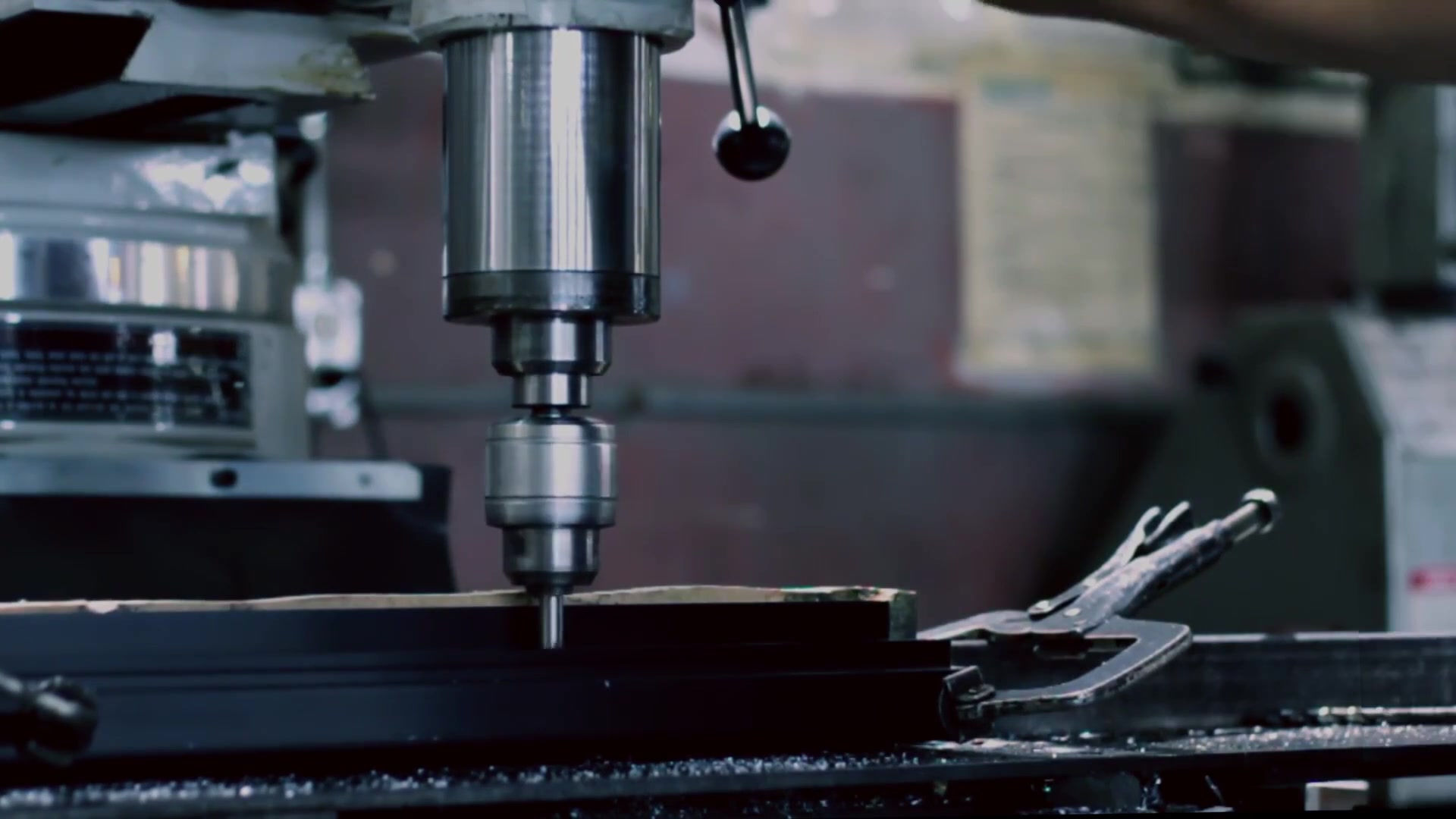
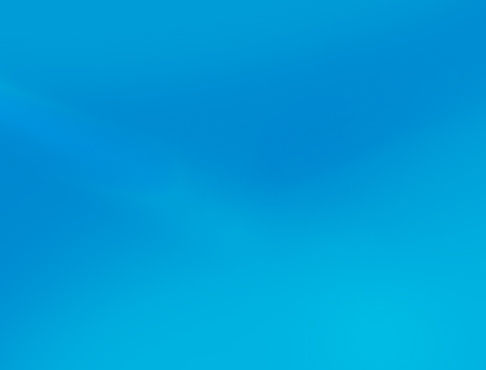
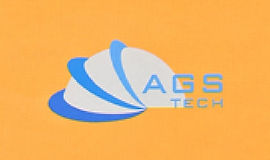
Globaler kundenspezifischer Hersteller, Integrator, Konsolidierer, Outsourcing-Partner für eine Vielzahl von Produkten und Dienstleistungen.
