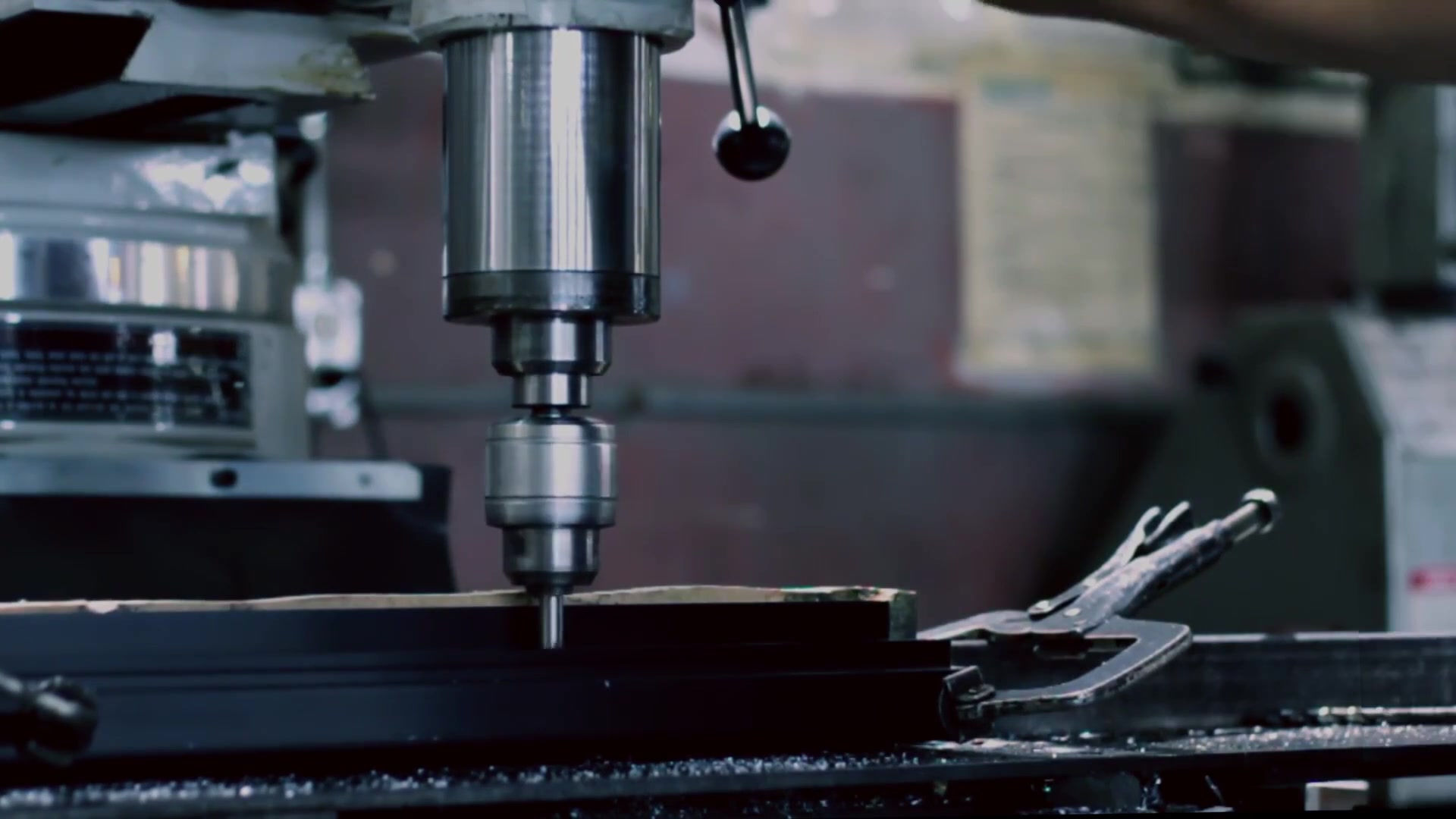
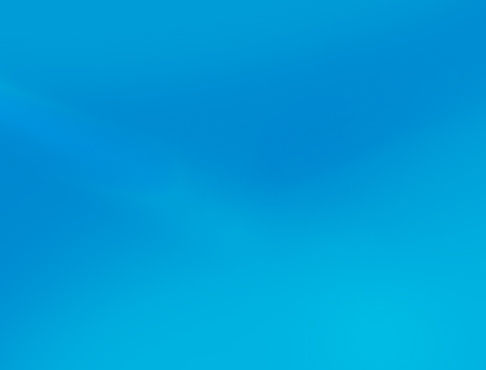
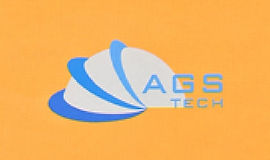
Global Custom Manufacturer, Integrator, Consolidator, Outsourcing Partner for en bred vifte af produkter og tjenester.
