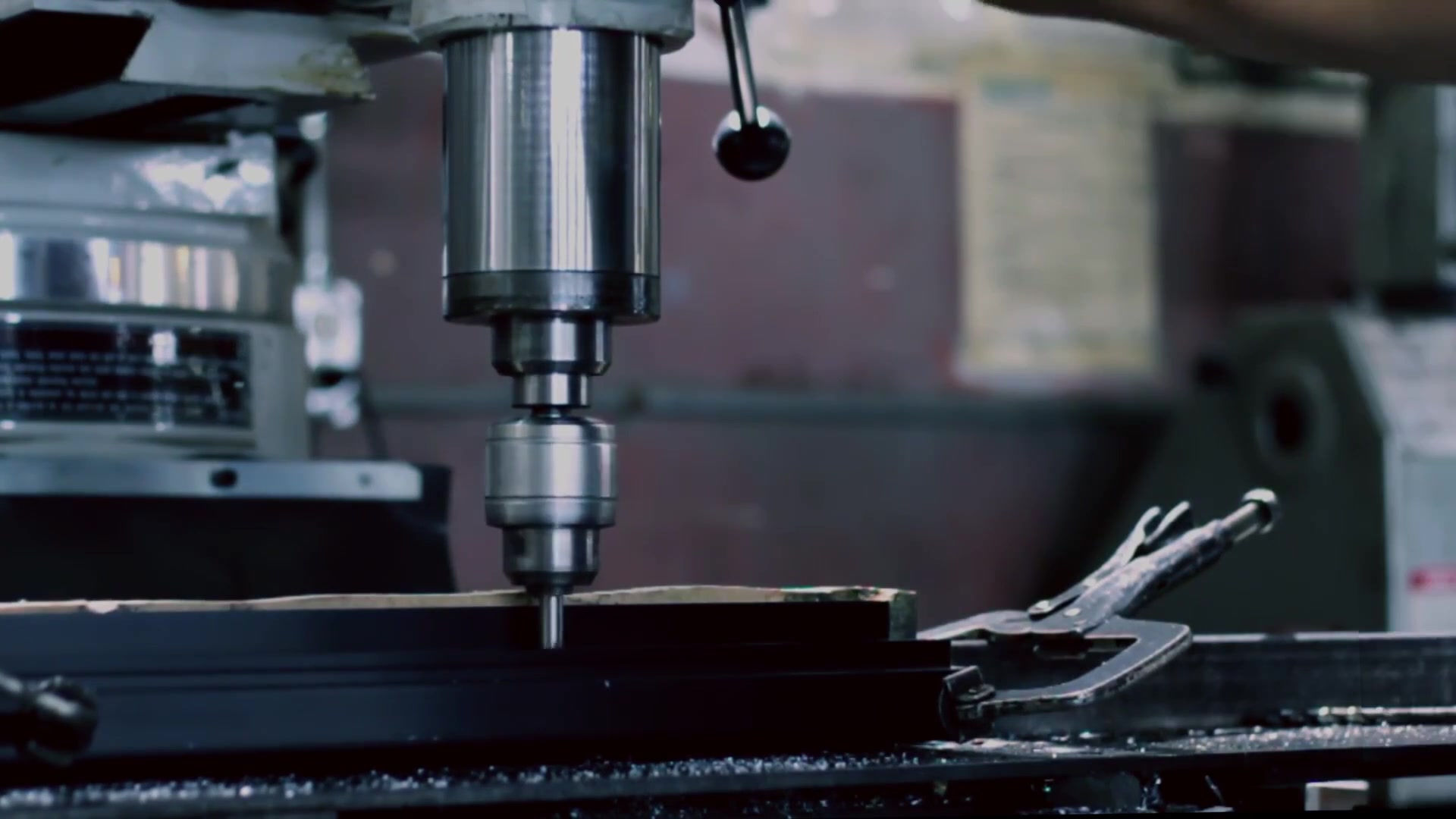
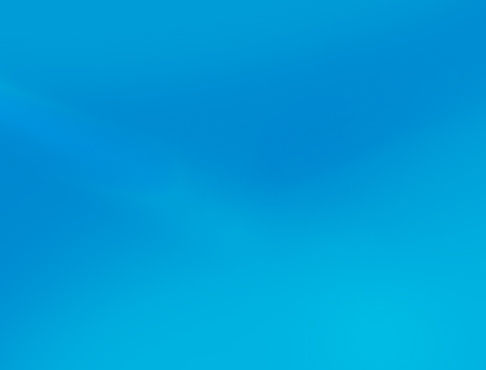
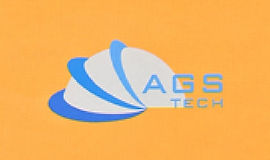
Fabricante global personalizado, integrador, consolidador, socio de outsourcing para unha ampla variedade de produtos e servizos.
Somos a súa fonte única para a fabricación, fabricación, enxeñaría, consolidación, integración e subcontratación de produtos e servizos fabricados a medida e dispoñibles.
