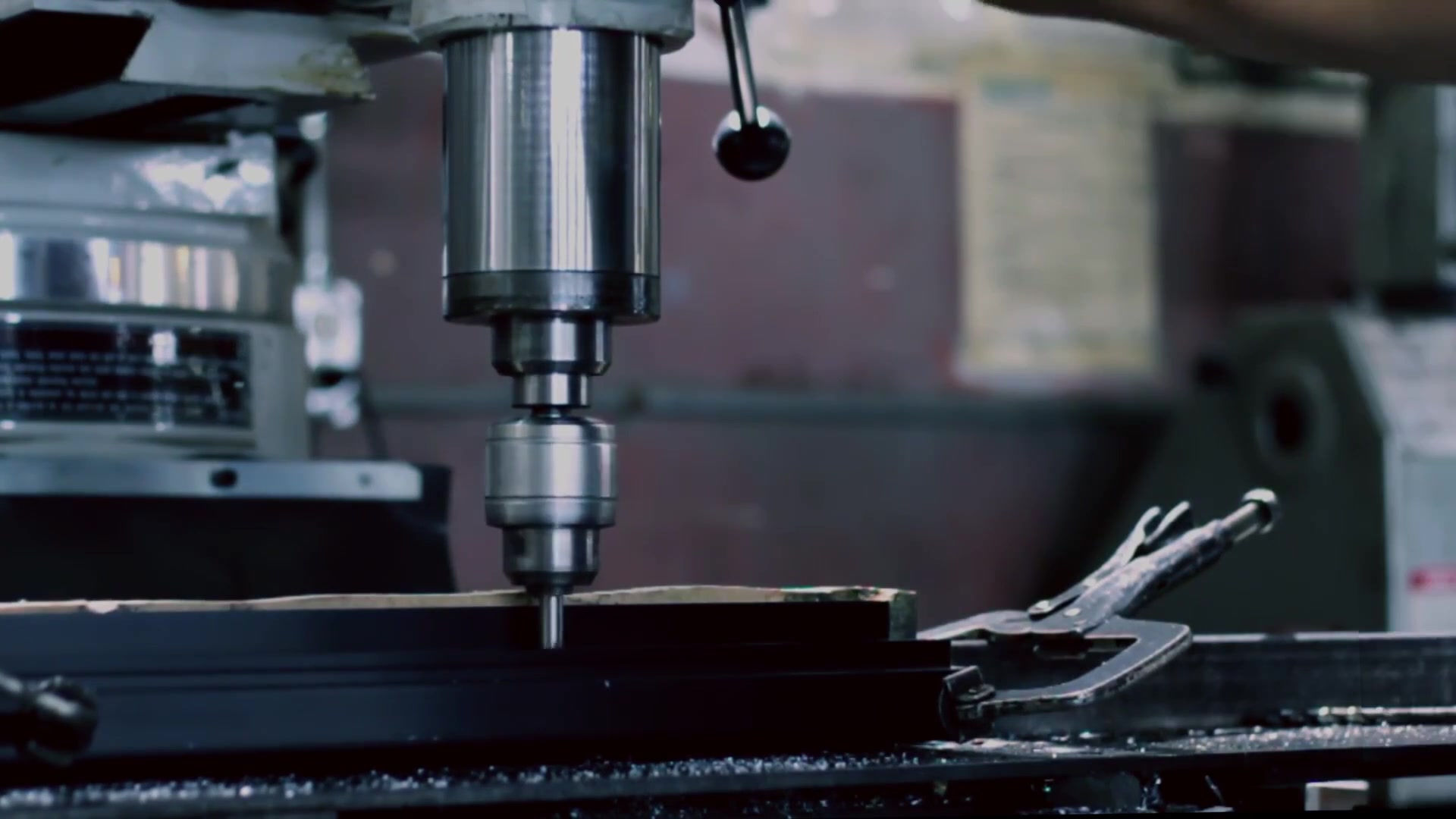
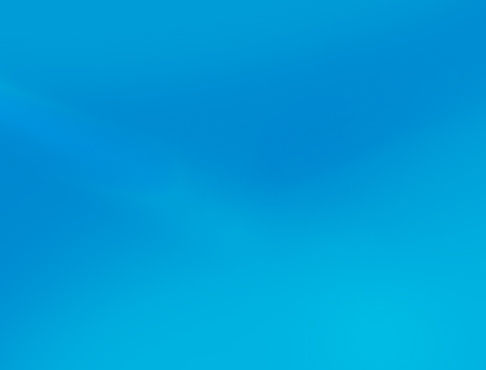
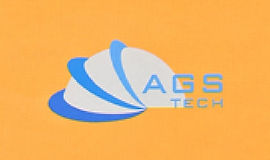
Global Custom Manufacturer, Integrator, Consolidator, Outsourcing Partner for a Wide Variety of Products & Services.
We are your one-stop source for manufacturing, fabrication, engineering, consolidation, integration, outsourcing of custom manufactured and off-shelf products & services. We also private label / white label your products with your brand name if you wish.