Vi er din one-stop-kilde til fremstilling, fremstilling, konstruktion, konsolidering, integration, outsourcing af specialfremstillede og hyldeprodukter og -tjenester.
Vælg dit sprog
-
Brugerdefineret fremstilling
-
Indenlandsk og global kontraktfremstilling
-
Outsourcing af produktion
-
Indenlandske og globale indkøb
-
Consolidation
-
Engineering Integration
-
Ingeniørtjenester
Vi samler, samler og fastgør dine fremstillede dele og forvandler dem til færdige eller halvfabrikata ved hjælp af SVEJSNING, SLODNING, LODNING, SINTERING, KLÆBNING, FASTSÆTNING, PRESSMASNING. Nogle af vores mest populære svejseprocesser er lysbue, oxyfuel gas, modstand, projektion, søm, stød, percussion, solid state, elektronstråle, laser, termit, induktionssvejsning. Vores populære loddeprocesser er brænder-, induktions-, ovn- og dyppelodning. Vores lodningsmetoder er jern, varmeplade, ovn, induktion, dip, wave, reflow og ultralydslodning. Til klæbende limning bruger vi ofte termoplast og termohærdende, epoxy, phenoler, polyurethan, klæbende legeringer samt nogle andre kemikalier og tape. Endelig består vores fastgørelsesprocesser af sømning, skruning, møtrikker og bolte, nitning, clinching, pinning, syning & hæftning og prespasning.
• SVEJSNING: Svejsning involverer sammenføjning af materialer ved at smelte emnerne og indføre fyldmaterialer, som også forbinder det smeltede svejsebad. Når området afkøles, opnår vi en stærk fuge. Der påføres pres i nogle tilfælde. I modsætning til svejsning involverer lodning og loddeoperationer kun smeltning af et materiale med lavere smeltepunkt mellem emnerne, og emner smelter ikke. Vi anbefaler, at du klikker her for atDOWNLOAD vores skematiske illustrationer af svejseprocesser af AGS-TECH Inc.
Dette vil hjælpe dig med bedre at forstå de oplysninger, vi giver dig nedenfor.
I ARRC WELDING bruger vi en strømforsyning og en elektrode til at skabe en elektrisk lysbue, der smelter metallerne. Svejsepunktet er beskyttet af en beskyttelsesgas eller damp eller andet materiale. Denne proces er populær til svejsning af autodele og stålkonstruktioner. Ved shelled metal arc welding (SMAW) eller også kendt som stavsvejsning, bringes en elektrodepind tæt på grundmaterialet, og der dannes en elektrisk lysbue mellem dem. Elektrodestangen smelter og fungerer som fyldmateriale. Elektroden indeholder også flux, der fungerer som et slaggelag og afgiver dampe, der fungerer som beskyttelsesgassen. Disse beskytter svejseområdet mod miljøforurening. Der bruges ingen andre fyldstoffer. Ulemperne ved denne proces er dens langsomhed, behovet for at udskifte elektroder hyppigt, behovet for at spåne den resterende slagge, der stammer fra flux, væk. En række metaller såsom jern, stål, nikkel, aluminium, kobber...osv. Kan svejses. Dens fordele er dets billige værktøjer og brugervenlighed. Gasmetalbuesvejsning (GMAW) også kendt som metal-inert gas (MIG), vi har kontinuerlig tilførsel af et forbrugsbart elektrodetrådfyldstof og en inert eller delvist inert gas, der strømmer rundt om tråden mod miljømæssig forurening af svejseområdet. Stål, aluminium og andre ikke-jernholdige metaller kan svejses. Fordelene ved MIG er høje svejsehastigheder og god kvalitet. Ulemperne er dets komplicerede udstyr og udfordringer i blæsende udendørs miljøer, fordi vi skal holde beskyttelsesgassen omkring svejseområdet stabil. En variant af GMAW er flux-coreed arc welding (FCAW), som består af et fint metalrør fyldt med fluxmaterialer. Nogle gange er fluxen inde i røret tilstrækkelig til beskyttelse mod miljøforurening. Submerged Arc Welding (SAW) er i vid udstrækning en automatiseret proces, der involverer kontinuerlig