Wir sind Ihre One-Stop-Quelle für Fertigung, Fertigung, Engineering, Konsolidierung, Integration, Outsourcing von kundenspezifisch gefertigten und handelsüblichen Produkten und Dienstleistungen.
Wählen Sie Ihre Sprache
-
Kundenspezifische Fertigung
-
Nationale und globale Auftragsfertigung
-
Produktions-Outsourcing
-
Nationale und globale Beschaffung
-
Konsolidierung
-
Engineering-Integration
-
Technische Dienstleistungen
Unter der großen Anzahl von MECHANISCHEN PRÜFGERÄTEN konzentrieren wir uns auf die wichtigsten und beliebtesten: IMPACTERS, SCHMIMERTEST, SCHMIMERTEST, DT , ZUGPRÜFGERÄTE, KOMPRESSIONSPRÜFMASCHINEN, TORSIONSPRÜFGERÄTE, ERMÜDUNGSPRÜFMASCHINE, DREI- UND VIER-PUNKT-BIEGEPRÜFGERÄTE, REIBUNGSKOEFFIZIENT-PRÜFGERÄTE, HÄRTE- UND DICKENPRÜFGERÄTE, OBERFLÄCHENRAUHEITSMESSGERÄTE, SCHWINGUNGSPRÜFGERÄTE PRÄZISE ANALYSEWAAGE. Wir bieten unseren Kunden Qualitätsmarken wie z. B. SADT, SINOAGE zu Preisen unter dem Listenpreis.
Um den Katalog unserer Mess- und Prüfgeräte der Marke SADT herunterzuladen, KLICKEN SIE HIER. Hier finden Sie einige dieser Prüfgeräte wie Betonprüfgeräte und Oberflächenrauheitsprüfgeräte.
Sehen wir uns diese Testgeräte einmal genauer an:
SCHMIDT HAMMER / CONCRETE TESTER : This test instrument, also sometimes called a SWISS HAMMER or a REBOUND HAMMER, ist ein Gerät zur Messung der elastischen Eigenschaften oder Festigkeit von Beton oder Gestein, hauptsächlich Oberflächenhärte und Eindringwiderstand. Der Hammer misst den Rückprall einer federbelasteten Masse, die gegen die Oberfläche der Probe schlägt. Der Prüfhammer schlägt mit einer vorgegebenen Energie auf den Beton. Der Rückprall des Hammers hängt von der Härte des Betons ab und wird vom Prüfgerät gemessen. Anhand einer Umrechnungstabelle kann anhand des Rückprallwertes die Druckfestigkeit bestimmt werden. Der Schmidt-Hammer ist eine willkürliche Skala von 10 bis 100. Schmidt-Hämmer gibt es in verschiedenen Energiebereichen. Ihre Energiebereiche sind: (i) Typ L – 0,735 Nm Schlagenergie, (ii) Typ N – 2,207 Nm Schlagenergie; und (iii) Typ M-29,43 Nm Aufprallenergie. Lokale Variation in der Probe. Um lokale Schwankungen in den Proben zu minimieren, wird empfohlen, eine Auswahl von Messwerten zu nehmen und deren Mittelwert zu nehmen. Vor der Prüfung muss der Schmidt-Hammer mit einem vom Hersteller gelieferten Kalibrierprüfamboss kalibriert werden. Es sollten 12 Messwerte genommen werden, wobei der höchste und der niedrigste gemessen werden und dann der Durchschnitt der zehn verbleibenden Messwerte genommen wird. Diese Methode gilt als indirekte Messung der Festigkeit des Materials. Es liefert eine Angabe basierend auf Oberflächeneigenschaften zum Vergleich zwischen Proben. Dieses Testverfahren zum Testen von Beton wird von ASTM C805 geregelt. Andererseits beschreibt die Norm ASTM D5873 das Verfahren zum Testen von Gestein. In unserem SADT-Markenkatalog finden Sie die folgenden Produkte: DIGITALER BETONPRÜFHAMMER SADT-Modelle HT-225D/HT-75D/HT-20D - Das SADT-Modell HT-225D ist ein integrierter digitaler Betonprüfhammer, der Datenprozessor und Prüfhammer in einer einzigen Einheit kombiniert. Es wird häufig zur zerstörungsfreien Qualitätsprüfung von Beton und Baumaterialien eingesetzt. Aus dem Rückprallwert lässt sich die Druckfestigkeit von Beton automatisch berechnen. Alle Testdaten können im Speicher gespeichert und per USB-Kabel oder drahtlos per Bluetooth auf den PC übertragen werden. Die Modelle HT-225D und HT-75D haben einen Messbereich von 10 – 70 N/mm2, während das Modell HT-20D nur 1 – 25 N/mm2 hat. Die Schlagenergie von HT-225D beträgt 0,225 kgm und eignet sich zum Testen gewöhnlicher Gebäude- und Brückenkonstruktionen, die Schlagenergie von HT-75D beträgt 0,075 kgm und eignet sich zum Testen kleiner und stoßempfindlicher Teile aus Beton und Kunststein und schließlich Die Schlagenergie von HT-20D beträgt 0,020 kgm und eignet sich zum Testen von Mörtel- oder Tonprodukten.
