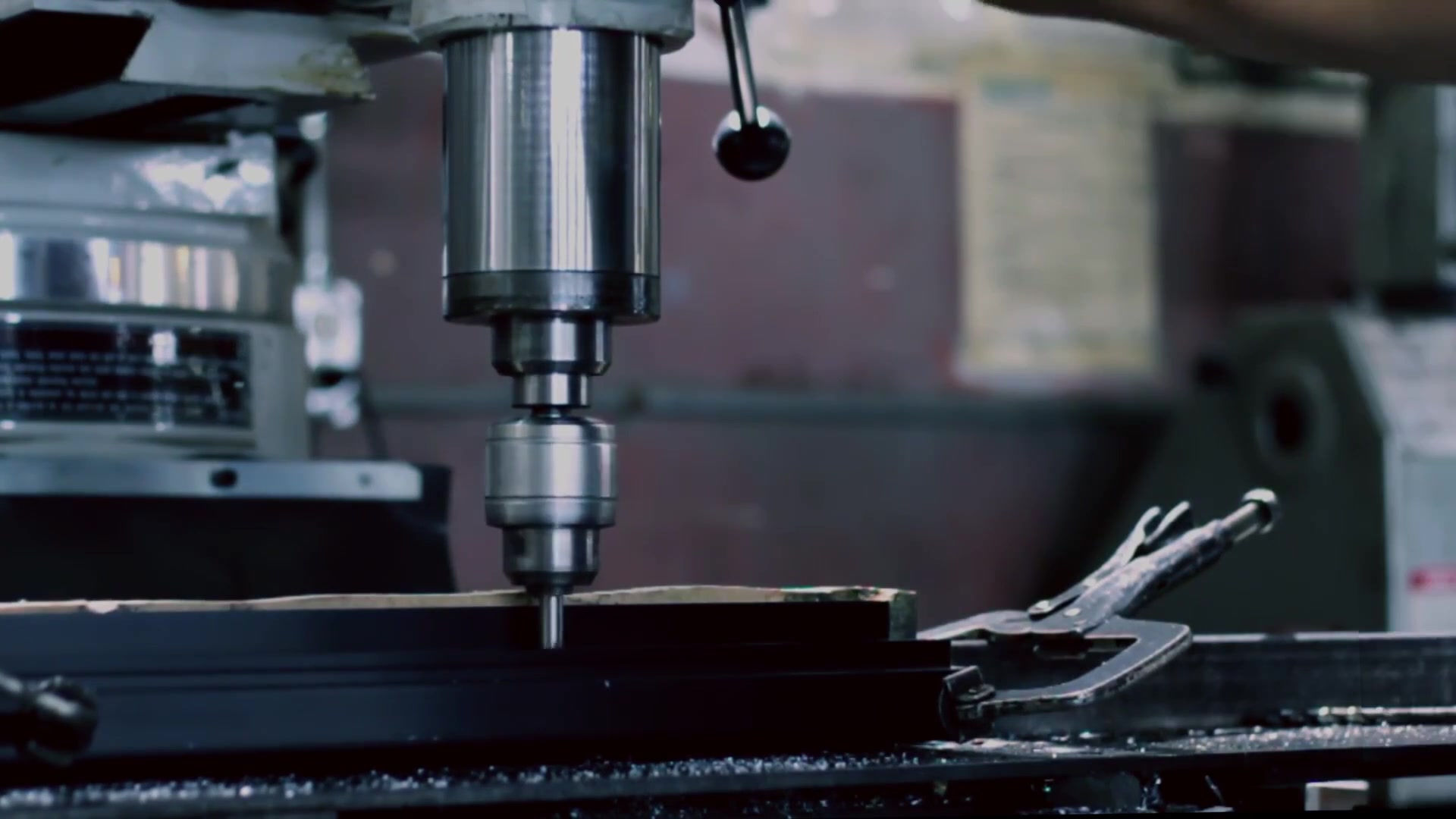
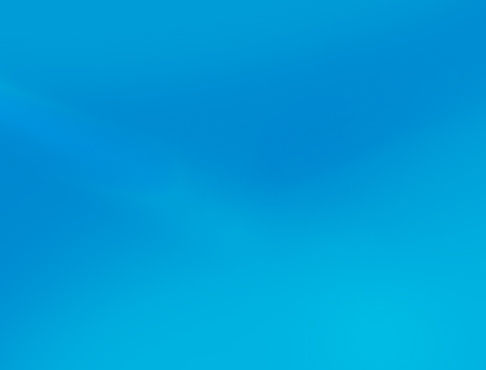
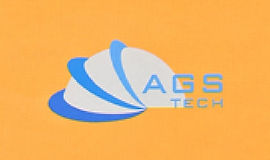
Globaler kundenspezifischer Hersteller, Integrator, Konsolidierer, Outsourcing-Partner für eine Vielzahl von Produkten und Dienstleistungen.