trådfremføring og lysbue, der slås under et lag af fluxdæksel. Produktionshastigheden og kvaliteten er høj, svejseslagger slipper let af, og vi har et røgfrit arbejdsmiljø. Ulempen er, at den kun kan bruges til at svejse parts i bestemte positioner. Ved gaswolframbuesvejsning (GTAW) eller wolfram-inert gassvejsning (TIG) bruger vi en wolframelektrode sammen med et separat fyldstof og inerte eller næsten inerte gasser. Som vi ved har wolfram et højt smeltepunkt, og det er et meget velegnet metal til meget høje temperaturer. Tungsten i TIG indtages ikke i modsætning til de andre metoder forklaret ovenfor. En langsom, men en højkvalitets svejseteknik fordelagtig i forhold til andre teknikker til svejsning af tynde materialer. Velegnet til mange metaller. Plasmabuesvejsning ligner, men bruger plasmagas til at skabe lysbuen. Lysbuen ved plasmabuesvejsning er relativt mere koncentreret sammenlignet med GTAW og kan bruges til et bredere udvalg af metaltykkelser ved meget højere hastigheder. GTAW- og plasmabuesvejsning kan anvendes på mere eller mindre de samme materialer.
OXY-FUEL / OXYFUEL WELDING også kaldet oxyacetylensvejsning, oxysvejsning, gassvejsning udføres ved hjælp af gasbrændstoffer og ilt til svejsning. Da der ikke bruges strøm, er den bærbar og kan bruges, hvor der ikke er strøm. Ved hjælp af en svejsebrænder opvarmer vi stykkerne og fyldmaterialet for at producere en fælles pool af smeltet metal. Forskellige brændstoffer kan bruges såsom acetylen, benzin, brint, propan, butan ... osv. Ved oxy-fuel svejsning bruger vi to beholdere, en til brændstoffet og den anden til ilt. Ilten oxiderer brændstoffet (forbrænder det).
MODSTANDSVEJSNING: Denne type svejsning udnytter joule-opvarmning, og varme genereres på det sted, hvor der tilføres elektrisk strøm i en vis tid. Høje strømme føres gennem metallet. Puljer af smeltet metal dannes på dette sted. Modstandssvejsemetoder er populære på grund af deres effektivitet, lille forureningspotentiale. Ulemperne er imidlertid, at udstyrsomkostningerne er relativt betydelige og den iboende begrænsning til relativt tynde arbejdsemner. PUNTSVEJSNING er en hovedtype af modstandssvejsning. Her forbinder vi to eller flere overlappende plader eller arbejdsemner ved at bruge to kobberelektroder til at klemme pladerne sammen og føre en høj strøm gennem dem. Materialet mellem kobberelektroderne opvarmes, og der dannes en smeltet pool på det sted. Strømmen stoppes derefter, og kobberelektrodespidserne afkøler svejsestedet, fordi elektroderne er vandkølede. At påføre den rigtige mængde varme til det rigtige materiale og tykkelse er nøglen til denne teknik, for hvis den påføres forkert, vil samlingen være svag. Punktsvejsning har den fordel, at den ikke forårsager nogen væsentlig deformation af emner, energieffektivitet, let automatisering og fremragende produktionshastigheder og ikke kræver nogen fyldstoffer. Ulempen er, at da svejsning finder sted på steder i stedet for at danne en kontinuerlig søm, kan den samlede styrke være relativt lavere sammenlignet med andre svejsemetoder. SØMSVEJSNING på den anden side producerer svejsninger på de falsende overflader af lignende materialer. Sømmen kan være numse eller overlappende samling. Sømsvejsning starter i den ene ende og bevæger sig gradvist til den anden. Denne metode bruger også to elektroder fra kobber til at påføre tryk og strøm til svejseområdet. De skiveformede elektroder roterer med konstant kontakt langs sømlinjen og laver en kontinuerlig svejsning. Også her afkøles elektroder af vand. Svejsningerne er meget stærke og pålidelige. Andre metoder er projektion, flash og forstyrrede svejseteknikker.
