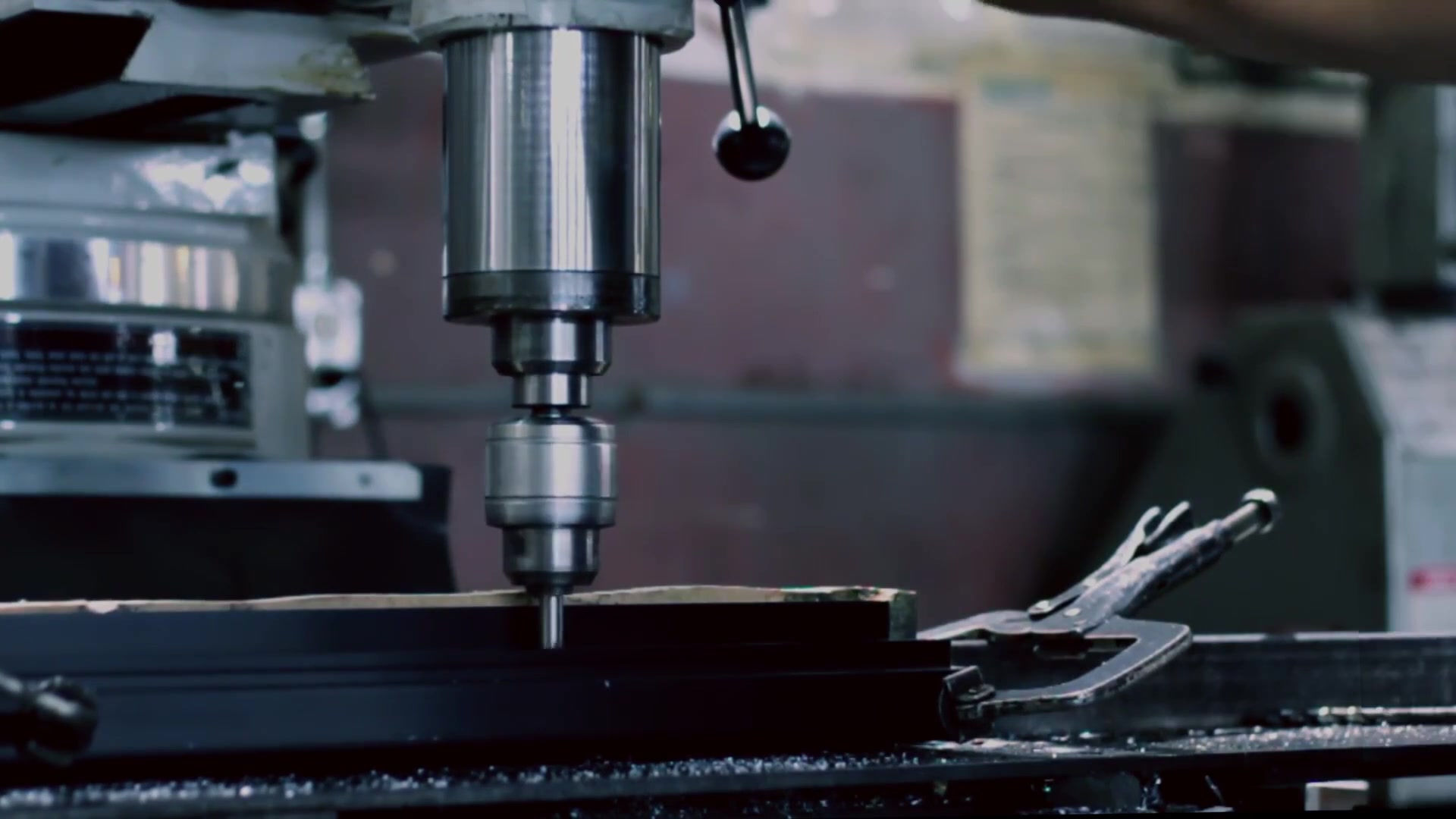
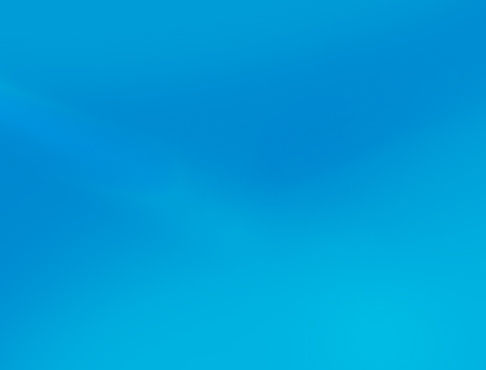
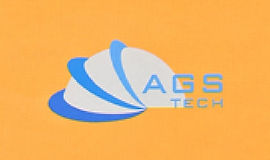
Global Custom Manufacturer, Integrator, Consolidator, Outsourcing Partner for a Wide Variety of Products & Services.