SCHLAGPRÜFER: In vielen Fertigungsprozessen und während ihrer Lebensdauer müssen viele Bauteile Schlagbelastungen ausgesetzt werden. Bei der Schlagprüfung wird die gekerbte Probe in ein Schlagprüfgerät gelegt und mit einem schwingenden Pendel gebrochen. Es gibt zwei Haupttypen dieses Tests: The CHARPY TEST und the IZOD TEST. Beim Charpy-Versuch werden die Proben an beiden Enden gelagert, während sie beim Izod-Versuch nur an einem Ende wie ein freitragender Balken gelagert werden. Aus der Schwingweite des Pendels ergibt sich die Energie, die beim Brechen der Probe verbraucht wird, diese Energie ist die Schlagzähigkeit des Materials. Mit den Schlagversuchen können wir die Duktil-Spröd-Übergangstemperaturen von Werkstoffen bestimmen. Materialien mit hoher Schlagfestigkeit haben im Allgemeinen eine hohe Festigkeit und Duktilität. Diese Tests zeigen auch die Empfindlichkeit der Schlagzähigkeit eines Materials gegenüber Oberflächenfehlern, da die Kerbe in der Probe als Oberflächenfehler angesehen werden kann.
TENSION TESTER : Mit diesem Test wird das Festigkeits-Verformungs-Verhalten von Materialien ermittelt. Testproben werden gemäß ASTM-Standards hergestellt. Typischerweise werden massive und runde Proben getestet, aber auch flache Bleche und röhrenförmige Proben können mit dem Zugtest getestet werden. Die Originallänge einer Probe ist der Abstand zwischen den Messmarken darauf und beträgt typischerweise 50 mm. Es wird als lo bezeichnet. Je nach Proben und Produkten können längere oder kürzere Längen verwendet werden. Die ursprüngliche Querschnittsfläche wird als Ao bezeichnet. Die Ingenieurspannung oder auch Nennspannung genannt ergibt sich dann zu:
Sigma = P / Ao
Und die technische Dehnung wird angegeben als:
e = (l – lo) / lo
Im linearelastischen Bereich dehnt sich die Probe proportional zur Belastung bis zur Proportionalitätsgrenze. Jenseits dieser Grenze, wenn auch nicht linear, verformt sich die Probe bis zur Streckgrenze Y weiter elastisch. In diesem elastischen Bereich kehrt das Material zu seiner ursprünglichen Länge zurück, wenn wir die Belastung entfernen. In diesem Bereich gilt das Hookesche Gesetz und gibt uns den Elastizitätsmodul:
E = Sigma / e
Wenn wir die Belastung erhöhen und über die Streckgrenze Y hinausgehen, beginnt das Material zu fließen. Mit anderen Worten, die Probe beginnt sich plastisch zu verformen. Plastische Verformung bedeutet bleibende Verformung. Die Querschnittsfläche der Probe nimmt permanent und gleichmäßig ab. Wird die Probe an dieser Stelle entlastet, folgt die Kurve im elastischen Bereich einer geraden Linie nach unten und parallel zur ursprünglichen Linie. Wird die Last weiter erhöht, erreicht die Kurve ein Maximum und beginnt abzufallen. Der maximale Spannungspunkt wird als Zugfestigkeit oder Höchstzugfestigkeit bezeichnet und als UTS bezeichnet. Die UTS kann als Gesamtfestigkeit von Materialien interpretiert werden. Wenn die Belastung größer als die UTS ist, tritt an der Probe eine Einschnürung auf und die Dehnung zwischen den Messmarken ist nicht mehr gleichmäßig. Mit anderen Worten, die Probe wird an der Stelle, an der die Einschnürung auftritt, sehr dünn. Beim Einschnüren sinkt die elastische Spannung. Wird der Versuch fortgesetzt, sinkt die Ingenieurspannung weiter ab und die Probe bricht im Einschnürungsbereich. Das Spannungsniveau beim Bruch ist die Bruchspannung. Die Bruchdehnung ist ein Indikator für die Duktilität. Die Dehnung bis zur UTS wird als Gleichdehnung und die Bruchdehnung als Gesamtdehnung bezeichnet.