Escolla o seu idioma
-
Fabricación personalizada
-
Fabricación por contrato nacional e global
-
Outsourcing de Manufactura
-
Compras domésticas e globais
-
Consolidación
-
Integración de enxeñería
-
Servizos de Enxeñaría
Entre as moitas técnicas de UNIÓN que implementamos na fabricación, dáselle especial énfase á SOLDADURA, SOLDADURA, SOLDADURA, ENLACE ADHESIVO e MONTAXE MECÁNICO PERSONALIZADO porque estas técnicas son amplamente utilizadas en aplicacións como a fabricación de conxuntos herméticos, fabricación de produtos de alta tecnoloxía e selado especializado. Aquí concentrarémonos nos aspectos máis especializados destas técnicas de unión xa que están relacionados coa fabricación de produtos e conxuntos avanzados.
SOLDADURA POR FUSIÓN: Utilizamos a calor para fundir e unir materiais. A calor é subministrada por electricidade ou vigas de alta enerxía. Os tipos de soldadura por fusión que implantamos son SOLDADURA POR GAS OXICOMBUSTIBLE, SOLDADURA POR ARCO, SOLDADURA POR FACES DE ALTA ENERXÍA.
SOLDADURA EN ESTADO SÓLIDO: Unimos pezas sen fundir e fusión. Os nosos métodos de soldadura en estado sólido son FRÍO, ULTRASONS, RESISTENCIA, FRICCIÓN, SOLDADURA POR EXPLOSIÓN e ENLACE POR DIFUSIÓN.
SOLDADURA E SOLDADURA: Empregan metais de recheo e dannos a vantaxe de traballar a temperaturas máis baixas que na soldadura, polo que menos danos estruturais aos produtos. A información sobre a nosa instalación de soldadura que produce accesorios de cerámica a metal, selado hermético, pasaxes ao baleiro, baleiro alto e ultraalto e compoñentes de control de fluídos pódese atopar aquí:Folleto de Brazing Factory
ENLACE ADHESIVO: debido á diversidade de adhesivos utilizados na industria e tamén á diversidade de aplicacións, temos unha páxina dedicada para iso. Para ir á nosa páxina sobre unión adhesiva, prema aquí.
MONTAXE MECÁNICA PERSONALIZADA: utilizamos unha variedade de elementos de fixación como parafusos, parafusos, porcas, remaches. Os nosos fixadores non se limitan a fixadores estándar fóra de estante. Deseñamos, desenvolvemos e fabricamos fixadores especiais que están feitos de materiais non estándar para que poidan cumprir os requisitos para aplicacións especiais. Ás veces é desexable a non condutividade eléctrica ou térmica, mentres que ás veces a condutividade. Para algunhas aplicacións especiais, un cliente pode querer fixadores especiais que non se poden quitar sen destruír o produto. Hai infinitas ideas e aplicacións. Temos todo para ti, se non está dispoñible, podemos desenvolvelo rapidamente. Para ir á nosa páxina sobre montaxe mecánica, prema aquí. Examinemos con máis detalle as nosas diversas técnicas de unión.
SOLDADURA CON GAS OXICOMBUSTIBLE (OFW): Utilizamos un gas combustible mesturado con osíxeno para producir a chama de soldadura. Cando usamos o acetileno como combustible e osíxeno, chamámoslle soldadura con gas oxiacetileno. No proceso de combustión de gas oxicombustible ocorren dúas reaccións químicas:
C2H2 + O2 ------» 2CO + H2 + Calor
2CO + H2 + 1,5 O2--------» 2 CO2 + H2O + Calor
A primeira reacción disocia o acetileno en monóxido de carbono e hidróxeno ao tempo que produce preto do 33% da calor total xerada. O segundo proceso anterior representa unha maior combustión do hidróxeno e do monóxido de carbono mentres produce preto do 67% da calor total. As temperaturas na chama están entre 1533 e 3573 Kelvin. A porcentaxe de osíxeno na mestura de gases é importante. Se o contido de osíxeno é máis da metade, a chama convértese nun axente oxidante. Isto é indesexable para algúns metais pero desexable para outros. Un exemplo cando é desexable a chama oxidante son as aliaxes a base de cobre porque forman unha capa de pasivación sobre o metal. Por outra banda, cando se reduce o contido de osíxeno, a combustión total non é posible e a chama convértese nunha chama redutora (cementadora). As temperaturas nunha chama redutora son máis baixas e, polo tanto, é adecuada para procesos como a soldadura e a soldadura. Outros gases tamén son potenciais combustibles, pero teñen algunhas desvantaxes sobre o acetileno. Ocasionalmente subministramos metais de recheo á zona de soldadura en forma de varillas de recheo ou fío. Algúns deles están recubertos de fundente para retardar a oxidación das superficies e protexer así o metal fundido. Un beneficio adicional que nos proporciona o fluxo é a eliminación de óxidos e outras substancias da zona de soldadura. Isto leva a unha unión máis forte. Unha variación da soldadura con gas oxicombustible é a SOLDADURA POR GAS A PRESIÓN, onde os dous compoñentes quentan na súa interface usando soplete de gas oxiacetileno e unha vez que a interface comeza a fundirse, retírase o soplete e aplícase unha forza axial para presionar as dúas partes xuntas. ata que se solidifique a interface.