We are your one-stop source for manufacturing, fabrication, engineering, consolidation, integration, outsourcing of custom manufactured and off-shelf products & services. We also private label / white label your products with your brand name if you wish.
Choose your Language
-
Custom Manufacturing of Parts, Components, Assemblies, Finished Products, Machines and Industrial Equipment
-
Domestic & Global Contract Manufacturing
-
Manufacturing Outsourcing
-
Domestic, Global Procurement of Industrial Products
-
Private labeling / White Labeling your Products with your Brand Name
-
Product Finding & Locating Services
-
Global Design and Channel Partnership
-
Engineering Integration
-
Engineering Services
-
Global Consolidation, Warehousing, Logistics
We custom manufacture plastic and rubber moulds and moulded parts using injection moulding, transfer molding, thermoforming, compression moulding, thermoset moulding, vacuum forming, blow moulding, rotational moulding, insert moulding, pour moulding, metal to rubber and metal to plastic bonding, ultrasonic welding, secondary manufacturing & fabrication processes. We recommend that you click here to DOWNLOAD our Schematic Illustrations of Plastic and Rubber Molding Processes by AGS-TECH Inc.
This will help you better understand the information we are providing you below.
• INJECTION MOULDING: A thermoset compound is fed and injected with a high speed reciprocating screw or plunger system. Injection molding can produce small to medium sized parts in high volume economically, tight tolerances, consistency between parts and good strength can be achieved. This technique is the most common plastic products manufacturing method of AGS-TECH Inc. Our standard moulds have cycle times in the order of 500,000 times and are made of P20 tool steel. With larger injection moulds and deeper cavities consistency and hardness throughout the material becomes even more important, therefore we only use certified highest quality tool steel from major suppliers with strong traceability and quality assurance systems. Not all P20 tool steels are the same. Their quality can vary from supplier to supplier and from country to country. Therefore for even our injection moulds manufactured in China we use tool steel imported from US, Germany and Japan. We have accumulated the know-how of using modified P20 steel chemistries for injection moulding of products with surfaces requiring very tight tolerance mirror finishes. This makes us capable of manufacturing even optical lens moulds. Another type of challenging surface finish is textured surfaces. These necessitate consistent hardness across the surface. Therefore any inhomogeneity in the steel can result in less than perfect surface textures. For this reason some of our steel used for such moulds incorporates special alloying elements and is cast using advanced metallurgical techniques. Miniature plastic parts and gears are components that require know how on suitable plastic materials and processes which we have gained over the years. We manufacture tiny precision plastic components with tight tolerances for a company making micromotors. Not every plastic moulding company is capable of producing such tiny accurate parts, because it requires know-how which is acquired only through years of research and development experience. We offer the various types of this molding technique, including gas assisted injection molding.
• INSERT MOULDING : Inserts can either be incorporated at the time of the molding process, or be inserted after the molding process. When incorporated as part of the molding process, the inserts can be loaded by robots or by the operator. If the inserts are incorporated after the molding operation, they can usually be applied any time after the molding process. A common insert moulding process is the process of molding plastic around preformed metal inserts. For example, electronic connectors do have metal pins or components enclosed by the sealing plastic material. We have acquired years of experience keeping the cycle time constant from shot to shot even in post moulding insertion, because variations in cycle time between shots will result in poor quality.
• THERMOSET MOLDING : This technique is characterized by the requirement of heating the mold versus cooling for thermoplastic. Parts manufactured by thermoset molding are ideal for applications requiring high mechanical strength, widely usable temperature range and unique dielectric properties. Thermosetting plastics can be molded in any of the three molding processes: Compression, Injection or Transfer molding. The delivery method of the material into the mold cavities distinguishes these three techniques. For all three processes, a mold constructed of mild or hardened tool steel is heated. The mold is chrome plated to reduce wear on the mold and improve part release. Parts are ejected with hydraulically actuated ejector pins and air poppets. Part removal can either be manual or automatic. Thermoset moulded components for electrical applications require stability against flow and melt at elevated temperatures. As everyone knows, electrical and electronic components warm up during operation and only suitable plastic materials can be used for safety and long term operation. We are experienced in CE and UL qualifications of plastic components for the electronic industry.
