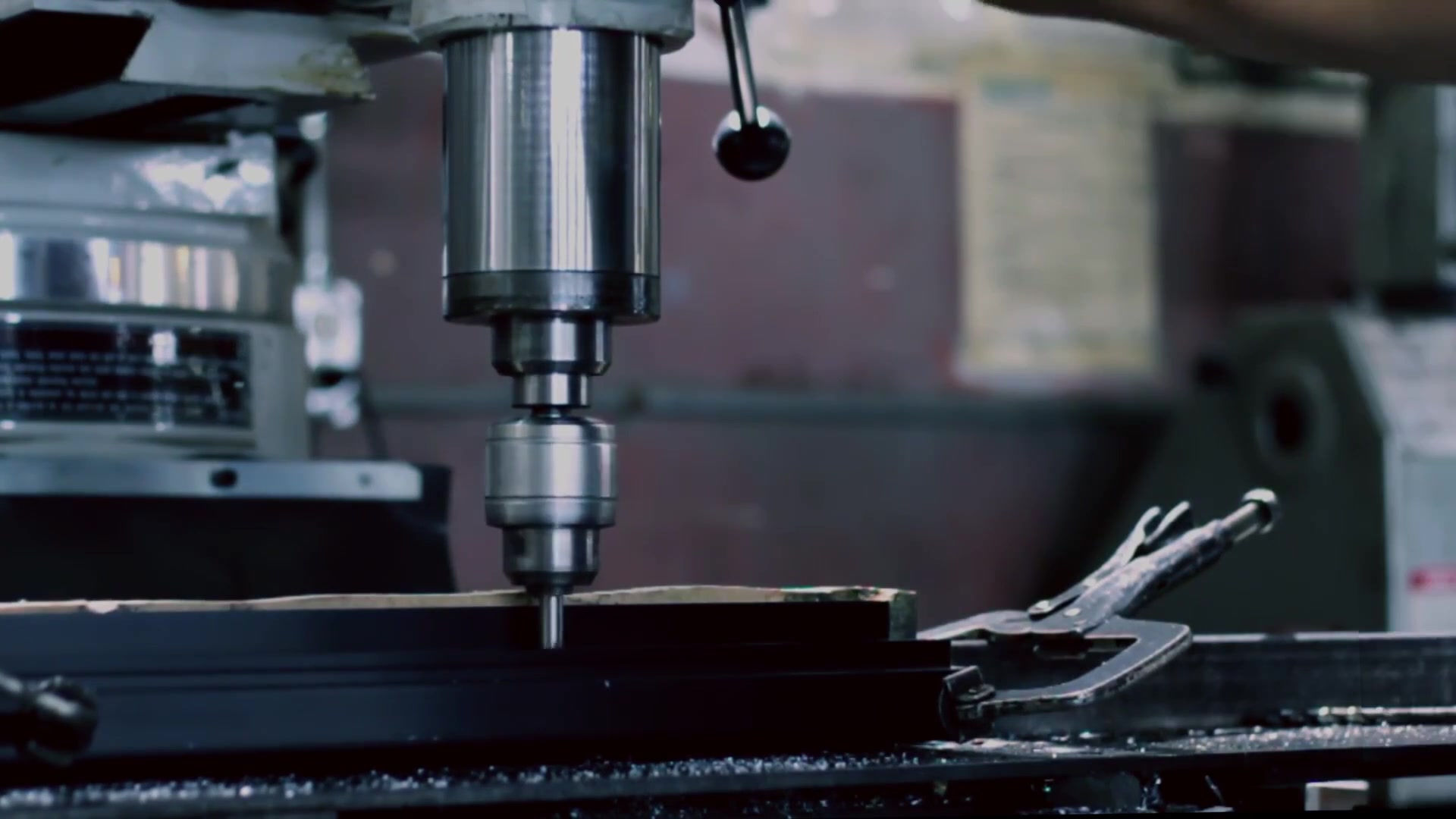
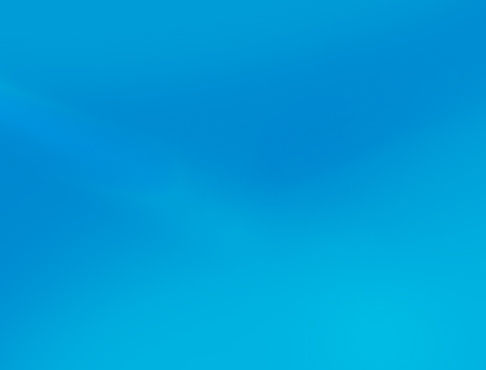
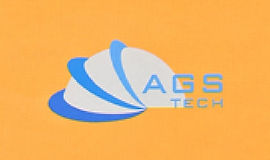
Globaler kundenspezifischer Hersteller, Integrator, Konsolidierer, Outsourcing-Partner für eine Vielzahl von Produkten und Dienstleistungen.