SVEJSNING i fast tilstand er en smule anderledes end de foregående metoder, der er forklaret ovenfor. Koalescens finder sted ved temperaturer under smeltetemperaturen for de sammenføjede metaller og uden brug af metalfyldstof. Tryk kan bruges i nogle processer. Forskellige metoder er COEKTRUSIONSVEJSNING, hvor uens metaller ekstruderes gennem den samme matrice, KOLDTRYKSVEJSNING, hvor vi samler bløde legeringer under deres smeltepunkter, DIFFUSIONSVEJSNING en teknik uden synlige svejselinjer, EKSPLOSIONSSVEJSNING til sammenføjning af forskellige materialer, f.eks. korrosionsbestandige legeringer stål, ELEKTROMAGNETISK PULSVEJSNING, hvor vi accelererer rør og plader ved elektromagnetiske kræfter, SMEDESVEJSNING, der består i at opvarme metallerne til høje temperaturer og hamre dem sammen, FRIKTIONS-SVEJSNING, hvor der med tilstrækkelig friktionssvejsning udføres, FRIKTIONS-STØRSVEJSNING, der involverer en roterende ikke- forbrugsværktøj, der krydser samlingslinjen, VARMTRYKSVEJSNING, hvor vi presser metaller sammen ved forhøjede temperaturer under smeltetemperaturen i vakuum eller inerte gasser, VARMT ISOSTATISK TRYKSVEJSNING en proces, hvor vi påfører tryk ved hjælp af inaktive gasser inde i en beholder, RULLESVEJSNING, hvor vi samler uens materialer ved at tvinge dem imellem to roterende hjul, ULTRALYDSVEJSNING hvor tynde metal- eller plastplader svejses ved hjælp af højfrekvent vibrationsenergi.
Vores andre svejseprocesser er ELEKTRONSVEJSNING med dyb indtrængning og hurtig bearbejdning, men da vi er en dyr metode, betragter vi det i specielle tilfælde, ELEKTROSLAG-SVEJSNING en metode, der kun er egnet til tunge tykke plader og emner af stål, INDUKTIONSVEJSNING, hvor vi anvender elektromagnetisk induktion og opvarme vores elektrisk ledende eller ferromagnetiske emner, LASERSTRALSVEJSNING også med dyb indtrængning og hurtig bearbejdning, men en dyr metode, LASER HYBRID-SVEJSNING, der kombinerer LBW med GMAW i samme svejsehoved og er i stand til at bygge bro mellem plader på 2 mm, PERKUSSIONSVEJSNING, der involverer en elektrisk udladning efterfulgt af smedning af materialerne med påført tryk, THERMIT-SVEJSNING, der involverer eksoterm reaktion mellem aluminium- og jernoxidpulvere., ELEKTROGAS-SVEJSNING med forbrugselektroder og kun brugt med stål i lodret position, og til sidst STUDBUUSVEJSNING til sammenføjning af tap til bund. materiale med varme og tryk.
Vi anbefaler, at du klikker her for atDOWNLOAD vores skematiske illustrationer af lodning, lodning og klæbemiddelprocesser af AGS-TECH Inc.
Dette vil hjælpe dig med bedre at forstå de oplysninger, vi giver dig nedenfor.
