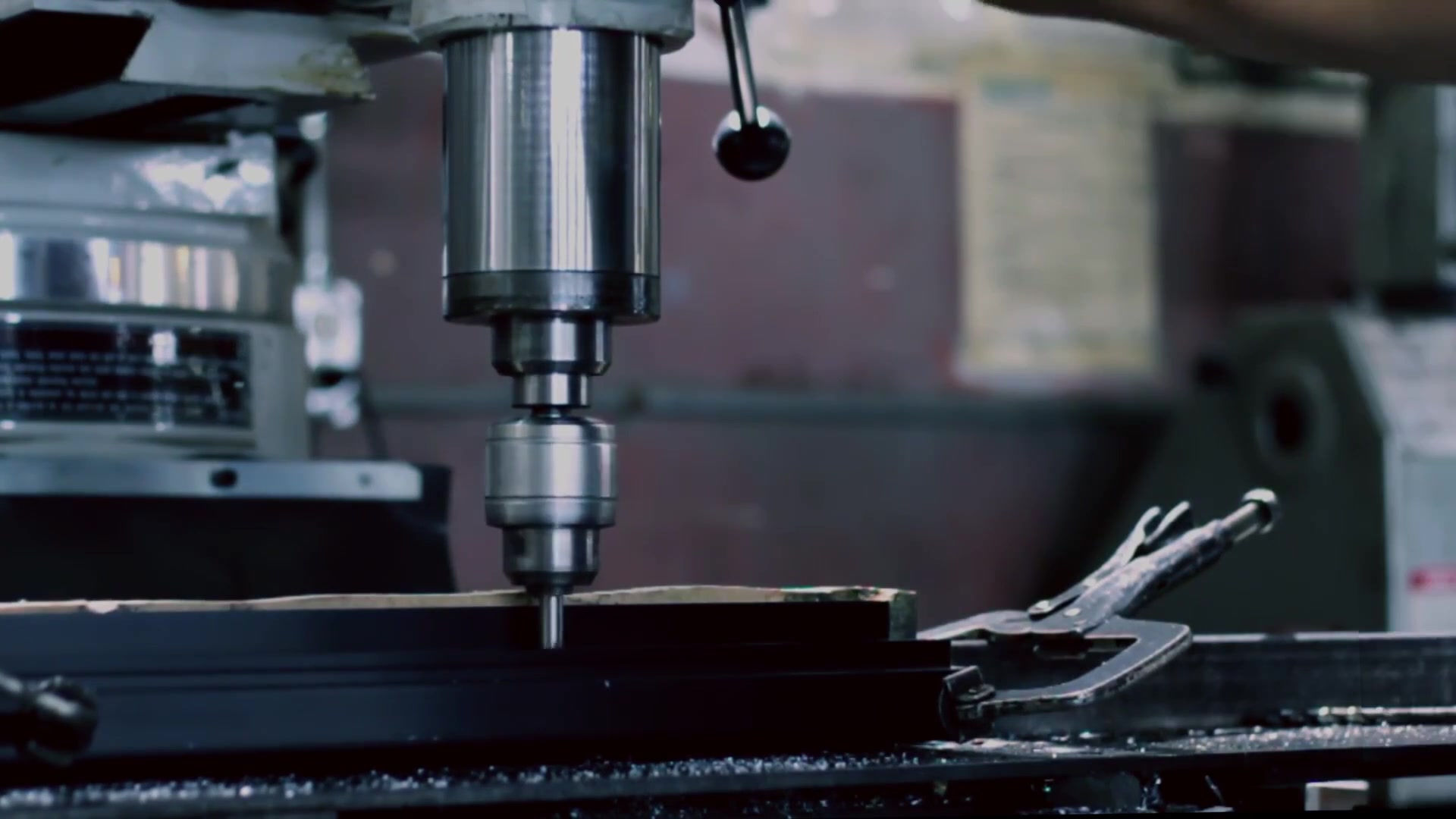
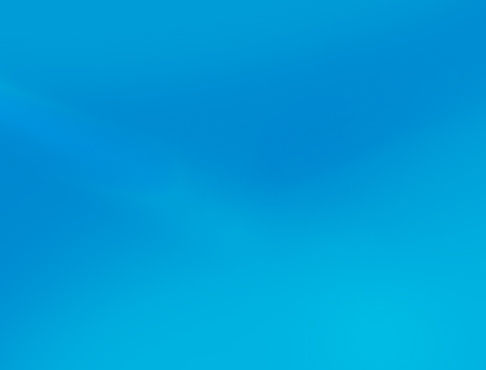
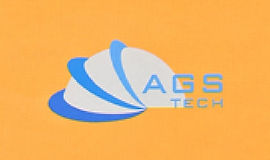
Fabricante global personalizado, integrador, consolidador, socio de outsourcing para unha ampla variedade de produtos e servizos.
