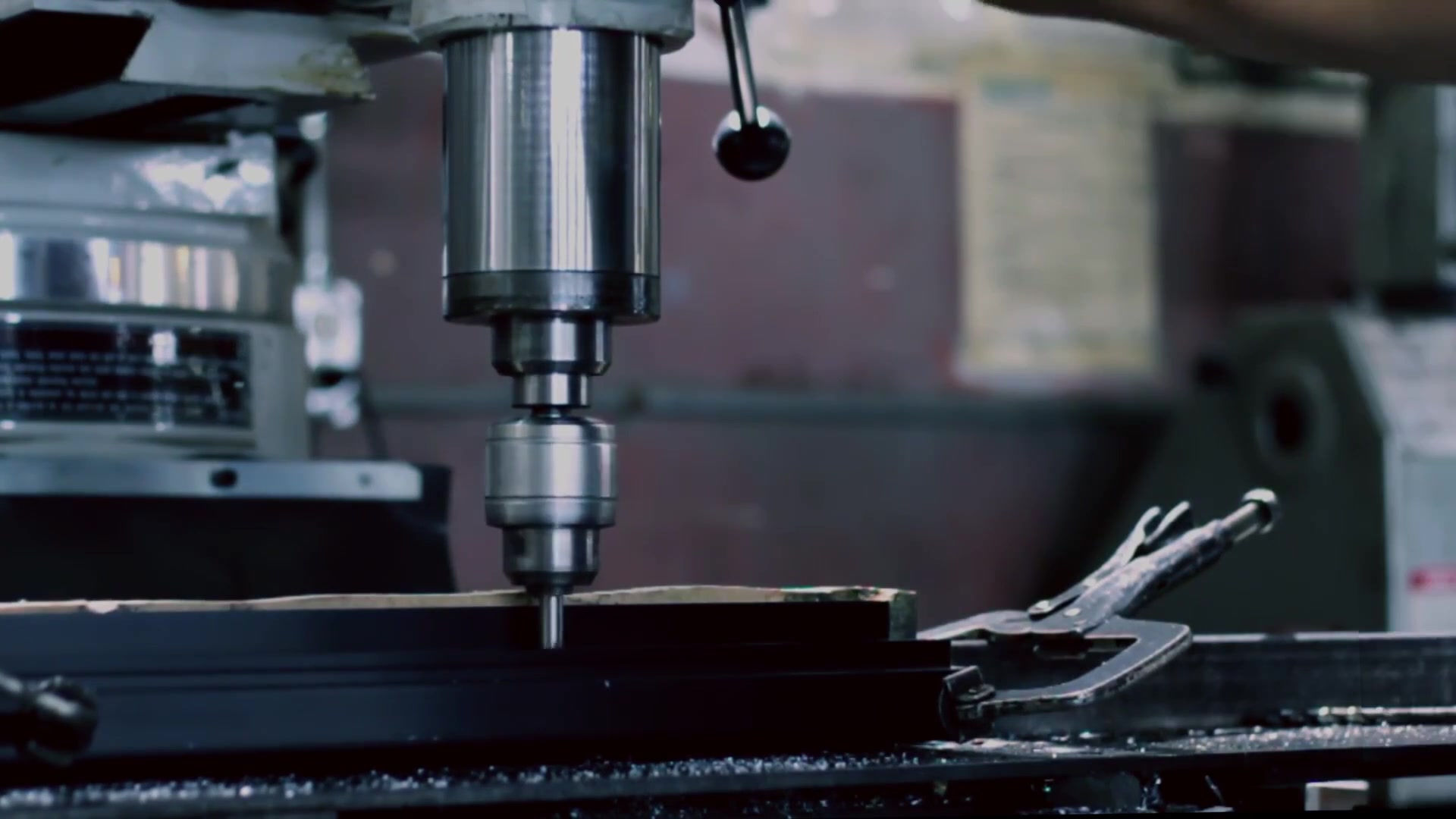
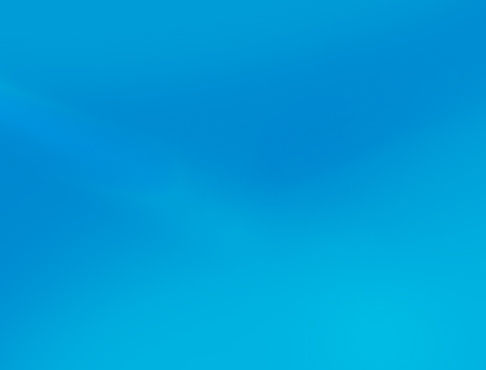
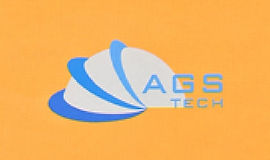
Global Custom Manufacturer, Integrator, Consolidator, Outsourcing Partner for a Wide Variety of Products & Services.
