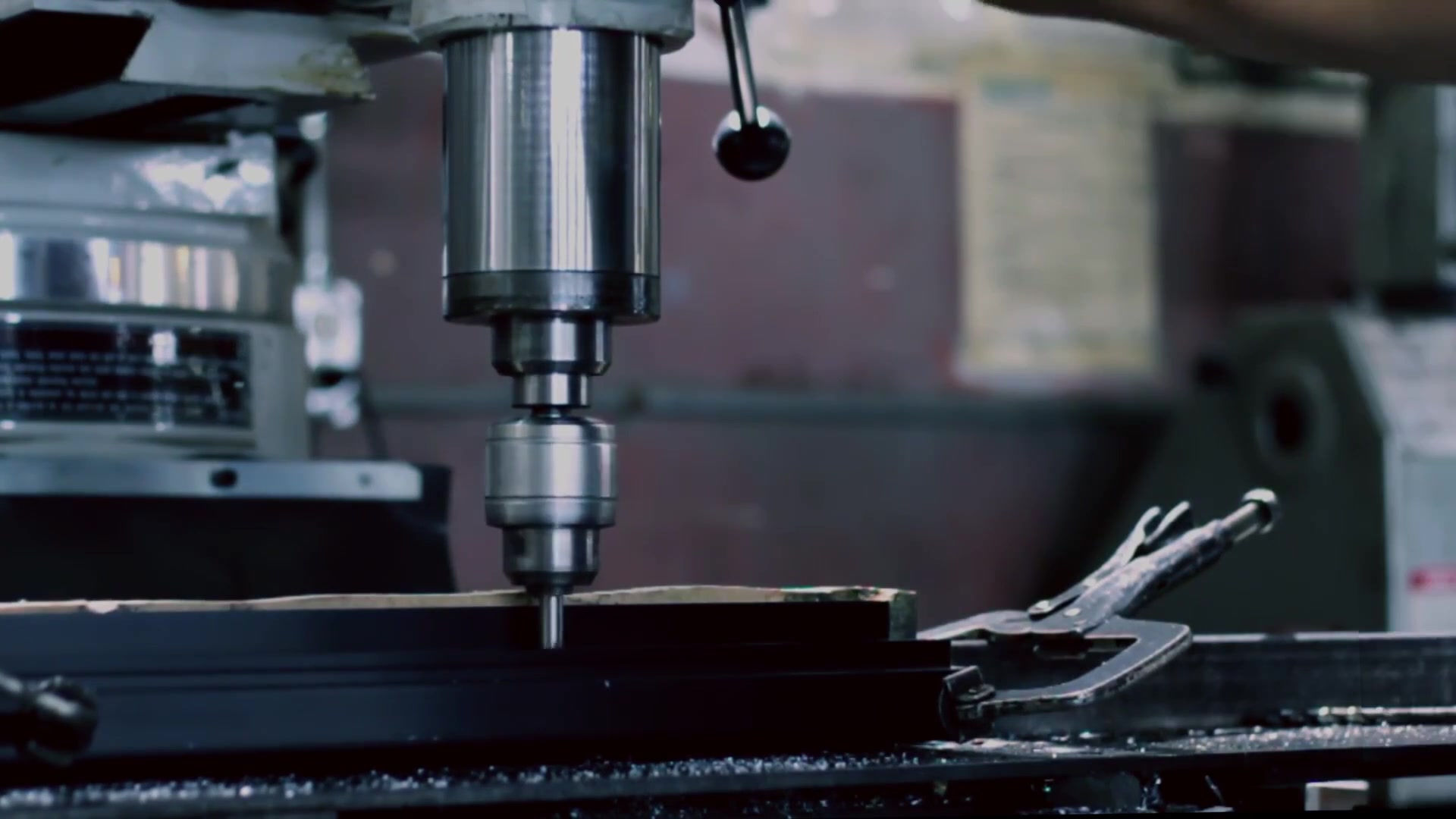
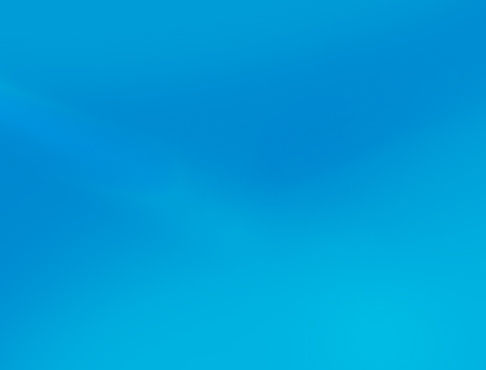
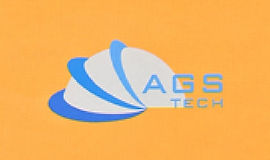
Global Custom Manufacturer, Integrator, Consolidator, Outsourcing Partner for a Wide Variety of Products & Services.
