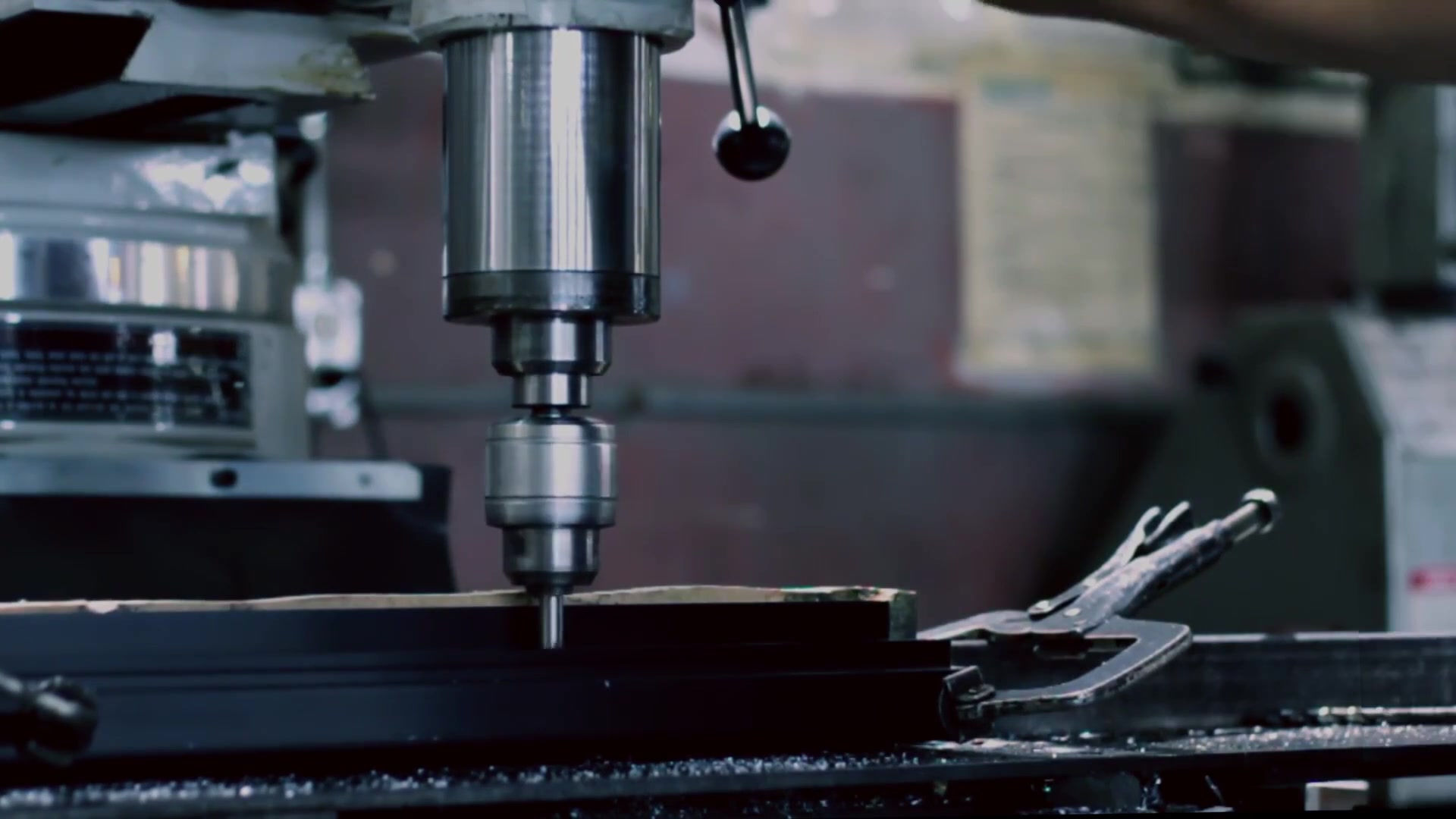
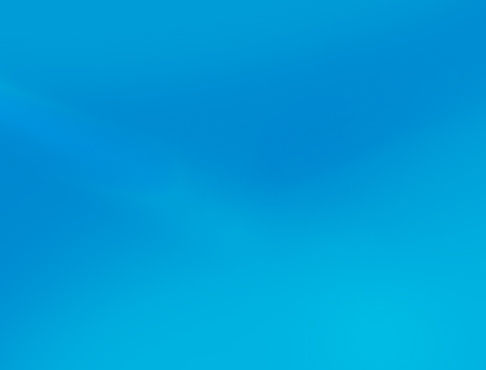
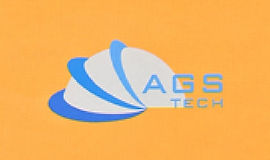
Global Custom Manufacturer, Integrator, Consolidator, Outsourcing Partner for a Wide Variety of Products & Services.
