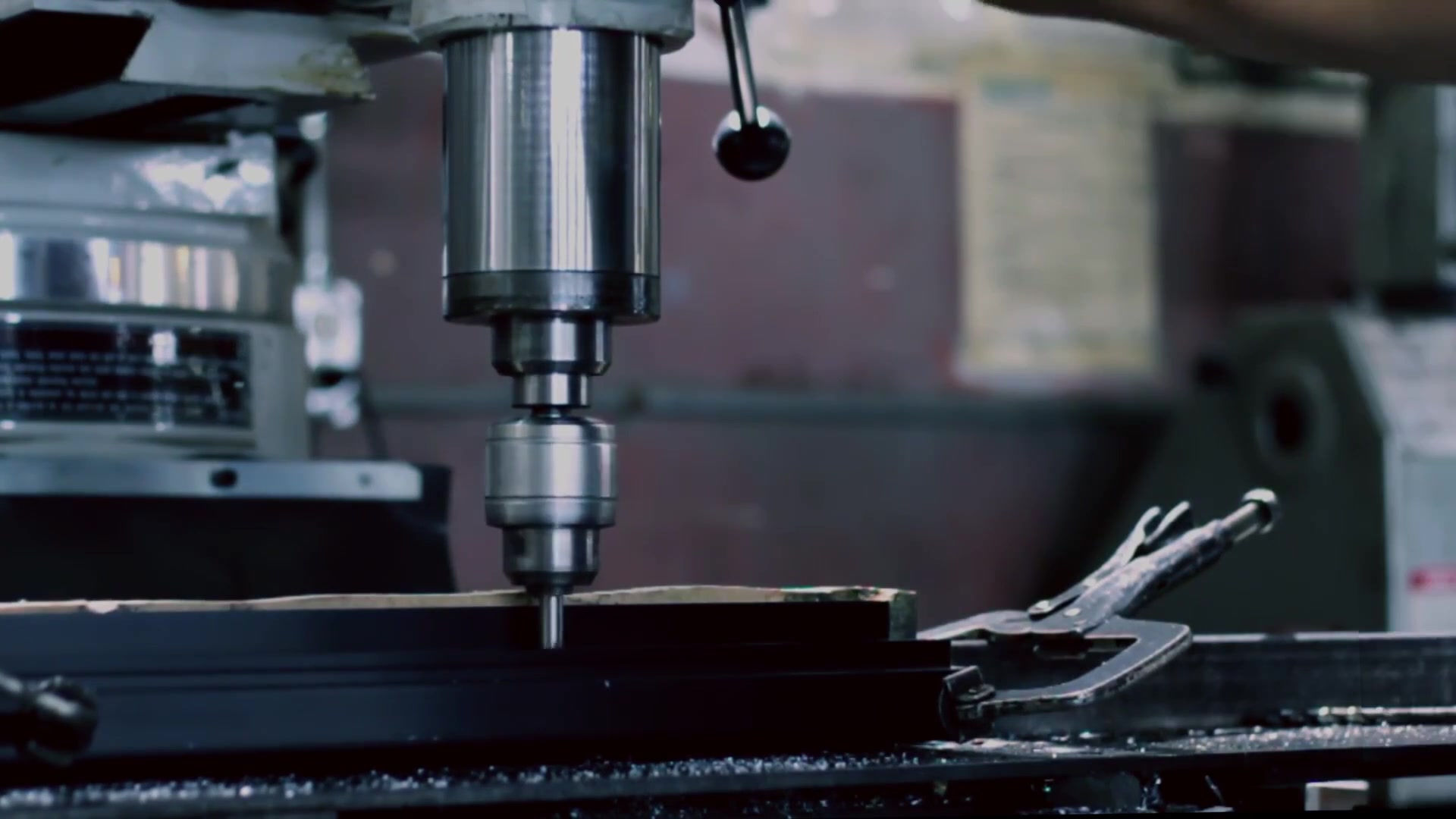
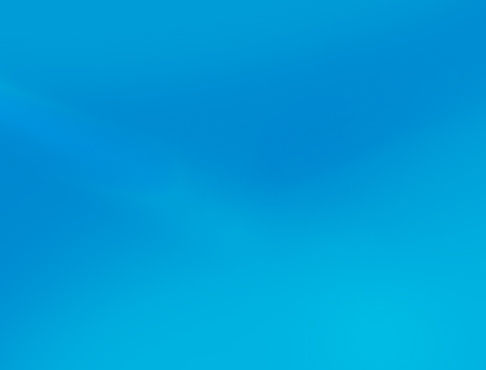
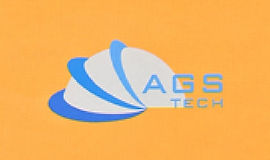
Fabricante global personalizado, integrador, consolidador, socio de outsourcing para unha ampla variedade de produtos e servizos.