We are your one-stop source for manufacturing, fabrication, engineering, consolidation, integration, outsourcing of custom manufactured and off-shelf products & services. We also private label / white label your products with your brand name if you wish.
Choose your Language
-
Custom Manufacturing of Parts, Components, Assemblies, Finished Products, Machines and Industrial Equipment
-
Domestic & Global Contract Manufacturing
-
Manufacturing Outsourcing
-
Domestic, Global Procurement of Industrial Products
-
Private labeling / White Labeling your Products with your Brand Name
-
Product Finding & Locating Services
-
Global Design and Channel Partnership
-
Engineering Integration
-
Engineering Services
-
Global Consolidation, Warehousing, Logistics
The type of METAL FORGING processes we offer are hot and cold die, open die and closed die, impression die & flashless forgings, cogging, fullering, edging and precision forging, near-net-shape, heading, swaging, upset forging, metal hobbing, press & roll & radial & orbital & ring & isothermal forgings, coining, riveting, metal ball forging, metal piercing, sizing, high energy rate forging.
Our POWDER METALLURGY and POWDER PROCESSING techniques are powder pressing and sintering, impregnation, infiltration, hot and cold isostatic pressing, metal injection molding, roll compaction, powder rolling, powder extrusion, loose sintering, spark sintering, hot pressing.
We recommend that you click here to
DOWNLOAD our Schematic Illustrations of Forging Processes by AGS-TECH Inc.
DOWNLOAD our Schematic Illustrations of Powder Metallurgy Processes by AGS-TECH Inc.
These downloadable files with photos and sketches will help you better understand the information we are providing you below.
In metal forging, compressive forces are applied and the material is deformed and the desired shape is obtained. The most common forged materials in industry are iron and steel, but numerous others such as aluminum, copper, titanium, magnesium are also widely forged. Forged metal parts have improved grain structures in addition to sealed cracks and closed empty spaces, thus the strength of parts obtained by this process is higher. Forging produces parts that are significantly stronger for their weight than parts made by casting or machining. Since forged parts are shaped by making the metal flow into its final shape, the metal takes on a directional grain structure that accounts for the superior strength of the parts. In other words, parts obtained by forging process reveal better mechanical properties as compared to simple cast or machined parts. The weight of metal forgings can range from small lightweight parts to hundreds of thousands of pounds. We manufacture forgings mostly for mechanically demanding applications where high stresses are applied on parts such as automotive parts, gears, work tools, hand tools, turbine shafts, motorcycle gear. Because tooling and set-up costs are relatively high, we recommend this manufacturing process only for high volume production and for low volume but high value critical components such as aerospace landing gear. Besides cost of tooling, the manufacturing lead times for large quantity forged parts can be longer compared to some simple machined parts, but the technique is crucial for parts that require extraordinary strength such as bolts, nuts, special application fasteners, automotive, forklift, crane parts.
• HOT DIE and COLD DIE FORGING : Hot die forging, as the name implies is carried out at high temperatures, the ductility is therefore high and strength of material low. This facilitates easy deformation and forging. To the contrary, cold die forging is carried out at lower temperatures and requires higher forces which results in strain hardening, better surface finish and accuracy of the manufactured parts.