Somos a súa fonte única para a fabricación, fabricación, enxeñaría, consolidación, integración e subcontratación de produtos e servizos fabricados a medida e dispoñibles.
Escolla o seu idioma
-
Fabricación personalizada
-
Fabricación por contrato nacional e global
-
Outsourcing de Manufactura
-
Compras domésticas e globais
-
Consolidación
-
Integración de enxeñería
-
Servizos de Enxeñaría
Unimos, montamos e suxeitamos as súas pezas manufacturadas e convertémolas en produtos acabados ou semielaborados mediante SOLDADURA, SOLDADURA, SINTERIZACIÓN, ENGOLADO ADHESIVO, FIXACIÓN, EMPRUNTADO. Algúns dos nosos procesos de soldadura máis populares son arco, gas oxicombustible, resistencia, proxección, costura, alteración, percusión, estado sólido, feixe de electróns, láser, termita, soldadura por indución. Os nosos procesos de soldadura máis populares son o soplete, a indución, o forno e a soldadura por inmersión. Os nosos métodos de soldadura son ferro, placa quente, forno, indución, inmersión, onda, refluxo e soldadura por ultrasóns. Para a unión adhesiva usamos con frecuencia termoplásticos e termoestables, epoxi, fenólicos, poliuretano, aliaxes adhesivas, así como algúns outros produtos químicos e cintas. Finalmente, os nosos procesos de suxeición consisten en cravar, aparafusar, porcas e parafusos, remachar, enganchar, enganchar, pegar e grapar e encaixar a prensa.
• SOLDADURA: A soldadura consiste na unión de materiais mediante a fusión das pezas de traballo e a introdución de materiais de recheo, que tamén se unen ao baño de soldadura fundido. Cando a zona arrefría, obtemos unha xunta forte. Nalgúns casos aplícase presión. Ao contrario da soldadura, as operacións de soldadura e soldadura só implican a fusión dun material con menor punto de fusión entre as pezas de traballo, e as pezas non se funden. Recomendamos que faga clic aquí paraDESCARGA as nosas ilustracións esquemáticas de procesos de soldadura de AGS-TECH Inc.
Isto axudarache a comprender mellor a información que che proporcionamos a continuación.