Somos a súa fonte única para a fabricación, fabricación, enxeñaría, consolidación, integración e subcontratación de produtos e servizos fabricados a medida e dispoñibles.
Escolla o seu idioma
-
Fabricación personalizada
-
Fabricación por contrato nacional e global
-
Outsourcing de Manufactura
-
Compras domésticas e globais
-
Consolidación
-
Integración de enxeñería
-
Servizos de Enxeñaría
O tipo de fabricación de vidro que ofrecemos son vidro de envases, soplado de vidro, fibra de vidro e tubos e varilla, vidro doméstico e industrial, lámpadas e lámpadas, molduras de vidro de precisión, compoñentes e conxuntos ópticos, vidro plano e de folla e flotado. Realizamos tanto o conformado manual como a máquina.
Os nosos populares procesos de fabricación de cerámica técnica son o prensado con troquel, o prensado isostático, o prensado isostático en quente, o prensado en quente, a fundición deslizante, a fundición de cinta, a extrusión, o moldeo por inxección, o mecanizado en verde, a sinterización ou cocción, o rectificado de diamante, as montaxes herméticas.
Recomendamos que faga clic aquí para
DESCARGA as nosas ilustracións esquemáticas dos procesos de conformación e conformación de vidro de AGS-TECH Inc.
Estes ficheiros descargables con fotos e esbozos axudaranche a comprender mellor a información que che proporcionamos a continuación.
• FABRICACIÓN DE VIDRO DE CONTENEDOR: Contamos con liñas automatizadas de PRENSA E SOPLO e SOPLO E SOPLO para a súa fabricación. No proceso de golpe e soplado botamos un gob nun molde en branco e formamos o pescozo aplicando un golpe de aire comprimido desde arriba. Inmediatamente despois disto, inflárase aire comprimido unha segunda vez dende a outra dirección a través do pescozo do recipiente para formar a preforma da botella. A continuación, esta preforma transfírese ao molde real, quenta de novo para suavizar e aplícase aire comprimido para darlle á preforma a súa forma final de recipiente. Máis explícitamente, presúrase e empúxase contra as paredes da cavidade do molde de soplado para tomar a forma desexada. Finalmente, o recipiente de vidro fabricado trasládase a un forno de recocido para o seu posterior recalentamento e eliminación das tensións producidas durante o moldeado e arrefríase de forma controlada. No método de prensa e soplado, os gobs fundidos colócanse nun molde parison (molde en branco) e preséntanse na forma de parison (forma en branco). A continuación, os espazos en branco son transferidos a moldes de soplado e soplados de xeito similar ao proceso descrito anteriormente en "Proceso de soplado e soplado". Os pasos posteriores como o recocido e o alivio de tensión son similares ou iguais.
