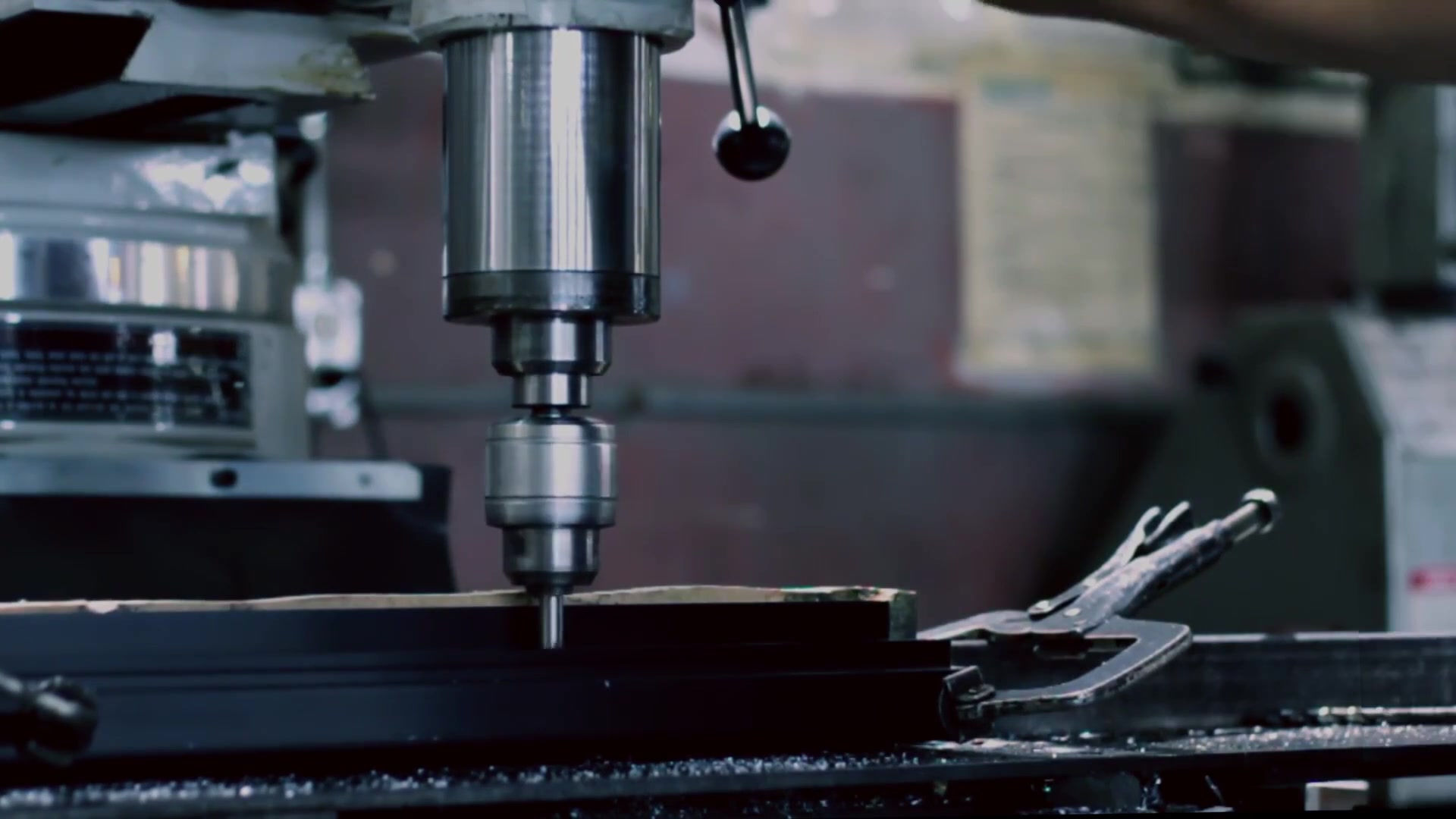
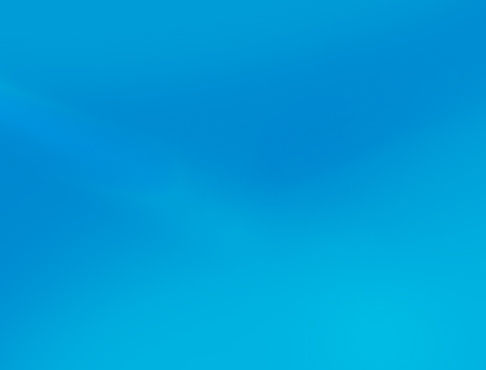
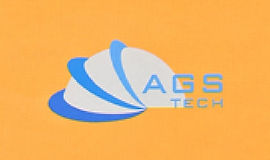
Fabricante global personalizado, integrador, consolidador, socio de outsourcing para unha ampla variedade de produtos e servizos.
