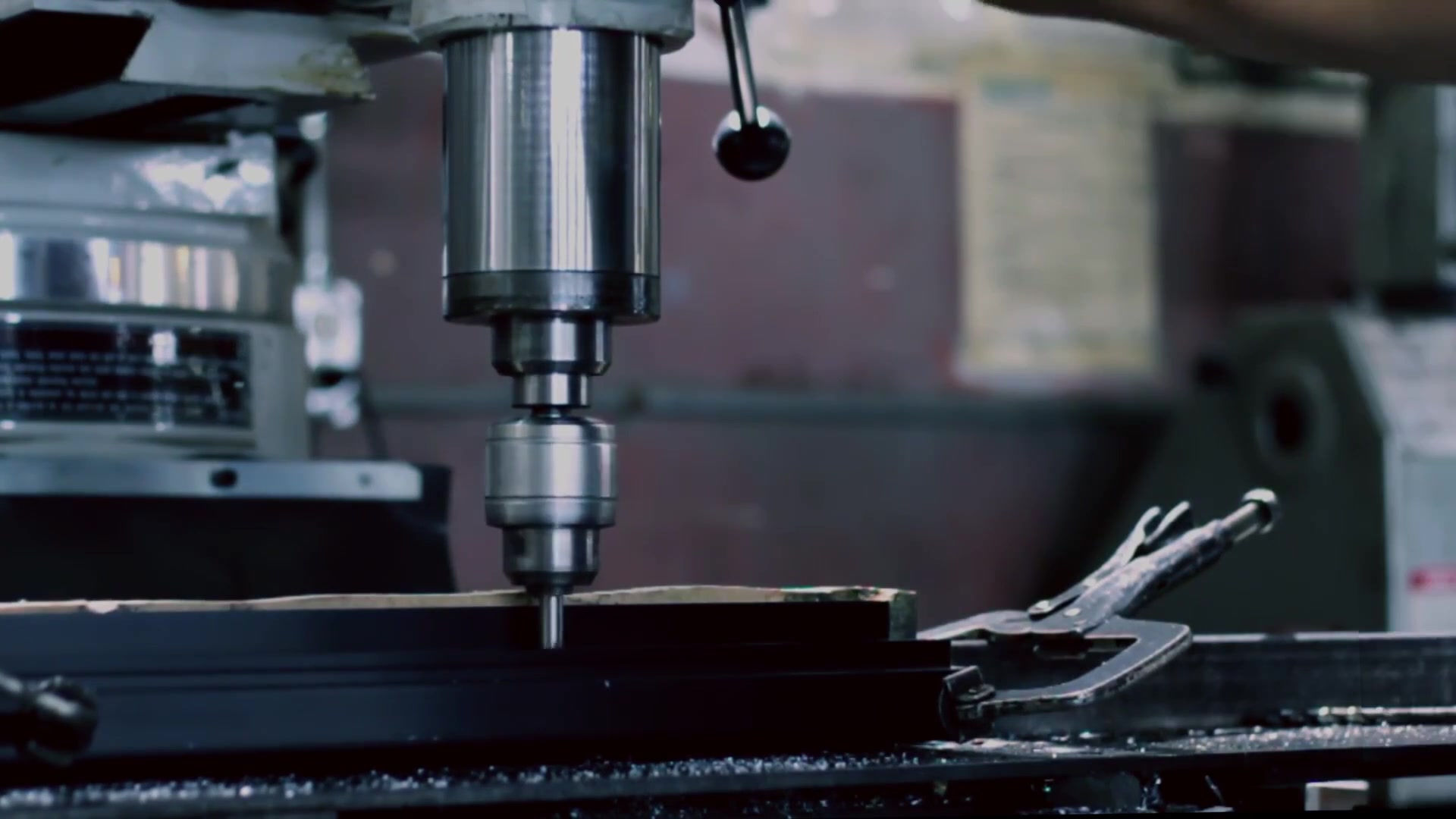
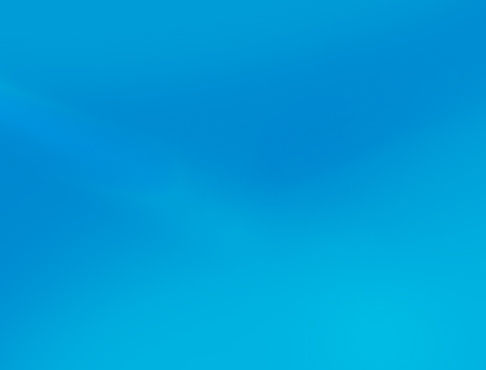
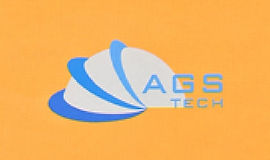
Global Custom Manufacturer, Integrator, Consolidator, Outsourcing Partner for a Wide Variety of Products & Services.