• OPEN DIE and IMPRESSION DIE FORGING : In open die forging, the dies do not constrain the material being compressed, whereas in impression die forging the cavities within the dies restrict material flow while it is forged into desired shape. UPSET FORGING or also called UPSETTING, which is actually not the same but a very similar process, is an open die process where the work piece is sandwiched between two flat dies and a compressive force reduces its height. As the height is reduced, the work piece width increases. HEADING, an upset forging process involves cylindrical stock that is upset at its end and its cross section is increased locally. In heading the stock is fed through the die, forged and then cut to length. The operation is capable to produce high quantities of fasteners rapidly. Mostly it is a cold working operation because it is used to make nail ends, screw ends, nuts and bolts where the material needs to be strengthened. Another open die process is COGGING, where the work piece is forged in a series of steps with each step resulting in compression of the material and the subsequent motion of the open die along the length of the work piece. At each step, the thickness is reduced and length is increased by a small amount. The process resembles a nervous student biting his pencil all along in small steps. A process called FULLERING is another open die forging method we often deploy as an earlier step to distribute the material in the work piece before other metal forging operations take place. We use it when the work piece requires several forging operations. In the operation, die with convex surfaces deform and cause metal flow out to both sides. A similar process to fullering, EDGING on the other hand involves open die with concave surfaces to deform the work piece. Edging also a preparatory process for subsequent forging operations makes the material flow from both sides into an area in the center. IMPRESSION DIE FORGING or CLOSED DIE FORGING as it is also called uses a die / mold that compresses the material and restricts its flow within itself. The die closes and the material takes the shape of the die / mould cavity. PRECISION FORGING, a process requiring special equipment and mold, produces parts with no or very little flash. In other words, the parts will have near final dimensions. In this process a well controlled amount of material is carefully inserted and positioned inside the mold. We deploy this method for complex shapes with thin sections, small tolerances and draft angles and when the quantities are large enough to justify the mold and equipment costs.
• FLASHLESS FORGING : The workpiece is placed in the die in such a way that no material can flow out of the cavity to form flash. No undesired flash trimming is thus needed. It is a precision forging process and thus requires close control of the amount of material used.
• METAL SWAGING or RADIAL FORGING : A work piece is circumferentially acted upon by die and forged. A mandrel may as well be used to forge the interior work piece geometry. In the swaging operation the work piece typically receives several strokes per second. Typical items produced by swaging are pointed tip tools, tapered bars, screwdrivers.
• METAL PIERCING : We use this operation frequently as an additional operation in the manufacturing of parts. A hole or cavity is created with piercing on the work piece surface without breaking through it. Please note that piercing is different than drilling which results in a through hole.
• HOBBING : A punch with the desired geometry is pressed into the work piece and creates a cavity with the desired shape. We call this punch a HOB. The operation involves high pressures and is carried out at cold. As a result the material is cold worked and strain hardened. Therefore this process is very suitable for manufacturing molds, die and cavities for other manufacturing processes. Once the hob is manufactured, one can easily manufacture many identical cavities without the need to machine them one by one.
• ROLL FORGING or ROLL FORMING : Two opposing rolls are used to shape the metal part. The work piece is fed into the rolls, the rolls turn and pull the work into the gap, the work is then fed through the grooved portion of the rolls and the compressive forces give the material its desired shape. It is not a rolling process but a forging process, because it is a discrete rather than a continuous operation. The geometry on the rolls groves forges the material to the required shape and geometry. It is performed hot. Because of being a forging process it produces parts with outstanding mechanical properties and therefore we use it for manufacturing automotive parts such as shafts that need to have extraordinary endurance in tough work environments.
• ORBITAL FORGING : Work piece is put in a forging die cavity and forged by an upper die that travels in an orbital path as it revolves on an inclined axis. At each revolution, the upper die completes exerting compressive forces to the entire work piece. By repeating these revolutions a number of times, sufficient forging is performed. The advantages of this manufacturing technique are its low noise operation and lower forces needed. In other words with small forces one can revolve a heavy die around an axis to apply large pressures on a section of the work piece that is in contact with the die. Disc or conical shaped parts are sometimes a good fit for this process.
