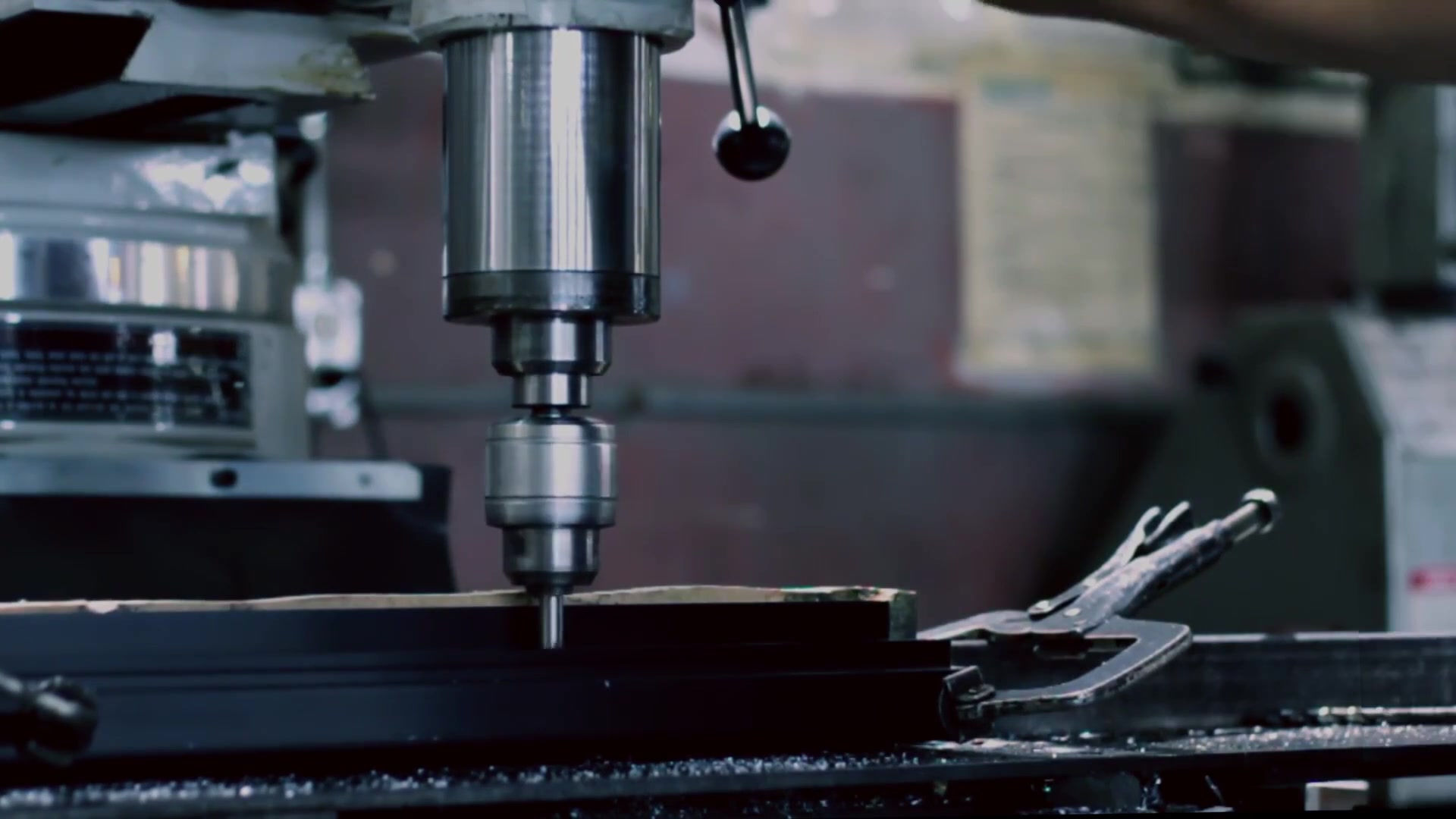
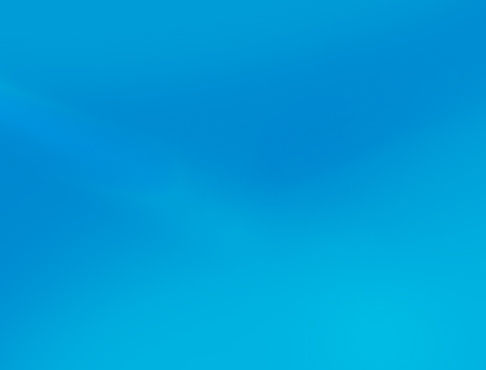
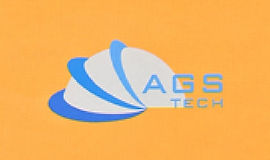
Global Custom Manufacturer, Integrator, Consolidator, Outsourcing Partner for a Wide Variety of Products & Services.
We are your one-stop source for manufacturing, fabrication, engineering, consolidation, integration, outsourcing of custom manufactured and off-shelf products & services. We also private label / white label your products with your brand name if you wish.