• SOPLADO DE VIDRO: estivemos fabricando produtos de vidro mediante o soplado manual convencional, así como utilizando aire comprimido con equipos automatizados. Para algúns pedidos é necesario o soplado convencional, como proxectos que impliquen obras de arte en vidro ou proxectos que requiren un número menor de pezas con tolerancias soltas, proxectos de prototipado/demo... etc. O soplado de vidro convencional implica mergullar un tubo metálico oco nunha pota de vidro fundido e facer xirar o tubo para recoller algunha cantidade de material de vidro. O vidro recollido na punta do tubo enróllase sobre ferro plano, da forma que se desexa, alargado, quentado de novo e soplado con aire. Cando estea listo, métese nun molde e bótase aire. A cavidade do molde está húmida para evitar o contacto do vidro co metal. A película de auga actúa como un coxín entre eles. O soplado manual é un proceso lento que require moito traballo e só é apto para prototipos ou artigos de alto valor, non é adecuado para pedidos de gran volume por peza barato.
• FABRICACIÓN DE VIDRO DOMÉSTICO E INDUSTRIAL: utilizando varios tipos de material de vidro estase producindo unha gran variedade de vidro. Algúns vasos son resistentes á calor e axeitados para vidro de laboratorio, mentres que outros son o suficientemente bos para soportar moitas veces os lavalouzas e son aptos para facer produtos domésticos. Usando máquinas Westlake estanse producindo decenas de miles de pezas de vasos ao día. Para simplificar, recóllese o vidro fundido ao baleiro e insírese en moldes para facer as preformas. Despois infórmase aire nos moldes, estes trasládanse a outro molde e bótase de novo aire e o vidro toma a súa forma definitiva. Como no soplado manual, estes moldes mantéñense mollados con auga. O estiramento adicional forma parte da operación de acabado onde se está formando o pescozo. O exceso de vidro está queimado. A continuación, o proceso controlado de requecemento e arrefriamento descrito anteriormente.
• FORMACIÓN DE TUBO DE VIDRO E VARILLA: Os principais procesos que utilizamos para a fabricación de tubos de vidro son os procesos DANNER e VELLO. No proceso Danner, o vidro dun forno flúe e cae sobre unha manga inclinada feita de materiais refractarios. A manga lévase sobre un eixe oco ou soplete xiratorio. A continuación, o vidro envólvese ao redor da manga e forma unha capa suave que flúe pola manga e sobre a punta do eixe. No caso do conformado de tubos, o aire é soprado por un soplete con punta oca, e no caso do conformado de varillas utilizamos puntas sólidas no eixe. A continuación, os tubos ou varillas pasan sobre os rolos de transporte. As dimensións como o espesor da parede e o diámetro dos tubos de vidro axústanse aos valores desexados configurando o diámetro da manga e insuflando presión de aire ao valor desexado, axustando a temperatura, a taxa de fluxo do vidro e a velocidade de extracción. O proceso de fabricación do tubo de vidro Vello, por outra banda, implica o vidro que sae dun forno a unha cunca cun mandril oco ou campá. O vidro atravesa entón o espazo de aire entre o mandril e a cunca e toma forma de tubo. Despois, viaxa sobre rolos ata unha máquina de debuxo e arrefríase. Ao final da liña de refrixeración prodúcese o corte e o procesamento final. As dimensións do tubo pódense axustar igual que no proceso Danner. Ao comparar o proceso Danner con Vello, podemos dicir que o proceso Vello é máis adecuado para a produción de grandes cantidades, mentres que o proceso Danner pode ser un mellor para pedidos precisos de tubos de menor volume.
• PROCESAMIENTO DE LÁMINAS E VIDRO PLANO E FLOTADOR: Dispoñemos de grandes cantidades de vidro plano en espesores que van desde espesores submilimétricos ata varios centímetros. As nosas lentes planas son dunha perfección case óptica. Ofrecemos vidro con revestimentos especiais como revestimentos ópticos, onde se utiliza a técnica de deposición química de vapor para poñer revestimentos como revestimentos antirreflectantes ou espellos. Tamén son comúns os revestimentos condutores transparentes. Tamén están dispoñibles os revestimentos hidrófobos ou hidrófilos sobre o vidro e un revestimento que fai que o vidro se autolimpe. Os lentes temperados, antibalas e laminados son outros elementos populares. Cortamos o vidro na forma desexada coas tolerancias desexadas. Existen outras operacións secundarias como curvar ou dobrar o vidro plano.
