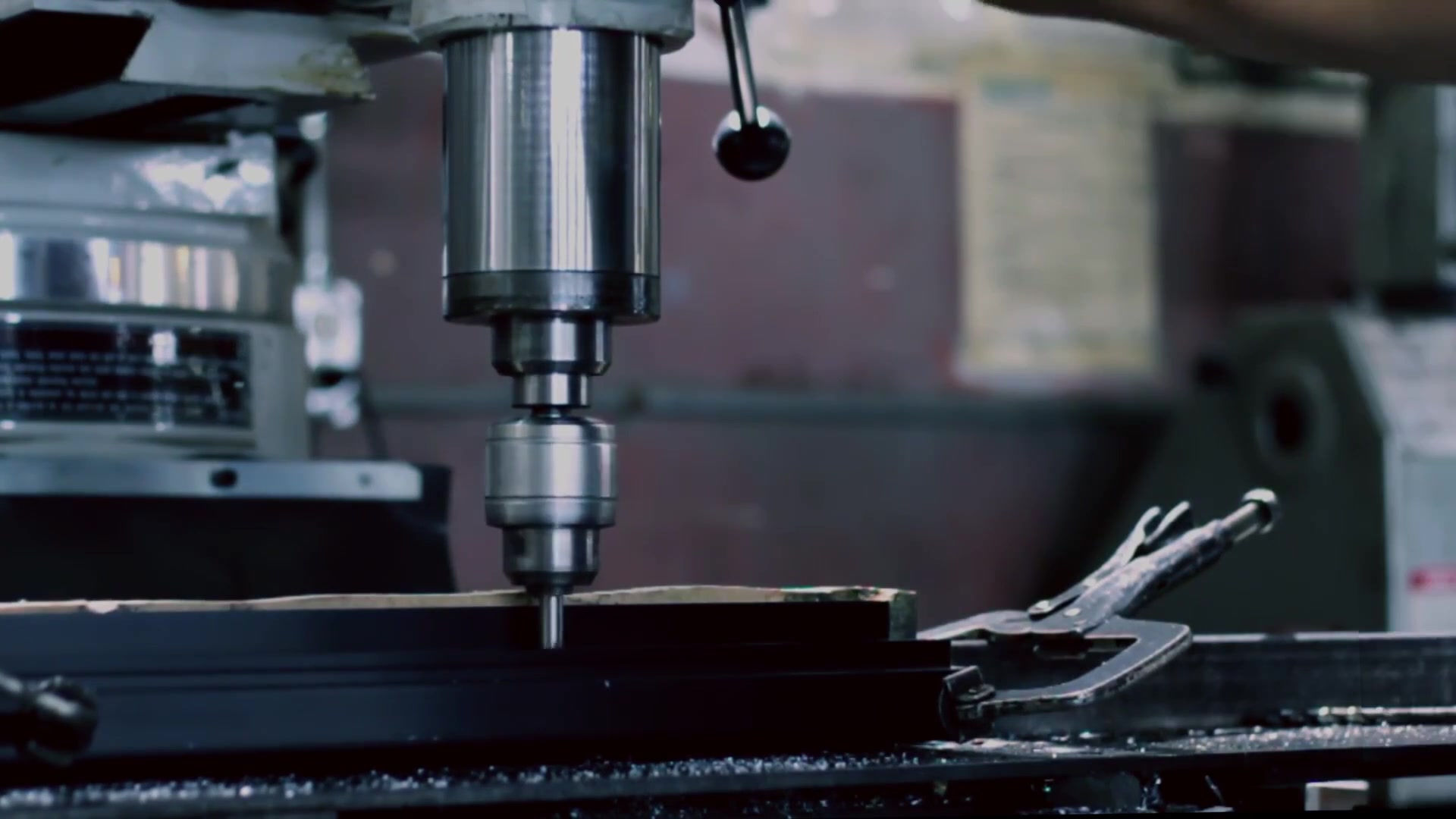
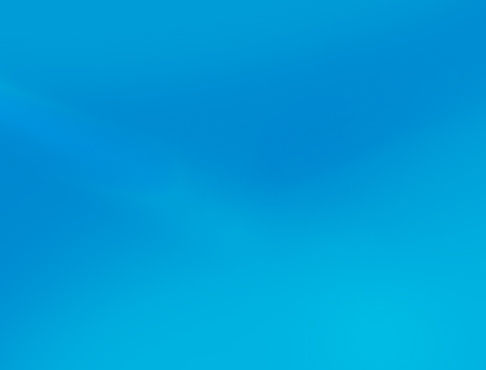
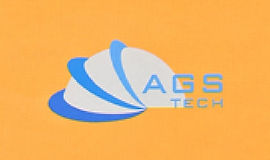
Globaler kundenspezifischer Hersteller, Integrator, Konsolidierer, Outsourcing-Partner für eine Vielzahl von Produkten und Dienstleistungen.