• TRANSFER MOLDING : A measured amount of molding material is preheated and inserted into a chamber known as the transfer pot. A mechanism known as the plunger forces the material from the pot through the channels known as sprue and runner system into mold cavities. While material is inserted the mold remains closed and is only opened when it is time to release the produced part. Keeping the mold walls at a higher than melting temperature of the plastic material assures fast flow of material through the cavities. We use this technique for frequently for:
- Encapsulation purposes where complex metallic inserts are molded into the part
- Small to medium sized parts at reasonably high volume
- When parts with tight tolerances are needed and low shrinkage materials are necessary
- Consistency is needed because the transfer molding technique allows consistent material delivery
• THERMOFORMING : This is a generic term used to describe a group of processes to produce plastic parts from flat sheets of plastic under temperature and pressure. In this technique plastic sheets are heated and formed over a male or female mold. After forming they are trimmed to create a usable product. The trimmed material is reground and recycled. Basically there are two types of thermoforming processes, namely vacuum forming and pressure forming (which are explained below). Engineering and tooling costs are low and turnaround times are short. Therefore this method is well suited for prototyping and low volume production. Some thermoform plastic materials are ABS, HIPS, HDPE, HMWPE, PP, PVC, PMMA, modified PETG. The process is suitable for large panels, enclosures and housings and is preferable for such products to injection molding due to lower cost and faster tooling manufacture. Thermoforming is best suited for parts with important features mostly confined to one of its sides. However, AGS-TECH Inc. is capable to use the technique together with additional methods such as trimming, fabrication and assembly to manufacture parts that have critical features on
both sides.
• COMPRESSION MOULDING : Compression molding is a forming process where a plastic material is placed directly into a heated metal mold, where it is softened by the heat and forced to conform to the shape of the mold as the mold closes. Ejector pins in the bottom of the molds quickly eject finished pieces from the mold and the process is finished. Thermoset plastic in either preform or granular pieces is commonly used as the material. Also high-strength fiberglass reinforcements are suitable for this technique. To avoid excess flash, the material is measured prior to molding. The advantages of compression molding are its ability to mold large intricate parts, being one of the lowest cost molding methods compared with other methods such as injection moulding; little material waste. On the other hand, compression molding often provides poor product consistency and relatively difficult control of flash. When compared to injection molding, there are fewer knit lines produced and a smaller amount of fiber length degradation occurs. Compression-molding is also suitable for ultra-large basic shape production in sizes beyond the capacity of extrusion techniques. AGS-TECH uses this technique to manufacture mostly electrical parts, electrical housings, plastic cases, containers, knobs, handles, gears, relatively large flat and moderately curved parts. We possess the know-how of determining the right amount of raw material for cost efficient operation and reduced flash, adjusting to the right amount of energy and time for heating the material, choosing the most suitable heating technique for each project, calculating the required force for optimal shaping of material, optimized mould design for fast cooling after each compression cycle.
• VACUUM FORMING (also described as a simplified version of THERMOFORMING) : A plastic sheet is heated until soft and draped over a mold. Vacuum is then applied and the sheet is being sucked into the mold. After the sheet takes the desired shape of the mould, it is cooled off and ejected from the mold. AGS-TECH uses sophisticated pneumatic, heat and hydrolic control to achieve high speeds in production by vacuum forming. Materials suitable for this technique are extruded thermoplastic sheets such as ABS, PETG, PS, PC, PVC, PP, PMMA, acrylic. The method is most suitable for forming plastic parts that are rather shallow in depth. However we also manufacture relatively deep parts by mechanically or pneumatically stretching the formable sheet prior to bringing it into contact with the mold surface and applying vacuum. Typical products molded by this technique are foot trays & containers, enclosures, sandwich boxes, shower trays, plastic pots, automobile dashboards. Because the technique uses low pressures, inexpensive mold materials can be used and molds can be manufactured in short time inexpensively. Low quantity production of large parts is thus a possibility. Depending on quantity of production mould functionality can be enhanced when high volume production is needed. We are professional in determining what quality of mold each project requires. It would be a waste of customer’s money and resources to manufacture an unnecessarily complex mold for a low volume production run. For example products such as enclosures for large sized medical machines for production quantities in the range of 300 to 3000 units/year can be vacuum formed from heavy gauge raw materials instead of manufactured with expensive techniques such as injection moulding or sheet metal forming.
• BLOW MOULDING : We use this technique for producing hollow plastic parts (also glass parts). A preform or parison which is a tube-like plastic piece is clamped into a mould and compressed air is blown into it through the hole in one end. As a result the plastic perform / parison is pushed outward and acquires the shape of the mould cavity. After the plastic is cooled and solidified, it is ejected from the mould cavity. There are three types of this technique:
-Extrusion blow moulding
-Injection blow moulding
-Injection stretch blow moulding
Common materials used in these processes are PP, PE, PET, PVC. Typical items produced using this technique are plastic bottles, buckets, containers.