SOLDADURA POR ARCO: Utilizamos enerxía eléctrica para producir un arco entre a punta do electrodo e as pezas a soldar. A fonte de alimentación pode ser AC ou DC mentres que os electrodos son consumibles ou non. A transferencia de calor na soldadura por arco pódese expresar coa seguinte ecuación:
H/l = ex VI/v
Aquí H é a entrada de calor, l é a lonxitude da soldadura, V e I son a tensión e corrente aplicada, v é a velocidade de soldadura e e é a eficiencia do proceso. Canto maior sexa a eficiencia "e", máis beneficiosa é a enerxía dispoñible para fundir o material. A entrada de calor tamén se pode expresar como:
H = ux (Volumen) = ux A xl
Aquí u é a enerxía específica para fundir, A a sección transversal da soldadura e l a lonxitude da soldadura. Das dúas ecuacións anteriores podemos obter:
v = ex VI / u A
Unha variación da soldadura por arco é a SOLDADURA POR ARCO METÁLICO APINTADO (SMAW) que constitúe preto do 50% de todos os procesos de soldadura industrial e de mantemento. A SOLDADURA CON ARCO ELÉCTRICO (SOLD WELDING) realízase tocando a punta dun electrodo revestido coa peza de traballo e retirándoa rapidamente a unha distancia suficiente para manter o arco. Chamámoslle a este proceso tamén soldadura por varillas porque os electrodos son varas finas e longas. Durante o proceso de soldadura, a punta do electrodo fúndese xunto co seu revestimento e o metal base nas proximidades do arco. Unha mestura de metal base, metal do electrodo e substancias do revestimento do electrodo solidificase na zona de soldadura. O revestimento do electrodo desoxidase e proporciona un gas protector na rexión de soldadura, protexendo así do osíxeno do ambiente. Polo tanto, o proceso denomínase soldadura por arco metálico blindado. Usamos correntes entre 50 e 300 amperios e niveis de potencia xeralmente inferiores a 10 kW para un rendemento óptimo da soldadura. Tamén é importante a polaridade da corrente continua (dirección do fluxo de corrente). A polaridade recta onde a peza é positiva e o eléctrodo negativo é preferible na soldadura de chapas metálicas pola súa penetración pouco profunda e tamén para xuntas con fendas moi amplas. Cando temos polaridade inversa, é dicir, o electrodo é positivo e a peza negativa podemos conseguir penetracións de soldadura máis profundas. Con corrente alterna, xa que temos arcos pulsantes, podemos soldar seccións grosas utilizando electrodos de gran diámetro e correntes máximas. O método de soldadura SMAW é axeitado para espesores de pezas de 3 a 19 mm e aínda máis utilizando técnicas de múltiples pasadas. A escoura formada na parte superior da soldadura debe ser eliminada mediante un cepillo de arame, para que non haxa corrosión e falla na zona de soldadura. Isto, por suposto, engádese ao custo da soldadura por arco de metal blindado. Non obstante, o SMAW é a técnica de soldadura máis popular na industria e nos traballos de reparación.
SOLDADURA POR ARCO SUMMERXIDO (SAW): Neste proceso protexemos o arco de soldadura utilizando materiais de fluxo granular como cal, sílice, floruro de calcio, óxido de manganeso... etc. O fluxo granular introdúcese na zona de soldadura mediante un fluxo por gravidade a través dunha boquilla. O fluxo que cobre a zona de soldadura fundida protexe significativamente de chispas, fumes, radiación UV... etc. e actúa como illante térmico, deixando así que a calor penetre profundamente na peza de traballo. O fluxo non fundido é recuperado, tratado e reutilizado. Unha bobina desnuda úsase como eléctrodo e lévase a través dun tubo ata a zona de soldadura. Usamos correntes entre 300 e 2000 Amperios. O proceso de soldadura por arco mergullado (SAW) está limitado a posicións horizontais e planas e soldaduras circulares se é posible a rotación da estrutura circular (como tubos) durante a soldadura. As velocidades poden alcanzar os 5 m/min. O proceso SAW é axeitado para placas grosas e dá como resultado soldaduras de alta calidade, resistentes, dúctiles e uniformes. A produtividade, é dicir, a cantidade de material de soldadura depositado por hora é de 4 a 10 veces a cantidade en comparación co proceso SMAW.
Outro proceso de soldadura por arco, a saber, a SOLDADURA POR ARCO DE GAS METAL (GMAW) ou alternativamente denominada SOLDADURA DE GAS INERTE METAL (MIG) baséase en que a zona de soldadura está protexida por fontes externas de gases como helio, argón, dióxido de carbono, etc. Pode haber desoxidantes adicionais presentes no metal do electrodo. O fío consumible é alimentado a través dunha boquilla na zona de soldadura. A fabricación de metais tanto férreos como non férreos realízase mediante soldadura por arco de metal con gas (GMAW). A produtividade da soldadura é aproximadamente 2 veces a do proceso SMAW. Empréganse equipos de soldadura automatizados. O metal transfírese dun dos tres xeitos neste proceso: a "Transferencia de pulverización" implica a transferencia de varios centos de pequenas gotas de metal por segundo desde o electrodo á zona de soldadura. En "Transferencia Globular", por outra banda, utilízanse gases ricos en dióxido de carbono e glóbulos de metal fundido son impulsados polo arco eléctrico. As correntes de soldadura son altas e a penetración da soldadura máis profunda, a velocidade de soldadura maior que na transferencia de pulverización. Así, a transferencia globular é mellor para soldar seccións máis pesadas. Finalmente, no método de "Curtocircuíto", a punta do electrodo toca o baño de soldadura fundido, curtocircuítao xa que o metal a velocidades superiores a 50 gotas/segundo transfírese en gotas individuais. Utilízanse correntes e voltaxes baixas xunto cun fío máis fino. As potencias utilizadas son duns 2 kW e as temperaturas relativamente baixas, o que fai que este método sexa adecuado para chapas finas de menos de 6 mm de espesor.