Wir sind Ihre One-Stop-Quelle für Fertigung, Fertigung, Engineering, Konsolidierung, Integration, Outsourcing von kundenspezifisch gefertigten und handelsüblichen Produkten und Dienstleistungen.
Wählen Sie Ihre Sprache
-
Kundenspezifische Fertigung
-
Nationale und globale Auftragsfertigung
-
Produktions-Outsourcing
-
Nationale und globale Beschaffung
-
Konsolidierung
-
Engineering-Integration
-
Technische Dienstleistungen
Funktionelle Beschichtungen / Dekorative Beschichtungen / Dünnschicht / Dickschicht
A COATING ist eine Beschichtung, die auf die Oberfläche eines Objekts aufgebracht wird. Coatings can be in the form of THIN FILM (less than 1 micron thick) or THICK FILM ( über 1 Mikron dick). Je nach Verwendungszweck der Beschichtung können wir Ihnen DECORATIVE COATINGS und/oder FUNCTIONAL COATINGS oder beides anbieten. Manchmal bringen wir funktionelle Beschichtungen auf, um die Oberflächeneigenschaften des Substrats zu verändern, wie z. B. Haftung, Benetzbarkeit, Korrosionsbeständigkeit oder Verschleißfestigkeit. In einigen anderen Fällen, wie z. B. bei der Herstellung von Halbleitergeräten, tragen wir die Funktionsbeschichtungen auf, um eine völlig neue Eigenschaft wie Magnetisierung oder elektrische Leitfähigkeit hinzuzufügen, die zu einem wesentlichen Bestandteil des Endprodukts werden.
Unsere beliebtesten FUNCTIONAL COATINGS sind:
Klebebeschichtungen: Beispiele sind Klebeband, Bügelgewebe. Andere funktionelle Haftbeschichtungen werden aufgetragen, um die Hafteigenschaften zu verändern, wie z. B. antihaftbeschichtete PTFE-Kochpfannen, Grundierungen, die eine gute Haftung nachfolgender Beschichtungen fördern.
Tribologische Beschichtungen: Diese funktionellen Beschichtungen beziehen sich auf die Wirkprinzipien Reibung, Schmierung und Verschleiß. Jedes Produkt, bei dem ein Material über ein anderes gleitet oder reibt, ist von komplexen tribologischen Wechselwirkungen betroffen. Produkte wie Hüftimplantate und andere künstliche Prothesen werden auf bestimmte Weise geschmiert, während andere Produkte ungeschmiert sind, wie bei Hochtemperatur-Gleitkomponenten, bei denen herkömmliche Schmiermittel nicht verwendet werden können. Als Verschleißschutz für solche gleitenden mechanischen Teile hat sich die Bildung von verdichteten Oxidschichten erwiesen. Tribologische Funktionsbeschichtungen haben enorme Vorteile in der Industrie, da sie den Verschleiß von Maschinenelementen minimieren, Verschleiß und Toleranzabweichungen in Fertigungswerkzeugen wie Gesenken und Formen minimieren, den Energiebedarf minimieren und Maschinen und Anlagen energieeffizienter machen.
Optische Beschichtungen: Beispiele sind Antireflexbeschichtungen (AR), reflektierende Beschichtungen für Spiegel, UV-absorbierende Beschichtungen zum Schutz der Augen oder zur Verlängerung der Lebensdauer des Substrats, Tönungen, die bei einigen farbigen Beleuchtungen verwendet werden, getönte Verglasungen und Sonnenbrillen.
Katalytische Beschichtungen wie sie auf selbstreinigendem Glas aufgetragen werden.