• ROTATIONAL MOULDING (also called ROTAMOULDING or ROTOMOULDING) is a technique suitable to produce hollow plastic products. In rotational molding heating, melting, shaping and cooling occur after the polymer is put into the mold. No external pressure is applied. Rotamolding is economical for producing large products, mold costs are low, products are stress free, no polymer weld lines, few design constraints to deal with. The rotomolding process begins with charging the mold, in other words a controlled amount of polymer powder is put in the mould, closed and loaded into oven. Inside the oven the second process step is carried out: Heating and Fusion. The mould is rotated around two axes with relatively low speed, heating takes place and the molten polymer powder melts and sticks to the mould walls. Thereafter the third step, the cooling takes place solidifying the polymer inside the mould. Lastly, the unloading step involves opening of the mould and removal of the product. These four process steps are then repeated again and again. Some materials used in rotomoulding are LDPE, PP, EVA, PVC. Typical products produced are large plastic products such as SPA, childrens playground slides, large toys, large containers, rainwater tanks, traffic cones, canoes and kayaks...etc. Since rotationally moulded products are generally of large geometries and costly to ship, an important point to remember in rotational moulding is to consider designs that facilitate stacking of products into each other prior to shipment. We help our clients during their design phase if required.
• POUR MOLDING : This method is used when multiple items need to be produced. A hollowed out block is used as a mold and filled by simply pouring the liquid material such as melted thermoplastic or a mixture of resin and hardener into it. By doing this one either produces the parts or another mold. The liquid such as plastic is then left to harden and takes on the shape of the mold cavity. Release agent materials are commonly used to release parts from the mold. Pour molding is also sometimes referred to as Plastic Potting or Urethane Casting. We use this process for inexpensively manufacturing products in the shape of statues, ornaments….etc., products that do not need excellent uniformity or excellent material properties but rather only the shape of an object. We sometimes make silicon molds for prototyping purposes. Some of our low volume projects are processed using this technique. Pour moulding can be used for manufacturing glass, metal and ceramic parts as well. Since the set-up and tooling costs are minimal, we consider this technique whenever low quantity production of multiple
items with minimal tolerance requirements is on the table. For high volume production, the pour molding technique is generally not suitable because it is slow and therefore expensive when large quantities need to be manufactured. There are however exceptions where pour moulding can be used for large quantity production, such as pour molding potting compounds to encapsulate electronic and electrical components and assemblies for insulation and protection.
• RUBBER MOLDING – CASTING – FABRICATION SERVICES : We custom manufacture rubber components from natural as well as synthetic rubber using some of the above explained processes. We can adjust the hardness and other mechanical properties according to your application. By incorporating other organic or inorganic additives, we can increase the heat stability of your rubber parts such as balls for high temperature cleaning purposes. Various other properties of rubber can be modified as needed and desired. Also be assured that we do not use toxic or hazardous materials for manufacturing toys or other elastomer / elastomeric molded products. We provide
Material Safety Data Sheets (MSDS), conformance reports, material certifications and other documents such as ROHS compliance for our materials and products. Additional special tests are carried out at certified government or government approved laboratories if needed. We have been manufacturing automobile mats from rubber, small rubber statues and toys for many years.
• SECONDARY MANUFACTURING & FABRICATION PROCESSES : Finally, keep in mind that we also offer a large variety of secondary processes such as chrome coating of plastic products for mirror-type applications or giving plastics the metal-like shiny finish. Ultrasonic welding is another example of a secondary process offered for plastic components. Yet a third example of secondary process on plastics can be surface treatment prior to coating to enhance coating adhesion. Automobile bumpers are well known to benefit from this secondary process. Metal-rubber bonding, metal-plastic bonding are other common processes we are experienced with. When we evaluate your project, we can jointly determine which secondary processes would be the most suitable for your product.
Here are some of commonly used plastic products. Since these are off-the-shelf, you can save on mould costs in case any of these fits your requirements.
Click here to download our economic 17 Series Hand Held Plastic Enclosures from AGS-Electronics
Click here to download our 10 Series Sealed Plastic Enclosures from AGS-Electronics
Click here to download our 08 Series Plastic Cases from AGS-Electronics
Click here to download our 18 Series Special Plastic Enclosures from AGS-Electronics
Click here to download our 24 Series DIN Plastic Enclosures from AGS-Electronics
Click here to download our 37 Series Plastic Equipment Cases from AGS-Electronics
Click here to download our 15 Series Modular Plastic Enclosures from AGS-Electronics
Click here to download our 14 Series PLC Enclosures from AGS-Electronics
Click here to download our 31 Series Potting and Power Supply Enclosures from AGS-Electronics
Click here to download our 20 Series Wall-Mounting Enclosures from AGS-Electronics
Click here to download our 03 Series Plastic and Steel Enclosures from AGS-Electronics
Click here to download our 16 Series DIN rail module enclosures from AGS-Electronics
Click here to download our 19 Series Desktop Enclosures from AGS-Electronics
Click here to download our 21 Series Card Reader Enclosures from AGS-Electronics