Outra variación do proceso de SOLDADURA POR ARCO DE NÚCLEO FLUXANTE (FCAW) é similar á soldadura por arco metálico con gas, excepto que o electrodo é un tubo cheo de fluxo. As vantaxes de usar electrodos de fluxo con núcleo é que producen arcos máis estables, dannos a oportunidade de mellorar as propiedades dos metais de soldadura, a natureza menos fráxil e flexible do seu fluxo en comparación coa soldadura SMAW, os contornos de soldadura mellorados. Os electrodos con núcleo autoprotexidos conteñen materiais que protexen a zona de soldadura contra a atmosfera. Usamos uns 20 kW de potencia. Do mesmo xeito que o proceso GMAW, o proceso FCAW tamén ofrece a oportunidade de automatizar procesos para a soldadura continua, e é económico. Pódense desenvolver diferentes químicas de metal de soldadura engadindo varias aliaxes ao núcleo de fluxo.
En SOLDADURA ELECTROGÁS (EGW) soldamos as pezas colocadas bordo a bordo. Ás veces tamén se lle chama SOLDADURA A BORDE. O metal de soldadura colócase nunha cavidade de soldadura entre dúas pezas a unir. O espazo está pechado por dúas presas refrixeradas por auga para evitar que a escoura fundida se derrame. As presas son movidas cara arriba mediante accionamentos mecánicos. Cando se pode xirar a peza de traballo, tamén podemos utilizar a técnica de soldadura electrogás para soldar circunferenciais de tubos. Os electrodos son alimentados a través dun conduto para manter un arco continuo. As correntes poden ser duns 400 amperios ou 750 amperios e os niveis de potencia duns 20 kW. Os gases inertes orixinados a partir dun electrodo con núcleo de fluxo ou dunha fonte externa proporcionan protección. Utilizamos a soldadura por electrogás (EGW) para metais como aceiros, titanio….etc con espesores de 12 mm a 75 mm. A técnica é adecuada para grandes estruturas.
Porén, noutra técnica chamada ELECTROSLAG WELDING (ESW) encéndese o arco entre o electrodo e a parte inferior da peza e engádese fluxo. Cando a escoura fundida chega á punta do electrodo, o arco apágase. A enerxía é continuamente subministrada a través da resistencia eléctrica da escoura fundida. Podemos soldar chapas con espesores entre 50 mm e 900 mm e incluso superiores. As correntes son duns 600 amperios mentres que as tensións están entre 40 e 50 V. As velocidades de soldadura son de 12 a 36 mm/min. As aplicacións son similares á soldadura por electrogás.
Un dos nosos procesos de electrodos non consumibles, a SOLDADURA POR ARCO DE TUNGSTENO (GTAW) tamén coñecida como SOLDADURA DE GAS INERTE DE TUNGSTENO (TIG) implica a subministración dun metal de recheo mediante un fío. Para xuntas axustadas ás veces non usamos o metal de recheo. No proceso TIG non usamos fluxo, senón que usamos argón e helio para a blindaxe. O volframio ten un alto punto de fusión e non se consume no proceso de soldadura TIG, polo que se pode manter a corrente constante así como os espazos de arco. Os niveis de potencia están entre 8 e 20 kW e as correntes de 200 amperios (CC) ou 500 amperios (CA). Para o aluminio e o magnesio utilizamos corrente alterna para a súa función de limpeza de óxidos. Para evitar a contaminación do electrodo de wolframio, evitamos o seu contacto con metais fundidos. A soldadura por arco de tungsteno con gas (GTAW) é especialmente útil para soldar metais finos. As soldaduras GTAW son de moi alta calidade cun bo acabado superficial.
Debido ao maior custo do gas hidróxeno, unha técnica de uso menos frecuente é a SOLDADURA ATÓMICA DE HIDRÓGENO (AHW), onde xeramos un arco entre dous electrodos de wolframio nunha atmosfera de protección de gas hidróxeno en fluxo. O AHW tamén é un proceso de soldadura de electrodos non consumibles. O gas hidróxeno diatómico H2 descompón a súa forma atómica preto do arco de soldadura onde as temperaturas superan os 6273 Kelvin. Mentres se rompe, absorbe gran cantidade de calor do arco. Cando os átomos de hidróxeno chocan contra a zona de soldadura que é unha superficie relativamente fría, recombínanse en forma diatómica e liberan a calor almacenada. A enerxía pódese variar cambiando a peza de traballo á distancia do arco.