Wir sind Ihre One-Stop-Quelle für Fertigung, Fertigung, Engineering, Konsolidierung, Integration, Outsourcing von kundenspezifisch gefertigten und handelsüblichen Produkten und Dienstleistungen.
Wählen Sie Ihre Sprache
-
Kundenspezifische Fertigung
-
Nationale und globale Auftragsfertigung
-
Produktions-Outsourcing
-
Nationale und globale Beschaffung
-
Konsolidierung
-
Engineering-Integration
-
Technische Dienstleistungen
Die Arten der Glasherstellung, die wir anbieten, sind Behälterglas, Glasblasen, Glasfasern und Rohre und Stäbe, Haushalts- und Industrieglaswaren, Lampen und Glühbirnen, Präzisionsglasformen, optische Komponenten und Baugruppen, Flach-, Flach- und Floatglas. Wir führen sowohl manuelles als auch maschinelles Formen durch.
Unsere beliebten Herstellungsverfahren für technische Keramik sind Gesenkpressen, isostatisches Pressen, heißisostatisches Pressen, Heißpressen, Schlickerguss, Bandguss, Extrusion, Spritzguss, Grünbearbeitung, Sintern oder Brennen, Diamantschleifen, hermetische Anordnungen.
Wir empfehlen Ihnen, hier zu klicken
LADEN Sie unsere schematischen Darstellungen von Glasformungs- und Formgebungsprozessen von AGS-TECH Inc. HERUNTER.
Diese herunterladbaren Dateien mit Fotos und Skizzen helfen Ihnen, die Informationen, die wir Ihnen unten zur Verfügung stellen, besser zu verstehen.
• HERSTELLUNG VON BEHÄLTERGLAS: Wir verfügen über automatisierte PRESS-and-Blow- sowie Blow-and-Blow-Linien für die Herstellung. Beim Blas- und Blasverfahren lassen wir einen Tropfen in die Rohlingform fallen und formen den Hals, indem wir von oben einen Druckluftstoß anwenden. Unmittelbar danach wird ein zweites Mal Druckluft aus der anderen Richtung durch den Behälterhals geblasen, um den Vorformling der Flasche zu bilden. Dieser Vorformling wird dann in die eigentliche Form überführt, zum Erweichen erneut erhitzt und mit Druckluft beaufschlagt, um dem Vorformling seine endgültige Behälterform zu geben. Genauer gesagt wird es unter Druck gesetzt und gegen die Wände des Blasformhohlraums gedrückt, um seine gewünschte Form anzunehmen. Abschließend wird der hergestellte Glasbehälter zum anschließenden Wiedererhitzen und Abbauen von Spannungen, die während des Formens entstanden sind, in einen Temperofen überführt und kontrolliert abgekühlt. Beim Press-Blas-Verfahren werden geschmolzene Glasposten in eine Vorform (Rohling) gegeben und in die Vorform (Rohling) gepresst. Anschließend werden die Rohlinge in Blasformen überführt und ähnlich wie oben unter „Blas- und Blasprozess“ beschrieben geblasen. Nachfolgende Schritte wie Glühen und Spannungsabbau sind ähnlich oder gleich.