We are your one-stop source for manufacturing, fabrication, engineering, consolidation, integration, outsourcing of custom manufactured and off-shelf products & services. We also private label / white label your products with your brand name if you wish.
Choose your Language
-
Custom Manufacturing of Parts, Components, Assemblies, Finished Products, Machines and Industrial Equipment
-
Domestic & Global Contract Manufacturing
-
Manufacturing Outsourcing
-
Domestic, Global Procurement of Industrial Products
-
Private labeling / White Labeling your Products with your Brand Name
-
Product Finding & Locating Services
-
Global Design and Channel Partnership
-
Engineering Integration
-
Engineering Services
-
Global Consolidation, Warehousing, Logistics
Among the large number of MECHANICAL TEST INSTRUMENTS we focus our attention to the most essential and popular ones: IMPACT TESTERS, CONCRETE TESTERS / SCHMIDT HAMMER, TENSION TESTERS, COMPRESSION TESTING MACHINES, TORSION TEST EQUIPMENT, FATIGUE TEST MACHINE, THREE & FOUR POINT BENDING TESTERS, COEFFICIENT OF FRICTION TESTERS, HARDNESS & THICKNESS TESTERS, SURFACE ROUGHNESS TESTERS, VIBRATION METERS, TACHOMETERS, PRECISION ANALYTICAL BALANCE. We offer our customers quality brands such as ELCOMETER, SADT, SINOAGE for under list prices. Please choose from the downloadable catalogs below the brand name and model number of the equipment you need and tell us whether you want a brand new or refurbished / used equipment:
AMETEK-LLOYD Instruments Materials Testing (Versatile Materials Testing Equipment, Universal Test Machines, Tensile Strength, Compressibility, Hardness, Elasticity, Peeling, Adhesion...etc.)
ELCOMETER Inspection Equipment Catalog (Physical Test Equipment, Concrete Inspection Equipment, Concrete Test Hammers, Fineness Of Grind/Dispersion, Density & Specific Gravity, Viscosity & Flow Measurement, Film Application & Test Charts, Drying Time & Permeability, Washability & Abrasion, Hardness & Scratch Resistance, Elasticity, Bend & Impact Testers, Flash Point)
HAIDA Adhesive Tape Peel Test Machine
HAIDA Computerized Universal Test Machine with Extensometer
HAIDA Computerized Universal Test Machine with Large Capacity (Double Column)
HAIDA Computer Servo Tensile Test Machine
HAIDA Desktop Tensile Test Machine
HAIDA Double-Column Universal Testing Machine
HAIDA Electro-Hydraulic Universal Testing Machine
HAIDA Extra - Height Tensile Test Machine
HAIDA Universal Testing Machine
HAIDA Universal Test Machine with Temperature Chamber
INSTRON Compression and Tension Test Instruments
SADT-SINOAGE Brand Metrology and Test Equipment, please CLICK HERE. Here you will find some of these testing equipment such as concrete testers and surface roughness tester.