Noutro proceso de electrodos non consumibles, a SOLDADURA POR ARCO DE PLASMA (PAW), temos un arco de plasma concentrado dirixido cara á zona de soldadura. As temperaturas alcanzan os 33.273 Kelvin en PAW. Un número case igual de electróns e ións compoñen o gas do plasma. Un arco piloto de baixa corrente inicia o plasma que está entre o electrodo de wolframio e o orificio. As correntes de funcionamento son xeralmente arredor dos 100 amperios. Pódese alimentar un metal de recheo. Na soldadura por arco de plasma, a blindaxe realízase mediante un anel de protección exterior e utilizando gases como argón e helio. Na soldadura por arco de plasma, o arco pode estar entre o electrodo e a peza de traballo ou entre o electrodo e a boquilla. Esta técnica de soldadura ten as vantaxes sobre outros métodos de maior concentración de enerxía, capacidade de soldadura máis profunda e estreita, mellor estabilidade do arco, velocidades de soldadura máis altas de ata 1 metro/min, menos distorsión térmica. Normalmente utilizamos soldadura por arco de plasma para espesores inferiores a 6 mm e ás veces ata 20 mm para aluminio e titanio.
SOLDADURA POR FAIS DE ALTA ENERXÍA: Outro tipo de método de soldadura por fusión con soldadura por feixe de electróns (EBW) e soldadura con láser (LBW) como dúas variantes. Estas técnicas son de especial valor para o noso traballo de fabricación de produtos de alta tecnoloxía. Na soldadura por feixe de electróns, os electróns de alta velocidade golpean a peza e a súa enerxía cinética convértese en calor. O feixe estreito de electróns viaxa facilmente na cámara de baleiro. Xeralmente usamos alto baleiro na soldadura por feixe electrónico. Pódense soldar placas de 150 mm de grosor. Non se necesitan gases de protección, fundentes ou materiais de recheo. As pistolas de feixe Elecron teñen unha capacidade de 100 kW. Son posibles soldaduras profundas e estreitas con relacións de aspecto altas de ata 30 e pequenas zonas afectadas pola calor. As velocidades de soldadura poden alcanzar os 12 m/min. Na soldadura por raio láser utilizamos láseres de alta potencia como fonte de calor. Os raios láser de tan pequenos como 10 micras con alta densidade permiten unha penetración profunda na peza de traballo. Coa soldadura con láser é posible unha relación de profundidade a ancho de ata 10. Usamos tanto láseres de ondas pulsadas como continuas, sendo o primeiro en aplicacións para materiais finos e o segundo principalmente para pezas grosas de ata uns 25 mm. Os niveis de potencia son de ata 100 kW. A soldadura por raio láser non é adecuada para materiais ópticamente moi reflectores. Tamén se poden utilizar gases no proceso de soldadura. O método de soldadura por raio láser é adecuado para a automatización e a fabricación de gran volume e pode ofrecer velocidades de soldadura entre 2,5 m/min e 80 m/min. Unha das principais vantaxes que ofrece esta técnica de soldadura é o acceso a zonas onde non se poden utilizar outras técnicas. Os raios láser poden viaxar facilmente a rexións tan difíciles. Non se necesita baleiro como na soldadura por feixe de electróns. Soldaduras con boa calidade e resistencia, baixa contracción, baixa distorsión e baixa porosidade pódense obter coa soldadura con láser. Os raios láser pódense manipular e dar forma facilmente mediante cables de fibra óptica. Así, a técnica é moi adecuada para soldar conxuntos herméticos de precisión, paquetes electrónicos, etc.
Vexamos as nosas técnicas de SOLDADURA DE ESTADO SÓLIDO. A SOLDADURA EN FRÍO (CW) é un proceso no que se aplica presión en lugar de calor mediante matrices ou rolos ás pezas que se acoplan. Na soldadura en frío, polo menos unha das partes de acoplamento debe ser dúctil. Os mellores resultados obtéñense con dous materiais similares. Se os dous metais a unir coa soldadura en frío son diferentes, poderemos ter xuntas débiles e quebradizas. O método de soldadura en frío é moi adecuado para pezas brandas, dúctiles e pequenas, como conexións eléctricas, bordos de recipientes sensibles á calor, tiras bimetálicas para termostatos... etc. Unha variación da soldadura en frío é a unión de rolos (ou soldadura de rolos), onde a presión se aplica a través dun par de rolos. Ás veces realizamos soldadura en rolo a temperaturas elevadas para unha mellor resistencia da interface.
Outro proceso de soldadura en estado sólido que utilizamos é a SOLDADURA ULTRASÓNICA (USW), onde as pezas están sometidas a unha forza normal estática e esforzos cortantes oscilantes. Os esforzos de cizallamento oscilante aplícanse a través da punta dun transdutor. A soldadura ultrasónica desprega oscilacións con frecuencias de 10 a 75 kHz. Nalgunhas aplicacións, como a soldadura de costura, usamos un disco de soldadura xiratorio como punta. Os esforzos de cizallamento aplicados ás pezas provocan pequenas deformacións plásticas, rompen capas de óxido, contaminantes e conducen a unión en estado sólido. As temperaturas implicadas na soldadura por ultrasóns están moi por debaixo das temperaturas do punto de fusión dos metais e non se produce fusión. Usamos frecuentemente o proceso de soldadura ultrasóns (USW) para materiais non metálicos como plásticos. Nos termoplásticos, as temperaturas alcanzan puntos de fusión.
