consolidator, Outsourcing Partner for en bred vifte af produkter og tjenester.
Vi er din one-stop-kilde til fremstilling, fremstilling, konstruktion, konsolidering, integration, outsourcing af specialfremstillede og hyldeprodukter og -tjenester.
Vælg dit sprog
-
Brugerdefineret fremstilling
-
Indenlandsk og global kontraktfremstilling
-
Outsourcing af produktion
-
Indenlandske og globale indkøb
-
Consolidation
-
Engineering Integration
-
Ingeniørtjenester
Vores specialfremstillede støbe- og bearbejdningsteknikker er forbrugs- og ikke-forbrugbare støbegods, jernholdig og ikke-jernholdig støbning, sand, matrice, centrifugal, kontinuerlig, keramisk form, investering, tabt skum, næsten-net-form, permanent form (gravitation trykstøbning), gips støbeforme (gipsstøbning) og skalstøbning, bearbejdede dele fremstillet ved fræsning og drejning ved brug af konventionelt såvel som CNC-udstyr, bearbejdning af schweizisk type til højkapacitets- og billige små præcisionsdele, skruebearbejdning til fastgørelseselementer, ikke-konventionel bearbejdning. Vær opmærksom på, at udover metaller og metallegeringer, bearbejder vi keramik-, glas- og plastkomponenter også i nogle tilfælde, når fremstillingen af en form ikke er tiltalende eller ikke er muligheden. Bearbejdning af polymermaterialer kræver den specialiserede erfaring, vi har på grund af den udfordring, plast og gummi giver på grund af deres blødhed, ikke-stivhed...osv. For bearbejdning af keramik og glas, se venligst vores side om ikke-konventionel fremstilling. AGS-TECH Inc. fremstiller og leverer både lette og tunge støbegods. Vi har leveret metalstøbegods og bearbejdede dele til kedler, varmevekslere, biler, mikromotorer, vindmøller, madpakkeudstyr og meget mere. Vi anbefaler, at du klikker her for at DOWNLOAD vores skematiske illustrationer af bearbejdnings- og støbeprocesser af AGS-TECH Inc.
Dette vil hjælpe dig med bedre at forstå de oplysninger, vi giver dig nedenfor. Lad os se nærmere på nogle af de forskellige teknikker, vi tilbyder:
• FORBRUGSTØBNING: Denne brede kategori refererer til metoder, der involverer midlertidige og ikke-genanvendelige forme. Eksempler er sand, gips, skal, investering (også kaldet lost-wax) og gipsstøbning.
• SANDSTØBNING: En proces, hvor sand bruges som formmateriale. En meget gammel metode og stadig meget populær i det omfang, at størstedelen af metalstøbegods er fremstillet ved denne teknik. Lave omkostninger selv ved lave mængder produktion. Velegnet til fremstilling af små og store dele. Teknikken kan bruges til at fremstille dele inden for dage eller uger med meget lidt investering. Det fugtige sand bindes sammen med ler, bindemidler eller specialolier. Sand er generelt indeholdt i formkasser, og hulrums- og portsystem skabes ved at komprimere sandet omkring modeller. Processerne er:
1.) Anbringelse af modellen i sand for at lave formen
2.) Indbygning af model og sand i et portsystem
3.) Fjernelse af model
4.) Fyldning af formhulrum med smeltet metal
5.) Køling af metallet
6.) Brydning af sandformen og fjernelse af støbningen
• GIPSSTØBNING: I lighed med sandstøbning, og i stedet for sand, bruges gips som formmateriale. Korte produktionstider som sandstøbning og billig. Gode dimensionstolerancer og overfladefinish. Dens største ulempe er, at den kun kan bruges med metaller med lavt smeltepunkt som aluminium og zink.
• SKALSTØBNING: Ligner også til sandstøbning. Formhule opnået ved en hærdet skal af sand og termohærdende harpiksbindemiddel i stedet for en kolbe fyldt med sand som i sandstøbeprocessen. Næsten ethvert metal, der er egnet til at blive støbt med sand, kan støbes ved skalstøbning. Processen kan opsummeres som:
1.) Fremstilling af skalformen. Det anvendte sand har en meget mindre kornstørrelse sammenlignet med sand, der bruges til sandstøbning. Det fine sand blandes med termohærdende harpiks. Metalmønsteret er belagt med et skillemiddel for at gøre det nemmere at fjerne skallen. Derefter opvarmes metalmønsteret, og sandblandingen poreres eller blæses på det varme støbemønster. En tynd skal dannes på overfladen af mønsteret. Tykkelsen af denne skal kan justeres ved at variere, hvor lang tid sandharpiksblandingen er i kontakt med metalmønsteret. Det løse sand fjernes derefter med det skaldækkede mønster tilbage.