En SOLDADURA POR ARCO, utilizamos unha fonte de alimentación e un electrodo para crear un arco eléctrico que funde os metais. O punto de soldadura está protexido por un gas ou vapor de protección ou outro material. Este proceso é popular para soldar pezas de automóbiles e estruturas de aceiro. Na soldadura por arco metálico protexido (SMAW) ou tamén coñecida como soldadura por varilla, achégase unha varilla de electrodo ao material base e xérase un arco eléctrico entre eles. A varilla do electrodo funde e actúa como material de recheo. O electrodo tamén contén fluxo que actúa como unha capa de escoura e desprende vapores que actúan como gas protector. Estes protexen a zona de soldadura da contaminación ambiental. Non se están a utilizar outros recheos. As desvantaxes deste proceso son a súa lentitude, a necesidade de substituír os electrodos con frecuencia, a necesidade de descascarar as escouras residuais orixinadas polo fluxo. Varios metais como ferro, aceiro, níquel, aluminio, cobre, etc. Pódese soldar. As súas vantaxes son as súas ferramentas económicas e a facilidade de uso. Soldadura por arco metálico con gas (GMAW) tamén coñecida como gas metal-inerte (MIG), temos a alimentación continua dun recheo de fío de electrodo consumible e un gas inerte ou parcialmente inerte que flúe ao redor do fío contra a contaminación ambiental da rexión de soldadura. Pódense soldar aceiro, aluminio e outros metais non férreos. As vantaxes do MIG son as altas velocidades de soldadura e a boa calidade. As desvantaxes son os seus complicados equipos e os retos aos que se enfrontan en ambientes exteriores ventosos porque temos que manter estable o gas protector ao redor da zona de soldadura. Unha variación de GMAW é a soldadura por arco con núcleo de fluxo (FCAW) que consiste nun tubo de metal fino cheo de materiais fundentes. Ás veces, o fluxo dentro do tubo é suficiente para protexerse da contaminación ambiental. A soldadura por arco mergullado (SAW) é un proceso amplamente automatizado, que implica unha alimentación continua do fío e un arco que se produce baixo unha capa de cuberta de fluxo. As taxas de produción e a calidade son altas, a escoria de soldadura despréndese facilmente e temos un ambiente de traballo libre de fume. A desvantaxe é que só se pode usar para soldar parts en determinadas posicións. Na soldadura por arco de tungsteno con gas (GTAW) ou soldadura con gas tungsteno-inerte (TIG) usamos un electrodo de tungsteno xunto cun recheo separado e gases inertes ou case inertes. Como sabemos, o volframio ten un alto punto de fusión e é un metal moi axeitado para temperaturas moi altas. O volframio en TIG non se consume ao contrario dos outros métodos explicados anteriormente. Unha técnica de soldadura lenta pero de alta calidade vantaxosa sobre outras técnicas na soldadura de materiais finos. Adecuado para moitos metais. A soldadura por arco de plasma é similar pero usa gas plasma para crear o arco. O arco na soldadura por arco de plasma é relativamente máis concentrado en comparación co GTAW e pódese usar para unha gama máis ampla de espesores de metal a velocidades moito máis altas. A soldadura por arco de plasma e GTAW pódese aplicar a máis ou menos os mesmos materiais.
A SOLDADURA OXY-FUEL / OXYFUEL tamén chamada soldadura de oxiacetileno, a soldadura de oxi, a soldadura de gas realízase utilizando combustibles de gas e osíxeno para soldar. Dado que non se utiliza enerxía eléctrica é portátil e pódese usar onde non hai electricidade. Usando un soplete quentamos as pezas e o material de recheo para producir unha piscina de metal fundido compartido. Pódense empregar varios combustibles como acetileno, gasolina, hidróxeno, propano, butano, etc. Na soldadura de oxicombustibles empregamos dous recipientes, un para o combustible e outro para osíxeno. O osíxeno oxida o combustible (queimao).
SOLDADURA POR RESISTENCIA: Este tipo de soldadura aproveita o quecemento en joule e xérase calor no lugar onde se aplica corrente eléctrica durante un tempo determinado. Polo metal pásanse correntes elevadas. Neste lugar fórmanse piscinas de metal fundido. Os métodos de soldadura por resistencia son populares debido á súa eficiencia, pouco potencial de contaminación. Non obstante, as desvantaxes son que os custos dos equipos son relativamente importantes e a limitación inherente a pezas de traballo relativamente delgadas. A SOLDADURA POR PUNTOS é un dos principais tipos de soldadura por resistencia. Aquí unimos dúas ou máis follas ou pezas de traballo superpostas usando dous electrodos de cobre para unir as follas e facer pasar unha corrente elevada a través delas. O material entre os electrodos de cobre quéntase e nese lugar xérase unha piscina fundida. A corrente detense entón e as puntas dos electrodos de cobre arrefrían a localización da soldadura porque os electrodos están arrefriados por auga. Aplicar a cantidade correcta de calor ao material e grosor correctos é fundamental para esta técnica, xa que se se aplica incorrectamente a unión será débil. A soldadura por puntos ten as vantaxes de non provocar deformacións significativas nas pezas de traballo, eficiencia enerxética, facilidade de automatización e excelentes taxas de produción e non require ningún recheo. A desvantaxe é que, dado que a soldadura ten lugar en puntos en lugar de formar unha costura continua, a resistencia global pode ser relativamente menor en comparación con outros métodos de soldadura. A SOLDADURA DE COSTURA, pola súa banda, produce soldaduras nas superficies de contacto de materiais similares. A costura pode ser a tope ou solapada. A soldadura de costura comeza nun extremo e vaise progresivamente cara ao outro. Este método tamén usa dous electrodos de cobre para aplicar presión e corrente á rexión de soldadura. Os electrodos en forma de disco xiran con contacto constante ao longo da liña de costura e fan unha soldadura continua. Aquí tamén, os electrodos son arrefriados por auga. As soldaduras son moi fortes e fiables. Outros métodos son as técnicas de soldadura por proxección, flash e revolto.