We are your one-stop source for manufacturing, fabrication, engineering, consolidation, integration, outsourcing of custom manufactured and off-shelf products & services. We also private label / white label your products with your brand name if you wish.
Choose your Language
-
Custom Manufacturing of Parts, Components, Assemblies, Finished Products, Machines and Industrial Equipment
-
Domestic & Global Contract Manufacturing
-
Manufacturing Outsourcing
-
Domestic, Global Procurement of Industrial Products
-
Private labeling / White Labeling your Products with your Brand Name
-
Product Finding & Locating Services
-
Global Design and Channel Partnership
-
Engineering Integration
-
Engineering Services
-
Global Consolidation, Warehousing, Logistics
In recent years, we have seen an increase in demand for RAPID MANUFACTURING or RAPID PROTOTYPING. This process may be also called DESKTOP MANUFACTURING or FREE-FORM FABRICATION. Basically a solid physical model of a part is made directly from a three dimensional CAD drawing. We use the term ADDITIVE MANUFACTURING for these various techniques where we build parts in layers. Using integrated computer-driven hardware and software we perform additive manufacturing. Our rapid prototyping and manufacturing techniques are STEREOLITHOGRAPHY, POLYJET, FUSED-DEPOSITION MODELING, SELECTIVE LASER SINTERING, ELECTRON BEAM MELTING, THREE-DIMENSIONAL PRINTING, DIRECT MANUFACTURING, RAPID TOOLING. We recommend that you click here to DOWNLOAD our Schematic Illustrations of Additive Manufacturing and Rapid Manufacturing Processes by AGS-TECH Inc.
This will help you better understand the information we are providing you below.
Rapid prototyping provides us: 1.) The conceptual product design is viewed from different angles on a monitor using a 3D / CAD system. 2.) Prototypes from nonmetallic and metallic materials are manufactured and studied from functional, technical and aesthetic aspects. 3.) Low cost prototyping in a very short time is accomplished. Additive manufacturing can be resembled to the construction of a loaf of bread by stacking and bonding individual slices on top of each other. In other words, the product is manufactured slice by slice, or layer by layer deposited onto each other. Most parts can be produced within hours. The technique is good if parts are needed very quickly or if quantities needed are low and making a mold and tooling is too expensive and time taking. However the cost of a part is expensive due to the expensive raw materials.
Rapid Parts & Prototypes Brochure Download
• STEREOLITHOGRAPHY : This technique also abbreviated as STL, is based on curing and hardening of a liquid photopolymer into a specific shape by focusing a laser beam on it. The laser polymerizes the photopolymer and cures it. By scanning the UV laser beam according to the programmed shape along the surface of the photopolymer mixture the part is produced from the bottom up in individual slices cascaded on top of each other. The scanning of the laser spot is repeated many times to achieve the geometries programmed into the system. After the part is completely manufactured, it is removed from the platform, blotted and cleaned ultrasonically and with alcohol bath. Next, it is exposed to UV irradiation for a few hours to make sure the polymer is fully cured and hardened. To summarize the process, a platform that is dipped into a photopolymer mixture and a UV laser beam are controled and moved through a servo-control system according tp the shape of the desired part and the part is obtained by photocuring the polymer layer by layer. Of course the maximum dimensions of the produced part are determined by the stereolithography equipment.
• POLYJET : Similar to inkjet printing, in polyjet we have eight print heads that deposit photopolymer on the build tray. Ultraviolet light placed alongside the jets immediately cures and hardens each layer. Two materials are used in polyjet. The first material is for manufacturing the actual model. The second material, a gel-like resin is used for support. Both of these materials are deposited layer by layer and simultaneously cured. After the completion of the model, the support material is removed with an aqueous solution. Resins used are similar to stereolithography (STL). The polyjet has the following advantages over stereolithography: 1.) No need for cleaning parts. 2.) No need for postprocess curing 3.) Smaller layer thicknesses are possible and thus we get better resolution and can manufacture finer parts.
• FUSED DEPOSITION MODELING : Also abbreviated as FDM, in this method a robot-controlled extruder head moves in two principle directions over a table. The cable is lowered and raised as needed. From the orifice of a heated die on the head, a thermoplastic filament is extruded and an initial layer is deposited on a foam foundation. This is accomplished by the extruder head that follows a predetermined path. After the initial layer, the table is lowered and subsequent layers are deposited on top of each other. Sometimes when manufacturing a complicated part, support structures are needed so that deposition can continue in certain directions. In these cases, a support material is extruded with a less dense spacing of filament on a layer so that it is weaker than the model material. These support structures can later be dissolved or broken off after the completion of the part. The extruder die dimensions determine the thickness of the extruded layers. The FDM process produces parts with stepped surfaces on oblique exterior planes. If this roughness is unacceptable, chemical vapor polishing or a heated tool can be used for smoothing these. Even a polishing wax is available as a coating material to eliminate these steps and achieve reasonable geometric tolerances.