Let us examine these test devices in some detail:
SCHMIDT HAMMER / CONCRETE TESTER : This test instrument, also sometimes called a SWISS HAMMER or a REBOUND HAMMER, is a device to measure the elastic properties or strength of concrete or rock, mainly surface hardness and penetration resistance. The hammer measures the rebound of a spring-loaded mass impacting against the surface of the sample. The test hammer will hit the concrete with a predetermined energy. The hammer’s rebound depends on the hardness of the concrete and is measured by the test equipment. Taking a conversion chart as a reference, the rebound value can be used to determine the compressive strength. The Schmidt hammer is an arbitrary scale ranging from 10 to 100. Schmidt hammers come with several different energy ranges. Their energy ranges are: (i) Type L-0.735 Nm impact energy, (ii) Type N-2.207 Nm impact energy; and (iii) Type M-29.43 Nm impact energy. Local variation in the sample. To minimize local variation in the samples it is recommended to take a selection of readings and take their average value. Prior to testing, the Schmidt hammer needs to be calibrated using a calibration test anvil supplied by the manufacturer. 12 readings should be taken, dropping the highest and lowest, and then taking the average of the ten remaining readings. This method is considered an indirect measurement of the strength of the material. It provides an indication based on surface properties for comparison between samples. This test method for testing concrete is governed by ASTM C805. On the other hand, the ASTM D5873 standard describes the procedure for testing of rock. Inside of our SADT brand catalog you will find the following products: DIGITAL CONCRETE TEST HAMMER SADT Models HT-225D/HT-75D/HT-20D - The SADT Model HT-225D is an integrated digital concrete test hammer combining data processor and test hammer into a single unit. It is widely used for non destructive quality testing of concrete and building materials. From its rebound value, the compressive strength of concrete can be calculated out automatically. All test data can be stored in memory and transferred to PC by USB cable or wirelessly by Bluetooth. The models HT-225D and HT-75D have measuring range of 10 – 70N/mm2, whereas the model HT-20D has only 1 – 25N/mm2. The impact energy of HT-225D is 0.225 Kgm and is suitable for testing ordinary building and bridge construction, the impact energy of HT-75D is 0.075 Kgm and is suitable for testing small and impact-sensitive parts of concrete and artificial brick, and finally the impact energy of HT-20D is 0.020Kgm and suitable for testing mortar or clay products.
IMPACT TESTERS: In many manufacturing operations and during their service lives, many components need to be subjected to impact loading. In the impact test, the notched specimen is placed in an impact tester and broken with a swinging pendulum. There are two major types of this test: The CHARPY TEST and the IZOD TEST. For the Charpy test the specimen are supported at both ends, whereas for the Izod test they are supported only at one end like a cantilever beam. From the amount of swing of the pendulum, the energy dissipated in breaking the specimen is obtained, this energy is the impact toughness of the material. Using the impact tests, we can determine the ductile-brittle transition temperatures of materials. Materials with high impact resistance generally have high strength and ductility. These tests also reveal the sensitivity of a material’s impact toughness to surface defects, because the notch in the specimen can be considered a surface defect.
TENSION TESTER : The strength-deformation characteristics of materials are determined using this test. Test specimen are prepared according to ASTM standards. Typically, solid and round specimens are tested, but flat sheets and tubular samples may also be tested using tension test. The original length of a specimen is the distance between gage marks on it and is typically 50 mm long. It is denoted as lo. Longer or shorter lengths can be used depending on the specimens and products. The original cross-sectional area is denoted as Ao. The engineering stress or also called nominal stress is then given as:
Sigma = P / Ao
And the engineering strain is given as:
e = (l – lo) / lo
In the linear elastic region, the specimen elongates proportionately to the load up to the proportional limit. Beyond this limit, even though not linearly, the specimen will continue to deform elastically up to the yield point Y. In this elastic region, the material will return to its original length if we remove the load. Hooke’s Law applies in this region and gives us the Young’s Modulus:
E = Sigma / e
If we increase the load and move beyond the yield point Y, the material begins to yield. In other words, the specimen begins to undergo plastic deformation. Plastic deformation means permanent deformation. The cross-sectional area of the specimen decreases permanently and uniformly. If specimen is unloaded at this point, the curve follows a straight line downward and parallel to the original line in the elastic region. If the load is further increased, the curve reaches a maximum and begins to decrease. The maximum stress point is called the tensile strength or ultimate tensile strength and is denoted as UTS. The UTS can be interpreted as the overall strength of materials. When load is greater than the UTS, necking occurs on the specimen and the elongation between gage marks is no longer uniform. In other words, the specimen becomes really thin at the location where necking occurs. During necking, the elastic stress drops. If the test is continued, the engineering stress drops further and the specimen fractures at the necking region. The stress level at fracture is the fracture stress. The strain at point of fracture is an indicator of ductility. The strain up to the UTS is referred to as uniform strain, and the elongation at fracture is referred to as total elongation.
Elongation = ((lf – lo) / lo) x 100
Reduction of Area = ((Ao – Af) / Ao) x 100
Elongation and reduction of area are good indicators of ductility.