Outra técnica popular, na SOLDADURA POR FRICCIÓN (FRW) a calor xérase a través da fricción na interface das pezas a unir. Na soldadura por fricción mantemos unha das pezas de traballo estacionaria mentres que a outra peza se mantén nun dispositivo e xira a unha velocidade constante. A continuación, as pezas póñense en contacto baixo unha forza axial. A velocidade de rotación da superficie na soldadura por fricción pode alcanzar 900 m/min nalgúns casos. Despois dun contacto interfacial suficiente, a peza de traballo xiratoria deténse de forma súbita e aumenta a forza axial. A zona de soldadura é xeralmente unha rexión estreita. A técnica de soldadura por fricción pódese usar para unir pezas sólidas e tubulares feitas de diversos materiais. Algún flash pode desenvolverse na interface en FRW, pero este flash pódese eliminar mediante mecanizado secundario ou rectificado. Existen variacións no proceso de soldadura por fricción. Por exemplo, a "soldadura por fricción por inercia" implica un volante cuxa enerxía cinética de rotación se utiliza para soldar as pezas. A soldadura está completa cando o volante se detén. A masa xiratoria pode ser variada e, polo tanto, a enerxía cinética rotacional. Outra variación é a "soldadura por fricción lineal", onde se impón o movemento alternativo lineal de polo menos un dos compoñentes a unir. Na soldadura por fricción lineal as pezas non teñen que ser circulares, poden ser rectangulares, cadradas ou doutra forma. As frecuencias poden estar en decenas de Hz, amplitudes no rango de milímetros e presións en decenas ou centos de MPa. Finalmente a "soldadura por fricción" é algo diferente ás outras dúas explicadas anteriormente. Mentres que na soldadura por fricción por inercia e na soldadura por fricción lineal o quecemento das interfaces conséguese por fricción frotando dúas superficies de contacto, no método de soldadura por fricción axitada un terceiro corpo frotase contra as dúas superficies que se van unir. Ponse en contacto coa xunta unha ferramenta rotativa de 5 a 6 mm de diámetro. As temperaturas poden aumentar a valores entre 503 e 533 Kelvin. Prodúcese o quecemento, mestura e axitación do material na unión. Usamos a soldadura por fricción nunha variedade de materiais, incluíndo aluminio, plásticos e compostos. As soldaduras son uniformes e a calidade é alta con mínimos poros. Non se producen fumes nin salpicaduras na soldadura por fricción e o proceso está ben automatizado.
SOLDADURA POR RESISTENCIA (RW): A calor necesaria para a soldadura prodúcese pola resistencia eléctrica entre as dúas pezas a unir. Non se utilizan fluxos, gases de protección nin electrodos consumibles na soldadura por resistencia. O quecemento Joule ten lugar na soldadura por resistencia e pódese expresar como:
H = (Cadro I) x R xtx K
H é a calor xerada en joules (vatios-segundos), I a corrente en amperios, R a resistencia en ohmios, t é o tempo en segundos que atravesa a corrente. O factor K é menor que 1 e representa a fracción de enerxía que non se perde pola radiación e a condución. As correntes nos procesos de soldadura por resistencia poden alcanzar niveis tan altos como 100.000 A pero as tensións son normalmente de 0,5 a 10 voltios. Os electrodos son normalmente feitos de aliaxes de cobre. Pódense unir tanto materiais similares como distintos mediante soldadura por resistencia. Existen varias variacións para este proceso: a "soldadura por puntos por resistencia" implica que dous electrodos redondos opostos entran en contacto coas superficies da unión de solapa das dúas follas. Aplícase presión ata que se desconecte a corrente. A pepita de soldadura adoita ter un diámetro de ata 10 mm. A soldadura por puntos por resistencia deixa marcas de sangría lixeiramente descoloridas nos puntos de soldadura. A soldadura por puntos é a nosa técnica de soldadura por resistencia máis popular. Na soldadura por puntos utilízanse varias formas de electrodos para chegar a zonas difíciles. O noso equipo de soldadura por puntos está controlado por CNC e ten varios electrodos que se poden usar simultaneamente. Outra variación "soldadura de costura por resistencia" realízase con electrodos de roda ou rolo que producen soldaduras por puntos continuas sempre que a corrente alcanza un nivel suficientemente alto no ciclo de alimentación de CA. As unións producidas pola soldadura de costura por resistencia son estancas a líquidos e gases. Velocidades de soldadura de aproximadamente 1,5 m/min son normais para chapas finas. Pódense aplicar correntes intermitentes para que as soldaduras por puntos se produzan nos intervalos desexados ao longo da costura. En "soldadura por proxección por