2.) Dernæst varmes skallen og mønsteret i en ovn, så skallen stivner. Efter hærdning er fuldført, skydes skallen ud af mønsteret ved hjælp af stifter indbygget i mønsteret.
3.) To sådanne skaller samles sammen ved limning eller fastspænding og udgør den komplette form. Nu lægges skalformen ind i en beholder, hvori den under støbeprocessen understøttes af sand eller metalskud.
4.) Nu kan det varme metal hældes i skalformen.
Fordele ved skalstøbning er produkter med meget god overfladefinish, mulighed for fremstilling af komplekse dele med høj dimensionel nøjagtighed, proces let at automatisere, økonomisk til produktion af store mængder.
Ulemperne er, at formene kræver god ventilation på grund af gasser, der dannes, når smeltet metal kommer i kontakt med bindemiddelkemikaliet, de termohærdende harpikser og metalmønstre er dyre. På grund af omkostningerne ved metalmønstre egner teknikken sig muligvis ikke godt til små produktionskørsler.
• INVESTERINGSSTØBNING (også kendt som LOST-WAX CASTING): Også en meget gammel teknik og velegnet til fremstilling af kvalitetsdele med høj nøjagtighed, repeterbarhed, alsidighed og integritet fra mange metaller, ildfaste materialer og specielle højtydende legeringer. Små såvel som store dele kan fremstilles. En dyr proces sammenlignet med nogle af de andre metoder, men en stor fordel er muligheden for at producere dele med næsten netform, indviklede konturer og detaljer. Så omkostningerne er noget opvejet af eliminering af efterbearbejdning og bearbejdning i nogle tilfælde. Selvom der kan være variationer, er her en oversigt over den generelle investeringscastingproces:
1.) Oprettelse af originalt mastermønster fra voks eller plastik. Hver støbning har brug for et mønster, da disse ødelægges i processen. Form, hvorfra der fremstilles mønstre, er også nødvendig, og det meste af tiden er formen støbt eller bearbejdet. Fordi formen ikke skal åbnes, kan komplekse støbninger opnås, mange voksmønstre kan forbindes som grenene af et træ og hældes sammen, hvilket muliggør produktion af flere dele fra en enkelt udstøbning af metallet eller metallegeringen.
2.) Dernæst dyppes eller hældes mønsteret over med en ildfast opslæmning sammensat af meget finkornet silica, vand, bindemidler. Dette resulterer i et keramisk lag over overfladen af mønsteret. Det ildfaste lag på mønster efterlades til at tørre og hærde. Dette trin er, hvor navnet investeringsstøbning kommer fra: Ildfast gylle lægges over voksmønsteret.
3.) På dette trin vendes den hærdede keramiske form på hovedet og varmes op, så voksen smelter og hælder ud af formen. Der efterlades et hulrum til metalstøbningen.
4.) Efter at voksen er ude, opvarmes den keramiske form til endnu en højere temperatur, hvilket resulterer i forstærkning af formen.
5.) Metalstøbning hældes i den varme form, der fylder alle indviklede sektioner.
6.) Støbning får lov til at størkne
7.) Til sidst knækkes den keramiske form og fremstillede dele skæres fra træet.
Her er et link til Investment Casting Plant Brochure
• FORdampningsmønsterstøbning: Processen bruger et mønster lavet af et materiale såsom polystyrenskum, der vil fordampe, når varmt smeltet metal hældes i formen. Der er to typer af denne proces: LOST FOAM CASTING, som bruger ubundet sand, og FULL MOLD CASTING, der bruger bundet sand. Her er de generelle procestrin:
1.) Fremstil mønsteret af et materiale såsom polystyren. Når der skal fremstilles store mængder, støbes mønsteret. Hvis en del har en kompleks form, skal flere sektioner af et sådant skummateriale muligvis klæbes sammen for at danne mønsteret. Vi belægger ofte mønsteret med en ildfast masse for at skabe en god overfladefinish på støbningen.
2.) Mønsteret lægges derefter i formsand.