A SOLDADURA EN ESTADO SÓLIDO é un pouco diferente dos métodos anteriores explicados anteriormente. A coalescencia ten lugar a temperaturas inferiores á temperatura de fusión dos metais unidos e sen uso de recheo metálico. A presión pódese utilizar nalgúns procesos. Varios métodos son a SOLDADURA POR COEXTRUSIÓN na que se extruyen metais diferentes a través da mesma matriz, a SOLDADURA A PRESIÓN FRÍA onde unimos aliaxes brandas por debaixo dos seus puntos de fusión, a SOLDADURA POR DIFUSIÓN unha técnica sen liñas de soldadura visibles, a SOLDADURA POR EXPLOSIÓN para unir materiais diferentes, por exemplo, aliaxes resistentes á corrosión a estruturas. aceiros, SOLDADURA POR IMPULSO ELECTROMAGNÉTICO onde aceleramos tubos e chapas por forzas electromagnéticas, SOLDADURA DE FORXA que consiste en quentar os metais a altas temperaturas e martelalos entre si, SOLDADURA POR FRCCIÓN onde se realiza coa suficiente soldadura por rozamento, SOLDADURA POR FRICCIÓN SISTIR que implica un ferramenta consumible que atravesa a liña de unión, SOLDADURA POR PRESIÓN CALENTE onde presionamos os metais xuntos a temperaturas elevadas por debaixo da temperatura de fusión no baleiro ou gases inertes, SOLDADURA POR PRESIÓN ISOSTÁTICA CALENTE un proceso no que aplicamos presión mediante gases inertes no interior dun recipiente, SOLDADURA POR RODOLO onde unimos materiais diferentes forzándoos entre eles dúas rodas xiratorias, SOLDADURA ULTRASONICA onde se sueldan láminas finas de metal ou plástico mediante enerxía vibratoria de alta frecuencia.
Outros dos nosos procesos de soldadura son a SOLDADURA POR FIXES ELECTRÓNICOS con penetración profunda e procesamento rápido, pero sendo un método caro considerámolo para casos especiais, SOLDADURA ELECTROSALGADA un método axeitado para placas de grosor e pezas de aceiro só, SOLDADURA POR INDUCCIÓN onde utilizamos indución electromagnética e quentar as nosas pezas eléctricamente condutoras ou ferromagnéticas, SOLDADURA LÁSER tamén cunha penetración profunda e procesamento rápido pero un método caro, SOLDADURA LÁSER HÍBRIDA que combina LBW con GMAW no mesmo cabezal de soldadura e capaz de salvar ocos de 2 mm entre placas, SOLDADURA POR PERCUSIÓN que implica unha descarga eléctrica seguida de forxa dos materiais coa presión aplicada, SOLDADURA TÉRMICA que implica reacción exotérmica entre po de aluminio e óxido de ferro., SOLDADURA ELECTROGÁS con electrodos consumibles e empregada só con aceiro en posición vertical, e finalmente SOLDADURA POR ARCO DE PERNOS para a unión de pernos a base. material con calor e presión.
Recomendamos que faga clic aquí paraDESCARGA as nosas ilustracións esquemáticas dos procesos de soldadura, soldadura e unión adhesiva de AGS-TECH Inc
Isto axudarache a comprender mellor a información que che proporcionamos a continuación.