Somos a súa fonte única para a fabricación, fabricación, enxeñaría, consolidación, integración e subcontratación de produtos e servizos fabricados a medida e dispoñibles.
Escolla o seu idioma
-
Fabricación personalizada
-
Fabricación por contrato nacional e global
-
Outsourcing de Manufactura
-
Compras domésticas e globais
-
Consolidación
-
Integración de enxeñería
-
Servizos de Enxeñaría
As nosas técnicas de fundición e mecanizado personalizados son fundición prescindible e non prescindible, fundición férrica e non ferrosa, area, matriz, centrífuga, molde continuo, cerámico, investimento, escuma perdida, forma case rede, molde permanente (fundición por gravidade), xeso. moldes (fundición de xeso) e fundición de casca, pezas mecanizadas producidas por fresado e torneado utilizando equipos convencionais e CNC, mecanizado de tipo suízo para pezas pequenas e baratas de alta precisión, mecanizado de parafusos para elementos de fixación, mecanizado non convencional. Teña en conta que, ademais de metais e aliaxes metálicas, mecanizamos compoñentes de cerámica, vidro e plástico, nalgúns casos cando fabricar un molde non é atractivo ou non é a opción. O mecanizado de materiais poliméricos require da experiencia especializada que temos polo reto que presentan os plásticos e o caucho pola súa suavidade, non rixidez...etc. Para o mecanizado de cerámica e vidro, consulte a nosa páxina sobre Fabricación non convencional. AGS-TECH Inc. fabrica e fornece pezas de fundición lixeiras e pesadas. Estivemos a subministrar fundicións metálicas e pezas mecanizadas para caldeiras, intercambiadores de calor, automóbiles, micromotores, aeroxeradores, equipos de envasado de alimentos e moito máis. Recomendámosche que fagas clic aquí para DESCARGA as nosas ilustracións esquemáticas de procesos de mecanizado e fundición de AGS-TECH Inc.
Isto axudarache a comprender mellor a información que che proporcionamos a continuación. Vexamos en detalle algunhas das diversas técnicas que ofrecemos:
• FUNDACIÓN DE MOLDES EXPENDABLES: esta categoría ampla refírese aos métodos que implican moldes temporais e non reutilizables. Son exemplos de area, xeso, cuncha, revestimento (tamén chamado de cera perdida) e fundición de xeso.