• LØDNING : Vi forbinder to eller flere metaller ved at opvarme fyldmetaller imellem dem over deres smeltepunkter og bruge kapillærvirkning til at sprede sig. Processen ligner lodning, men de involverede temperaturer for at smelte fyldstoffet er højere ved lodning. Ligesom ved svejsning beskytter flux fyldmaterialet mod atmosfærisk forurening. Efter afkøling sammenføjes emnerne. Processen involverer følgende nøgletrin: God pasform og frigang, korrekt rengøring af basismaterialer, korrekt fastgørelse, korrekt valg af flux og atmosfære, opvarmning af samlingen og endelig rengøring af loddet samling. Nogle af vores slaglodningsprocesser er TORCH BRAZING, en populær metode, der udføres manuelt eller på en automatiseret måde. Den er velegnet til lave produktionsordrer og specialiserede sager. Varme tilføres ved hjælp af gasflammer i nærheden af samlingen, der loddes. OVNSLODNING kræver mindre operatørfærdighed og er en halvautomatisk proces, der er velegnet til industriel masseproduktion. Både temperaturstyring og styring af atmosfæren i ovnen er fordele ved denne teknik, fordi førstnævnte gør det muligt for os at have kontrollerede varmecyklusser og eliminere lokal opvarmning, som det er tilfældet ved brænderlodning, og sidstnævnte beskytter delen mod oxidation. Ved at bruge jigging er vi i stand til at reducere produktionsomkostningerne til et minimum. Ulemperne er højt strømforbrug, udstyrsomkostninger og mere udfordrende designovervejelser. VAKUUMSLODNING foregår i en ovn af vakuum. Temperaturens ensartethed bibeholdes, og vi opnår fluxfrie, meget rene fuger med meget få restspændinger. Varmebehandlinger kan finde sted under vakuumlodning på grund af de lave restspændinger, der er til stede under langsomme opvarmnings- og afkølingscyklusser. Den største ulempe er dens høje omkostninger, fordi skabelsen af et vakuummiljø er en dyr proces. Endnu en anden teknik DIP-LODNING forbinder fastmonterede dele, hvor loddemasse påføres på parrende overflader. Derefter dyppes de faste dele i et bad med et smeltet salt såsom natriumchlorid (bordsalt), der fungerer som et varmeoverførselsmedium og flusmiddel. Luft er udelukket, og derfor finder der ingen oxiddannelse sted. I INDUKTIONSLODNING samler vi materialer med et fyldmetal, der har et lavere smeltepunkt end basismaterialerne. Vekselstrømmen fra induktionsspolen skaber et elektromagnetisk felt, som inducerer induktionsopvarmning på for det meste jernholdige magnetiske materialer. Metoden giver selektiv opvarmning, gode samlinger med fyldstoffer, der kun flyder i ønskede områder, lille oxidation, fordi der ikke er flammer til stede, og afkøling er hurtig, hurtig opvarmning, konsistens og egnethed til fremstilling af store mængder. For at fremskynde vores processer og for at sikre ensartethed bruger vi ofte præforme. Oplysninger om vores loddeanlæg, der producerer keramiske til metalfittings, hermetisk forsegling, vakuumgennemføringer, høj- og ultrahøjvakuum- og væskekontrolkomponenter kan findes her:_cc781905-156-5cde_cc781905-916-5cde_cc781905-916-5cdeLodningsfabriksbrochure
• LODNING : Ved lodning har vi ikke smeltning af emnerne, men et fyldmetal med et lavere smeltepunkt end de sammenføjningsdele, der flyder ind i samlingen. Fyldmetallet ved lodning smelter ved lavere temperatur end ved lodning. Vi bruger blyfri legeringer til lodning og har RoHS-overensstemmelse og til forskellige anvendelser og krav har vi forskellige og egnede legeringer såsom sølvlegering. Lodning giver os samlinger, der er gas- og væsketætte. I BLØD LØDNING har vores fyldmetal et smeltepunkt under 400 Celsius, hvorimod vi ved SØLVLODNING og LODNING har brug for højere temperaturer. Blød lodning bruger lavere temperaturer, men resulterer ikke i stærke samlinger til krævende applikationer ved høje temperaturer. Sølvlodning på den anden side kræver høje temperaturer leveret af brænderen og giver os stærke samlinger, der