Lichtempfindliche Beschichtungen werden zur Herstellung von Produkten wie Fotofilmen verwendet
Schutzbeschichtungen: Farben können neben dem dekorativen Zweck auch als Schutz der Produkte angesehen werden. Harte Antikratzbeschichtungen auf Kunststoffen und anderen Materialien sind eine unserer am häufigsten verwendeten funktionellen Beschichtungen, um Kratzer zu reduzieren, die Verschleißfestigkeit zu verbessern usw. Sehr beliebt sind auch Korrosionsschutzbeschichtungen wie Galvanik. Andere schützende Funktionsbeschichtungen werden auf wasserdichte Stoffe und Papiere aufgebracht, antimikrobielle Oberflächenbeschichtungen auf chirurgische Instrumente und Implantate.
Hydrophile / hydrophobe Beschichtungen: Benetzende (hydrophile) und nicht benetzende (hydrophobe) funktionelle Dünn- und Dickschichten sind wichtig für Anwendungen, bei denen eine Wasseraufnahme entweder erwünscht oder unerwünscht ist. Mit fortschrittlicher Technologie können wir Ihre Produktoberflächen verändern, um sie entweder leicht benetzbar oder unbenetzbar zu machen. Typische Anwendungen sind Textilien, Verbände, Lederstiefel, pharmazeutische oder chirurgische Produkte. Hydrophile Natur bezieht sich auf eine physikalische Eigenschaft eines Moleküls, das sich vorübergehend mit Wasser (H2O) durch Wasserstoffbindung verbinden kann. Dies ist thermodynamisch günstig und macht diese Moleküle nicht nur in Wasser, sondern auch in anderen polaren Lösungsmitteln löslich. Hydrophile und hydrophobe Moleküle sind auch als polare Moleküle bzw. unpolare Moleküle bekannt.
Magnetische Beschichtungen: Diese funktionellen Beschichtungen verleihen Produkten magnetische Eigenschaften, wie es bei magnetischen Disketten, Kassetten, Magnetstreifen, magneto-optischen Speichern, induktiven Aufzeichnungsmedien, Magnetoresist-Sensoren und Dünnschichtköpfen der Fall ist. Magnetische Dünnfilme sind Folien aus magnetischem Material mit einer Dicke von wenigen Mikrometern oder weniger, die hauptsächlich in der Elektronikindustrie verwendet werden. Magnetische Dünnfilme können in der Anordnung ihrer Atome einkristalline, polykristalline, amorphe oder mehrlagige Funktionsschichten sein. Es werden sowohl ferro- als auch ferrimagnetische Folien verwendet. Bei den ferromagnetischen Funktionsschichten handelt es sich in der Regel um übergangsmetallbasierte Legierungen. Beispielsweise ist Permalloy eine Nickel-Eisen-Legierung. Die ferrimagnetischen funktionellen Beschichtungen wie Granate oder die amorphen Filme enthalten Übergangsmetalle wie Eisen oder Kobalt und seltene Erden, und die ferrimagnetischen Eigenschaften sind in magnetooptischen Anwendungen vorteilhaft, wo ein niedriges magnetisches Gesamtmoment ohne eine signifikante Änderung der Curie-Temperatur erreicht werden kann . Einige Sensorelemente funktionieren nach dem Prinzip der Änderung elektrischer Eigenschaften, beispielsweise des elektrischen Widerstands, mit einem Magnetfeld. Nach diesem Prinzip funktioniert in der Halbleitertechnik der in der Plattenspeichertechnik eingesetzte Magnetoresistkopf. Sehr große Magnetoresistsignale (Riesenmagnetowiderstand) werden in magnetischen Mehrfachschichten und Verbundwerkstoffen beobachtet, die ein magnetisches und nichtmagnetisches Material enthalten.
Elektrische oder elektronische Beschichtungen: Diese funktionellen Beschichtungen verleihen Produkten wie Widerständen elektrische oder elektronische Eigenschaften wie Leitfähigkeit, Isolationseigenschaften wie im Fall von Magnetdrahtbeschichtungen, die in Transformatoren verwendet werden.