Choose your Language
-
Custom Manufacturing of Parts, Components, Assemblies, Finished Products, Machines and Industrial Equipment
-
Domestic & Global Contract Manufacturing
-
Manufacturing Outsourcing
-
Domestic, Global Procurement of Industrial Products
-
Private labeling / White Labeling your Products with your Brand Name
-
Product Finding & Locating Services
-
Global Design and Channel Partnership
-
Engineering Integration
-
Engineering Services
-
Global Consolidation, Warehousing, Logistics
Surfaces cover everything. The appeal and functions material surfaces provide us are of utmost importance. Therefore SURFACE TREATMENT and SURFACE MODIFICATION are among our everyday industrial operations. Surface treatment & modification leads to enhanced surface properties and can be performed either as a final finishing operation or prior to a coating or joining operation. The processes of surface treatments and modification (also referred to as SURFACE ENGINEERING), tailor the surfaces of materials and products to:
- Control friction and wear
- Improve corrosion resistance
- Enhance adhesion of subsequent coatings or joined parts
- Change physical properties conductivity, resistivity, surface energy and reflection
- Change chemical properties of surfaces by introducing functional groups
- Change dimensions
- Change the appearance, e.g., color, roughness…etc.
- Clean and / or disinfect the surfaces
Using surface treatment and modification, the functions and service lives of materials can be improved. Our common surface treatment and modification methods can be divided into two major categories:
Surface Treatment and Modification That Covers Surfaces:
Organic Coatings: The organic coatings apply paints, cements, laminates, fused powders and lubricants on the surfaces of materials.
Inorganic Coatings: Our popular inorganic coatings are electroplating, autocatalytic plating (electroless platings), conversion coatings, thermal sprays, hot dipping, hardfacing, furnace fusing, thin film coatings such as SiO2, SiN on metal, glass, ceramics,….etc. Surface treatment and modification involving coatings is explained in detail under the related submenu, please click here Functional Coatings / Decorative Coatings / Thin Film / Thick Film
Surface Treatment and Modification That Alters Surfaces: Here on this page we will concentrate on these. Not all of the surface treatment and modification techniques we describe below are on the micro or nano-scale, but we will nevertheless mention about them briefly since the basic objectives and methods are similar to significant extent to those that are on the micromanufacturing scale.
Hardening: Selective surface hardening by laser, flame, induction and electron beam.
High Energy Treatments: Some of our high energy treatments include ion implantation, laser glazing & fusion, and electron beam treatment.
Thin Diffusion Treatments: Thin diffusion processes include ferritic-nitrocarburizing, boronizing, other high temperature reaction processes such as TiC, VC.
Heavy Diffusion Treatments: Our heavy diffusion processes include carburizing, nitriding, and carbonitriding.
Special Surface Treatments: Special treatments such as cryogenic, magnetic, and sonic treatments affect both the surfaces and the bulk materials.
The selective hardening processes can be carried out by flame, induction, electron beam, laser beam. Large substrates are deep hardened using flame hardening. Induction hardening on the other hand is used for small parts. Laser and electron beam hardening are sometimes not distinguished from those in hardfacings or high-energy treatments. These surface treatment and modification processes are applicable only to steels that have sufficient carbon and alloy content to allow quench hardening. Cast irons, carbon steels, tool steels, and alloy steels are suitable for this surface treatment and modification method. Dimensions of parts are not significantly altered by these hardening surface treatments. Depth of hardening can vary from 250 microns to the whole section depth. However, in the whole section case, the section must be thin, less than 25 mm (1 in), or small, since the hardening processes require a rapid cooling of materials, sometimes within a second. This is difficult to achieve in large workpieces, and therefore in large sections, only the surfaces can be hardened. As a popular surface treatment and modification process we harden springs, knife blades, and surgical blades among many other products.
High-energy processes are relatively new surface treatment and modification methods. Properties of surfaces are changed without changing the dimensions. Our popular high-energy surface treatment processes are electron beam treatment, ion implantation, and laser beam treatment.
Electron Beam Treatment: Electron beam surface treatment alters the surface properties by rapid heating and rapid cooling — in the order of 10Exp6 Centigrade/sec (10exp6 Fahrenheit/sec) in a very shallow region around 100 microns near the material surface. Electron beam treatment can also be used in hardfacing to produce surface alloys.
Ion Implantation: This surface treatment and modification method uses electron beam or plasma to convert gas atoms to ions with sufficient energy, and implant/insert the ions into atomic lattice of the substrate, accelerated by magnetic coils in a vacuum chamber. Vacuum makes it easier for ions to move freely in the chamber. The mismatch between implanted ions and the surface of the metal creates atomic defects that hardens the surface.
Laser Beam Treatment: Like the electron beam surface treatment and modification, laser beam treatment alters the surface properties by rapid heating and rapid cooling in a very shallow region near the surface. This surface treatment & modification method can also be used in hardfacing to produce surface alloys.
A know-how in Implant dosages and treatment parameters makes it possible for us to use these high energy surface treatment techniques in our fabrication plants.