er egnede til højtemperaturapplikationer. Lodning kræver de højeste temperaturer, og der bruges normalt en brænder. Da loddesamlinger er meget stærke, er de gode kandidater til at reparere tunge jerngenstande. I vores produktionslinjer bruger vi både manuel håndlodning samt automatiserede loddelinjer. INDUKTIONSLODNING bruger højfrekvent vekselstrøm i en kobberspole for at lette induktionsopvarmning. Strømme induceres i den loddede del, og som følge heraf genereres varme ved den høje modstand joint. Denne varme smelter fyldmetallet. Flux bruges også. Induktionslodning er en god metode til at lodde cyclindere og rør i en kontinuerlig proces ved at vikle spolerne omkring dem. Lodning af nogle materialer såsom grafit og keramik er vanskeligere, fordi det kræver plettering af emnerne med et passende metal før lodning. Dette letter grænsefladebinding. Vi lodder sådanne materialer især til hermetiske emballageapplikationer. Vi fremstiller vores printkort (PCB) i høj volumen, for det meste ved hjælp af BØLGELODNING. Kun til små mængder af prototypeformål bruger vi håndlodning med loddekolbe. Vi bruger bølgelodning til både gennemgående huller såvel som overflademonterede PCB-samlinger (PCBA). En midlertidig lim holder komponenterne fastgjort til printpladen, og samlingen placeres på en transportør og bevæger sig gennem et udstyr, der indeholder smeltet loddemetal. Først fluxes PCB'en og går derefter ind i forvarmningszonen. Det smeltede loddemiddel er i en gryde og har et mønster af stående bølger på overfladen. Når printet bevæger sig over disse bølger, kommer disse bølger i kontakt med bunden af printet og klæber til loddepuderne. Loddet bliver kun på stifter og puder og ikke på selve printkortet. Bølgerne i det smeltede loddemateriale skal være godt kontrolleret, så der ikke er sprøjt, og bølgetoppene ikke rører ved og forurener uønskede områder af pladerne. I REFLOW SOLDERING bruger vi en klæbrig loddepasta til midlertidigt at fastgøre de elektroniske komponenter til pladerne. Herefter sættes pladerne gennem en reflowovn med temperaturkontrol. Her smelter loddet og forbinder komponenterne permanent. Vi bruger denne teknik til både overflademonteringskomponenter såvel som til gennemgående hulkomponenter. Korrekt temperaturkontrol og justering af ovntemperaturer er afgørende for at undgå ødelæggelse af elektroniske komponenter på kortet ved at overophede dem over deres maksimale temperaturgrænser. I processen med reflow-lodning har vi faktisk flere regioner eller trin, hver med en særskilt termisk profil, såsom forvarmningstrin, termisk iblødsætningstrin, reflow og afkølingstrin. Disse forskellige trin er afgørende for en skadesfri reflow-lodning af printkortsamlinger (PCBA). ULTRALYDSLODNING er en anden hyppigt brugt teknik med unikke egenskaber- Den kan bruges til at lodde glas, keramiske og ikke-metalliske materialer. For eksempel fotovoltaiske paneler, som er ikke-metalliske, har brug for elektroder, som kan fastgøres ved hjælp af denne teknik. Ved ultralydslodning anvender vi en opvarmet loddespids, der også udsender ultralydsvibrationer. Disse vibrationer producerer kavitationsbobler ved grænsefladen mellem substratet og det smeltede loddemateriale. Den implosive energi fra kavitation modificerer oxidoverfladen og fjerner snavs og oxider. I løbet af denne tid dannes der også et legeringslag. Loddet på bindingsoverfladen inkorporerer ilt og muliggør dannelsen af en stærk fælles binding mellem glasset og loddemetal. DIPLODNING kan betragtes som en enklere version af bølgelodning, der kun er egnet til produktion i mindre skala. Første renseflux påføres som i andre processer. PCB'er med monterede komponenter dyppes manuelt eller på en semi-automatisk måde i en tank indeholdende smeltet lod. Det smeltede loddemiddel klæber til de udsatte metalliske områder ubeskyttet af loddemaske på brættet. Udstyret er enkelt og billigt.