• GLASBLASEN: Wir stellen Glasprodukte her, indem wir sowohl herkömmliches Handblasen als auch Druckluft mit automatisierten Geräten verwenden. Für einige Aufträge ist konventionelles Blasen erforderlich, wie z. B. Projekte mit Glaskunstwerken oder Projekte, die eine kleinere Anzahl von Teilen mit losen Toleranzen erfordern, Prototyping / Demo-Projekte usw. Beim herkömmlichen Glasblasen wird ein hohles Metallrohr in einen Topf mit geschmolzenem Glas getaucht und das Rohr gedreht, um eine gewisse Menge des Glasmaterials zu sammeln. Das an der Rohrspitze gesammelte Glas wird auf Flacheisen gerollt, wie gewünscht geformt, verlängert, erneut erhitzt und mit Luft geblasen. Wenn es fertig ist, wird es in eine Form eingesetzt und Luft wird eingeblasen. Der Formhohlraum ist nass, um einen Kontakt des Glases mit Metall zu vermeiden. Der Wasserfilm wirkt wie ein Kissen zwischen ihnen. Das manuelle Blasen ist ein arbeitsintensiver, langsamer Prozess und nur für Prototypen oder hochwertige Artikel geeignet, nicht für kostengünstige Stückzahlen in hohen Stückzahlen.
• HERSTELLUNG VON GLASWAREN FÜR DEN HAUSHALT UND DIE INDUSTRIE: Unter Verwendung verschiedener Arten von Glasmaterialien wird eine große Vielfalt an Glaswaren hergestellt. Einige Gläser sind hitzebeständig und für Laborglas geeignet, während andere gut genug sind, um viele Male Spülmaschinen zu überstehen und für die Herstellung von Haushaltsprodukten geeignet sind. Auf Westlake-Maschinen werden täglich zehntausende Trinkgläser produziert. Zur Vereinfachung wird geschmolzenes Glas durch Vakuum gesammelt und in Formen eingesetzt, um die Vorformen herzustellen. Dann wird Luft in die Formen geblasen, diese werden in eine andere Form überführt und erneut Luft geblasen und das Glas nimmt seine endgültige Form an. Wie beim Handblasen werden diese Formen mit Wasser feucht gehalten. Weiteres Strecken ist Teil des Endbearbeitungsvorgangs, bei dem der Hals geformt wird. Überschüssiges Glas wird abgebrannt. Danach folgt der oben beschriebene kontrollierte Wiederaufheiz- und Abkühlprozess.
• GLASROHR- UND STABFORMUNG: Die Hauptverfahren, die wir für die Herstellung von Glasrohren verwenden, sind die DANNER- und VELLO-Verfahren. Beim Danner-Verfahren fließt und fällt Glas aus einem Ofen auf eine geneigte Hülse aus feuerfesten Materialien. Die Hülse wird auf einer rotierenden Hohlwelle oder einem Blasrohr getragen. Das Glas wird dann um die Hülse gewickelt und bildet eine glatte Schicht, die die Hülse hinunter und über die Spitze des Schafts fließt. Bei der Rohrumformung wird Luft durch ein Blasrohr mit Hohlspitze geblasen, bei der Stabumformung verwenden wir massive Spitzen auf der Welle. Die Rohre oder Stäbe werden dann über Tragrollen gezogen. Die Abmessungen wie Wandstärke und Durchmesser der Glasrohre werden auf gewünschte Werte eingestellt, indem der Durchmesser der Hülse und der Blasluftdruck auf einen gewünschten Wert eingestellt werden, indem die Temperatur, die Glasfließgeschwindigkeit und die Ziehgeschwindigkeit eingestellt werden. Bei der Herstellung von Vello-Glasröhren hingegen wird Glas aus einem Ofen in eine Schüssel mit einem hohlen Dorn oder einer Glocke geleitet. Das Glas geht dann durch den Luftraum zwischen dem Dorn und der Schale und nimmt die Form einer Röhre an. Danach läuft es über Walzen zu einer Ziehmaschine und wird gekühlt. Am Ende der Kühlstrecke erfolgt der Zuschnitt und die Endbearbeitung. Die Rohrabmessungen können wie beim Danner-Verfahren angepasst werden. Beim Vergleich des Danner- mit dem Vello-Prozess können wir sagen, dass der Vello-Prozess besser für die Produktion großer Mengen geeignet ist, während der Danner-Prozess möglicherweise besser für präzise Rohrbestellungen mit kleinerem Volumen geeignet ist.