3.) Det smeltede metal hældes i formen, hvorved skummønsteret, dvs. polystyren i de fleste tilfælde, fordamper, når det strømmer gennem formhulen.
4.) Det smeltede metal efterlades i sandformen for at hærde.
5.) Efter at det er hærdet, fjerner vi støbningen.
I nogle tilfælde kræver det produkt, vi fremstiller, en kerne i mønsteret. Ved fordampningsstøbning er det ikke nødvendigt at placere og sikre en kerne i formhulrummet. Teknikken er velegnet til fremstilling af meget komplekse geometrier, den kan let automatiseres til højvolumen produktion, og der er ingen skillelinjer i den støbte del. Den grundlæggende proces er enkel og økonomisk at implementere. For produktion af store mængder, da en matrice eller form er nødvendig for at fremstille mønstrene fra polystyren, kan dette være noget dyrt.
• IKKE-EKSPANDERBAR FORMSTØBNING: Denne brede kategori refererer til metoder, hvor formen ikke skal reformeres efter hver produktionscyklus. Eksempler er permanent, matrice, kontinuerlig og centrifugalstøbning. Repeterbarhed opnås, og dele kan karakteriseres som NEAR NET SHAPE.
• PERMANENT STØBNING : Genanvendelige forme fremstillet af metal bruges til flere støbninger. En permanent form kan generelt bruges i titusindvis af gange, før den bliver slidt. Tyngdekraft, gastryk eller vakuum bruges generelt til at fylde formen. Forme (også kaldet matrice) er generelt lavet af jern, stål, keramik eller andre metaller. Den generelle proces er:
1.) Bearbejd og lav formen. Det er almindeligt at bearbejde formen af to metalblokke, der passer sammen og kan åbnes og lukkes. Både delens funktioner såvel som portsystemet er generelt bearbejdet i støbeformen.
2.) De indvendige formoverflader er belagt med en opslæmning, der indeholder ildfaste materialer. Dette hjælper med at kontrollere varmestrømmen og fungerer som et smøremiddel for nem fjernelse af den støbte del.
3.) Dernæst lukkes de permanente formhalvdele, og formen opvarmes.
4.) Smeltet metal hældes i form og lades stille til størkning.
5.) Inden der sker meget afkøling, fjerner vi delen fra den permanente form ved hjælp af ejektorer, når formhalvdelene åbnes.
Vi bruger ofte permanent formstøbning til lavsmeltende metaller som zink og aluminium. Til stålstøbegods bruger vi grafit som formmateriale. Nogle gange opnår vi komplekse geometrier ved hjælp af kerner i permanente forme. Fordele ved denne teknik er støbegods med gode mekaniske egenskaber opnået ved hurtig afkøling, ensartet egenskaber, god nøjagtighed og overfladefinish, lave afvisningsprocenter, mulighed for at automatisere processen og producere høje volumener økonomisk. Ulemperne er høje initiale opsætningsomkostninger, som gør den uegnet til lavvolumenoperationer, og begrænsninger på størrelsen af de fremstillede dele.
• DISTØBNING: En matrice bearbejdes, og smeltet metal skubbes under højt tryk ind i formhulrum. Både ikke-jernholdige såvel som jernholdige trykstøbninger er mulige. Processen er velegnet til produktion af store mængder af små til mellemstore dele med detaljer, ekstremt tynde vægge, dimensionskonsistens og god overfladefinish. AGS-TECH Inc. er i stand til at fremstille vægtykkelser helt ned til 0,5 mm ved hjælp af denne teknik. Ligesom ved permanent formstøbning skal formen bestå af to halvdele, der kan åbne og lukke for at fjerne den producerede del. En trykstøbeform kan have flere hulrum for at muliggøre produktion af flere støbegods med hver cyklus. Trykstøbeforme er meget tunge og meget større end de dele, de producerer, og derfor også dyre. Vi reparerer og udskifter slidte matricer gratis for vores kunder, så længe de genbestiller deres dele hos os. Vores matricer har lang levetid i flere hundrede tusinde cyklusser.
Her er de grundlæggende forenklede procestrin:
1.) Fremstilling af formen generelt af stål
2.) Form installeret på trykstøbemaskine
3.) Stemplet tvinger smeltet metal til at flyde i matricehulrummene og udfylder de indviklede funktioner og tynde vægge
4.) Efter fyldning af formen med det smeltede metal, lades støbegodset hærde under tryk
5.) Form åbnes og støbning fjernes ved hjælp af udkasterstifter.