• FUNDACIÓN EN AREA: Proceso no que se utiliza area como material do molde. Un método moi antigo e aínda moi popular na medida en que a maioría das fundicións metálicas producidas son feitas por esta técnica. Baixo custo mesmo con produción en cantidade baixa. Adecuado para a fabricación de pezas pequenas e grandes. A técnica pódese usar para fabricar pezas en días ou semanas cun investimento moi reducido. A area húmida únase con arxila, aglutinantes ou aceites especiais. A area xeralmente está contida en caixas de moldes e o sistema de cavidades e portas créase compactando a area arredor dos modelos. Os procesos son:
1.) Colocación do modelo en area para facer o molde
2.) Incorporación de maqueta e area nun sistema de gating
3.) Eliminación do modelo
4.) Recheo da cavidade do molde con metal fundido
5.) Arrefriamento do metal
6.) Rotura do molde de area e retirada da fundición
• FUNDACIÓN DE MOLDES DE xeso: Similar á fundición en area, e en lugar de area, utilízase o xeso de París como material do molde. Prazos de produción curtos como fundición en area e barato. Boas tolerancias dimensionales e acabado superficial. A súa principal desvantaxe é que só se pode usar con metais de baixo punto de fusión como o aluminio e o cinc.
• FUNDACIÓN DE MOLDES DE CONCHAS : Tamén é semellante á fundición en area. Cavidade do molde obtida por casca de area endurecida e aglutinante de resina termoendurecible en lugar do matraz cheo de area como no proceso de fundición en area. Case calquera metal axeitado para ser fundido con area pode ser fundido mediante moldura de cuncha. O proceso pódese resumir como:
1.) Fabricación do molde de casca. A area utilizada é de gran tamaño moito menor en comparación coa area utilizada na fundición en area. A area fina mestúrase con resina termoendurecible. O patrón metálico está revestido cun axente de separación para facilitar a eliminación da cuncha. Despois diso, o patrón metálico quéntase e a mestura de area é porosa ou soplada sobre o patrón de fundición en quente. Na superficie do patrón fórmase unha capa fina. O grosor desta cuncha pódese axustar variando o tempo que a mestura de resina de area está en contacto co patrón metálico. Despois elimínase a area solta quedando o patrón cuberto de casca.
2.) A continuación, a casca e o patrón quéntanse nun forno para que a cuncha se endureza. Despois de completar o endurecemento, a cuncha é expulsada do patrón usando alfinetes incorporados ao patrón.
3.) Dúas cunchas deste tipo únense pegando ou abrazando e compoñen o molde completo. Agora o molde de cuncha insírese nun recipiente no que está sostido por area ou granalla metálica durante o proceso de fundición.
4.) Agora o metal quente pódese verter no molde de cuncha.
As vantaxes da fundición de cunchas son produtos con moi bo acabado superficial, posibilidade de fabricar pezas complexas con alta precisión dimensional, proceso fácil de automatizar, económico para a produción de grandes volumes.
As desvantaxes son que os moldes necesitan unha boa ventilación debido aos gases que se crean cando o metal fundido entra en contacto co produto químico aglutinante, as resinas termoendurecibles e os patróns metálicos son caros. Debido ao custo dos patróns metálicos, é posible que a técnica non se adapte ben a producións de baixa cantidade.
• FUNDACIÓN POR INVESTIMENTO (tamén coñecida como FUNDA A CERA PERDIDA ): técnica tamén moi antiga e apta para fabricar pezas de calidade con gran precisión, repetibilidade, versatilidade e integridade a partir de moitos metais, materiais refractarios e aliaxes especiais de alto rendemento. Pódense producir pezas pequenas e grandes. Un proceso caro en comparación con algúns dos outros métodos, pero a principal vantaxe é a posibilidade de producir pezas cunha forma case neta, contornos e detalles complicados. Polo tanto, o custo vese algo compensado coa eliminación de reelaboración e mecanizado nalgúns casos. Aínda que pode haber variacións, aquí tes un resumo do proceso xeral de fundición de investimento:
1.) Creación dun patrón mestre orixinal a partir de cera ou plástico. Cada fundición necesita un patrón xa que estes son destruídos no proceso. Tamén é necesario un molde a partir do que se fabrican os patróns e a maioría das veces o molde é fundido ou mecanizado. Debido a que non é necesario abrir o molde, pódense conseguir fundicións complexas, moitos patróns de cera pódense conectar como as ramas dunha árbore e verter xuntos, permitindo así a produción de varias pezas a partir dunha única vertida do metal ou da aliaxe metálica.