• MOLDEADO DE VIDRO DE PRECISIÓN: utilizamos esta técnica principalmente para fabricar compoñentes ópticos de precisión sen necesidade de técnicas máis caras e que consumen moito tempo, como esmerilado, lapeado e pulido. Esta técnica non sempre é suficiente para sacar o máximo proveito das mellores ópticas, pero nalgúns casos, como produtos de consumo, cámaras dixitais, ópticas médicas, pode ser unha boa opción menos custosa para a fabricación de gran volume. Tamén ten vantaxe sobre as outras técnicas de conformación de vidro onde se requiren xeometrías complexas, como no caso das asferas. O proceso básico consiste na carga da parte inferior do noso molde co branco de vidro, a evacuación da cámara de proceso para a eliminación de osíxeno, preto do peche do molde, o quecemento rápido e isotérmico da matriz e do vidro con luz infravermella, o peche adicional das metades do molde. presionar lentamente o vidro amolecido de forma controlada ata o espesor desexado, e finalmente arrefriar o vidro e encher a cámara con nitróxeno e eliminar o produto. O control preciso da temperatura, a distancia de peche do molde, a forza de peche do molde, a coincidencia dos coeficientes de expansión do molde e do material de vidro son fundamentais neste proceso.
• FABRICACIÓN DE COMPOÑENTES E CONXUNTOS ÓPTICOS DE VIDRO: Ademais do moldeado de precisión de vidro, utilizamos unha serie de procesos valiosos para fabricar compoñentes e conxuntos ópticos de alta calidade para aplicacións esixentes. Moer, lapear e pulir lentes de calidade óptica en lechadas abrasivas especiais finas é unha arte e ciencia para facer lentes ópticas, prismas, planos e moito máis. A planitude da superficie, a ondulación, a suavidade e as superficies ópticas sen defectos requiren moita experiencia con estes procesos. Pequenos cambios no ambiente poden producir produtos fóra das especificacións e deter a liña de fabricación. Hai casos nos que unha soa limpeza na superficie óptica cun pano limpo pode facer que un produto cumpra as especificacións ou falla a proba. Algúns materiais de vidro populares utilizados son sílice fundida, cuarzo, BK7. Tamén a montaxe de tales compoñentes require unha experiencia especializada en nichos. Ás veces úsanse colas especiais. Non obstante, ás veces unha técnica chamada contacto óptico é a mellor opción e non implica ningún material entre as lentes ópticas adxuntas. Consiste en poñer en contacto fisicamente superficies planas para unilas entre si sen pegar. Nalgúns casos, para ensamblar os compoñentes ópticos a determinadas distancias e con certas orientacións xeométricas, nalgúns casos, están a utilizarse separadores mecánicos, varillas ou bolas de vidro de precisión, abrazaderas ou compoñentes metálicos mecanizados. Imos examinar algunhas das nosas técnicas populares para fabricar ópticas de gama alta.
TRITURADO E LAPEADO E PULIDO: A forma rugosa do compoñente óptico obtense co moenda dun branco de vidro. Despois, o lapeado e o pulido realízanse xirando e fregando as superficies rugosas dos compoñentes ópticos contra ferramentas coas formas de superficie desexadas. Entre a óptica e as ferramentas de conformación están a verterse puríns con pequenas partículas abrasivas e fluídos. Os tamaños de partículas abrasivas en tales suspensións pódense escoller segundo o grao de planitude desexado. As desviacións das superficies ópticas críticas das formas desexadas exprésanse en termos de lonxitudes de onda da luz que se utiliza. A nosa óptica de alta precisión ten tolerancias de décimas de lonxitude de onda (Lonxitude de onda/10) ou é posible aínda máis axustado. Ademais do perfil da superficie, as superficies críticas son dixitalizadas e avalíanse para outras características e defectos da superficie, como dimensións, arañazos, astillas, pozos, manchas... etc. O estricto control das condicións ambientais na planta de fabricación de ópticas e os extensos requisitos de metroloxía e probas con equipos de última xeración fan desta industria unha rama desafiante.
