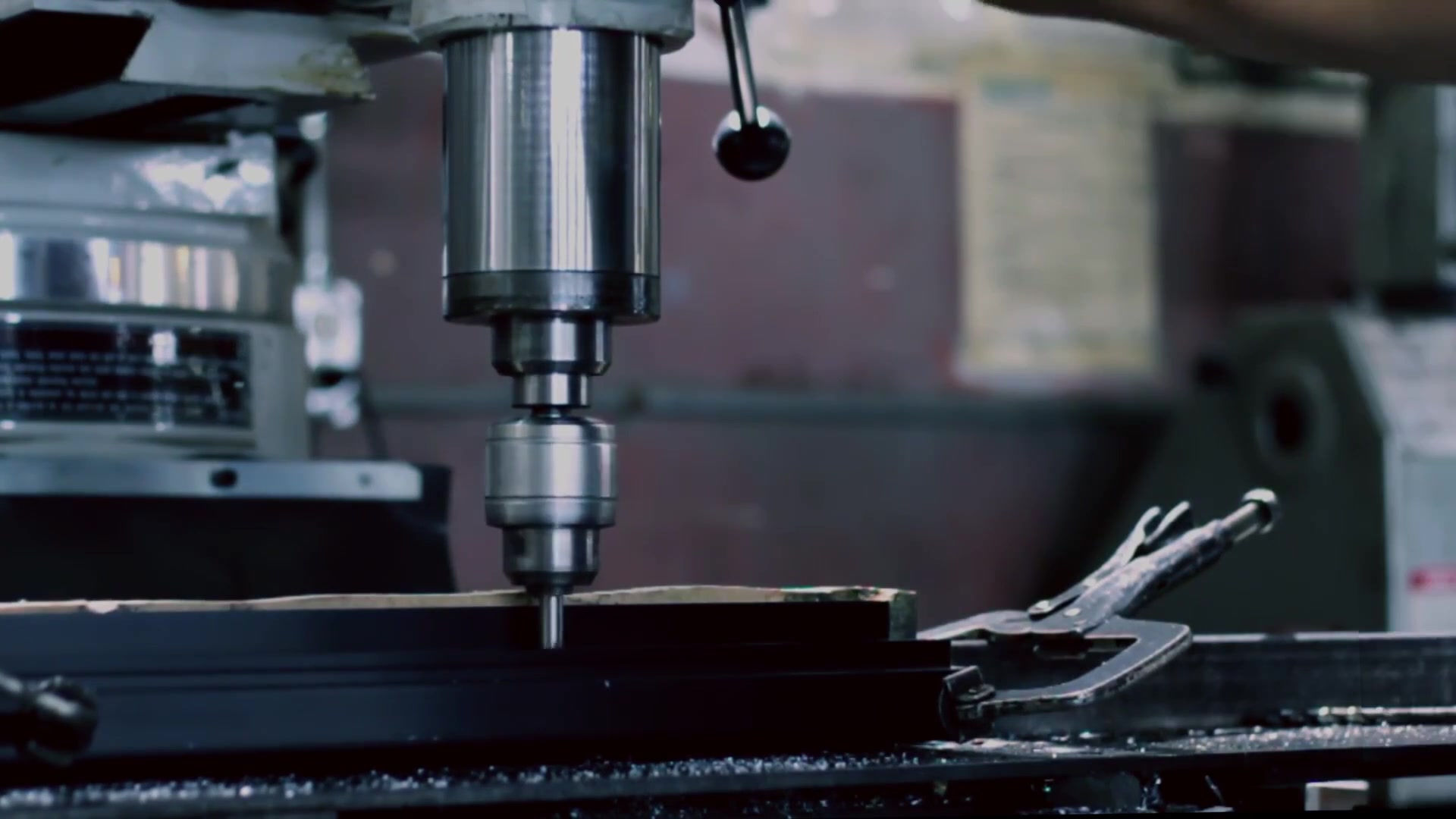
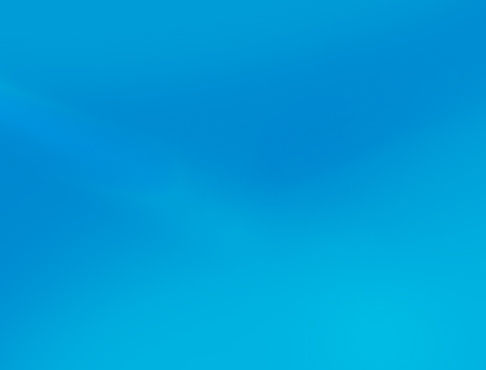
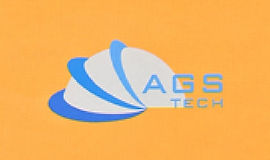
Global Custom Manufacturer, Integrator, Consolidator, Outsourcing Partner for a Wide Variety of Products & Services.