2.) A continuación, o patrón é mergullado ou vertido cunha suspensión refractaria composta de sílice de gran fino, auga e aglutinantes. Isto dá lugar a unha capa de cerámica sobre a superficie do patrón. A capa refractaria do patrón déixase secar e endurecer. Este paso é de onde provén o nome de fundición de investimento: o lodo refractario inviste sobre o patrón de cera.
3.) Neste paso, o molde de cerámica endurecida bótase boca abaixo e quéntase para que a cera se derrita e saia do molde. Déixase unha cavidade para a fundición de metal.
4.) Despois de que a cera está fóra, o molde de cerámica quéntase ata unha temperatura máis alta, o que resulta no fortalecemento do molde.
5.) A fundición de metal bótase no molde quente enchendo todas as seccións complicadas.
6.) Permítese solidificar a fundición
7.) Finalmente rómpese o molde de cerámica e córtanse partes manufacturadas da árbore.
Aquí tes unha ligazón ao folleto da planta de fundición de investimento
• FUNDACIÓN DE PATRÓN EVAPORATIVO: O proceso utiliza un patrón feito a partir dun material como a espuma de poliestireno que se evapora cando se vierte metal fundido quente no molde. Existen dous tipos deste proceso: FUNDACIÓN DE ESPUMA PERDIDA que utiliza area sen unir e FUNDACIÓN DE MOLDES COMPLETOS que utiliza area adherida. Aquí están os pasos xerais do proceso:
1.) Fabrica o patrón a partir dun material como o poliestireno. Cando se fabriquen grandes cantidades, o patrón é moldeado. Se a parte ten unha forma complexa, é posible que teñan que unir varias seccións deste material de escuma para formar o patrón. Moitas veces recubrimos o patrón cun composto refractario para crear un bo acabado superficial na fundición.
2.) O patrón é entón colocado en area de moldeo.
3.) O metal fundido bótase no molde, evaporando o patrón de escuma, é dicir, poliestireno na maioría dos casos mentres flúe pola cavidade do molde.
4.) O metal fundido déixase no molde de area para endurecer.
5.) Despois de que estea endurecido, retiramos a fundición.
Nalgúns casos, o produto que fabricamos require un núcleo dentro do patrón. Na fundición por evaporación, non hai necesidade de colocar e asegurar un núcleo na cavidade do molde. A técnica é axeitada para a fabricación de xeometrías moi complexas, pódese automatizar facilmente para a produción de gran volume e non hai liñas de separación na peza fundida. O proceso básico é sinxelo e económico de implementar. Para a produción de grandes volumes, xa que se necesita unha matriz ou un molde para producir os patróns a partir de poliestireno, isto pode ser algo custoso.
• FUNDACIÓN DE MOLDES NON EXPANDIBLES: esta categoría ampla refírese aos métodos nos que o molde non precisa ser reformado despois de cada ciclo de produción. Exemplos son a fundición permanente, a matriz, continua e centrífuga. Conséguese repetibilidade e as pezas pódense caracterizar como NEAR NET SHAPE.
• FUNDACIÓN DE MOLDES PERMANENTES: Os moldes reutilizables feitos de metal utilízanse para varias fundicións. Un molde permanente xeralmente pódese usar decenas de miles de veces antes de que se desgaste. A gravidade, a presión do gas ou o baleiro úsanse xeralmente para encher o molde. Os moldes (tamén chamados troqueles) están feitos xeralmente de ferro, aceiro, cerámica ou outros metais. O proceso xeral é:
1.) Mecanizar e crear o molde. É habitual mecanizar o molde a partir de dous bloques metálicos que encaixan e que se poden abrir e pechar. Tanto as características da peza como o sistema de compuerta son xeralmente mecanizados no molde de fundición.