6.) Nu smøres den tomme matrice igen og spændes fast til næste cyklus.
Ved trykstøbning bruger vi hyppigt indsatsstøbning, hvor vi indarbejder en ekstra del i formen og støber metallet rundt om den. Efter størkning bliver disse dele en del af det støbte produkt. Fordele ved trykstøbning er delenes gode mekaniske egenskaber, mulighed for indviklede funktioner, fine detaljer og god overfladefinish, høje produktionshastigheder, nem automatisering. Ulemper er: Ikke særlig velegnet til lav volumen på grund af høje matrice- og udstyrsomkostninger, begrænsninger i forme, der kan støbes, små runde mærker på støbte dele som følge af kontakt med udkasterstifter, tynde metalglimt presset ud ved skillelinjen, behov for udluftninger langs skillelinjen mellem formen, nødvendigheden af at holde formtemperaturerne lave ved hjælp af vandcirkulation.
• CENTRIFUGALSTØBNING: Smeltet metal hældes ind i midten af den roterende form ved rotationsaksen. Centrifugalkræfter kaster metallet mod periferien, og det lades størkne, mens formen bliver ved med at rotere. Både vandrette og lodrette akserotationer kan anvendes. Der kan støbes dele med runde indvendige overflader samt andre ikke-runde former. Processen kan opsummeres som:
1.) Smeltet metal hældes i centrifugalform. Metallet tvinges derefter til ydervæggene på grund af spinding af formen.
2.) Når formen roterer, hærder metalstøbningen
Centrifugalstøbning er en velegnet teknik til produktion af hule cylindiriske dele som rør, intet behov for indløb, stigrør og portelementer, god overfladefinish og detaljerede funktioner, ingen krympningsproblemer, mulighed for at producere lange rør med meget store diametre, høj produktionskapacitet .
• KONTINUERLIG STØBNING ( STRANDSTØBNING ): Bruges til at støbe en kontinuerlig længde af metal. Grundlæggende er det smeltede metal støbt ind i en todimensionel profil af formen, men dens længde er ubestemt. Nyt smeltet metal tilføres konstant i formen, efterhånden som støbegodset bevæger sig nedad med dets længde stigende med tiden. Metaller som kobber, stål, aluminium støbes til lange tråde ved hjælp af kontinuerlig støbeproces. Processen kan have forskellige konfigurationer, men den almindelige kan forenkles som:
1.) Smeltet metal hældes i en beholder placeret højt over støbeformen ved velberegnet mængder og strømningshastigheder og strømmer gennem den vandkølede støbeform. Metalstøbningen, der hældes i formen, størkner til en startstang placeret i bunden af formen. Denne startstang giver rullerne noget at tage fat i i starten.
2.) Den lange metalstreng bæres af ruller med konstant hastighed. Rullerne ændrer også retningen af strømmen af metalstreng fra lodret til vandret.
3.) Efter den kontinuerlige støbning har tilbagelagt en vis vandret afstand, skærer en brænder eller sav, der bevæger sig med støbningen, den hurtigt til de ønskede længder.
Kontinuerlig støbeproces kan integreres med ROLLING PROCESS, hvor det kontinuerligt støbte metal kan føres direkte ind i et valseværk for at producere I-Beams, T-Beams….osv. Kontinuerlig støbning giver ensartede egenskaber i hele produktet, det har en høj størkningshastighed, reducerer omkostninger på grund af meget lavt materialetab, tilbyder en proces, hvor læsning af metal, støbning, størkning, skæring og støbefjernelse alt sammen foregår i en kontinuerlig drift og hvilket resulterer i høj produktivitet og høj kvalitet. En vigtig overvejelse er dog den høje initialinvestering, opsætningsomkostninger og pladsbehov.
