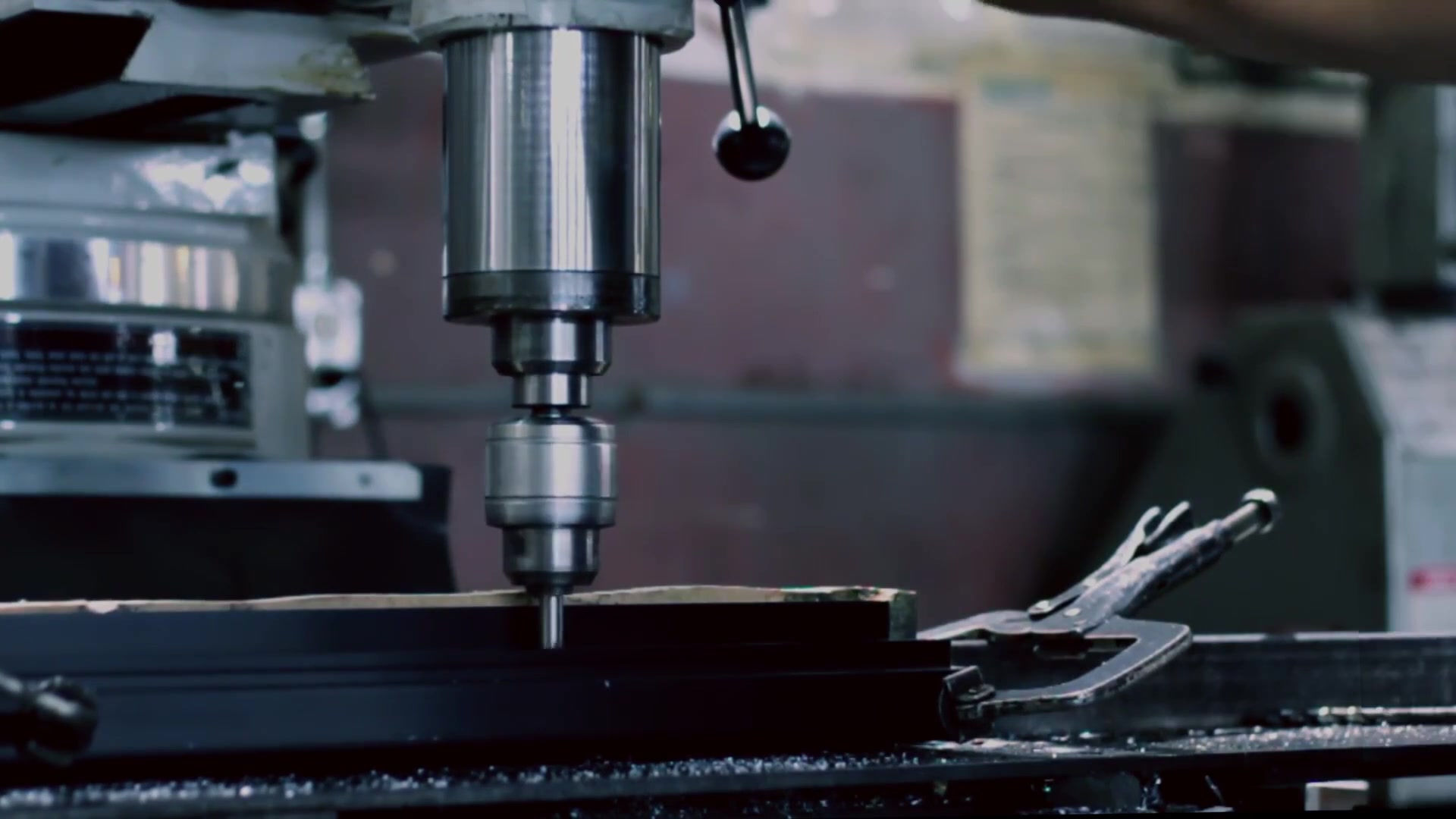
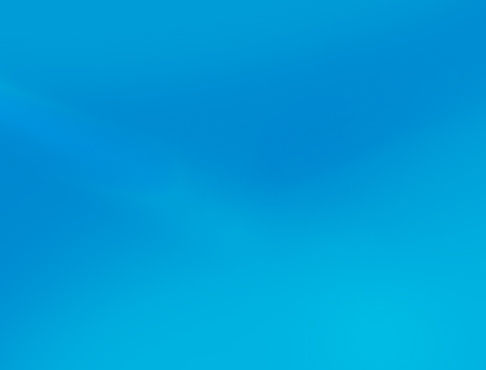
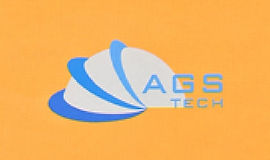
Global Custom Manufacturer, Integrator, Consolidator, Outsourcing Partner for a Wide Variety of Products & Services.