Wir sind Ihre One-Stop-Quelle für Fertigung, Fertigung, Engineering, Konsolidierung, Integration, Outsourcing von kundenspezifisch gefertigten und handelsüblichen Produkten und Dienstleistungen.
Wählen Sie Ihre Sprache
-
Kundenspezifische Fertigung
-
Nationale und globale Auftragsfertigung
-
Produktions-Outsourcing
-
Nationale und globale Beschaffung
-
Konsolidierung
-
Engineering-Integration
-
Technische Dienstleistungen
Die Arten von METALLSCHMIEDE-Prozessen, die wir anbieten, sind Warm- und Kaltgesenk, offenes Gesenk und geschlossenes Gesenk, Prägegesenk und gratfreie Schmiedeteile, Cogging, Walken, Kanten und Präzisionsschmieden, Near-Net-Shape, Heading , Gesenkschmieden, Stauchschmieden, Wälzfräsen aus Metall, Press- und Roll- sowie Radial- und Orbital- und Ring- und Isothermschmiedestücke, Prägen, Nieten, Schmieden von Metallkugeln, Metallstanzen, Kalibrieren, Schmieden mit hoher Energierate.
Unsere PULVERMETALLURGIE- und PULVERVERARBEITUNGS-Techniken sind Pulverpressen und -sintern, Imprägnieren, Infiltrieren, heiß- und kaltisostatisches Pressen, Metallspritzguss, Walzenverdichtung, Pulverwalzen, Pulverextrusion, loses Sintern, Funkensintern, Heißpressen.
Wir empfehlen Ihnen, hier zu klicken
LADEN Sie unsere schematischen Darstellungen von Schmiedeprozessen von AGS-TECH Inc. HERUNTER
Diese herunterladbaren Dateien mit Fotos und Skizzen helfen Ihnen, die Informationen, die wir Ihnen unten zur Verfügung stellen, besser zu verstehen.
Beim Metallschmieden werden Druckkräfte aufgebracht und das Material verformt und die gewünschte Form erhalten. Die gebräuchlichsten Schmiedematerialien in der Industrie sind Eisen und Stahl, aber auch zahlreiche andere wie Aluminium, Kupfer, Titan, Magnesium werden häufig geschmiedet. Geschmiedete Metallteile haben neben versiegelten Rissen und geschlossenen Hohlräumen verbesserte Kornstrukturen, wodurch die Festigkeit der durch dieses Verfahren erhaltenen Teile höher ist. Beim Schmieden entstehen Teile, die für ihr Gewicht deutlich stärker sind als Teile, die durch Gießen oder maschinelle Bearbeitung hergestellt werden. Da geschmiedete Teile geformt werden, indem das Metall in seine endgültige Form fließt, nimmt das Metall eine gerichtete Kornstruktur an, die für die überlegene Festigkeit der Teile verantwortlich ist. Mit anderen Worten, durch Schmiedeverfahren erhaltene Teile zeigen bessere mechanische Eigenschaften im Vergleich zu einfachen gegossenen oder maschinell bearbeiteten Teilen. Das Gewicht von Metallschmiedestücken kann von kleinen, leichten Teilen bis zu Hunderttausenden von Pfund reichen. Wir fertigen Schmiedeteile hauptsächlich für mechanisch anspruchsvolle Anwendungen, bei denen Teile wie Autoteile, Zahnräder, Arbeitswerkzeuge, Handwerkzeuge, Turbinenwellen, Motorradgetriebe hohen Belastungen ausgesetzt sind. Da die Werkzeug- und Rüstkosten relativ hoch sind, empfehlen wir dieses Herstellungsverfahren nur für die Großserienfertigung und für Kleinserien, aber hochwertige kritische Komponenten wie Fahrwerke für die Luft- und Raumfahrt. Abgesehen von den Werkzeugkosten können die Fertigungsvorlaufzeiten für geschmiedete Teile in großen Mengen im Vergleich zu einigen einfach bearbeiteten Teilen länger sein, aber die Technik ist entscheidend für Teile, die eine außergewöhnliche Festigkeit erfordern, wie Schrauben, Muttern, Spezialanwendungen Verbindungselemente, Automobil, Gabelstapler, Kranteile.