2.) As superficies internas do molde están recubertas cunha suspensión que incorpora materiais refractarios. Isto axuda a controlar o fluxo de calor e actúa como lubricante para facilitar a eliminación da parte fundida.
3.) A continuación, péchanse as metades do molde permanente e quéntase o molde.
4.) O metal fundido bótase no molde e déixase quieto para a solidificación.
5.) Antes de que se produza moito arrefriamento, retiramos a peza do molde permanente mediante expulsores cando se abren as metades do molde.
Usamos con frecuencia a fundición permanente en moldes para metais de baixo punto de fusión como o cinc e o aluminio. Para as fundicións de aceiro, usamos grafito como material do molde. Ás veces obtemos xeometrías complexas utilizando núcleos dentro de moldes permanentes. Vantaxes desta técnica son as fundicións con boas propiedades mecánicas obtidas por arrefriamento rápido, uniformidade nas propiedades, boa precisión e acabado superficial, baixas taxas de rexeitamento, posibilidade de automatizar o proceso e producir grandes volumes de xeito económico. As desvantaxes son os altos custos de configuración inicial que o fan inadecuado para operacións de baixo volume e as limitacións no tamaño das pezas fabricadas.
• FUNDACIÓN A PRESIÓN: mecanízase unha matriz e empúxase o metal fundido a alta presión nas cavidades do molde. Son posibles fundicións tanto de metais non férreos como férreos. O proceso é adecuado para tiradas de produción en grandes cantidades de pezas pequenas e medianas con detalles, paredes extremadamente finas, consistencia dimensional e bo acabado superficial. AGS-TECH Inc. é capaz de fabricar espesores de paredes tan pequenos como 0,5 mm usando esta técnica. Do mesmo xeito que na fundición de moldes permanentes, o molde debe constar de dúas metades que se poidan abrir e pechar para eliminar a parte producida. Un molde de fundición a presión pode ter varias cavidades para permitir a produción de varias fundicións con cada ciclo. Os moldes de fundición son moi pesados e moito máis grandes que as pezas que producen, polo que tamén son caros. Reparamos e substituímos matrices desgastadas de xeito gratuíto para os nosos clientes, sempre que nos soliciten de novo as súas pezas. Os nosos troqueles teñen unha longa vida útil no rango de varios centos de miles de ciclos.
Aquí están os pasos básicos do proceso simplificado:
1.) Produción do molde xeralmente a partir de aceiro
2.) Molde instalado na máquina de fundición a presión
3.) O pistón obriga o metal fundido a fluír nas cavidades da matriz enchendo as características complicadas e as paredes finas
4.) Despois de encher o molde co metal fundido, a fundición déixase endurecer a presión
5.) Ábrese o molde e elimínase a fundición coa axuda de pasadores expulsores.
6.) Agora a matriz baleira lubricase de novo e fíxase para o seguinte ciclo.
Na fundición a presión, usamos frecuentemente moldaxe de inserción onde incorporamos unha parte adicional ao molde e fundimos o metal ao seu redor. Despois da solidificación, estas pezas pasan a formar parte do produto fundido. As vantaxes da fundición a presión son boas propiedades mecánicas das pezas, posibilidade de características complexas, detalles finos e bo acabado superficial, altas taxas de produción, fácil automatización. As desvantaxes son: non moi axeitado para volumes baixos debido ao alto custo do troquel e do equipamento, limitacións nas formas que se poden fundir, pequenas marcas redondas nas pezas de fundición derivadas do contacto dos pasadores do expulsor, un brillo fino de metal espremido na liña de separación, necesidade. para ventilacións ao longo da liña de separación entre a matriz, necesidade de manter as temperaturas do molde baixas usando circulación de auga.