• KLÆBENDE KLÆBNING: Dette er en anden populær teknik, vi ofte bruger, og den involverer limning af overflader ved hjælp af lim, epoxy, plastikmidler eller andre kemikalier. Binding opnås ved enten at fordampe opløsningsmidlet, ved varmehærdning, ved UV-lyshærdning, ved trykhærdning eller afventning i en vis tid. Forskellige højtydende lime bruges i vores produktionslinjer. Med korrekt konstruerede påførings- og hærdningsprocesser kan klæbemiddelbinding resultere i meget lave spændingsbindinger, der er stærke og pålidelige. Klæbemidler kan være gode beskyttere mod miljøfaktorer som fugt, forurenende stoffer, ætsende, vibrationer...osv. Fordele ved klæbende limning er: de kan påføres materialer, der ellers ville være svære at lodde, svejse eller lodde. Det kan også være at foretrække for varmefølsomme materialer, der ville blive beskadiget ved svejsning eller andre højtemperaturprocesser. Andre fordele ved klæbemidler er, at de kan påføres uregelmæssigt formede overflader og øger samlingsvægten med meget meget små mængder sammenlignet med andre metoder. Også dimensionsændringer i dele er meget minimale. Nogle lime har indeksmatchende egenskaber og kan bruges mellem optiske komponenter uden at reducere lyset eller den optiske signalstyrke væsentligt. Ulemperne på den anden side er længere hærdetider, som kan forsinke fremstillingslinjerne, krav til fastgørelse, krav til overfladeforberedelse og vanskeligheder ved at skille ad, når der er behov for efterbearbejdning. De fleste af vores adhæsive liming operationer involverer følgende trin:
-Overfladebehandling: Særlige rengøringsprocedurer såsom deioniseret vandrensning, alkoholrensning, plasma- eller coronarensning er almindelige. Efter rengøring kan vi påføre vedhæftningsfremmende midler på overfladerne for at sikre de bedst mulige samlinger.
-Delmontering: Til både klæbemiddelpåføring såvel som til hærdning designer og bruger vi tilpassede armaturer.
-Klæbemiddelanvendelse: Vi bruger nogle gange manuelle, og nogle gange afhængigt af sagen, automatiserede systemer såsom robotter, servomotorer, lineære aktuatorer til at levere klæbemidlerne til det rigtige sted, og vi bruger dispensere til at levere det i den rigtige volumen og mængde.
-Hærdning: Afhængigt af klæbemidlet kan vi bruge simpel tørring og hærdning samt hærdning under UV-lys, der fungerer som katalysator eller varmehærdning i en ovn eller ved hjælp af resistive varmeelementer monteret på jigs og armaturer.
Vi anbefaler, at du klikker her for atDOWNLOAD vores skematiske illustrationer af fastgørelsesprocesser af AGS-TECH Inc.
Dette vil hjælpe dig med bedre at forstå de oplysninger, vi giver dig nedenfor.