• Gesenk- und Gesenkschmieden: Warmgesenkschmieden wird, wie der Name schon sagt, bei hohen Temperaturen durchgeführt, daher ist die Duktilität hoch und die Festigkeit des Materials gering. Dies erleichtert ein leichtes Verformen und Schmieden. Im Gegensatz dazu wird das Kaltgesenkschmieden bei niedrigeren Temperaturen durchgeführt und erfordert höhere Kräfte, was zu Kaltverfestigung, besserer Oberflächengüte und Genauigkeit der hergestellten Teile führt.
• Freiform- und Gesenkschmieden: Beim Freiformschmieden beschränken die Gesenke das zu komprimierende Material nicht, während beim Gesenkschmieden die Hohlräume innerhalb der Gesenke den Materialfluss einschränken, während es in die gewünschte Form geschmiedet wird. UPSET FORGING oder auch UPSETTING genannt, was eigentlich nicht dasselbe, aber ein sehr ähnlicher Prozess ist, ist ein Open-Die-Prozess, bei dem das Werkstück zwischen zwei flachen Gesenken eingeklemmt wird und eine Druckkraft seine Höhe verringert. Da die Höhe is reduziert ist, nimmt die Werkstückbreite zu. HEADING, ein Stauchschmiedeverfahren, beinhaltet zylindrisches Material, das an seinem Ende gestaucht und sein Querschnitt lokal vergrößert wird. Beim Vortrieb wird das Material durch das Gesenk geführt, geschmiedet und dann auf Länge geschnitten. Der Betrieb ist in der Lage, große Mengen an Verbindungselementen schnell zu produzieren. Meistens handelt es sich um eine Kaltumformung, da sie zur Herstellung von Nagelenden, Schraubenenden, Muttern und Bolzen verwendet wird, bei denen das Material verstärkt werden muss. Ein weiterer Freiformprozess ist COGGING, bei dem das Werkstück in einer Reihe von Schritten geschmiedet wird, wobei jeder Schritt zu einer Kompression des Materials und der anschließenden Bewegung der Freiform entlang der Länge des Werkstücks führt. Bei jedem Schritt wird die Dicke verringert und die Länge um einen kleinen Betrag erhöht. Der Prozess ähnelt einem nervösen Studenten, der die ganze Zeit in kleinen Schritten auf seinen Bleistift beißt. Ein Prozess namens FULLERING ist eine weitere Freiformschmiedemethode, die wir häufig als früheren Schritt einsetzen, um das Material im Werkstück zu verteilen, bevor andere Metallschmiedevorgänge stattfinden. Wir verwenden es, wenn das Werkstück mehrere forging operationen erfordert. Im Betrieb verformen sich Matrizen mit konvexen Oberflächen und bewirken, dass Metall zu beiden Seiten herausfließt. Ein ähnlicher Prozess wie das Walken, KANTEN hingegen beinhaltet eine offene Matrize mit konkaven Oberflächen, um das Werkstück zu verformen. Das Kanten, auch ein vorbereitender Prozess für nachfolgende Schmiedeoperationen, lässt das Material von beiden Seiten in einen Bereich in der Mitte fließen. IMPRESSION DIE FORGING oder CLOSED DIE FORGING, wie es auch genannt wird, verwendet ein Gesenk / eine Form, die das Material komprimiert und seinen Fluss in sich selbst einschränkt. Das Werkzeug schließt sich und das Material nimmt die Form des Werkzeug-/Formnests an. PRÄZISIONSSCHMIEDEN, ein Prozess, der eine spezielle Ausrüstung und Form erfordert, produziert Teile ohne oder mit sehr wenig Grat. Mit anderen Worten, die Teile haben nahezu Endabmessungen. Bei diesem Vorgang wird eine gut kontrollierte Materialmenge sorgfältig in die Form eingeführt und positioniert. Wir setzen dieses Verfahren bei komplexen Formen mit dünnen Querschnitten, kleinen Toleranzen und Entformungswinkeln ein und wenn die Stückzahlen groß genug sind, um die Werkzeug- und Ausrüstungskosten zu rechtfertigen.