We are your one-stop source for manufacturing, fabrication, engineering, consolidation, integration, outsourcing of custom manufactured and off-shelf products & services. We also private label / white label your products with your brand name if you wish.
Choose your Language
-
Custom Manufacturing of Parts, Components, Assemblies, Finished Products, Machines and Industrial Equipment
-
Domestic & Global Contract Manufacturing
-
Manufacturing Outsourcing
-
Domestic, Global Procurement of Industrial Products
-
Private labeling / White Labeling your Products with your Brand Name
-
Product Finding & Locating Services
-
Global Design and Channel Partnership
-
Engineering Integration
-
Engineering Services
-
Global Consolidation, Warehousing, Logistics
Simply defined, COMPOSITES or COMPOSITE MATERIALS are materials consisting of two or multiple materials with different physical or chemical properties, but when combined they become a material that is different than the constituent materials. We need to point out that the constituent materials remain separate and distinct in the structure. The goal in manufacturing a composite material is to obtain a product that is superior than its constituents and combines each constituent’s desired features. As an example; strength, low weight or lower price may be the motivator behind designing and producing a composite. The type of composites we offer are particle-reinforced composites, fiber-reinforced composites including ceramic-matrix / polymer-matrix / metal-matrix / carbon-carbon / hybrid composites, structural & laminated & sandwich-structured composites and nanocomposites.
The fabrication techniques we deploy in composite material manufacturing are: Pultrusion, prepreg production processes, advanced fiber placement, filament winding, tailored fiber placement, fiberglass spray lay-up process, tufting, lanxide process, z-pinning.
Many composite materials are made up of two phases, the matrix, which is continuous and surrounds the other phase; and the dispersed phase which is surrounded by the matrix.
We recommend that you click here to DOWNLOAD our Schematic Illustrations of Composites and Composite Materials Manufacturing by AGS-TECH Inc.
This will help you better understand the information we are providing you below.
• PARTICLE-REINFORCED COMPOSITES : This category consists of two types: Large-particle composites and dispersion-strengthened composites. In the former type, particle-matrix interactions cannot be treated on the atomic or molecular level. Instead continuum mechanics is valid. On the other hand, in dispersion-strengthened composites particles are generally much smaller in the tens of nanometer ranges. An example of large particle composite is polymers to which fillers have been added. The fillers improve the properties of the material and may replace some of the polymer volume with a more economical material. The volume fractions of the two phases influences the behaviour of the composite. Large particle composites are used with metals, polymers and ceramics. The CERMETS are examples of ceramic / metal composites. Our most common cermet is cemented carbide. It consists of refractory carbide ceramic such as tungsten carbide particles in a matrix of a metal such as cobalt or nickel. These carbide composites are widely used as cutting tools for hardened steel. The hard carbide particles are responsible for the cutting action and their toughness is enhanced by the ductile metal matrix. Thus we obtain the advantages of both materials in a single composite. Another common example of a large particle composite we use is carbon black particulates mixed with vulcanized rubber to obtain a composite with high tensile strength, toughness, tear and abrasion resistance. An example of a dispersion-strengthened composite is metals and metal alloys strengthened and hardened by the uniform dispersion of fine particles of a very hard and inert material. When very small aluminum oxide flakes are added to aluminum metal matrix we obtain sintered aluminum powder which has an enhanced high-temperature strength.