Thin Diffusion Surface Treatments:
Ferritic nitrocarburizing is a case hardening process that diffuses nitrogen and carbon into ferrous metals at sub-critical temperatures. The processing temperature is usually at 565 Centigrade (1049 Fahrenheit). At this temperature steels and other ferrous alloys are still in a ferritic phase, which is advantageous compared to other case hardening processes that occur in the austenitic phase. The process is used to improve:
•scuffing resistance
•fatigue properties
•corrosion resistance
Very little shape distortion occurs during the hardening process thanks to the low processing temperatures.
Boronizing, is the process where boron is introduced to a metal or alloy. It is a surface hardening and modification process by which boron atoms are diffused into the surface of a metal component. As a result the surface contains metal borides, such as iron borides and nickel borides. In their pure state these borides have extremely high hardness and wear resistance. Boronized metal parts are extremely wear resistant and will often last up to five times longer than components treated with conventional heat treatments such as hardening, carburizing, nitriding, nitrocarburizing or induction hardening.
Heavy Diffusion Surface Treatment and Modification: If the carbon content is low (less than 0.25% for example) then we can increase the carbon content of the surface for hardening. The part can be either heat-treated by quenching in a liquid or cooled in still air depending on the properties desired. This method will only allow local hardening on the surface, but not in the core. This is sometimes very desirable because it allows for a hard surface with good wear properties as in gears, but has a tough inner core that will perform well under impact loading.
In one of the surface treatment and modification techniques, namely Carburizing we add carbon to the surface. We expose the part to a Carbon rich atmosphere at an elevated temperature and allow diffusion to transfer the Carbon atoms into the steel. Diffusion will happen only if the steel has low carbon content, because diffusion works on the differential of the concentrations principle.
Pack Carburizing: Parts are packed in a high carbon medium such as carbon powder and heated in a furnace for 12 to 72 hours at 900 Centigrade (1652 Fahrenheit). At these temperatures CO gas is produced which is a strong reducing agent. The reduction reaction occurs on the surface of the steel releasing carbon. The carbon is then diffused into the surface thanks to the high temperature. The Carbon on the surface is 0.7% to 1.2% depending on process conditions. The hardness achieved is 60 - 65 RC. The depth of the carburized case ranges from about 0.1 mm up to 1.5 mm. Pack carburizing requires good control of temperature uniformity and consistency in heating.
Gas Carburizing: In this variant of surface treatment, Carbon Monoxide (CO) gas is supplied to a heated furnace and the reduction reaction of deposition of carbon takes place on the surface of the parts. This process overcomes most of the problems of pack carburizing. One concern however is the safe containment of the CO gas.
Liquid Carburizing: The steel parts are immersed in a molten carbon rich bath.
Nitriding is a surface treatment and modification process involving diffusion of Nitrogen into the surface of steel. Nitrogen forms Nitrides with elements such as Aluminum, Chromium, and Molybdenum. The parts are heat-treated and tempered before nitriding. The parts are then cleaned and heated in a furnace in an atmosphere of dissociated Ammonia (containing N and H) for 10 to 40 hours at 500-625 Centigrade (932 - 1157 Fahrenheit). Nitrogen diffuses into the steel and forms nitride alloys. This penetrates to a depth of up to 0.65 mm. The case is very hard and distortion is low. Since the case is thin, surface grinding is not recommended and therefore nitriding surface treatment may not be an option for surfaces with very smooth finishing requirements.
Carbonitriding surface treatment and modification process is most suitable for low carbon alloy steels. In the carbonitriding process, both Carbon and Nitrogen are diffused into the surface. The parts are heated in an atmosphere of a hydrocarbon (such as methane or propane) mixed with Ammonia (NH3). Simply put, the process is a mix of Carburizing and Nitriding. Carbonitriding surface treatment is performed at temperatures of 760 - 870 Centigrade (1400 - 1598 Fahrenheit), It is then quenched in a natural gas (Oxygen free) atmosphere. The carbonitriding process is not suitable for high precision parts due to the distortions that are inherent. The hardness achieved is similar to carburizing (60 - 65 RC) but not as high as Nitriding (70 RC). The case depth is between 0.1 and 0.75 mm. The case is rich in Nitrides as well as Martensite. Subsequent tempering is needed to reduce brittleness.
Special surface treatment and modification processes are in the early stages of development and their effectiveness is as yet unproven. They are:
Cryogenic Treatment: Generally applied on hardened steels, slowly cool down the substrate to about -166 Centigrade (-300 Fahrenheit) to increase the density of the material and thus increase the wear resistance and dimension stability.
Vibration Treatment: These intend to relieve thermal stress built-up in heat treatments through vibrations and increase the wear life.
Magnetic Treatment: These intend to alter the line-up of atoms in materials through magnetic fields and hopefully improve the wear life.
The effectiveness of these special surface treatment and modification techniques still remains to be proven. Also these three techniques above affect the bulk material besides surfaces.
Please download our catalogs and brochures by clicking on the blue colored text below:
- Private Label Nano Surface Protection Car Care Products We can label these products with your name and logo if you wish
- Private Label Nano Surface Protection Industrial Products We can label these products with your name and logo if you wish
- Private Label Nano Surface Protection Marine Products We can label these products with your name and logo if you wish
- Private Label Nano Surface Protection Products We can label these products with your name and logo if you wish