We are your one-stop source for manufacturing, fabrication, engineering, consolidation, integration, outsourcing of custom manufactured and off-shelf products & services. We also private label / white label your products with your brand name if you wish.
Choose your Language
-
Custom Manufacturing of Parts, Components, Assemblies, Finished Products, Machines and Industrial Equipment
-
Domestic & Global Contract Manufacturing
-
Manufacturing Outsourcing
-
Domestic, Global Procurement of Industrial Products
-
Private labeling / White Labeling your Products with your Brand Name
-
Product Finding & Locating Services
-
Global Design and Channel Partnership
-
Engineering Integration
-
Engineering Services
-
Global Consolidation, Warehousing, Logistics
LASER CUTTING is a HIGH-ENERGY-BEAM MANUFACTURING technology that uses a laser to cut materials, and is typically used for industrial manufacturing applications. In LASER BEAM MACHINING (LBM), a laser source focuses optical energy on the surface of the workpiece. Laser cutting directs the highly focused and high-density output of a high-power laser, by computer, at the material to be cut. The targeted material then either melts, burns, vaporizes away, or is blown away by a jet of gas, in a controlled manner leaving an edge with a high-quality surface finish. Our industrial laser cutters are suitable for cutting flat-sheet material as well as structural and piping materials, metallic and nonmetallic workpieces. Generally no vacuum is required in the laser beam machining and cutting processes. There are several types of lasers used in laser cutting and manufacturing. The pulsed or continuous wave CO2 LASER is suited for cutting, boring, and engraving. The NEODYMIUM (Nd) and neodymium yttrium-aluminum-garnet (Nd-YAG) LASERS are identical in style and differ only in application. The neodymium Nd is used for boring and where high energy but low repetition is required. The Nd-YAG laser on the other hand is used where very high power is required and for boring and engraving. Both CO2 and Nd/ Nd-YAG lasers can be used for LASER WELDING. Other lasers we use in manufacturing include Nd:GLASS, RUBY and EXCIMER. In Laser Beam Machining (LBM), the following parameters are important: The reflectivity and thermal conductivity of the workpiece surface and its specific heat and latent heat of melting and evaporation. The efficiency of the Laser Beam Machining (LBM) process increases with decreasing of these parameters. The cutting depth can be expressed as:
t ~ P / (v x d)
This means, the cutting depth “t” is proportional to the power input P and inversely proportional to cutting speed v and laser-beam spot diameter d. The surface produced with LBM is generally rough and has a heat-affected zone.
CARBONDIOXIDE (CO2) LASER CUTTING and MACHINING: The DC-excited CO2 lasers get pumped by passing a current through the gas mix whereas the RF-excited CO2 lasers use radio frequency energy for excitation. The RF method is relatively new and has become more popular. DC designs require electrodes inside the cavity, and therefore they can have electrode erosion and plating of electrode material on the optics. To the contrary, RF resonators have external electrodes and therefore they are not prone to those problems. We use CO2 lasers in industrial cutting of many materials such as mild steel, aluminum, stainless steel, titanium and plastics.
YAG LASER CUTTING and MACHINING: We use YAG lasers for cutting and scribing metals and ceramics. The laser generator and external optics require cooling. Waste heat is generated and transferred by a coolant or directly to air. Water is a common coolant, usually circulated through a chiller or heat transfer system.