• VERARBEITUNG VON BLECH-, FLACH- UND FLOATGLAS: Wir haben große Mengen an Flachglas in Dicken von Submillimeterdicken bis zu mehreren Zentimetern. Unsere flachen Gläser sind von nahezu optischer Perfektion. Wir bieten Glas mit speziellen Beschichtungen wie optischen Beschichtungen an, bei denen die chemische Gasphasenabscheidungstechnik verwendet wird, um Beschichtungen wie Antireflexions- oder Spiegelbeschichtungen aufzubringen. Auch transparente leitfähige Beschichtungen sind üblich. Ebenfalls erhältlich sind hydrophobe oder hydrophile Beschichtungen auf Glas und Beschichtungen, die Glas selbstreinigend machen. Gehärtete, kugelsichere und laminierte Gläser sind weitere beliebte Artikel. Wir schneiden Glas in gewünschte Form mit gewünschten Toleranzen. Andere sekundäre Operationen wie das Biegen oder Biegen von Flachglas sind verfügbar.
• PRÄZISIONSGLASFORMEN: Wir verwenden diese Technik hauptsächlich zur Herstellung präziser optischer Komponenten, ohne dass teurere und zeitaufwändigere Techniken wie Schleifen, Läppen und Polieren erforderlich sind. Diese Technik reicht nicht immer aus, um das Beste aus den besten Optiken zu machen, aber in einigen Fällen, wie Konsumgütern, Digitalkameras, medizinischen Optiken, kann sie eine kostengünstigere gute Option für die Massenfertigung sein. Außerdem hat es einen Vorteil gegenüber den anderen Glasformungstechniken, wenn komplexe Geometrien erforderlich sind, wie im Fall von Asphären. Der Grundprozess beinhaltet das Beladen der Unterseite unserer Form mit dem Glasrohling, Evakuieren der Prozesskammer zur Sauerstoffentfernung, nahezu Schließen der Form, schnelles und isothermes Aufheizen von Form und Glas mit Infrarotlicht, weiteres Schließen der Formhälften langsames kontrolliertes Pressen des erweichten Glases auf die gewünschte Dicke und schließlich Abkühlen des Glases und Füllen der Kammer mit Stickstoff und Entnahme des Produkts. Präzise Temperaturkontrolle, Formschließabstand, Formschließkraft, Abstimmung der Ausdehnungskoeffizienten von Form und Glasmaterial sind dabei entscheidend.