COMPRESSION TESTING MACHINE ( COMPRESSION TESTER ) : In this test, the specimen is subjected to a compressive load contrary to the tensile test where the load is tensile. Generally, a solid cylindrical specimen is placed between two flat plates and compressed. Using lubricants at the contact surfaces, a phenomenon known as barreling is prevented. Engineering strain rate in compression is given by:
de / dt = - v / ho, where v is die speed, ho original specimen height.
True strain rate on the other hand is:
de = dt = - v/ h, with h being the instantaneous specimen height.
To keep the true strain rate constant during the test, a cam plastometer thru a cam action reduces the magnitude of v proportionally as the specimen height h decreases during the test. Using the compression test ductilities of materials are determined by observing cracks formed on barreled cylindrical surfaces. Another test with some differences in the die and workpiece geometries is the PLANE-STRAIN COMPRESSION TEST, which gives us the yield stress of the material in plane strain denoted widely as Y’. Yield stress of materials in plane strain can be estimated as:
Y’ = 1.15 Y
TORSION TEST MACHINES (TORSIONAL TESTERS) : The TORSION TEST is another widely used method for determining material properties. A tubular specimen with a reduced mid-section is used in this test. Shear stress, T is given by:
T = T / 2 (Pi) (square of r) t
Here, T is the applied torque, r is the mean radius and t is the thickness of the reduced section in the middle of the tube. Shear strain on the other hand is given by:
ß = r Ø / l
Here l is the length of the reduced section and Ø is the twist angle in radians. Within the elastic range, the shear modulus (modulus of rigidity) is expressed as:
G = T / ß
The relation between shear modulus and the modulus of elasticity is:
G = E / 2( 1 + V )
The torsion test is applied to solid round bars at elevated temperatures to estimate the forgeability of metals. The more twists the material can withstand prior to failure, the more forgeable it is.
THREE & FOUR POINT BENDING TESTERS : For brittle materials, the BEND TEST (also called FLEXURE TEST) is suitable. A rectangularly shaped specimen is supported at both ends and a load is applied vertically. The vertical force is applied at either one point as in the case of three point bending tester, or at two points as in the case of a four point test machine. The stress at fracture in bending is referred to as the modulus of rupture or transverse rupture strength. It is given as:
Sigma = M c / I
Here, M is the bending moment, c is one-half of the specimen depth and I is the moment of inertia of the cross-section. The magnitude of stress is the same in both three and four-point bending when all other parameters are kept constant. The four-point test is likely to result in a lower modulus of rupture as compared to the three-point test. Another superiority of the four-point bending test over the three point bending test is that its results are more consistent with less statistical scattering of values.
FATIGUE TEST MACHINE: In FATIGUE TESTING, a specimen is subjected repeatedly to various states of stress. The stresses are generally a combination of tension, compression and torsion. The test process can be resembled to bending a piece of wire alternately in one direction, then the other until it fractures. The stress amplitude can be varied and is denoted as “S”. The number of cycles to cause total failure of the specimen is recorded and is denoted as “N”. Stress amplitude is the maximum stress value in tension and compression to which the specimen is subjected. One variation of the fatigue test is performed on a rotating shaft with a constant downward load. The endurance limit (fatigue limit) is defined as the max. stress value the material can withstand without fatigue failure regardless of the number of cycles. Fatigue strength of metals is related to their ultimate tensile strength UTS.
COEFFICIENT OF FRICTION TESTER : This test equipment measures the ease with which two surfaces in contact are able to slide past one another. There are two different values associated with the coefficient of friction, namely the static and kinetic coefficient of friction. Static friction applies to the force necessary to initialize motion between the two surfaces and kinetic friction is the resistance to sliding once the surfaces are in relative motion. Appropriate measures need to be taken prior to testing and during testing to ensure freedom from dirt, grease and other contaminants that could adversely affect test results. ASTM D1894 is the main coefficient of friction test standard and is used by many industries with different applications and products. We are here to offer you the most suitable test equipment. If you need a custom set-up specifically designed for your application, we can modify existing equipment accordingly in order to meet your requirements and needs.
HARDNESS TESTERS : Please go to our related page by clicking here
THICKNESS TESTERS : Please go to our related page by clicking here
SURFACE ROUGHNESS TESTERS : Please go to our related page by clicking here
VIBRATION METERS : Please go to our related page by clicking here
TACHOMETERS : Please go to our related page by clicking here
For details and other similar equipment, please visit our equipment website: http://www.sourceindustrialsupply.com