EXCIMER LASER CUTTING and MACHINING: An excimer laser is a kind of laser with wavelengths in the ultraviolet region. The exact wavelength depends on the molecules used. For example the following wavelengths are associated with the molecules shown in parantheses: 193 nm (ArF), 248 nm (KrF), 308 nm (XeCl), 353 nm (XeF). Some excimer lasers are tunable. Excimer lasers have the attractive property that they can remove very fine layers of surface material with almost no heating or change to the remainder of the material. Therefore excimer lasers are well suited to precision micromachining of organic materials such as some polymers and plastics.
GAS-ASSISTED LASER CUTTING: Sometimes we use laser beams in combination with a gas stream, like oxygen, nitrogen or argon for cutting thin sheet materials. This is done using a LASER-BEAM TORCH. For stainless steel and aluminum we use high-pressure inert-gas-assisted laser cutting using nitrogen. This results in oxide-free edges to improve weldability. These gas streams also blow away molten and vaporized material from workpiece surfaces.
In a LASER MICROJET CUTTING we have a water-jet guided laser in which a pulsed laser beam is coupled into a low-pressure water jet. We use it to perform laser cutting while using the water jet to guide the laser beam, similar to an optical fiber. The advantages of laser microjet are that the water also removes debris and cools the material, it is faster than traditional ''dry'' laser cutting with higher dicing speeds, parallel kerf and omnidirectional cutting capability.
We deploy different methods in cutting using lasers. Some of the methods are vaporization, melt and blow, melt blow and burn, thermal stress cracking, scribing, cold cutting and burning, stabilized laser cutting.
- Vaporization cutting: The focused beam heats the surface of the material to its boiling point and creates a hole. The hole leads to a sudden increase in absorptivity and quickly deepens the hole. As the hole deepens and the material boils, the generated vapor erodes the molten walls blowing material out and further enlarging the hole. Non melting material such as wood, carbon and thermoset plastics are usually cut by this method.
- Melt and blow cutting: We use high-pressure gas to blow molten material from the cutting area, decreasing the required power. The material is heated to its melting point and then a gas jet blows the molten material out of the kerf. This eliminates the need to raise the temperature of the material any further. We cut metals with this technique.
- Thermal stress cracking: Brittle materials are sensitive to thermal fracture. A beam is focused on the surface causing localized heating and thermal expansion. This results in a crack that can then be guided by moving the beam. We use this technique in glass cutting.
- Stealth dicing of silicon wafers: The separation of microelectronic chips from silicon wafers is performed by the stealth dicing process, using a pulsed Nd:YAG laser, the wavelength of 1064 nm is well adopted to the electronic band gap of silicon (1.11 eV or 1117 nm). This is popular in semiconductor device fabrication.
- Reactive cutting: Also called flame cutting, this technique can be resembled to oxygen torch cutting but with a laser beam as the ignition source. We use this for cutting carbon steel in thicknesses over 1 mm and even very thick steel plates with little laser power.
PULSED LASERS provide us a high-power burst of energy for a short period and are very effective in some laser cutting processes, such as piercing, or when very small holes or very low cutting speeds are required. If a constant laser beam was used instead, the heat could reach the point of melting the entire piece being machined. Our lasers have the ability to pulse or cut CW (Continuous Wave) under NC (numerical control) program control. We use DOUBLE PULSE LASERS emitting a series of pulse pairs to improve material removal rate and hole quality. The first pulse removes material from the surface and the second pulse prevents the ejected material from readhering to the side of the hole or cut.
Tolerances and surface finish in laser cutting and machining are outstanding. Our modern laser cutters have positioning accuracies in the neighborhood of 10 micrometers and repeatabilities of 5 micrometers. Standard roughnesses Rz increase with the sheet thickness, but decreases with laser power and cutting speed. The laser cutting and machining processes are capable of achieving close tolerances, often to within 0.001 inch (0.025 mm) Part geometry and the mechanical features of our machines are optimized to achieve best tolerance capabilities. Surface finishes we can obtain from laser beam cutting may range between 0.003 mm to 0.006 mm. Generally we easily achieve holes with 0.025 mm diameter, and holes as small as 0.005 mm and hole depth-to-diameter ratios of 50 to 1 have been produced in various materials. Our simplest and most standard laser cutters will cut carbon steel metal from 0.020–0.5 inch (0.51–13 mm) in thickness and can easily be up to thirty times faster than standard sawing.