• FIBER-REINFORCED COMPOSITES : This categoy of composites is in fact the most important. The goal to achieve is high strength and stiffness per unit weight. The fiber composition, length, orientation and concentration in these composites is critical in determining the properties and usefulness of these materials. There are three groups of fibers we use: whiskers, fibers and wires. WHISKERS are very thin and long single crystals. They are among the strongest materials. Some example whisker materials are graphite, silicon nitride, aluminum oxide. FIBERS on the other hand are mostly polymers or ceramics and are in polycrystalline or amorphous state. The third group is fine WIRES that have relatively large diameters and consist frequently of steel or tungsten. An example of wire reinforced composite is car tires that incorporates steel wire inside rubber. Depending on the matrix material, we have the following composites:
POLYMER-MATRIX COMPOSITES : These are made of a polymer resin and fibers as the reinforcement ingredient. A subgroup of these called Glass Fiber-Reinforced Polymer (GFRP) Composites contain continuous or discontinuous glass fibers within a polymer matrix. Glass offers high strength, it is economical, easy to fabricate into fibers, and is chemically inert. The disadvantages are their limited rigidity and stiffness, service temperatures being only up to 200 – 300 Centigrade. Fiberglass is suitable for automotive bodies and transportation equipment, marine vehicle bodies, storage containers. They are not suitable for aerospace nor bridge making due to limited rigidity. The other subgroup is called Carbon Fiber-Reinforced Polymer (CFRP) Composite. Here, carbon is our fiber material in the polymer matrix. Carbon is known for its high specific modulus and strength and its capability to maintain these at high temperatures. Carbon fibers can offer us standard, intermediate, high and ultrahigh tensile moduli. Furthermore, carbon fibers do offer diverse physical and mechanical characteristics and therefore a suitable for various custom tailored engineering applications. CFRP composites can be considered to manufacture sports and recreational equipment, pressure vessels and aerospace structural components. Yet, another subgroup, the Aramid Fiber-Reinforced Polymer Composites are also high-strength and modulus materials. Their strength to weight ratios are outstandingly high. Aramid fibers are also known by trade names KEVLAR and NOMEX. Under tension they perform better than other polymeric fiber materials, but they are weak in compression. Aramid fibers are tough, impact resistant, creep and fatigue resistant, stable at high temperatures, chemically inert except against strong acids and bases. Aramid fibers are widely used in sporting goods, bulletproof vests, tires, ropes, fiber optic cable sheats. Other fiber reinforcement materials exist but are used to a lesser degree. These are boron, silicon carbide, aluminum oxide mainly. The polymer matrix material on the other hand is also critical. It determines the maximum service temperature of the composite because the polymer has generally a lower melting and degradation temperature. Polyesters and vinyl esters are widely used as the polymer matrix. Resins are also used and they have excellent moisture resistance and mechanical properties. For example polyimide resin can be used up to about 230 Degrees Celcius.
METAL-MATRIX COMPOSITES : In these materials we use a ductile metal matrix and the service temperatures are generally higher than their constituent components. When compared to polymer-matrix composites, these can have higher operating temperatures, be nonflammable, and may have better degradation resitance against organic fluids. However they are more expensive. Reinforcement materials such as whiskers, particulates, continuous and discontinuous fibers; and matrix materials such as copper, aluminum, magnesium, titanium, superalloys are being commonly used. Example applications are engine components made of aluminum alloy matrix reinforced with aluminum oxide and carbon fibers.
CERAMIC-MATRIX COMPOSITES : Ceramic materials are known for their outstandingly good high temperature reliability. However they are very brittle and have low values for fracture toughness. By embedding particulates, fibers or whiskers of one ceramic into the matrix of another we are able to achieve composites with higher fracture toughnesses. These embedded materials basically inhibit crack propagation inside the matrix by some mechanisms such as deflecting the crack tips or forming bridges across crack faces. As an example, aluminas that are reinforced with SiC whiskers are used as cutting tool inserts for machining hard metal alloys. These can reveal better performances as compared to cemented carbides.