Choose your Language
-
Custom Manufacturing of Parts, Components, Assemblies, Finished Products, Machines and Industrial Equipment
-
Domestic & Global Contract Manufacturing
-
Manufacturing Outsourcing
-
Domestic, Global Procurement of Industrial Products
-
Private labeling / White Labeling your Products with your Brand Name
-
Product Finding & Locating Services
-
Global Design and Channel Partnership
-
Engineering Integration
-
Engineering Services
-
Global Consolidation, Warehousing, Logistics
We use the EXTRUSION process to manufacture products with a fixed cross sectional profile such as tubes, pipes and heat sinks. Even though many materials can be extruded, our most common extrusions are made of metal, polymers / plastic, ceramic obtained by either cold, warm or hot extrusion method. We call the extruded parts extrudate or extrudates if plural. Some specialized versions of the process we also perform are overjacketing, coextrusion and compound extrusion. We recommend that you click here to DOWNLOAD our Schematic Illustrations of Metal Ceramic and Plastic Extrusion Processes by AGS-TECH Inc.
This will help you better understand the information we are providing you below.
In extrusion material to be extruded is pushed or drawn through a die that has the desired cross-sectional profile. The process can be used to manufacture complex cross-sections with excellent surface finish and to work on brittle material. One can produce any length of parts using this process. To simplify the process steps:
1.) In warm or hot extrusions the material is heated and loaded into a container in the press. The material is pressed and pushed out of the die.
2.) Produced extrudate is is stretched for straightening, heat treated or cold worked for enhancing its properties.
On the other hand COLD EXTRUSION takes place at around room temperature and has the advantages of less oxidation, high strength, closer tolerances, good surface finish and fastness.
WARM EXTRUSION is performed above room temperature but below recrystallization point. It offers a compromise and balance for required forces, ductility and material properties and is therefore the choice for some applications.
HOT EXTRUSION takes place above the material’s recrystallization temperature. This way it is easier to push the material through the die. However the equipment cost is high.
The more complex an extruded profile, the more costly is the die (tooling) and the lower is the rate of production. The die cross sections as well as thicknesses have limitations that depend on the material to be extruded. Sharp corners in extrusion dies are always undesirable and to be avoided unless necessary.
According to the material that is being extruded, we offer:
• METAL EXTRUSIONS : Most common ones we produce are aluminum, brass, zinc, copper, steel, titanium, magnesium
• PLASTIC EXTRUSION : Plastic is melted and formed into a continuous profile. Our common materials processed are polyethylene, nylon, polystyrene, polyvinyl chloride, polypropylene, ABS plastic, polycarbonate, acrylic. Typical products we manufacture include pipes and tubing, plastic frames. In the process small plastic beads / resin is gravity fed from hopper into barrel of the extrusion machine. Frequently we also mix colorants or other additives into hopper to give the product the required specifications and properties. The material entering the heated barrel is forced by the rotating screw to leave the barrel at the end and move through the screen pack for removal of contaminants in the molten plastic. After passing the screen pack the plastic enters the extrusion die. The die gives the moving soft plastic its profile shape as it passes through. Now the extrudate goes through a water bath for cooling.
Other techniques AGS-TECH Inc. has been using for many years are:
• PIPE & TUBING EXTRUSION : Plastic pipes and tubes are formed when plastics is extruded through a round shaping die and cooled in a water bath, then cut to length or coiled / spooled. Clear or colored, striped, single or dual wall, flexible or rigid, PE, PP, polyurethane, PVC, nylon, PC, silicone, vinyl or else, we have it all. We have stocked tubes as well as the capability to produce according to your specifications. AGS-TECH manufactures tubing to FDA, UL, and LE requirements for medical, electric & electronic, industrial and other applications.
• OVERJACKETING / OVER JACKETING EXTRUSION : This technique applies an outer layer of plastic onto existing wire or cable. Our insulation wires are manufactured with this method.
• COEXTRUSION : Multiple layers of material are simultaneously extruded. The multiple layers are delivered by multiple extruders. The various layer thicknesses can be adjusted to meet customer specifications. This process makes it possible to use multiple polymers each having a different functionality in the product. As a result, one can optimize a range of properties.
• COMPOUND EXTRUSION: A single or multiple polymers are mixed with additives to obtain a plastic compound. Our twin-screw extruders produce compounding extrusions.
Extrusion dies are generally inexpensive compared to metal moulds. If you are paying much more than a few thousand dollars for a small or medium size extrusion die extruding aluminum, you are probably paying too much. We are experts in determining which technique is the most cost effective, fastest and most suitable for your application. Sometimes extruding and then machining a part can save you a lot of cash. Before making a firm decision, ask us our opinion first. We have helped many customers make the right decisions. For some widely used metal extrusions, you can download our brochures and catalogs by clicking on the colored text below. If it is an off-shelf product meeting your requirements, it will be more economical.
Download our medical tube and pipe extrusion capabilities
Download our extruded heat sinks
• SECONDARY MANUFACTURING & FABRICATION PROCESSES FOR EXTRUSIONS :
Among value added processes we offer for extruded products are:
-Custom tube & pipe bending, forming and shaping, tube cutoff, tube end forming, tube coiling, machining and finishing, hole drilling & piercing & punching,
-Custom pipe and tube assemblies, tubular assembly, welding, brazing and soldering
-Custom extrusion bending, forming and shaping
-Cleaning, degreasing, pickling, passivation, polishing, anodizing, plating, painting, heat treating, annealing and hardening, marking, engraving and labeling, custom packaging.