DEKORATIVE BESCHICHTUNGEN: Wenn wir von dekorativen Beschichtungen sprechen, sind die Möglichkeiten nur durch Ihre Vorstellungskraft begrenzt. Sowohl Dick- als auch Dünnschichtbeschichtungen wurden in der Vergangenheit erfolgreich entwickelt und auf die Produkte unserer Kunden aufgebracht. Unabhängig von der Schwierigkeit in der geometrischen Form und dem Material des Substrats und den Anwendungsbedingungen sind wir immer in der Lage, die chemischen, physikalischen Aspekte wie den genauen Pantone-Farbcode und die Anwendungsmethode für Ihre gewünschten dekorativen Beschichtungen zu formulieren. Auch komplexe Muster mit Formen oder unterschiedlichen Farben sind möglich. Wir können Ihre Kunststoff-Polymer-Teile metallisch aussehen lassen. Wir können Profile mit verschiedenen Mustern eloxieren und es sieht nicht einmal eloxiert aus. Wir können ein seltsam geformtes Teil spiegeln. Darüber hinaus können dekorative Beschichtungen formuliert werden, die gleichzeitig auch als funktionale Beschichtungen fungieren. Jede der unten erwähnten Dünn- und Dickschichtabscheidungstechniken, die für funktionale Beschichtungen verwendet werden, kann für dekorative Beschichtungen eingesetzt werden. Hier sind einige unserer beliebten dekorativen Beschichtungen:
- Dekorative PVD-Dünnschichtbeschichtungen
- Galvanisierte dekorative Beschichtungen
- CVD- und PECVD-Dünnschicht-Dekorbeschichtungen
- Dekorative Beschichtungen durch thermische Verdampfung
- Dekorative Beschichtung von Rolle zu Rolle
- Dekorative E-Beam-Oxid-Interferenzbeschichtungen
- Ionenplattierung
- Kathodische Lichtbogenverdampfung für dekorative Beschichtungen
- PVD + Photolithographie, schwere Vergoldung auf PVD
- Aerosolbeschichtungen für die Glasfärbung
- Anlaufschutzbeschichtung
- Dekorative Kupfer-Nickel-Chrom-Systeme
- Dekorative Pulverbeschichtung
- Dekorative Malerei, kundenspezifische Farbformulierungen mit Pigmenten, Füllstoffen, kolloidalem Silica-Dispergiermittel usw.
Wenn Sie sich mit Ihren Anforderungen an dekorative Beschichtungen an uns wenden, können wir Ihnen unser Gutachten erstellen. Wir verfügen über fortschrittliche Tools wie Farblesegeräte, Farbkomparatoren usw. um eine gleichbleibende Qualität Ihrer Beschichtungen zu gewährleisten.
DÜNN- UND DICKSCHICHTBESCHICHTUNGSVERFAHREN: Hier sind die am weitesten verbreiteten unserer Techniken.
Galvanik / Chemische Beschichtung (Hartchrom, chemisches Nickel)
Galvanisieren ist der Prozess des Plattierens eines Metalls auf ein anderes durch Hydrolyse zu dekorativen Zwecken, zum Korrosionsschutz eines Metalls oder zu anderen Zwecken. Durch Galvanisieren können wir kostengünstige Metalle wie Stahl oder Zink oder Kunststoffe für den Hauptteil des Produkts verwenden und dann verschiedene Metalle auf der Außenseite in Form eines Films aufbringen, um das Aussehen, den Schutz und andere gewünschte Eigenschaften des Produkts zu erzielen. Das stromlose Plattieren, auch bekannt als chemisches Plattieren, ist ein nicht-galvanisches Plattierungsverfahren, das mehrere gleichzeitige Reaktionen in einer wässrigen Lösung beinhaltet, die ohne die Verwendung von externer elektrischer Energie ablaufen. Die Reaktion kommt zustande, wenn Wasserstoff durch ein Reduktionsmittel freigesetzt und oxidiert wird, wodurch eine negative Ladung auf der Oberfläche des Teils erzeugt wird. Vorteile dieser dünnen und dicken Schichten sind gute Korrosionsbeständigkeit, niedrige Verarbeitungstemperatur, Abscheidungsmöglichkeit in Bohrungen, Schlitzen etc. Nachteile sind die begrenzte Auswahl an Beschichtungsmaterialien, relativ weiche Beschaffenheit der Beschichtungen, umweltbelastende Behandlungsbäder, die benötigt werden einschließlich Chemikalien wie Cyanid, Schwermetalle, Fluoride, Öle, begrenzte Genauigkeit der Oberflächennachbildung.
Diffusion Processes (Nitrieren, Nitrocarburieren, Borieren, Phosphatieren etc.)