• HERSTELLUNG VON OPTISCHEN GLASKOMPONENTEN UND BAUGRUPPEN: Neben dem Präzisionsglasformen gibt es eine Reihe wertvoller Verfahren, die wir zur Herstellung hochwertiger optischer Komponenten und Baugruppen für anspruchsvolle Anwendungen verwenden. Das Schleifen, Läppen und Polieren von Gläsern optischer Qualität in feinen Spezialschleifschlämmen ist eine Kunst und Wissenschaft zur Herstellung von optischen Linsen, Prismen, Planscheiben und mehr. Ebenheit, Welligkeit, Glätte und fehlerfreie optische Oberflächen erfordern viel Erfahrung mit solchen Prozessen. Kleine Änderungen in der Umgebung können zu Produkten führen, die nicht den Spezifikationen entsprechen, und die Fertigungslinie zum Stillstand bringen. Es gibt Fälle, in denen ein einziges Abwischen der optischen Oberfläche mit einem sauberen Tuch dazu führen kann, dass ein Produkt die Spezifikationen erfüllt oder den Test nicht besteht. Einige beliebte verwendete Glasmaterialien sind Quarzglas, Quarz, BK7. Auch die Montage solcher Komponenten erfordert spezialisierte Nischenerfahrung. Manchmal werden spezielle Klebstoffe verwendet. Manchmal ist jedoch eine Technik, die als optisches Kontaktieren bezeichnet wird, die beste Wahl und beinhaltet kein Material zwischen angebrachten optischen Gläsern. Es besteht aus physikalisch berührenden flachen Oberflächen, die ohne Klebstoff aneinander befestigt werden können. In einigen Fällen werden mechanische Abstandshalter, Präzisionsglasstäbe oder -kugeln, Klammern oder maschinell bearbeitete Metallkomponenten verwendet, um die optischen Komponenten in bestimmten Abständen und mit bestimmten geometrischen Orientierungen zueinander zusammenzubauen. Lassen Sie uns einige unserer beliebten Techniken zur Herstellung von High-End-Optiken untersuchen.
SCHLEIFEN & LÄPFEN & POLIEREN: Die grobe Form der optischen Komponente wird durch Schleifen eines Glasrohlings erhalten. Danach werden Läppen und Polieren ausgeführt, indem die rauen Oberflächen der optischen Komponenten gedreht und gegen Werkzeuge mit gewünschten Oberflächenformen gerieben werden. Zwischen die Optik und die Formwerkzeuge werden Schlämme mit winzigen Schleifpartikeln und Flüssigkeit gegossen. Die Korngrößen der Schleifmittel in solchen Aufschlämmungen können entsprechend dem gewünschten Grad an Ebenheit gewählt werden. Die Abweichungen kritischer optischer Oberflächen von gewünschten Formen werden in Form von Wellenlängen des verwendeten Lichts ausgedrückt. Unsere hochpräzisen Optiken haben Toleranzen von einem Zehntel einer Wellenlänge (Wellenlänge/10) oder noch engere sind möglich. Neben dem Oberflächenprofil werden die kritischen Oberflächen gescannt und auf andere Oberflächenmerkmale und Defekte wie Abmessungen, Kratzer, Späne, Vertiefungen, Flecken usw. untersucht. Die strenge Kontrolle der Umgebungsbedingungen in der Optikfertigung und umfangreiche Mess- und Prüfanforderungen mit modernster Ausrüstung machen diesen Industriezweig zu einem herausfordernden Industriezweig.
• SEKUNDÄRE PROZESSE IN DER GLASHERSTELLUNG: Auch hier sind uns bei den Sekundär- und Veredelungsprozessen von Glas nur Ihre Vorstellungskraft begrenzt. Hier listen wir einige davon auf:
-Beschichtungen auf Glas (optisch, elektrisch, tribologisch, thermisch, funktional, mechanisch...). Beispielsweise können wir die Oberflächeneigenschaften von Glas verändern, sodass es beispielsweise Wärme reflektiert, sodass Gebäudeinnenräume kühl bleiben, oder mithilfe von Nanotechnologie eine Seite infrarotabsorbierend machen. Dies trägt dazu bei, das Innere von Gebäuden warm zu halten, da die äußerste Glasschicht die Infrarotstrahlung im Inneren des Gebäudes absorbiert und ins Innere zurückstrahlt.