• SOLDADURA: Unimos dous ou máis metais quentando metais de recheo entre eles por encima dos seus puntos de fusión e empregando a acción capilar para estenderse. O proceso é similar á soldadura, pero as temperaturas implicadas para fundir o recheo son máis altas na soldadura. Do mesmo xeito que na soldadura, o fluxo protexe o material de recheo da contaminación atmosférica. Despois do arrefriamento, as pezas únense entre si. O proceso implica os seguintes pasos clave: bo axuste e separación, limpeza adecuada dos materiais de base, fixación adecuada, selección adecuada do fluxo e da atmosfera, quecemento do conxunto e finalmente a limpeza do conxunto soldado. Algúns dos nosos procesos de soldadura son o SOPORTE CON TORCH, un método popular que se realiza manualmente ou de forma automatizada. É axeitado para pedidos de produción de baixo volume e casos especializados. A calor aplícase usando chamas de gas preto da unión que se está soldando. A SOLDADURA A FORNO require menos habilidade do operador e é un proceso semiautomático axeitado para a produción industrial en masa. Tanto o control da temperatura como o control da atmosfera no forno son vantaxes desta técnica, porque a primeira permite ter ciclos de calor controlados e eliminar o quecemento local como é o caso da soldadura con soplete, e a segunda protexe a peza da oxidación. Usando jigging somos capaces de reducir os custos de fabricación ao mínimo. As desvantaxes son o alto consumo de enerxía, os custos dos equipos e consideracións de deseño máis desafiantes. A SOLDADURA A VALO realízase nun forno de baleiro. Mantense a uniformidade da temperatura e obtemos unións sen fluxo, moi limpas e con moi poucos esforzos residuais. Os tratamentos térmicos poden realizarse durante a soldadura ao baleiro, debido ás baixas tensións residuais presentes durante os ciclos lentos de quecemento e arrefriamento. A principal desvantaxe é o seu alto custo porque a creación dun ambiente de baleiro é un proceso caro. Outra técnica de soldadura por inmersión une pezas fixas onde se aplica o composto de soldadura ás superficies de acoplamento. Despois, as pezas fixtured son mergulladas nun baño dun sal fundido como o cloruro de sodio (sal de mesa) que actúa como medio de transferencia de calor e fluxo. O aire está excluído e, polo tanto, non se produce formación de óxidos. En SOLDADURA POR INDUCIÓN unimos materiais mediante un metal de recheo que ten un punto de fusión máis baixo que os materiais de base. A corrente alterna da bobina de indución crea un campo electromagnético que induce quecemento por indución en materiais magnéticos principalmente férreos. O método proporciona quecemento selectivo, boas xuntas con recheos que só flúen nas áreas desexadas, pouca oxidación porque non hai chamas e o arrefriamento é rápido, quentamento rápido, consistencia e idoneidade para a fabricación de gran volume. Para axilizar os nosos procesos e garantir a coherencia, utilizamos con frecuencia preformas. A información sobre as nosas instalacións de soldadura que producen accesorios de cerámica a metal, selado hermético, pasaxes ao baleiro, baleiro alto e ultraalto e compoñentes de control de fluídos pódese atopar aquí:_cc781905-5cde-bb31905-5cde-bb31984Folleto de Brazing Factory
• SOLDADURA : Na soldadura non temos fusión das pezas de traballo, senón un metal de aporte cun punto de fusión inferior ao das pezas de unión que desemboca na unión. O metal de recheo na soldadura funde a temperatura máis baixa que na soldadura. Usamos aliaxes sen chumbo para soldar e cumprimos RoHS e para diferentes aplicacións e requisitos temos aliaxes diferentes e adecuadas, como a aliaxe de prata. A soldadura ofrécenos unións estancas a gases e líquidos. En SOLDADURA BLANDA, o noso metal de recheo ten un punto de fusión inferior a 400 centígrados, mentres que en SOLDADURA DE PRATA e SOLDADURA necesitamos temperaturas máis altas. A soldadura suave usa temperaturas máis baixas pero non resulta en xuntas fortes para aplicacións esixentes a temperaturas elevadas. A soldadura de prata, por outra banda, require altas temperaturas proporcionadas polo facho e dános unións fortes e adecuadas para aplicacións a altas temperaturas. A