• FASTGØRELSESPROCESSER: Vores mekaniske sammenføjningsprocesser falder i to kategorier: FASTNINGSMIDLER og INTEGRALE SAMLINGER. Eksempler på fastgørelsesmidler vi bruger er skruer, stifter, møtrikker, bolte, nitter. Eksempler på integrerede samlinger, vi bruger, er snap- og krympepasninger, sømme, krympninger. Ved at bruge en række forskellige fastgørelsesmetoder sikrer vi, at vores mekaniske samlinger er stærke og pålidelige til mange års brug. SKRUER og BOLTE er nogle af de mest almindeligt anvendte fastgørelsesanordninger til at holde genstande sammen og positionere. Vores skruer og bolte opfylder ASME-standarder. Forskellige typer skruer og bolte er installeret, herunder sekskantskruer og sekskantskruer, lagskruer og bolte, dobbeltskruer, dyvelskruer, øjeskruer, spejlskruer, metalpladeskruer, finjusteringsskruer, selvborende og selvskærende skruer , sætskrue, skruer med indbyggede spændeskiver,...og mere. Vi har forskellige skruehovedertyper såsom forsænket, kuppel, rundt, flangehoved og forskellige skruetræktyper såsom slot, phillips, firkantet, sekskantet fatning. En RIVET på den anden side er et permanent mekanisk fastgørelseselement bestående af et glat cylindrisk skaft og et hoved på den ene side. Efter indsættelse deformeres den anden ende af nitten, og dens diameter udvides, så den bliver på plads. Med andre ord, før installationen har en nitte et hoved, og efter installationen har den to. Vi installerer forskellige typer nitter afhængigt af anvendelse, styrke, tilgængelighed og omkostninger, såsom solide/runde nitter, strukturelle, semi-tubulære, blinde, oscar, drive, flush, friktionslåse, selvgennemborende nitter. Nitning kan foretrækkes i tilfælde, hvor varmedeformation og ændringer i materialeegenskaber på grund af svejsevarme skal undgås. Nitning giver også let vægt og især god styrke og udholdenhed mod forskydningskræfter. Mod trækbelastninger kan skruer, møtrikker og bolte dog være mere egnede. I CLINCHING-processen bruger vi specielle stanser og matricer til at danne en mekanisk sammenlåsning mellem metalplader, der samles. Stansen skubber lagene af metal ind i matricehulrummet og resulterer i dannelsen af en permanent samling. Ingen opvarmning og ingen køling er påkrævet i clinching, og det er en kold arbejdsproces. Det er en økonomisk proces, der i nogle tilfælde kan erstatte punktsvejsning. I PINNING bruger vi stifter, som er maskinelementer, der bruges til at sikre positioner af maskindele i forhold til hinanden. Vigtigste typer er gaffelstifter, splinter, fjederstift, dyvelstifter, og splitstift. I STAPLING bruger vi hæftepistoler og hæfteklammer, som er to-benede fastgørelseselementer, der bruges til at sammenføje eller binde materialer. Hæftning har følgende fordele: Økonomisk, enkel og hurtig at bruge, hæfteklammernes krone kan bruges til at bygge bro over materialer, der er stødt sammen, Kronen på hæfteklammer kan lette at bygge bro over et stykke som et kabel og fastgøre det til en overflade uden at punktere eller beskadigende, forholdsvis nem fjernelse. PRESSMONTERING udføres ved at skubbe dele sammen og friktionen mellem dem fastgør delene. Presspasningsdele, der består af et overdimensioneret skaft og et underdimensioneret hul, samles generelt ved en af to metoder: Enten ved at påføre kraft eller udnytte termisk udvidelse eller sammentrækning af delene. Når en presfitting etableres ved at påføre en kraft, bruger vi enten en hydraulisk presse eller en håndbetjent presse. På den anden side, når presfitting etableres ved termisk ekspansion, opvarmer vi de omsluttende dele og samler dem på deres plads, mens de er varme. Når de afkøles, trækker de sig sammen og vender tilbage til deres normale dimensioner. Dette resulterer i en god prespasning. Dette kalder vi alternativt SHRINK-FITTING. Den anden måde at gøre dette på er ved at afkøle de omsluttede dele før montering og derefter skubbe dem ind i deres parringsdele. Når samlingen varmer op, udvider de sig, og vi opnår en tæt pasform. Sidstnævnte metode kan være at foretrække i tilfælde, hvor opvarmning udgør en risiko for at ændre materialeegenskaber. Køling er mere sikker i disse tilfælde.
Pneumatiske og hydrauliske komponenter og samlinger
• Ventiler, hydrauliske og pneumatiske komponenter såsom O-ring, skive, tætninger, pakning, ring, mellemlæg.
Da ventiler og pneumatiske komponenter findes i et stort udvalg, kan vi ikke liste alt her. Afhængigt af de fysiske og kemiske miljøer i din applikation, har vi specielle produkter til dig. Angiv venligst anvendelse, type komponent, specifikationer, miljøforhold såsom tryk, temperatur, væsker eller gasser, der vil være i kontakt med dine ventiler og pneumatiske komponenter; og vi vil vælge det mest passende produkt til dig eller fremstille det specielt til din applikation.