• RING FORGING : We frequently use to manufacture seamless rings. Stock is cut to length, upset and then pierced all the way through to create a central hole. Then it is put on a mandrel and a forging die hammers it from above as the ring is slowly rotated until desired dimensions are obtained.
• RIVETING : A common process for joining parts, starts with a straight metal piece inserted in pre made holes through the parts. Thereafter the two ends of the metal piece are forged by squeezing the joint between an upper and lower die.
• COINING : Another popular process carried out by mechanical press, exerting large forces over a short distance. The name “coining” comes from the fine details that are forged on the surfaces of metal coins. It is mostly a finishing process for a product where fine details are obtained on the surfaces as a result of the large force applied by the die that transfers these details to the work piece.
• METAL BALL FORGING : Products such as ball bearings require high quality precisely manufactured metal balls. In one technique called SKEW ROLLING, we use two opposing rolls that continuously rotate as the stock is being continuously fed into the rolls. At the one end of the two rolls metal spheres are ejected as the product. A second method for metal ball forging is using die that squeeze the material stock placed in between them taking the spherical shape of the mould cavity. Oftentimes balls produced require some additional steps such as finishing and polishing in order to become a high quality product.
• ISOTHERMAL FORGING / HOT DIE FORGING : An expensive process performed only when the benefit / cost value is justified. A hot working process where the die are heated to about the same temperature as the work piece. Since both die and work are about the same temperature, there is no cooling and the flow characteristics of the metal are improved. The operation is a good fit for super alloys and materials with inferior forgeability and materials whose
mechanical properties are very sensitive to small temperature gradients and changes.
• METAL SIZING : It is a cold finishing process. Material flow is unrestricted in all directions with the exception of the direction in which the force is applied. As a result, very good surface finish and accurate dimensions are obtained.
• HIGH ENERGY RATE FORGING : The technique involves an upper mold attached to the arm of a piston that is rapidly pushed as a fuel-air mixture is ignited by a spark plug. It resembles the operation of pistons in a car engine. The mold hits the work piece very fast and then returns to its original position very fast thanks to the backpressure. The work is forged within a few milliseconds and therefore there is no time for the work to cool down. This is useful for hard to forge parts that have very temperature sensitive mechanical properties. In other words the process is so fast that the part is formed under constant temperature throughout and the there won’t be temperature gradients at the mold/work piece interfaces.
• In DIE FORGING, metal is beaten between two matching steel blocks with special shapes in them, called dies. When the metal is hammered between the dies, it assumes the same shape as the shapes in the die. When it reaches its final shape, it is taken out to cool. This process produces strong parts that are of a precise shape, but requires a larger investment for the specialized dies. Upset forging increases the diameter of a piece of metal by flattening it. It is generally used to make small parts, especially to form heads on fasteners like bolts and nails.
• POWDER METALLURGY / POWDER PROCESSING : As the name implies, it involves manufacturing processes for making solid parts of certain geometries and shapes from powders. If metal powders are used for this purpose it is the realm of powder metallurgy and if non-metal powders are used it is powder processing. Solid parts are produced from powders by pressing and sintering.
POWDER PRESSING is used to compact powders into desired shapes. First, the primary material is physically powdered, dividing it into many small individual particles. Powder mixture is filled into the die and a punch moves towards the powder and compacts it into the desired shape. Mostly performed at room temperature, with powder pressing a solid part is obtained and it is called green compact. Binders and lubricants are commonly used to enhance compactability. We are capable of powder press forming using hydraulic presses with several thousand tons of capacity. Also we have double action presses with opposing top & bottom punches as well as multiple action presses for highly complex part geometries. Uniformity which is an important challenge for many powder metallurgy / powder processing plants is no big problem for AGS-TECH because of our extensive experience in custom manufacturing such parts for many years. Even with thicker parts where uniformity poses a challenge we have succeeded. If we commit to your project, we will make your parts. If we see any potential risks, we will inform you in
advance.
