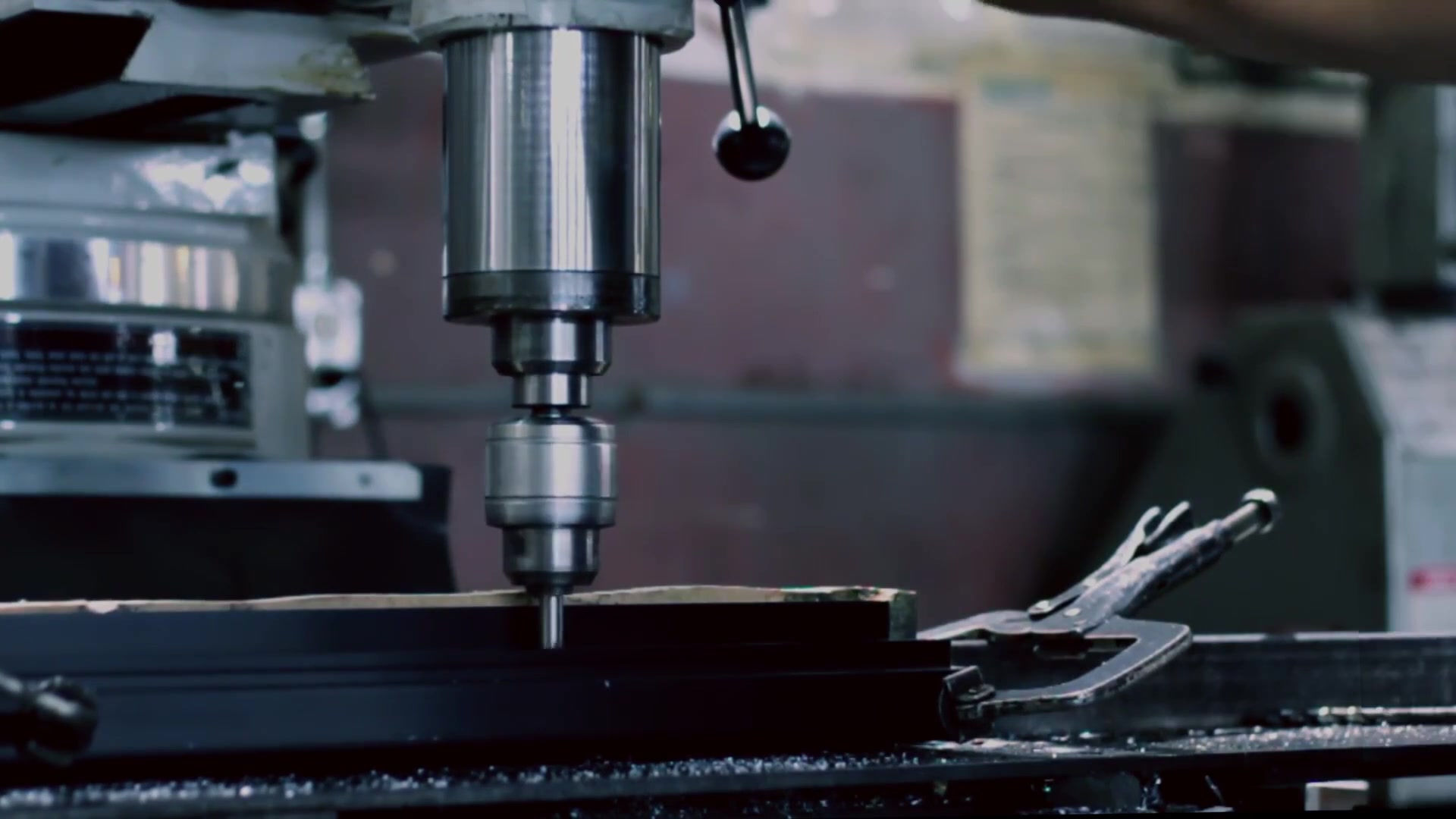
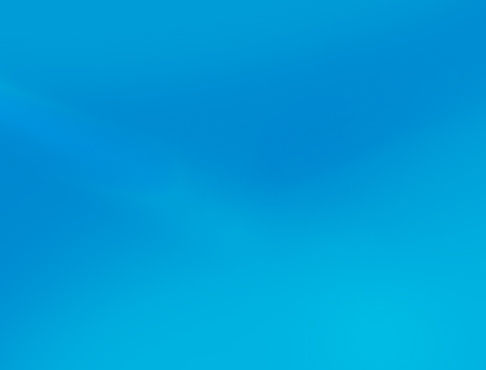
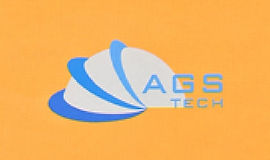
Globální zakázkový výrobce, integrátor, konsolidátor, partner pro outsourcing pro širokou škálu produktů a služeb.
Jsme vaším komplexním zdrojem pro výrobu, výrobu, inženýrství, konsolidaci, integraci, outsourcing zakázkově vyráběných i volně prodejných produktů a služeb.