CARBON-CARBON COMPOSITES : Both the reinforcement as well as the matrix are carbon. They have high tensile moduli and strengths at high temperatures over 2000 Centigrade, creep resistance, high fracture toughnesses, low thermal expansion coefficients, high thermal conductivities. These properties make them ideal for applications requiring thermal shock resistance. The weakness of carbon-carbon composites is however its vulnerability against oxidation at high temperatures. Typical examples of usage are hot-pressing molds, advanced turbine engine components manufacturing.
HYBRID COMPOSITES : Two or more different types of fibers are mixed in a single matrix. One can thus tailor a new material with a combination of properties. An example is when both carbon and glass fibers are incorporated into a polymeric resin. Carbon fibers provide low density stiffness and strength but are expensive. The glass on the other hand is inexpensive but lack the stiffness of carbon fibers. The glass-carbon hybrid composite is stronger and tougher and can be manufactured at a lower cost.
PROCESSING OF FIBER-REINFORCED COMPOSITES : For continuous fiber-reinforced plastics with uniformly distributed fibers oriented in the same direction we use the following techniques.
PULTRUSION: Rods, beams and tubes of continuous lengths and constant cross-sections are manufactured. Continuous fiber rovings are impregnated with a thermosetting resin and are pulled through a steel die to preform them to a desired shape. Next, they pass through a precision machined curing die to attain its final shape. Since the curing die is heated, it cures the resin matrix. Pullers draw the material through the dies. Using inserted hollow cores, we are able to obtain tubes and hollow geometries. The pultrusion method is automated and offers us high production rates. Any length of product is possible to produce.
PREPREG PRODUCTION PROCESS : Prepreg is a continuous-fiber reinforcement preimpregnated with a partially cured polymer resin. It is widely used for structural applications. The material comes in tape form and is shipped as a tape. The manufacturer moulds it directly and fully cures it without the need to add any resin. Since prepregs undergo curing reactions at room temperatures, they are stored at 0 Centigrade or lower temperatures. After use the remaining tapes are stored back at low temperatures. Thermoplastic and thermosetting resins are used and reinforcement fibers of carbon, aramid and glass are common. To use prepregs, the the carrier backing paper is first removed and then the fabrication is carried out by laying of the prepreg tape onto a tooled surface (the lay-up process). Several plies may be laid up to obtain the desired thicknesses. Frequent practice is to alternate the fiber orientation to produce a cross-ply or angle-ply laminate. Finally heat and pressure are applied for curing. Both hand processing as well as automated processes are used for cutting prepregs and lay-up.
FILAMENT WINDING : Continuous reinforcing fibers are accurately positioned in a predetermined pattern to follow a hollow and usually cyclindirical shape. The fibers first go through a resin bath and then are wound onto a mandrel by an automated system. After several winding repetitions desired thicknesses are obtained and curing is performed either at room temperature or inside an oven. Now the mandrel is removed and the product is demolded. Filament winding can offer very high strength-to-weight ratios by winding the fibers in circumferential, helical and polar patterns. Pipes, tanks, casings are manufactured using this technique.
• STRUCTURAL COMPOSITES : Generally these are made up of both homogeneous and composite materials. Therefore the properties of these are determined by the constituent materials and geometrical design of its elements. Here are the major types:
LAMINAR COMPOSITES : These structural materials are made of two dimensional sheets or panels with preferred high-strength directions. Layers are stacked and cemented together. By alternating the high-strength directions in the two perpendicular axes, we obtain a composite that has high-strength in both directions in the two-dimensional plane. By adjusting the angles of the layers one can manufacture a composite with strength in the preferred directions. Modern ski is manufactured this way.
SANDWICH PANELS : These structural composites are lightweight but yet have high stiffness and strength. Sandwich panels consist of two outer sheets made of a stiff and strong material like aluminum alloys, fiber reinforced plastics or steel and a core in between the outer sheets. The core needs to be lightweight and most of the time have a low modulus of elasticity. Popular core materials are rigid polymeric foams, wood and honeycombs. Sandwich panels are widely used in the construction industry as roofing material, floor or wall material, and also in the aerospace industries.
• NANOCOMPOSITES : These new materials consist of nanosized particles particles embedded in a matrix. Using nanocomposites we can manufacture rubber materials that are very good barriers to air penetration while maintaning their rubber properties unchanged.