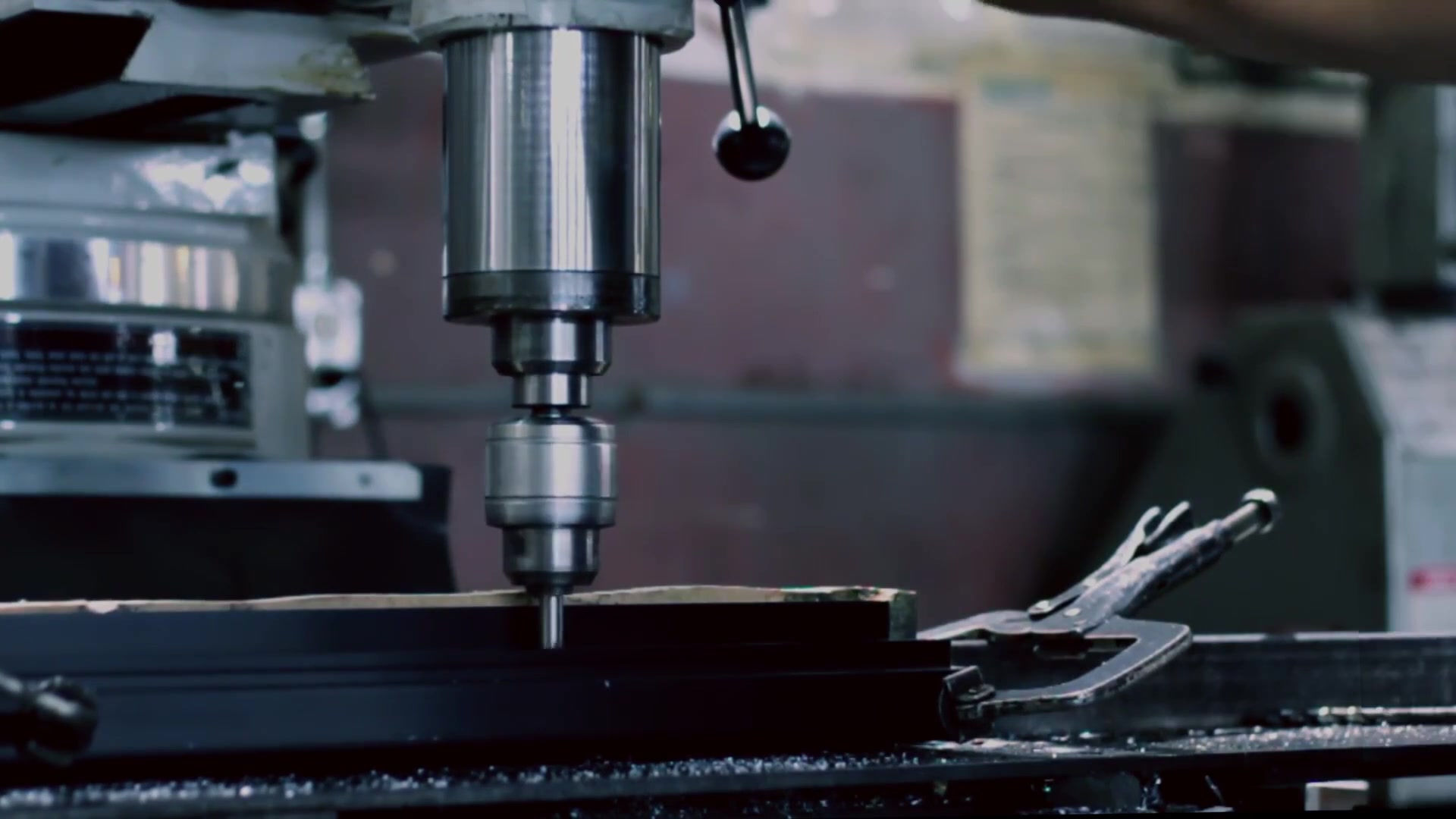
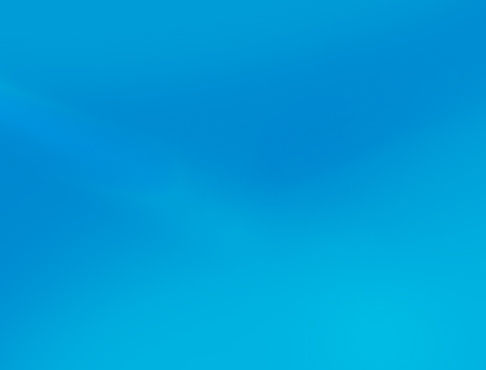
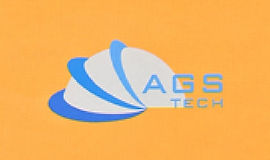
Global Custom Manufacturer, Integrator, Consolidator, Outsourcing Partner for a Wide Variety of Products & Services.