Choose your Language
-
Zakázková výroba
-
Domácí a globální smluvní výroba
-
Outsourcing výroby
-
Domácí a globální zadávání zakázek
-
Konsolidace
-
Engineering Integration
-
Inženýrské služby
We use the PLASMA CUTTING and PLASMA MACHINING processes to cut and machine steel, aluminum, metals and other materials of různé tloušťky pomocí plazmového hořáku. Při řezání plazmou (někdy také nazývané PLASMA-ARC CUTTING) je inertní plyn nebo stlačený vzduch vyfukován vysokou rychlostí z trysky a současně se tímto plynem vytváří elektrický oblouk z trysky do povrch je řezán, čímž se část tohoto plynu změní na plazmu. Pro zjednodušení lze plazmu popsat jako čtvrté skupenství hmoty. Tři skupenství hmoty jsou pevná, kapalná a plynná. Pro běžný příklad, voda, tyto tři skupenství jsou led, voda a pára. Rozdíl mezi těmito stavy se týká jejich energetické hladiny. Když k ledu přidáme energii ve formě tepla, roztaje a vytvoří vodu. Když přidáme více energie, voda se vypaří ve formě páry. Přidáním více energie do páry se tyto plyny ionizují. Tento proces ionizace způsobuje, že se plyn stává elektricky vodivým. Tento elektricky vodivý ionizovaný plyn nazýváme „plazma“. Plazma je velmi horké a taví řezaný kov a zároveň odfukuje roztavený kov pryč z řezu. Plazmu používáme pro řezání tenkých i silných, železných i neželezných materiálů. Naše ruční hořáky obvykle dokážou řezat ocelový plech o tloušťce až 2 palce a naše silnější počítačem řízené hořáky mohou řezat ocel o tloušťce až 6 palců. Plazmové řezačky vytvářejí velmi horký a lokalizovaný kužel pro řezání, a jsou proto velmi vhodné pro řezání plechů v zakřivených a úhlových tvarech. Teploty vznikající při řezání plazmovým obloukem jsou velmi vysoké a kolem 9673 Kelvinů v kyslíkovém plazmovém hořáku. To nám nabízí rychlý proces, malou šířku řezu a dobrou povrchovou úpravu. V našich systémech využívajících wolframové elektrody je plazma inertní, vytvořená pomocí argonu, argonu-H2 nebo dusíku. Někdy však používáme také oxidační plyny, jako je vzduch nebo kyslík, a v těchto systémech je elektroda měděná s hafniem. Výhodou vzduchového plazmového hořáku je, že používá vzduch místo drahých plynů, čímž potenciálně snižuje celkové náklady na obrábění.
Naše HF-TYPE PLAZMOVÉ ŘEZÁNÍ stroje používají vysokofrekvenční, vysokonapěťovou vzduchovou jiskru a iniciují ionizační hlavu. Naše vysokofrekvenční plazmové řezačky nevyžadují, aby byl hořák na začátku v kontaktu s materiálem obrobku, a jsou vhodné pro aplikace zahrnující COMPUTER NUMERICAL CONTROL (CNC)_cc781905-5cde-3bdbad5cf355 Jiní výrobci používají primitivní stroje, které ke spuštění vyžadují kontakt hrotu se základním kovem a poté dojde k oddělení mezery. Tyto primitivnější plazmové řezačky jsou náchylnější k poškození kontaktního hrotu a štítu při startu.
Naše PILOT-ARC TYPE PLASMA machines používají k výrobě plazmy dvoustupňový proces, bez nutnosti počátečního kontaktu. V prvním kroku je použit vysokonapěťový nízkoproudý obvod k inicializaci velmi malé jiskry o vysoké intenzitě v těle hořáku, která vytváří malou kapsu plazmového plynu. Toto se nazývá pilotní oblouk. Pilotní oblouk má zpětnou elektrickou dráhu zabudovanou v hlavě hořáku. Pilotní oblouk je udržován a zachován, dokud není přiveden do blízkosti obrobku. Tam pilotní oblouk zapálí hlavní plazmový řezací oblouk. Plazmové oblouky jsou extrémně horké a jejich teplota se pohybuje v rozmezí 25 000 °C = 45 000 °F.
Tradičnější metoda, kterou také používáme, je OXYFUEL-GAS CUTTING (OFC) kde používáme hořák jako při svařování. Operace se používá při řezání oceli, litiny a ocelolitiny. Princip řezání při řezání kyslíkem a plynem je založen na oxidaci, hoření a tavení oceli. Šířka řezu při řezání kyslíkem a plynem se pohybuje v rozmezí 1,5 až 10 mm. Plazmový obloukový proces byl považován za alternativu k kyslíko-palivovému procesu. Plazmový obloukový proces se liší od kyslíko-palivového procesu v tom, že pracuje s použitím oblouku k roztavení kovu, zatímco při kyslíko-palivovém procesu kyslík oxiduje kov a teplo z exotermické reakce kov taví. Proto, na rozdíl od kyslíko-palivového procesu, lze plazmový proces použít pro řezání kovů, které tvoří žáruvzdorné oxidy, jako je nerezová ocel, hliník a neželezné slitiny.