POWDER SINTERING, which is the second step, involves the raising of temperature to a certain degree and maintenance of the temperature at that level for a certain time so that the powder particles in the pressed part can bond together. This results in much stronger bonds and strengthening of the work piece. Sintering takes place close to the melting temperature of the powder. During sintering shrinkage will occur, material strength, density, ductility, thermal conductivity, electrical conductivity are increased. We do have batch and continuous furnaces for sintering. One of our capabilities is adjusting the level of porosity of the parts we produce. For example we are able to produce metal filters by keeping the parts porous to some degree.
Using a technique called IMPREGNATION, we fill the pores in the metal with a fluid such as oil. We do produce for example oil impregnated bearings that are self-lubricating. In the INFILTRATION process we fill a metal’s pores with another metal of lower melting point than the base material. The mixture is heated to a temperature in between the melting temperatures of the two metals. As a result some special properties can be obtained. We also frequently perform secondary operations such as machining and forging on powder manufactured parts when special features or properties need to be obtained or when the part can be manufactured with less process steps.
ISOSTATIC PRESSING : In this process fluid pressure is being used to compact the part. Metal powders are placed in a mold made of a sealed flexible container. In isostatic pressing, pressure is applied from all around, contrary to axial pressure seen in conventional pressing. The advantages of isostatic pressing are uniform density within the part, especially for larger or thicker parts, superior properties. Its disadvantage is long cycle times and relatively low geometric accuracies. COLD ISOSTATIC PRESSING is carried out at room temperature and the flexible mold is made of rubber, PVC or urethane or similar materials. Fluid used for pressurizing and compacting is oil or water. Conventional sintering of the green compact follows this. HOT ISOSTATIC PRESSING on the other hand is carried out at high temperatures and the mould material is sheet metal or ceramic with high enough melting point that resists the temperatures. Pressurizing fluid is usually an inert gas. The pressing and sintering operations are performed in one step. Porosity is almost completely eliminated, a uniform grain structure is obtained. The advantage of hot isostatic pressing is that it can produce parts comparable to casting and forging combined while making materials that are not suitable for casting and forging possible to be used. Disadvantage of hot isostatic pressing is its high cycle time and therefore cost. It is suitable for critical parts of low volume.
METAL INJECTION MOLDING : Very suitable process for producing complex parts with thin walls and detailed geometries. Most suitable for smaller parts. Powders and polymer binder are mixed, heated and injected into a mold. The polymer binder coats the surfaces of the powder particles. After molding, the binder is removed by either low temperature heating of dissolved using a solvent.
ROLL COMPACTION / POWDER ROLLING : Powders are used to produce continuous strips or sheet. Powder is fed from a feeder and compacted by two rotating rolls into sheet or strips. The operation is carried out cold. The sheet is carried into a sintering furnace. The sintering process may be repeated a second time.
POWDER EXTRUSION : Parts with large length to diameter ratios are manufactured by extruding a thin sheet metal container with powder.
LOOSE SINTERING : As the name implies, it is a pressureless compaction and sintering method, suitable for producing very porous parts such as metal filters. Powder is fed into mold cavity without compacting.
LOOSE SINTERING : As the name implies, it is a pressureless compaction and sintering method, suitable for producing very porous parts such as metal filters. Powder is fed into mold cavity without compacting.
SPARK SINTERING : The powder is compressed in the mold by two opposing punch and a high power electric current is applied to the punch and passes through the compacted powder sandwiched in between them. The high current burns away surface films from the powder particles and sinters them with the heat generated. The process is fast because heat is not applied from outside but instead it is generated from within the mold.
HOT PRESSING : The powders are pressed and sintered in a single step in a mold that can withstand the high temperatures. As the die compacts the powder heat is applied to it. Good accuracies and mechanical properties achieved by this method makes it an attractive option. Even refractory metals can be processed by using mold materials such as graphite.