We are your one-stop source for manufacturing, fabrication, engineering, consolidation, integration, outsourcing of custom manufactured and off-shelf products & services. We also private label / white label your products with your brand name if you wish.
Choose your Language
-
Custom Manufacturing of Parts, Components, Assemblies, Finished Products, Machines and Industrial Equipment
-
Domestic & Global Contract Manufacturing
-
Manufacturing Outsourcing
-
Domestic, Global Procurement of Industrial Products
-
Private labeling / White Labeling your Products with your Brand Name
-
Product Finding & Locating Services
-
Global Design and Channel Partnership
-
Engineering Integration
-
Engineering Services
-
Global Consolidation, Warehousing, Logistics
We also supply other pneumatic, hydraulic and vacuum system components not mentioned elsewhere here under any menu page. These are:
BOOSTER REGULATORS: They save money and energy by increasing the main line pressure by multiple times while also protecting downstream systems from pressure fluctuations. The pneumatic booster regulator, when connected to an air supply line, multiplies pressure and the main air supply pressure may be set low. Desired pressure increases and output pressures can be easily adjusted. Pneumatic booster regulators boost local line pressures without requiring additional power by 2 to 4 times. The use of pressure boosters is particularly recommended when the pressure in a system needs to be selectively increased. A system or sections of it do not have to be supplied with excessively high pressure, because this would lead to substantially higher operating costs. Pressure boosters can also be used for mobile pneumatics. An initial low pressure can be generated using relatively small compressors, and then reinforced with the help of the booster. Keep in mind however that pressure boosters are not a replacement for compressors. Some of our pressure boosters require no other source than compressed air. Pressure boosters are classified as twin-piston pressure boosters and are intended for compressing air. The basic variant of the booster consists of a double piston system and a directional control valve for continuous operation. These boosters double the input pressure automatically. It is not possible to adjust the pressure to lower values. Pressure boosters which also have a pressure regulator can boost pressures to less than double the set value. In this case the pressure regulator reduces the pressure in the outside chambers. Pressure boosters cannot vent themselves, the air can only flow in one direction. Therefore pressure boosters cannot necessarily be used in a working line between valves and cylinders.
SENSORS and GAUGES (pressure, vacuum….etc): Your pressure, vacuum range, fluid flow range temperature range….etc. will determine which instrument to select. We have a wide range of standard off-shelf sensors and gauges for pneumatics, hydraulics and vacuum. Capacitance Manometers, Pressure Sensors, Pressure Switches, Pressure Control Subsystems, Vacuum & Pressure Gauges, Vacuum & Pressure Transducers, Indirect Vacuum Gauge Transducers & Modules and Vacuum & Pressure Gauge Controllers are some of the popular products. To select the right pressure sensor for a specific application, besides the pressure range, the type of pressure measurement has to be considered. Pressure sensors measure a certain pressure in comparison to a reference pressure and can be categorized into 1.) Absolute 2.) gage and 3.) differential devices. Absolute piezoresistive pressure sensors measure the pressure relative to a high vacuum reference sealed behind its sensing diaphragm (in practice referred to as Absolute Pressure). The vacuum is negligible compared to the pressure to be measured. Gage Pressure is measured relative to the ambient atmospheric pressure. Changes in the atmospheric pressure due to weather conditions or altitude influence the output of a gage pressure sensor. A gage pressure higher than ambient pressure is referred to as positive pressure. If the gage pressure is below the atmospheric pressure, it is called negative or vacuum gage pressure. According to its quality, vacuum can be categorized into different ranges such as low, high and ultra high vacuum. Gage pressure sensors only offer one pressure port. The ambient air pressure is directed through a vent hole or a vent tube to the back side of the sensing element and thus compensated. Differential pressure is the difference between any two process pressures p1 and p2. Because of this, differential pressure sensors must offer two separate pressure ports with connections. Our amplified pressure sensors are able to measure positive and negative pressure differences, corresponding to p1>p2 and p1<p2. These sensors are called bidirectional differential pressure sensors. In contrast, unidirectional differential pressure sensors only operate in the positive range (p1>p2) and the higher pressure has to be applied to the pressure port defined as ''high pressure port''. Another class of gauges available are Flow Meters. Systems requiring continuous monitoring of flow use in general electronic flow sensors rather than flow meters, which require no power. Electronic flow sensors can use a variety of sensing elements to generate an electronic signal proportional to the flow. The signal is then sent to an electronic display panel or control circuit. However, flow sensors produce no visual indication of flow by themselves, and they need some source of external power to transmit a signal to an analog or digital display. Self-contained flow meters, on the other hand, rely on the dynamics of flow to provide a visual indication of it. Flow meters operate on the principle of dynamic pressure. Because measured flow depends on fluid dynamics, changes in a fluid's physical properties can affect flow readings. This is due to the fact that a flow meter is calibrated to a fluid having a certain specific gravity within a range of viscosities. Wide variations in temperatures can change a hydraulic fluid's specific gravity and viscosity. Therefore when a flow meter is used when the fluid is very hot or very cold, flow readings may not conform to manufacturers' specifications. Other products include Temperature Sensors and Gauges.