We are your one-stop source for manufacturing, fabrication, engineering, consolidation, integration, outsourcing of custom manufactured and off-shelf products & services. We also private label / white label your products with your brand name if you wish.
Choose your Language
-
Custom Manufacturing of Parts, Components, Assemblies, Finished Products, Machines and Industrial Equipment
-
Domestic & Global Contract Manufacturing
-
Manufacturing Outsourcing
-
Domestic, Global Procurement of Industrial Products
-
Private labeling / White Labeling your Products with your Brand Name
-
Product Finding & Locating Services
-
Global Design and Channel Partnership
-
Engineering Integration
-
Engineering Services
-
Global Consolidation, Warehousing, Logistics
FILTERS remove dirt, water, and other contaminants that can decrease the efficiency and eventually destroy pneumatic and hydraulic equipment. Our filters have high dirt-holding capacity for long life, improved flow paths that lead to better energy efficiency, and some filters can even alert users when they need maintenance. TREATMENT COMPONENTS on the other hand include devices such as regulators, mist separators, dryers, lubricators, adsorber lters eliminating odors. Both off-shelf as well as custom manufactured filters and treatment components can be sourced from us.
PNEUMATIC FILTERS and TREATMENT COMPONENTS: Repairable-inline-filters protect small air tools including grinders, impact wrenches, and screwdrivers. The light and compact aluminum units can install directly before an air tool. Repairable inline filters extend tool life and reduce downtime by capturing foreign particles in the air stream. Repairable inline filters can also be used in low-pressure hydraulic applications. Our other Air-Preparation Units have a lightweight polymer construction and smooth surfaces, and are useful in industries like food and packaging. These includes filter choices of activated carbon, as well as regulators, lubricators, and other modular components that permit standard and custom combinations. Air-preparation units can be customized with lockout or soft-start valves, distribution blocks, filter-regulator combinations, and other accessories. Rapid-clamping system lets users of our filter systems remove and replace one element from the group without disassembling the others. Some of our systems include filters that use centrifugal forces to force water and large solid particles against the side of the housing, where they collect and eventually precipitate to the lower part of the bowl. The air filter captures smaller particles. The units also include adjustable regulators and lubricators that control oil dispersal with an adjustable needle valve. Variations include stacking filters and regulators, bowl and drain options. Metal bowls and bowl guards are now available for modular air-preparation products, in addition to standard polycarbonate bowls. The metal bowls have nylon sight tubes and manual or auto drains for filters. Air-preparation units can include a filters, mist separators, regulators, and lubricators in various combinations. Some of our modular units include pressure regulators, on/off and soft-start valves, filters, dryers, and lubricators, as well as integrated sensors for remote adjustability and monitoring. Differential pressure gages warn users when pressure drop exceeds a certain value and the element should be changed. All our modules can be replaced without disassembling the entire system. Some units can be combined with soft-start and quick-exhaust valves for rapid venting during an emergency shutdown in safety-critical areas. Our Stainless Steel Air Preparation Units include filters with all metal SS 316 stainless steel components, including internal components. All particulate filters use dense-pack elements to ensure maximum impaction, minimal pressure drop, and long duty life. The stainless steel units resist chemical degradation and are well suited for food & beverage, pharmaceutical, natural gas, wastewater-treatment and marine applications. Our Stainless Steel Three-Stage Filtration Systemremoves water vapor, particulates, and oil from compressed air and hydrocarbon gases in corrosive environments. It is designed for applications