resistencia" gravamos unha ou varias proxeccións (coviñas) nunha das superficies da peza a soldar. Estas proxeccións poden ser redondas ou ovaladas. Nestes puntos en relevo alcánzanse altas temperaturas localizadas que entran en contacto coa parte de apareamento. Os electrodos exercen presión para comprimir estas proxeccións. Os electrodos na soldadura por proxección por resistencia teñen puntas planas e son aliaxes de cobre refrixeradas por auga. A vantaxe da soldadura por proxección por resistencia é a nosa capacidade para realizar varias soldaduras nun só golpe, polo que a vida útil prolongada do electrodo, a capacidade de soldar follas de varios grosores, a capacidade de soldar porcas e parafusos a follas. A desvantaxe da soldadura por proxección de resistencia é o custo adicional de gravar as coviñas. Outra técnica máis, na "soldadura por flash" xérase calor a partir do arco nos extremos das dúas pezas cando comezan a facer contacto. Este método tamén pode considerar alternativamente a soldadura por arco. A temperatura na interface sobe e o material ablandase. Aplícase unha forza axial e fórmase unha soldadura na rexión suavizada. Despois de completar a soldadura flash, a unión pódese mecanizar para mellorar o aspecto. A calidade da soldadura obtida mediante soldadura flash é boa. Os niveis de potencia son de 10 a 1500 kW. A soldadura por flash é adecuada para a unión de bordo a bordo de metais similares ou disímiles de ata 75 mm de diámetro e chapas de entre 0,2 mm e 25 mm de espesor. A "soldadura por arco de pernos" é moi similar á soldadura por flash. O espárrago, como un parafuso ou varilla roscada, serve como un electrodo mentres se une a unha peza de traballo como unha placa. Para concentrar a calor xerada, evitar a oxidación e reter o metal fundido na zona de soldadura, colócase un anel de cerámica desbotable arredor da unión. Finalmente "soldadura por percusión" outro proceso de soldadura por resistencia, utiliza un capacitor para subministrar a enerxía eléctrica. Na soldadura por percusión, a potencia descárgase en milisegundos de tempo moi rapidamente desenvolvendo unha elevada calor localizada na unión. Usamos amplamente a soldadura por percusión na industria de fabricación de produtos electrónicos onde se debe evitar o quecemento de compoñentes electrónicos sensibles nas proximidades da unión.
Unha técnica chamada SOLDADURA POR EXPLOSIÓN consiste na detonación dunha capa de explosivo que se coloca sobre unha das pezas a unir. A moi alta presión exercida sobre a peza produce unha interface turbulenta e ondulada e ten lugar un enclavamiento mecánico. As forzas de unión na soldadura explosiva son moi altas. A soldadura por explosión é un bo método para o revestimento de placas con metais diferentes. Despois do revestimento, as placas pódense enrolar en seccións máis finas. Ás veces usamos soldadura por explosión para tubos de expansión para que queden selados firmemente contra a placa.
O noso último método dentro do dominio da unión en estado sólido é o ENLACE POR DIFUSIÓN ou SOLDADURA POR DIFUSIÓN (DFW) na que se consegue unha boa unión principalmente por difusión de átomos pola interface. Algunha deformación plástica na interface tamén contribúe á soldadura. As temperaturas implicadas son ao redor de 0,5 Tm onde Tm é a temperatura de fusión do metal. A forza de unión na soldadura por difusión depende da presión, temperatura, tempo de contacto e limpeza das superficies en contacto. Ás veces usamos metais de recheo na interface. A calor e a presión son necesarias na unión por difusión e son subministradas por resistencia eléctrica ou forno e pesos mortos, prensa ou ben. Pódense unir metais similares e disímiles coa soldadura por difusión. O proceso é relativamente lento debido ao tempo que tardan os átomos en migrar. DFW pódese automatizar e úsase amplamente na fabricación de pezas complexas para as industrias aeroespacial, electrónica e médica. Os produtos fabricados inclúen implantes ortopédicos, sensores e membros estruturais aeroespaciais. A unión por difusión pódese combinar con SUPERPLÁSTIC FORMING para fabricar estruturas complexas de chapa metálica. Os lugares seleccionados das follas son primeiro unidos por difusión e despois as rexións non unidas son expandidas nun molde usando presión de aire. As estruturas aeroespaciais con altas relacións de rixidez-peso son fabricadas mediante esta combinación de métodos. O proceso combinado de soldadura por difusión/formado superplástico reduce o número de pezas necesarias eliminando a necesidade de fixadores, resultando en pezas moi precisas de baixo estrés de xeito económico e con curtos prazos de entrega.