• FLASHLOSES SCHMIEDEN : Das Werkstück wird so in das Gesenk eingelegt, dass kein Material aus der Kavität fließen kann, um Grate zu bilden. Somit ist kein unerwünschter Blitzabgleich erforderlich. Es ist ein Präzisionsschmiedeprozess und erfordert daher eine genaue Kontrolle der verwendeten Materialmenge.
• METALLSCHMIEDEN oder RADIALSCHMIEDEN: Ein Werkstück wird in Umfangsrichtung von einem Gesenk beaufschlagt und geschmiedet. Ein Dorn kann auch verwendet werden, um die innere Werkstückgeometrie zu schmieden. Beim Stauchvorgang erhält das Werkstück typischerweise mehrere Hübe pro Sekunde. Typische Gegenstände, die durch Hämmern hergestellt werden, sind Werkzeuge mit spitzer Spitze, konische Stäbe, Schraubendreher.
• PIERCING VON METALL: Wir verwenden diesen Vorgang häufig als zusätzlichen Vorgang bei der Herstellung von Teilen. Durch Einstechen entsteht ein Loch oder eine Kavität auf der Werkstückoberfläche, ohne diese zu durchbrechen. Bitte beachten Sie, dass das Lochen anders ist als das Bohren, das zu einem Durchgangsloch führt.
• FRÄSEN: Ein Stempel mit der gewünschten Geometrie wird in das Werkstück gepresst und erzeugt eine Kavität mit der gewünschten Form. Wir nennen diesen Punsch ein HOB. Die Operation beinhaltet hohe Drücke und wird bei Kälte durchgeführt. Dadurch wird das Material kaltverformt und kaltverfestigt. Daher eignet sich dieses Verfahren sehr gut zur Herstellung von Formen, Gesenken und Kavitäten für andere Fertigungsverfahren. Sobald das Wälzfräser hergestellt ist, können problemlos viele identische Hohlräume hergestellt werden, ohne dass sie einzeln bearbeitet werden müssen.
• WALZENSCHMIEDEN oder WALZENFORMEN: Zwei gegenüberliegende Walzen werden verwendet, um das Metallteil zu formen. Das Werkstück wird in die Walzen eingeführt, die Walzen drehen sich und ziehen das Werkstück in den Spalt, das Werkstück wird dann durch den genuteten Teil der Walzen geführt und die Druckkräfte geben dem Material seine gewünschte Form. Es ist kein Walzprozess, sondern ein Schmiedeprozess, da es sich eher um einen diskreten als um einen kontinuierlichen Vorgang handelt. Die Geometrie der Walzenrillen schmiedet das Material in die erforderliche Form und Geometrie. Es wird heiß ausgeführt. Da es sich um einen Schmiedeprozess handelt, werden Teile mit hervorragenden mechanischen Eigenschaften hergestellt, und deshalb verwenden wir ihn für die Herstellung von Automobilteilen wie Wellen, die in harten Arbeitsumgebungen eine außergewöhnliche Haltbarkeit aufweisen müssen.
• ORBITALSCHMIEDEN: Das Werkstück wird in einen Schmiedegesenkhohlraum gelegt und durch ein oberes Gesenk geschmiedet, das sich auf einer Umlaufbahn bewegt, während es sich um eine geneigte Achse dreht. Bei jeder Umdrehung vervollständigt das obere Werkzeug das Ausüben von Druckkräften auf das gesamte Werkstück. Durch mehrmaliges Wiederholen dieser Umdrehungen wird ein ausreichendes Schmieden durchgeführt. Die Vorteile dieser Herstellungstechnik sind ein geräuscharmer Betrieb und geringere benötigte Kräfte. Mit anderen Worten, mit kleinen Kräften kann man einen schweren Stempel um eine Achse drehen, um große Drücke auf einen Abschnitt des Werkstücks auszuüben, der mit dem Stempel in Kontakt ist. Scheiben- oder konische Formteile eignen sich manchmal gut für diesen Prozess.
• RINGSCHMIEDEN: Wir stellen häufig nahtlose Ringe her. Der Schaft wird auf Länge geschnitten, gestaucht und dann vollständig durchbohrt, um ein zentrales Loch zu erzeugen. Dann wird es auf einen Dorn gesetzt und ein Schmiedegesenk hämmert es von oben, während der Ring langsam gedreht wird, bis die gewünschten Abmessungen erreicht sind.