PLASMA GOUGING proces podobný plazmovému řezání se obvykle provádí na stejném zařízení jako plazmové řezání. Místo řezání materiálu používá plazmové dlabání jinou konfiguraci hořáku. Tryska hořáku a difuzér plynu jsou obvykle odlišné a pro odfukování kovu je zachována delší vzdálenost hořáku od obrobku. Plazmové drážkování lze použít v různých aplikacích, včetně odstranění svaru pro přepracování.
Některé z našich plazmových řezaček jsou zabudovány do CNC stolu. CNC stoly mají počítač pro ovládání hlavy hořáku, aby produkovaly čisté ostré řezy. Naše moderní CNC plazmové zařízení je schopné víceosého řezání silných materiálů a umožňuje tak složité svarové spoje, které jinak nejsou možné. Naše plazmové obloukové řezačky jsou vysoce automatizované díky použití programovatelných ovládacích prvků. U tenčích materiálů dáváme přednost řezání laserem před řezáním plazmou, většinou kvůli vynikajícím schopnostem naší laserové řezačky při řezání otvorů. Nasazujeme také vertikální CNC plazmové řezací stroje, které nám nabízejí menší půdorys, zvýšenou flexibilitu, lepší bezpečnost a rychlejší provoz. Kvalita ostří plazmového řezu je podobná jako u procesů kyslíko-palivového řezání. Protože však plazmový proces řeže tavením, charakteristickým znakem je vyšší stupeň tavení směrem k horní části kovu, což má za následek zaoblení horní hrany, špatnou pravoúhlost hrany nebo zkosení na hraně řezu. Používáme nové modely plazmových hořáků s menší tryskou a tenčím plazmovým obloukem, abychom zlepšili zúžení oblouku a vytvořili rovnoměrnější ohřev v horní a spodní části řezu. To nám umožňuje dosáhnout přesnosti blízké laseru na plazmě řezaných a obráběných hranách. Naše High TOLERANCE PLAZMOVÉ OBLOUBENÍ (HTPAC) systémy pracují s vysoce omezenou plazmou. Zaostření plazmy je dosaženo nucením plazmy generované kyslíkem vířit, když vstupuje do plazmového otvoru a sekundární proud plynu je vstřikován po proudu od plazmové trysky. Máme samostatné magnetické pole obklopující oblouk. To stabilizuje plazmový paprsek udržováním rotace vyvolané vířícím plynem. Kombinací přesného CNC řízení s těmito menšími a tenčími hořáky jsme schopni vyrábět díly, které vyžadují malou nebo žádnou konečnou úpravu. Rychlosti úběru materiálu při plazmovém obrábění jsou mnohem vyšší než u procesů elektroerozivního obrábění (EDM) a obrábění laserovým paprskem (LBM) a díly lze obrábět s dobrou reprodukovatelností.
PLAZMOVÉ OBLOUKOVÉ SVAŘOVÁNÍ (PAW) je proces podobný svařování plynovým wolframovým obloukem (GTAW). Elektrický oblouk je vytvořen mezi elektrodou obecně vyrobenou ze slinutého wolframu a obrobkem. Klíčovým rozdílem od GTAW je to, že u PAW lze umístěním elektrody do těla hořáku plazmový oblouk oddělit od obalu ochranného plynu. Plazma je poté protlačováno měděnou tryskou s jemným vrtáním, která zužuje oblouk a plazma vystupující z otvoru při vysokých rychlostech a teplotách blížících se 20 000 °C. Svařování plazmovým obloukem je pokrokem oproti procesu GTAW. Proces svařování PAW využívá netavnou wolframovou elektrodu a oblouk zúžený přes měděnou trysku s jemným otvorem. PAW lze použít ke spojování všech kovů a slitin, které jsou svařitelné pomocí GTAW. Je možné několik základních variací procesu PAW změnou proudu, průtoku plazmového plynu a průměru otvoru, včetně:
Mikroplazma (< 15 ampérů)
Režim tavení (15–400 ampér)
Režim klíčové dírky (>100 Ampérů)
Při svařování plazmovým obloukem (PAW) získáváme větší koncentraci energie ve srovnání s GTAW. Je dosažitelný hluboký a úzký průnik s maximální hloubkou 12 až 18 mm (0,47 až 0,71 palce) v závislosti na materiálu. Větší stabilita oblouku umožňuje mnohem delší délku oblouku (odstup) a mnohem větší toleranci ke změnám délky oblouku.
Nevýhodou však je, že PAW vyžaduje relativně drahé a složité vybavení ve srovnání s GTAW. Také údržba hořáku je kritická a náročnější. Další nevýhody PAW jsou: Svařovací postupy bývají složitější a méně tolerantní k variacím ve fit-upu atd. Potřebné dovednosti operátora jsou o něco více než u GTAW. Výměna clony je nutná.