-Ätzung auf Glas
-Applied Ceramic Labeling (ACL)
-Gravur
-Flammpolieren
-Chemisches Polieren
-Färbung
HERSTELLUNG VON TECHNISCHER KERAMIK
• MATRIZENPRESSEN: Besteht aus einachsiger Verdichtung von körnigem Pulver, das in einer Matrize eingeschlossen ist
• HEISSPRESSEN: Ähnlich wie beim Matrizenpressen, jedoch mit zusätzlicher Temperatur zur Verbesserung der Verdichtung. Pulver oder verdichtete Vorform werden in eine Graphitmatrize gegeben und uniaxialer Druck ausgeübt, während die Matrize auf hohen Temperaturen wie 2000°C gehalten wird. Die Temperaturen können je nach Art des zu verarbeitenden Keramikpulvers unterschiedlich sein. Bei komplizierten Formen und Geometrien können andere Nachbearbeitungen wie Diamantschleifen erforderlich sein.
• ISOSTATISCHES PRESSEN: Körniges Pulver oder formgepresste Presslinge werden in luftdichte Behälter gegeben und dann in einen geschlossenen Druckbehälter mit darin enthaltener Flüssigkeit. Danach werden sie durch Erhöhen des Druckbehälterdrucks verdichtet. Die Flüssigkeit im Inneren des Gefäßes überträgt die Druckkräfte gleichmäßig über die gesamte Oberfläche des luftdichten Behälters. Das Material wird somit gleichmäßig verdichtet und nimmt die Form seines flexiblen Behälters sowie sein Innenprofil und seine Eigenschaften an.
• HEISSES ISOSTATISCHES PRESSEN: Ähnlich dem isostatischen Pressen, aber zusätzlich zur Druckgasatmosphäre sintern wir den Pressling bei hoher Temperatur. Heißisostatisches Pressen führt zu zusätzlicher Verdichtung und erhöhter Festigkeit.
• SCHMUTZGUSS / ABLAUFGUSS: Wir füllen die Form mit einer Suspension aus mikrometergroßen Keramikpartikeln und Trägerflüssigkeit. Diese Mischung wird als „Schlicker“ bezeichnet. Die Form hat Poren und daher wird die Flüssigkeit in der Mischung in die Form gefiltert. Als Ergebnis wird auf den Innenflächen der Form ein Guss gebildet. Nach dem Sintern können die Teile aus der Form genommen werden.
• BANDGIESSEN: Wir stellen Keramikbänder her, indem wir Keramikschlämme auf flache, sich bewegende Trägeroberflächen gießen. Die Aufschlämmungen enthalten Keramikpulver gemischt mit anderen Chemikalien für Bindungs- und Transportzwecke. Wenn die Lösungsmittel verdunsten, bleiben dichte und flexible Keramikschichten zurück, die je nach Wunsch geschnitten oder gerollt werden können.
• EXTRUSIONSFORMEN: Wie bei anderen Extrusionsverfahren wird eine weiche Mischung aus Keramikpulver mit Bindemitteln und anderen Chemikalien durch eine Düse geleitet, um ihre Querschnittsform anzunehmen, und wird dann auf die gewünschte Länge geschnitten. Der Prozess wird mit kalten oder erhitzten Keramikmischungen durchgeführt.
• NIEDERDRUCK-SPRITZGUSS: Wir bereiten eine Mischung aus Keramikpulver mit Bindemitteln und Lösungsmitteln vor und erhitzen es auf eine Temperatur, bei der es leicht gepresst und in den Werkzeughohlraum gedrückt werden kann. Sobald der Formzyklus abgeschlossen ist, wird das Teil ausgeworfen und die Bindechemikalie wird abgebrannt. Durch den Spritzguss können wir komplizierte Teile in großen Stückzahlen wirtschaftlich herstellen. Löcher , die einen winzigen Bruchteil eines Millimeters auf einer 10 mm dicken Wand ausmachen, sind möglich, Gewinde sind ohne weitere Bearbeitung möglich, Toleranzen von bis zu +/- 0,5 % sind möglich und sogar noch geringer, wenn Teile bearbeitet werden sind Wandstärken in der Größenordnung von 0,5 mm bis zu einer Länge von 12,5 mm ebenso möglich wie Wandstärken von 6,5 mm bis zu einer Länge von 150 mm.