• FUNDACIÓN CENTRÍFUGA: bótase metal fundido no centro do molde rotativo no eixe de rotación. As forzas centrífugas arroxan o metal cara á periferia e déixase solidificar mentres o molde segue xirando. Pódense utilizar rotacións de eixe tanto horizontais como verticais. Pódense fundir pezas con superficies internas redondas, así como outras formas non redondas. O proceso pódese resumir como:
1.) O metal fundido bótase nun molde centrífugo. O metal é entón forzado ás paredes exteriores debido ao xiro do molde.
2.) A medida que o molde xira, a fundición de metal endurece
A fundición centrífuga é unha técnica axeitada para a produción de pezas cilíndricas ocas como tubos, sen necesidade de sprues, risers e elementos de compuerta, bo acabado superficial e características detalladas, sen problemas de encollemento, posibilidade de producir tubos longos con diámetros moi grandes, alta capacidade de produción. .
• FUNDACIÓN CONTINUA ( STRAND CASTING ): Úsase para fundir unha lonxitude continua de metal. Basicamente, o metal fundido é fundido nun perfil bidimensional do molde pero a súa lonxitude é indeterminada. Novo metal fundido introdúcese constantemente no molde mentres a fundición viaxa cara abaixo coa súa lonxitude aumentando co tempo. Os metais como o cobre, o aceiro e o aluminio son fundidos en longas cadeas mediante un proceso de fundición continua. O proceso pode ter varias configuracións, pero a común pódese simplificar como:
1.) O metal fundido bótase nun recipiente situado moi por riba do molde en cantidades e caudals ben calculados e flúe a través do molde arrefriado por auga. A fundición metálica vertida no molde solidifícase ata formar unha barra de arranque situada na parte inferior do molde. Esta barra de inicio dálle aos rolos algo ao que agarrarse inicialmente.
2.) A longa cadea metálica é levada por rolos a unha velocidade constante. Os rolos tamén cambian a dirección do fluxo de fío metálico de vertical a horizontal.
3.) Despois de que a fundición continua percorreu unha certa distancia horizontal, un facho ou serra que se move coa fundición córtaa rapidamente ás lonxitudes desexadas.
O proceso de fundición continua pódese integrar co PROCESO DE LAMINACIÓN, onde o metal de fundición continua pode ser alimentado directamente nun laminador para producir vigas en I, vigas en T... etc. A fundición continua produce propiedades uniformes en todo o produto, ten unha alta taxa de solidificación, reduce o custo debido á moi baixa perda de material, ofrece un proceso onde a carga de metal, o vertido, a solidificación, o corte e a eliminación da fundición teñen lugar nunha operación continua e resultando así unha alta taxa de produtividade e alta calidade. Non obstante, unha consideración importante é o alto investimento inicial, os custos de instalación e os requisitos de espazo.
• SERVIZOS DE MECANIZADO: Ofrecemos mecanizado de tres, catro e cinco eixos. O tipo de procesos de mecanizado que utilizamos son TORNEADO, FRESADO, PERFORADO, MANDRADO, BROCHADO, CESPILADO, ASERRADO, AFILADO, LAPEADO, PULIDO e MECANIZADO NON TRADICIONAL que se elabora máis adiante nun menú diferente da nosa web. Para a maior parte da nosa fabricación, usamos máquinas CNC. Non obstante, para algunhas operacións as técnicas convencionais encaixan mellor e, polo tanto, tamén confiamos nelas. As nosas capacidades de mecanizado alcanzan o nivel máis alto posible e algunhas pezas máis esixentes están fabricadas nunha planta certificada AS9100. As palas de motores a reacción requiren unha experiencia de fabricación altamente especializada e o equipo axeitado. A industria aeroespacial ten estándares moi estritos. Algúns compoñentes con estruturas xeométricas complexas fabrícanse máis facilmente mediante un mecanizado de cinco eixes, que só se atopa nalgunhas plantas de mecanizado, incluída a nosa. A nosa planta certificada aeroespacial ten a experiencia necesaria cumprindo os requisitos de documentación extenso da industria aeroespacial.