soldadura esixe as temperaturas máis altas e normalmente úsase un facho. Dado que as xuntas de soldadura son moi fortes, son un bo candidato para reparar obxectos pesados de ferro. Nas nosas liñas de fabricación utilizamos tanto soldadura manual manual como liñas de soldadura automatizadas. A SOLDADURA POR INDUCCIÓN utiliza corrente alterna de alta frecuencia nunha bobina de cobre para facilitar o quecemento por indución. Indúcense correntes na parte soldada e, como resultado, xérase calor na alta resistencia joint. Esta calor derrete o metal de recheo. Tamén se usa fluxo. A soldadura por indución é un bo método para soldar cilindros e tubos nun proceso continuo envolvendo as bobinas ao seu redor. Soldar algúns materiais como grafito e cerámica é máis difícil porque require o revestimento das pezas cun metal adecuado antes da soldadura. Isto facilita a unión interfacial. Soldamos estes materiais especialmente para aplicacións de envases herméticos. Fabricamos as nosas placas de circuíto impreso (PCB) en gran volume, principalmente mediante SOLDADURA DE ONDA. Só para pequenas cantidades de prototipos utilizamos soldadura manual mediante soldador. Usamos soldadura por ondas tanto para conxuntos de PCB de montaxe en superficie (PCBA) como de orificios pasantes. Unha cola temporal mantén os compoñentes unidos á placa de circuíto e o conxunto colócase nun transportador e móvese a través dun equipo que contén soldadura fundida. Primeiro o PCB é fluxo e despois entra na zona de prequecemento. A soldadura fundida está nunha tixola e ten un patrón de ondas estacionarias na súa superficie. Cando o PCB se move sobre estas ondas, estas ondas entran en contacto coa parte inferior do PCB e adhírense ás almofadas de soldadura. A soldadura permanece só en pins e almofadas e non na propia PCB. As ondas na soldadura fundida teñen que estar ben controladas para que non haxa salpicaduras e as partes superiores das ondas non toquen e contaminen áreas non desexadas das placas. En REFLOW SOLDERING, usamos unha pasta de soldadura pegajosa para unir temporalmente os compoñentes electrónicos ás placas. A continuación, as táboas pasan por un forno de refluxo con control de temperatura. Aquí a soldadura se funde e conecta os compoñentes de forma permanente. Usamos esta técnica tanto para compoñentes de montaxe en superficie como para compoñentes de orificios pasantes. O control adecuado da temperatura e o axuste das temperaturas do forno é fundamental para evitar a destrución dos compoñentes electrónicos da placa por sobrequentamento por encima dos seus límites máximos de temperatura. No proceso de soldadura por refluxo, en realidade temos varias rexións ou etapas cada unha cun perfil térmico distinto, como o paso de prequecemento, o paso de remollo térmico, os pasos de refluxo e de arrefriamento. Estes diferentes pasos son esenciais para unha soldadura por refluxo sen danos dos conxuntos de placas de circuíto impreso (PCBA). A SOLDADURA POR ULTRASONS é outra técnica de uso frecuente con capacidades únicas: pódese usar para soldar vidro, cerámica e materiais non metálicos. Por exemplo, os paneis fotovoltaicos que non son metálicos necesitan electrodos que se poidan colocar mediante esta técnica. Na soldadura por ultrasóns, implantamos unha punta de soldadura quente que tamén emite vibracións ultrasónicas. Estas vibracións producen burbullas de cavitación na interface do substrato co material de soldadura fundido. A enerxía implosiva da cavitación modifica a superficie do óxido e elimina a sucidade e os óxidos. Durante este tempo tamén se forma unha capa de aliaxe. A soldadura na superficie de unión incorpora osíxeno e permite a formación dunha forte unión compartida entre o vidro e a soldadura. A SOLDADURA POR INMERSIÓN pode considerarse como unha versión máis sinxela da soldadura por onda adecuada só para a produción a pequena escala. O primeiro fluxo de limpeza aplícase como noutros procesos. Os PCB con compoñentes montados son mergullados manualmente ou de forma semiautomatizada nun tanque que contén soldadura fundida. A soldadura fundida adhírese ás áreas metálicas expostas sen protección pola máscara de soldadura no taboleiro. O equipo é sinxelo e barato.