Laser-beam machining is used widely for drilling and cutting of metals, nonmetals and composite materials. Advantages of laser cutting over mechanical cutting include easier workholding, cleanliness and reduced contamination of the workpiece (since there is no cutting edge as in traditional milling or turning which can become contaminated by the material or contaminate the material, i.e. bue build-up). The abrasive nature of composite materials may make them difficult to machine by conventional methods but easy by laser machining. Because the laser beam does not wear during the process, precision obtained may be better. Because laser systems have a small heat-affected zone, there is also a lesser chance of warping the material that is being cut. For some materials laser cutting can be the only option. Laser-beam cutting processes are flexible, and fiber optic beam delivery, simple fixturing, short set-up times, availability of three dimensional CNC systems make it possible for laser cutting and machining to compete successfully with other sheet metal fabrication processes such as punching. This being said, laser technology can sometimes be combined with the mechanical fabrication technologies for improved overall efficiency.
Laser cutting of sheet metals has the advantages over plasma cutting of being more precise and using less energy, however, most industrial lasers cannot cut through the greater metal thickness that plasma can. Lasers operating at higher powers such as 6000 Watts are approaching plasma machines in their ability to cut through thick materials. However the capital cost of these 6000 Watt laser cutters is much higher than that of plasma cutting machines capable of cutting thick materials like steel plate.
There are also disadvantages of laser cutting and machining. Laser cutting involves high power consumption. Industrial laser efficiencies may range from 5% to 15%. The power consumption and efficiency of any particular laser will vary depending on output power and operating parameters. This will depend on type of laser and how well the laser matches the work at hand. Amount of laser cutting power required for a particular task depends on the material type, thickness, process (reactive/inert) used and the desired cutting rate. The maximum production rate in laser cutting and machining is limited by a number of factors including laser power, process type (whether reactive or inert), material properties and thickness.
In LASER ABLATION we remove material from a solid surface by irradiating it with a laser beam. At low laser flux, the material is heated by the absorbed laser energy and evaporates or sublimates. At high laser flux, the material is typically converted to a plasma. High power lasers clean a large spot with a single pulse. Lower power lasers use many small pulses which may be scanned across an area. In laser ablation we remove material with a pulsed laser or with a continuous wave laser beam if the laser intensity is high enough. Pulsed lasers can drill extremely small, deep holes through very hard materials. Very short laser pulses remove material so quickly that the surrounding material absorbs very little heat, therefore laser drilling can be done on delicate or heat-sensitive materials. Laser energy can be selectively absorbed by coatings, therefore CO2 and Nd:YAG pulsed lasers can be used to clean surfaces, remove paint and coating, or prepare surfaces for painting without damaging the underlying surface.
We use LASER ENGRAVING and LASER MARKING to engrave or mark an object. These two techniques are in fact the most widely used applications. No inks are used, nor does it involve tool bits which contact the engraved surface and wear out which is the case with traditional mechanical engraving and marking methods. Materials specially designed for laser engraving and marking include laser-sensitive polymers and special new metal alloys. Although laser marking and engraving equipment is relatively more expensive compared to alternatives such as punches, pins, styli, etching stamps….etc., they have become more popular due to their accuracy, reproducibility, flexibility, ease of automation and on-line application in a wide variety of manufacturing environments.
Finally, we use laser beams for several other manufacturing operations:
- LASER WELDING
- LASER HEAT TREATING: Small-scale heat treating of metals and ceramics to modify their surface mechanical and tribological properties.
- LASER SURFACE TREATMENT / MODIFICATION: Lasers are used to clean surfaces, introduce functional groups, modify surfaces in an effort to improve adhesion prior to coating deposition or joining processes.