• NIETEN: Ein übliches Verfahren zum Verbinden von Teilen, beginnt mit einem geraden Metallstück, das in vorgefertigte Löcher durch die Teile eingeführt wird. Danach werden die beiden Enden des Metallstücks geschmiedet, indem die Verbindung zwischen einem oberen und einem unteren Gesenk zusammengedrückt wird.
• PRÄGUNG: Ein weiterer beliebter Prozess, der durch mechanische Pressen durchgeführt wird, wobei große Kräfte über eine kurze Distanz ausgeübt werden. Der Name „Prägen“ kommt von den feinen Details, die auf die Oberflächen von Metallmünzen geschmiedet werden. Es handelt sich hauptsächlich um einen Endbearbeitungsprozess für ein Produkt, bei dem feine Details auf den Oberflächen als Ergebnis der großen Kraft erhalten werden, die von der Matrize ausgeübt wird, die diese Details auf das Werkstück überträgt.
• SCHMIEDEN VON METALLKUGELN: Produkte wie Kugellager erfordern präzise hergestellte Metallkugeln von hoher Qualität. Bei einer Technik namens SKEW ROLLING verwenden wir zwei gegenüberliegende Rollen, die sich kontinuierlich drehen, während das Material kontinuierlich in die Rollen eingeführt wird. Am einen Ende der beiden Walzen werden Metallkugeln als Produkt ausgeworfen. Ein zweites Verfahren zum Schmieden von Metallkugeln ist die Verwendung von Gesenken, die das dazwischen platzierte Material zusammendrücken und die sphärische Form des Formhohlraums annehmen. Oftmals erfordern hergestellte Bälle einige zusätzliche Schritte wie Veredeln und Polieren, um ein qualitativ hochwertiges Produkt zu werden.
• ISOTHERMISCHES SCHMIEDEN/WARMGEFORMSCHMIEDEN: Ein teurer Prozess, der nur durchgeführt wird, wenn der Kosten-/Nutzenwert gerechtfertigt ist. Ein Warmbearbeitungsprozess, bei dem die Matrize auf etwa die gleiche Temperatur wie das Werkstück erhitzt wird. Da sowohl Form als auch Werkstück etwa die gleiche Temperatur haben, findet keine Kühlung statt und die Fließeigenschaften des Metalls werden verbessert. Der Betrieb eignet sich gut für Superlegierungen und Materialien mit schlechter Schmiedbarkeit und Materialien deren
mechanische Eigenschaften reagieren sehr empfindlich auf kleine Temperaturgradienten und -änderungen.
• METALLBESCHICHTUNG: Es handelt sich um einen Kaltveredelungsprozess. Der Materialfluss ist in alle Richtungen mit Ausnahme der Krafteinwirkungsrichtung uneingeschränkt. Dadurch werden eine sehr gute Oberflächengüte und genaue Abmessungen erzielt.
• SCHMIEDE MIT HOHER ENERGIERATE: Die Technik beinhaltet eine obere Form, die am Arm eines Kolbens befestigt ist, der schnell gedrückt wird, wenn ein Kraftstoff-Luft-Gemisch von einer Zündkerze gezündet wird. Es ähnelt dem Betrieb von Kolben in einem Automotor. Die Form trifft sehr schnell auf das Werkstück und kehrt dann dank des Gegendrucks sehr schnell wieder in ihre ursprüngliche Position zurück. Das Werk wird innerhalb weniger Millisekunden geschmiedet und somit bleibt dem Werk keine Zeit zum Abkühlen. Dies ist nützlich für schwer zu schmiedende Teile mit sehr temperaturempfindlichen mechanischen Eigenschaften. Mit anderen Worten, der Prozess ist so schnell, dass das Teil unter konstanter Temperatur geformt wird und es keine Temperaturgradienten an den Schnittstellen Form/Werkstück gibt.
• Beim DIE FORGING (GESENKSCHMIEDEN) wird Metall zwischen zwei zusammenpassenden Stahlblöcken mit speziellen Formen darin, den so genannten Matrizen, geschlagen. Wenn das Metall zwischen die Matrizen gehämmert wird, nimmt es die gleiche Form wie die Formen in der Matrize an. Wenn es seine endgültige Form erreicht hat, wird es zum Abkühlen herausgenommen. Dieses Verfahren erzeugt starke Teile mit präziser Form, erfordert jedoch eine größere Investition für die Spezialwerkzeuge. Stauchschmieden vergrößert den Durchmesser eines Metallstücks, indem es abgeflacht wird. Es wird im Allgemeinen zur Herstellung von Kleinteilen verwendet, insbesondere zum Formen von Köpfen an Befestigungselementen wie Schrauben und Nägeln.