• ENLACE ADHESIVO: Esta é outra técnica popular que utilizamos con frecuencia e consiste na unión de superficies mediante colas, epoxi, axentes plásticos ou outros produtos químicos. A unión realízase mediante a evaporación do disolvente, o curado térmico, o curado por luz UV, o curado a presión ou agardando un tempo determinado. Nas nosas liñas de produción utilízanse varias colas de alto rendemento. Cuns procesos de aplicación e curado debidamente deseñados, a unión adhesiva pode producir unións de tensión moi baixa, fortes e fiables. As unións adhesivas poden ser bos protectores contra factores ambientais como humidade, contaminantes, corrosivos, vibracións, etc. As vantaxes da unión adhesiva son: pódense aplicar a materiais que doutro xeito serían difíciles de soldar, soldar ou soldar. Tamén pode ser preferible para materiais sensibles á calor que serían danados pola soldadura ou outros procesos de alta temperatura. Outras vantaxes dos adhesivos son que poden aplicarse a superficies de forma irregular e aumentar o peso da montaxe en cantidades moi moi pequenas en comparación con outros métodos. Tamén os cambios dimensionais nas pezas son moi mínimos. Algunhas colas teñen propiedades de coincidencia de índices e pódense usar entre compoñentes ópticos sen diminuír significativamente a intensidade do sinal de luz ou óptico. As desvantaxes, por outra banda, son os tempos de curado máis longos que poden ralentizar as liñas de fabricación, os requisitos de fixación, os requisitos de preparación da superficie e a dificultade para desmontar cando se precisa un retraballo. A maioría das nosas operacións de unión adhesiva implican os seguintes pasos:
-Tratamento de superficies: son habituais procedementos especiais de limpeza como a limpeza con auga desionizada, a limpeza con alcohol, a limpeza de plasma ou de coroa. Despois da limpeza podemos aplicar promotores de adherencia nas superficies para asegurar as mellores unións posibles.
-Fijación de pezas: tanto para a aplicación de adhesivo como para o curado, deseñamos e utilizamos accesorios personalizados.
-Aplicación de adhesivos: ás veces utilizamos sistemas manuais, e outras segundo o caso, automatizados como robótica, servomotores, actuadores lineais para entregar os adhesivos no lugar correcto e utilizamos dispensadores para entregalos no volume e cantidade adecuados.
-Curamento: dependendo do adhesivo, podemos utilizar o secado e o curado sinxelos, así como o curado baixo luces UV que actúan como catalizador ou curado térmico nun forno ou mediante elementos calefactores resistivos montados en plantillas e accesorios.
Recomendamos que faga clic aquí paraDESCARGA as nosas ilustracións esquemáticas dos procesos de fixación de AGS-TECH Inc.
Isto axudarache a comprender mellor a información que che proporcionamos a continuación.