In Wärmebehandlungsöfen stammen die diffundierten Elemente normalerweise von Gasen, die bei hohen Temperaturen mit den Metalloberflächen reagieren. Dies kann eine reine thermische und chemische Reaktion als Folge der thermischen Dissoziation der Gase sein. In einigen Fällen stammen diffundierte Elemente von Festkörpern. Die Vorteile dieser thermochemischen Beschichtungsverfahren sind gute Korrosionsbeständigkeit, gute Reproduzierbarkeit. Die Nachteile sind relativ weiche Beschichtungen, begrenzte Auswahl an Grundmaterial (das zum Nitrieren geeignet sein muss), lange Verarbeitungszeiten, damit verbundene Umwelt- und Gesundheitsgefährdung, erforderliche Nachbehandlung.
CVD (chemische Dampfabscheidung)
CVD ist ein chemischer Prozess, der zur Herstellung hochwertiger, leistungsstarker, fester Beschichtungen verwendet wird. Das Verfahren erzeugt auch dünne Filme. Bei einer typischen CVD werden die Substrate einem oder mehreren flüchtigen Vorläufern ausgesetzt, die auf der Substratoberfläche reagieren und/oder sich zersetzen, um den gewünschten dünnen Film zu erzeugen. Vorteile dieser dünnen und dicken Schichten sind ihre hohe Verschleißfestigkeit, das Potenzial, dickere Beschichtungen wirtschaftlich herzustellen, die Eignung für Bohrungen, Schlitze usw. Nachteile von CVD-Prozessen sind ihre hohen Verarbeitungstemperaturen, die Schwierigkeit oder Unmöglichkeit von Beschichtungen mit mehreren Metallen (z. B. TiAlN), das Verrunden von Kanten, der Einsatz von umweltgefährdenden Chemikalien.
PACVD / PECVD (Plasmaunterstützte chemische Gasphasenabscheidung)
PACVD wird auch als PECVD bezeichnet und steht für Plasma Enhanced CVD. Während bei einem PVD-Beschichtungsprozess die Dünn- und Dickschichtmaterialien aus einer festen Form verdampft werden, erfolgt die Beschichtung bei PECVD aus einer Gasphase. Vorläufergase werden im Plasma gecrackt, um für die Beschichtung verfügbar zu werden. Vorteile dieser Dünn- und Dickschichtabscheidungstechnik sind, dass im Vergleich zu CVD deutlich niedrigere Prozesstemperaturen möglich sind, es werden präzise Beschichtungen abgeschieden. Nachteile von PACVD sind, dass es nur bedingt für Bohrungen, Schlitze etc. geeignet ist.
PVD (Physical Vapour Deposition)
PVD-Prozesse sind eine Vielzahl von rein physikalischen Vakuumabscheidungsverfahren, die verwendet werden, um Dünnfilme durch Kondensation einer verdampften Form des gewünschten Filmmaterials auf Werkstückoberflächen abzuscheiden. Sputtern und Aufdampfbeschichtungen sind Beispiele für PVD. Vorteile: keine umweltschädlichen Stoffe und Emissionen, große Vielfalt an Beschichtungen herstellbar, Beschichtungstemperaturen unterhalb der Wärmeendtemperatur der meisten Stähle, exakt reproduzierbare dünne Beschichtungen, hohe Verschleißfestigkeit, niedriger Reibwert. Nachteile sind Bohrungen, Schlitze ...etc. kann nur bis zu einer Tiefe beschichtet werden, die dem Durchmesser oder der Breite der Öffnung entspricht, korrosionsbeständig nur unter bestimmten Bedingungen, und um gleichmäßige Schichtdicken zu erhalten, müssen die Teile während der Beschichtung gedreht werden.
Die Haftung von funktionalen und dekorativen Beschichtungen ist substratabhängig. Darüber hinaus hängt die Lebensdauer von Dünn- und Dickschichtbeschichtungen von Umgebungsparametern wie Feuchtigkeit, Temperatur usw. ab. Bevor Sie eine funktionale oder dekorative Beschichtung in Betracht ziehen, fragen Sie uns daher nach unserer Meinung. Wir können die am besten geeigneten Beschichtungsmaterialien und Beschichtungstechniken auswählen, die zu Ihren Substraten und Ihrer Anwendung passen, und sie unter strengsten Qualitätsstandards abscheiden. Wenden Sie sich an AGS-TECH Inc., um Einzelheiten zu den Möglichkeiten zur Abscheidung von Dünn- und Dickfilmen zu erfahren. Benötigen Sie Unterstützung bei der Gestaltung? Sie benötigen Prototypen? Benötigen Sie Massenfertigung? Wir sind hier, um dir zu helfen.