Dehnung = ((lf – lo) / lo) x 100
Flächenreduktion = ((Ao – Af) / Ao) x 100
Dehnung und Flächenverringerung sind gute Indikatoren für Duktilität.
KOMPRESSIONSPRÜFMASCHINE ( KOMPRESSIONSTESTER ) : Bei diesem Test wird die Probe einer Druckbelastung ausgesetzt, im Gegensatz zur Zugprüfung, bei der die Belastung Zug ist. Im Allgemeinen wird ein massiver zylindrischer Probekörper zwischen zwei flache Platten gelegt und zusammengedrückt. Durch die Verwendung von Schmiermitteln an den Kontaktflächen wird ein als Barreling bekanntes Phänomen verhindert. Die technische Dehnungsrate bei Kompression ist gegeben durch:
de / dt = - v / ho, wobei v die Werkzeuggeschwindigkeit, ho die ursprüngliche Probenhöhe ist.
Die wahre Dehnungsrate ist dagegen:
de = dt = - v/ h, wobei h die momentane Probenhöhe ist.
Um die wahre Dehnungsrate während des Tests konstant zu halten, reduziert ein Nockenplastometer durch eine Nockenwirkung die Größe von v proportional zur Abnahme der Probenhöhe h während des Tests. Unter Verwendung des Kompressionstests werden Duktilitäten von Materialien durch Beobachten von Rissen bestimmt, die sich auf tonnenförmigen zylindrischen Oberflächen gebildet haben. Ein weiterer Test mit einigen Unterschieden in den Werkzeug- und Werkstückgeometrien ist der PLANE-STRAIN COMPRESSION TEST, der uns die Streckgrenze des Materials bei ebener Dehnung liefert, allgemein als Y' bezeichnet. Die Streckspannung von Materialien bei ebener Dehnung kann wie folgt abgeschätzt werden:
Y' = 1,15 Y
TORSIONSPRÜFMASCHINEN (TORSIONAL TESTERS) : Der TORSION TEST ist eine weitere weit verbreitete Methode zur Bestimmung von Materialeigenschaften. Bei diesem Test wird eine röhrenförmige Probe mit reduziertem Mittelteil verwendet. Scherspannung, T ist gegeben durch:
T = T / 2 (Pi) (Quadrat von r) t
Dabei ist T das aufgebrachte Drehmoment, r der mittlere Radius und t die Dicke des reduzierten Abschnitts in der Rohrmitte. Die Scherspannung hingegen ist gegeben durch:
ß = r Ø / l
Dabei ist l die Länge des reduzierten Abschnitts und Ø der Verdrehwinkel im Bogenmaß. Innerhalb des elastischen Bereichs wird der Schubmodul (Steifigkeitsmodul) ausgedrückt als:
G = T / ß
Die Beziehung zwischen Schubmodul und Elastizitätsmodul ist:
G = E / 2( 1 + V )
Der Torsionsversuch wird an massiven Rundstäben bei erhöhten Temperaturen angewendet, um die Schmiedbarkeit von Metallen abzuschätzen. Je mehr Verwindungen das Material bis zum Versagen aushalten kann, desto schmiedbarer ist es.