• BEARBEJDNINGSSERVICE: Vi tilbyder tre-, fire- og femakset bearbejdning. Den type bearbejdningsprocesser, vi bruger, er DREJNING, FRÆSNING, BORING, BORING, BRINGNING, HØVNING, SAVNING, SLIBNING, LAPPING, POLIERING og IKKE-TRADITIONEL BEARBEJDNING, som er yderligere uddybet under en anden menu på vores hjemmeside. Til det meste af vores produktion bruger vi CNC-maskiner. Men til nogle operationer passer konventionelle teknikker bedre, og derfor stoler vi også på dem. Vores bearbejdningsevner når det højest mulige niveau, og nogle af de mest krævende dele er fremstillet på et AS9100-certificeret anlæg. Jetmotorvinger kræver højt specialiseret fremstillingserfaring og det rigtige udstyr. Luftfartsindustrien har meget strenge standarder. Nogle komponenter med komplekse geometriske strukturer fremstilles nemmest ved femakset bearbejdning, som kun findes i nogle bearbejdningsanlæg, inklusive vores. Vores rumfartscertificerede anlæg har den nødvendige erfaring med at overholde omfattende dokumentationskrav fra luftfartsindustrien.
Ved DREJE-operationer roteres et emne og bevæges mod et skæreværktøj. Til denne proces bruges en maskine kaldet drejebænk.
I FRÆSNING har en maskine kaldet fræsemaskine et roterende værktøj til at bringe skærekanter til at ligge an mod et emne.
BORING involverer en roterende fræser med skærekanter, der producerer huller ved kontakt med emnet. Borepresser, drejebænke eller møller anvendes generelt.
Ved BORING-operationer flyttes et værktøj med en enkelt bøjet spids spids ind i et groft hul i et roterende emne for at forstørre hullet lidt og forbedre nøjagtigheden. Det bruges til fine efterbehandlingsformål.
BRACHING involverer et fortandet værktøj til at fjerne materiale fra et emne i en gang af brochen (tandværktøj). Ved lineær brobning løber brochen lineært mod en overflade af emnet for at udføre snittet, hvorimod ved roterende brochning roteres brochen og presses ind i arbejdsemnet for at skære en aksesymmetrisk form.
SWISS TYPE MACHINING er en af vores værdifulde teknikker, vi bruger til fremstilling af små højpræcisionsdele i store mængder. Ved at bruge drejebænk af schweizisk type drejer vi små, komplekse præcisionsdele billigt. I modsætning til konventionelle drejebænke, hvor emnet holdes stationært og værktøj i bevægelse, i drejecentre af schweizisk type, tillades emnet at bevæge sig i Z-aksen, og værktøjet er stationært. Ved bearbejdning af schweizisk type holdes stangen i maskinen og føres frem gennem en styrebøsning i z-aksen, hvilket blot blotlægger den del, der skal bearbejdes. På denne måde sikres et stramt greb, og nøjagtigheden er meget høj. Tilgængeligheden af levende værktøjer giver mulighed for at fræse og bore, efterhånden som materialet kommer frem fra styrebøsningen. Y-aksen i det schweiziske udstyr giver fuld fræsekapacitet og sparer meget tid i fremstillingen. Ydermere har vores maskiner bor og boreværktøj, der opererer på delen, når den holdes i underspindelen. Vores bearbejdningskapacitet af schweizisk type giver os en fuldautomatisk komplet bearbejdningsmulighed i en enkelt operation.
Bearbejdning er et af de største segmenter af AGS-TECH Inc. forretning. Vi bruger det enten som en primær operation eller en sekundær operation efter støbning eller ekstrudering af en del, så alle tegningsspecifikationer overholdes.
• OVERFLADEBEHANDLING: Vi tilbyder en bred vifte af overfladebehandlinger og overfladebehandling, såsom overfladebehandling for at forbedre vedhæftningen, aflejring af tyndt oxidlag for at forbedre vedhæftningen af belægningen, sandblæsning, kemisk film, anodisering, nitrering, pulverlakering, spraybelægning , forskellige avancerede metalliserings- og belægningsteknikker, herunder sputtering, elektronstråle, fordampning, plettering, hårde belægninger såsom diamantlignende kulstof (DLC) eller titaniumbelægning til bore- og skæreværktøjer.
• PRODUKTMÆRKNING & ETIKETTERING: Mange af vores kunder kræver mærkning og mærkning, lasermærkning, gravering på metaldele. Hvis du har et sådant behov, så lad os diskutere, hvilken løsning der vil være den bedste for dig.
Her er nogle af de mest brugte metalstøbte produkter. Da disse er hyldevare, kan du spare på formomkostningerne, hvis nogen af disse passer til dine krav:
KLIK HER FOR AT DOWNLOAD vores 11 serie trykstøbte aluminiumskasser fra AGS-Electronics