PNEUMATIC CYLINDER CONTROLS: Our speed controls have built in one-touch fittings minimizing installation time, reducing mounting height and enabling compact machine design. Our speed controls allow the body to be rotated to facilitate simple installation. Available in thread sizes in both inch and metric, with varying tube sizes, with optional elbow and universal style for increased flexibility, our speed controls are designed to meet most applications. There are several methods to control the extending and retracting speed of pneumatic cylinders. We offer Flow Controls, Speed Control mufflers, Quick Exhaust Valves for speed control. Double-acting cylinders can have both the out and in stroke controlled, and you can have several different control methods on each port.
CYLINDER POSITION SENSORS: These sensors are used for the detection of magnet-equipped pistons on pneumatic and other types of cylinders. The magnetic field of a magnet embedded in the piston is detected by the sensor through the cylinder housing wall. These non-contact sensors determine the position of the cylinder piston without diminishing the integrity of the cylinder itself. These position sensors operate without intruding upon the cylinder, keeping the system completely intact.
SILENCERS / EXHAUST CLEANERS: Our silencers are extremely effective in reducing air exhaust noise originating from pumps and other pneumatic devices. Our silencers reduce noise levels by up to 30dB while allowing high flow rates with minimal back pressure. We have filters that enable direct exhaust of air in a clean room. Air can be directly exhausted in a clean room only by mounting these exhaust cleaners to the pneumatic equipment in the clean room. There is no need for piping for exhaust and relief air. Product reduces piping installation work and space.
FEEDTHROUGHS: These are generally electrical conductors or optical fibers used to carry a signal through an enclosure, chamber, vessel or interface. Feedthroughs can be divided into power and instrumentation categories. Power feedthroughs carry either high currents or high voltages. Instrumentation feedthroughs on the other hand are used to carry electrical signals, such as thermocouples, which are generally low current or voltage. Lastly, RF-feedthroughs are designed to carry very high frequency RF or microwave electrical signals. A feedthrough electrical connection may have to withstand considerable pressure difference across its length. Systems that operate under high vacuum, like vacuum chambers require electrical connections through the vessel. Submersible vehicles also require feedthrough connections between exterior instruments and devices and the controls within the vehicle pressure hull. Hermetically sealed feedthroughs are frequently used for instrumentation, high amperage and voltage, coaxial, thermocouple and fiber optic applications. Fiber optic feedthroughs transmit fiber optical signals through the interfaces. Mechanical feedthroughs transmit mechanical motion from one side of the interface (for example from the outside of the pressure chamber) to the other side (to the inside of the pressure chamber). Our feedthroughs incorporate ceramic, glass, metal / metal alloy parts, metal coatings on fibers for solderability and specialty silicones and epoxies, all chosen carefully according to the application. All our feedthrough assemblies have passed rigorous tests including environmental cycling test and related industrial standards.
VACUUM REGULATORS: These devices assure that the vacuum process remains stable even through wide variations in flow rate and supply pressures. Vacuum regulators directly control vacuum pressures by modulating the flow from the system to the vacuum pump. Using our precision vacuum regulators is relatively simple. You simply connect your vacuum pump or vacuum utililty to the Outlet port. You connect the process you want to control to the Inlet port. By adjusting the vacuum knob you achieve the desired vacuum level.
Please click on highlighted text below to download our product brochures for pneumatic & hydraulic & vacuum system components:
- Private Label Gauges, Filters, Regulators, Temperature Instruments (We private label these with your brand name and logo if you wish)
- Private Label Pneumatic Compressed Air Hoses Fittings (We private label these with your brand name and logo if you wish)
- Private Label Pneumatic Couplings, Plugs and Nipples (We private label these with your brand name and logo if you wish)
- Process Automation Solutions (We private label these with your brand name and logo if you wish)
- YC Series Hydraulic Cyclinder - Accumulators from AGS-TECH Inc
- Information on our facility producing ceramic to metal fittings, hermetic sealing, vacuum feedthroughs, high and ultrahigh vacuum and fluid control components can be found here: Fluid Control Factory Brochure