• GRÜNE BEARBEITUNG: Mit den gleichen Metallbearbeitungswerkzeugen können wir gepresste Keramikmaterialien bearbeiten, während sie noch weich wie Kreide sind. Toleranzen von +/- 1% sind möglich. Für bessere Toleranzen verwenden wir Diamantschleifen.
• SINTERN oder BRENNEN: Sintern ermöglicht eine vollständige Verdichtung. Bei den Grünlingen tritt eine erhebliche Schwindung auf, dies ist jedoch kein großes Problem, da wir diese Dimensionsänderungen bei der Konstruktion des Teils und der Werkzeuge berücksichtigen. Pulverpartikel werden miteinander verbunden und die durch den Verdichtungsprozess induzierte Porosität wird weitgehend entfernt.
• DIAMANTSCHLEIFEN: Das härteste Material der Welt, „Diamant“, wird zum Schleifen von harten Materialien wie Keramik verwendet und es werden Präzisionsteile erhalten. Toleranzen im Mikrometerbereich und sehr glatte Oberflächen werden erreicht. Aufgrund des hohen Aufwands ziehen wir diese Technik nur dann in Betracht, wenn wir sie wirklich brauchen.
• HERMETISCHE VERBINDUNGEN sind solche, die praktisch keinen Austausch von Stoffen, Feststoffen, Flüssigkeiten oder Gasen zwischen Grenzflächen zulassen. Hermetische Versiegelung ist luftdicht. Zum Beispiel sind hermetische Elektronikgehäuse solche, die den empfindlichen Inneninhalt eines verpackten Geräts vor Feuchtigkeit, Verunreinigungen oder Gasen schützen. Nichts ist zu 100 % hermetisch, aber wenn wir von Hermetik sprechen, meinen wir praktisch, dass eine solche Hermetik vorliegt, dass die Leckrate so gering ist, dass die Geräte unter normalen Umgebungsbedingungen sehr lange sicher sind. Unsere hermetischen Baugruppen bestehen aus Metall-, Glas- und Keramikkomponenten, Metall-Keramik, Keramik-Metall-Keramik, Metall-Keramik-Metall, Metall-auf-Metall, Metall-Glas, Metall-Glas-Metall, Glas-Metall-Glas, Glas- Metall und Glas auf Glas und alle anderen Kombinationen von Metall-Glas-Keramik-Verbindungen. Wir können zum Beispiel die Keramikkomponenten mit Metall beschichten, damit sie fest mit anderen Komponenten in der Baugruppe verbunden werden können und eine hervorragende Dichtungsfähigkeit aufweisen. Wir haben das Know-how, optische Fasern oder Durchführungen mit Metall zu beschichten und sie an die Gehäuse zu löten oder zu löten, damit keine Gase in die Gehäuse gelangen oder austreten. Daher werden sie zur Herstellung von Elektronikgehäusen verwendet, um empfindliche Geräte zu verkapseln und vor der äußeren Atmosphäre zu schützen. Neben ihren hervorragenden Dichtungseigenschaften sind weitere Eigenschaften wie Wärmeausdehnungskoeffizient, Verformungsbeständigkeit, nicht ausgasende Eigenschaften, sehr lange Lebensdauer, nichtleitende Eigenschaften, Wärmeisolationseigenschaften, antistatische Eigenschaften usw. machen Glas- und Keramikwerkstoffe zur ersten Wahl für bestimmte Anwendungen. Informationen zu unserer Anlage zur Herstellung von Keramik-Metall-Fittings, hermetischer Abdichtung, Vakuumdurchführungen, Hoch- und Ultrahochvakuum- und Fluidsteuerungskomponenten finden Sie hier:Hermetische Komponenten Fabrikbroschüre