SOLDADURA: As técnicas de soldadura forte implican temperaturas máis baixas que as necesarias para a soldadura. Non obstante, as temperaturas de soldadura son máis altas que as de soldadura. Na soldadura colócase un metal de recheo entre as superficies a unir e as temperaturas elévanse ata a temperatura de fusión do material de recheo por encima de 723 Kelvin pero por debaixo das temperaturas de fusión das pezas de traballo. O metal fundido enche o espazo entre as pezas de traballo. O arrefriamento e a posterior solidificación do metal de lima produce xuntas fortes. Na soldadura por soldadura, o metal de recheo deposítase na unión. Úsase considerablemente máis metal de recheo na soldadura por soldadura en comparación coa soldadura. O soplete de oxiacetileno con chama oxidante úsase para depositar o metal de recheo na soldadura por soldadura. Debido ás temperaturas máis baixas na soldadura, os problemas nas zonas afectadas pola calor como a deformación e as tensións residuais son menores. Canto menor é o espazo libre na soldadura, maior é a resistencia ao corte da unión. Non obstante, a máxima resistencia á tracción conséguese nun intervalo óptimo (un valor máximo). Por debaixo e por riba deste valor óptimo, a resistencia á tracción na soldadura diminúe. Os xogos típicos en soldadura poden estar entre 0,025 e 0,2 mm. Usamos unha variedade de materiais de soldadura con diferentes formas, como performs, po, aneis, arame, tiras... etc. e pode fabricar estes traballos especialmente para o seu deseño ou xeometría do produto. Tamén determinamos o contido dos materiais de soldadura segundo os seus materiais de base e aplicación. Usamos con frecuencia fundentes nas operacións de soldadura para eliminar as capas de óxido non desexadas e evitar a oxidación. Para evitar a corrosión posterior, os fluxos son xeralmente eliminados despois da operación de unión. AGS-TECH Inc. usa varios métodos de soldadura, incluíndo:
- Soldadura con soplete
- Soldadura ao forno
- Soldadura por indución
- Soldadura por resistencia
- Soldadura por inmersión
- Soldadura por infravermellos
- Soldadura por difusión
- Feixe de alta enerxía
Os nosos exemplos máis comúns de unións soldadas están feitos de metais diferentes con boa resistencia, como brocas de carburo, insercións, paquetes herméticos optoelectrónicos, selos.
SOLDADURA: Esta é unha das nosas técnicas máis utilizadas onde a soldadura (metal de recheo) enche a unión como na soldadura entre compoñentes que se axustan. As nosas soldaduras teñen puntos de fusión inferiores a 723 Kelvin. Implementamos soldadura manual e automatizada nas operacións de fabricación. En comparación coa soldadura, as temperaturas de soldadura son máis baixas. A soldadura non é moi adecuada para aplicacións de alta temperatura ou de alta resistencia. Usamos soldaduras sen chumbo, así como aliaxes de estaño-chumbo, estaño-zinc, chumbo-prata, cadmio-prata, cinc-aluminio ademais doutras para soldar. Tanto a base de resinas non corrosivas como os ácidos e sales inorgánicos úsanse como fundente na soldadura. Usamos fluxos especiais para soldar metais con baixa soldabilidade. Nas aplicacións nas que temos que soldar materiais cerámicos, vidro ou grafito, primeiro chapamos as pezas cun metal axeitado para aumentar a soldabilidade. As nosas técnicas de soldadura populares son:
- Soldadura por reflujo ou pasta
- Soldadura por onda
- Soldadura ao forno
- Soldadura con soplete
- Soldadura por indución
- Soldadura de ferro
- Soldadura por resistencia
- Soldadura por inmersión
- Soldadura por ultrasóns
- Soldadura por infravermellos
A soldadura por ultrasóns ofrécenos unha vantaxe única pola que se elimina a necesidade de fluxos debido ao efecto de cavitación ultrasónica que elimina as películas de óxido das superficies que se unen. A soldadura por refluxo e por onda son as nosas técnicas destacadas industrialmente para a fabricación de grandes volumes en electrónica e, polo tanto, merece a pena explicarlas con máis detalle. Na soldadura por refluxo, usamos pastas semisólidas que inclúen partículas de metal de soldadura. A pasta colócase sobre a unión mediante un proceso de cribado ou stencil. En placas de circuíto impreso (PCB) utilizamos con frecuencia esta técnica. Cando os compoñentes eléctricos se colocan sobre estas almofadas a partir de pasta, a tensión superficial mantén os paquetes de montaxe en superficie aliñados. Despois de colocar os compoñentes, quentamos o conxunto nun forno para que se produza a soldadura por refluxo. Durante este proceso, os disolventes na pasta evaporan, o fluxo na pasta actívase, os compoñentes prequentanse, as partículas de soldadura fúndense e mollan a unión e, finalmente, o conxunto de PCB arrefríase lentamente. A nosa segunda técnica popular para a produción de placas de PCB en grandes cantidades, a saber, a soldadura por ondas, baséase no feito de que as soldaduras fundidas mollan as superficies metálicas e forman boas unións só cando o metal se quenta previamente. Unha onda laminar estacionaria de soldadura fundida é xerada por primeira vez por unha bomba e os PCB precalentados e prefluxados son transportados sobre a onda. A soldadura só molla superficies metálicas expostas, pero non molla os paquetes de polímero IC nin as placas de circuíto revestidas de polímero. Un chorro de auga quente de alta velocidade expulsa o exceso de soldadura da unión e impide a ponte entre os cables adxacentes. Na soldadura por onda de paquetes de montaxe en superficie, primeiro unímolos de forma adhesiva á placa de circuíto antes de soldar. De novo utilízase cribado e esténcil pero esta vez para epoxi. Despois de colocar os compoñentes nos seus lugares correctos, o epoxi se cura, as placas invírtense e prodúcese a soldadura por onda.