• PROCESOS SECUNDARIOS NA FABRICACIÓN DE VIDRO: De novo, só estamos limitados coa túa imaxinación cando se trata de procesos secundarios e de acabado do vidro. Aquí enumeramos algúns deles:
-Recubrimentos sobre vidro (ópticos, eléctricos, tribolóxicos, térmicos, funcionais, mecánicos...). Por exemplo, podemos alterar as propiedades da superficie do vidro facendo que, por exemplo, reflicta a calor para manter frescos os interiores dos edificios, ou facer que un lado absorba os infravermellos mediante a nanotecnoloxía. Isto axuda a manter quente o interior dos edificios porque a capa superficial máis externa de vidro absorberá a radiación infravermella dentro do edificio e irradiala de volta ao interior.
-Grabado en vidro
- Etiquetado cerámico aplicado (ACL)
- Gravado
-Pulido á chama
-Pulido químico
-A mancha
FABRICACIÓN DE CERÁMICA TÉCNICA
• PRESENTACIÓN DE TROQUELAS: Consiste na compactación uniaxial de polvos granulares confinados nunha matriz.
• PRENSADO EN CALENTE: Similar ao prensado con troquel pero con adición de temperatura para mellorar a densificación. O po ou a preforma compactada colócase nunha matriz de grafito e aplícase presión uniaxial mentres a matriz se mantén a altas temperaturas, como 2000 C. As temperaturas poden ser diferentes dependendo do tipo de po cerámico que se procese. Para formas e xeometrías complicadas poden ser necesarios outros procesamentos posteriores, como a moenda con diamante.
• PRENSA ISOSTÁTICA: Pos granulares ou compactos prensados con troquel colócanse en recipientes herméticos e despois nun recipiente a presión pechado con líquido no interior. Despois son compactados aumentando a presión do recipiente a presión. O líquido no interior do recipiente transfire as forzas de presión uniformemente sobre toda a superficie do recipiente hermético. O material compáctase así uniformemente e toma a forma do seu recipiente flexible e do seu perfil e características internas.
• PRENSADO ISOSTÁTICO EN CALENTE: Similar ao prensado isostático, pero ademais da atmosfera de gas presurizado, sinterizamos o compacto a alta temperatura. O prensado isostático en quente dá como resultado unha densificación adicional e unha maior resistencia.
• FUNDACIÓN POR DESLIZACIÓN / FUNDACIÓN POR DRENADO: Enchemos o molde cunha suspensión de partículas cerámicas de tamaño micrómetro e líquido portador. Esta mestura chámase "deslizamento". O molde ten poros e, polo tanto, o líquido da mestura fíltrase no molde. Como resultado, fórmase un molde nas superficies internas do molde. Despois da sinterización, as pezas pódense sacar do molde.
• FUNDACIÓN DE CINTAS: Fabricamos cintas cerámicas fundindo pastas cerámicas sobre superficies planas móbiles. Os puríns conteñen pos cerámicos mesturados con outros produtos químicos para fins de unión e transporte. A medida que se evaporan os disolventes quedan láminas densas e flexibles de cerámica que se poden cortar ou enrolar como se desexe.
• FORMACIÓN POR EXTRUSIÓN: Como noutros procesos de extrusión, unha mestura suave de po cerámico con aglutinantes e outros produtos químicos pásase a través dunha matriz para adquirir a súa forma de sección transversal e despois córtase na lonxitude desexada. O proceso realízase con mesturas cerámicas frías ou quentadas.