where clean and dry air is critical to protect downstream equipment and sensitive instruments from premature failure. The three-stage filtration system has two general-purpose filters that remove particles and water, and a third filter, a stainless-steel coalescer, removing oil. Some of our filters are for high-flow applications. Our High-Flow Filters are suited for heavy-duty applications that demand minimum pressure drop. Large filter-element surfaces provide low pressure drop and long life, and an internal deflector plate creates swirling of the air stream to ensure efficient water and dirt separation. Our high-flow filters deploy large-capacity bowls that minimize maintenance operations. Our Compact Modular-Style Air Filters combine the element and bowl in one piece, simplifying element replacement. The units are much smaller compared to others and reduce space requirements. Their bowl is covered with a transparent bowl guard, allowing 360 degrees circumferential monitoring. The modular design permits simple connection with other air-preparation and treatment components. The Energy Efficient Filters are designed to minimize pressure losses and reduce the operating costs of pneumatic systems. The housing’s “bell-mouth” inlet provides a smooth, turbulent-free transition that lets air enter the filters without restriction. A smooth 90° elbow directs air into the filter element, reducing turbulence and pressure losses. Some models of our energy efficient filters also include aerospace turning vanes which efficiently channel air throughout the filter; and upper flow distributors and lower conical diffusers which provide turbulent-free flow through the entire media, including the lowest section of the element. This further increases filters performance and reduces energy consumption. Deep-pleated elements and specially treated filtration media have much much greater filtration surface area compared to conventional wrapped filters and typical pleated filter elements. The elements significantly reduce pressure losses and energy consumption in these filters.
HYDRAULIC FILTERS and TREATMENT COMPONENTS: Over 90% of all hydraulic system failures are caused by contaminants in the fluids. Even when immediate failures do not occur, high contamination levels can drastically decrease operating efficiency. Contamination, which is foreign materials, particles, substances in a fluid system, can exist as a gas, liquid or solid. High contamination levels accelerate component wear, decrease service life and increase maintenance costs. Contaminants either enter the system from outside (ingestion) or are generated from within (ingression). New systems often have contaminants left behind from manufacturing and assembly operations. If they are not filtered as they enter the circuit, both the original fluid and make-up fluids are likely to contain more contaminants than the system can tolerate. Most systems ingest contaminants through components such as inefficient air breathers and worn cylinder rod seals during operation. Airborne contaminants can gain admittance during routine servicing or maintenance, friction and heat can also produce internally generated contamination. Pick up high-quality hydraulic filters from AGS-TECH to help keep your hydraulic fluid reservoir safe from particle and water vapor damage. Shop with us and you'll find hydraulic spin-on filter heads with a variety of filter ratings. You can trust us to provide you with high-quality hydraulic filters to help you keep your systems running smoothly. AGS-TECH can help you select the correct filters which will provide the optimal cleanliness solution for your hydraulic system. We supply different types of hydraulic filters:
• Suction filters
• Return line filters
• Bypass filter systems
• Pressure filters
• Fillers and breathers
• Filter elements
We also supply interchange elements at competitive prices and equivalent or better quality compared to the OEM's originally installed hydraulic filter elements. AGS-TECH Inc. can also supply the indicators that monitor a system's contamination levels. Contamination indicators ensure that our customers can maintain the cleanliness of their hydraulic systems and their filters efficiency and condition.