• PULVERMETALLURGIE / PULVERVERARBEITUNG: Wie der Name schon sagt, handelt es sich um Herstellungsprozesse zur Herstellung von festen Teilen mit bestimmten Geometrien und Formen aus Pulvern. Werden zu diesem Zweck Metallpulver verwendet, handelt es sich um die Pulvermetallurgie, bei Nichtmetallpulvern um die Pulververarbeitung. Aus Pulvern werden durch Pressen und Sintern Massivteile hergestellt.
PULVERPRESSEN wird verwendet, um Pulver in gewünschte Formen zu verdichten. Zunächst wird das Ausgangsmaterial physikalisch pulverisiert und in viele kleine Einzelpartikel zerlegt. Pulvergemisch wird in die Matrize gefüllt und ein Stempel fährt auf das Pulver zu und verdichtet es in die gewünschte Form. Meist bei Raumtemperatur durchgeführt, wird beim Pulverpressen ein festes Teil erhalten, das als Grünling bezeichnet wird. Bindemittel und Gleitmittel werden üblicherweise verwendet, um die Kompaktierbarkeit zu verbessern. Wir sind in der Lage, Pulverpressformen mit hydraulischen Pressen mit mehreren tausend Tonnen Kapazität durchzuführen. Außerdem haben wir doppelt wirkende Pressen mit gegenüberliegenden Ober- und Unterstempeln sowie mehrfach wirkende Pressen für hochkomplexe Teilegeometrien. Die Gleichmäßigkeit, die für viele Pulvermetallurgie- / Pulververarbeitungsanlagen eine wichtige Herausforderung darstellt, ist für AGS-TECH aufgrund unserer langjährigen Erfahrung in der kundenspezifischen Fertigung solcher Teile kein großes Problem. Auch bei dickeren Teilen, bei denen die Gleichmäßigkeit eine Herausforderung darstellt, ist uns das gelungen. Wenn wir uns für Ihr Projekt engagieren, fertigen wir Ihre Teile. Wenn wir potenzielle Risiken sehen, werden wir Sie in informieren.
voraus.
Beim PULVERSINTERN, dem zweiten Schritt, wird die Temperatur auf ein bestimmtes Maß angehoben und für eine bestimmte Zeit auf diesem Niveau gehalten, damit sich die Pulverpartikel im Pressling verbinden können. Dies führt zu viel stärkeren Bindungen und einer Festigung des Werkstücks. Das Sintern findet nahe der Schmelztemperatur des Pulvers statt. Während des Sinterns tritt Schrumpfung auf, Materialfestigkeit, Dichte, Duktilität, Wärmeleitfähigkeit, elektrische Leitfähigkeit werden erhöht. Wir verfügen über Chargen- und Durchlauföfen zum Sintern. Eine unserer Fähigkeiten ist die Anpassung des Porositätsgrades der von uns hergestellten Teile. Beispielsweise können wir Metallfilter herstellen, indem wir die Teile bis zu einem gewissen Grad porös halten.
Mit einer Technik namens IMPRÄGNIERUNG füllen wir die Poren im Metall mit einer Flüssigkeit wie Öl. Wir produzieren zum Beispiel ölimprägnierte Lager, die selbstschmierend sind. Beim INFILTRATION-Prozess füllen wir die Poren eines Metalls mit einem anderen Metall mit niedrigerem Schmelzpunkt als das Grundmaterial. Die Mischung wird auf eine Temperatur zwischen den Schmelztemperaturen der beiden Metalle erhitzt. Dadurch können einige besondere Eigenschaften erzielt werden. Wir führen auch häufig sekundäre Operationen wie maschinelle Bearbeitung und Schmieden an pulvergefertigten Teilen durch, wenn besondere Merkmale oder Eigenschaften erzielt werden müssen oder wenn das Teil mit weniger Prozessschritten hergestellt werden kann.