• MOLDEADO POR INXECCIÓN A BAIXA PRESIÓN: Preparamos unha mestura de po cerámico con aglutinantes e disolventes e quentamos a unha temperatura onde poida ser facilmente presionado e forzado na cavidade da ferramenta. Unha vez que se completa o ciclo de moldeo, a peza é expulsada e o produto químico aglutinante é queimado. Usando o moldeado por inxección, podemos obter pezas complicadas en grandes volumes de forma económica. Son posibles orificios que son unha pequena fracción de milímetro nunha parede de 10 mm de espesor, pódense roscar sen máis mecanizado, tolerancias tan axustadas como +/- 0,5 % e aínda máis baixas cando se mecanizan pezas. , son posibles espesores de parede da orde de 0,5 mm a unha lonxitude de 12,5 mm, así como grosores de parede de 6,5 mm a unha lonxitude de 150 mm.
• MECANIZADO VERDE : Usando as mesmas ferramentas de mecanizado de metais, podemos mecanizar materiais cerámicos prensados mentres estean aínda brandos como o giz. Son posibles tolerancias de +/- 1%. Para mellores tolerancias usamos moenda de diamante.
• SINTERIZACIÓN ou COCCIÓN: A sinterización permite a densificación total. Prodúcese unha contracción significativa nas pezas compactas verdes, pero este non é un gran problema xa que temos en conta estes cambios dimensionais cando deseñamos a peza e as ferramentas. As partículas de po únense entre si e elimínase en gran medida a porosidade inducida polo proceso de compactación.
• MOLIENDA DE DIAMANTE: o “diamante” do material máis duro do mundo está a ser usado para moer materiais duros como cerámica e obtéñense pezas de precisión. Estase a conseguir tolerancias no rango micrométrico e superficies moi lisas. Debido ao seu custo, só consideramos esta técnica cando realmente a necesitamos.
• OS CONXUNTOS HERMÉTICOS son aqueles que practicamente non permiten ningún intercambio de materia, sólidos, líquidos ou gases entre interfaces. O selado hermético é hermético. Por exemplo, as caixas electrónicas herméticas son aquelas que manteñen o sensible contido interior dun dispositivo embalado ileso pola humidade, os contaminantes ou os gases. Nada é 100% hermético, pero cando falamos de hermeticidade queremos dicir que, en termos prácticos, que hai hermeticidade na medida en que a taxa de fuga é tan baixa que os dispositivos están seguros en condicións ambientais normais durante moito tempo. Os nosos conxuntos herméticos consisten en compoñentes de metal, vidro e cerámica, metal-cerámica, cerámica-metal-cerámica, metal-cerámica-metal, metal a metal, metal-vidro, metal-vidro-metal, vidro-metal-vidro, vidro. metal e vidro a vidro e todas as outras combinacións de unión metal-vidro-cerámica. Podemos, por exemplo, recubrir de metal os compoñentes cerámicos para que poidan unirse fortemente a outros compoñentes do conxunto e ter unha excelente capacidade de selado. Temos o know-how de revestir fibras ópticas ou pasadores con metal e soldalas ou soldalas aos recintos, para que non pasen nin se filtren gases aos recintos. Polo tanto, utilízanse para a fabricación de caixas electrónicas para encapsular dispositivos sensibles e protexelos da atmosfera exterior. Ademais das súas excelentes características de selado, outras propiedades como o coeficiente de expansión térmica, resistencia á deformación, natureza sen desgasificación, vida útil moi longa, natureza non condutora, propiedades de illamento térmico, natureza antiestática... etc. facer que os materiais de vidro e cerámica sexan a elección para determinadas aplicacións. A información sobre as nosas instalacións que producen accesorios de cerámica a metal, selado hermético, pasadores de baleiro, baleiro alto e ultraalto e compoñentes de control de fluídos pódese atopar aquí:Folleto da fábrica de compoñentes herméticos