• PROCESOS DE FIXACIÓN: Os nosos procesos de unión mecánica divídense en dúas categorías: FIXADORS e UNIDADES INTEGRALES. Exemplos de elementos de fixación que usamos son parafusos, pasadores, porcas, parafusos, remaches. Exemplos de xuntas integrais que usamos son os encaixes, as costuras e os engastes. Usando unha variedade de métodos de fixación, asegurámonos de que as nosas unións mecánicas sexan fortes e fiables durante moitos anos de uso. OS PARAFUSOS e os parafusos son algúns dos elementos de fixación máis utilizados para suxeitar e colocar obxectos. Os nosos parafusos e parafusos cumpren as normas ASME. Implíganse varios tipos de parafusos e parafusos, incluíndo parafusos hexagonales e parafusos hexagonales, parafusos e parafusos, parafusos de dobre punta, parafuso de espiga, parafuso de ollo, parafuso de espello, parafuso de chapa, parafuso de axuste fino, parafusos autoperforantes e autorroscantes. , parafuso de fixación, parafusos con arandelas incorporadas,... e moito máis. Temos varios tipos de cabeza de parafuso, como cabeza avellanada, cúpula, redonda, con brida e varios tipos de unidades de parafuso, como ranura, Phillips, cadrada, hexagonal. Pola súa banda, un RIVET é un elemento de fixación mecánico permanente que consiste nun eixe cilíndrico liso e unha cabeza por unha banda. Despois da inserción, o outro extremo do remache defórmase e o seu diámetro se expande para que quede no seu lugar. Noutras palabras, antes da instalación un remache ten unha cabeza e despois da instalación ten dúas. Instalamos varios tipos de remaches dependendo da aplicación, resistencia, accesibilidade e custo, como remaches de cabeza sólida/redondo, estruturais, semitubulares, cegos, oscar, drive, enrasados, de bloqueo por fricción, autoperforantes. O remache pode ser preferido nos casos en que se debe evitar a deformación térmica e o cambio nas propiedades do material debido á calor de soldadura. O remachado tamén ofrece un peso lixeiro e especialmente unha boa resistencia e resistencia contra as forzas de corte. Contra as cargas de tracción, non obstante, os parafusos, porcas e parafusos poden ser máis axeitados. No proceso de CLINCHING utilizamos punzóns e matrices especiais para formar un enclavamiento mecánico entre as chapas que se unen. O punzón empurra as capas de chapa na cavidade da matriz e resulta na formación dunha unión permanente. Non se require ningún quentamento nin arrefriamento no clinch e é un proceso de traballo en frío. É un proceso económico que pode substituír a soldadura por puntos nalgúns casos. En PINNING usamos pasadores que son elementos da máquina que se utilizan para asegurar posicións das pezas da máquina entre si. Os principais tipos son pasadores de horquilla, pasadores de chaveta, pasadores de resorte, pasadores de pasadores, e pasadores divididos. En STAPLING utilizamos pistolas de grapado e grapas que son fixadores de dúas puntas que se usan para unir ou unir materiais. O grapado ten as seguintes vantaxes: Económico, sinxelo e rápido de usar, a coroa das grapas pódese usar para unir materiais unidos entre si, A coroa da grapa pode facilitar a ponte dunha peza como un cable e suxeitala a unha superficie sen perforar ou prexudicial, eliminación relativamente fácil. O MONTADO A PRENSA realízase empuxando pezas xuntas e a fricción entre elas fixa as pezas. As pezas axustadas a presión que consisten nun eixe sobredimensionado e un burato de tamaño inferior ensamblan xeralmente por un dos dous métodos: ben aplicando forza ou aproveitando a expansión ou contracción térmica das pezas. Cando se establece un accesorio de prensa aplicando unha forza, utilizamos unha prensa hidráulica ou unha prensa manual. Por outra banda, cando se establece o encaixe a prensa por expansión térmica, quentamos as pezas envolventes e montamos no seu lugar estando quentes. Cando se arrefrían contraen e volven ás súas dimensións normais. Isto dá como resultado un bo axuste de prensa. Chamámoslle a isto alternativamente SHRINK-FITTING. A outra forma de facelo é arrefriando as pezas envolventes antes da montaxe e despois deslizándoas nas súas partes de acoplamento. Cando se quenta o conxunto expándense e conseguimos un axuste axustado. Este último método pode ser preferible nos casos en que o quecemento supón o risco de alterar as propiedades do material. O arrefriamento é máis seguro neses casos.
Compoñentes e conxuntos pneumáticos e hidráulicos
• Válvulas, compoñentes hidráulicos e pneumáticos como junta tórica, arandela, xuntas, xunta, anel, cuña.
Dado que as válvulas e os compoñentes pneumáticos veñen nunha gran variedade, non podemos enumerar todo aquí. Dependendo do ambiente físico e químico da súa aplicación, temos produtos especiais para vostede. Especifíquenos a aplicación, o tipo de compoñente, as especificacións, as condicións ambientais como presión, temperatura, líquidos ou gases que estarán en contacto coas súas válvulas e compoñentes pneumáticos; e escolleremos o produto máis axeitado para ti ou fabricarémolo especialmente para a túa aplicación.