• SELECTIVE LASER SINTERING : Also denoted as SLS, the process is based on sintering of a polymer, ceramic or metallic powders selectively into an object. The bottom of the processing chamber has two cylinders: A part-build cylinder and a powder-feed cylinder. The former is lowered incrementally to where the sintered part is being formed and the latter is raised incrementally to supply powder to the part-build cylinder through a roller mechanism. First a thin layer of powder is deposited in the part-build cylinder, then a laser beam is focused on that layer, tracing and melting /sintering a particular cross section, which then resolidifies into a solid. The powder is areas that are not hit by the laser beam remain loose but still supports the solid portion. Then another layer of powder is deposited and the process repeated many times to obtain the part. At the end, the loose powder particles are shaken off. All these are carried out by a process-control computer using instructions generated by the 3D CAD program of the part being manufactured. Various materials such as polymers (such as ABS, PVC, polyester), wax, metals and ceramics with appropriate polymer binders can be deposited.
• ELECTRON-BEAM MELTING : Similar to selective laser sintering, but using electron beam to melt titanium or cobalt chrome powders to make prototypes in vacuum. Some developments have been made to perform this process on stainless steels, aluminum and copper alloys. If the fatigue strength of the produced parts need to be increased, we use hot isostatic pressing subsequent to part manufacture as a secondary process.
• THREE-DIMENSIONAL PRINTING : Also denoted by 3DP, in this technique a print head deposits an inorganic binder onto a layer of either nonmetallic or metallic powder. A piston carrying the powder bed is incrementally lowered and at each step the binder is deposited layer by layer and fused by the binder. Powder materials used are polymers blends and fibers, foundry sand, metals. Using different binder heads simultaneously and different color binders we can obtain various colors. The process is similar to inkjet printing but instead of obtaining a colored sheet we obtain a colored three dimensional object. The parts produced may be porous and therefore may require sintering and metal infiltration to increase its density and strength. Sintering will burn off the binder and fuse the metal powders together. Metals such a stainless steel, aluminum, titanium can be used to make the parts and as infiltration materials we commonly use copper and bronze. The beauty of this technique is that even complicated and moving assemblies can be manufactured very quickly. For example a gear assembly, a wrench as a tool can be made and will have moving and turning parts ready to be used. Different components of the assembly can be manufactured with different colors and all in one shot. Download our brochure on: Metal 3D Printing Basics
• DIRECT MANUFACTURING and RAPID TOOLING : Besides design evaluation, troubleshooting we use rapid prototyping for direct manufacture of products or direct application into products. In other words, rapid prototyping can be incorporated into conventional processes to make them better and more competitive. For example, rapid prototyping can produce patterns and molds. Patterns of a melting and burning polymer created by rapid prototyping operations can be assembled for investment casting and invested. Another example to mention is using 3DP to produce ceramic casting shell and use that for shell casting operations. Even injection molds and mold inserts can be produced by rapid prototyping and one can save many weeks or months of mold making lead time. By only analyzing a CAD file of the desired part, we can produce the tool geometry using software. Here are some of our popular rapid tooling methods:
RTV (Room-Temperature Vulcanizing) MOLDING / URETHANE CASTING : Using rapid prototyping can be used to make the pattern of the desired part. Then this pattern is coated with a parting agent and liquid RTV rubber is poured over the pattern to produce the mold halves. Next, these mold halves are used to injection mold liquid urethanes. The mold life is short, only like 0 or 30 cycles but enough for small batch production.
ACES (Acetal Clear Epoxy Solid) INJECTION MOLDING : Using rapid prototyping techniques such as stereolithography, we produce injection molds. These molds are shells with an open end to allow filling with materials such as epoxy, aluminum-filled epoxy or metals. Again mold life is limited to tens or maximum hundreds of parts.
SPRAYED METAL TOOLING PROCESS : We use rapid prototyping and make a pattern. We spray a zinc-aluminum alloy on the pattern surface and coat it. The pattern with the metal coating is then placed inside a flask and potted with an epoxy or aluminum-filled epoxy. Finally, it is removed and by producing two such mold halves we obtain a complete mold for injection molding. These molds have longer lives, in some cases depending on material and temperatures they can produce parts in the thousands.
KEELTOOL PROCESS : This technique can produce molds with 100,000 to 10 Million cycle lives. Using rapid prototyping we produce an RTV mold. The mold is next filled with a mixture consisting of A6 tool steel powder, tungsten carbide, polymer binder and let to cure. This mold is then heated to get the polymer burned off and the metal powders to fuse. The next step is copper infiltration to produce the final mold. If needed, secondary operations such as machining and polishing can be performed on the mold for better dimensional accuracies.