Nas operacións de TORNEADO, unha peza de traballo é xirada e móvese contra unha ferramenta de corte. Para este proceso estase a utilizar unha máquina chamada torno.
En FRESADO, unha máquina chamada fresadora ten unha ferramenta xiratoria para levar os bordos cortantes a unha peza de traballo.
As operacións de perforación implican unha fresa xiratoria con bordos cortantes que produce buracos ao contacto coa peza. En xeral utilízanse perforadoras, tornos ou molinos.
Nas operacións de ABADURADO, unha ferramenta cunha única punta de punta dobrada móvese a un burato áspero dunha peza de traballo xirando para ampliar lixeiramente o burato e mellorar a precisión. Utilízase para fins de acabado fino.
O BROCHADO consiste nunha ferramenta dentada para eliminar o material dunha peza de traballo nunha pasada da brocha (ferramenta dentada). No brochado lineal, a brocha corre linealmente contra unha superficie da peza de traballo para efectuar o corte, mentres que no brochado rotativo, a brocha é xirada e presionada na peza de traballo para cortar unha forma simétrica do eixe.
O MECANIZADO DE TIPO SUÍZO é unha das nosas valiosas técnicas que utilizamos para a fabricación de grandes volumes de pezas pequenas de alta precisión. Usando un torno de tipo suízo transformamos pezas pequenas, complexas e de precisión a un prezo económico. A diferenza dos tornos convencionais, nos que a peza se mantén estacionaria e a ferramenta en movemento, nos centros de torneado de tipo suízo, a peza pode moverse no eixe Z e a ferramenta está estacionaria. No mecanizado de tipo suízo, o stock de barras mantense na máquina e avanza a través dunha casquiña guía no eixe z, deixando só ao descuberto a parte a mecanizar. Deste xeito, garante un agarre firme e a precisión é moi alta. A dispoñibilidade de ferramentas activas ofrece a oportunidade de fresar e perforar a medida que o material avanza dende o buxo guía. O eixe Y dos equipos de tipo suízo ofrece capacidades de fresado completas e aforra moito tempo na fabricación. Ademais, as nosas máquinas dispoñen de brocas e ferramentas de mandrinar que operan sobre a peza cando se suxeita no subfuso. A nosa capacidade de mecanizado de tipo suízo ofrécenos unha oportunidade de mecanizado completo totalmente automatizado nunha soa operación.
O mecanizado é un dos maiores segmentos do negocio de AGS-TECH Inc. Utilizámolo como operación principal ou como operación secundaria despois da fundición ou extrusión dunha peza para que se cumpran todas as especificacións do deseño.
• SERVIZOS DE ACABADO DE SUPERFICIES: Ofrecemos unha gran variedade de tratamentos de superficie e acabados de superficies, como o acondicionamento de superficies para mellorar a adhesión, a deposición de fina capa de óxido para mellorar a adhesión do revestimento, chorro de area, película química, anodizado, nitruración, recubrimento en po, recubrimento por pulverización. , varias técnicas avanzadas de metalización e revestimento, incluíndo sputtering, feixe de electróns, evaporación, recubrimentos, recubrimentos duros como o diamante como o carbono (DLC) ou o revestimento de titanio para ferramentas de perforación e corte.
• SERVIZOS DE MARCADO E ETIQUETADO DE PRODUTOS: Moitos dos nosos clientes requiren marcado e etiquetado, marcado con láser, gravado en pezas metálicas. Se tes algunha necesidade, imos discutir cal é a mellor opción para ti.
Aquí tes algúns dos produtos de fundición metálica de uso común. Dado que estes están dispoñibles, pode aforrar en custos de moldes no caso de que algún destes se adapte ás súas necesidades:
PREME AQUÍ PARA DESCARGAR as nosas caixas de aluminio fundido da serie 11 de AGS-Electronics