Suction Filters: The suction filters provide protection of the hydraulic pumps from particles larger than 10 microns. Suction filters are useful if there is any likelihood of pump damage due to larger particles or pieces of dirt. This can occur when it is difficult to clean the tank or if several hydraulic systems use the same tank for oil supply. Characteristics of suction filters are their low cost, servicing difficulty, because mounting is below fluid level, grade of filtration which is coarse filtration, 25 to 90 microns using stainless steel filter mesh, 10 microns using paper, 10 to 25 microns using glass fiber, they are equipped with bypass check valves and have very low opening pressures.
Pressure Line Filters: They are also referred to as a high pressure filters, and are most commonly used in a hydraulic systems. Pressure line filters are also equipped with bypass check valves. When pressure line filters are installed directly in the back of pumps, they act as the main filters for the complete flow and protect hydraulic components against wear. Characteristics of pressure line filters are their medium cost, high grade of filtration, easy use of clogging indicators, their grade of filtration which is the finest level, 25 to 660 microns using stainless steel filter mesh, 1 to 20 microns using paper / glass fiber and polyester, they are equipped with bypass check valves that open at 7 bar (maximum). Pressure line filters act as safety filters when installed in front of an endangered component such as a servo control valve. To ensure maximum functionality of these critical components, the normal practice is that the pressure line safety filter must be fitted as close as possible to the component it is protecting.
Return Line Filters: Almost every hydraulic system uses return line filters which are designed to mount directly onto the tank cover. Therefore, you can easily replace filter element(s) when needed. Users select return line filter based on the maximum flow of the hydraulic system. Characteristics of a return line filter are their low cost, ease of servicing, no downtime because they incorporate duplex filters, their grade of fine filtration, 40 to 90 microns using stainless steel filter mesh, 10 microns using filter paper, 10 to 25 microns using glass fiber, return line filters are equipped with a bypass check valve that opens at 2 bar (maximum).
Bypass Filtration: Hydraulic systems use bypass filters as main flow filters, i.e. system filters or working filters. These systems generally consist of bypass units complete with pumps, filters and oil coolers. Bypass filters are also used in mobile hydraulics and are connected to the pressure side of the system. Flow control valves ensure constant flow with low-flow pulsations. Characteristics of bypass filters are their high costs, high returns due to improved component lifetime and slowing down of the ageing process of the hydraulic fluids, very high grade of filtration around 0.5 microns, silt removal from the fluid, flow through bypass filters are completely free of pressure shocks, possibility of offline filtration. With 0.5 micron filtration capability, bypass filters allow very dense hydraulic filtration by removing even the smallest dirt particles. Silt would otherwise degrade the dopes, that are added to the hydraulic oil to form a protecting layer for the moving parts of the system.
Fillers and Breathers: Breathers or fillers are used when the air compresses or expands due to increasing/decreasing levels of fluid in the tank. The function of a breather is to filter the air flowing in and out of the tank. Breathers may be designed to work as fillers. Breathers are currently considered to be the most important components for filtration in hydraulic systems. A large amount of ambient contamination enters hydraulic systems through low quality ventilation devices. Other measures, such as the pressurization of oil tanks, are generally speaking uneconomic when compared to the highly effective breathers we have.
Contamination Indicators: The grade of filtration determines the level of contamination in filters. Contamination indicators can determine the level of contamination in filters. Contamination indicators consist of a sensor and warning device. Generally, the hydraulic fluid enters the inlet of the filter, passes through the filter element, and leaves the filter through the outlet. As the fluid passes through the filter element, impurities are deposited on the outside of the element. With accumulating deposits, a differential pressure is build up between the inlet and outlet of the filter. The pressure is sensed across the contamination indicator switch, and actuates a warning device such as flashing lights. When warning signal is observed or heard, the hydraulic pump is stopped and the filter serviced, cleaned, or replaced. Filters with a grade of filtration of 1 micron are more vulnerable to clogging than filters with a filtration grade of 10 microns.
Please click on highlighted text below to download our product brochures for pneumatic filters:
- Private Label Industrial Filters (We can put your company name and logo on these filters)