ISOSTATISCHES PRESSEN: Bei diesem Prozess wird der Flüssigkeitsdruck verwendet, um das Teil zu verdichten. Metallpulver werden in eine Form gegeben, die aus einem versiegelten flexiblen Behälter besteht. Beim isostatischen Pressen wird von allen Seiten Druck ausgeübt, im Gegensatz zum axialen Druck, der beim herkömmlichen Pressen auftritt. Die Vorteile des isostatischen Pressens sind gleichmäßige Dichte innerhalb des Teils, insbesondere bei größeren oder dickeren Teilen, überlegene Eigenschaften. Ihr Nachteil sind lange Zykluszeiten und relativ geringe geometrische Genauigkeiten. KALTES ISOSTATISCHES PRESSEN wird bei Raumtemperatur durchgeführt und die flexible Form besteht aus Gummi, PVC oder Urethan oder ähnlichen Materialien. Das zum Druckbeaufschlagen und Verdichten verwendete Fluid ist Öl oder Wasser. Daran schließt sich das konventionelle Sintern des Grünlings an. HEISSISOSTATISCHES PRESSEN hingegen wird bei hohen Temperaturen durchgeführt und das Formmaterial ist Blech oder Keramik mit einem Schmelzpunkt, der hoch genug ist, um den Temperaturen standzuhalten. Das Druckfluid ist normalerweise ein Inertgas. Die Press- und Sintervorgänge werden in einem Schritt durchgeführt. Die Porosität wird fast vollständig eliminiert, eine gleichmäßige Kornstruktur wird erhalten. Der Vorteil des heißisostatischen Pressens besteht darin, dass es Teile herstellen kann, die mit dem Gießen und Schmieden in Kombination vergleichbar sind, wobei Materialien verwendet werden können, die für das Gießen und Schmieden nicht geeignet sind. Nachteil des heißisostatischen Pressens ist die hohe Taktzeit und damit die Kosten. Es eignet sich für kritische Teile mit geringem Volumen.
METALL-SPRITZGUSS: Sehr geeignetes Verfahren zur Herstellung komplexer Teile mit dünnen Wänden und detaillierten Geometrien. Am besten geeignet für kleinere Teile. Pulver und Polymerbindemittel werden gemischt, erhitzt und in eine Form gespritzt. Das Polymerbindemittel beschichtet die Oberflächen der Pulverpartikel. Nach dem Formen wird das Bindemittel entweder durch Erhitzen bei niedriger Temperatur oder durch Auflösen unter Verwendung eines Lösungsmittels entfernt.
WALZENVERDICHTUNG / PULVERWALZUNG: Pulver werden zur Herstellung von Endlosbändern oder -platten verwendet. Pulver wird von einem Beschicker zugeführt und von zwei rotierenden Walzen zu Platten oder Streifen verdichtet. Die Operation wird kalt durchgeführt. Das Blech wird in einen Sinterofen transportiert. Der Sintervorgang kann ein zweites Mal wiederholt werden.
PULVEREXTRUSION: Teile mit einem großen Verhältnis von Länge zu Durchmesser werden durch Extrudieren eines dünnen Blechbehälters mit Pulver hergestellt.
LOSE SINTERUNG: Wie der Name schon sagt, handelt es sich um ein druckloses Verdichtungs- und Sinterverfahren, das sich zur Herstellung sehr poröser Teile wie Metallfilter eignet. Pulver wird ohne Verdichtung in den Formhohlraum eingeführt.
LOSE SINTERUNG: Wie der Name schon sagt, handelt es sich um ein druckloses Verdichtungs- und Sinterverfahren, das sich zur Herstellung sehr poröser Teile wie Metallfilter eignet. Pulver wird ohne Verdichtung in den Formhohlraum eingeführt.
FUNKSINTERN: Das Pulver wird in der Form durch zwei gegenüberliegende Stempel komprimiert und ein elektrischer Strom hoher Leistung wird an den Stempel angelegt und fließt durch das komprimierte Pulver, das zwischen ihnen eingebettet ist. Der hohe Strom brennt Oberflächenfilme von den Pulverpartikeln ab und sintert sie mit der erzeugten Hitze. Der Prozess ist schnell, da die Wärme nicht von außen zugeführt wird, sondern innerhalb der Form erzeugt wird.
HEISSPRESSEN: Die Pulver werden in einem einzigen Schritt in einer Form gepresst und gesintert, die den hohen Temperaturen standhalten kann. Während sich die Form verdichtet, wird ihr die Pulverwärme zugeführt. Die durch dieses Verfahren erzielten guten Genauigkeiten und mechanischen Eigenschaften machen es zu einer attraktiven Option. Auch Refraktärmetalle können durch den Einsatz von Formstoffen wie Graphit verarbeitet werden.