THREE & FOUR POINT BENDING TESTERS : For brittle materials, the BEND TEST (also called FLEXURE TEST) ist geeignet. Eine rechteckig geformte Probe wird an beiden Enden gestützt und vertikal belastet. Die vertikale Kraft wird entweder an einem Punkt wie im Fall einer Dreipunkt-Biegeprüfmaschine oder an zwei Punkten wie im Fall einer Vierpunkt-Prüfmaschine aufgebracht. Die Bruchspannung beim Biegen wird als Bruchmodul oder Querbruchfestigkeit bezeichnet. Es wird angegeben als:
Sigma = M c / I
Dabei ist M das Biegemoment, c die halbe Probentiefe und I das Trägheitsmoment des Querschnitts. Die Größe der Spannung ist sowohl beim Drei- als auch beim Vierpunktbiegen gleich, wenn alle anderen Parameter konstant gehalten werden. Der Vier-Punkte-Test führt im Vergleich zum Drei-Punkte-Test wahrscheinlich zu einem niedrigeren Bruchmodul. Eine weitere Überlegenheit des Vierpunkt-Biegetests gegenüber dem Dreipunkt-Biegetest besteht darin, dass seine Ergebnisse bei geringerer statistischer Streuung der Werte konsistenter sind.
FATIGUE TEST MACHINE: In FATIGUE TESTING wird ein Prüfling wiederholt verschiedenen Belastungszuständen ausgesetzt. Die Beanspruchungen sind im Allgemeinen eine Kombination aus Zug, Druck und Torsion. Der Testvorgang kann dem Biegen eines Stücks Draht abwechselnd in die eine Richtung und dann in die andere Richtung bis zum Bruch ähnlich sein. Die Spannungsamplitude kann variiert werden und wird mit „S“ bezeichnet. Die Anzahl der Zyklen bis zum vollständigen Versagen der Probe wird aufgezeichnet und als „N“ bezeichnet. Die Spannungsamplitude ist der maximale Spannungswert bei Zug und Druck, dem die Probe ausgesetzt ist. Eine Variation des Ermüdungstests wird an einer rotierenden Welle mit konstanter nach unten gerichteter Belastung durchgeführt. Die Dauerfestigkeit (Ermüdungsgrenze) ist definiert als die max. Spannungswert, dem das Material unabhängig von der Anzahl der Zyklen ohne Ermüdungsbruch standhalten kann. Die Ermüdungsfestigkeit von Metallen hängt mit ihrer Zugfestigkeit UTS zusammen.
REIBUNGSKOEFFIZIENT TESTER : Dieses Testgerät misst die Leichtigkeit, mit der zwei sich berührende Oberflächen aneinander vorbeigleiten können. Dem Reibungskoeffizienten sind zwei verschiedene Werte zugeordnet, nämlich der statische und der kinetische Reibungskoeffizient. Haftreibung gilt für die Kraft, die erforderlich ist, um die Bewegung zwischen den beiden Oberflächen zu initialisieren, und kinetische Reibung ist der Widerstand gegen das Gleiten, sobald sich die Oberflächen in Relativbewegung befinden. Vor dem Testen und während des Testens müssen geeignete Maßnahmen ergriffen werden, um sicherzustellen, dass kein Schmutz, Fett und andere Verunreinigungen vorhanden sind, die die Testergebnisse beeinträchtigen könnten. ASTM D1894 ist der wichtigste Teststandard für den Reibungskoeffizienten und wird von vielen Branchen mit unterschiedlichen Anwendungen und Produkten verwendet. Wir sind hier, um Ihnen die am besten geeigneten Testgeräte anzubieten. Wenn Sie eine speziell auf Ihre Anwendung zugeschnittene Konfiguration benötigen, können wir vorhandene Geräte entsprechend modifizieren, um Ihre Anforderungen und Bedürfnisse zu erfüllen.
HÄRTEPRÜFER : Bitte gehen Sie zu unserer verwandten Seite, indem Sie hier klicken
DICKENPRÜFER : Bitte gehen Sie zu unserer verwandten Seite, indem Sie hier klicken
OBERFLÄCHENRAUHEITSTESTER : Bitte gehen Sie zu unserer verwandten Seite, indem Sie hier klicken
VIBRATIONSMESSGERÄTE : Bitte gehen Sie zu unserer verwandten Seite, indem Sie hier klicken
DREHZAHLMESSER : Bitte gehen Sie zu unserer verwandten Seite, indem Sie hier klicken
Einzelheiten und andere ähnliche Geräte finden Sie auf unserer Geräte-Website: http://www.sourceindustrialsupply.com